滚动轴承寿命计1
发电厂-滚动轴承寿命计算(检修标准)

滚动轴承寿命计算一、额定寿命与额定动载荷1、轴承寿命在一定载荷作用下,轴承在出现点蚀前所经历的转数或小时数,称为轴承寿命。
由于制造精度,材料均匀程度的差异,即使是同样材料,同样尺寸的同一批轴承,在同样的工作条件下使用,其寿命长短也不相同。
若以统计寿命为1单位,最长的相对寿命为4单位,最短的为0.1-0.2单位,最长与最短寿命之比为20-40倍。
为确定轴承寿命的标准,把轴承寿命与可靠性联系起来。
2、额定寿命同样规格(型号、材料、工艺)的一批轴承,在同样的工作条件下使用,90%的轴承不产生点蚀,所经历的转数或小时数称为轴承额定寿命。
3、基本额定动载荷为比较轴承抗点蚀的承载能力,规定轴承的额定寿命为一百万转(106)时,所能承受的最大载荷为基本额定动载荷,以C表示。
也就是轴承在额定动载荷C作用下,这种轴承工作一百万转(106)而不发生点蚀失效的可靠度为90%,C越大承载能力越高。
对于基本额定动载荷(1)向心轴承是指纯径向载荷(2)推力球轴承是指纯轴向载荷(3)向心推力轴承是指产生纯径向位移得径向分量二、轴承寿命的计算公式:洛阳轴承厂以208轴承为对象,进行大量的试验研究,建立了载荷与寿命的数字关系式和曲线。
式中:--轴承载荷为P时,所具有的基本额定寿命(106转)L10C--基本额定动载荷 Nε--指数对球轴承:ε=3对滚子轴承:ε=10/3P--当量动载荷(N)把在实际条件下轴承上所承受的载荷: A、R ,转化为实验条件下的载荷称为当量动载荷,对轴承元件来讲这个载荷是变动的,实验研究时,轴承寿命用106转为单位比较方便(记数器),但在实际生产中一般寿命用小时表示,为此须进行转换L10×106=Lh×60n所以滚动轴承寿命计算分为:1、已知轴承型号、载荷与轴的转速,计算Lh;2、已知载荷、转速与预期寿命,计算C ,选取轴承型号。
通常取机器的中修或大修界限为轴承的设计寿命,一般取L h '=5000,对于高温下工作的轴承应引入温度系数ftCt=ftC上两式变为:对于向心轴承对于推力轴承三、当量动载荷P的计算在实际生产中轴承的工作条件是多种多样的,为此,要把实际工作条件下的载荷折算为假想寿命相同的实验载荷--当量载荷。
滚动轴承疲劳寿命威布尔分布三参数的研究
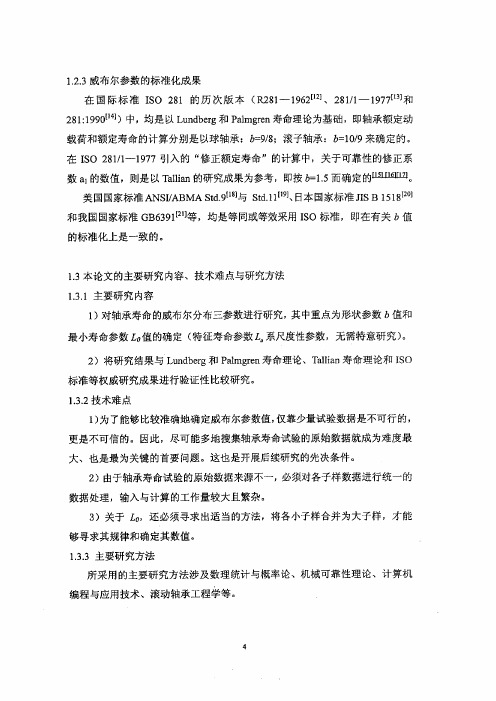
绘制出一条直线。该直线与F(三)=63.2%水平线相交的点所对应的寿命值,即 为三。值。若该直线与横坐标的夹角为0,则可得
二参数威布尔分布的研究重点是形状参数b值的确定,其代表性研究成果 为Lundberg和Palmgren寿命理论。三参数威布尔分布的研究重点则是在二参 数威布尔分布研究的基础上,主要关注最小寿命参数岛值的确定,其代表性研 究成果为Tallian寿命理论。ISO标准和有关国家标准则对轴承寿命的威布尔形 状参数作了权威性认同与规定。但是,由于威布尔参数的精确(高可靠性与高 置信度的)确定,特别是位置参数即最小寿命参数岛值的确定,需要大量的试 验作支撑,以寻求其统计规律性,财力、物力与时间耗费巨大,因此,有关研 究成果在种种局限性之下所导致的或者难以涉及,或者做不深入,或者做不准 确,就成为必然之事。也正因为如此,继续深入开展相关研究,以求不断完善 威布尔分布、尤其是三参数威布尔分布在轴承寿命方面的应用,其理论意义与 实用价值就十分重大。
