硫酸锌浸出液的净化
湿法炼锌净化工艺的选择

湿法炼锌净化工艺的选择广西来宾冶炼厂锌冶炼系统年产电锌3万t,为传统的湿法工艺流程,即:锌精矿-沸腾焙烧-焙砂硫酸浸出*浸出液净化—净化液电积—电锌。
2002 年3月开始技术改造扩建工程,使得电锌产量达到了年产6万t,在技术改造过程中,最关键的净化工艺拟采用三段连续净化取代改造前的两段间断净化。
因此,该工艺在生产中无论在设备上装置上还是在工艺操作中都引入了许多先进高效和适用的技术,有利于降低劳动强度、提高产率并实现生产过程的自动化控制。
1净化过程基本原理1.1净化方法净化过程是根据硫酸锌浸出液中不同的杂质及其含量,大多采用锌粉置换和加特殊试剂化学沉淀的方法将溶液中杂质除去。
工厂根据锌焙砂中性浸出上清液的特点,选择釆用加锌粉置换的逆歸净化方法。
1.2置换原理置换是一种氧化还原反应,置换的热力学过程可用金属活泼性的大小或电子得失的难易等来定性描述,中性浸出上清液锌粉置换反应为:MeSO4 + Zn = Z11SO4 + Me I置换过程中金属的平衡电位如表1所示。
表1置换过程中金属的平衡电位(298 K) V电极反应E°E平衡Zn2* +2e=Zn■0.763-0.752(150 g/L)Cd2* +2e=Cd-0.403-0.752(2xl0-7mg/L)Cu2+ +2e= Cu+ 0.337-0.752(3.18x 10-35 mg/L)Co2+ +2e=Co-0.227-0.752(5 x IQ-12 mg/L)Ni2+ +2e=Ni-0.250-0.752( 1.5x 10-17 mg/L)SbH3 = Sb+3H+ +3e+ 0.510+ 0.752(pH = 4, Pgb% = 202.65 Pa)A S H3 = As+ 3H*+3e+ 0.600+0.752(P H=4,P A1H3 = 202.65 Pa)置换的动力学过程的反应机理:加入的锌粉作为微电池的阳极溶入液相,在那里发生水化作用,继而向溶液深处扩散并参与溶液的对流运动。
湿法高效除氯及除氯渣技术

精品整理
湿法高效除氯及除氯渣技术
一、技术概述
在常压富氧浸锌过程中,硫酸锌浸出液的净化是关键环节之一。
当硫酸锌净化液中氯含量超过300mg/L时,阳极板会出现溶解“烧板”现象,严重腐蚀阳极板。
电流效率下降,电锌产品杂质升高,贵重的阳极板损害严重,生产设备腐蚀严重,增加生产成本,同时加重现场环境污染。
这些影响随氯含量的增加而加剧,进而会导致整个电解过程瘫痪。
针对湿法炼锌氯含量高的问题,寻求一条有效途径,高效脱除硫酸锌溶液中氯,迫在眉睫。
本技术提出采用铜渣除氯及除氯渣资源化利用。
铜渣除氯基本原理是利用铜及二价铜离子与溶液中的氯离子相互作用,生成难溶的氯化亚铜沉淀,进而从溶液中将氯除去。
铜渣除氯的反应式为:Cu+2Cl-+Cu2+=Cu2Cl2。
所用的铜渣可以是两段净化除铜镉时产出的铜渣,也可以用从铜镉渣中回收镉后产出的铜渣。
采用此法除氯时,应在除铜前进行,否则除氯后的溶液又被铜离子污染,还需再次除铜。
二、技术优势
采用除铜浓密底流渣加入直接浸出中上清液实现高效脱氯,其优化工艺条件为,中上清pH2.0-3.0,除氯温度<60℃,净化时间30-60min,铜渣加入量为2-5g/L中上清液。
工业运行实验表明,溶液中的氯降至200mg/L以下,氯脱除率>80%。
随着中上清pH值的增加,脱氯率逐渐下降。
温度升高有利于除氯,但过高可能导致氯化亚铜的返溶,反而降低除氯效果。
净化时间增加不利于氯的脱除,一般可控制在30-60min。
所得的除氯铜渣直接加入铜富氧熔炼,进行铜回收,以实现资源化利用。
三、适用范围
锌冶炼清洁生产。
2、硫酸锌溶液的净化
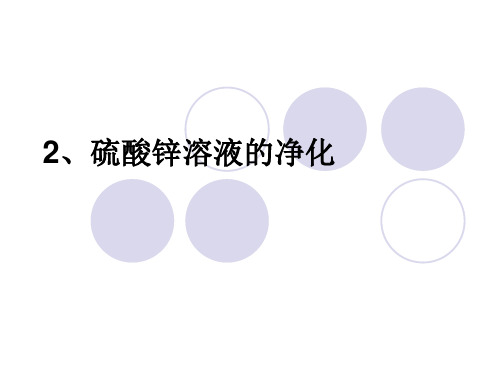
2.1 湿法炼锌净化过程
(1)硫酸锌溶液净化的目的
