ISO17637-2003 中-焊缝无损检测-目视检验
ISO 17636:2003中文版 焊缝的无损检验.熔焊接头的放射检验
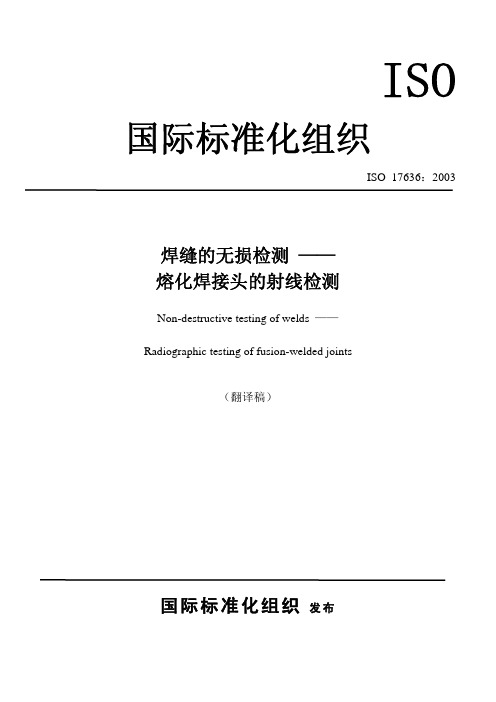
ISO国际标准化组织ISO 17636:2003焊缝的无损检测 —— 熔化焊接头的射线检测Non-destructive testing of welds —— Radiographic testing of fusion-welded joints(翻译稿)国际标准化组织 发布ww .b z f xw .c o m国际标准化组织标准焊缝的无损检测 —— 熔化焊接头的射线检测翻译单位:哈尔滨焊接研究所 翻 译:陈宇校 对:朴东光 编 辑:朴东光2006年8月ww .b zf xw .c o1 范围本国际标准规定了金属材料熔化焊接头射线检验的基本方法。
目标是通过经济的方法得到满意的和可重复的结果。
该方法总体基于该学科中认可的实践和基本原理。
本国际标准适用于板或管的熔化焊接头检验。
它遵循ISO5579中给出的规则。
本国际标准没有规定缺陷的验收等级。
注:由于本国际标准的目的,术语“管”适用于“导管”、“管”、“水管”、“锅炉”和“压力导管”。
2 规范性引用文件下列文件对于本标准的应用是不可或缺的。
对于注日期的引用文件,只能引用指定的版本。
对于未注日期的引用文件,应采用其最新版本(包含所有修改版)。
ISO2504 焊缝射线检验和胶片观察条件——推荐模式的图象质量指示器的使用 ISO5580 无损检测——工业射线照明——最低要求ISO11699-1 无损检测——工业射线胶片——第一部分:工业射线照相系统分级ISO11699-2 无损检测——工业射线胶片——第二部分:照相过程控制,通过参考值的方法3 术语和定义由于本文件的目的,使用以下术语和定义。
3.1 公称壁厚 t指母材的公称厚度。
注:制造偏差不予考虑。
3.2 透照厚度 w射线入射方向上的材料厚度,基于公称壁厚来计算。
注:多壁透照时的透照厚度由公称壁厚计算取得。
3.3工件—胶片的距离 b在射线中心束方向上被检工件的非射线照射一侧至胶片间的距离。
3.4射线源的尺寸 d放射性源的尺寸。
ISO17635:2003_焊缝的无损检测-金属材料熔化焊焊缝的一般原则

焊缝的无损检测—— 金属材料熔化焊焊缝的一般原则
1 范围
本标准给出了金属材料熔化焊无损检测方法选择指导,主要根据材料、焊缝 厚度、焊接工艺、质量控制细则和检测范围来选择。本标准规定了金属材料不同 检测方法应用的标准,以及方法选择活验收等级总则。测量方法可以单独(或组 合)使用。
本标准适用于下列材料及其合金(或其相互组合)的熔化焊焊缝的无损检测: ——钢铁; ——铝; ——铜; ——镍; ——钛。 注:本标准可用于其他金属材料的检测,但可能需要做进一步的规定。
6 人员资格
从事焊缝无损检验和最终结果评定的人员应具有资格和能力。人员资格的评 定建议按 ISO9712 或有关工业部门相应等级的类似标准。
Page 6 of 13
应用同一种方法。
8.2 检测后的文件
