铸钢件的制作方案
铸钢件生产工艺流程 PPT

一.铸钢件生产工艺流程图
二.前道生产各工艺 1.造型和制芯 (1)任务(内容) 制备形成铸件的模型。 (2)重要性(地位)是砂型铸造生产的主要或者说是基本工序,往往以
该道工序来衡量/计算铸造生产能力、劳动生产率(效率)、生产技术 的先进性。 (3)支持配合的工序 A.模型 模型对铸件的尺寸精度起决定性的影响; 模型直接影响着整个铸造厂的操作方法,生产效率; 模型的生产管理; 有关模型的技术标准; 可以说模型影响着整个铸造厂(车间)的生产。
65%以上,锆英粉的特点是耐火度高,化学稳定性好,高温下热膨胀系
数小,能有效地防粘砂、冲砂、夹砂等缺陷,涂料中有一些挥发物,高
温下有较大的发气量,会带来铸件的皮下气孔,因此刷涂料后要烘干,
过高的烘烤温度有损于醇基涂料中的粘结剂,削弱了涂料层,要避免
(一般控制在200°C以下)。涂料中有一定量的醇类物质,在使用过程
-4-
2.烘烤和上涂料
(1)任务(目的) 对制备好的砂型和砂芯烘烤,上涂料,防止铸件出现气 孔,防止粘砂、冲刷,提高铸件表面光洁度。
(2)重要性 对提高铸件表面光洁度,防止粘砂、冲砂,防止气孔起很大 的甚至是决定性的作用。
(3)涂料 我公司用锆英粉醇基涂料,涂料的基本组成(骨料)是锆英粉,
化学结构式是ZrO2·SiO2, ZrO2含量越高越好,铸钢生产要求含ZrO2
中因醇类物质的挥发涂料变粘度,影响涂刷,用工业无水酒精稀释。刷
涂料时要避免涂料堆集,影响铸件尺寸,过厚的涂料层不易烘干,会造
成铸件气孔。
-5-
3.合箱(配模) (1)任务(内容)将制备好的砂型和砂芯装配起来,准备浇注。有时要放内
冷铁和芯撑。 (2)重要性 是制备铸件模型的最后一道工序,决定铸件尺寸,形状,铸件
制造铸钢件的工艺流程

制造铸钢件的工艺流程
铸钢的机械性能比铸铁高,但其铸造性能却比铸铁差。
因为铸钢的熔点较高,钢液易氧化、钢水的流动性差、收缩大,其体收缩率为10~14%,线收缩为 1.8~2.5%。
为防止铸钢件产生浇不足、冷隔、缩孔和缩松、裂纹及粘砂等缺陷,必须采取比铸铁复杂的工艺措施:
1、由于钢液的流动性差,为防止铸钢件产生冷隔和浇不足,铸钢件的壁厚不能小于8mm;浇注系统的结构力求简单、且截面尺寸比铸铁的大;采用干铸型或热铸型;适当提高浇注温度,一般为1520°~1600℃,因为浇注温度高,钢水的过热度大、保持液态的时间长,流动性可得到改善。
但是浇温过高,会引起晶粒粗大、热裂、气孔和粘砂等缺陷。
因此一般小型、薄壁及形状复杂的铸件,其浇注温度约为钢的熔点温度+150℃;大型、厚壁铸件的浇注温度比其熔点高出100℃左右。
2、由于铸钢的收缩大大超过铸铁,为防止铸件出现缩孔、缩松缺陷,在铸造工艺上大都采用冒口和、冷铁和补贴等措施,以实现顺序凝固。
此外,为防止铸钢件产生缩孔、缩松、气孔和裂纹缺陷,应使其壁厚均匀、避免尖角和直角结构、在铸型用型砂中加锯末、在型芯中加焦炭、以及采用空心型芯和油砂芯等来改善砂型或型芯的退让性和透气性。
铸钢件生产工艺流程
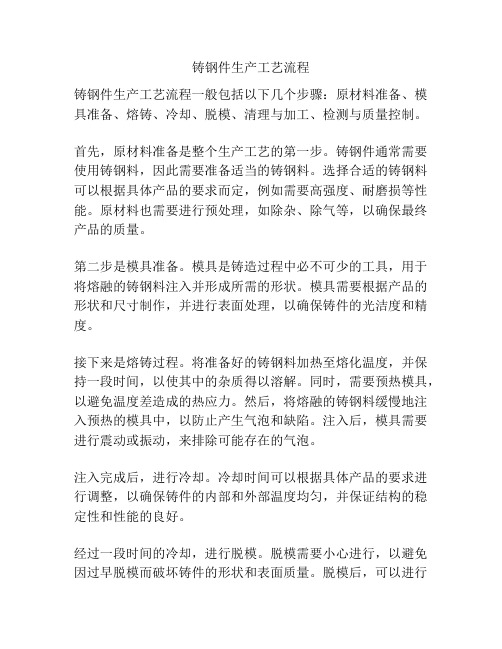
铸钢件生产工艺流程铸钢件生产工艺流程一般包括以下几个步骤:原材料准备、模具准备、熔铸、冷却、脱模、清理与加工、检测与质量控制。
