刀尖半径补偿
刀尖半径补偿的概念和指令格式

刀尖半径补偿的概念和指令格式
刀尖半径补偿是数控编程中的一种功能,用于在铣削、切割等加工过程中对刀具进行补偿,以保证加工精度和避免工具干涉。
以下是刀尖半径补偿的概念和指令格式的简要说明:
概念:
刀尖半径补偿是指在进行数控加工时,通过编程指令将加工轮廓的实际位置与所设定的轮廓进行调整,以补偿刀具切削时的偏差,从而获得准确的加工结果。
刀尖半径补偿通常适用于具有曲线形状的轮廓加工,如圆弧、椭圆等。
指令格式:
刀尖半径补偿指令通常分为两种,分别为G41和G42,其指令格式如下:
1. G41 Dn (n为刀具号):
- 启用刀尖半径补偿,并指定刀具的刀尖半径补偿偏移量为Dn。
- 刀具号(n)可根据实际情况进行设置。
2. G42 Dn (n为刀具号):
- 启用刀尖半径补偿,并指定刀具的刀尖半径补偿偏移量为Dn。
- 刀具号(n)可根据实际情况进行设置。
注意事项:
- 在启用刀尖半径补偿之前,需要先定义刀具的刀尖半径补偿偏移量,可以通过G10指令来定义和修改。
- 刀尖半径补偿的偏移量Dn可以为正值或负值,具体取决于刀具和加工的特性。
- 在加工中,刀具路径将根据刀尖半径补偿的偏移量进行自动调整,以保证加工精度和避免工具干涉。
以上是关于刀尖半径补偿概念和指令格式的简要说明,具体的应用还需要根据不同的数控系统和加工需求进行详细设置和调整。
G41和G42刀尖半径补偿
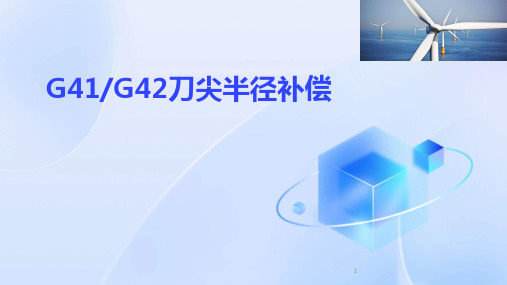
1
G41,G42:刀尖半径补偿
由于实际刀具有一定的刀尖圆角半径,当刀具长度补偿建立后,由于 假想刀尖随编程轨迹运行,对非平行坐标轴方向的轮廓加工时将造成 一定的加工误差(过车或欠车),刀尖半径越大,误差越大。采用刀 具半径补偿可解决。
刀具必须有相应的D号才能有效。刀尖半径补偿通过G41/G42生效。 控制器自动计算出当前刀具运行所产生的、与编程轮廓等距离的刀 具轨迹。 必须处于G18(ZX平面)有效状态! G41 X… Z…;在工件轮廓左边刀补有效; G42 X… Z…;在工件轮廓右边刀补有效; G40 取消刀尖半径补偿。 注释:只有在线性插补时(G0,G1)才可以进行G41/G42的选择。
2
无刀尖半径补偿示例
3
G41,G42:刀尖半径补偿的方向
4
G41,G42:刀尖半径补偿的引入和取消A M来自N05
G41,G42:刀尖半径补偿应用示例
6
THANKS
感谢观看
7
刀尖半径补偿编程实例
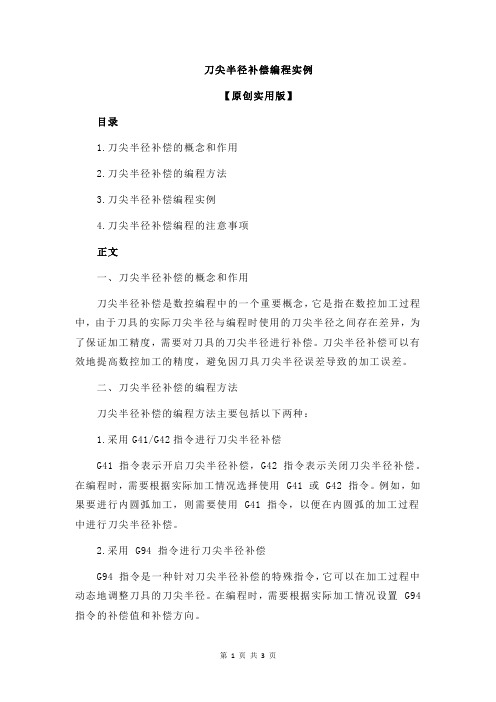
刀尖半径补偿编程实例【原创实用版】目录1.刀尖半径补偿的概念和作用2.刀尖半径补偿的编程方法3.刀尖半径补偿编程实例4.刀尖半径补偿编程的注意事项正文一、刀尖半径补偿的概念和作用刀尖半径补偿是数控编程中的一个重要概念,它是指在数控加工过程中,由于刀具的实际刀尖半径与编程时使用的刀尖半径之间存在差异,为了保证加工精度,需要对刀具的刀尖半径进行补偿。
刀尖半径补偿可以有效地提高数控加工的精度,避免因刀具刀尖半径误差导致的加工误差。
二、刀尖半径补偿的编程方法刀尖半径补偿的编程方法主要包括以下两种:1.采用G41/G42指令进行刀尖半径补偿G41 指令表示开启刀尖半径补偿,G42 指令表示关闭刀尖半径补偿。
在编程时,需要根据实际加工情况选择使用 G41 或 G42 指令。
例如,如果要进行内圆弧加工,则需要使用 G41 指令,以便在内圆弧的加工过程中进行刀尖半径补偿。
