探伤报告
焊接探伤报告

焊接探伤报告
报告编号:WSR20210802
受检单位:XXX公司
焊接方式:手工电弧焊
探伤工艺:超声波探伤
检验标准:GB/T 13298-2013
检验时间:2021年8月2日
检验人员:XXX
1. 检验目的
本次检验旨在了解焊缝内部缺陷情况,保证焊接质量,确保设备的安全运行和生产顺利进行。
2. 检验结果
经过超声波探伤,共检测焊缝数量13个,其中11个焊缝未发现任何缺陷,符合GB/T 13298-2013标准要求。
2个焊缝出现错误信号,经过重复检查,确认为焊接过程中气孔引起的误测,不存在缺陷。
3. 检验结论
本次焊接探伤合格,其中13个焊缝中11个符合GB/T 13298-2013标准要求,2个焊缝的误测已经排除,设备焊接质量符合生产要求。
4. 后续建议
针对2个焊缝误测问题,建议焊接人员加强焊接工艺控制,注意气孔等缺陷的控制,确保未来焊接质量能够更加稳定可靠。
5. 报告附图
(见下图)
(备注:此报告所有信息仅供参考,如有疑问,请和相应的检测机构联系)。
焊缝探伤报告
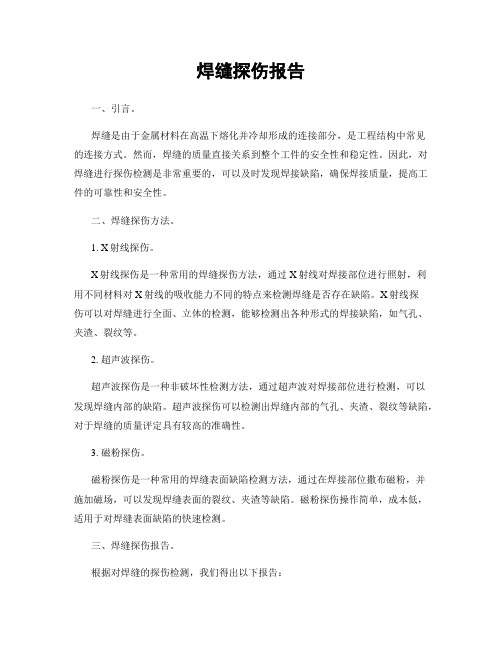
焊缝探伤报告一、引言。
焊缝是由于金属材料在高温下熔化并冷却形成的连接部分,是工程结构中常见的连接方式。
然而,焊缝的质量直接关系到整个工件的安全性和稳定性。
因此,对焊缝进行探伤检测是非常重要的,可以及时发现焊接缺陷,确保焊接质量,提高工件的可靠性和安全性。
二、焊缝探伤方法。
1. X射线探伤。
X射线探伤是一种常用的焊缝探伤方法,通过X射线对焊接部位进行照射,利用不同材料对X射线的吸收能力不同的特点来检测焊缝是否存在缺陷。
X射线探伤可以对焊缝进行全面、立体的检测,能够检测出各种形式的焊接缺陷,如气孔、夹渣、裂纹等。
2. 超声波探伤。
超声波探伤是一种非破坏性检测方法,通过超声波对焊接部位进行检测,可以发现焊缝内部的缺陷。
超声波探伤可以检测出焊缝内部的气孔、夹渣、裂纹等缺陷,对于焊缝的质量评定具有较高的准确性。
3. 磁粉探伤。
磁粉探伤是一种常用的焊缝表面缺陷检测方法,通过在焊接部位撒布磁粉,并施加磁场,可以发现焊缝表面的裂纹、夹渣等缺陷。
磁粉探伤操作简单,成本低,适用于对焊缝表面缺陷的快速检测。
三、焊缝探伤报告。
根据对焊缝的探伤检测,我们得出以下报告:1. 焊缝内部存在气孔和夹渣,对焊接质量造成一定影响,需重新进行焊接处理。
2. 焊缝表面存在裂纹,需要进行修补处理,确保焊缝的完整性和稳定性。
3. 焊缝连接部位存在局部变形,需要重新进行焊接处理,确保焊接部位的稳固性。
四、结论。
焊缝探伤是确保焊接质量的重要手段,通过对焊缝的全面检测,可以及时发现焊接缺陷,保证焊接质量,提高工件的可靠性和安全性。
在进行焊接工艺时,需要严格按照工艺要求进行操作,确保焊接质量,减少焊接缺陷的产生。
