进口环氧树脂灌封料工艺流动性改进研究
灌封工艺

一、灌封工艺灌封产品的质量,主要与产品设计、元件选择、组装及所用灌封材料密切相关,灌封工艺也是不容忽视的因素。
环氧灌封有常态和真空两种灌封工艺。
环氧树脂.胺类常温固化灌封料,一般用于低压电器,多采用常态灌封。
环氧树脂.酸酐加热固化灌封料,一般用于高压电子器件灌封,多采用真空灌封工艺,是我们本节研究的重点。
目前常见的有手工真空灌封和机械真空灌封两种方式,而机械真空灌封又可分为A、B组分先混合脱泡后灌封和先分别脱泡后混合灌封两种情况。
其工艺流程如下:(1)手工真空灌封工艺(2)机械真空灌封工艺先混合脱泡后灌封工艺A、B先分别脱泡后混合灌封工艺相比之下,机械真空灌封,设备投资大,维护费用高,但在产品的一致性、可靠性等方面明显优于手工真空灌封工艺。
无论何种灌封方式,都应严格遵守给定的工艺条件,否则很难得到满意的产品。
二、灌封产品常出现的问题及原因分析(1)局部放电起始电压低,线间打火或击穿电视机、显示器行输出变压器,汽车、摩托车点火器等高压电子产品,常因灌封工艺不当,工作时会出现局部放电(电晕)、线间打火或击穿现象,是因为这类产品高压线圈线径很小,一般只有0.02~0.04mm,灌封料未能完全浸透匝间,使线圈匝间存留空隙。
由于空隙介电常数远小于环氧灌封料,在交变高压条件下,会产生不均匀电场,引起界面局部放电,使材料老化分解,引起绝缘破坏。
从工艺角度分析,造成线间空隙有以下两方面原因:1)灌封时真空度不够高,线间空气未能完全排除,使材料无法完全浸渗。
2)灌封前试件预热温度不够,灌人试件物料黏度不能迅速降低,影响浸渗。
对于手工灌封或先混合脱泡后真空灌封工艺,物料混合脱泡温度高、作业时间长或超过物料适用期,以及灌封后产品未及时进入加热固化程序,都会造成物料黏度增大,影响对线圈的浸渗。
据上海常祥实业有限公司的专家介绍,热固化环氧灌封材料复合物,起始温度越高,黏度越小,随时间延长,黏度增长也越迅速。
因此为使物料对线圈有良好的浸渗性,操作上应注意如下几点:1)灌封料复合物应保持在给定的温度范围内,并在适用期内使用完毕。
环氧树脂浇注电流互感器的工艺缺陷及改进

合 为一次 混料 , 在 一 次 混 料 中加 人 固化 剂 为 二次
} 昆料 。一 次 混 料 的 作 用 是 使 填 料 被 树 脂 充 分 浸
润 。 因为 环 氧树脂 与酸 酐 固化剂 的反应 是放 热反 应, 填料 是导 热性好 的材 料 , 它能被 反应 释放 的热
6 1 4
陆为赞 : 环 氧 树 脂 浇 注 电 流 互 感 器 的 工 艺 缺 陷 及 改 进
的局部 放 电( P D) 以及 二 次 开 路 等 。从 本 次 事 故 TA 损坏 的状 况 来 看 , 可以先排除 T A 二 次 侧 开 路 因素 , 因为 损坏 的 T A 二次 铁心 及线 圈完 好 , 无 过 压现 象 。其 次 可 以排 除进 水 受 潮 这 一 因素 , 因 为受损 的 TA 安 装 地 点在 接地 变 室 内 , 进 水 受潮 的可能性 不大 。从 TA 的外绝 缘伤 痕可 以诊 断为 TA 内部 存 在 缺 陷 。分 析 认 为 , 可 能 是 TA 经 过