2.采用 G94 指令进行刀尖半径补偿G94 指令是一种针对刀尖半径补偿的特殊指令,它可以在加工过程中动态地调整刀具的刀尖半径。
在编程时,需要根据实际加工情况设置 G94 指令的补偿值和补偿方向。
三、刀尖半径补偿编程实例假设我们要加工一个直径为 100mm 的内圆弧,使用一把刀具半径为5mm 的刀具进行加工,加工过程中需要进行刀尖半径补偿。
我们可以按照以下步骤进行编程:1.首先,设置刀具的半径补偿值。
根据刀具半径和加工直径的比例,我们可以计算出刀尖半径补偿值 R 为2.5mm(5mm * 0.5)。
2.然后,在编程时使用 G41 指令开启刀尖半径补偿,并设置刀尖半径补偿值 R 为 2.5mm。
3.接下来,编写加工程序。
假设刀具的初始位置为 X0,Z0,则加工程序可以表示为:```G00 X0 Z0G94 R2.5G1 X100 Z-100```在上述程序中,G00 指令表示快速移动刀具到初始位置,G94 指令表示设置刀尖半径补偿值,G1 指令表示进行直线插补运动。
刀尖圆弧补偿(详细介绍)

刀尖圆弧补偿数控车削加工是以假想刀尖进行编程,而切削加工时,由于刀尖圆弧半径的存在,实际切削点与假想刀尖不重合,从而产生加工误差。
为满足加工精度要求,又方便编程,需对刀尖圆弧半径进行补偿。
本文对刀尖半径补偿的概念,刀尖方位的确定、补偿方法和参数设置进行了介绍。
同时阐述了刀尖半径补偿的过程并分析了实例,就应用过程中出现的问题加以介绍。
数控机床是按照程序指令来控制刀具运动的。
众所周知,我们在编制数控车床加工程序时,都是把车刀的刀尖当成一个点来考虑,即假想刀尖,如图1所示的A点。
编程时就以该假想刀尖点A来编程,数控系统控制A点的运动轨迹。
但实际车刀尤其是精车刀,在其刀尖部分都存在一个刀尖圆弧,这一圆角一方面可以提高刀尖的强度,另一方面可以改善加工表面的表面粗糙度。
由于刀尖圆弧的存在,车削时实际起作用的切削刃是圆弧各切点。
而常用的对刀操作是以刀尖圆弧上X、Z方向相应的最突出点为准。
如图1所示,这样在X向、Z向对刀所获得的刀尖位置是一个假想刀尖。
按假想刀尖编出的程序在车削外圆、内孔等与Z轴平行的表面时,是没有误差的,即刀尖圆弧的大小并不起作用;但当车右端面、锥面及圆弧时,就会造成过切或少切,引起加工表面形状误差,如图2所示为以假想刀尖位置编程时的过切及少切现象。
编程时若以刀尖圆弧中心编程,可避免过切和少切的现象,但计算刀位点比较麻烦,并且如果刀尖圆弧半径值发生变化,还需改动程序。
数控系统的刀具半径补偿功能正是为解决这个问题所设定的。
它允许编程者不必考虑具体刀具的刀尖圆弧半径,而以假想刀尖按工件轮廓编程,在加工时将刀具的半径值R存入相应的存储单元,系统会自动读入,与工件轮廓偏移一个半径值,生成刀具路径,即将原来控制假想刀尖的运动转换成控制刀尖圆弧中心的运动轨迹,则可以加工出相对准确的轮廓。
这种偏移称为刀尖半径补偿。
如图3所示。
一、刀尖半径补偿的方式现代机床基本都具有刀具补偿功能,为编程提供了方便。
刀尖圆弧半径补偿是通过G41、G42、G40代码及T代码指定的假想刀尖号加入或取消的,如表所示。
刀尖半径补偿计算公式

刀尖半径补偿计算公式刀尖半径补偿是数控加工中常用的技术,用于解决加工过程中刀具的半径误差。
该技术可以在加工过程中根据刀具的真实半径,自动调整加工轨迹,从而达到更高的加工精度和效率。
在实际应用中,刀尖半径补偿计算是非常重要的一环。
刀尖半径补偿计算公式的初衷是为了解决因刀具半径误差产生的加工误差。
在CNC数控机床的加工中,刀具的半径并不是完全一致的,而是有一定的偏差。