首先,原材料准备是整个生产工艺的第一步。
铸钢件通常需要使用铸钢料,因此需要准备适当的铸钢料。
选择合适的铸钢料可以根据具体产品的要求而定,例如需要高强度、耐磨损等性能。
原材料也需要进行预处理,如除杂、除气等,以确保最终产品的质量。
第二步是模具准备。
模具是铸造过程中必不可少的工具,用于将熔融的铸钢料注入并形成所需的形状。
模具需要根据产品的形状和尺寸制作,并进行表面处理,以确保铸件的光洁度和精度。
接下来是熔铸过程。
将准备好的铸钢料加热至熔化温度,并保持一段时间,以使其中的杂质得以溶解。
同时,需要预热模具,以避免温度差造成的热应力。
然后,将熔融的铸钢料缓慢地注入预热的模具中,以防止产生气泡和缺陷。
注入后,模具需要进行震动或振动,来排除可能存在的气泡。
注入完成后,进行冷却。
冷却时间可以根据具体产品的要求进行调整,以确保铸件的内部和外部温度均匀,并保证结构的稳定性和性能的良好。
经过一段时间的冷却,进行脱模。
脱模需要小心进行,以避免因过早脱模而破坏铸件的形状和表面质量。
脱模后,可以进行初步的修整和清理工作,以去除可能存在的毛刺和其他缺陷。
清理与加工是下一个步骤。
铸钢件通常需要经过进一步的清理和加工,以达到最终的形状和精度要求。
清理可以包括砂芯的去除、毛刺的修剪等。
加工可以包括切割、修整、钻孔、磨削等,以满足产品的尺寸和形状要求。
最后是检测与质量控制。
铸钢件需要经过一系列的检测和测试,以确保其质量符合规定的技术要求和技术标准。
常用的检测方法包括尺寸测量、硬度测试、金相组织观察、力学性能测试等。
根据检测结果,可以对铸钢件进行分类和修整,以达到产品质量的要求。
综上所述,铸钢件生产工艺流程涵盖了原材料准备、模具准备、熔铸、冷却、脱模、清理与加工、检测与质量控制等多个步骤。
这些步骤有机地配合,确保了铸钢件的质量和性能。
铸钢件生产工艺流程
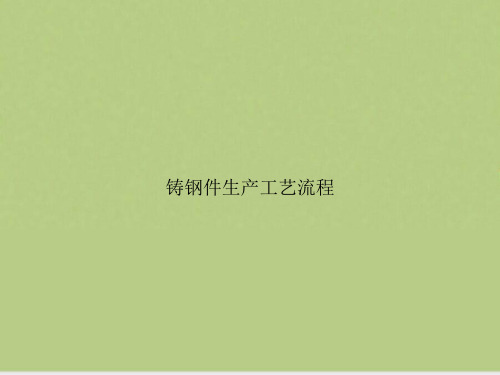
件的形状和尺寸。
※(型1)砂(任对务生2产打)成开重本浇的注要影后响的性很铸(大型,,地有取些出位砂铸种)件占,是成打本碎砂的已比型浇例注铸很后大的造。铸生型,产取出的铸主件。要或者说是基本工序,往往以 ((14) )任设务备该:去热除道处热理工处炉理序,时冷生来却成水衡的池氧量。化皮/计算铸造生产能力、劳动生产率(效率)、生产技术
-8-
三. 后道工序 1.开箱落砂 (1)任务 打开浇注后的铸型,取出铸件,打碎已浇注后的铸型,取出
铸件。是后道工序的第一步,是砂再生处理的第一步; (2)重要性 (注意事项) 及时开箱,保证砂箱的流转,浇出来的铸件
及时进入下道工序,防止铸件出现裂纹和震坏。 2.清砂 (1)任务 将铸件表面、内腔残留的型砂清除掉,去除芯骨和铸件表面的
-4-
2.烘烤和上涂料
(1)任务(目的) 对制备好的砂型和砂芯烘烤,上涂料,防止铸件出现气 孔,防止粘砂、冲刷,提高铸件表面光洁度。
(2)重要性 对提高铸件表面光洁度,防止粘砂、冲砂,防止气孔起很大 的甚至是决定性的作用。
(3)涂料 我公司用锆英粉醇基涂料,涂料的基本组成(骨料)是锆英粉,
化学结构式是ZrO2·SiO2, ZrO2含量越高越好,铸钢生产要求含ZrO2
