复合材料与工程专业毕业设计外文文献翻译
超好的环氧树脂复合材料英文文献

/Journal of Reinforced Plastics and Composites/content/30/19/1621The online version of this article can be found at:DOI: 10.1177/07316844114268102011 30: 1621 originally published online 7 November 2011Journal of Reinforced Plastics and Composites N. Venkateshwaran, A. ElayaPerumal and M. S. JagatheeshwaranEffect of fiber length and fiber content on mechanical properties of banana fiber/epoxy compositePublished by: can be found at:Journal of Reinforced Plastics and Composites Additional services and information for/cgi/alerts Email Alerts:/subscriptions Subscriptions: /journalsReprints.nav Reprints:/journalsPermissions.nav Permissions:/content/30/19/1621.refs.html Citations:What is This?- Nov 7, 2011OnlineFirst Version of Record- Dec 16, 2011Version of Record >>ArticleEffect of fiber length and fiber contenton mechanical properties of banana fiber/epoxy compositeN.Venkateshwaran,A.ElayaPerumal and M.S.JagatheeshwaranAbstractThe main factors that influence the properties of composite are fiber length and content.Hence the prediction of optimum fiber length and content becomes important,so that composite can be prepared with best mechanical prop-erties.Experiments are carried out as per ASTM standards to find the mechanical properties namely,tensile strength and modulus,flexural strength and modulus,and impact strength.In addition to mechanical properties,water absorption capacity of the composite is also studied.Further,fractured surface of the specimen are subjected to morphological study using scanning electron microscope.The investigation revealed the suitability of banana fiber as an effective reinforce-ment in epoxy matrix.Keywordspolymer composites,banana fiber,mechanical properties,scanning electron microscopeIntroductionNowadays,polymers are used everywhere in the day-to-day life.Plastics found its way when the need for low weight high strength material became important for various applications.The research in thefield of poly-mer and polymer-based components has gained wide-spread recognition owing to its property;however,its bio-degradability is still a matter of concern.Further, glassfiber reinforced polymers(GFRP)have become appealing substitutes for aluminum,concrete,and steel due to its high strength-to-weight ratio,ease of handling,and for being corrosion-free.Moreover, they can also be engineered to get the desired proper-ties.1Since large-scale production and fabrication of glassfiber causes environmental problems and also health hazards,a suitable alternate which is environ-mental friendly is the need of the hour.Naturalfibers that are low cost,lightweight and environmental friendly provide an excellent alternative to glassfiber. Joshi et al.2reviewed the life cycle assessment of natural fiber and glassfiber composite and found that natural fibers are environmentally superior to glassfiber,and also reduces the polymer content as reinforcement. Schmidt and Beyer,Wotzel et al.,and Corbiere et al.carried out some important works using the natural fibers as reinforcement in polymer matrix for use in automobile parts.Schmit and Beyer3have replaced the glassfiber polypropylene(PP)with hemp-PP com-posite for auto-insulation application.Wotzel et al.4 have used hemp-epoxy to replace glassfiber acryloni-trile butadien–styrene(ABS)for usage in auto-side panel.Similarly,Corbiere et al.5replaced glassfiber PP with Curaua PP for transporting pallet.All these studies revealed that the naturalfiber based polymer composite has successfully replaced the glassfiber. Pothan et al.6studied the effect offiber length and con-tent on the mechanical properties of the short banana/ polyester composite.Study shows that30–40mmfiber length and40%fiber loading provides better mechan-ical properties.Idicula et al.7investigated the mechan-ical performance of banana/sisal hybrid composite and Department of Mechanical Engineering,Anna University,Chennai,India.Corresponding author:N.Venkateshwaran,Department of Mechanical Engineering,Anna University,Chennai,IndiaEmail:venkatcad@Journal of Reinforced Plasticsand Composites30(19)1621–1627!The Author(s)2011Reprints and permissions:/journalsPermissions.navDOI:10.1177/0731684411426810the positive hybrid effect for tensile strength was found to be in the ratio of4:1(banana:sisal). Further,the tensile strength of the composite is better when bananafiber is used as skin and sisal as core material.Visco-elastic property of the banana/ sisal(1:1ratio)hybrid composite was studied by Idicula et al.8The study shows that sisal/polyester composite has maximum damping behavior and high-est impact strength as compared to banana/polyester and hybrid composite.Sapuan et al.9prepared the composite by reinforcing woven bananafibers with epoxy matrix.Tensile test result showed that the woven kind of reinforcement has better strength and the same was confirmed using Anova technique also. Venkateshwaran and ElayaPerumal10reviewed the various work in thefield of bananafiber reinforced with polymer matrix composite with reference to phys-ical properties,structure,and application. Venkateshwaran et al.11studied the effect of hybridi-zation on mechanical and water absorption properties. Investigation revealed that the addition of sisal in bananafiber composite upto50%increases the mechanical properties.Sapuan et al.12designed and fabricated the household telephone stand using woven banana fabric and epoxy as resin.Zainudin et al.13studied the thermal stability of banana pseudo-stem(BPS)filled unplastisized polyvinyl chlo-ride(UPVC)composites using thermo-gravimetric analysis.The study revealed that the incorporation of bananafiller decreases the thermal stability of the composite.Zainudin et al.14investigated the effect of bananafiller content in the UPVC matrix.The inser-tion offiller increases the modulus of the composite and not the tensile andflexural strength.Zainudin et al.15studied the effect of temperature on storage modulus and damping behavior of bananafiber rein-forced with UPVC.Uma Devi et al.16studied the mechanical properties of pineapple leaffiber rein-forced with polyester composite.Study found that optimum mechanical properties are achieved at 30mmfiber length and30%fiber content.Dabade et al.17investigated the effect offiber length and weight ratio on tensile properties of sun hemp and palmyra/polyester composite.The optimumfiber length and weight ratio were30mm and around 55%,respectively.From the above literatures,it is evident that the fiber length and content are the important factors that affect properties of the composite.Hence in this work,the effect offiber length and weight percentage on the mechanical and water absorption properties of the bananafiber epoxy composite is investigated. Further,the fractured surface of the composite are subjected to fractography study to evaluate the frac-ture mechanism.ExperimentalFabrication of compositeA molding box made of well-seasoned teak wood of dimensions300Â300Â3mm3is used to make a com-posite specimen.The top,bottom surfaces of the mold and the walls are coated with remover and kept for drying.Fibers of different length(5,10,15,and 20mm)and weight percentage(8,12,16,and20)are used along with Epoxy(LY556)and Hardener (HY951)for the preparation of composite.Testing standardsThe tensile strength of the composite was determined using Tinnus Olsen Universal Testing Machine (UTM)as per ASTM D638standard.The test speed was maintained at5mm/min.In this case,five specimens were tested with variedfiber length andfiber weight ratio.The average value of tensile load at breaking point was calculated.Theflexural strength was determined using the above-mentioned UTM as per ASTM D790procedure.The test speed was maintained between1.3and1.5mm/min. In this case,five samples were tested and the average flexural strength was reported.The impact strength of the composite specimen was determined using an Izod impact tester according to ASTM D256 Standards.In this case,five specimens were tested to obtain the average value.Figures1to5show the effect offiber length and weight content on ten-sile,flexural,and impact properties.Water absorp-tion behavior of banana/epoxy composites in water at room temperature was studied as per ASTM D570to study the kinetics of water absorption. The samples were taken out periodically andFigure1.Effect of fiber length and weight percentage on tensile strength.1622Journal of Reinforced Plastics and Composites30(19)weighed immediately,after wiping out the water from the surface of the sample and using a precise 4-digit balance to find out the content of water absorbed.All the samples were dried in an oven until constant weight was reached before immersing again in the water.The percentage of moisture absorption was plotted against time (hours)and are shown in Figures 6–13.Scanning electron microscopeThe fractured surfaces of the specimens were exam-ined directly by scanning electron microscope Hitachi-S3400N.The fractured portions of the sam-ples were cut and gold coated over the surface uni-formly for examination.The accelerating voltage used in this work was 10kV.Figures 14to 17show the fractured surface characteristics of the compositespecimen.Figure 6.Effect of moisture on fiber content;Fiber length –5mm.Figure 3.Effect of fiber length and weight percentage on flexural strength.Figure 2.Effect of fiber length and weight percentage on tensilemodulus.Figure 4.Effect of fiber length and weight percentage on flexuralmodulus.Figure 5.Effect of fiber length and weight percentage on impact strength.Venkateshwaran et al.1623Figure 12.Effect of moisture on fiber length;Fiber wt%–16.Figure 7.Effect of moisture on fiber content;Fiber length –10mm.Figure 11.Effect of moisture on fiber length;Fiber wt%–12.Figure 10.Effect of moisture on fiber length;Fiber wt%–8.Figure 8.Effect of moisture on fiber content;Fiber length –15mm.Figure 9.Effect of moisture on fiber content;Fiber length –20mm.1624Journal of Reinforced Plastics and Composites 30(19)Results and discussion Mechanical propertiesFor the tensile test,composite specimens are made of fibers of different length (5,10,15,and 20mm)and weight ratio (8,12,16,and 20)were used to calculate the tensile strength.Figures 1and 2show the effect of fiber length and weight ratios on tensile strength and modulus of the composite,respectively.Figure 1shows that the increase in fiber length and weight ratio increases the tensile strength and modulus upto 15mm fiber length and 12%weight ratio.Further increases cause the properties to decrease because of lower fiber–matrix adhesion and the quantity of fiber content being more than matrix.From Figures 1and 2,the maximum tensile strength and modulus oftheFigure 14.SEM micrograph of tensile fracturedspecimen.Figure 15.SEM micrograph of fractured specimen under flexuralload.Figure 16.SEM micrograph of fractured specimen under impactload.Figure 17.Micrograph of poorinterface.Figure 13.Effect of moisture on fiber length;Fiber wt%–20.Venkateshwaran et al.1625composite are16.39MPa and0.652GPa,respectively for thefiber length of5mm and12%weight ratio. Flexural strength and modulus for differentfiber lengths(5,10,15,and20mm)and weight ratios(8, 12,16,and20)are shown in Figures3and4,respec-tively.It was found that the maximumflexural strength and modulus are57.53MPa and8.92GPa,respectively for thefiber length of15mm andfiber weight of16%.The results of the pendulum impact test are shown in Figure 5.As thefiber