8.2.1 单独的检测记录 所有的检测结果应根据书面工艺规程或用于该方法的标准进行记录。 8.2.2 最终报告 对于每个被检构件或每组被检构件,其最终报告应包含检测计划所要求的信 息,至少包括如下: —构件标识; —被检焊缝标识和/或标识这些焊缝的文件编号; —实施检测的人员和机构标识; —根据按照相关检测标准编制的所有报告; —包含状态(没有检测、合格和不合格)在内的单独的检测记录; —应用的标准在检测技术和验收等级方面的偏差记录。
表面缺欠检查应在内部缺欠检测之前进行,一旦发现不合格表面缺陷,可以 将成本降到最低。
10.4 不合格缺陷
应规定处理不合格缺陷的规程,比如参考某个应用标准。 所有修复焊缝至少要按照原始焊缝的质量等级进行检测。 附录 D 给出了在不合格缺陷检查之后附加检测指南。
Page 9 of 13
附录 A (资料性附录)
本国际标准也给出了基于质量控制目的的无损检测结果评定导则,主要根据 材料、焊缝厚度、焊接工艺、质量控制细则和检测范围来选择。
ISO17637:2003_焊缝的无损检测-熔化焊接头的外观检验
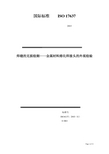
国际标准ISO 176372003焊缝的无损检测——金属材料熔化焊接头的外观检验标准号ISO4137:2003(E)© ISO目录1 范围 (3)2 检测条件和设备 (3)3 人员资格 (4)4 外观检验 (4)5 检测报告 (6)焊缝的无损检测——金属材料熔化焊接头的外观检验1 范围本标准规定了金属材料熔化焊焊缝的外观检验方法。
本标准也可用于焊接之前的接头外观检验。
2 检测条件和设备表面光照度至少应达到350LX,推荐采用500LX的光照度。
为了便于直接检查,在检查表面600mm,视角至少30°范围内,应为外观检测备好足够的空间(见图1)。
a 范围图1 检测范围当不具备图1规定的检测范围条件,或应用标准另有规定时,应考虑采用放大镜、内窥镜、纤维光导或相机做间接检查。
为了获得缺欠和背景之间良好对比和鲜明的效果,可采用辅助光源。
外观检验无法提供决定性结果时,应附加其他表面无损试验方法。
附录A给出了外观检验设备示例。
3 人员资格焊缝外观检验和最终结果评定应由具备资格和能力的人员进行。
人员资格的评定建议按ISO9712或有关工业部门相应等级的类似标准。
4 外观检验4.1 总则本国际标准不规定外观检验的范围。
外观检验范围应根据应用文件或产品标准事先规定。
检查人员应有条件获得必要的检验文件和产品文件。
所有焊前、焊接过程中或焊后的外观检验应在操作可达性条件下进行。
这可能包括含表面处理的外观检验。
4.2 坡口的外观检验要求做焊前外观检验时,应对接头做如下检查:a)焊接坡口的形状和尺寸满足焊接工艺规程的要求;b)熔化面和相邻表面是清洁的,根据应用标准或产品标准进行了所要求的表面处理;c)按照图样和工艺指令,对被焊工件进行了正确的固定。
4.3 焊接过程中的外观检验有要求时,在焊接过程应对焊缝进行如下检查:a)每条焊道或焊层被后续焊道覆盖前进行了清理,特别要注意焊缝金属和熔化面的结合处;b)无外观缺陷,比如裂纹或气孔;如果发现缺陷,应做记录以便在进一步焊接之前进行补救;c)焊道之间、焊缝与母材之间的过渡良好,便于下道焊缝熔合良好;d)为了保证能按照规定完整地去除焊缝金属,气刨的深度和形状应符合WPS要求,或与原始坡口大体一致;e)进行了所有必要的修复或补救措施之后,焊缝符合WPS的原始要求。