量 向外传 导 , 使 浇 注物 内应 力 均 匀分 布 。二 次 混
料 时间要 确保 固化 剂 混 合 均 匀 , 其 温 度 和真 空 度 的参 数十 分重 要 。温度 过 高 , 将 使 混 合料 黏 度 迅 速增加 , 影 响脱 气 浇 注 工 序 。真 空度 用 以保 证 混 合料 的脱 气 、 脱水 , 但 不 能 导致 固化剂 的汽 化 , 所
注工艺 , 大致 分为 5大 工艺 : 1 )原材 料 的预 处 理 在 一定 温 度 下 加 热 一 定时间, 经过 真空 处理 脱去 原材料 中吸附 的水分 、 气 体及 低分 子挥 发物 。 2 )混料 混 料 的作 用使 环 氧 树 脂 、 填料 、 固 化剂 等混合 均 匀 , 便 于 化 学 反应 。树脂 与填 料 混
环氧树脂灌封胶技术指导书
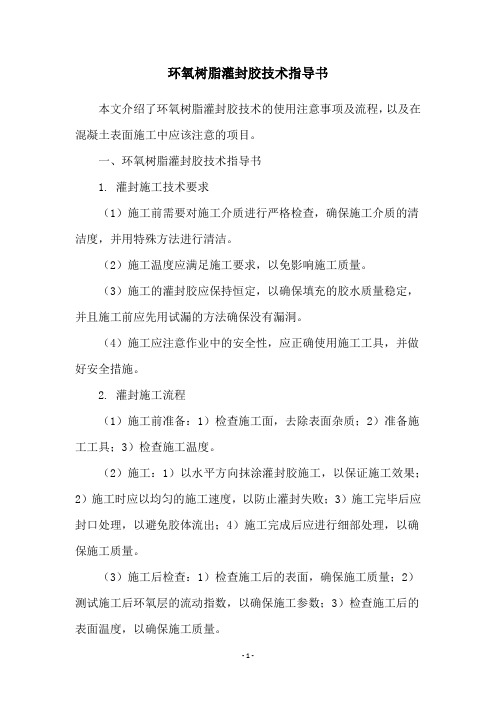
环氧树脂灌封胶技术指导书
本文介绍了环氧树脂灌封胶技术的使用注意事项及流程,以及在混凝土表面施工中应该注意的项目。
一、环氧树脂灌封胶技术指导书
1. 灌封施工技术要求
(1)施工前需要对施工介质进行严格检查,确保施工介质的清洁度,并用特殊方法进行清洁。
(2)施工温度应满足施工要求,以免影响施工质量。
(3)施工的灌封胶应保持恒定,以确保填充的胶水质量稳定,并且施工前应先用试漏的方法确保没有漏洞。
(4)施工应注意作业中的安全性,应正确使用施工工具,并做好安全措施。
2. 灌封施工流程
(1)施工前准备:1)检查施工面,去除表面杂质;2)准备施工工具;3)检查施工温度。
(2)施工:1)以水平方向抹涂灌封胶施工,以保证施工效果;2)施工时应以均匀的施工速度,以防止灌封失败;3)施工完毕后应封口处理,以避免胶体流出;4)施工完成后应进行细部处理,以确保施工质量。
(3)施工后检查:1)检查施工后的表面,确保施工质量;2)测试施工后环氧层的流动指数,以确保施工参数;3)检查施工后的表面温度,以确保施工质量。
三、在混凝土表面施工时应注意的事项
(1)混凝土表面应干燥;
(2)有轻微裂缝的应做好补强;
(3)施工前应作好清洁处理;
(4)使用施工工具时应注意安全卫生;
(5)施工时应控制施工温度;
(6)注意施工方法和施工顺序;
(7)完成后应注意保护,使施工结果有较长时间的保护效果。
单组分环氧结构胶的性能改进与创新研究
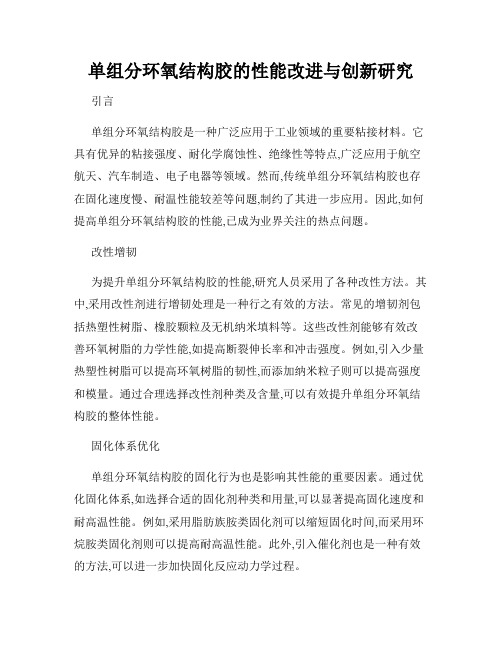
单组分环氧结构胶的性能改进与创新研究引言单组分环氧结构胶是一种广泛应用于工业领域的重要粘接材料。
它具有优异的粘接强度、耐化学腐蚀性、绝缘性等特点,广泛应用于航空航天、汽车制造、电子电器等领域。
然而,传统单组分环氧结构胶也存在固化速度慢、耐温性能较差等问题,制约了其进一步应用。
因此,如何提高单组分环氧结构胶的性能,已成为业界关注的热点问题。
改性增韧为提升单组分环氧结构胶的性能,研究人员采用了各种改性方法。