1)将溶液中的杂质除至电积过程的允许含量范围之内, 确保电积过程的正常进行并生产出较高等级的锌片; 2)通过净化过程的富集作用,使原料中的有价伴生元 素,如铜、镉、钴、铟、铊等得到富集,便于从渣中进 一步回收有价金属成分。
(2) 在湿法炼锌工艺中,浸出液经过的三个净化 过程 1)中性浸出时控制溶液终点pH值,使某些能够 发生水解的杂质元素从浸液中沉淀下来(中和水 解法); 2)酸性浸出时的除铁; 3)针对打入净化工序的中浸液除杂,使之符合 电积锌的要求。在实际的生产中,这些过程并不 全是在净化单元完成,如:杂质Fe、As、Sb、Si 大部分在浸出过程除去,而Cu,Cd,Co,Ni, Ge等则在净化过程除去。
锌粉置换法的反应式表示如下:
(2)影响置换过程的因素
1)锌粉质量 选用较为纯净的锌粉;锌粉的表面积合适。
2)搅拌速度 选择适宜的搅拌强度。
3)温度 加锌粉置换除Cu,Cd应控制适当的反应温度,一般 为60℃左右。
4)浸出液的成分 生产实践一般控制浸出液含锌量在150~ 180g/L为宜。生产实践中,为使净化溶液残余的Cu, Cd达到净化要求,须维持溶液的pH值在3.5以上。
(3)湿法炼锌工艺 流程
虚线框中的工序在实际 生产中是放在浸出单元过 程中完成,产出合格浸出 液(上清液)打入净化单 元过程。
表2-1 湿法炼锌工艺流程
含锌物料 浸出
含大量杂质的硫酸锌溶液
中性浸出 除 去 Fe 、 As 、 Sb 、 Si , 仍 含 有 Cu 、 Ge等杂质的合格上清液
净化 加Zn粉
Cu2++Zn==Cu+Zn2+ 置换过程的反应及限度:在有过量置换金属存在的情况下,将一直进行到 两种金属的电化学可逆电位相等时为止。反应平衡条件为:
湿法炼锌

湿法炼锌-中性浸出液的净化置换沉淀法除铜镉钴镍A 置换净化的热力学在水溶液中用一种金属取代另一种金属的过程为置换。
从热力学讲,只能用较负电性金属去置换溶液中的较正电性金属。
例如,用金属锌能将溶液中的铜置换出来:Zn+Cu2+ ==== Zn2++Cu↓因此,置换的次序决定于水溶液中金属的电位次序,而且置换趋势的大小决定于它们的电位差。
这一点可以通过热力学计算来说明。
从热力学分析可知,采用锌粉置换Cu,Cd,Co,Ni均可净化得很彻底,可使Cu,Cd,Co,Ni的离子活度分别为Zn离子活度的10-38,10-11.63,10-16.81,与10-17.69倍。
B 置换净化的动力学采用锌粉置换净化Cu,Cd比较容易,而净化除Co,Ni并不是很容易。
用理论量锌粉很容易沉淀除Cu,用几倍于理论量的锌粉也可以使Cd除去,但是用甚至几百倍理论量的锌粉也难以将Co除去至符合锌电积的要求。
Co难以除去的原因,国内外较多的文献都解释为Co2+还原析出时具有高的超电压的缘故,同时还有一个反应速率的问题。
置换反应的速率,可以理解为负电性金属在含有正电性金属离子的溶液中溶解速率,并可用下式表示:dc A- —— = k — cdt V式中 k——速率常数;A——与溶液的接触面积;V——溶液的体积;c——正电性金属离子的浓度;t——反应时间。
积分上式得到:V 1 c2k = - —·— ln —A t c1——为正电性金属离子反应前的浓度;式中 c1c——为正电性金属离子反应t时间后的浓度。
2置换过程速率可能是扩散控制,或者是化学反应控制。
研究证实,反应Zn+Cd2+ ==== Cd+Zn2+在50℃,当转速在250r/min以下时,置换反应速率常数k与转速n呈正比。
当转速在250r/min以上时,置换反应速率保持不变。
表明当低转速时,置换反应在扩散区进行,高转速时反应在动力学区进行。
置换反应速率与温度的关系式:(是在25~85℃范围内)1350lgk = 13.54 - ———T活化能 = 4.95 x 5650J/mol = 23.14kJ/mol,即反应没有纯扩散的特征。