VT检测规程

7.做好目视检测记录,并整理现场。
对检测结果进行评级:依据EN5817对外部缺陷进行评定,评定分组C级或者B级。
100 裂纹 不允许
104 弧坑裂纹 不允许
2017 表面气孔 d﹤ mm
将可能出现的各种目视缺陷的要求列出。ቤተ መጻሕፍቲ ባይዱ
报告:有关检测对象的说明:检测范围、检测技术、鉴定结果、日期、地点和签名等。
检测条件:如有需要将表面刷干净(没有夹渣),清除焊接飞溅物;:检测条件:光照度大于500lx,检测距离小于600mm,视角大于30°。
检测前的准备和实施的详细说明:
1.穿戴好劳保用品,准备好检测的量具;
2.测量检测部位光照度是否符合标准;
3.检查焊缝的清理和打磨情况;
4.检查焊缝的外形和尺寸;
5.检查焊缝的根部和表面;
VT检测规程
前言:对需要检测的焊缝进行检测,参见图纸,检测参考ISO17637,检测规程由三级人员制定并经质量安全机构许可通过,且只能由参与制定的机构进行修改。
人员:从事目视检测人员至少取得ISO9712的Ⅰ级人员资格,评定人员至少取得Ⅱ级人员资格,检测人员视力符合ISO9712标准,且在一年有效期内。
使用的仪器:反射镜、5倍放大镜、手电筒、焊缝量规、游标卡尺、3分度焊缝量规、照明度测量仪(常用的),所有的测量器具必须是受企业监控的,并征得许可的。
成果(描述或者绘图包括感兴趣的领域以及检测母的):钢结构的环焊缝、纵焊缝,包括热影响区以及邻近的母材区域。目视检测所有焊缝的焊接缺陷,使用焊缝量规焊缝余高和轴线偏移。
ISO17639:2003_金属材料焊缝的破坏性试验-焊缝宏观和微观检验
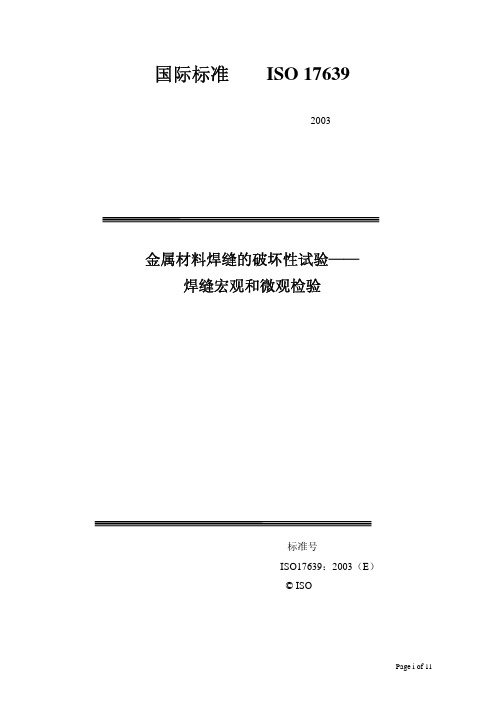
附录 A (资料性附录)
试验报告实例
根据 ISO17639(1)试(WPAR):No.(d):
生产厂:
检验目的:
试件:
试样:
母材:
焊接材料:
焊厚热处理或时效处理:
说明(b)
宏观检验(e)
微观检验(e)
(g)和(f)
(g)和(f)
图:No
图:No
位置(c)
位置(c)
放大倍数(g)
7 试样的截取
试样的截取方向一般垂直于焊缝轴线(横截面),试样包括焊缝熔敷金属和
焊缝两侧的热影响区。然而,也可以从其它方向截取试样。
在试验前应确定试件的位置、方向和数量,例如参照应用标准。
表 1 宏观和微观检验评定特性指南
特征
根据 ISO6521-1 不腐蚀宏 腐蚀宏观 不腐蚀微
缺欠
观检验
检验
观检验
-
-
×
-
15 纤维组织(晶粒)方向
-
-
×
-
16 偏析
-
-
×
-
17 沉淀
-
-
-
-
18 使用情况和不均匀性
-
(×)
×
(×)
19 力/热影响
-
-
×
-
×表示显示的特征;(×)表示显示或不显示的特征
注:表中列的特征数可能超出光学显微镜的分辨率,例如沉淀和夹渣。
腐蚀微 观检验
× × × × × × × (×) × × × × × × ×
Page 7 of 11
—腐蚀剂:xy。
43 92
54