其中,采用改性剂进行增韧处理是一种行之有效的方法。
常见的增韧剂包括热塑性树脂、橡胶颗粒及无机纳米填料等。
这些改性剂能够有效改善环氧树脂的力学性能,如提高断裂伸长率和冲击强度。
例如,引入少量热塑性树脂可以提高环氧树脂的韧性,而添加纳米粒子则可以提高强度和模量。
通过合理选择改性剂种类及含量,可以有效提升单组分环氧结构胶的整体性能。
固化体系优化单组分环氧结构胶的固化行为也是影响其性能的重要因素。
通过优化固化体系,如选择合适的固化剂种类和用量,可以显著提高固化速度和耐高温性能。
例如,采用脂肪族胺类固化剂可以缩短固化时间,而采用环烷胺类固化剂则可以提高耐高温性能。
此外,引入催化剂也是一种有效的方法,可以进一步加快固化反应动力学过程。
界面改性单组分环氧结构胶的粘接性能很大程度上取决于其与基材之间的界面结合情况。
通过对界面进行改性处理,如引入silane偶联剂或等离子处理,可以显著提高环氧树脂与基材之间的结合力,从而提升整体的粘接强度。
这种界面改性技术不仅适用于金属基材,对于玻璃纤维增强复合材料基材也同样有效。
创新配方设计除了上述常规的改性方法外,研究人员还从配方设计的角度探索了一些创新性的解决方案。
例如,采用双组分环氧树脂体系,通过合理配比两种不同反应活性的环氧单体,可以实现室温下快速固化,大幅提高生产效率。
又如,引入具有特殊官能团的改性单体,可以赋予环氧树脂一些特殊性能,如自愈合能力、导电性等。
通过创新性配方设计,不断拓展单组分环氧结构胶的应用范围。
新型改性水性环氧树脂的制备及性能研究
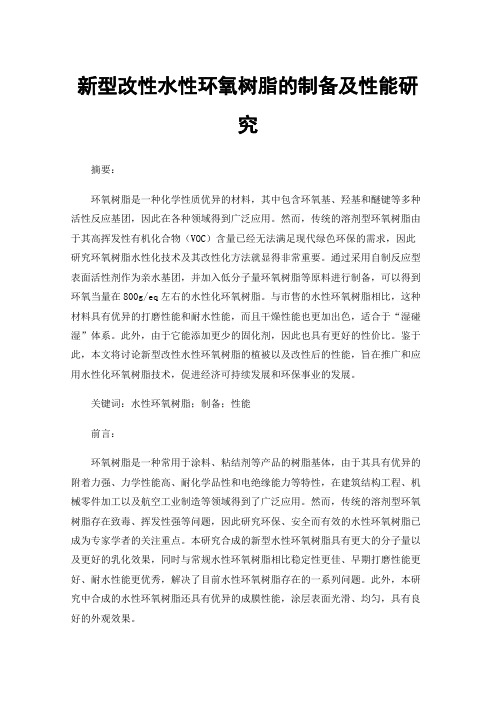
新型改性水性环氧树脂的制备及性能研究摘要:环氧树脂是一种化学性质优异的材料,其中包含环氧基、羟基和醚键等多种活性反应基团,因此在各种领域得到广泛应用。
然而,传统的溶剂型环氧树脂由于其高挥发性有机化合物(VOC)含量已经无法满足现代绿色环保的需求,因此研究环氧树脂水性化技术及其改性化方法就显得非常重要。
通过采用自制反应型表面活性剂作为亲水基团,并加入低分子量环氧树脂等原料进行制备,可以得到环氧当量在800g/eq左右的水性化环氧树脂。
与市售的水性环氧树脂相比,这种材料具有优异的打磨性能和耐水性能,而且干燥性能也更加出色,适合于“湿碰湿”体系。
此外,由于它能添加更少的固化剂,因此也具有更好的性价比。
鉴于此,本文将讨论新型改性水性环氧树脂的植被以及改性后的性能,旨在推广和应用水性化环氧树脂技术,促进经济可持续发展和环保事业的发展。
关键词:水性环氧树脂;制备;性能前言:环氧树脂是一种常用于涂料、粘结剂等产品的树脂基体,由于其具有优异的附着力强、力学性能高、耐化学品性和电绝缘能力等特性,在建筑结构工程、机械零件加工以及航空工业制造等领域得到了广泛应用。
然而,传统的溶剂型环氧树脂存在致毒、挥发性强等问题,因此研究环保、安全而有效的水性环氧树脂已成为专家学者的关注重点。
本研究合成的新型水性环氧树脂具有更大的分子量以及更好的乳化效果,同时与常规水性环氧树脂相比稳定性更佳、早期打磨性能更好、耐水性能更优秀,解决了目前水性环氧树脂存在的一系列问题。