中因醇类物质的挥发涂料变粘度,影响涂刷,用工业无水酒精稀释。刷
涂料时要避免涂料堆集,影响铸件尺寸,过厚的涂料层不易烘干,会造
成铸件气孔。
-5-
3.合箱(配模) (1)任务(内容)将制备好的砂型和砂芯装配起来,准备浇注。有时要放内
铸钢件的工艺流程
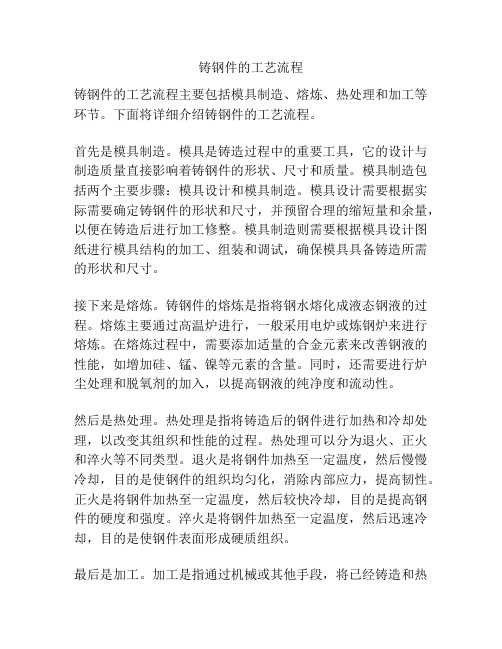
铸钢件的工艺流程铸钢件的工艺流程主要包括模具制造、熔炼、热处理和加工等环节。
下面将详细介绍铸钢件的工艺流程。
首先是模具制造。
模具是铸造过程中的重要工具,它的设计与制造质量直接影响着铸钢件的形状、尺寸和质量。
模具制造包括两个主要步骤:模具设计和模具制造。
模具设计需要根据实际需要确定铸钢件的形状和尺寸,并预留合理的缩短量和余量,以便在铸造后进行加工修整。
模具制造则需要根据模具设计图纸进行模具结构的加工、组装和调试,确保模具具备铸造所需的形状和尺寸。
接下来是熔炼。
铸钢件的熔炼是指将钢水熔化成液态钢液的过程。
熔炼主要通过高温炉进行,一般采用电炉或炼钢炉来进行熔炼。
在熔炼过程中,需要添加适量的合金元素来改善钢液的性能,如增加硅、锰、镍等元素的含量。
同时,还需要进行炉尘处理和脱氧剂的加入,以提高钢液的纯净度和流动性。
然后是热处理。
热处理是指将铸造后的钢件进行加热和冷却处理,以改变其组织和性能的过程。
热处理可以分为退火、正火和淬火等不同类型。
退火是将钢件加热至一定温度,然后慢慢冷却,目的是使钢件的组织均匀化,消除内部应力,提高韧性。
正火是将钢件加热至一定温度,然后较快冷却,目的是提高钢件的硬度和强度。
淬火是将钢件加热至一定温度,然后迅速冷却,目的是使钢件表面形成硬质组织。
最后是加工。
加工是指通过机械或其他手段,将已经铸造和热处理完成的钢件进行切割、车削、铣削、钻孔等工艺操作,最终得到符合要求的形状、尺寸和表面粗糙度的成品。
加工的过程中需要根据铸钢件的具体要求,在保证尺寸和性能的前提下,尽可能减小加工余量,以提高加工效率和降低成本。
综上所述,铸钢件的工艺流程包括模具制造、熔炼、热处理和加工等环节。
通过合理的模具设计和制造,精确的熔炼和热处理,以及高效的加工工艺,可以生产出质量优良、尺寸精确的铸钢件。
大型铸钢件的生产流程

大型铸钢件的生产流程
大型铸钢件的生产流程包括以下几个主要步骤:
1. 钢材准备:选择合适的钢材,进行熔化和准备加工所需的钢水。
2. 建模和模具制作:根据产品的设计要求,制作出相应的模具和模型,用于形成铸件的空腔。
3. 熔炼和浇注:将准备好的钢水倒入模具中,允许其冷却和凝固,形成铸件的初始形状。
4. 脱模和清理:当铸件完全冷却和凝固后,从模具中取出,并进行清理和修整,去除多余的材料和砂型等。
5. 热处理:对铸件进行加热和冷却处理,以改变其物理性质和增强其机械性能。
6. 机械加工:对铸件进行必要的机械加工,例如铣削、钻孔、研磨等,以达到设计要求的尺寸和表面质量。
7. 修整和表面处理:对铸件进行修整和表面处理,包括修磨、抛光、涂漆等,以提高其外观和耐蚀性能。
8. 检验和质量控制:进行铸件的尺寸、外观、材料成分、机械性能等方面的检验和测试,确保产品符合质量标准和要求。
9. 包装和出厂:对成品进行包装和标识,准备出厂,并安排运输和交付给客户。