为了保证加工精度,就需要进行补偿,把偏差考虑进去。
在常见的加工中,刀具的偏差主要分为两种:正向补偿和负向补偿。
如果刀具实际半径大于理论半径,则需要进行负向补偿,即在加工程序中的刀补指令后加上“-”符号,以表示半径补偿量。
如:G41 X... Y... D... Z... H... -R0.5 F...。
其中,-R0.5表示刀具实际半径比理论半径小0.5mm,这个值是由加工过程中的实际测量得出的。
如果刀具实际半径小于理论半径,则需要进行正向补偿,即在加工程序中的刀补指令后加上“+”符号,以表示半径补偿量。
如:G42 X... Y... D... Z... H... +R0.2 F...。
其中,+R0.2表示刀具实际半径比理论半径大0.2mm。
在实际应用中,刀具的半径偏差需要通过测量得出,然后根据计算公式进行补偿。
刀具的半径偏差可以通过多种方法进行测量,常见的方法有“触发法”和“影像测量法”。
触发法是将刀具接触到工件上,然后使用触发测量仪器来测量刀具的半径。
常用的测量仪器有三角板、球规、千分表和测微计等。
影像测量法则是使用光学测量仪器来测量刀具的大小和形状,一般采用CCD影像测量仪、激光扫描仪等设备。
相比于触发法,影像测量法更加准确和精确,成为目前主要的刀具测量方法之一。
刀尖半径补偿计算公式的求解过程是比较复杂的,在实际应用中一般使用数控加工机床自带的计算软件或专业的刀具选型软件来进行计算。
一般来说,计算公式是由加工轨迹、刀具半径、刀具方向等多个因素组成的,具体的数学推导过程较为繁琐,在此不进行详细介绍。
刀尖半径补偿计算公式

刀尖半径补偿计算公式
刀尖半径补偿是数控加工中的一项重要技术,用于保证加工轮廓的尺寸精度。
刀具的尺寸并不是完全准确的,因此在加工过程中会出现误差,特别是在弯曲或曲线轮廓的加工中,误差会更加明显。
为了解决这个问题,引入了刀尖半径补偿技术。
刀尖半径补偿的基本原理是将刀具轨迹进行补偿,以抵消刀具的尺寸误差。
在进行刀尖半径补偿时,需要计算出刀尖半径补偿量,以便于校正刀具的轨迹。
刀尖半径补偿的计算公式可以根据不同的数控系统和加工方式有所不同,下面是一种常见的计算公式作为参考:
补偿值 = 理论值 - 实际值
其中,理论值是在进行数控编程时设定的轮廓大小,实际值是实际加工得到的轮廓大小。
通过计算补偿值,可以得到刀尖半径补偿量,从而进行刀具轨迹的补偿。
此外,刀尖半径补偿还涉及到切入角度和切入刀宽等参数的计算。
在进行刀尖半径补偿时,需要根据刀具的特性和加工要求,综合考虑切入角度和切入刀宽等因素,确定合适的补偿值。
刀尖半径补偿的计算公式不仅仅是一个简单的公式,还涉及到数学模型、机床的调整参数等一系列的考虑因素。
在实际应用中,还需要结合具体的加工情况和数控系统的要求,选择合适的计算公式和计算方法。
总之,刀尖半径补偿是数控加工中的一项重要技术,可以有效提高加工精度。
在实际应用中,需要根据具体情况选择合适的计算公式和方法,以实现刀具轨迹的精确控制。
刀具半径补偿(G41、G42)和刀尖号
(1)、在数控车床中,着先沿着 Z 轴的正方向向负方向观察,然后顺着刀具运动的方向观察,若 刀具在工件的左边,用 G41;反之用 G42。外圆加工用 G41,内孔加工取 G42
G40(G41/G42) G01(G00) X Z F G40:取削刀尖圆弧半径补偿. G41:刀尖圆弧半径左补偿(左刀补)。顺着刀具运动方向看,刀具在工件左侧,如图(左)。 G42:刀尖圆弧半径右补偿(右刀补)。顺着刀具运动方向看,刀具在工件右侧,如图(右).