此外,本研究中合成的水性环氧树脂还具有优异的成膜性能,涂层表面光滑、均匀,具有良好的外观效果。
一、水性环氧树脂改性研究进展(一)聚氨酯改性水性环氧树脂聚氨酯具有良好的韧性、耐冲击性和耐腐蚀性等优点,对环氧树脂进行改性可以有效改善其本身的质脆、耐冲击性不足的缺点,提高涂膜的综合性能。
改性方法可以采用物理共混合共聚改性法。
通过将不同粒径的水性聚氨酯与市售水性环氧乳液进行物理共混,当水性聚氨酯粒径为55nm且比例为5%时,可明显增强环氧树脂的韧性,并提高拉伸性能和涂膜的耐冲击性和柔韧性等[1]。
环氧树脂浇注工艺方法之真空浇注工艺

环氧树脂浇注工艺方法之真空浇注工艺(总9页)本页仅作为文档封面,使用时可以删除This document is for reference only-rar21year.March环氧树脂浇注工艺方法之真空浇注工艺时间:2009-10-29来源: 作者:耐磨陶瓷胶真空浇注工艺是目前环氧树脂浇注中应用最为广泛、工艺条件最为成熟的工乙方法。
对于一件环氧树脂浇注的电器绝缘制品,它要求外观完美、尺寸稳定、力学年耍:—电性能合格。
它的这些性能取决于制件本身的设计、模具的质量、浇注用材料的选择、浇注工艺条件的控制等各个方面。
环氧树脂真空浇注的技术要点就是尽可能减少浇注制品中的气隙和气泡。
为了达到这一目的,在原料的预处理、混料、浇注等各个工序都需要控制好真空皮、温度及工序时间。
环氧树脂浇注及浇注材料时间:2009-10-29来源: 作者:耐磨陶瓷胶环氧树脂浇注是将环氧树脂、固化剂和其他配合料浇注到设定的模具内,由热塑性流体交联固化成热卧性制品的过程。
由于环氧树脂浇注产品集优良的电性能和力学性能于一体,因此环氧树脂浇注在电器工业中得到了广泛的应用和决速的发展。
环氧树脂浇注的工艺方法,从不同的工艺条件去理解有不同的区分方法。
从物料进入模具的方式来区分可分为浇注和压注。
浇注指物料自流进入模具。
它又分常压浇注和真空浇注。
压注指物料在外界压力下进入模具,并且为了强制补缩,在物料固化过程中,仍保持着一定的外压,它由过去的简单加压凝胶法发展成现在成熟的自动压力凝胶法。
从物料固化温度来区分可分为常温浇注法和高温浇注法。
选用常温或高温浇注法由浇注材料的本身性质所决定的,其根本区别是浇注材料固化过程中所必需的温度条件。
从物料固化的速度来区分可分为普通固化法和快速固化法。
物料进入模具至拆模所需的时间为初固化时间,普通固化法需几个甚至十几个小时,快速固化法只需十几分钟至几十分钟。
环氧树脂在电子电器领域的应用时间:2009-10-29来源: 作者:耐磨陶瓷胶环氧树脂的介电性能、力学性能、粘接性能、耐腐蚀性能优异,固化收缩率和线胀系数小,尺寸稳定性好,工艺性好,综合性能极佳,更由于环氧材料配方设计的灵活性和多样性,使得能够获得几乎能适应各种专门性能要求的环氧材料,从而使它在电子电器领域得到广泛的应用。
灌封工艺
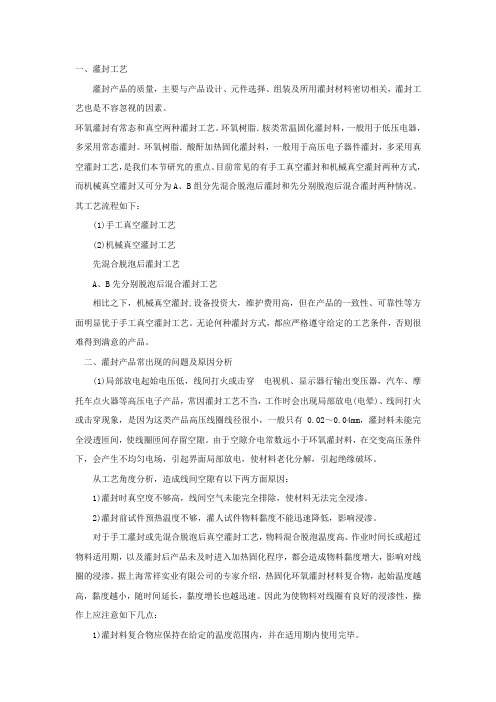