weight and length increases impact strength also increases upto16%fiber weight ratio and then begin to decrease.The maximum impact strength of 2.25J/m was found for thefiber length 20mm and16%fiber weight.Although the variousfiber lengths and weight per-centage provides the maximum mechanical properties, from Figures10,12,and14it can be concluded that the optimumfiber length andfiber weight percentage is 15mm and16%respectively as the properties variation with15mm and16%are negligible when compared to the maximum mechanical properties provided by differ-entfiber lengths and weight percentage indicated as above.The mechanical properties provided above are better than coir18and palmyra.19Water absorption studyThe effects offiber length and content on the water absorption study are shown in Figures6–13.Figures 6to9show the effect offiber content on the water absorption property of the banana/epoxy composite. It shows that as thefiber content increases the moisture uptake of the composite also increases.This is due to the affinity of the bananafiber towards the moisture. The maximum moisture absorption for the composite is around5%for all length and weight percentage of composite.Figures10to13show the effect offiber length on the water uptake capability of composite.It indicates that the variation of length(5,10,15,and 20mm)does not have much impact as compared with thefiber content.The moisture absorption percentage of bananafiber/epoxy composite seems to be lesser than hempfiber20andflaxfiber21composite. Fractography studyMicrographs of fractured tensile,flexural,and impact specimens are shown in Figures14–17.Figure14shows the micrograph of fractured surface of specimen under tensile load.It clearly indicates that the failure is due to fiber pull out phenomenon.Figure15shows the frac-tured surface of the specimen under bending load. Micrograph also shows the bending offibers due to the application of load.Figure16shows the failure of the composite under impact load.Further,it also shows the striation occurring on the matrix surface and the presence of hole due tofiber pull out.Figure17shows the micrograph of20mmfiber length and20%fiber weight composite specimen.It clearly indicates that the clustering offibers result in poor interface with matrix,and in turn decreases the mechanical properties of the composite.ConclusionBased on thefindings of this investigation the following conclusions can be drawn:.The optimumfiber length and weight ratio are 15mm and16%,respectively for bananafiber/ epoxy composite..Moisture absorption percentage of banana/epoxy composite for all length and weight percentage is around5..Also,the moisture uptake capability of the compos-ite is greatly influenced byfiber content than length. .SEM image shows that increasing thefiber content above16%results in poor interface betweenfiber and matrix.References1.Houston N and Acosta F.Environmental effect of glassfiber reinforced polymers.In:Proceedings of2007Earth Quake Engineering Symposium for Young Researcher, Seattle,Washington,2007.2.Joshi SV,Drzal LT,Mohanty AK and Arora S.Are nat-ural fiber composites environmentally superior to glass fiber reinforced posite Part A2004;35: 371–376.3.Schmidt WP and Beyer HM.Life cycle study on a naturalfiber reinforced component.In:SAE Technical Paper 982195.SAE Total Life-Cycle Conference,1–3 December,1998,Graz,Austria.4.Wotzel K,Wirth R and Flake R.Life cycle studies onhemp fiber reinforced components and ABS for automo-tive parts.Die Angewandte Makromolekulare Chemie1999;272:121–127.5.Corbiere-Nicollier T,Laban BG and Lundquist.Lifecycleassessment of bio-fibers replacing glass fibers as reinforce-ment in plastics.Resour Conserv Recycl2001;33:267–287.6.Pothan LA,Thomas S and Neelakantan NR.Shortbanana fiber reinforced polyester composites:mechanical, failure and aging characteristics.J Reinf Plast Compos 1997;16:744–765.7.Idicula M,Neelakantan NR and Oommen Z.A study ofthe mechanical properties of randomly oriented short banana and sisal hybrid fibre reinforced polyester compos-ites.J Appl Polym Sci2005;96:1699–1709.1626Journal of Reinforced Plastics and Composites30(19)8.Idicula M,Malhotra SK,Joseph K and Thomas S.Dynamic mechanical analysis of randomly oriented short banana/sisal hybrid fibre reinforced polyester pos Sci Technol2005;65:1077–1085.9.Sapuan SM,Leenie A,Harimi M and Beng YK.Mechanical property analysis of woven banana/epoxy composite.Mater Design2006;27:689–693.10.Venkateshwaran N and ElayaPerumal A.Banana fiberreinforced polymer composite-a review.J Reinf Plast Compos2010;29:2387–2396.11.Venkateshwaran N,ElayaPerumal A,Alavudeen A andThiruchitrambalam M.Mechanical and water absorption behavior of banana/sisal reinforced hybrid composites.Mater Design2011;32:4017–4021.12.Sapuan SM and Maleque MA.Design and fabrication ofnatural woven fabric reinforced epoxy composite for household telephone stand.Mater Design2005;26: 65–71.13.Zainudin ES,Sapuan SM,Abdan K and MohamadMTM.Thermal degradation of banana pseudo-stem fibre reinforced unplastisized polyvinyl chloride compos-ites.Mater Design2009;30:557–562.14.Zainudin ES,Sapuan SM,Abdan K and MohamadMTM.The mechanical performance of banana pseudo-stem reinforced unplastisized polyvinyl chloride compos-ites.Polym Plast Technol Eng2009;48:97–101.15.Zainudin ES,Sapuan SM,Abdan K and MohamadMTM.Dynamic mechanical behaviour of bananapseudo-stem filled unplasticized polyvinyl chloride com-posites.Polym Polym Compos2009;17:55–62.16.Uma Devi L,Bhagawan SS and Sabu Thomas.Mechanical properties of pineapple leaf fiber-reinforced polyester composites.J Appl Polym Sci1997;64: 1739–1748.17.Dabade BM,Ramachandra Reddy G,Rajesham S andUdaya kiran C.Effect of fiber length and fiber weight ratio on tensile properties of sun hemp and palmyra fiber reinforced polyester composites.J Reinf Plast Compos 2006;25:1733–1738.18.Harish S,Peter Michael D,Bensely A,Mohan Lal D andRajadurai A.Mechanical property evaluation of natural fiber coir composite.Mater Characterisation2009;60: 44–49.19.Velmurugan R and Manikandan V.Mechanical proper-ties of palmyra/glass fiber hybrid posite Part-A2009;38:2216–2226.20.Dhakal HN,Zhang ZY and Richardson MOW.Effect ofwater absorption on the mechanical properties of hemp fibre reinforced unsaturated polyester composites.Compos Sci Technol2007;67:1674–1683.21.Alix S,Philippe E,Bessadok A,Lebrun V,Morvan V andMarais S.Effect of chemical treatments on water sorption and mechanical properties of flax fibres.Bioresour Technol2009;100:4742–4749.Venkateshwaran et al.1627。
毕业设计外文参考资料及译文

Fundamental information, including the effects of porosity, water-to-cement ratio, cement paste characteristic, volume fraction of coarse aggregates, size of coarse aggregates on pervious concrete strength, had been studied [3, 9−12]. However, for the reason that the porosity played a key role in the functional and structural performances of pervious concretes [13 − 14], there was still a need to understand more about the mechanical responses of pervious concretes proportioned for desired levels of porosities. Although it was possible to have widely different pore structure features for a given porosity, or similar pore structure features for varied porosities in pervious concrete, it was imperative to focus on the mechanical responses of pervious concrete at different designed porosities. However, compared with the related research on conventional concrete, very limited study had been conducted on the fracture and fatigue behaviors of pervious concrete, which were especially important for pavement concrete subjected to heavy traffic and to severe seasonal temperature change. The presented work outlined the raw materials and mixing proportions to produce high-strength supplementary cementitious material (SCM) modified pervious concrete (SPC) and polymer-intensified pervious concrete (PPC) at different porosities within the range of 15%−25%. Then, the mechanical properties of pervious concrete, including the compressive and flexural strengths, fracture energy, as well as fatigue property, were investigated in details.
复合材料与工程专业专业英语
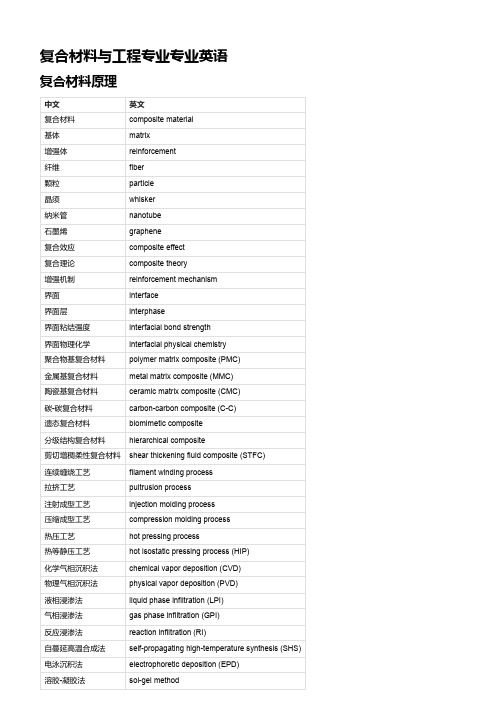
复合材料与工程专业专业英语复合材料原理中文英文复合材料composite material基体matrix增强体reinforcement纤维fiber颗粒particle晶须whisker纳米管nanotube石墨烯graphene复合效应composite effect复合理论composite theory增强机制reinforcement mechanism界面interface界面层interphase界面粘结强度interfacial bond strength界面物理化学interfacial physical chemistry聚合物基复合材料polymer matrix composite (PMC)金属基复合材料metal matrix composite (MMC)陶瓷基复合材料ceramic matrix composite (CMC)碳-碳复合材料carbon-carbon composite (C-C)遗态复合材料biomimetic composite分级结构复合材料hierarchical composite剪切增稠柔性复合材料shear thickening fluid composite (STFC)连续缠绕工艺filament winding process拉挤工艺pultrusion process注射成型工艺injection molding process压缩成型工艺compression molding process热压工艺hot pressing process热等静压工艺hot isostatic pressing process (HIP)化学气相沉积法chemical vapor deposition (CVD)物理气相沉积法physical vapor deposition (PVD)液相浸渗法liquid phase infiltration (LPI)气相浸渗法gas phase infiltration (GPI)反应浸渗法reaction infiltration (RI)自蔓延高温合成法self-propagating high-temperature synthesis (SHS)电泳沉积法electrophoretic deposition (EPD)溶胶-凝胶法sol-gel method复合材料工艺中文英文复合材料工艺学composite material processing science复合材料加工技术composite material processing technology复合材料成型方法composite material forming method复合材料固化方法composite material curing method复合材料后处理方法composite material post-processing method复合材料接头技术composite material joint technology复合材料修复技术composite material repair technology复合材料表面处理技术composite material surface treatment technology复合材料工艺参数composite material process parameters复合材料工艺性能composite material process performance复合材料工艺缺陷composite material process defects复合材料工艺模拟composite material process simulation复合材料工艺优化composite material process optimization手糊法hand lay-up method喷射成型法spray-up method真空吸附法vacuum bagging method自动糊层机法automatic tape laying method (ATL)自动纤维放置法automated fiber placement method (AFP)树脂传输成型法resin transfer molding method (RTM)树脂膜层叠加成型法resin film infusion method (RFI)真空辅助树脂传输成型法vacuum assisted resin transfer molding method (VARTM)真空辅助树脂注射成型法vacuum assisted resin injection molding method (VARI)树脂浸渍拉挤成型法resin impregnation pultrusion method树脂浸渍缠绕成型法resin impregnation winding method树脂浸渍编织成型法resin impregnation weaving method预浸料成型法prepreg molding method预浸料自动糊层机法prepreg automatic tape laying method预浸料自动纤维放置法prepreg automated fiber placement method预浸料真空吸附法prepreg vacuum bagging method预浸料热压成型法prepreg hot pressing method预浸料热等静压成型法prepreg hot isostatic pressing method预浸料自动模具线成型法prepreg automatic mold line method (AML)模塑复合材料成型法molded compound molding method压缩模塑复合材料成型法compression molded compound molding method注射模塑复合材料成型法injection molded compound molding method转移模塑复合材料成型法transfer molded compound molding method挤出模塑复合材料成型法extrusion molded compound molding method热解复合材料制备方法pyrolysis composite preparation method复合材料结构设计中文英文复合材料结构设计composite material structural design复合材料结构分析composite material structural analysis复合材料结构优化composite material structural optimization复合材料结构可靠性composite material structural reliability复合材料结构失效模式composite material structural failure mode复合材料结构失效准则composite material structural failure criterion复合材料结构强度composite material structural strength复合材料结构刚度composite material structural stiffness复合材料结构稳定性composite material structural stability复合材料结构疲劳性能composite material structural fatigue performance 复合材料结构断裂韧性composite material structural fracture toughness 复合材料结构损伤容限composite material structural damage tolerance复合材料层合板composite material