五、致谢。
感谢对本次焊缝探伤工作给予支持和帮助的各位专家和同事,在他们的指导和帮助下,我们完成了本次焊缝探伤工作,并得出了相应的报告。
六、参考文献。
[1] 焊接工程手册。
[2] 焊接质量检测技术。
[3] 焊接工艺规程。
以上就是本次焊缝探伤报告的全部内容,希望能对大家有所帮助。
金属探伤实验报告

一、实验目的1. 熟悉金属探伤的基本原理和方法;2. 掌握超声波探伤的操作技能;3. 了解金属探伤在工程中的应用。
二、实验原理金属探伤是利用超声波在金属中传播时,遇到缺陷时会发生反射、折射、散射等现象,通过检测这些现象来发现金属内部的缺陷。
超声波探伤具有无损、高效、可靠等优点,是金属探伤的主要方法。
三、实验设备与材料1. 超声波探伤仪;2. 标准试块;3. 被检金属工件;4. 记录本、笔。
四、实验步骤1. 超声波探伤仪的校准(1)将探伤仪接通电源,预热10分钟;(2)根据试块材质选择合适的探头,调整探头频率;(3)将探头放置在试块上,调整探头位置,使超声波垂直于试块表面;(4)调节增益,使信号清晰可辨。
2. 超声波探伤操作(1)将被检金属工件放置在试验台上,确保工件表面平整;(2)将探头放置在工件表面,沿工件长度方向移动,进行连续扫查;(3)观察显示屏,记录超声波信号的变化,分析缺陷位置、形状、大小等信息;(4)对发现缺陷的部位进行重点检测,确认缺陷类型。
3. 数据记录与分析(1)记录探伤过程中发现的所有缺陷,包括位置、形状、大小等信息;(2)分析缺陷产生的原因,如材料缺陷、加工缺陷、热处理缺陷等;(3)根据缺陷情况,评估工件质量,提出改进措施。
五、实验结果与分析1. 实验结果通过超声波探伤,发现被检金属工件存在以下缺陷:(1)长度为10mm的裂纹,位于工件表面;(2)直径为5mm的孔洞,位于工件内部;(3)长度为20mm的划痕,位于工件表面。
2. 结果分析(1)裂纹产生的原因可能是工件在加工过程中受到外力作用,导致材料产生应力集中;(2)孔洞可能是由于加工过程中工具磨损或操作失误造成的;(3)划痕可能是由于工件在运输或安装过程中受到碰撞造成的。
针对以上缺陷,提出以下改进措施:(1)加强工件加工过程中的质量控制,避免应力集中;(2)定期检查加工工具,确保其锋利度;(3)在运输和安装过程中,采取保护措施,避免工件受到碰撞。
探伤检查统计报告模板

探伤检查统计报告模板1. 引言本报告旨在对某公司某期间内进行的探伤检查进行统计分析,以便帮助公司了解设备的健康状况和探伤检查的效果。
通过本次统计分析报告,公司将能够做出合理的决策,以提高设备的可靠性和安全性。
2. 数据统计2.1 检查时间和频率本次统计分析报告涵盖了某期间内的探伤检查情况。
探伤检查时间总共为X天,每天进行Y次探伤检查,共进行了Z次探伤检查。
2.2 受检设备和部位本次探伤检查涵盖了公司目前所拥有的设备,并对设备的关键部位进行了检测。