例 1 a)试验对象:仅焊缝金属 检验—ISO17639—I—E—43—5.4/9.2/43/xy 式中 ISO17639=参照的国际标准; I=微观检验; E=经腐蚀; 43=试验对象; 5.4=钢,Cr 含量≤9%,Mo 含量≤40%; 9.2=奥氏体不锈钢 43=焊缝金属:Ni/Fe/Cr/Mo,Ni 含量≤1.2%; xy=腐蚀剂。 注:xy 代表 ISO/TR16060 相关附录中表数字代号。
ISO 17639-2003 中文版 金属材料焊缝的破坏性试验-焊缝宏观和微观检验
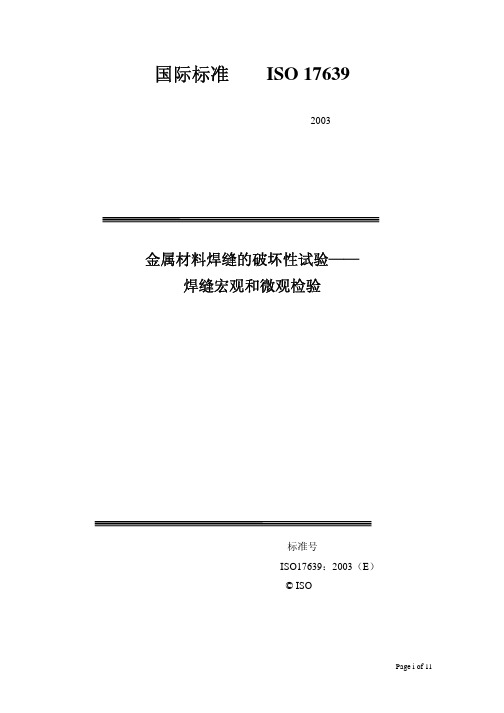
本标准采用的术语及定义如下:
3.1 宏观检验
用肉眼或低倍(一般放大倍数小于 50)检查试样,试样表面腐蚀或不腐蚀。
3.2 微观检验
Page 3 of 11
用显微镜检查试样,一般放大倍数 50-500,试样表面腐蚀或不腐蚀。
3.3 操作工
进行宏观和/或微观检验的操作人员。
ISO6520-1 焊接及相关工艺——金属材料中几何缺欠的分类 ——第 1 部 分:熔化焊
ISO9956-3 金属材料焊接工艺规程和认可——第 3 部分:钢电弧焊焊接工艺 试验
ISO9956-4 金属材料焊接工艺规程和认可——第 4 部分:铝及其合金电弧焊 焊接工艺试验
ISO/TR15608 焊接——金属材料分组体系指南 ISO/TR16060 金属材料焊缝的破坏性试验——宏观和微观检验用腐蚀剂
例 1 b)试验对象:焊缝金属和左侧母材 检验—ISO17639—I—E—43,5.4—5.4/9.2/43/xy ISO17639=参照的国际标准; I=微观检验; E=经腐蚀; 43,5.4=试验对象; 5.4=钢,Cr 含量≤9%,Mo 含量≤40%; 9.2=奥氏体不锈钢 43=焊缝金属:Ni/Fe/Cr/Mo,Ni 含量≤1.2%; xy=腐蚀剂。
8.5 腐蚀剂
ISO/TR16060 给出了不同母材、焊缝熔敷金属、检验目的和种类。 根据要求的信息,腐蚀剂的种类和浓度以及腐蚀温度和时间取决于检验材料 和类型。 相同的接头可以使用不同的腐蚀剂。
8.6 安全措施
Page 6 of 11
应遵守下列安全措施: —采取合适的保护眼或脸的措施; —使用合适的手套或夹钳处理腐蚀剂; —在排烟柜里或在排烟罩下配腐蚀剂; —总是把酸倒入水中,决不能相反操作; —总是把溶质倒入溶剂中,例如少量(溶质)倒入大量(溶剂)。
外观检验ISO17637

外观检验ISO17637:2003-焊缝外观检验-熔化焊接头外观检验1 范围本国际标准的覆盖范围是金属材料熔化焊外观检验。
它也可以用于接头的焊前外观检验。
2 检测条件和设备表面光照度至少应达到350LX,建议应达到500LX。
出于直接实施检查的目的,在将实施检查的表面600mm之内,应给外观检测备好足够的空间,而且其检测角度不应小于大约30°(见图1)。
a 范围图1 检测范围当不能根据图1的检测范围或有应用标准规定时,应考虑采用放大镜、内窥镜、纤维光导或相机间接检查。
可采用辅助光源获得缺陷和背景之间的良好对比和鲜明效果。
在有疑义的情况下,对表面有缺陷之处,应采用其他无损试验方法来辅助外观检测。
外观检验检测设备的举例在附录A中给出。
3 人员资格从事焊缝外观检验和最终结果评定应该是有资格和能力的人。