以上是大型铸钢件的一般生产流程,具体的流程和步骤可能会因不同的产品和生产工艺而有所差异。
铸钢件生产工艺流程(精)
模型的生产管理;
有关模型的技术标准; 可以说模型影响着整个铸造厂(车间)的生产。
-3-
B.型砂 ※型砂直接影响着造型、制芯的生产操作,影响或者说决定生 产节奏和效率。
※型砂对铸件质量起着极大的影响,液体合金充型,在型砂中
流动、冷却、凝固、再冷却。在整个过程中有自身的、合金与 铸型的以及合金与空气的物理变化和化学反应。铸件的大多数 缺陷都与型砂直接或间接的有关,如粘砂、夹砂、气孔、裂纹、 折皱等等,还直接影响表面质量。 ※型砂直接影响劳动条件和环境。 ※型砂对生产成本的影响很大,有些砂种占成本的比例很大。
害元素、去除夹杂物、脱氧、除气调整化学成分,最后获得
合格的钢水。 (4)支持、配合的工作(工序) A.筑炉; B.备料(废钢、合金、增碳剂、脱氧剂、氧气、矿石、造渣材料 等); C.化学分析。 -7-
5.浇注
(1)任务 将钢水浇入铸型中。 (2)重要性 是直接形成铸件的一道工序。
(3)支持配合的工作:
10.入库前的抛丸:
(1)碳钢,中低合金钢铸件的最后一道工序,决定了铸件的外 观质量。
(2)对于不锈钢铸件,为最后一次钝化做准备,一定要将缺陷 彻底暴露。
11.防锈处理 (1)碳钢不锈钢铸件在表面质量合格并抛丸后应立即刷防锈油, 入库 (2)不锈钢铸件在表面质量合格抛丸后,酸洗钝化处理入库。 -15-
-12-
7.热处理:
通过热加工制度(加热、保温、冷却)改变铸件性能的加工方法 (1)任务 改变金相组织,消除应力,获得所需要的工艺性能(机加工)和使 用性能(机械性能和化学性能等) (2)重要性 铸件仅化学成分合格还不能满足用户的使用要求或工艺要求,还 需要通过热处理来使铸件满足这些要求,通过热处理可以: ※满足用户需要的机械性能;※满足用户需要的耐腐蚀性能; ※满足用户需要的工艺性能;※消除应力,稳定尺寸等。 (3)常见的热处理方法有:退火,正火,淬火,回火。 (4)设备:热处理炉,冷却水池。 -13-
铸钢件制造方式
铸钢件制造方式
铸钢件的制造方式主要包括以下几个步骤。
1.炼钢:首先需要将原材料(如铁、钢、合金等)进行炼制,得到所需的钢水。
2.浇注:将炼制好的钢水倒入预先准备好的模具中,这个阶段需要保证浇注温度、浇注速度和浇注深度等参数的合理控制,以确保铸件的质量和精度。
3.冷却:钢水在模具中逐渐冷却,凝固成形,形成铸钢件的毛坯。
4.清理:将铸钢件从模具中取出,去除浇注系统、打磨去毛刺、清理缺陷等,使铸钢件表面光洁,形状符合要求。
5.检查:对铸钢件进行尺寸、形状、重量、表面质量等方面的检查,确保铸件的质量达到标准要求。
6.热处理:对铸钢件进行热处理,如退火、正火、回火等,以改善铸件的机械性能和加工性能。
7.机械加工:根据需要,对铸钢件进行车、铣、刨、磨等机械加工,使其达到设计要求的精度和表面质量。
8.涂装:对铸钢件进行防腐、防锈处理,如涂刷防锈漆、喷涂防腐涂料等,以延长铸件的使用寿命。
以上就是铸钢件的制造方式,其中涉及到很多细节和工艺参数,需要严格控制,以保证铸件的质量。
铸钢件生产工艺流程
铸钢件生产工艺流程
朋友!今天跟您唠唠铸钢件生产这档子事儿。