1.3本论文的主要研究内容、技术难点与研究方法 1.3.1主要研究内容
1)对轴承寿命的威布尔分布三参数进行研究,其中重点为形状参数b值和 最小寿命参数如值的确定(特征寿命参数L系尺度性参数,无需特意研究)。
2)将研究结果与Lundberg和Palmgren寿命理论、Tallian寿命理论和ISO 标准等权威研究成果进行验证性比较研究。 1.3.2技术难点
#
图2--3 r=O,a=2,而∥取不同数值时的,(f)曲线
滚动轴承受力计算及寿命计算

滚动轴承相关计算1.当量动载荷轴承承受的载荷,虽有单一径向载荷或轴向载荷,但是,实际上却往往是同时承受径向载荷与轴向载荷的联合载荷,而且其大小和方向也会发生变化。
在这种情况下,计算轴承疲劳寿命不能直接采用轴承承受的载荷。
为此,就要假定一个在各种旋转条件与载荷条件下,都能保证与轴承实际疲劳寿命等同,大小恒定,且通过轴承中心的假想载荷。
这一假想载荷,称为当量动载荷。
设径向当量载荷为P r,径向载荷为F r,轴向载荷为F a,接触角为α,则径向当量载荷与轴承载荷的关系将近似于下列公式:P r=XF r+YF a (1)式中, X:径向载荷系数Y:轴向载荷系数轴向载荷系数随接触角而变;滚子轴承接触角恒定,与接触角无关;单列深沟球轴承与角触球轴承的接触角却随着轴向载荷加大而增大。
接触角的这种变化,可用基本而定静载荷C0r与轴向载荷F a的比值来表示。
为此,在表1中列出了该比值莹莹接触角的轴向载荷系数。
当同时承受径向载荷与轴向载荷、接触角α≠90°时,推力轴承的轴向当量载荷P a为:P a=XF r+YF a (2)2.三列组合角接触球轴承的当量动载荷当使用角接触球轴承并要求承受较大轴向载荷时,如图所示,采用3套单列轴承组合的组合方法有3种,分别以联装代号DBD、DFD、DTD来表示。
在计算这种组合轴承的疲劳寿命时,与单列轴承或双列轴承一样,也采用由轴承承受的径向载荷与轴向载荷求出的当量动载何进行计算。
设径向当量载荷为P r,径向载荷为F r,轴向载荷为F a,接触角为α,则径向当量载荷与轴承载荷的关系将近似于下列公式:P r=XF r+YF a (1)式中, X:径向载荷系数Y:轴向载荷系数轴向载荷系数,会随着接触角而变化。
接角角较小的角接触球轴承在轴向载荷增大时,接触角也会变大。
接触角的这一变化.可以用基本额定静载荷C0r与轴向载荷F a的比值来表示。
因此、接触角为15°的角接触球轴承,就表示与该比值相应接触角的轴向载荷系数。
滚动轴承寿命校核
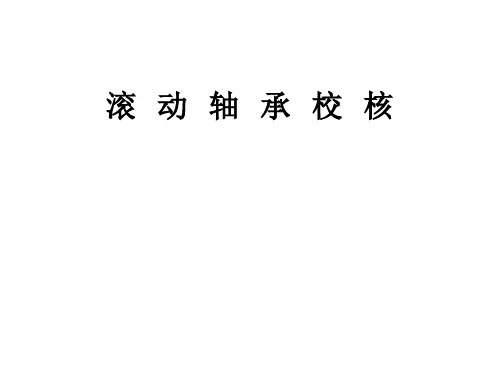
70000B(=40°) Fd=1.14Fr
2
Fa1 C0
1005.05 20000
0.0503
Fa 2 C0
605.05 20000
0.0303
由表2进行插值计算,得e1=0.422,e2=0.401。再计算
5、应用
例 设某支撑根据工作条件决定选用深沟球轴承。轴承径向载
荷Fr=5500N,轴向载荷Fa=2700N,轴承转速n=1250r/min,装轴