42硫酸锌浸出液的净化的基本原理5

4 2硫酸锌浸出液的净化的基本原理54.2.4硫酸锌溶液中其它杂质的净化4.2.4.1净化除氟湿法炼锌中,氟的主要来源是在处理含有氟的氧化锌粉和升华物烟尘时,被带入到浸出液中的。
当锌电积液中含氟高时,将对剥锌造成困难。
为此,一般对处理含氟较高的氧化锌时,须经预先焙烧除氟后再行浸出。
国内某厂采用多膛炉焙烧氧化锌除氟。
目前从溶液中除氟的比较理想的方法尚少,已知的方法有如下几种。
(1)利用钍的盐类从溶液中除氟其原理是氟与钍形成难溶的化合物沉淀除去。
但钍盐昂贵,工业上不宜采用。
(2)在浸出过程中加入少量的石灰乳除氟其原理是氟与钙生成难溶化合物氟化钙(CaF2)。
各元素沉淀的次序为:Ca>Mg>Pb>Ba>Si>Mn但是,净化作业过程在中性溶液中进行,溶液中的氟将与硫酸锌和硫酸锰作用,生成ZnF+与MnF+型配离子,使之无法达到除氟的目的。
(3)硅胶除氟硅胶除氟的基本原理是:在酸性溶液中,氟以氢氟酸(HF)分子状态与硅酸聚合,并吸附在硅酸胶体上;而在中性或碱性溶液中,氢氟酸则不参加硅酸的组成,经水淋洗后,即可脱氟,而硅胶可再生。
国内某厂用冷却塔冷却后的混合液进行硅胶除氟,已在工业生产中应用,混合液在钢板衬铅的交换桶中进行交换,交换后的溶液用泵打入电积循环分配槽,然后向桶内通入自来水淋洗使硅胶再生。
实践证明,硅胶除氟率可达26.6%~53.8%,可降低氟离子对电积过程的危害,降低铝板单耗,改善析出锌的剥离。
4.2.4.2净化除氯在湿法炼锌过程中,由于处理的锌焙砂、各种烟尘、氧化锌以及其他含锌物料(如铸型渣与镀锌渣等)含有一定量的氯,这些物料中的氯在浸出过程中,几乎全部进入溶液。
同时,由于整个系统使用大量的自来水,也带入一定量的氯。
氯的存在影响锌电积过程,使铅阳极和设备遭受腐蚀,电积液含铅升高,使阴极析出锌质量降低。
Cl—的危害不容忽视,因为Cl—半径小,易从阳极保护膜细小孔隙中渗入到阳极内部与铅作用:Pb+2Cl——2e=PbCl2PbCl2=Pb2++2Cl—Pb2++SO42-=PbSO4(固)这种周而复始的反应,造成阳极腐蚀,PbSO4以机械夹杂形式进入阴极沉淀物,并与Pb2+放电沉淀,降低了电锌质量,导致锌反溶。
湿法炼锌-中性浸出过程的水解除杂质(一)

湿法炼锌-中性浸出过程的水解除杂质(一)在湿法炼锌工艺中,浸出液要经过三个净化过程,第一个是焙烧料在中性浸出时,控制浸出终点pH值,使杂质元素水解,存留于浸出渣中。
第二个是中性浸出液,在电解锌前必须进行净化除杂,使中性浸出液中的杂质含量符合电积锌的要求。
第三个净化过程是酸浸液的除铁,这是因为在热酸浸出中,大量的铁进入溶液,要使溶液中的铁沉淀除去。
中性漫出过程的水解除杂质这一过程是在中性浸出中完成的,即在浸出终了调节溶液pH值,使锌离子不致水解,而杂质金属离子全部或部分以氢氧化物Me(OH)n形式析出。
金属离子水解按下式进行。
Me n++nH20 ==== Me(OH)n+nH+ (10)该反应式(10)无电子迁移、离子活度只与pH有关。
反应的平衡条件是1pH=pHө- — lgaMen+n当水溶液介质的pH大于标准pHө时,aMen+就小于1,金属离子便水解沉淀。
反之,水溶液介质的pH小于标准pHө时,aMe n+大于1,Me(OH)n便溶解。
所以pHө是金属离子Me n+水解程度的重要数值。
按上述式(10)反应计算得出的pH25ө和PH70ө值见下表。
根据pHө值便可以计算出有关金属离子水解平衡的pH值。
1按反应式(10)的平衡关系,即 pH=pHө- — lgaMen+作图,见下图。
由它可以看出金属离子n活度在溶液中的稳定性随pH变化而变化的情况。
ө注:t=25℃,t=70℃,a=1时的数据。
随着浸出过程的进行,溶液中酸度逐渐降低,由上图可知某些杂质随着pH值升高,稳定度发生变化,并能发生水解被除去。