共检查了A个设备和B个部位。
2.3 检测结果根据探伤检查的结果,统计了正常和异常情况的次数。
- 正常检测结果次数:N次- 异常检测结果次数:M次3. 异常情况分析3.1 异常类型根据异常检测结果的分类,对不同类型的异常进行了统计。
具体异常类型如下:- 异常类型1:X次- 异常类型2:Y次- 异常类型3:Z次3.2 异常发现频率根据异常检测结果的时间分布,统计了不同时段异常检测结果的分布。
具体异常发现频率如下:- 早晨(6:00-9:00):A次- 上午(9:00-12:00):B次- 下午(12:00-18:00):C次- 晚上(18:00-21:00):D次- 夜间(21:00-6:00):E次3.3 异常部位分布根据异常检测结果所涉及的部位,统计了不同部位的异常分布。
具体异常部位分布如下:待填入数据表格4. 建议和改进措施根据以上统计结果,结合公司的实际情况,我们向公司提出以下建议和改进措施,以进一步提升设备的可靠性和安全性:1. 建议加强对异常部位的监测和维护,特别是X部位和Y部位。
可以增加探伤检查的频率或采用更先进的检测技术。
2. 建议提高探伤检查的准确性和可靠性,可以考虑引入更高精度的设备或邀请专业技术人员进行培训。
3. 建议对异常类型1进行深入研究,并制定相应的预防措施,以避免类似异常再次发生。
5. 结论通过本次探伤检查统计分析报告,我们对公司设备的健康状况和探伤检查效果进行了全面的分析。
超声波探伤报告格式
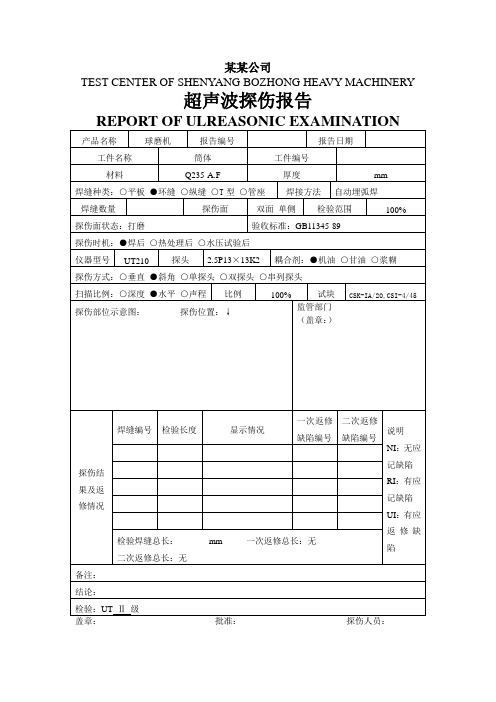
试块
CSK-IA/20,CSI-4/45
探伤部位示意图:探伤位置:↓
监管部门
(盖章:)
探伤结果及返修情况
焊缝编号
检验长度
显示情况
一次返修缺陷编号
二次返修缺陷编号
说明
NI:无应记缺陷
RI:有应记缺陷
UI:有应返修缺陷
检验焊缝总长:mm
一次返修总长:无
二次返修总长:无
备注:
结论:
检验:UTⅡ级
盖章:批准:探伤人员:
自动埋弧焊
焊缝数量
探伤面
双面单侧
检验范围
100%
探伤面状态:打磨
验收标准:GB11345-89
探伤时机:●焊后 ○热处理后 ○水压试验后
仪器型号
UT21剂:●机油 ○甘油 ○浆糊
探伤方式:○垂直 ●斜角 ○单探头 ○双探头 ○串列探头
扫描比例:○深度●水平 ○声程
比例
某某公司
TESTCENTEROFSHENYANGBOZHONG HEAVY MACHINERY
超声波探伤报告
REPORT OF ULREASONIC EXAMINATION
产品名称
球磨机
报告编号
报告日期
工件名称
筒体
工件编号
材料
Q235-A.F
厚度
mm
焊缝种类:○平板●环缝 ○纵缝 ○T型 ○管座
焊接方法
超生波探伤实验报告(3篇)