laminate复合材料夹层板composite material sandwich panel复合材料桁架composite material truss复合材料梁composite material beam复合材料板壳composite material plate-shell复合材料管壳composite material tube-shell复合材料网格壳composite material grid-shell复合材料蜂窝板composite material honeycomb panel纤维方向角fiber orientation angle层厚比thickness ratio层间剪切模量interlaminar shear modulus层间剪切强度interlaminar shear strength层间正应力强度因子interlaminar normal stress intensity factor层间剪应力强度因子interlaminar shear stress intensity factor层间断裂韧度interlaminar fracture toughness层间脱层interlaminar delamination层间裂纹扩展速率interlaminar crack propagation rate层间裂纹扩展阻力曲线interlaminar crack resistance curve (R-curve)层内应力分布intralaminar stress distribution层内应变分布intralaminar strain distribution层内失效模式intralaminar failure mode层内失效准则intralaminar failure criterion复合材料力学中文英文复合材料力学composite material mechanics复合材料弹性理论composite material elasticity theory复合材料弹塑性理论composite material elasto-plasticity theory复合材料粘弹性理论composite material viscoelasticity theory复合材料热弹性理论composite material thermoelasticity theory复合材料非线性力学composite material nonlinear mechanics复合材料动力学composite material dynamics复合材料疲劳力学composite material fatigue mechanics复合材料断裂力学composite material fracture mechanics复合材料损伤力学composite material damage mechanics复合材料微观力学composite material micromechanics复合材料宏观力学composite material macromechanics复合材料多尺度力学composite material multiscale mechanics复合材料本构关系composite material constitutive relation复合材料本构方程composite material constitutive equation复合材料本构模型composite material constitutive model复合材料本构参数composite material constitutive parameter复合材料本构参数识别方法composite material constitutive parameter identification method纤维增强复合材料单元细胞模型fiber reinforced composite unit cell model纤维增强复合材料等效模量计算方法fiber reinforced composite equivalent modulus calculation method纤维增强复合材料等效泊松比计算方法fiber reinforced composite equivalent poisson ratio calculation method纤维增强复合材料等效热膨胀系数计算方法fiber reinforced composite equivalent thermal expansion coefficient calculation method纤维增强复合材料等效热导率计算方法fiber reinforced composite equivalent thermal conductivity calculation method 纤维增强复合材料等效电导率计算方法fiber reinforced composite equivalent electrical conductivity calculation method 纤维增强复合材料等效介电常数计算方法fiber reinforced composite equivalent dielectric constant calculation method 颗粒增强复合材料单元细胞模型particle reinforced composite unit cell model颗粒增强复合材料等效模量计算方法particle reinforced composite equivalent modulus calculation method颗粒增强复合材料等效泊松比计算方法particle reinforced composite equivalent poisson ratio calculation method颗粒增强复合材料等效热膨胀系数计算方法particle reinforced composite equivalent thermal expansion coefficient calculation method颗粒增强复合材料等效热导率计算方法particle reinforced composite equivalent thermal conductivity calculation method 颗粒增强复合材料等效电导率计算方法particle reinforced composite equivalent electrical conductivity calculation method 颗粒增强复合材料等效介电常数计算方法particle reinforced composite equivalent dielectric constant calculation method 晶须增强复合材料单元细胞模型whisker reinforced composite unit cell model晶须增强复合材料等效模量计算方法whisker reinforced composite equivalent modulus calculation method晶须增强复合材料等效泊松比计算方法whisker reinforced composite equivalent poisson ratio calculation method晶须增强复合材料等效热膨胀系数计算方法whisker reinforced composite equivalent thermal expansion coefficient calculation method晶须增强复合材料等效热导率计算方法whisker reinforced composite equivalent thermal conductivity calculation method 晶须增强复合材料等效电导率计算方法whisker reinforced composite equivalent electrical conductivity calculation method晶须增强复合材料等效介电常数计算方法whisker reinforced composite equivalent dielectric constant calculation method 纳米复合材料中文英文纳米复合材料nanocomposite material纳米粒子nanoparticle纳米纤维nanofiber纳米管nanotube纳米线nanowire纳米带nanoribbon纳米棒nanorod纳米片nanosheet纳米球nanosphere纳米星nanostar纳米花nanoflower纳米棘轮nanoratchet纳米泡沫nanofoam纳米多孔材料nanoporous material纳米气凝胶nanoaerogel纳米海绵nanosponge纳米网格nanogrid纳米蜂窝结构nanohoneycomb structure纳米层状结构nanolayered structure纳米纤维素复合材料nanocellulose composite material石墨烯复合材料graphene composite material二维纳米材料复合材料two-dimensional nanomaterial composite material量子点复合材料quantum dot composite material全息纳米复合材料holographic nanocomposite material超分子纳米复合材料supramolecular nanocomposite material生物医用复合材料中文英文生物医用复合材料biomedical composite material生物相容性biocompatibility生物降解性biodegradability生物吸收性bioabsorbability生物活性bioactivity生物力学性能biomechanical performance生物功能化biofunctionalization药物缓释drug delivery组织工程tissue engineering骨组织工程bone tissue engineering软骨组织工程cartilage tissue engineering皮肤组织工程skin tissue engineering神经组织工程nerve tissue engineering血管组织工程vascular tissue engineering心脏组织工程cardiac tissue engineering肝脏组织工程liver tissue engineering肾脏组织工程kidney tissue engineering胰腺组织工程pancreas tissue engineering肺组织工程lung tissue engineering骨水泥复合材料bone cement composite material骨替代材料复合材料bone substitute material composite material 骨修复板复合材料bone fixation plate composite material骨钉复合材料bone screw composite material骨髓钉复合材料bone nail composite material骨髓钉复合材料bone nail composite material人工关节复合材料artificial joint composite material人工韧带复合材料artificial ligament composite material人工心脏瓣膜复合材料artificial heart valve composite material人工血管复合材料artificial blood vessel composite material 人工角膜复合材料artificial cornea composite material人工耳蜗复合材料artificial cochlea composite material人工牙齿复合材料artificial tooth composite material人工皮肤复合材料artificial skin composite material人工肝脏复合材料artificial liver composite material复合材料测试与评价中文英文复合材料测试与评价composite material testing and evaluation复合材料测试方法composite material testing method复合材料测试标准composite material testing standard复合材料测试仪器composite material testing instrument复合材料测试数据composite material testing data复合材料测试结果composite material testing result复合材料测试分析composite material testing analysis复合材料评价方法composite material evaluation method复合材料评价指标composite material evaluation index复合材料评价模型composite material evaluation model复合材料评价系统composite material evaluation system复合材料评价报告composite material evaluation report静态力学性能测试static mechanical performance test动态力学性能测试dynamic mechanical performance test疲劳性能测试fatigue performance test断裂性能测试fracture performance test热性能测试thermal performance test电性能测试electrical performance test光学性能测试optical performance test磁学性能测试magnetic performance test磁学性能测试magnetic performance test损伤性能测试damage performance test环境适应性能测试environmental adaptability performance test 耐腐蚀性能测试corrosion resistance performance test耐磨性能测试wear resistance performance test耐老化性能测试aging resistance performance test耐辐射性能测试radiation resistance performance test耐火性能测试fire resistance performance test耐水性能测试water resistance performance test耐化学品性能测试chemical resistance performance test。
复合材料与工程专业设计外文文献翻译本科本科毕业论文

毕业设计外文资料翻译题目POLISHING OF CERAMIC TILES抛光瓷砖学院材料科学与工程专业复合材料与工程班级复材0802学生学号20080103114指导教师二〇一二年三月二十八日MATERIALS AND MANUFACTURING PROCESSES, 17(3), 401–413 (2002) POLISHING OF CERAMIC TILESC. Y. Wang,* X. Wei, and H. YuanInstitute of Manufacturing Technology, Guangdong University ofTechnology,Guangzhou 510090, P.R. ChinaABSTRACTGrinding and polishing are important steps in the production of decorative vitreous ceramic tiles. Different combinations of finishing wheels and polishing wheels are tested to optimize their selection. The results show that the surface glossiness depends not only on the surface quality before machining, but also on the characteristics of the ceramic tiles as well as the performance of grinding and polishing wheels. The performance of the polishing wheel is the key for a good final surface quality. The surface glossiness after finishing must be above 208 in order to get higher polishing quality because finishing will limit the maximum surface glossiness by polishing. The optimized combination of grinding and polishing wheels for all the steps will achieve shorter machining times and better surface quality. No obvious relationships are found between the hardness of ceramic tiles and surface quality or the wear of grinding wheels; therefore, the hardness of the ceramic tile cannot be used for evaluating its machinability.Key Words: Ceramic tiles; Grinding wheel; Polishing wheelINTRODUCTIONCeramic tiles are the common decoration material for floors and walls of hotel, office, and family buildings. Nowadays, polished vitreous ceramic tiles are more popular as decoration material than general vitreous ceramic tiles as they can *Corresponding author. E-mail: cywang@401Copyright q 2002 by Marcel Dekker, Inc. have a beautiful gloss on different colors. Grinding and polishing of ceramic tiles play an important role in the surface quality, cost, and productivity of ceramic tiles manufactured for decoration. The grinding and polishing of ceramic tiles are carried out in one pass through polishing production line with many different grinding wheels or by multi passes on a polishing machine, where different grinding wheels are used.Most factories utilize the grinding methods similar to those used for stone machining although the machining of stone is different from that of ceramic tiles. Vitreous ceramic tiles are thin, usually 5–8mm in thickness, and are a sintered material,which possess high hardness, wear resistance, and brittleness. In general, the sintering process causes surface deformation in the tiles. In themachining process, the ceramic tiles are unfixed and put on tables. These characteristics will cause easy breakage and lower surface quality if grinding wheel or grinding parameters are unsuitable. To meet the needs of ceramic tiles machining, the machinery, grinding parameters (pressure, feed speed, etc.), and grinding wheels (type and mesh size of abrasive, bond, structure of grinding wheel, etc.) must be optimized. Previous works have been reported in the field of grinding ceramic and stone[1 –4]. Only a few reports have mentioned ceramic tile machining[5 –8], where the grinding mechanism of ceramic tiles by scratching and grinding was studied. It was pointed out that the grinding mechanism of ceramic tiles is similar to that of other brittle materials. For vitreous ceramic tiles, removing the plastic deformation grooves, craters (pores), and cracks are of major concern, which depends on the micro-structure of the ceramic tile, the choice of grinding wheel and processing parameters, etc. The residual cracks generated during sintering and rough grinding processes, as well as thermal impact cracks caused by the transformation of quartz crystalline phases are the main reasons of tile breakage during processing. Surface roughness Ra and glossiness are different measurements of the surface quality. It is suggested that the surface roughness can be used to control the surface quality of rough grinding and semi-finish grinding processes, and the surface glossiness to assess the quality of finishing and polishing processes. The characteristics of thegrinding wheels, abrasive mesh size for the different machining steps, machining time, pressure, feed, and removing traces of grinding wheels will affect the processing of ceramic tiles[9].In this paper, based on the study of grinding mechanisms of ceramic tiles, the manufacturing of grinding wheels is discussed. The actions and optimization of grinding and polishing wheels for each step are studied in particular for manualpolishing machines.GRINDING AND POLISHING WHEELS FOR CERAMIC TILEMACHININGT he mac hi ni ng of cer ami c t i l e s i s a vol ume-pr oduc t i on pr oc e s s t ha t uses significant numbers of grinding wheels. The grinding and polishing wheels forceramic tile machining are different from those for metals or structural ceramics. In this part, some results about grinding and polishing wheels are introduced for better understanding of the processing of ceramic tiles.Grinding