控制浸出终点的pH值愈高,杂质的水解除去则愈彻底。
但硫酸锌在一定pH值下也发生水解沉淀,锌水解pH值与其浓度有关,如生产实践浸出液锌的浓度在130~140g/L,则浸出终了所能允许的最大pH值不得超过5.5~5.6。
故工业生产中为了确保规定的锌浓度,浸出终点pH值取5.2~5.4。
综上所述,当浸出终点pH控制在5.2~5.4时,根据上表和上图各种杂质水解除去的可能性,以及浸出后续工序的需要,在生产实践中浸出后期水解除杂质主要是针对铁、砷、锑、硅几个元素进行,由于铁与砷、锑,铁与硅之间在水解沉淀过程中有着密切的关系,这些元素水解的好坏不仅关系它们本身净化的程度,而且还成为浸出矿浆能否很好澄清、过滤的关键。
关于硫酸锌溶液深度净化除钴的研究
95科学技术Science and technology关于硫酸锌溶液深度净化除钴的研究杨 阳,肖毕高,付 光(云南驰宏锌锗股份有限公司会泽冶炼分公司,云南 曲靖 654200)摘 要:锌作为一种重要金属,在工业发展中占据重要地位。
锌熔点低,容易成型的特点广泛用在制造业上,如汽车、航空等都使用了大量的锌。
本文综合部分参考文献,就目前硫酸锌溶液深度净化除钴的方法进行研究,概述了近些年发展的现状,指出了各种方法的优缺点。
关键词:硫酸锌溶液;深度净化;除钴中图分类号:TF813 文献标识码:A 文章编号:11-5004(2020)24-0095-2 收稿日期:2020-12作者简介:杨阳,男,生于1991年,云南曲靖人,本科,助理工程师,研究方向:冶金工程(锌湿法冶炼)。
60年代起,提炼锌主要使用湿法炼锌,后来这种工艺开始广泛用在工业生产上,湿法炼锌技术也在不断发展。
很多国外厂商,利用深度净化的方法来除去硫酸锌中的钴,提高溶液质量。
我国对硫酸锌溶液深度净化钴也做了一定研究,部分研究成果已经用于实际生产当中。
1 锌的性质和用途锌是一种没有放射性的同位素,它的外观是一种灰白色金属,不容易与空气发生反应,但是在潮湿的空气中,锌的表面会逐渐形成一种薄膜层,其主要成分为碱式碳酸锌,目的是防止锌氧化。
锌的作用主要是保护钢材,防止氧化,用途主要是镀锌。
锌能与很多金属反应,从而形成合金,增加硬度。
例如锌与铜可以组合成青铜,或者黄铜,这些都是应用广泛的合金材料。
同时锌的熔点较低,所以经常用在制造业上,一些精密部件,都离不开锌的作用。
而高纯度锌广泛使用在航天事业上,制作的AgZn 电池,释放出的能量巨大,可以用在航天器上。
锌粉也广泛用在工业上,湿法炼锌中可以出去铜钴等杂质。
在二十世纪初,一些发达国家就已经开始广泛使用锌,当时用的主要是镀锌,或者用来制造合金[1]。
2 锌的冶炼工艺湿法炼锌占据了锌产量的百分之八十以上,湿法炼锌这一方法最早起源地在美国,在1951年便有工厂使用。
用纤维素黄原酸酯去除硫酸锌浸出液中的重金属杂质
( 蝌师 范 学 院 化 学 系 漳 蝌 3 3 0) 漳 60 0 关t词 硫 酸 锌 , , , , , 维紊 黄原 酸酯 铜 镉 钴 镍 纤
周 冬 京
( 潭大学化学系 湘 湘潭)
中图丹类号 : 5. ; S 32 06 2 6 TF 0 . 5
文献标识 码 : A
实 际工 业 浸 出液 的 除杂 质实 验 : 硫 酸锌 中性 浸 出液 10 0mL, 取 0 根据 对模 拟 溶液 除 杂实 验得 出的
最 佳条件 进 行两段 除杂质 处理后 , C 、d C ”、 和 Z 的含 量进行 测定 . 对 u C ”、 o Ni n
结 果 与讨 论
生成 二价 黄 原 酸镉 沉淀 , 杂剂在 此 只起 沉 淀剂 的作 用.而 在 C 的去 除过 程 中 , 杂剂 既 起还 原 剂 除 u 除 的作 用 , 起沉 淀剂 的作用 , 又 一部分 除杂剂 先将 C 还 原为 C , u u 然后 C 再 与剩余 的除 杂剂 反应 生成 u