人员资格评定推荐按ISO9712或相关工业部门的适当水平的同等标准。
4 外观检验4.1 总则本国际标准没有定义外观检验的范围。
然而,这些必须事先定义,比如参考某应用或产品标准。
检查者应可接近进行检测和查找产品文件。
焊前、焊接过程中或焊后的所有外观检验必须在物理可接近的情况下进行。
这可能包含表面处理的外观检验。
4.2 接头外观检验准备如果焊前需要外观检验,应检验接头以确定:a)焊接接头坡口准备的外形和尺寸达到焊接工艺规程的要求;b)熔化面和相邻表面是清洁的,且已进行了所有根据应用或产品标准的表面处理;c)将被焊的部分根据划线或说明互相对正正确。
4.3 焊接过程中的外观检验如果需要的话,须检测焊接过程以确定:a)每条焊道或层应在被覆盖前进行清理,特别要注意焊缝金属和熔化面的结合处;b)没有外观缺陷,比如裂纹或孔;如果发现缺陷,应提出来以便在进一步焊接之前进行补救;c)焊道之间、焊缝与母材之间的过渡成型良好,以便下一道完成良好;d)刨削的深度和外形是根据WPS的或与原始凹槽外形比较以确定焊缝金属按规定的完全去除;e)在所有必要的修补或补救措施之后,焊缝符合WPS的原始要求。
欧标目视检验培训解析

目视检验基础
3.目视检测条件
I. 被检工件表面的光照度应至少达到350Lx, 推荐值为500Lx。 II. 眼睛距离被检区域的距离应不超过600mm III. 眼睛与被检工件的夹角应大于30°。 IV. 经商定可采用其他检测设备,如内窥镜。
支连接;
ISO 5817介绍
—— 以下遵照ISO 4063的焊接过程及其规定的中 间过程:
—— 11 无气体保护的金属电弧焊接; —— 12 水下电弧焊接; —— 13 气体保护金属电弧焊接; —— 14 非自耗电极气体保护焊接; —— 15 等离子弧焊接; —— 31 氧燃气焊接(只用于钢材); 冶金学方面的因素,例如粒度、硬度等等,不在
ISO 5817介绍 4.缺陷限定值
ISO 5817介绍
ISO 5817介绍
ISO 5817介绍
ISO 5817介绍
ISO 5817介绍
EN 1090-2介绍
ISO 13920:1996焊接结构公差
EN 1090-2介绍
ISO 13920:1996焊接结构公差
EN 1090-2介绍
EN 1090-2制作公差
EN 1090-2介绍
EN 1090-2介绍
EN 1090-2介绍
EN 1090-2介绍
喷涂工艺检验
1.喷涂工艺标准
EN 1090-2 钢结构和铝结构的施工-第 2 部分:钢结构的施工技术要 求 EN ISO 8501(所有部分),涂装油漆和有关产品前钢材预处理 — 表面清洁度的目视评定 EN ISO 8503-1,涂装油漆和有关产品前钢材预处理 — 喷射清理钢 材的表面粗糙度特性。第 1 部分:磨料喷射清理表面粗糙度的 ISO 评定 (ISO 8503-1:1988) EN ISO 8503-2,涂装油漆和有关产品前钢材预处理 — 喷射清理钢 材的表面粗糙度特性。第 2 部分:磨料喷射清理表面粗糙度的定级 方法 — 比较方法 (ISO 8503-2:1988) EN ISO 12944(所有部分),色漆和清漆 — 防护漆体系对钢结构的 腐蚀防护 (ISO 12944:1998) ISO 19840,色漆和清漆 — 用防护漆系统对钢结构的腐蚀防护 — 粗面上干膜厚度的测量和验收标准