and Polishing WheelsCeramic tiles machining in a manual-polishing machine can be divided into four steps—each using different grinding wheels. Grinding wheels are marked as 2#, 3#, and 4# grinding wheels, and 0# polishing wheel; in practice, 2# and 3# grinding wheels are used for flattening uneven surfaces. Basic requirements of rough grinding wheels are long life, high removal rate, and lower price. For 2# and 3# gr inding wheel s, Si C a brasi ve s wi th me s h #180 (#320)a r e bonde d by m a g n e s i u m o x yc h l o r i d e c e m e n t(M O C)t o g e t h e r w i t h s o m e p o r o u s f i l l s, waterproof additive, etc. The MOC is used as a bond because of its low price, simple manufacturing process, and proper performance.T he 4# grinding wheel will refine the surface to show the brightness of ceramic tile. The GC#600 abrasives and some special polishingmaterials, etc., are bonded by MOC. In order to increase the performance such as elasticity, etc., of the grinding wheel, the bakelite is always added. The 4# grinding wheels must be able to rapidly eliminate all cutting grooves and increase the surface glossiness of the ceramic tiles. The 0# polishing wheel is used for obtaining final surface glossiness, whichis made of fine Al2O3 abrasives and fill. It is bonded by unsaturated resin. The polishing wheels must be able to increase surface glossiness quickly and make the glossy ceramic tile surface permanent.Manufacturing of Magnesium Oxychloride Cement Grinding WheelsAfter the abrasives, the fills and the bond MOC are mixed and poured into the models for grinding wheels, where the chemical reaction of MOC will solidify the shape of the grinding wheels. The reaction will stop after 30 days but the hardness of grinding wheel is essentially constant after 15 days. During the initial 15-day period, the grinding wheels must be maintained at a suitable humidity and temperature.For MOC grinding wheels, the structure of grinding wheel, the quality of abrasives, and the composition of fill will affe ct their grinding ability. All the factors related to the chemical reaction of MOC, such as the mole ratio of MgO/MgCl2, the specific gravity of MgCl2, the temperature and humidity to care the cement will also affect the performance of the MOC grinding wheels.Mole Ratio of MgO/MgCl2When MOC is used as the bond for the grinding wheels, hydration reaction takes place between active MgO and MgCl2, which generates a hard XMg e OH T2·Y e MgCl2T·ZH2O phase. Through proper control of the mole ratio of MgO/MgCl2, a reaction product with stable performance is formed. The bond is composed of 5Mg e OH T2·e MgCl2T·8H2O and 3Mg e OH T2·e MgCl2T·8H2O: As the former is more stable, optimization of the mole ratio of MgO/MgCl2 to produce more 5Mg e OH T2·e MgCl2T·8H2O is required. In general, the ideal range for the mole ratio of MgO/MgCl2 is 4–6. When the contents of the active MgO and MgCl2 are known, the quantified MgO and MgCl2 can be calculated.Active MgOThe content of active MgO must be controlled carefully so that hydration reaction can be successfully completed with more 5Mg e OH T2·e MgCl2T·8H2O: If the content of active MgO is too high, the hydration reaction time will be too short with a large reaction heat, which increases too quickly. The concentrations of the thermal stress can cause generation of cracks in the grinding wheel. On thecontrary, if the content of active MgO is too low, the reaction does not go to completion and the strength of the grinding wheel is decreased.Fills and AdditivesThe fills and additives play an important role in grinding wheels. Some porous fills must be added to 2# and 3# grinding wheels in order to improve the capacity to contain the grinding chips, and hold sufficient cutting grit. Waterproof additives such as sulfates can ensure the strength of grinding wheels in processing under water condition. Some fills are very effective in increasing the surface quality of ceramic tile, but the principle is not clear.Manufacturing of Polishing WheelsFine Al2O3 and some soft polishing materials, such as Fe2O3, Cr2O3, etc., are mixed together with fills. Unsaturated resin is used to bond these powders, where a chemical reaction takes place between the resin and the hardener by means of an activator. The performance of polishing wheels depends on the properties of resin and the composition of the polishing wheel. In order to contain the fine chips, which are generated by micro-cutting, some cheap soluble salt can be fed into the coolant. On the surface of the polishing wheel, the salt will leave uniform pores, which not only increase the capacity to contain chips and self-sharpening of the polishing wheel, but also improves the contact situation between polishing wheel and ceramic tiles.Experimental ProcedureTests were carried out in a special manual grinding machine for ceramictiles. Two grinding wheels were fixed in the grinding disc that was equipped to the grinding machine. The diameter of grinding disc was 255 mm. The rotating speed of the grinding disc was 580 rpm. The grinding and polishing wheels are isosceles trapezoid with surface area 31.5 cm2 (the upper edge: 2 cm, base edge: 5 cm, height: 9 cm). The pressure was adjusted by means of the load on the handle for different grinding procedures. A zigzag path was used as the moving trace for the grinding disc. To maintain flatness and edge of the ceramic tiles, at least one third of the tile must be under the grinding disc. During the grinding process, sufficient water was poured to both cool and wash the grinding wheels and the tiles. Four kinds of vitreous ceramic tiles were examined, as shown in Table 1.Two different sizes of ceramic A, A400 (size: 400 £400 £5mm3T and A500(size: 500 £500 £5mm3T were tested to understand the effect of the tile size. Forceramic tile B or C, the size was 500 £500 £5mm3: The phase composition of thetiles was determined by x-ray diffraction technique. Surface reflection glossiness and surface roughness of the ceramic tiles and the wear of grinding wheels were measured.The grinding and polishing wheels were made in-house. The 2# grindingwheels with abrasives of mesh #150 and 3# grinding wheels with mesh #320 were used during rough grinding. Using the ceramic tiles with different surface toughness ground by the 2# grinding wheel for 180 sec, the action of the 3# grinding wheels were tested. The ceramic tile was marked as A500-1 (or B500-1, C500-1, A400-1) with higher initial surface toughness or A500-2 (or B500-2, C500-2, A400-2) with lower initial surface toughness.Two kinds of finishing wheels, 4#A and 4#B were made with the same structure, abrasivity, and process, but different composition of fills and additives. Only in 4#B, a few Al2O3, barium sulfate, and magnesium stearate were added for higher surface glossiness. The composition of the polishing wheels 0#A and 0#B were different as well. In 0#B, a few white alundum (average diameter 1mm), barium sulfate, and chrome oxide were used as polishing additives, specially. After ground by 4#A (or 4#B) grinding wheel, the ceramic tiles were polished with 0#A (or 0#B). The processing combinations with 4# grinding wheels and 0#RESULTS AND DISCUSSIONSEffects of 2# and 3# Grinding WheelsSurface QualityIn rough grinding with a 2# grinding wheel, the surface roughness for all the tiles asymptotically decreases as the grinding time increases, see Fig. 1. The initial asymptote point of this curve represents the optimized rough grinding time, as continued grinding essentially has no effect on the surface roughness. In these tests, the surface roughness curves decrease with grindingtime and become smooth at ,120 sec. The final surface quality for different kinds of ceramic tiles is slightly different. In terms of the initial size of the tile, the surface roughness of ceramic tile A400 e £400 £5mm3T is lower than that of A500 e500 £500 £5mm3T: The surface roughness ofc e r a m i c t i l e B500r a p id l y d r o p s a s t he g r i n d i n g t i m e i n c r e a s e s.Thus, it is easier to remove surface material from the hardest of thethree kinds of the ceramic tiles (Table 1). However, as the final surface roughness of ceramic tile A500 is the same as that of ceramic tile C500, the hardness of theceramic tile does not have a direct relationship with the final surface quality.In the 3# grinding wheel step, all craters and cracks on the surface of ceramic tiles caused by the 2# grinding wheel must be removed. If residual cracks and craters exist, it will be impossible to get a high surface quality in the next step. The surface roughness obtained by the 2# grinding wheel willalso affect the surfaceFigure 1. Surface roughness of several ceramic tiles as a function of grinding time for 2# grindingwheel.quality of next grinding step by the 3# grinding wheel. In Fig. 2, the actions of the 3# grinding wheels are given using the ceramic tiles with different initial R a, which were ground by the 2# grinding wheel for 180 sec. The curves of surface vs. grinding time rapidly decrease in 60 sec. Asymptotic behavior essentially becomes constant after 60 sec. In general, the larger the initial surface roughness, the worse the final surface roughness. For example, for ceramic tile B500-1, the initial R a was 1.53mm, the finial R a was 0.59mm after being ground by the 3# grinding wheel. When the initial R a was 2.06mm for ceramic tile B500-2, the finial R a was 0.67mm. In Ref. [8], we studied the relations between abrasive mesh size and evaluation indices of surface quality, such as surface roughness and surface glossiness. In rough grinding, the ground surface of ceramic tile shows fracture craters. These craters scatter the light, so that the surface glossiness values are almost constant at a low level. It is difficult to improve the surface glossiness after these steps. Figure 3 shows the slow increase in surface glossiness with time by means of the 3# grinding wheel. It can be seen that the glossiness of ceramic tile B500-1 is the highest. The surface glossiness of ceramic tile A400-1 is better than that of A500-1 because the effective grinding times per unit area for former is longer than for latter. These trends are similar to those for surface r o u g h n e s s i nFig. 2.Wear of Grinding WheelsThe wear of grinding wheels is one of the factors controlling the machining cost. As shown in Fig.4, the wear of grinding wheels is proportional to grindingFigure 2. Surface roughness of several ceramic tiles as a function of grinding time for 3# grindingwheel.Figure 3. Surface glossiness of several ceramic tiles as a function of grinding time by 3# grindingwheel.time for both the grinding wheels and the three types of ceramic tiles. The wear rate of the 3# grinding wheel is larger than the 2# grinding wheel. It implies that the wear resistance of the 3# grinding wheel is not as good as 2# for constant grinding time of 180 sec. When the slope of thecurve is smaller, life of thegrinding wheels will be longer. Comparison of the ceramic tiles hardness (Table 1) with the wear resistance behavior in Fig. 4 does not reveal a strong dependency. Therefore, the hardness of the ceramic tile cannot be used to distinguish the machinability. The difference ofFigure 4. Wear of grinding wheels of several ceramic tiles as a function of grinding time for 2# and3# grinding wheels.initial surface roughness of ceramic tile will affect the wear of grinding wheel. In Fig. 4, the wear of the 3# grinding