的除杂剂 , 有效 地 除去硫 酸锌 溶液 中的重金属 离 子 , 且成本 比传统 使用 的锌 粉置换 法要 低 , 可 而 可望 能 为 湿法 炼锌 行业 和立德 粉生产行业 提 供一种 简单廉 价 的除杂质 新方 法. 按文 献 [3 法制备 纤维素黄 原 酸酯 , 以此为 原料 制成实 验用 的除 杂剂 ( x)该 除杂剂可 去除硫 8方 并 c ,
分理 想 ; 黄原 酸钾除 Co ”的效果虽 好 , 它 散发 出恶臭 , 但 荇染环 境 , 动条件 差 ; 劳 萃取 法的 除杂质 效率 虽 很 高 , 萃取 剂部 分溶解 , 但 对后 面的 电解过 程有 不 良影响 ; 吸附 法也 由于 受 到吸 附剂 吸 附容量 等 因素 的
湿法炼锌硫酸锌溶液的深度净化
中氧化铋除氯法具有 工业简单 、成本低以及氯离 子脱除率高等 优
点 ,主 要 化 学 反 应 为 :BiOCl+NaOH+H2O=Bi(OH)3+NaC1和
有机 试剂 沉淀 法主要 包括 黄药净 化法 和亚 硝基 B一苯酚 净
工 序 。
化 法 ,通过相 关有机试剂 的添加 来对湿 法炼锌 过程 中产 生的 镉 、
(2)硫 酸锌 溶 液净 化 :此 步需 净化 除去 铜 、镉 、钴及 氟 氯. 镍 、钴 等杂质 进行置换 ,其 中主要 是进行钴 杂质 的去除 。但 在生
简要 概 述 湿 法 炼锌 硫 酸锌 溶 液 的概 念 ,并 结合 近年 来 国 内外硫 酸锌 溶 液 深度 净 化 的现 状 ,提 出具 有针 对 性 的 建议 ,一起 对我 国
未 来湿 法 炼锌 硫 酸锌 溶液 的深度 净 化 的发展 提 供 参考 依 据 。
关键 词 :湿法 炼锌 ;硫 酸 锌 溶液 ;深度 净 化
价钴 ,试 验采用先加 氧化剂再加 除钴剂的方 法去除溶 液中的钴 。 2.4 氧化铋除氯法
净 化过程 的富集作用 ,使 原料 中镉 、钴 、铊等有价 元素得到富集 ,
由于在 湿法炼锌的过程 中会 产生大量的氯离子 ,而硫酸锌溶
达 到从净化 渣中回收有价 金属成分 的 目的 。
液可 以通过与氯离子进行 反应来消除多余的氯离子 。除氯的方法
槽 、阴极 、阳极 、供电设 备 、载 流 母线 、冷 却 电解 液设 备 以及 剥 2.3 除钻 剂沉淀)去(新型的除钻 方法 )
锌机 等设备 …。
除钻剂 AnBm 中含 有黄原 酸基 团,能 与溶 液 中的钻 离子 生
1.2 硫酸锌溶液的初步净化
湿法炼锌的浸出过程
湿法炼锌的浸出过程湿法炼锌是一种将锌矿石中的锌以浸出的方式提取出来的炼锌方法。
它是一种重要的工业生产技术,用于生产高纯度的锌。
下面将从湿法炼锌的浸出过程进行详细介绍。
首先,在湿法炼锌的浸出过程中,最关键的步骤是锌矿石料浸酸。
浸酸的作用是将锌矿石中的锌转化为可溶于酸的锌盐,从而使锌得以浸出。
浸酸过程采用的主要酸是硫酸。
硫酸具有较高的溶解能力,能够有效溶解锌矿石中的锌。
在浸酸过程中,首先将锌矿石破碎,以增加其表面积,便于酸的侵蚀。
然后将破碎后的锌矿石料与稀硫酸进行混合浸泡,使锌与酸接触并发生化学反应。
浸酸过程通常在反应釜中进行,反应釜内的搅拌装置可保证物料的均匀混合,促进反应的进行。
在浸酸的反应中,硫酸与锌矿石中的锌产生反应,生成硫酸锌溶液。
反应的化学方程式如下:ZnS+H2SO4→ZnSO4+H2S↑在这个反应过程中,硫酸锌溶液中的锌已经溶解出来,而硫酸铁等其他杂质则仍然留在固体废渣中。
这种溶液的形成是湿法炼锌的核心。
接下来,需要对硫酸锌溶液进行进一步的处理,以分离出所需的锌。
处理的过程通常包括净化和电解两个主要步骤。
净化过程是通过向硫酸锌溶液中加入氢氧化钠,使溶液发生中和反应。
这个过程的主要目的是去除溶液中的铁、铜、镍等杂质。
在中和反应中生成的沉淀物是金属氢氧化物,它们与锌的溶液进行气液分离,以便于后续处理。