第1篇一、实验目的1. 理解超声波探伤的基本原理和操作流程。
2. 掌握超声波探伤仪器的使用方法和操作技巧。
3. 通过实际操作,了解超声波探伤在检测金属缺陷中的应用。
4. 分析超声波探伤结果的准确性和可靠性。
二、实验背景超声波探伤是一种利用超声波在材料中传播的特性,对材料内部缺陷进行检测的技术。
由于超声波具有穿透能力强、方向性好、无损检测等优点,因此在工业、军事、医学等领域得到广泛应用。
三、实验原理超声波探伤的基本原理是利用超声波在材料中传播时,遇到缺陷会发生反射、折射、散射等现象。
通过分析反射波的特征,可以判断材料内部的缺陷位置、大小和性质。
四、实验器材1. 超声波探伤仪:用于发射和接收超声波信号。
2. 探头:用于发射和接收超声波。
3. 试块:用于模拟实际材料的缺陷。
4. 耦合剂:用于改善探头与试块之间的耦合效果。
5. 记录仪:用于记录实验数据。
五、实验步骤1. 将探头安装到超声波探伤仪上,调整探头频率和探头间距。
2. 将耦合剂均匀涂抹在试块表面,确保探头与试块之间良好耦合。
3. 将探头放置在试块表面,开始发射超声波。
4. 分析接收到的超声波信号,判断材料内部的缺陷。
5. 记录实验数据,包括缺陷位置、大小和性质。
六、实验结果与分析1. 通过实验,成功检测到试块内部的缺陷,包括裂纹、气孔等。
2. 分析缺陷反射波的特征,可以判断缺陷的位置、大小和性质。
3. 实验结果表明,超声波探伤具有较高的检测准确性和可靠性。
七、实验总结1. 超声波探伤是一种有效的无损检测技术,可以用于检测金属材料内部的缺陷。
2. 掌握超声波探伤仪器的使用方法和操作技巧,可以提高检测准确性和可靠性。
3. 实验结果表明,超声波探伤在检测金属缺陷方面具有较高的应用价值。
八、实验建议1. 在实际应用中,应根据被检测材料的特性选择合适的探头频率和探头间距。
2. 注意耦合剂的选择和涂抹,确保探头与试块之间良好耦合。
3. 分析反射波特征时,应注意缺陷定位、大小和性质的判断。
焊缝射线探伤报告
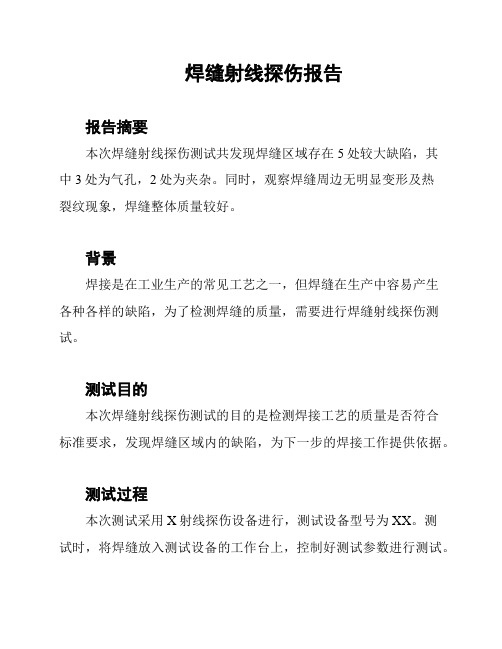
焊缝射线探伤报告
报告摘要
本次焊缝射线探伤测试共发现焊缝区域存在5处较大缺陷,其
中3处为气孔,2处为夹杂。
同时,观察焊缝周边无明显变形及热
裂纹现象,焊缝整体质量较好。
背景
焊接是在工业生产的常见工艺之一,但焊缝在生产中容易产生
各种各样的缺陷,为了检测焊缝的质量,需要进行焊缝射线探伤测试。
测试目的
本次焊缝射线探伤测试的目的是检测焊接工艺的质量是否符合
标准要求,发现焊缝区域内的缺陷,为下一步的焊接工作提供依据。
测试过程
本次测试采用X射线探伤设备进行,测试设备型号为XX。
测
试时,将焊缝放入测试设备的工作台上,控制好测试参数进行测试。
测试结果
测试结果显示,焊缝区域存在5处较大缺陷,其中3处为气孔,2处为夹杂。