- 1、下载文档前请自行甄别文档内容的完整性,平台不提供额外的编辑、内容补充、找答案等附加服务。
- 2、"仅部分预览"的文档,不可在线预览部分如存在完整性等问题,可反馈申请退款(可完整预览的文档不适用该条件!)。
- 3、如文档侵犯您的权益,请联系客服反馈,我们会尽快为您处理(人工客服工作时间:9:00-18:30)。
1 范围 本国际标准的适用范围是金属材料熔化焊外观检测,它也可以用于接头的焊前外观检
测。 2 检测条件和设备
表面光照度至少应达到 350Lx,建议应达到 500Lx。 出于直接实施检测的目的,在距实施检测的表面 600mm 之内,应给外观检测备好足够 的空间,且其检测角度不应小于大约 30°(见图 1)。
平焊缝
凹形
凸面
对接 焊缝
测量 范围
mm
读数 精度
mm
夹角或角 焊缝角度
夹角或角 焊缝允许
偏差
错边量钩状检查器具
测量板材和管材对接焊缝坡
—
—
—
X
0~100
0.05
—
—
口错边量。
万用对接焊缝测量器具
测量接头准备和完成的对接
焊缝:
1)坡口角度
2)根部间隙宽度
X
3)焊缝余高
4)焊缝表面宽度
5)咬边的深度
6)填充材料的直径
A.3 表 1 中详细列出了典型测量设备和量规。 注:这些设备和量规是检测设备的一个例子,其中的一些设计可能是注册的设计或专利。
焊缝量具
附录 A(资料性)检测设备举例
表 A.1 测量仪器和焊缝量具——测量范围和读数精度
焊缝类型
说明
平焊缝
角焊缝 凹形
凸面
对接 焊缝
测量 范围
mm
读数 精度
mm
夹角或角 焊缝角度
4.4.5 焊后热处理 焊后热处理之后可能需要进一步的检测。
4.5 修补焊缝外观检测 4.5.1 总则
如果焊缝不符合或部分符合合格标准且需要修补时,焊接接头须在重新焊接前根据 4.5.2 和 4.5.3 进行检测。
所有修补焊缝须被检测同样符合原始焊缝要求。 4.5.2 部分修补焊缝
焊缝金属挖掘须足够深和长,以便去掉所有缺陷。切口的侧面和端部的底面到表面应有 一定的坡度,切口的宽度和外形应足以进行重新焊接。 4.5.3 完全修补焊缝
附录 A (资料性) 检测设备举例
A.1 以下列出的是用于焊接接头外观检测的典型设备: a)1mm 或更小精度的直尺或测量带; b)游标测量尺要求见 ISO3599; c)塞尺的测量范围在 0.1mm 和 3mm 之间,精度为 0.1mm; d)范围量规; e)2 至 5 倍的放大镜,镜子上应有刻度,见 ISO3058; f)灯。
X
焊喉厚度和焊缝余高。
万用焊接测量器具
测量任务:
角焊缝形状和尺寸; 对接焊缝:错边量、接头准备
X
(角度)、焊缝余高、焊缝宽
度、咬边。
间隙测量器具 测量间隙宽度
—
0ห้องสมุดไป่ตู้45
X
X
X
0~50
0.3
(倒角
无
角度)
X
X
X
0~30
0.1
—
±25%
—
—
X
0~6
0.1
—
—
焊缝量具
说明
表 A.1 (续) 焊缝类型
角焊缝
X
X
X
0~30
0.1
—
±25%