沉淀物中的主要杂质可通过过滤和洗涤进行分离。
之后,所得的锌硫酸盐溶液进一步进行电解,以将其中的锌分离出来。
这个步骤通常采用铁板作为阳极和铅板作为阴极,通过电流作用使溶液中的锌在阴极上析出。
电解过程中,锌盐溶液中的锌离子被还原为纯净的金属锌,析出在电极上。
而其他杂质则仍然溶于溶液中,形成电解液。
纯净的锌以颗粒形式析出后,可以通过过滤和洗涤获得。
最后,所得的纯锌颗粒进行干燥处理,以去除残余的水分。
干燥后的锌可用于制备锌合金、电池、防腐涂层等产品。
总结起来,湿法炼锌的浸出过程包括锌矿石料浸酸、硫酸锌溶液净化和电解三个主要步骤。
- 1、下载文档前请自行甄别文档内容的完整性,平台不提供额外的编辑、内容补充、找答案等附加服务。
- 2、"仅部分预览"的文档,不可在线预览部分如存在完整性等问题,可反馈申请退款(可完整预览的文档不适用该条件!)。
- 3、如文档侵犯您的权益,请联系客服反馈,我们会尽快为您处理(人工客服工作时间:9:00-18:30)。
4硫酸锌浸出液的净化-概述此外,还需要指出一点,在用锌粉置换的条件下,有析出砷化氢(H3As)的可能性,而且随着溶液酸度的增加,pH值下降,可能性就更大。
4.2.1.2锌粉置换法除铜镉从热力学分析,采用锌粉置换Cu,Cd,Co,Ni均可净化得很彻底,但在实践中,采用锌粉置换净化Cu,Cd比较容易,而净化除Co,Ni就并不是那么容易。
用理论量锌粉很容易沉淀除Cu,用几倍于理论量的锌粉也可以使Cd除去,但是用大量的锌粉,甚至几百倍理论量的锌粉也难以将Co除去至锌电积的要求。
Co难以除去的原因,国内外较多的文献都解释为Co2+还原析出时具有高的超电压的缘故,同时还有一个反应速率的问题。
一般认为,锌粉置换除铜、镉受扩散控制,因此在生产实践中要注意以下几个方面,以改善传质条件,提高净化效果,同时也要注意某些副反应的发生。
(1)锌粉的质量与用量锌粉的纯度应该比较高,除了不应带入新的杂质外,还应避免锌粉被氧化,以避免增大锌粉的耗量。
从增大比表面以加速置换反应的观点考虑,锌粉粒度固然越小越好,但如果粒度过小会导致其飘浮在溶液表面,显然也不利于锌粉的有效利用。
如果一次加锌粉同时沉积铜和镉,锌粉粒度一般为0.15~0.07mm;如果按两段分别沉积铜和镉,则可先用较粗的锌粉沉积铜,再用较细的锌粉沉积镉。
对铜的沉积而言,锌粉用量约为理论量的1.2~1.5倍便足够了,但对镉来说,为了有效防止镉的复溶,需增加锌粉用量至理论量的3~6倍。
当然,锌粉用量还与溶液成分、锌粉纯度与粒度有关,纯度低和粒度粗的锌粉,其消耗量显然要大些。
(2)搅拌速度置换过程是在搅拌槽中进行,提高搅拌速度以强化扩散传质对加速置换反应显然是有利的。
从这一点出发,流态化床净化技术具有优越性。
(3)温度提高温度既有利于置换反应的加速,也会增进锌粉的溶解和镉的复溶,一般以控制60~70℃为宜。
对镉的置换来说,由于镉在40~55℃之间存在同素异形体的转变,当温度过高时会促使镉的复溶,工艺上一般控制在50~60℃之间。
(4)浸出液成分浸出液的浓度低些固然有利于锌粉表面Zn2+的扩散传质,但如果浓度过低则因为增大了锌与氢之间的电势差而有利于H2的析出,从而导致锌粉消耗量的增大,故锌浓度一般以150~180g/L较为合适。
溶液的PH值越低越有利于H2的析出,但会增大锌粉无益耗损和镉的复溶。
在锌粉用量为理论量的3倍时,要使溶液残余的铜和镉符合要求,溶液的PH值应维持在3以上。
如果溶液含铜高而需要优先沉积铜保留镉,则宜将中性浸出液酸化至含H2SO40.1~0.2g/L,以便活化锌表面,促进铜的沉积。
(5)预防副反应的发生前已述及,溶液中的砷和锑在置换过程中尤其在酸度较高的情况下,可能会析出极毒气体AsH3和SbH3,因此,应尽可能在中性浸出时将砷和锑沉淀完全。