咱先说说这铸钢件生产啊,那可真是个技术活!我刚入行的时候,哇,简直一头雾水,啥都不懂!
先说这原材料准备吧,就跟做饭得先买菜似的。
咱得选好钢料,这可不能马虎,要是选差了,后面全白搭!我记得有一次,我好像选错了料,唉,那批货可砸手里啦!不过吃一堑长一智,从那以后我可学精了。
然后就是熔炼环节,那炉子一开,呼呼的火,温度高得吓人!这时候可得盯紧喽,不然一不小心就容易出岔子。
造型这步也重要得很呐!我跟您说,有一回我们造型的时候,那模具出了点问题,可把我们急坏了!
浇注的时候,那钢水哗哗地流,就跟瀑布似的,可壮观啦!不过这时候可不能光顾着看,得注意控制速度和温度。
说到这,我突然想起个事儿,之前有个同行,浇注的时候没弄好,结果铸出来的钢件全是次品,损失惨重啊!
铸完了还没完,后面还有清理、热处理啥的。
这清理就跟给人洗澡似的,得把脏东西都弄干净。
热处理呢,就好比给钢件“健身”,让它更结实耐用。
我在这行干了 20 多年啦,中间犯过不少错,也学到了不少东西。
这工艺啊,也是不断在进步,以前觉得难的,现在可能都不算啥了。
就像现在流行的那些新技术,我有时候都还搞不太明白呢,还得继续学习。
不知道您听我这么一说,心里有没有点谱啦?要是您有啥想法,赶紧跟我交流交流!我这又扯远啦,反正大概就是这么个流程,您自个儿琢磨琢磨!。
铸钢件生产工艺流程及所用耐火材料
铸钢件生产工艺流程及所用耐火材料下载温馨提示:该文档是我店铺精心编制而成,希望大家下载以后,能够帮助大家解决实际的问题。
文档下载后可定制随意修改,请根据实际需要进行相应的调整和使用,谢谢!并且,本店铺为大家提供各种各样类型的实用资料,如教育随笔、日记赏析、句子摘抄、古诗大全、经典美文、话题作文、工作总结、词语解析、文案摘录、其他资料等等,如想了解不同资料格式和写法,敬请关注!Download tips: This document is carefully compiled by theeditor. I hope that after you download them,they can help yousolve practical problems. The document can be customized andmodified after downloading,please adjust and use it according toactual needs, thank you!In addition, our shop provides you with various types ofpractical materials,such as educational essays, diaryappreciation,sentence excerpts,ancient poems,classic articles,topic composition,work summary,word parsing,copy excerpts,other materials and so on,want to know different data formats andwriting methods,please pay attention!铸钢件生产工艺流程。
1. 造型。