A.2 也可能需要以下设备: a)外形尺寸测量设备,丝直径或宽度小于等于 1mm,每个丝端应为圆形; b)焊缝压痕材料,比如冷作塑料或泥土; c)由于外观检测有限的可接近性,可使用镜子、内窥镜、.内孔表面检查仪、纤维光学
或 TV 照相机; d)其他测量设备,比如特殊设计的焊接量规,高度/深度量规,尺或量角器。
的角焊缝;
从 3mm 到 7mm: 精度为 0.5; X 上面是 8mm,10mm 和 12mm。
依据扇
X
—
—
3~12 状部分
90
无
该仪器用其三点接触的原理进
行测量。
焊缝量具
说明
有游标的焊缝测量尺 可测量角焊缝,也可用于测量 对接焊缝的余高。 此仪器的设计构造是这样的, 它能够利用其角部测量 V 型和 单面 V 型对接焊缝的 60°、 70°、80°和 90°的夹角。但 是会由于小的偏差而导致大的 误差。
X
X
X
0~15
0.1
90
小
焊缝量具
说明
表 A.1 (续) 焊缝类型
角焊缝
平焊缝
凹形
凸面
对接 焊缝
测量 范围
mm
读数 精度
mm
夹角或角 焊缝角度
夹角或角 焊缝允许
偏差
检查角焊缝形状的量具
检查角焊缝某尺寸的外形。这 种量具需要每种尺寸角焊缝
—
—
—
—
—
—
—
—
的一个模型。
多用途测量器具
用于测量倒角角度,角焊缝焊 腿长度、咬边、焊角不对称、
夹角或角 焊缝允许
偏差
简易焊缝量具
a) 可测量从 3mm 到 15mm 厚
度的角焊缝。仪器的曲线部分
将置放在熔合面上,有三个点
可与工件和角焊缝相接触;
X
X
—
X
3~15
≈0.5
90
小
b)用直线部分测量对接焊缝的
补强。由于仪器是用相对较软
的铝制作的,所以会逐渐遭到
磨损。
一套焊接测量样板
可测量从 3mm 到 12mm 厚度
表 A.1 (续) 焊缝类型
角焊缝
平焊缝
凹形
凸面
X
X
—
对接 焊缝
X
测量 范围 mm
0~20
读数 精度
mm
夹角或角 焊缝角度
夹角或角 焊缝允许
偏差
0.1
90
无
自制焊缝量具 测量内角 90°的角焊缝厚度
X
—
—
—
0~20
0.2
90
无
三刻度焊缝量具
测量厚度和腿长,也可测对接 焊缝余高。使用方便,同样适
X
用于不均匀角焊缝。
b)熔化面和相邻表面干净,且已进行了所有根据应用或产品标准的表面处理; c)将被焊的部分根据图纸或规程互相对位正确。 4.3 焊接过程中的外观检测 如果需要的话,须检测焊接过程以确定以下内容: a)每条焊道或层应在被覆盖前进行清理,特别要注意焊缝金属和熔化面的结合处; b)没有外观缺陷,比如裂纹或孔穴;如果发现缺陷,应提出来以便在下一步焊接之前 进行补救; c)焊道之间、焊缝与母材之间的过渡成型良好,以便下一道完成良好; d)刨削的深度和外形是根据 WPS 或与原来沟槽形状来比较,以确定焊缝金属可按规 定完全去除; e)在所有必要的修补或补救措施之后,焊缝应符合 WPS 的原来要求。 4.4 焊后的外观检测 4.4.1 总则 焊接完成后应检测判定其是否符合应用或产品标准及其他协议所接受的标准,例如 ISO 5817 或 ISO10042。焊后应至少根据 4.4.2 至 4.4.5 给出的要求进行检测。 