另外,研究结果表明,单独用锌粉置换沉积镉时,Cu2+具有催化作用,铜的浓度以0.20~0.25g/L为好。
4.2.1.3锌粉置换法除钴镍从Co/Co2+与Zn/Zn2+的标准电势来看,溶液中的钴Co2+应该可以被锌粉置换出来,溶液中残余的钴浓度可以下降到相当低的水平(约5×10-12mg/L)。
但是根据研究证实,即使溶液中钴的起始浓度很高,高到在实际上几乎遇不到的程度,加入过量很多的锌粉,甚至加数百倍当量的锌粉,置换过程的温度也很高,溶液稍微加以酸化,并且加入可观数量的、氢超电压相当高的阳离子(例如加入含镉0.8g/L的溶液,在10A/cm2时的氢超电压为0.981V),也不能使溶液中残余的钴量降到符合锌电积所要求的程度。
因此需要加入其它活化剂来实现加锌粉置换沉钴,采用的方法有砷盐净化法、锑盐净化法和合金锌粉法等。
添加锑盐、砷盐用锌粉置换钴的反应,是在锌粉表面形成微电池的电化反应。
这种电化反应的进行主要取决于电池两极的电势。
由于锌和钴的电势都为负值,当锌的析出电势绝对值大于钴的析出电势绝对值时,锌粉置换钴的反应便会不断进行。
通过研究发现,无论溶液温度多高,钴离子在锌表面析出的超电压很高,使得钴的析出电势绝对值高于锌的析出电势绝对值。
但钴离子在Sn、Sb等金属表面析出的超电压会随温度升高而下降。
所以如果采用合适的阴极金属和控制一定的温度,能够使Co2+的析出电势大大降低,达到远小于锌的溶出电势时,Co2+就容易被锌粉置换出来。
实验证明,加入Pb、Sn、As也可得到很好的结果。
(1)砒霜(砷盐)净化法根据实验研究,砷盐净化机理可作如下解释。
在含钴的硫酸锌溶液中,加锌粉置换除钴,在没有Cu2+存在的条件下是困难的。
因此加锌粉置换除钴的主要因素是CuSO4与锌粉的作用,促进这个作用进行的是亚砷酸盐。
由于铜的电势很正,容易被锌粉置换出来,这样在锌粉表面沉积的铜微粒与锌粉共存,形成微电池的两极,在铜阴极上发生下列反应:而在锌粉阳极上发生锌的溶解反应:Zn→Zn2++2e这样两极反应的结果,便将Co2+置换出来。
置换出来的钴便与Cu、As和Zn形成金属化合物,它比纯金属或与Cu和Zn形成的化合物的电势要正,因此能很有效地除去钴。
同样难于置换除去的Ni也被置换得很彻底。
这时合金电极和化合物电极的电势将比简单离子电极的电势要高得多。
但是在高温下氢在镉上的超电压低,在溶液pH=5时,镉易被氧化。
所以在砷盐净化阶段,溶液中的Cu、Ni、Co、As、Sb几乎完全沉下,而镉留在溶液中。
如果采用高温(可达95℃)更有利于Co和Ni沉淀,而镉复溶进入溶液。
至于H2的析出反应则取决于溶液的酸度及在阴极金属上析出的超电压,希望H2少析出以减少锌粉消耗。
砷盐净化法可以保证溶液中的Co2+、Ni2+除到要求的程度,得到高质量的净液(钴、镍含量降到1mg/L以下)。
但是此法仍然存在如下缺点:①原料中的铜不足时需要补加铜;②得到的Cu—Co渣被砷污染;③要求高温(80℃以上);④产生剧毒气体AsH3;⑤不迅速分离钴渣时某些杂质易复溶,致使有些结果不稳定。
(2)锑盐净化法除了用Sb2O3作锑活化剂外,有些工厂采用锑粉或其它含锑物料如酒石酸锑钾作锑活化剂,其实质是Sb的作用,统称为锑盐净化法。
锑盐净化与砷盐净化比较具有如下优点:①不需要加铜,在第一段中已除去镉,减少了镉进入钴渣,镉的回收率比砷盐净化(60%)高;②铜、镉先除后,加锑除钴的效果更好,含钴60mg/L(一般为15mg/L)时也能达到好的效果;③由于SbH3较AsH3容易分解,产生毒气的可能性较小;④锑的活性大,添加剂消耗少。
其主要工艺包括,第一段在低温下(55℃)加锌粉置换除Cu、Cd,第二段在较高温度下(85℃)加锌粉与锑活化剂除钴及其它杂质。
与砷盐净化法比较,锑盐净化所采用的高低温度恰恰倒过来,第一段为低温,第二段为高温,故称逆锑净化法或返向锑盐法。