wheel for ceramic tile B500-1 is smaller than that for ceramic tile B500-2. The initial surface roughness of the latter is higher than that of the former so that additional grinding time is required to remove the deeper residual craters on the surface. Improvement of the initial surface roughness can be the principal method for obtaining better grinding quality and grinding wheel life during rough grinding.Effects of 4# Grinding Wheels and 0# Polishing WheelsSurface QualityThe combination and the performance of 4# grinding and 0# polishingwheels show different results for each ceramic tile. The grinding quality vs. grinding (polishing) time curves are presented in Fig. 5, where all the ceramic tiles were previously ground by 2# and 3# grinding wheels to the same surface quality.The surface glossiness is used to assess surface quality because the surface roughness is nearly constant as finishing or polishing time increases[8]. In this test, the ceramic tile A400 were fast ground by 4#A and 4#B grinding wheels [Fig. 5(a)]. The surface glossiness increased rapidly during the initial 90 sec and then slowly increased. The surface glossiness by grinding wheel 4#B is higher than by 4#A. Afterwards, polishing was done by four different combinations of finishing wheel and polishing wheel. By means of polishing wheels 0#A and 0#B, we processed the surface finished by 4#A grinding wheel (described as 4#A–0#A and 4#A–0#B in Fig. 5), and the surfacef i n i s h e d b y4#Bg r i n d i n g wh e e l (described as 4#B–0#A and 4#B–0#B in Fig. 5). The curves of surface glossiness vs. polishing timeshow parabolic behavior. After 60 sec of polishing, the surface glossiness reaches to ,508, then slowly increases. The polishing wheel 0#B gives a better surface quality than 0#A.In Fig. 5(a), the maximum surface glossiness of ceramic tile A400 is about ,75 by 4#B–0#B.The relation between initial surface glossiness and the final surface quality is not strong. The effect of pre-polishing surface glossiness can be observed by 0#B polishing wheel as polishing ceramictile A500 [Fig. 5(b)]. The maximum surface glossiness that can be achieved is 748 in 240 sec by4#A–0#B or 4#B–0#B. This value is lower than that of ceramic tile A400 [Fig. 5(a)].The final surface glossiness by 4#A grinding wheel is highly different from that by 4#B grinding wheel for ceramic tile B500, as shown in Fig. 5(c), but the final polishing roughness is the same when 0#A polishing wheel is used. The better performance of 0#B polishing wheel is shown because the surface glossiness canincrease from 17 to 228 in 30 sec. The maximum surface glossiness is 658 by 4#B–0#B. Thecurves of polishing time vs. surface glossiness in Fig. 5(d) present the same results as polishing of ceramic tile B500 [Fig. 5(c)]. With 0#A polishingFigure 5. Surface glossiness for ceramic tiles (a) A400, (b) A500, (c) B500, and (d) C500 as afunction of grinding (polishing) time for 4# grinding wheels and 0# polishing wheels.wheel, the action of pre-polishing surface glossiness is significant. The best value of surface glossiness in 240 sec is 708 by 4#B–0#B as polishing ceramic tile C500. The results discussed earlier describe that the surface glossiness by 0# polishing wheel will depend not only on the pre-polishing surface glossiness formed by 4# grinding wheel, but also on the characteristics of the ceramic tiles and the performance of 0# polishing wheel. The differences of initial surface glossiness and final surface glossiness are larger for 4#A and 4#B. If the prepolishing surfaceroughness is lower, the final surface glossiness will be higher.Figure 5. Continued.The polishing time taken to achieve the maximum surface glossiness will be also shorter. The initial surface quality will limit the maximum value of polishing surface glossiness that can be obtained. To reach a final surface glossiness of above 608, the minimum pre-polishing surface glossiness must be above 208.The performance of the polishing wheel is the key to good surface quality. The polishing ability of the polishing wheels depends on the properties of the ceramic tiles as well. Even if the same grinding and polishing wheels are used, on all four ceramic tiles, the maximum surface glossiness values of ceramic tiles are different. The ceramic tile A500 shows the best surface glossiness, and ceramictile B500 shows the worst, although it is easier to roughly grind ceramic tile B500. The peak valueof the surface glossiness is also limited by the properties ofWear of Grinding and Polishing WheelsThe life of 4# grinding wheels and 0# polishing wheels (Fig. 6) are longer than those of the rough grinding wheels (Fig. 4). For finer grinding (Fig. 6), it is impossible to distinguish the relation between grinding wheels and ceramic tiles. Polishing wheels have longer life because they produce more plastic deformation than removal.SUMMARY OF RESULTS(1) The performance of grinding and polishing wheels will affect its life and the surface quality of ceramic tiles.(2) In ceramic tile machining, the surface quality gained in the previous step will limit the final surface quality in the next step. The surface glossiness of pre-polishing must be higher than 208 inorder to get the highest polishing quality. The optimization of the combination of grinding wheels and polishing wheels for all the steps will shorten machining time and improve surface quality. Optimization must be determined for each ceramics tiles.Figure 6. Wear of grinding wheels 4# and polishing wheels 0# for several ceramic tiles as afunction of grinding time.(3) The effect of hardness of ceramic tiles is not direct, thus the hardness of ceramic tiles cannot be used for evaluating the machinability ofACKNOWLEDGMENTThe authors thank Nature Science Foundation of Guangdong Province and Science Foundation of Guangdong High Education for their financial support.REFERENCES1. Wang, C.Y.; Liu, P.D.; Chen, P.Y. Grinding Mechanism of Marble. AbrasivesGrinding 1987, 2 (38), 6–10, (in Chinese).2. Inasaki, I. Grinding of Hard and Brittle Materials. Annals of the CIRP 1987, 36 (2),463–471.3. Zhang, B.; Howes, D. Material Removal Mechanisms in Grinding Ceramics. Annalsof the CIRP 1994, 45 (1), 263–266.4. Malkin, S.; Hwang, T.W. Grinding Mechanism for Ceramics. Annals of the CIRP1996, 46 (2), 569–580.5. Black, I. Laser Cutting Decorative Glass, Ceramic Tile. Am. Ceram. Soc. Bull. 1998,77 (9), 53–57.6. Black, I.; Livingstone, S.A.J.; Chua, K.L. A Laser Beam Machining (LBM) Database for the Cutting of Ceramic Tile. J. Mater. Process. Technol. 1998, 84 (1–3), 47–55.7. Jiang, D.F. Mirror Surface Polishing of Ceramic Tile. New Building Mater. 1994, 20(11), 27–30, (in Chinese).8. Ma, J.F. Analysis on Man-Made Floor Brick and Manufacture of Grinding SegmentUsed for Floor Brick. Diamond Abrasive Eng. 1996, 6 (95), 35–46, (in Chinese). 9. Wang, C.Y.; Wei, X.; Yuan, H. Grinding Mechanism of Vitreous Ceramic Tile. Chin.J. Mech. Eng. 1998, 9 (8), 9–11, 46 (in Chinese).材料与制造工艺17(3), 401–413 (2002)抛光瓷砖王CY,* 魏X, 袁H制造技术研究所,广东工业大学科技,广州510090,中国P.R.摘要研磨和抛光,是装饰玻璃陶瓷砖的生产中的重要步骤。
4性复合材料论文 中英文翻译
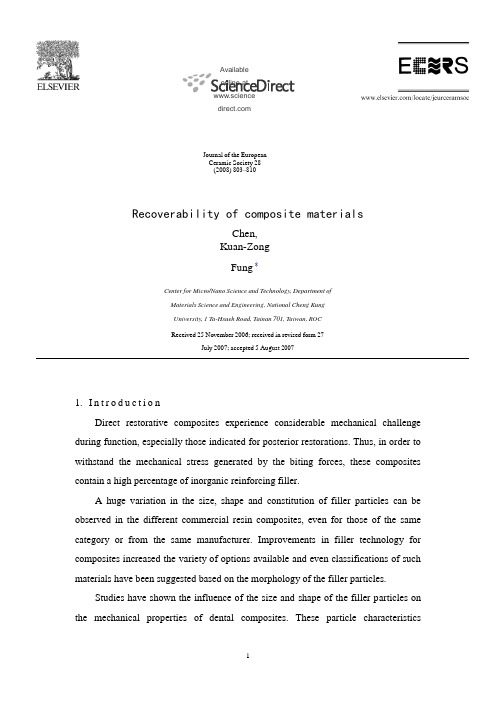
Availableonline atwww.sciencedirect.c omJournal of the EuropeanCeramic Society 28(2008) 803–810Recoverability of composite materialsChen,Kuan-ZongFung∗Center for Micro/N ano Science and T echnology, Department ofMaterials Science and Engine ering, National Cheng K ungUniversity, 1 Ta-Hsueh Road, Tainan 701, T aiwan, ROCReceived 25 November 2006; received in revised form 27July 2007; accepted 5 August 20071.I n t r o d u c t i o nDirect restorative composites experience considerable mechanical challenge during function, especially those indicated for posterior restorations. Thus, in order to withstand the mechanical stress generated by the biting forces, these composites contain a high percentage of inorganic reinforcing filler.A huge variation in the size, shape and constitution of filler particles can be observed in the different commercial resin composites, even for those of the same category or from the same manufacturer. Improvements in filler technology for composites increased the variety of options available and even classifications of such materials have been suggested based on the morphology of the filler particles.Studies have shown the influence of the size and shape of the filler particles on the mechanical properties of dental composites. These particle characteristicsdetermine what Braem et al. called “maximum particle packing fraction”, which is the ratio of true particle volume to the apparent volume occupied by the particles in the composite. According to the authors, important mechanical properties, such as Young's modulus, depend upon this ratio. Also, the presence of small spherical particles has been related to a high percentage of filler in the commercial composites, improving the mechanical properties.Nanotechnology has become a reality in different areas of engineering with the development, through physical and chemical methods, of materials and functional structures containing particles within a size interval of 0.1–100 nm. It is also one of the most noticeable advances in composite filler technology, involving the incorporation of silica fillers of nanometer size. Nanofillers are found in microfill and some hybrid composites that can be considered predecessors of the ne wer nanoparticulate composites. A study evaluating the mechanical properties of experimental composites with or without nanofillers was carried out by Musanje and Ferracane, who observed a positive effect of the presence of nanofiller particles, expressed by an improvement in flexural strength, surface hardness (H) and fracture toughness (K c).Nanoparticulate composites bring the perspective of creating another category of universal resin composite that joins the optical properties and the polishability required for anterior restorations with the mechanical properties demanded for posterior restorations. However, relatively little information about these new materials is available in the dental literature.Strength (σ) is an important property for a restorative material. It is dependent upon the material's microstructure, composition, testing method, environment and failure mechanisms. Strength values are valuable when representing information about the flaw population with potential to cause the failure of a restoration or prosthesis, and thus, must be interpreted within a context that involves the analysis of failure and structural reliability, rather than an isolated result. The presence of structural defects with potential to become critical defects, such as microcracks, grains or internal voids depend upon the volume of the material structure.Measurement of the strength of composites is often performed through flexural tests. The test indicated by the International Standards Organization to evaluate the strength of polymer-based restorative materials is the 3-point bending test (3PBT). This test employs bar-shaped specimens that bend under compressive loading equally distant from the lower supports, promoting tensile stresses in the lower surfaces that are more likely related to the fracture initiation (Fig. 1A). The test configuration tends to confine the area submitted to the stress between the supporting rollers and the loading rollers. The so-called 4-point bending test (4PBT) uses the same bar-shaped specimens, but a different configuration for load appliance based on two