4.4.2 清理和修磨 此类焊缝应进行检测以确定以下内容: a)应以人工或机械的方式除去所有的焊渣,这样可避免掩盖任何缺陷; b)不应有工具碰撞或击打的痕迹; c)当需要进行焊缝修磨时,应避免打磨所引起的接头过热和打磨痕迹,以及不平整的 收尾; d)对于角焊缝和对接焊缝进行齐平修磨,接头部分与母材金属应圆滑过渡,不应有不 平整之处。 如果造成缺陷(由于打磨或其他原因导致的),应提出以便进行修补。 4.4.3 外形和尺寸 焊缝应检测下列内容: a) 焊缝表面的外形和焊缝金属的余高是否符合验收标准的要求(见 4.4.1); b)焊接表面是否规则,焊波的形状和节距是否均匀一致,是否有满意的视觉外形。 当 WPS 要求时,测量最后一道焊层和母材金属的距离,或测量各焊层的位置; c)焊缝的宽度应与整个接头的宽度相一致,应符合焊接图纸中或验收标准的要求(见 4.4.1)。对于对接焊缝,应检测焊缝坡口是否完全填满 。 4.4.4 焊缝根部和表面 视觉可及的焊缝部分,比如单侧对接焊缝的焊缝根部和焊缝表面均应进行检测以确定与 验收标准之间的偏差(见 4.4.1)。 焊缝应检测焊缝以确定下列内容: a)对于单面对接焊缝,整个接头的焊透性、根部凹陷、烧穿和收缩沟槽是否处在验收 标准的规定限度; b)任何咬边均应符合验收标准; c)任何缺陷如裂缝或多孔,均应依照适当的验收准则,在焊接表面或热影响区,采用 光学的辅助检查; d)任何其目的是便于组装和生产而临时焊接到工件上的附件,都可能会影响到构件的 功能或影响检测工作,都应加以除去,从而不损坏工件,应检测固定附件的区域,以确信无 任何裂缝。
当有缺陷的焊缝被完全清除,在需要或不需要增加一个新衬垫的的情况下,焊接准备的 外形和尺寸应符合原始焊缝的规定要求。 5 检测报告
如果需要检测报告,至少应包含以下信息: a) 制造厂商名称; b) 检测机构名称,如果和 a)不同; c) 检测件标识; d) 材料; e) 接头类型; f) 材料厚度; g) 焊接工艺规程; h) 合格标准; i) 不符合合格标准的缺陷及其位置; j) 参考划线区域的检测范围; k) 使用的检测设备; l) 根据合格标准的检测结果; m) 检测者名字和检测日期。 已经被检测且合格的焊缝须被标记或标识。 如果需要被检焊缝的永久外观记录,对所有缺陷应拍照片或绘制准确的草图或两者都 作。
a 范围
图 1 检测状态
当不能满足图 1 的检测状态或相关应用标准规定时,应考虑采用放大镜、内窥镜、纤维 光导或相机间接检测。
可通过采用辅助光源,来获得缺陷和背景之间的良好对比和鲜明效果。 在有疑义的情况下,对表面有缺陷之处,应采用其他无损试验方法来辅助外观检测。 外观检测设备的举例在附录 A 中给出。 3 人员资格 从事焊缝外观检测和最终结果评定的应该是有资格和能力的人员。人员资格评定推荐按 ISO9712 或相关工业部门的适当水平的同等标准。 4 外观检测 4.1 总则 本国际标准没有定义外观检测的范围。然而,这些必须事先定义,比如参考某应用或产 品标准。 检测人员应查看进行检测和生产的产品文件。 焊前、焊接过程中或焊后的所有外观检测,必须在物理可接近的情况下进行。这可能包 含表面处理后的外观检测。 4.2 接头准备的外观检测 如果焊前需要进行外观检测,应检测接头以确定以下内容: a)焊接接头坡口准备的外形和尺寸达到焊接工艺规程的要求;