使用砂型或金属模具制作铸件的外形和内腔结构。
- 1、下载文档前请自行甄别文档内容的完整性,平台不提供额外的编辑、内容补充、找答案等附加服务。
- 2、"仅部分预览"的文档,不可在线预览部分如存在完整性等问题,可反馈申请退款(可完整预览的文档不适用该条件!)。
- 3、如文档侵犯您的权益,请联系客服反馈,我们会尽快为您处理(人工客服工作时间:9:00-18:30)。
铸钢件的制作方案
一. 概述
xxX主体育场并非简单构筑物,其中的铸钢件要求尺寸精度高且加工制作难度大,其既为一件精密的机械零件,又是一件精美的艺术品。
在xxX主体育场铸钢件的设计、模型制造、铸造、加工及质检等过程中,始终贯彻下述原则:我们在设计、生产制作过程中,认真执行相关国家、行业及特定验收标准。
严格控制每一生产过程,确保提供外型尺寸符合图纸要求;化学成分、机械性能达到设计要求;铸钢件内外质量满足检测要求的高品质铸钢件。
xxX主体育场铸钢件是集计算机辅助设计(CAD)、计算机辅助制造(CAM)、计算机辅助测量(CAM)及先进的铸造凝固模拟分析技术(CAE)为一体的高科技产品。
本内容详细介绍xxX主体育场铸钢件在设计、制作过程各个环节:难点及解决方案;铸钢件主要结构形式;制作工艺流程;铸钢件制作;质量控制;检验标准。
二. 关键点、难点及解决方案
(一)铸钢件的关键点
关键点:xxX主体育场铸钢件结构形式需要满足下列要求:
首先:铸钢件保证原设计的外部造型及整体受力要求。
其次:铸钢件保证尺寸精度及表面粗制度的设计要求。
最后:铸钢件内部结构符合铸造工艺的要求。
解决方案:针对以上铸钢件的关键点,利用三维造型软件、有限元受力分析软件、计算机凝固模拟分析软件相互协调,在原设计的基础上深化设计满足上述要求的铸钢件结构形式(铸钢件三维实体模型)。
(二)铸钢件的难点
难点:由于xxX主体育场铸钢件的特点种类多、数量多、分枝多,导致大量的模型制作工作量。
如何解决模型制作在满足设计的结构形式的前提下保证工期的要求是本工程的难点。
解决方案:针对以上铸钢件的难点。
利用三维造型软件。
在模型制作环节采用木模型及消石模相结合的形式。
既能满足生产过程对模型的要求;而且又能大大缩短模型制作周期。
进而确保整个铸钢件的制作周期,及铸钢节点的质量与精度的控制。
三. 罩棚结构铸节点的主要结构形式
本工程的铸钢节点在不同的单元中外形相似,但却不相同,按设计要求每个节点大于10个分枝(最大分枝为16)则选择铸钢形式。
我们选取罩棚结构划分单元的铸钢件节点的形式如下所示:
ZG11-1 ZG11-2
ZG12-1 ZG12-2
ZG12-3 ZG12-4
ZG12-5 ZG12-6
ZG13-1 ZG14-1
ZG14-2 ZG14-3
ZG14-4 ZG14-5
ZG14-6 ZG16-1
四. 铸钢件制作工艺流程
五. 铸钢件制作(以ZG16-1节点为例)
1.铸钢件三维实体模型设计
(1)设计依据:
xxX主体育场图纸及资料
中国工程建设标准化协会标准《建筑用铸钢件技术规程》
三维实体模型如下:
ZG16-1模型图
(2)计算机凝固模拟分析确定铸钢件铸造工艺方案
凝固模拟是以铸件充型过程、凝固过程数值模拟技术为核心对铸件进行铸造工艺分析。