锌盐净化的机理是在溶液中共存的锌粉表面上析出后,或锌粉中含有的其它金属作阴极,锌粉作为阳极,形成微电池,通过电化学作用,可促使Co2+还原析出。
有关原理在合金锌粉净化法中述及。
(3)合金锌粉净化法国外某企业曾经采用一种Pb-Sb合金锌粉,这种锌粉含0.02~0.05%的Sb和0.05~10%的Pb。
加入这种锌粉除Co,效果很好,并避免了钴的返溶。
合金锌粉中的锑对除钴有很大的促进作用。
当锌粉内含有一定量的锑时,二价钴离子容易被置换。
可以认为这是由于锑阴极及锌阳极所形成的微电池Zn|Zn2+||Co2+|Co(Sb),能使钴不断析出的缘故。
锑之所以有效,有人认为是锑作为微电池的阴极比其它金属对钴的亲合力大,也有人认为是由于与钴形成了一系列稳定的化合物如CoSb、CoSb2等,从而降低了二价钴离子的析出超电压。
合金锌粉中的Pb的作用主要是防止析出的Co反溶。
虽然锌粉中有锌锑时除钴效果较好,但在单独有锑存在的条件下,在锌粉表面析出的钴会有再溶的倾向,同时在有大量Cu2+存在的情况下,钴反溶加快,使除钴受到影响。
在合金锌粉中有Pb存在的条件下,可抑制Co的复溶,这是因为Pb是不溶解的,而且的电化学性不活泼,可以认为它没有以阴极金属参与电化学反应,所以Pb在锌粉表面形成凹凸不平的状态,在一定程度上阻止了Zn的溶解。
Pb含量过低,不能很有效地防止Co的复溶,但是Pb含量过高时,不免会减少合金锌粉中Zn的含量,从而减少Zn-Co微电池数,易引起钴在锑、铜上的复溶。
故铅的含量过高过低也都不利。
国内的工业性试验研究表明,当合金锌粉中含Pb3%左右,含Sb0.3%左右时净化效果最好。
另外还有人进行了以硫酸亚锡(SnSO4)为添加剂,用锌粉置换深度净化硫酸锌溶液的实验,并取得了一些成果。
4.2.2用特殊药剂法除钴镍在生产上应用的特殊试剂除钴法有黄药除钴及β一萘酚除钴。
4.2.2.1黄药除钴黄药是一种有机试剂,其中黄酸钾(C2H5OCSSK)和黄酸钠(C2H5OCSSNa)被用于湿法炼锌净化过程除钴。
黄药能与许多重金属形成难溶化合物,见表4—5。
从表中溶度积值看出,比锌的黄酸盐难溶的有Cu2+、Cd2+、Fe3+、Co3+的黄酸盐,所以加入黄药便可以除去锌溶液中的这些离子。
送住除钴的溶液杂质含量应越少越好,因为黄药几乎能与所有的有色金属离子作用,生成各种不同颜色的金属黄酸盐。
如黄酸铅呈白色沉淀,黄酸铜呈黄褐色沉淀,黄酸钴呈暗绿色沉淀,黄酸镍和黄酸铁呈褐棕色沉淀.而铝、砷、锑、镉.银等金属形成的黄酸盐皆是黄白色沉淀。
所以,溶液中含有杂质金属时,将增大黄药用量和延长除钴时间,且使除钴效率显著降低。
例如,当溶液中含镉量大于106mg/L时,黄药用基猛增到含钴量的31.9倍,较正常操作时增加一倍以上,并且使除钴时间延长到5小时左右,比正常操作时间延长一倍多。
(4)铜离子的使用除钴时使用硫酸铜在于使黄药氧化,生成复黄酸盐(双黄原酸),形成三价黄酸钴沉淀。
如铜量太少,氧化作用不彻底,除钴效率差;铜量过多又增加黄药消耗。
当容液含镉较多时,则黄药不但要除钴而且还要除镉,黄药量不足,铜离子又过多,此时铜离子不能及时除尽,残留在溶液中的硫酸铜还会置换稳定的黄酸镉中的镉,致使镉在槽内复溶而影响新液质量。
(5)铜镉渣的存在如一次净化后压滤的操作不慎,出现跑泄时,便会在溶液内带入铜镉渣,对除钴甚为不利。
因为这种铜镉渣除含铜和镉外,还含有锌粉。
由于锌粉进入溶液,破坏了除钴的氧化气氛,同时镉被强烈搅拌的空气氧化,形成镉离子(Cd2+)复溶,故增多黄药消耗。
在生产实践中,如除钴液发黑,说明有铜镉渣混入,此时便要增加黄药用量,以保证新液的质量。
生产实践证明,用黄药除钴后的溶液,含钴量可降到lmg/L以下。
由于溶液中钴的含量很低,要使反应迅速而彻底,必须加入过量的黄药。
实际的黄药加入量为溶液中钴量的10~15倍,一般为12倍。
而硫酸铜的消耗量为黄药量的1/5。