load cylinders over the upper surface of the specimens (Fig. 1B) that tend to expose a higher flaw containing area of the material to the stress when compared to the 3PBT. Therefore, it is expected that higher strengths are measured with the three-point bending test.Fig. 13-point (A) and 4-point (B) bending tests.Statistical parameters are commonly applied to data from mechanical strength tests to determine the level of structural reliability of the materials. The Weibull modulus (m), or shape parameter, describes the variation in the distribution of strength values from different materials and also establishes a direct relationship with the size and distribution of the defects present in a specific volume of material. In this sense, high Weibull modulus indicates a smaller error range, and potentially greater clinical reliability. In addition, the Weibull analysis can offer more clinically relevant parameters, such as the 5% failure probability (σ0.05).Data obtained from the flexural tests were submitted to Student's t-test for differences between composites in each flexural test and for the flexural test methods with the same composite (= 0.05). Weibull statistics were also carried out in ordersto obtain the shape (m) and scale (σ0) parameters of both composites.3. ResultsThere was no significant difference between the two composites evaluated, either for the 3PBT (p = 0.307) or the 4PBT (p = 0.275). However, a significantly higher flexural strength with the 3PBT was observed for both, the microhybrid (p = 0.004) and the nanofill composites (p = 0.005), in comparison with the 4PBT, confirming the hypothesis of the study4. DiscussionFiller morphology and size are always factors of concern when mechanical properties and fracture behavior of composite resins are evaluated, because they affect the filler volume fraction. In the present study, the flexural strength was not affected by the differences of three orders of magnitude in average filler size between the two composites (p = 0.307). This is in accordance with other studies that showed no significant difference in flexural strength bet ween Filtek Supreme™ (nanofill) and some microhybrid composites and. According to Mitra et al. a high filler loading was obtained in Filtek Supreme™ due to the wide particle distribution and the spherical shape of the filler particles, equaling physical and mechanical properties of microhybrid composites, including the flexural strength. The filler content of this composite is composed of 20 nm non-aggregated silica particles and nanoclusters of 75 nm agglomerated particles that are reported to reach a 0.6–1.4 μm size range that, in turn, corresponds to the average size of the filler particles of Filtek Z250™. In addition, both composites contain spherical-shaped particles that have been associated with reduced stress concentration as compared with the sharp edges present in irregular-shaped filler particles. These factors in association with the similar filler packing between the composites might have produced their similar mechanical behavior.The Weibull statistics is considered to be an acceptable approach in engineering to evaluate the reliability of a material or component. It provides a way of accessing the dependability of the material, disclosing the probability of failure at any selected level of stress. As a measure of the variability of strength in a material and its dependence on crack size distribution, a higher m, even in association with slightly lower mean fracture strength, is often preferable to a lower m associated with a higher mean fracture strength. A high m could also be useful as an indicator of a more favorable test design to evaluate and compare the strength of materials.The overall Weibull modulus results confirmed the variability of strength of both composites with the different tests, expressed by means of the standard deviation a nd the coefficient of variability. A significantly higher m was shown for the microhybrid composite when tested by 3PBT. No significant difference, however, was found between the tests for the nanofill composite. Similar results were found by Jin et al. when testing the flexural strength of ceramics. The authors concluded that it is difficult to determine, based on the Weibull modulus, the most suitable test design for different materials.Weibull statistics have been developed and used since the 1950s in the engineering community to determine equivalent strengths that have been measured by different test configurations. Weibull size scaling is routinely used to predict strength for a 3PBT when strength is measured by a 4PBT, or vice-versa. This is done by m eans of calculating “effective volumes” or “effective areas” that are under stress, and is fairly straightforward for the configurations of this study. Calculation of Weibull size scaling is done with the following formula: σ3/σ4 = (A4/A3)1/m, where σ3 and σ4 are the stresses measured under 3- and 4-point configurations, A3 and A4 are the effective areas of the associated configurations, and m is the Weibull modulus. The effective area for 3PBT is (S/4)[(m + 2)/(m + 1)2] and for 4PBT is (S/12)[(m + 2)(m + 3)/(m + 1)2], where S is the total specimen surface within the load span and is the same for both configurations, for the span lengths and specimen sizes are the same. Calculations predicted a 15% higher strength for the 3-pointconfiguration in comparison to the 4-point configuration for either material. This is slightly higher than the measured results (about 10%), but within experimental error.The fracture behavior of the composites was also expressed by σ0 and σ0.05. Both parameters indicated a lower stress for fracture of the composites when submitted to the 4PBT. This might be explained by the fact that a higher volume (53.4%) is exposed to the stress in the 4PBT comparing to the 3PBT (40%). The macroscopic observation of the composite specimens fractured by 4PBT disclosed fractures occurring in different places along the tensile surface over distances between the upper loading rollers, confirming also the wider volume of material involved in this test. In contrast and as expected, the specimens submitted to 3PBT fractured on the tensile surface midway between the two supports. According to Zeng et al. the 3PBT submits only a very small area to the maximum tensile stress, underestimating the flaws located far from the loading rollers and tending to induce a fracture initiation site. In this sense, although the 4PBT presented lower strength values for both composites, it may represent a more reliable approach as a measure of flexural strength of composites than the 3PBT. In addition, it may provide a more realistic and …safe‟ lower boundary for the resulting strength.The analysis of the fractured surface using fractographic principles is a well-established analytic tool to determine the failure behavior of brittle materials. It is based on the principle that the history of the fracture process is encoded on the fractured surface of the material. According to Le May and Begnall, “investigations of structural failure by brittle fracture should take into account, at least, two separate aspects: (1) the point from which the fracture developed is relevant in order to determine whether the fracture initiated from a manufacturing effect, whether it experienced a prior fatigue or stress corrosion that originated the crack that led to failure; (2) it should indicate that, for whatever the defect present, the load applied was enough for unstable fracture to occur”.Characteristically, brittle materials, such as composites, present a population of flaws of different sizes, geometries and orientations. Fracture occurs when the load exceeds a critical value for the propagation of the largest and most favorably orientedflaw. These flaws are induced by intrinsic imperfections in the structure of the material, by processing or by mechanical grinding and polishing, and might potentially reduce the strength of the material.The defects that led to the fracture initiation were identified as non-homogeneous distributions of organic and inorganic phases, inclusions, cracks and voids. Both, the manufacturing of the materials and the handling procedure might generate these defects. In the present study, defects similar presenting a smooth darker area of matrix, were strongly associated with the initiation of fracture.Surface flaws were identified as the fracture initiation site for 86.6–96.6% of the specimens, independent of the group. The low area exposed to the maximum tensile stress in the bending test makes fractures more likely to develop from the surface. In this sense, bending specimens are considerably sensitive to surface or edge damage during grinding or polishing. Internal critical defects were rare and always associated with moderate to high fracture strength. The internal irregular defects, are more stress inducing than internal spherical-shaped pores, requiring a lower load to propagate the fracture.The polymerization method employed, that was common to both tests, also might have affected the fracture behavior of the composites. According to Le May and Begnall, fracture initiation and propagation depend on the total local stress, which includes the externally applied load and the residual stress of the specimen. This is of major importance, because the production of 25 mm long bar-shaped specimens requires an overlapped light activation procedure when using an 11 mm diameter light guide, resulting in areas of the specimen that are exposed to twice the light and. Attempting to avoid the effect of the inhomogeneous polymerization of the specimens some authors have suggested the use of oven-LCUs.Natural and restored teeth are subjected to cyclic loading during normal masticatory function. Therefore, the wear process and failure due to fatigue stress are phenomena of relevance from the clinical standpoint and should instigate future work.5. ConclusionHigher flexural strength was produced by the 3-point bending test than by the 4-point bending test, independent of the composite evaluated. The flexural strength and the fracture behavior of both composites were similar, despite the difference of the average filler size of the composites tested, probably due to the microstructural arrangement of the nanofillers in clusters that approximate the average size of the filler of the microhybrid composite and due to the similar filler volume in both composites.AcknowledgmentThis work is financially supported by the Council of Agri- culture, Executive Y uan, Taiwan; Grant 96AS-10.1.1-AD-U1.References1. Etsell, T. H. and Flengas, S. N., Electrical properties of solid oxide elec- trolytes. Chem. Rev., 1970, 70, 339–376.2. Ishihara, T., Matsuda, H. and Takita, Y., Doped LaGaO3 perovskite type oxide as a new oxide ionic conductor. J. Am.Chem. Soc., 1994, 116,3801–3803.3. Huang, P. and Petric, A., Superior oxygen ion conductivity of lanthanu m gallate doped with strontium and magnesium. J.Electrochem. Soc., 1996,143, 1644–1648.4. Chen, T. Y. and Fu ng, K. Z., C omparison of dissolu tion behavior and ionic conduction between Sr and/or Mg dopedLaGaO3 and La Al O3. J. Power Sources, 2004, 132, 1–10.5. Stevenson, J. W., Armstrong, T. R., McC ready, D. E., Pederson, L. R. and W eber, W. J., Processing and electrical propertiesof alkaline earth-doped lanthanu m gallate. J. Electrochem. S oc., 1997, 144, 3613–3620.6. Huang, K., Tichy, R. S. and