(2)、在刀具形状参数里输入刀尖圆弧半径 R 和刀位点 T(1 到 9 九个),编程时程序里使用刀 尖圆弧半径补偿功能指令 G41(左)/G42(右)就可以了, 这样在车削的时候系统就可以对刀尖圆弧 半径进行补偿了,一般在车角度直线(或圆椎)和圆弧(倒角或倒圆弧)才用,车单一的圆柱或平面 可以不用。 一般情况下,常用的是 2、3、9。分别对应内形加工(镗孔)、外形加工(外圆),和球 头刀加工,如图 2.4 所示。
4 5 1
8 9 6
+X
刀尖圆弧半径补偿的概念和作用
数控机床在加工过程中,它所控制的是刀具中心的轨迹,为了方便起见,用户总是按零件轮廓编制加工程序,因而为了加工所需的零件轮廓,在进行内轮廓加工时,刀具中心必须向零件的内侧偏移一个刀具半径值;在进行外轮廓加工时,刀具中心必须向零件的外侧偏移一个刀具半径值。
这种根据按零件轮廓编制的程序和预先设定的偏置参数,数控装置能实时自动生成刀具中心轨迹的功能称为刀具半径补偿功能。
在概述图中,实线为所需加工的零件轮廓,虚线为刀具中心轨迹。
根据ISO标准,当刀具中心轨迹在编程轨迹(零件轮廓)前进方向的右边时,称为右刀补,用G42指令实现;反之称为左刀补,用G41指令实现。
1.B刀补特点:刀具中心轨迹段间都是用圆弧连接过渡。
优点:算法简单,实现容易。
缺点:(1)外轮廓加工时,由于圆弧连接时,刀具始终在一点切削,外轮廓尖角被加工成小圆角。
(2)内轮廓加工时,必须由编程人员人为的加一个辅助的过渡圆弧,且必须保证过渡圆弧的半径大于刀具半径。
这样:一是增加编程工作难度;二是稍有疏忽,过渡圆弧半径小于刀具半径时,会因刀具干涉而产生过切,使加工零件报废。
2.C刀补特点:刀具中心轨迹段间采用直线连接过渡。
直接实时自动计算刀具中心轨迹的转接交点。
优点:尖角工艺性好;在加工内轮廓时,可实现过切自动预报。
两种刀补在处理方法上的区别:B刀补采用读一段,算一段,走一段的处理方法。
故无法预计刀具半径造成的下一段轨迹对本段轨迹的影响。
C刀补采用一次对两段并行处理的方法。
先处理本段,再根据下一段来确定刀具中心轨迹的段间过渡状态,从而完成本段刀补运算处理。
(1)由于刀具的磨损或因换刀引起的刀具半径变化时,不必重新编程,只需修改相应的偏置参数即可。
(2)加工余量的预留可通过修改偏置参数实现,而不必为粗、精加工各编制一个程序。
(一)刀具半径补偿的过程刀具半径补偿的过程分三步。
1.刀补建立刀具从起点接近工件,在编程轨迹基础上,刀具中心向左(G41)或向右(G42)偏离一个偏置量的距离。
弧模式中半径补偿
弧模式中半径补偿
弧模式中半径补偿是一种用于调整刀具路径的技术,以确保加工零件的准确性。
半径补偿通常分为刀具半径补偿和刀尖半径补偿两种类型。
刀具半径补偿:
在弧模式中,刀具的实际尺寸可能会与理论尺寸略有偏差,为了弥补这种偏差,刀具半径补偿用于调整刀具轨迹。
刀具半径补偿主要包括刀具半径偏差的正负值,用来指导数控系统计算实际刀具路径。
刀尖半径补偏:
刀尖半径补偏是为了考虑刀具的圆弧切削轮廓,因为实际切削轮廓是由刀尖的轨迹所决定的。
数控车床刀尖圆弧半径补偿课件
02
G41
刀尖圆弧半径左补偿。
03
04
G42
刀尖圆弧半径右补偿。
G43
刀尖圆弧半径补偿取消,同时 补偿值清零。
G40/G41/G42/G43指令的使用方法
1. 补偿的启动与取消
使用G40、G41、G42、G43等指令启动或取消刀尖圆弧半径补偿。
2. 补偿的输入
在补偿启动前,需要输入补偿值(即刀尖圆弧半径),补偿值可以 通过刀补画面输入或手动输入。
补偿方法:刀尖圆弧半径补 偿通过编程指令实现,无需 手动设置