具体信息如下表所示:
结论
通过本次测试发现,焊缝存在5处较大缺陷,需要在下一步的
焊接工作中予以处理。
整体来看,焊缝的质量较好,焊缝周边无明
显变形及热裂纹现象。
射线探伤报告带内容
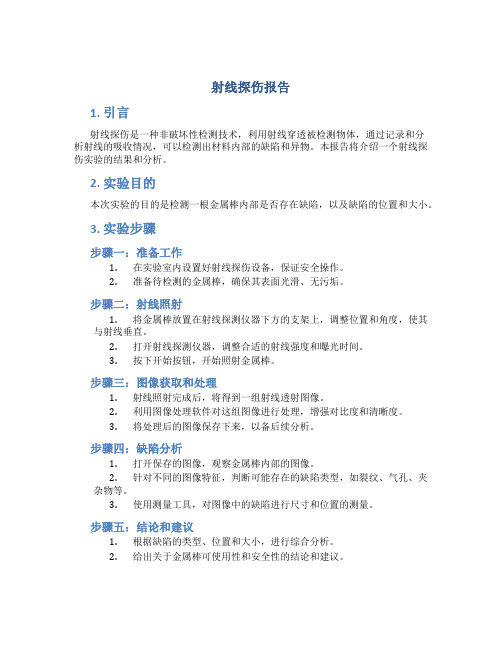
射线探伤报告1. 引言射线探伤是一种非破坏性检测技术,利用射线穿透被检测物体,通过记录和分析射线的吸收情况,可以检测出材料内部的缺陷和异物。
本报告将介绍一个射线探伤实验的结果和分析。
2. 实验目的本次实验的目的是检测一根金属棒内部是否存在缺陷,以及缺陷的位置和大小。
3. 实验步骤步骤一:准备工作1.在实验室内设置好射线探伤设备,保证安全操作。
2.准备待检测的金属棒,确保其表面光滑、无污垢。
步骤二:射线照射1.将金属棒放置在射线探测仪器下方的支架上,调整位置和角度,使其与射线垂直。
2.打开射线探测仪器,调整合适的射线强度和曝光时间。
3.按下开始按钮,开始照射金属棒。
步骤三:图像获取和处理1.射线照射完成后,将得到一组射线透射图像。
2.利用图像处理软件对这组图像进行处理,增强对比度和清晰度。
3.将处理后的图像保存下来,以备后续分析。
步骤四:缺陷分析1.打开保存的图像,观察金属棒内部的图像。
2.针对不同的图像特征,判断可能存在的缺陷类型,如裂纹、气孔、夹杂物等。
3.使用测量工具,对图像中的缺陷进行尺寸和位置的测量。
步骤五:结论和建议1.根据缺陷的类型、位置和大小,进行综合分析。
2.给出关于金属棒可使用性和安全性的结论和建议。
4. 结果与讨论通过对射线探测图像的分析,我们发现金属棒内部存在一个长度约为5cm的裂纹。
裂纹位于金属棒的中间位置,对金属棒的强度和可靠性造成一定的影响。
建议在使用该金属棒前进行修复或更换。
5. 结束语射线探伤技术是一种重要的非破坏性检测手段,可以帮助我们发现材料内部的缺陷和异物。
本次实验展示了如何进行射线探伤实验,并对实验结果进行分析和结论。
希望通过这次实验的介绍,读者对射线探伤技术有更深入的了解。
- 1、下载文档前请自行甄别文档内容的完整性,平台不提供额外的编辑、内容补充、找答案等附加服务。
- 2、"仅部分预览"的文档,不可在线预览部分如存在完整性等问题,可反馈申请退款(可完整预览的文档不适用该条件!)。
- 3、如文档侵犯您的权益,请联系客服反馈,我们会尽快为您处理(人工客服工作时间:9:00-18:30)。
未见
Ⅰ
29
未见
Ⅰ
30
未见
Ⅰ
报告编号:2016-11022第1页
焊缝射线检测报告
委托单位:报告编号:2016-11023
工
件
产品名称
弯头组合件
材料牌号
产品编号
E4
规格型号
Φ168
产品数量
1件
壁厚
8mm
检
测
条
件
及
工
艺
参
数
源种类
■X Ir192Co60
设备型号
XXH3005
焦点尺寸