它可以完成铸件的凝固分析、流动分析以及流动和传热耦合计算分析。
确定铸钢件的浇注温度、浇注速度、浇注时间、钢水需求量、砂型中冷却时间等工艺参数,同时预测铸件缩孔和缩松的倾向。
对改进和优化铸造工艺、提高铸件质量、降低废品率、保证工艺设计水平稳定等起到积极的作用。
通过凝固模拟预测铸件缺陷、优化铸造工艺,保证xxX主体育场铸钢件具有优良的质量。
钢水的充型过程虽然短暂,但他体现了工艺中浇注系统的设计是否合理。
合理的浇注系统在钢水充型过程应达到以下三方面的效果:首先在浇注过程中钢水流动相对平稳,杜绝造成大的涡流,避免导致卷气、卷渣、夹杂。
其次局部的流速不能过大,避免导致冲砂。
最后钢水充满瞬间型腔中的钢液温度分布相对均匀,避免导致冷隔、浇不足等缺陷,造成在凝固过程应力集中、补缩通道过早凝固,形成液相孤立区,达不到顺序凝固的作用。
或者冒口因此达不到最佳效果。
工艺中的冒口、冷铁、铬铁矿砂、工艺补贴等措施决定型腔中的钢液在凝固过程能否实现有效的顺序凝固,确保冒口对铸件进行最佳补缩效果。
避免出现补缩通道提前隔断,从而在铸件内部形成大的液相孤立区。
进而导致铸件内部缩松、缩孔缺陷。
影响铸件的内在质量,降低使用性能。
应用凝固模拟分析软件对xxX 主体育场铸钢节点ZG16-1铸造过程进行模拟分析,分析过程如下图片所示。
通过分析整个凝固过程。
工艺的各种措施能够确保铸件的凝固过程实现有效的顺序凝固。
凝固过程一凝固过程二
凝固过程三凝固过程四
凝固过程五凝固过程六
凝固过程七
2.模型制作
模型的设计与制造是铸钢件制作的关键步骤。
铸造中常用的模型制作方法有:木模型、蜡模型、金属型、消失模。
其中,蜡模型只适用于小件生产,金属型适用于铸钢件、批量生产。
因此铸钢件常用的模型制作为:木模型、消失模。
木模型特点:适合小批量生产的铸钢件,但模型制作周期长。
消失模特点:适合单件生产的铸钢件,模型制作周期相对缩短,但无法二次使用。
根据本项目的特点(多品种铸钢件)主要选用消失模,搭配木模型生产铸钢件。
3.铸造
铸造是获得良好铸钢件制作的重要环节之一,根据铸钢件的特殊性并结合消失模本身的特点,制定合理的铸造工艺是铸件能否成功的关键因素。
(1)涂料
涂料是为了增加型砂抵抗金属液的冲刷和侵蚀作用,防止铸件表面产生机械或化学粘砂获得表面光洁的铸件。
本铸件采用醇基涂料,这种涂料具有良好的透气性、强度高、干燥速度快等特点。
涂料层需>2毫米。
(2)浇注系统(具体到每种铸钢件需待模拟凝固后确定)
在铸造生产中,浇注系统是影响铸件质量的重要因素之一。
根据铸钢件铸造的特点,我们制定浇注系统的基本原则如下:
确保进入型腔的钢液平稳、没有涡流现象。
选择合理浇注位置,以利于铸件顺序凝固。
浇注系统不应在铸件上引起热应力。
保证在浇注过程中,金属液在铸型内有合适的上升速度。
浇注系统的结构应具排气、挡渣能力。
4.热处理
热处理是通过加热、保温和冷却的方法,来改变钢的内部组织结构,从而改善钢性能的一种工艺。
所以温度和时间是影响热处理过程的主要因素。
xxX主体育场铸钢件的加热速度取决于钢的化学成分、铸件的断面大小以及铸件的形状。
一般合金钢铸件的加热速度比碳钢铸件要低些。
铸件断面越大,形状复杂、断面厚薄相差较大时,加热速度要缓慢些。
保温时间取决于铸件的壁厚或炉子的堆料。