Goodenough, J. B., Superior perovskite oxide-ion conductor; strontium- andmagnesium-d oped La Ga O3. I: Phase relationships and electrical properties. J. Am. Chem. Soc., 1998, 81, 2565–2575.7. Huang, K., Feng, M. and Goodenough, J. B., W et chemical synthesis of Sr- and Mg-d oped La Ga O3, a perovskite-typeoxide-ion conductor. J. Am. Chem. Soc., 1996, 79, 1100–1104.8. Huang, K. and Goodenough, J. B., Wet chemical synthesis of Sr- and Mg- doped La Ga O3, a perovskit e-typ e oxide-ioncond ucto r. J. Solid S tate C hem.,1998, 136, 274–283.9. Simpson II, R. E., Habeger, C., R abinovich, A. and Adair, J. H., Enzyme- catalyzed inorganic precipitation of aluminumbasic sulfate. J. Am. Ceram. Soc., 1998, 81, 1377–1379.10. Tas, A. C., Majewski, P. J. and Aldinger, F., Chemical preparation of pure and strontium- and/or magnesiu m-dopedlanthanum gallate powder. J. Am. C eram. Soc., 2000, 83, 2954–2960.11. Cong, L., He, T., Ji, Y., Guan, P., Huang, Y. and Su, W., Syn- thesis andcharacterization of IT-electrolyte with perovskite structu re La0.8 Sr0.2Ga0.85Mg0.15O3−δ by glycine–nitrate combustion method. J.Alloys Compd., 2003, 348, 325–331.12. Djurado, E. and Labeau, M., Second phases in doped lanthanum gallate perovskites. J. Eur. Ceram. Soc., 1998, 18,1397–1404.13. Khanlou, A. A., Tietz, F. and Sto¨v er, D., Material properties ofLa0.8Sr0.2Ga0.9+x Mg x O3−δas a function of Ga content. Solid State Ionic,2000, 135, 543–547.14. Tas, A. C., Majewski, P. J. and Aldinger, F., Preparation of strontiu m- and zinc-do pe d LaGaO3 po wd ers via precipit ation inthe presen c e o f urea and/or enzyme urease. J. Am. Ceram. Soc., 2002, 85, 1414–1420.15. Shaw, W. H. R. and Bordeaux, J. J., The decomposition o f urea in aqueous media. J. Am. C hem. Soc., 1955, 77, 4729–4733.16. Blendell, J. E., B owen, H. K. and Coble, R. L., High purity alumina b y controlled precipitation from aluminum sulfatesolution. Am. Ceram. Soc. Bull., 1984, 63, 797–802.17. Sordelet, D. and Akinc, M., Preparation of spherical, monosized Y2O3precursor particles. J. Colloid Interface Sci., 1988, 122, 47–59.18. Chen,P.L.and Ch en,I.W., Re a ctive c e riu m(IV)oxide po wd ers by the homo- geneous precipitation method. J. Am. Ceram. Soc.,1993, 76, 1577–1583.19. Sordelet, D. J., Akinc, M., Panchula, M. L., Han, Y. and Han, M. H., Synthesis of yttrium alu minu m garnet precursorpowders by homogeneous precipitation. J. Eur. Ceram. Soc., 1994, 14, 123–127.20. Khanlou, A. A., Tietz, F. and Sto¨ver, D., Material properties ofLa0.8Sr0.2Ga0.9+x Mg x O3−δas a function of Ga content. Solid State Ionic,2000, 135, 543–547.21. Gregg, S. J. and Sing, K. S. W., Adsorption, Surface Area and P orosity.Academic Press, 1982, p. 35.22. Gorelov, V. P., B ronin, D. I., Sokolova, J. V., Nafe, H. and Aldinger, F., The effect of doping and processingconditions on properties of La1−x Sr x Ga1−y M g y O3−δ. J. Eur. C eram. Soc., 2001, 21, 2311–2317.。
毕业设计外文资料翻译——翻译译文

毕业设计外文资料翻译(二)外文出处:Jules Houde 《Sustainable development slowed down by bad construction practices and natural and technological disasters》2、外文资料翻译译文混凝土结构的耐久性即使是工程师认为的最耐久和最合理的混凝土材料,在一定的条件下,混凝土也会由于开裂、钢筋锈蚀、化学侵蚀等一系列不利因素的影响而易受伤害。
近年来报道了各种关于混凝土结构耐久性不合格的例子。
尤其令人震惊的是混凝土的结构过早恶化的迹象越来越多。
每年为了维护混凝土的耐久性,其成本不断增加。
根据最近在国内和国际中的调查揭示,这些成本在八十年代间翻了一番,并将会在九十年代变成三倍。
越来越多的混凝土结构耐久性不合格的案例使从事混凝土行业的商家措手不及。
混凝土结构不仅代表了社会的巨大投资,也代表了如果耐久性问题不及时解决可能遇到的成本,更代表着,混凝土作为主要建筑材料,其耐久性问题可能导致的全球不公平竞争以及行业信誉等等问题。
因此,国际混凝土行业受到了强烈要求制定和实施合理的措施以解决当前耐久性问题的双重的挑战,即:找到有效措施来解决现有结构剩余寿命过早恶化的威胁。
纳入新的结构知识、经验和新的研究结果,以便监测结构耐久性,从而确保未来混凝土结构所需的服务性能。
所有参与规划、设计和施工过程的人,应该具有获得对可能恶化的过程和决定性影响参数的最低理解的可能性。
这种基本知识能力是要在正确的时间做出正确的决定,以确保混凝土结构耐久性要求的前提。
加固保护混凝土中的钢筋受到碱性的钝化层(pH值大于12.5)保护而阻止了锈蚀。
这种钝化层阻碍钢溶解。
因此,即使所有其它条件都满足(主要是氧气和水分),钢筋受到锈蚀也都是不可能的。
混凝土的碳化作用或是氯离子的活动可以降低局部面积或更大面积的pH值。
当加固层的pH值低于9或是氯化物含量超过一个临界值时,钝化层和防腐保护层就会失效,钢筋受腐蚀是可能的。
欧洲先进的土木工程复合材料外文资料翻译学士学位论文
毕业设计外文资料翻译题目欧洲先进的土木工程复合材料学院土木建筑学院 _____________专业土木工程 ________________班级土木1110 _______________学生_______ x xx ________________学号20110622132 ____________________指导教师_______ xxx _________________二O—五年三月九日Structural Engineering In ternatio nal ,1999,9.pp.267-273.ISSN 1016-8664欧洲先进的土木工程复合材料Chris J. Burg oyne 博士剑桥大学,剑桥,英国摘要:复合材料在欧洲被认为用于结构许多年了。
用于结构的材料都具有低蠕变的特点,这些结构被期望能够承受显著永久荷载。
较高刚度的纤维,即碳、芳族聚酰胺、玻璃和聚酯等材料在大多数的应用中被使用。
不幸的是,高强度是以高成本为代价的,人们在试图寻找钢材的一对一替代品的过程中在材料成本的基础上犯了错误。
成功的应用都使用其他合适的材料,其中最重要的是重量轻和顺向易于处理。
预应力玻璃纤维棒1978 年,一个预应力系统(称为Polystal[2])用玻璃纤维并掺入树脂形成圆棒。
进行了大量的研究确定系统的性能,包括量化的应力破坏现象。
锚具是用树脂包裹成束并挤压入钢管中形成的。
这种钢管提供约束限制和可用于机械紧固。
许多桥都用这种刚结束建造:在杜塞尔多夫,一个简单的人行桥是两跨连续结构,内部筋。
二者被认为具有相当数量的未受力筋被设计为部分预应力。
这些例子紧随其后的是柏林的体外预应力筋还有德国和奥地利的一些地方。
尽管该系统技术成功还没有被认为是商业成功,但是这种钢筋已经停产。
预应力芳纶棒在20世纪80年代早期的研究开始于荷兰使用芳族聚酰胺纤维预应力挤压成型的形式,无论平条或圆棒全都命名为Arapree [3]。
复合材料与工程英语介绍范文
复合材料与工程英语介绍范文英文回答:Composite Materials in Engineering: A Comprehensive Overview.Introduction.Composite materials, often referred to as advanced materials, are gaining significant prominence in various engineering applications due to their unique combination of properties. These materials comprise two or more distinct phases or constituents, typically a reinforcing phase and a matrix phase. The reinforcing phase provides strength and stiffness, while the matrix phase holds the reinforcement together and transfers loads.Types and Properties.Composite materials encompass a wide range ofcombinations, with the most common types being fiber-reinforced composites, laminated composites, and polymer-matrix composites (PMCs). Fiber-reinforced composites, such as carbon fiber reinforced polymers (CFRPs), offer exceptional strength-to-weight ratios, stiffness, and thermal stability. Laminated composites, like fiberglass composites, combine multiple layers of material with different orientations, providing tailored mechanical and thermal properties. PMCs, such as glass-reinforced plastics (GRPs), exhibit high strength and durability, along with ease of fabrication.Applications.The versatility of composite materials has led to their adoption in numerous engineering sectors. In the aerospace industry, composites are prized for their lightweight and high strength-to-weight ratios, enabling the construction of lighter and more fuel-efficient aircraft. In the automotive industry, composites find applications in body panels, chassis components, and interior trims, offering improved strength, weight reduction, and corrosionresistance. In the construction industry, composites are used for structural elements such as beams, columns, and panels, providing superior strength, durability, andweather resistance.Advantages.Composite materials offer several advantages over traditional materials. Their high strength-to-weight ratio makes them lightweight and strong, allowing for efficient load-bearing applications. They possess excellent corrosion resistance, reducing the need for protective coatings and enhancing durability in harsh environments. Additionally, composites exhibit tailored mechanical and thermal properties, allowing engineers to optimize them forspecific applications.Challenges.Despite their numerous advantages, composite materials also face some challenges. One challenge lies in their cost, as they are typically more expensive to produce thantraditional materials. Another challenge is the difficultyin fabrication, as the manufacturing processes for composites require specialized equipment and expertise. Furthermore, the repair of composite structures can be complex and costly, necessitating advanced techniques and skilled technicians.Future Outlook.Composite materials continue to attract significant research and development efforts, driven by the demand for advanced and lightweight materials with tailored properties. Advancements in manufacturing technologies, such asadditive manufacturing and automated layup, are expected to reduce production costs and streamline fabrication. Additionally, the development of novel composite materials, including bio-based and self-healing composites, holds promise for sustainable and innovative applications.中文回答:复合材料在工程中的应用,全面综述。
复合材料英文文献
复合材料英文文献Composite materials are engineered to combine the best properties of different materials, creating a new material that is stronger, lighter, and more durable than its individual components.These innovative materials are widely used in various industries, from aerospace where they reduce weight and increase fuel efficiency, to construction where they enhance structural integrity and longevity.The versatility of composite materials lies in their ability to be tailored to specific applications. By varying the composition and arrangement of the constituent materials, engineers can optimize the material for strength, stiffness, or resistance to environmental factors.Recent advancements in nanotechnology have further expanded the capabilities of composites. The incorporation of nanomaterials into composite structures can significantly improve their mechanical and thermal properties.One of the key challenges in composite material research is the development of effective recycling strategies. As these materials become more prevalent, finding sustainable ways to reuse or recycle them will be crucial to minimize environmental impact.Educational institutions and industries alike are investing in research to explore new composite material applications. This includes everything from improving sports equipment to developing next-generation energy storage systems.In conclusion, composite materials represent asignificant leap forward in material science. Their unique properties and potential for customization make them indispensable in a wide range of applications, driving innovation and enhancing performance across multiple sectors.。
材料科学与工程专业英语第10章翻译
The word "ceramic" is derived from the Greek keramos, which means "potter's clay" or "pottery." Its origin is a Sanskrit term meaning "to burn." So the early Greeks used "keramous" when describing products obtained by heating clay-containing materials. The term has long included all products made from fired clay, for example, bricks, fireclay refractories, sanitaryware, and tableware.“陶瓷”这个词是来自希腊keramos,这意味着“陶土”或“陶”。
它的起源是梵文术语,意思是“燃烧”。
因此,早期的希腊人用“keramous”描述加热含粘土的物料获得的产品。
这个词早已包括所有陶土制成的产品,例如,砖,粘土质耐火材料,卫生洁具,餐具。
In 1822, refractory silica were first made. Although they contained no clay, the traditional ceramic process of shaping, drying, and firing was used to make them. So the term" ceramic," while retaining its original sense of a product made from clay, began to include other products made by the same manufacturing process. The field of ceramics (broader than the materials themselves) can be defined as the art and science of making and using solid articles that contain as their essential component a ceramic. This definition covers the purification of raw materials, the study and production of the chemical compounds concerned, their formation into components, and the study of structure, composition, and properties.1822年,耐火材料二氧化硅被首次提出。
- 1、下载文档前请自行甄别文档内容的完整性,平台不提供额外的编辑、内容补充、找答案等附加服务。
- 2、"仅部分预览"的文档,不可在线预览部分如存在完整性等问题,可反馈申请退款(可完整预览的文档不适用该条件!)。
- 3、如文档侵犯您的权益,请联系客服反馈,我们会尽快为您处理(人工客服工作时间:9:00-18:30)。