1.0×2.4 mm
未见
Ⅰ
7
条缺L=4
Ⅱ
8
未见
Ⅰ
9
未见
Ⅰ
10
未见
Ⅰ
11
未见
Ⅰ
12
圆缺3点
Ⅱ
13
未见
Ⅰ
14
未见
Ⅰ
15
未见
Ⅰ
16
未见
Ⅰ
17
未见
Ⅰ
18
圆缺2点
Ⅱ
19
未见
Ⅰ
20
未见
Ⅰ
报告编号:2016-11023第1页
检测结果
产品焊缝质量符合NB/T47013.2-2015标准的Ⅱ级要求,结果合格。
检测人(资格Ⅱ):
报告人(资格Ⅱ):
审核人(资格Ⅱ):
无损检测专用章
射线探伤底片评定表
工件
编号
底片
序号
缺陷的性质及当量
评定
级别
工件
编号
底片
序号
缺陷的性质及当量
评定
级别
E4
1
未见
Ⅰቤተ መጻሕፍቲ ባይዱ
2
未见
Ⅰ
3
未见
Ⅰ
4
条缺L=3
Ⅱ
5
未见
Ⅰ
6
检测人(资格Ⅱ):
曾阳
2016年11月18日
报告人(资格Ⅱ):
郝伟龙
2016年11月18日
审核人(资格Ⅱ):
无损检测专用章
射线探伤底片评定表
工件
编号
底片
序号
缺陷的性质及当量
评定
级别
工件
编号
底片
序号
缺陷的性质及当量
评定
级别
T1
1
未见
Ⅰ
T2
1
未见
Ⅰ
2
未见
Ⅰ
2
未见
Ⅰ
3
未见
Ⅰ
3
未见
Ⅰ
4
未见
Ⅰ
4
圆缺1点
Ⅰ
5
未见
合格级别(级)
Ⅱ
要求检测比例%
100
实际检测比例%
100
检测标准
NB/T47013.2-2015
合格片数
纵向焊缝
(张)
环向焊缝
(张)
相交焊缝接头(张)
共计
(张)
最终
评定结果
Ⅰ级
(张)
Ⅱ级
(张)
Ⅲ级
(张)
16
60
76
缺陷及返修情况说明
检测结果
产品焊缝质量符合NB/T47013.2-2015标准的Ⅱ级要求,结果合格。
胶片牌号
AGFA
增感方式
Pb前屏0.03 mm;后屏0.1mm
胶片规格
80×300 mm
像质计型号
10-16
冲洗条件
自动■手工
显影液配方
韵达配方
显影条件
时间4-6min;温度22℃
质量等级
■AB B
底片黑度D
2.0-4.0
焊缝编号
布片图
透照方式
双壁单影
E4底片序号(1-20)
L1(焦距)mm
500
能量kV
像质计型号
10-16
冲洗条件
自动■手工
显影液配方
韵达配方
显影条件
时间4-6min;温度22℃
质量等级
■AB B
底片黑度D
2.0-4.0
焊缝编号
布片图
透照方式
双壁单影
T1T2底片序号(1-38)
L1(焦距)mm
500
能量kV
180
管电流(mA)
5
曝光时间min
3
识别丝号
12
焊缝长度mm
L3 mm
220
焊缝射线检测报告
委托单位:报告编号:
工
件
产品名称
三通组合件
材料牌号
产品编号
T1 T2
规格型号
Φ325*325
产品数量
2件
壁厚
8mm
检
测
条
件
及
工
艺
参
数
源种类
■X Ir192Co60
设备型号