承处的轴颈直径可在50~60mm范围内选择,运转时有轻微冲击,
预期计算寿命Lh’=5000h。试选择其轴承型号。
解
1. 求比值
Fa Fr
2700 5500
产生派生轴向力的原因:承载区内每个滚动体的反力 都是沿滚动体与套圈接触点的法线方向传递的。
轴承安装不同时,产生的派生轴向力也不同。
工作情况2
派生力的方向总是由轴承宽度中点指向轴承载荷 中心。
S的方向:沿轴线由轴承外圈的宽边→窄边。
轴承所受总载荷的作用线与轴承轴心线的交点 , 即 为轴承载荷中心(支反力的作用点)。
4、滚动轴承寿命的计算公式
4.1 轴承的载荷-寿命曲线
如右图所示曲线是在
大量试验研究基础上得出
的代号为6208轴承的载荷寿命曲线。其它型号的轴
承也有与上述曲线的函数
规律完全一样的载荷-寿命
曲线。
该曲线公式表示为:
轴承的载荷-寿命曲线
L10
(C P
)(106 转)
式中,L10的单位为106r。 P为当量动载荷(N)。
角接触球轴承及圆锥滚子轴承的派生轴向力的大小取 决于该轴承所受的径向载荷和轴承结构,按下表计算。
§13-4 滚动轴承的寿命计算
滚动轴承寿命预测与故障诊断

滚动轴承寿命预测与故障诊断滚动轴承是机械传动系统中常用的一种关键零部件,因其结构简单、可靠性高、运转稳定等特点被广泛应用于工业制造、交通运输、航天航空等领域。
然而,在长期的使用中,由于负载、转速、温度等因素的影响,滚动轴承很容易出现各种故障,严重影响机械设备的正常性能。
因此,预测滚动轴承的寿命并对其故障进行诊断具有极其重要的意义,不仅能够减少机器设备的维修成本,更能提高机器设备的运行效率和安全性。
一、滚动轴承寿命预测的基本理论滚动轴承寿命预测是指通过对滚动轴承在特定工况下的运行情况进行数学模型建立和系统分析,来预测滚动轴承在未来一段时间内的使用寿命。
其基本理论是寿命公式理论,即基于统计学原理,通过对有限数量的试验数据进行分析,来估计大量相似产品的寿命。
该理论最早由Weibull提出,现广泛应用于各种设备的寿命预测中。
滚动轴承的寿命是指在一定的负载、转速、温度等工况条件下,维持基本性能的使用寿命。
通常将运转时间作为寿命评定标准,其评定方法有两种,即L10寿命和L50寿命。
其中L10寿命是指在有10%以上的滚动轴承失败的情况下所需要的运转时间,L50寿命则是指在有50%以上的滚动轴承失败的情况下所需的运转时间。
滚动轴承寿命预测的方法一般有以下几种:1、基于模型的预测法该方法是在通过对相关参数的观测和测量得到大量样本数据的基础上,建立滚动轴承故障模型,对其进行数学分析和计算,从而提出一定的预测理论。
该方法的优点是可以快速准确地预测滚动轴承的寿命,缺点是在模型建立过程中,需要考虑多种因素的影响,模型的建立难度较高。
2、基于统计模型的预测法该方法是通过统计分析大量实测数据,确定影响滚动轴承寿命的关键因素,建立相应的统计模型,并通过多种分析方法,包括生存分析、半参数估计和回归分析等来预测滚动轴承的寿命。
该方法的优点是具有较强的实用性和普适性,但缺点是要求样本数据的质量和数量均较高,在实际操作中要具备较为广泛的背景知识和大量的经验。
机械设计(9.5.1)--滚动轴承寿命计算公式

一、基本概念
1.轴承的寿命
在一定载荷作用下,轴承运转到任一滚动体或内、外圈滚道上出现疲劳点蚀前所经历的总转数。