一、灌封工艺灌封产品的质量,主要与产品设计、元件选择、组装及所用灌封材料密切相关,灌封工艺也是不容忽视的因素。
环氧灌封有常态和真空两种灌封工艺。
环氧树脂.胺类常温固化灌封料,一般用于低压电器,多采用常态灌封。
环氧树脂.酸酐加热固化灌封料,一般用于高压电子器件灌封,多采用真空灌封工艺,是我们本节研究的重点。
目前常见的有手工真空灌封和机械真空灌封两种方式,而机械真空灌封又可分为A、B组分先混合脱泡后灌封和先分别脱泡后混合灌封两种情况。
其工艺流程如下:(1)手工真空灌封工艺(2)机械真空灌封工艺先混合脱泡后灌封工艺A、B先分别脱泡后混合灌封工艺相比之下,机械真空灌封,设备投资大,维护费用高,但在产品的一致性、可靠性等方面明显优于手工真空灌封工艺。
无论何种灌封方式,都应严格遵守给定的工艺条件,否则很难得到满意的产品。
二、灌封产品常出现的问题及原因分析(1)局部放电起始电压低,线间打火或击穿电视机、显示器行输出变压器,汽车、摩托车点火器等高压电子产品,常因灌封工艺不当,工作时会出现局部放电(电晕)、线间打火或击穿现象,是因为这类产品高压线圈线径很小,一般只有0.02~0.04mm,灌封料未能完全浸透匝间,使线圈匝间存留空隙。
由于空隙介电常数远小于环氧灌封料,在交变高压条件下,会产生不均匀电场,引起界面局部放电,使材料老化分解,引起绝缘破坏。
从工艺角度分析,造成线间空隙有以下两方面原因:1)灌封时真空度不够高,线间空气未能完全排除,使材料无法完全浸渗。
2)灌封前试件预热温度不够,灌人试件物料黏度不能迅速降低,影响浸渗。
对于手工灌封或先混合脱泡后真空灌封工艺,物料混合脱泡温度高、作业时间长或超过物料适用期,以及灌封后产品未及时进入加热固化程序,都会造成物料黏度增大,影响对线圈的浸渗。
据上海常祥实业有限公司的专家介绍,热固化环氧灌封材料复合物,起始温度越高,黏度越小,随时间延长,黏度增长也越迅速。
因此为使物料对线圈有良好的浸渗性,操作上应注意如下几点:1)灌封料复合物应保持在给定的温度范围内,并在适用期内使用完毕。
环氧树脂胶生产工艺

环氧树脂胶生产工艺
环氧树脂胶的生产工艺通常包括以下步骤:
1. 原料准备:树脂和固化剂是环氧树脂胶的主要原料。
树脂可以选择固体环氧树脂或液体环氧树脂,而固化剂通常是胺类化合物。
在生产过程中,根据配方比例准备好所需量的树脂和固化剂。
2. 树脂配制:将树脂和固化剂按照一定的配方比例混合在一起,通常使用搅拌设备进行彻底混合。
同时,可以添加一些特殊的添加剂或填料,以改善产品的性能。
3. 调节黏度:树脂胶的黏度影响着其流动性和涂覆性能。
在生产过程中,可以使用适当的溶剂或稀释剂来调节树脂胶的黏度,以满足特定的工艺要求。
4. 充注灌装:将调制好的树脂胶充注到适当的容器中,如管状或罐状包装。
此过程通常需要保证充注的量控制准确,并避免空气泡的产生。
5. 固化:将充注好的树脂胶进行固化反应,使其从液体变为固体。
固化反应的时间和温度可能因产品种类而有所不同。
通常在固化过程中会使用加热设备或者环境温度进行控制。
6. 检验和包装:对固化后的树脂胶进行质量检验,确保其符合产品标准和规范。