XXH3005
焦点尺寸
1.0×2.4 mm
胶片牌号
AGFA
增感方式
Pb前屏0.03 mm;后屏0.1mm
胶片规格
80×300 mm
评定
级别
E3
1
未见
Ⅰ
2
未见
Ⅰ
3
未见
Ⅰ
4
圆缺1点
Ⅰ
5
未见
Ⅰ
6
未见
Ⅰ
7
条缺L=4
Ⅱ
8
未见
Ⅰ
9
未见
Ⅰ
10
未见
Ⅰ
11
未见
Ⅰ
12
未见
Ⅰ
13
圆缺2点
Ⅰ
14
未见
Ⅰ
15
未见
Ⅰ
16
圆缺3点
Ⅱ
17
未见
Ⅰ
18
未见
Ⅰ
19
条缺L=3
Ⅱ
20
未见
Ⅰ
21
未见
Ⅰ
22
圆缺1点
Ⅰ
23
未见
Ⅰ
24
未见
Ⅰ
25
圆缺1点
Ⅰ
26
未见
Ⅰ
27
圆缺1点
Ⅰ
180
管电流(mA)
5
曝光时间min
3
识别丝号
12
焊缝长度mm
L3 mm
220
合格级别(级)
Ⅱ
要求检测比例%
100
实际检测比例%
100
检测标准
NB/T47013.2-2015
合格片数
纵向焊缝
(张)
环向焊缝
(张)
相交焊缝接头(张)
共计
(张)
最终
评定结果
Ⅰ级
(张)
Ⅱ级
(张)
Ⅲ级
(张)
20
20
缺陷及返修情况说明
设备型号
XXH3005
焦点尺寸
1.0×2.4 mm
胶片牌号
AGFA
增感方式
Pb前屏0.03 mm;后屏0.1mm
胶片规格
80×300 mm
像质计型号
10-16
冲洗条件
自动■手工
显影液配方
韵达配方
显影条件
时间4-6min;温度22℃
质量等级
■AB B
底片黑度D
2.0-4.0
焊缝编号
布片图
透照方式
双壁单影
Ⅰ
20
未见
Ⅰ
20
圆缺1点
Ⅰ
21
未见
Ⅰ
21
未见
Ⅰ
22
圆缺2点
Ⅱ
22
未见
Ⅰ
23
未见
Ⅰ
23
未见
Ⅰ
24
未见
Ⅰ
24
未见
Ⅰ
25
未见
Ⅰ
25
圆缺3点
Ⅱ
26
未见
Ⅰ
26
未见
Ⅰ
27
未见
Ⅰ
27
未见
Ⅰ
28
未见
Ⅰ
28
未见
Ⅰ
29
圆缺1点
Ⅰ
29
未见
Ⅰ
30
未见
Ⅰ
30
条缺L=4
Ⅱ
31
未见
Ⅰ
31
未见
Ⅰ
32
未见
Ⅰ
32
未见
Ⅰ
33
未见
Ⅰ
33
未见
Ⅰ级
(张)
Ⅱ级
(张)
Ⅲ级
(张)
10
20
30
缺陷及返修情况说明
检测结果
产品焊缝质量符合NB/T47013.2-2015标准的Ⅱ级要求,结果合格。
检测人(资格Ⅱ):
报告人(资格Ⅱ):
审核人(资格Ⅱ):
无损检测专用章
射线探伤底片评定表
工件
编号
底片
序号
缺陷的性质及当量
评定
级别
工件
编号
底片
序号
缺陷的性质及当量
Ⅰ
34
条缺L=4
Ⅱ
34
未见
Ⅰ
35
未见
Ⅰ
35
未见
Ⅰ
36
未见
Ⅰ
36
圆缺1点
Ⅰ
37
未见
Ⅰ
37
未见
Ⅰ
38
未见
Ⅰ
38
未见
Ⅰ
报告编号:第1页
焊缝射线检测报告
委托单位:报告编号:2016-11022