寿命数据离散性非常大。
2.一批轴承的寿命
对于一批同型号的滚动轴承,在一定条件下进行疲劳试
验,对试验数据统计处理后,得
出轴承的疲劳破坏概率与转数间
的关系。
一、基本概念
3.基本额定寿命
一批同型号的轴承,在同一条件下运转,当有10%的轴承产生疲劳点蚀时,
轴承所经历的总转数L
(单位106转)或工作
10
(单位h),称为滚动轴承的基本小时数L
10h
额定寿命。
4.基本额定动载荷
=1(106)时轴承能
基本额定寿命L
10
够承受极限载荷称为基本额定动载荷,用C
表示。
反映了轴承承载能力的大小。
二、计算公式
L 10/106r 0151015C
P /N r 10,1610101010εε
εε
⎪⎭⎫ ⎝⎛=====P C L C L P C P L L P 时
当常数
二、计算公式
h
6010r 10t 6h 106t 10εε⎪⎭⎫ ⎝⎛=⎪⎭
⎫ ⎝⎛=P C f n L P C f
L 当轴承的预期寿命取定时,可求出轴承应具有的基本额定动载荷
9-5 滚承寿命算公式 三、不同可靠度下滚承寿命算
动轴计动轴计
三、不同可靠度下滚动轴承寿命计算
10
1L L n α=
可靠度R / %
909596979899α1 1.00.620.530.440.330.21。
滚动轴承的寿命
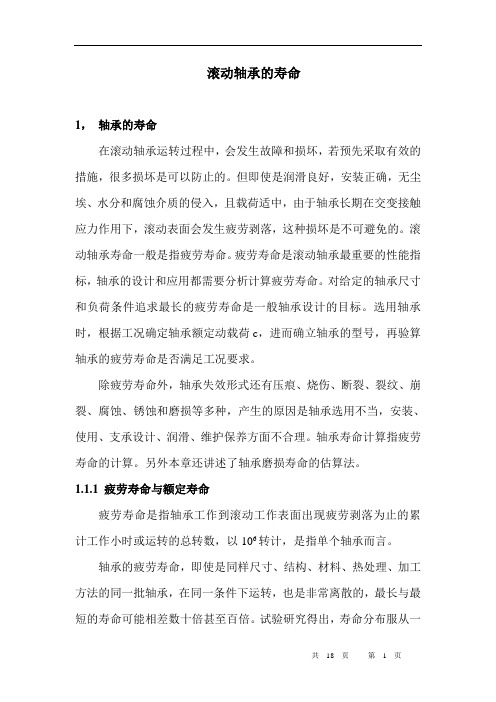
滚动轴承的寿命1,轴承的寿命在滚动轴承运转过程中,会发生故障和损坏,若预先采取有效的措施,很多损坏是可以防止的。
但即使是润滑良好,安装正确,无尘埃、水分和腐蚀介质的侵入,且载荷适中,由于轴承长期在交变接触应力作用下,滚动表面会发生疲劳剥落,这种损坏是不可避免的。
滚动轴承寿命一般是指疲劳寿命。
疲劳寿命是滚动轴承最重要的性能指标,轴承的设计和应用都需要分析计算疲劳寿命。
对给定的轴承尺寸和负荷条件追求最长的疲劳寿命是一般轴承设计的目标。
选用轴承时,根据工况确定轴承额定动载荷c,进而确立轴承的型号,再验算轴承的疲劳寿命是否满足工况要求。
除疲劳寿命外,轴承失效形式还有压痕、烧伤、断裂、裂纹、崩裂、腐蚀、锈蚀和磨损等多种,产生的原因是轴承选用不当,安装、使用、支承设计、润滑、维护保养方面不合理。
轴承寿命计算指疲劳寿命的计算。
另外本章还讲述了轴承磨损寿命的估算法。
1.1.1 疲劳寿命与额定寿命疲劳寿命是指轴承工作到滚动工作表面出现疲劳剥落为止的累计工作小时或运转的总转数,以106转计,是指单个轴承而言。
轴承的疲劳寿命,即使是同样尺寸、结构、材料、热处理、加工方法的同一批轴承,在同一条件下运转,也是非常离散的,最长与最短的寿命可能相差数十倍甚至百倍。
试验研究得出,寿命分布服从一定的统计规律,要用数理统计方法处理数据,以计算在一定损坏概率下的轴承寿命。
额定疲劳寿命,是指同一型号的一批轴承,在同一条件下运转,其中90%的轴承能够不出现疲劳剥落的运转总转数,以610转计。
或在一定旋转速度下的工作小时数,记作10L 。
1.1.2 基本额定动载荷C 和当量动载荷额定动载荷c 是指在轴承内圈旋转、外圈静止的条件下,额定寿命为100万转时轴承能够承受的载荷。