补偿效果:补偿后可提高加 工精度和表面粗糙度Βιβλιοθήκη 刀尖圆弧半径补偿的示例程序三
01
刀尖圆弧半径补偿指令: G41.1、G40
02
补偿过程:通过G41.1指令 对刀尖圆弧半径进行补偿, 补偿过程为刀尖沿圆弧方向 移动,补偿结束后通过G40 指令取消补偿
02
刀尖圆弧半径的大小对切削过程 和工件质量有重要影响。
刀尖圆弧半径补偿的重要性
消除刀尖圆弧对切削轨迹的影响,提 高工件的精度和表面质量。
补偿刀尖圆弧对切削力、切削热和切 削振动的影响,提高切削过程的稳定 性和效率。
刀尖圆弧半径补偿的类型
刀尖圆弧半径左补偿(G41)
01
在切削过程中,刀具左侧的圆弧半径产生影响,需要补偿。
03
补偿方法:刀尖圆弧半径补 偿通过编程指令实现,无需 手动设置
04
补偿效果:补偿后可提高加 工精度和表面粗糙度
05
刀尖圆弧半径补偿的注意事项
刀尖圆弧半径补偿的误差来源
刀具半径测量误差
刀具半径的测量值与实际值之间可能存在误差,导致补偿值不准 确。
刀具磨损
- 1、下载文档前请自行甄别文档内容的完整性,平台不提供额外的编辑、内容补充、找答案等附加服务。
- 2、"仅部分预览"的文档,不可在线预览部分如存在完整性等问题,可反馈申请退款(可完整预览的文档不适用该条件!)。
- 3、如文档侵犯您的权益,请联系客服反馈,我们会尽快为您处理(人工客服工作时间:9:00-18:30)。
注意:起刀程序段不能用于零件加工。
刀尖半径补偿的建立(起刀)
A—B
编程轨迹
A’—B’ 刀尖圆弧中心轨迹
A—C 理想刀尖轨迹
3、刀尖半径补偿的工作过程
3.2 刀尖半径补偿的进行 刀尖圆弧中心轨迹与编程轨迹始终偏离一个刀尖半径的距离
B
A
B‘
C C’ 刀尖半径补偿进行中 D D‘ 刀尖半径补偿的取消
o Z
●
X
四、刀尖半径补偿的参数设置
1、刀尖圆弧的半径值R
2、理想刀尖的方位号
箭头表示刀 尖方向。如 果按刀尖圆 弧中心编程, 则选用0或9
四、刀尖半径补偿的操作
几何形状 偏置号 X 轴 偏置值 Z 轴 偏置值 刀尖圆弧 刀 尖 半径值R 方位号T 0.8 3
G 11
G 12
-290.538
-288.553
编程规律
从右往左加工车外表面时,半径补偿指令用G42;
镗孔时,用G41。
从左往右加工车外表面时42。
二、刀尖半径补偿的编程方法
3、刀尖半径补偿的工作过程 3.1 刀尖半径补偿的建立(起刀) 从G40方式变为G41或G42方式的程序段叫做起刀程序段。
在起刀程序段中执行刀具半径补偿过渡运动。在起刀段的终点
G41
G42
左刀补
右刀补
刀尖圆弧中心沿编程轨迹左侧运动
刀尖圆弧中心沿编程轨迹右侧运动
G40
G41
G42
二、刀尖半径补偿的编程方法
2、工件位置、刀具运动和指令的关系
判别原则:判别刀具运动与工件位置关系用的图
形必须是从虚拟Y轴正向朝坐标原点看得到的图形。
G41
工件 X G42
Z
二、刀尖半径补偿的编程方法
N235 T0202 (切槽刀) N240 G00Z-59.2 N245 X44 N250 G01X25F0.02 N255 X44F0.5 N260 Z-59.8 N265 X15F0.02 N270 X44F0.5 N275 Z-59 N280 X4F0.02 N285 G00X100 N290 Z100 N295 M05 N300 M30 %
实际刀尖加工轨迹
一、刀尖半径补偿的由来
3、刀尖半径补偿的含义
数控系统为了消除刀尖圆弧对加工精度的影响而采用
的一种计算方法,将原来控制理想刀尖的运动轨迹转换成 控制刀尖圆弧中心的运动轨迹。
二、刀尖半径补偿的编程方法
1、与刀尖半径补偿有关的指令
G代码 G40 功能简称 取消补偿 刀具轨迹 理想刀尖沿编程轨迹运动