合格的产品将进行包装,并配备必要的标签和说明书,以便储存和使用。
需要注意的是,不同的树脂胶具有不同的生产工艺和配方要求。
在实际生产中,可能会根据具体情况进行适当的调整和改进。
以上只是一般流程的概述,具体的工艺细节可能因企业和产品种类而有所不同。
- 1、下载文档前请自行甄别文档内容的完整性,平台不提供额外的编辑、内容补充、找答案等附加服务。
- 2、"仅部分预览"的文档,不可在线预览部分如存在完整性等问题,可反馈申请退款(可完整预览的文档不适用该条件!)。
- 3、如文档侵犯您的权益,请联系客服反馈,我们会尽快为您处理(人工客服工作时间:9:00-18:30)。
大 , 出速率变小 , 挤 流动性 变差,因此该批灌封料粘 度大是 导致工艺 流动性差 的主要原因 。 响粘度的 影 因素主要有温度 、 填料 、 稀释剂等。
表 1 基料 粘度 对挤出速率的影响
3.. 8 1活 性 稀 释 剂 31 7
3. 2
填 料
现场 中使用 的 s 很 松散 ,经查 实为 国产 4带
S 2 而工 艺文件中要 求为进 口 s 。s 的增稠作 i , 0
用 明显 , 同品种 的 s 对基 料性 能 的影 响不 同 , 不 i 如 s 对 17 0 胶性 能的影 响见 表 3。从表 3可以看
主要基料 为二缩亚麻 油酸 二缩 水甘 油醚 , 环氧 当量
为 30—40,2 粘 度 为 40—90mP ・。 9 7 5 0 0 as
2 实验部 分
2. 进 口 三 组分 环 氧 树 脂 灌 封 料 配 制 殛 硬 度 测 试 1
3. 温 度 1
按配 比称取 8 8 7 、1 、s 等组分 配制 灌 2 、81 4 0 封料 , 搅匀后在 真空度 67×1 ~1 3 o P 下抽 0 l3 a 2 x 气除去气泡 , 灌封在产品 中, 行有硬度工 序试样 , 随 固化条件 为室 温/ 2 h再 6 4 0±5 / , 照 A T 2 h按 4 SM
维普资讯
・
4 ・ 8
裹 2 温 度对 粘 度 的 彤 响
航 空兵器
mP 5 囊・
2 0 年第 2期 O2
非话性稀 释剂不参 与 固化 反应 ,主要 作用 是增 加胶粘体 系的流 动性 , 长使用期 ,固化后有小 分 延 子残留物 ,降低粘接 性能 。 活性 稀释 剂是含有单 环 氧基 的化 合物 ( 5 1 ,或低粘 度 的环 氧 树脂 ( 如 0) 如 8 1, 7 ) 能同环氧 固化荆 发生 反应 , 为胶粘 剂交 联 成 结构 的组成部 分。单环 氧基化合 物的稀 释效果 比低 粘 度环 氧树脂 的好。
行 了研 究 , 论 了 温度 、填 科 及 活 性 稀 释 剂对 其 粘 度 的影 响 ,通 过 试 验 选 用适 量 国产 51 讨 0
稀释 剂,改善了工艺流动性,顺利 完成了产品的交付任 务。 关键词: 氧树脂 灌封料 环 流动性 粘度 活性稀释剂
1 引
言
D 24 标 准测试邵氏 D硬 度, 20 指标 要求大于或等于
8 . 0S D。
某产品中整流头罩 19 年 以前用进 口 组分环 93 三