对于向心轴承是纯径向载荷,对于推力轴承是指中心轴向载荷,它是表示滚动轴承的载荷能力,是轴承的一项主要性能参数,是选择轴承的主要技术依据。
每种轴承的额定动载荷都已按GB6391-94(等同ISO281/1-1977)计算,且标明在产品样本中。
滚动轴承的失效形式及寿命计算

轴承寿命曲线
滚动轴承的失效形式及寿命计算
1.3 基本额定动载荷及寿命计算
大量试验表明:对于相同型号的轴承,在不同载荷F1, F2 , F3 ,…作用下,若轴承的 寿命分别为L1 , L2 , L3 ,… (106转),则它们之间有如下的关系:
滚动轴承的失效形式及寿命计算
1.4 当量动载荷的计算
滚动轴承的基本额定动载荷是在一定条件下确定的。对向心轴承是指承受纯径向载荷; 对推力轴承是指承受中心轴向载荷。如果作用在轴承上的实际载荷与上述条件不一样,必须 将实际载荷换算为与上述条件相同的载荷后,才能与基本额定动载荷进行比较。换算后的载 荷是一种假定的载荷,称为当量动载荷。径向和轴向载荷分别用Fr和Fa表示。
对于向心轴承,径向当量动载荷P与实际载荷Fr和Fa的关系式为
径向轴承只承受径向载荷时,其当量动载荷为
推力轴承只能承受轴向载荷,其当量动载荷为
滚动轴承的失效形式及寿命计算
1.1 主要失效形式
1. 滚动体ห้องสมุดไป่ตู้力
滚动轴承在通过轴心线的轴向载荷(中心轴向载荷)犉犪作用下,可认为各滚动体所承 受的载荷是相等的。当轴承受纯径向载荷Fr作用时(见图),由于各接触点上存在弹性变形, 使内圈沿Fr方向下移一距离δ,上半圈滚动体不承受载荷,而下半圈各滚动体承受不同的载 荷。处于Fr作用线最下位置的滚动体受载最大Fmax ,而远离作用线的各滚动体,其受载就逐 渐减小。对于α=0°的向心轴承可以导出
滚动轴承的失效形式及寿命计算
2. 滚动轴承的失效形式
(1)疲劳破坏 (2)塑性变形
径向载荷的分布
滚动轴承的失效形式及寿命计算
1.2 轴承寿命
轴承的套圈或滚动体的材料首次出现疲劳点蚀前, 一个套圈相对于另一个套圈的转数,称为轴承的寿命。 寿命还可以用在恒定转速下的运转小时数来表示。
- 1、下载文档前请自行甄别文档内容的完整性,平台不提供额外的编辑、内容补充、找答案等附加服务。
- 2、"仅部分预览"的文档,不可在线预览部分如存在完整性等问题,可反馈申请退款(可完整预览的文档不适用该条件!)。
- 3、如文档侵犯您的权益,请联系客服反馈,我们会尽快为您处理(人工客服工作时间:9:00-18:30)。
滚动轴承寿命计算(角接触球轴承7009C,正装结构)'
c7r=25800; % 额定动载荷(N)
c70r=20500; % 额定静载荷(N)
s7a=round(0.4*fra); % A轴承内部轴向力(N)
s7b=round(0.4*frb); % B轴承内部轴向力(N)
if fa+s7b>=s7a
fa7a=fa+s7b; % 确定紧轴承A轴向载荷(N) fa7b=s7b; % 确定松轴承B轴向载荷(N) else
fa7b=abs(fa-s7a); % 确定紧轴承B轴向载荷(N) fa7a=s7a; % 确定松轴承A轴向载荷(N) end
xda=fa7a/c70r; % 轴承A相对轴向载荷
ea=0.465; % A判断参数(插值查表) xdb=fa7b/c70r; % 轴承B相对轴向载荷