2、刀尖半径补偿的编程:建立、进行和取消
3、与刀尖半径补偿有关的参数设置
零件加工操作演示
% O4185 N005 G40 G97 G99 N010 M03S1200 N015 T0101 (外圆刀) N020 G00X42.5Z2 N025 G01Z-60F0.2 N030 X48F0.5 N035 G00Z2 N040 X43 N045 G71U2R1 N050 G71P055Q085U0.2W0.2F0.2 N055 G00X22 N060 Z2 N065 G01Z-17.8 N070 X24 N075 X30Z-33 N080 G03X42Z-45R15 N085 G01X43 N090 G00Z100
数控车床的 刀尖半径补偿
一、刀尖半径补偿的由来
1、理想刀尖与实际刀尖 理想刀尖
A
实际刀尖
A
B
一、刀尖半径补偿的由来
2、刀尖圆弧引起的加工误差 ① 未使用刀尖半径补偿加工锥面的情形
A●
●
C
B
D
理想刀尖加工轨迹
实际刀尖加工轨迹
一、刀尖半径补偿的由来
② 未使用刀尖半径补偿加工圆弧的情形
●
●
理想刀尖加工轨迹
N165 M03S600T0202 (切槽刀) N170 G00X100Z-18 N175 X24 N180 G01X18.5F0.02 N185 X26F0.5 N190 G00X100Z100 N195 M03S800T0303 (螺纹刀) N200 G00X24Z5 N205 G76P011060Q60R0.2 N210 G76X19.85Z-16P974Q400F1.5 N215 G00X100 N220 Z100 N225 M00 N230 M03S600
-225.364
-218.416
G 13
G 14 G 15 G 16 G 17 G 18
-293.115
-220.318
五、 刀尖半径补偿引起的过切
直线轮廓加工时的过切
理论轮廓
刀尖圆弧中心轨迹和实际轮廓
五、 刀尖半径补偿引起的过切
内圆弧加工时的过切
理论轮廓
刀尖中心轨迹与实际轮廓
小 结
1、刀尖半径补偿的含义
A‘
刀尖半径补偿的建立
3、刀尖半径补偿的工作过程
3.3 刀具半径补偿的取消 刀具撤离工件,使理想刀尖轨迹的终点与编程轨迹的 终点 重合。它是刀补建立的逆过程。
注意:
同起刀程序段一 样,该程序段也不 能进行零件加工。
A—B 编程轨迹
A’—B’ 刀尖圆弧中心轨迹
C—B 理想刀尖轨迹
二、刀尖半径补偿的编程方法
N095 M03S1500T0101 (外圆刀) N100 G00X13.85Z5 N105 G42G01Z2F0.3 N110 X21.85Z-2F0.05 N115 Z-17 N120 X24 N125 Z-18 N130 X30Z-33 N135 G03X42Z-45R15 N140 G01Z-57 N145 X46F0.3 N150 G40G01X50 N155 G00X100Z100 N160 M00
4、刀尖半径补偿编程注意事项 ◆ G40、G41、G42都是模态的 ◆ 不能在G41方式下再指定G41 ◆ 不能在G42方式下再指定G42
三、编程举例
o Z
X
三、编程举例
N085 M03S1500T0101 (外圆刀) N090 G00X13.9Z5 N095 G42G01Z2F0.3 N100 X21.9Z-2F0.05 N102 Z-17 N105 X24 N106 Z-18 N110 X30Z-33 N115 G03X42Z-45R15 N120 G01Z-57 N125 X46F0.3 N130 G40G01X50 N135 G00X100Z100 N140 M00