2. 环 氧 当 量 测 定 2
氧树 脂灌封料进行灌封 , 9 3 以后用 国产化材料 , 1 年 9 都没有 出现问题。到 1 7 9 8 用 国产化 材料 后 9 、19 年 9 经高 低 温试 验 贮存 一 段 时 间 或交 付 后 出 现裂 纹 , 20 年年初决定改用进 口料 , 资部 门紧急采购 的 00 物 进口料 , 理化 入检环 氧当量和胺 值合格 ,在现场 使 用 中工艺流动性差, 粘度大 , 无法灌封。因产 品急 于 交付 , 重新购料周期长 , 浪费大 , 故对现, 加人适量 国产 5 1 0 稀释 剂, 粘度进行 调整 , 对 改善 工艺流动性 , 使其利 于灌封 ,从而顺利 完成 了 当年多发产 品的交付任务 。 进 口三组分环氧树脂灌封料 是 由环 氧树 脂 88 2、 8 1 胺类 固化剂 10和 s 填料 按 比例 配制而成 。 7、 4
收稿 日期 : 0 1 9 7 20 —0 —1
温度 对基料 粘度 的影 响见表 2 。随着温 度的升 高, 粘度降低。从表 2 以看 出温度 从 1 C 可 9。 升高到 2 , 2 5 88的粘 度降低 很多 , 因此可通过升 高温度降 低粘度 , 如在 5 烘箱 中烘热后或在 热水浴中配料 0 灌封 , 可降低粘度 , 改善流动性 , 但工艺较繁琐 , 不 适用于现场大批量作业 。
灌封 料组分之 一 8 1 7 为低粘 度环 氧树 脂 , 有活 性稀释荆 的作用 。 改变 888 1 可 2 1 的配 比,增大 81 7 7 的 比例 , 降低胶粘体 系的粘度 。 选用极端值 8 11 1 7 1 0 4 S =1 / /( 量 比) i 0 3 6重 00 进行 试验 , 度有 所 改善 , 粘 但效果不理 想。 3 3 2 0 活性稀释剂 . . 5 1 51 0 为单环 氧基化 合物 ,化学 名称 为环 氧丙烷
2 4 粘 度测试 . 环氧树 脂 8 8 8 1 2 、 7 及胺类 固化剂 1 ( 4 动力 ) 0 粘 度的测试采用旋转 粘度计 进行 测试。
3 结果与讨论
现场中灌 封料 流动 性 差,主 要原 因是 粘度 大。 粘度与挤出速 率 的关 系见表 1 。随着基料 粘 度的增
醚, 类同国产 E一5 及 68环氧树 脂 ,环氧 当量 为 1 1
由资料得知… : 8的主要基料为双酚 A二缩 水甘油 8 2
环 氧树 脂 88 8 1 5 1 2 、 7 及 0 稀释剂环 氧当量 的测
定按 照 P —C A一 5 s C 1 进行
2. 胺值 的 测 定 3
胺类 固化剂 1 4 0胺值 的测定 按照 P —C A一1 S C 6
进行 。
维普资讯
航 空兵器
2 0 年第 2期 02
・技术笔记 ・
4 ・ 7
进 口环 氧 树 脂 灌 封 料 工 艺 流 动 性 改进 研 究
苗蓉丽 殷胜昔 朱 锋 李新云
( 中国空空导弹研 究院
洛用, 7 09 4 10 )
摘
要: 对慕产品用进 1 三组分 环氧树脂 灌封科 8 8 7 1 0工艺流动性 的改善进 2 " 2 1 11 8 4