eb=0.41; % B判断参数(插值查表)
if fa7a/fra>ea % 轴承A轴向载荷与径向载荷之比
x7a=0.44; % 确定A轴承载荷折算系数X y7a=1.21; % 确定A轴承载荷折算系数Y else
x7a=1;
y7a=0;
end
p7a=round(x7a*fra+y7a*fa7a); % 轴承A当量动载荷(N)
if fa7b/frb>eb % 轴承B轴向载荷与径向载荷之比
x7b=0.44; % 确定B轴承载荷折算系数X y7b=1.37; % 确定B轴承载荷折算系数Y else
x7b=1;
y7b=0;
end
p7b=round(x7b*frb+y7b*fa7b); % 轴承B当量动载荷(N)
fp=1.5; % 轴承载荷系数(减速器中等冲击)
lh7a=round(1e6/60/n2*(c7r/fp/p7a)^3); % 计算轴承A寿命(h)
lh7b=round(1e6/60/n2*(c7r/fp/p7b)^3); % 计算轴承B寿命(h)
disp ' '
disp ' ========== 角接触球轴承寿命计算 ==========';
fprintf(1,' 7009C轴承额定动载荷 c7r = %3.0f N \n',c7r); fprintf(1,' 额定静载荷 c70r = %3.0f N \n',c70r); fprintf(1,' A轴承内部轴向力 s7a = %3.0f N \n',s7a); fprintf(1,' B轴承内部轴向力 s7b = %3.0f N \n',s7b);
fprintf(1,' [A轴承]-轴向载荷 fa7a = %3.0f N \n',fa7a); fprintf(1,' 相对轴向载荷 xda = %3.3f \n',xda); fprintf(1,' 判断参数 ea = %3.3f \n',ea);
fprintf(1,' 轴向与径向载荷之比 fae = %3.3f \n',fa7a/fra); fprintf(1,' 径向载荷系数 x7a = %3.2f \n',x7a); fprintf(1,' 轴向载荷系数 y7a = %3.2f \n',y7a); fprintf(1,' 当量动载荷 p7a = %3.0f N \n',p7a); fprintf(1,' 轴承寿命 lh7a = %3.0f h \n',lh7a); fprintf(1,' [B轴承]-轴向载荷 fa7b = %3.0f N \n',fa7b); fprintf(1,' 相对轴向载荷 xdb = %3.3f \n',xdb); fprintf(1,' 判断参数 eb = %3.3f \n',eb);
fprintf(1,' 轴向与径向载荷之比 fbe = %3.3f \n',fa7b/frb); fprintf(1,' 径向载荷系数 x7b = %3.2f \n',x7b); fprintf(1,' 轴向载荷系数 y7b = %3.2f \n',y7b); fprintf(1,' 当量动载荷 p7b = %3.0f N \n',p7b); fprintf(1,' 轴承寿命 lh7b = %3.0f h \n',lh7b);。