毕业设计外文资料翻译题目POLISHING OF CERAMIC TILES抛光瓷砖学院材料科学与工程专业复合材料与工程班级复材0802学生学号20080103114指导教师二〇一二年三月二十八日MATERIALS AND MANUFACTURING PROCESSES, 17(3), 401–413 (2002) POLISHING OF CERAMIC TILESC. Y. Wang,* X. Wei, and H. YuanInstitute of Manufacturing Technology, Guangdong University ofTechnology,Guangzhou 510090, P.R. ChinaABSTRACTGrinding and polishing are important steps in the production of decorative vitreous ceramic tiles. Different combinations of finishing wheels and polishing wheels are tested to optimize their selection. The results show that the surface glossiness depends not only on the surface quality before machining, but also on the characteristics of the ceramic tiles as well as the performance of grinding and polishing wheels. The performance of the polishing wheel is the key for a good final surface quality. The surface glossiness after finishing must be above 208 in order to get higher polishing quality because finishing will limit the maximum surface glossiness by polishing. The optimized combination of grinding and polishing wheels for all the steps will achieve shorter machining times and better surface quality. No obvious relationships are found between the hardness of ceramic tiles and surface quality or the wear of grinding wheels; therefore, the hardness of the ceramic tile cannot be used for evaluating its machinability.Key Words: Ceramic tiles; Grinding wheel; Polishing wheelINTRODUCTIONCeramic tiles are the common decoration material for floors and walls of hotel, office, and family buildings. Nowadays, polished vitreous ceramic tiles are more popular as decoration material than general vitreous ceramic tiles as they can *Corresponding author. E-mail: cywang@401Copyright q 2002 by Marcel Dekker, Inc. have a beautiful gloss on different colors. Grinding and polishing of ceramic tiles play an important role in the surface quality, cost, and productivity of ceramic tiles manufactured for decoration. The grinding and polishing of ceramic tiles are carried out in one pass through polishing production line with many different grinding wheels or by multi passes on a polishing machine, where different grinding wheels are used.Most factories utilize the grinding methods similar to those used for stone machining although the machining of stone is different from that of ceramic tiles. Vitreous ceramic tiles are thin, usually 5–8mm in thickness, and are a sintered material,which possess high hardness, wear resistance, and brittleness. In general, the sintering process causes surface deformation in the tiles. In themachining process, the ceramic tiles are unfixed and put on tables. These characteristics will cause easy breakage and lower surface quality if grinding wheel or grinding parameters are unsuitable. To meet the needs of ceramic tiles machining, the machinery, grinding parameters (pressure, feed speed, etc.), and grinding wheels (type and mesh size of abrasive, bond, structure of grinding wheel, etc.) must be optimized. Previous works have been reported in the field of grinding ceramic and stone[1 –4]. Only a few reports have mentioned ceramic tile machining[5 –8], where the grinding mechanism of ceramic tiles by scratching and grinding was studied. It was pointed out that the grinding mechanism of ceramic tiles is similar to that of other brittle materials. For vitreous ceramic tiles, removing the plastic deformation grooves, craters (pores), and cracks are of major concern, which depends on the micro-structure of the ceramic tile, the choice of grinding wheel and processing parameters, etc. The residual cracks generated during sintering and rough grinding processes, as well as thermal impact cracks caused by the transformation of quartz crystalline phases are the main reasons of tile breakage during processing. Surface roughness Ra and glossiness are different measurements of the surface quality. It is suggested that the surface roughness can be used to control the surface quality of rough grinding and semi-finish grinding processes, and the surface glossiness to assess the quality of finishing and polishing processes. The characteristics of thegrinding wheels, abrasive mesh size for the different machining steps, machining time, pressure, feed, and removing traces of grinding wheels will affect the processing of ceramic tiles[9].In this paper, based on the study of grinding mechanisms of ceramic tiles, the manufacturing of grinding wheels is discussed. The actions and optimization of grinding and polishing wheels for each step are studied in particular for manualpolishing machines.GRINDING AND POLISHING WHEELS FOR CERAMIC TILEMACHININGT he mac hi ni ng of cer ami c t i l e s i s a vol ume-pr oduc t i on pr oc e s s t ha t uses significant numbers of grinding wheels. The grinding and polishing wheels forceramic tile machining are different from those for metals or structural ceramics. In this part, some results about grinding and polishing wheels are introduced for better understanding of the processing of ceramic tiles.Grinding and Polishing WheelsCeramic tiles machining in a manual-polishing machine can be divided into four steps—each using different grinding wheels. Grinding wheels are marked as 2#, 3#, and 4# grinding wheels, and 0# polishing wheel; in practice, 2# and 3# grinding wheels are used for flattening uneven surfaces. Basic requirements of rough grinding wheels are long life, high removal rate, and lower price. For 2# and 3# gr inding wheel s, Si C a brasi ve s wi th me s h #180 (#320)a r e bonde d by m a g n e s i u m o x yc h l o r i d e c e m e n t(M O C)t o g e t h e r w i t h s o m e p o r o u s f i l l s, waterproof additive, etc. The MOC is used as a bond because of its low price, simple manufacturing process, and proper performance.T he 4# grinding wheel will refine the surface to show the brightness of ceramic tile. The GC#600 abrasives and some special polishingmaterials, etc., are bonded by MOC. In order to increase the performance such as elasticity, etc., of the grinding wheel, the bakelite is always added. The 4# grinding wheels must be able to rapidly eliminate all cutting grooves and increase the surface glossiness of the ceramic tiles. The 0# polishing wheel is used for obtaining final surface glossiness, whichis made of fine Al2O3 abrasives and fill. It is bonded by unsaturated resin. The polishing wheels must be able to increase surface glossiness quickly and make the glossy ceramic tile surface permanent.Manufacturing of Magnesium Oxychloride Cement Grinding WheelsAfter the abrasives, the fills and the bond MOC are mixed and poured into the models for grinding wheels, where the chemical reaction of MOC will solidify the shape of the grinding wheels. The reaction will stop after 30 days but the hardness of grinding wheel is essentially constant after 15 days. During the initial 15-day period, the grinding wheels must be maintained at a suitable humidity and temperature.For MOC grinding wheels, the structure of grinding wheel, the quality of abrasives, and the composition of fill will affe ct their grinding ability. All the factors related to the chemical reaction of MOC, such as the mole ratio of MgO/MgCl2, the specific gravity of MgCl2, the temperature and humidity to care the cement will also affect the performance of the MOC grinding wheels.Mole Ratio of MgO/MgCl2When MOC is used as the bond for the grinding wheels, hydration reaction takes place between active MgO and MgCl2, which generates a hard XMg e OH T2·Y e MgCl2T·ZH2O phase. Through proper control of the mole ratio of MgO/MgCl2, a reaction product with stable performance is formed. The bond is composed of 5Mg e OH T2·e MgCl2T·8H2O and 3Mg e OH T2·e MgCl2T·8H2O: As the former is more stable, optimization of the mole ratio of MgO/MgCl2 to produce more 5Mg e OH T2·e MgCl2T·8H2O is required. In general, the ideal range for the mole ratio of MgO/MgCl2 is 4–6. When the contents of the active MgO and MgCl2 are known, the quantified MgO and MgCl2 can be calculated.Active MgOThe content of active MgO must be controlled carefully so that hydration reaction can be successfully completed with more 5Mg e OH T2·e MgCl2T·8H2O: If the content of active MgO is too high, the hydration reaction time will be too short with a large reaction heat, which increases too quickly. The concentrations of the thermal stress can cause generation of cracks in the grinding wheel. On thecontrary, if the content of active MgO is too low, the reaction does not go to completion and the strength of the grinding wheel is decreased.Fills and AdditivesThe fills and additives play an important role in grinding wheels. Some porous fills must be added to 2# and 3# grinding wheels in order to improve the capacity to contain the grinding chips, and hold sufficient cutting grit. Waterproof additives such as sulfates can ensure the strength of grinding wheels in processing under water condition. Some fills are very effective in increasing the surface quality of ceramic tile, but the principle is not clear.Manufacturing of Polishing WheelsFine Al2O3 and some soft polishing materials, such as Fe2O3, Cr2O3, etc., are mixed together with fills. Unsaturated resin is used to bond these powders, where a chemical reaction takes place between the resin and the hardener by means of an activator. The performance of polishing wheels depends on the properties of resin and the composition of the polishing wheel. In order to contain the fine chips, which are generated by micro-cutting, some cheap soluble salt can be fed into the coolant. On the surface of the polishing wheel, the salt will leave uniform pores, which not only increase the capacity to contain chips and self-sharpening of the polishing wheel, but also improves the contact situation between polishing wheel and ceramic tiles.Experimental ProcedureTests were carried out in a special manual grinding machine for ceramictiles. Two grinding wheels were fixed in the grinding disc that was equipped to the grinding machine. The diameter of grinding disc was 255 mm. The rotating speed of the grinding disc was 580 rpm. The grinding and polishing wheels are isosceles trapezoid with surface area 31.5 cm2 (the upper edge: 2 cm, base edge: 5 cm, height: 9 cm). The pressure was adjusted by means of the load on the handle for different grinding procedures. A zigzag path was used as the moving trace for the grinding disc. To maintain flatness and edge of the ceramic tiles, at least one third of the tile must be under the grinding disc. During the grinding process, sufficient water was poured to both cool and wash the grinding wheels and the tiles. Four kinds of vitreous ceramic tiles were examined, as shown in Table 1.Two different sizes of ceramic A, A400 (size: 400 £400 £5mm3T and A500(size: 500 £500 £5mm3T were tested to understand the effect of the tile size. Forceramic tile B or C, the size was 500 £500 £5mm3: The phase composition of thetiles was determined by x-ray diffraction technique. Surface reflection glossiness and surface roughness of the ceramic tiles and the wear of grinding wheels were measured.The grinding and polishing wheels were made in-house. The 2# grindingwheels with abrasives of mesh #150 and 3# grinding wheels with mesh #320 were used during rough grinding. Using the ceramic tiles with different surface toughness ground by the 2# grinding wheel for 180 sec, the action of the 3# grinding wheels were tested. The ceramic tile was marked as A500-1 (or B500-1, C500-1, A400-1) with higher initial surface toughness or A500-2 (or B500-2, C500-2, A400-2) with lower initial surface toughness.Two kinds of finishing wheels, 4#A and 4#B were made with the same structure, abrasivity, and process, but different composition of fills and additives. Only in 4#B, a few Al2O3, barium sulfate, and magnesium stearate were added for higher surface glossiness. The composition of the polishing wheels 0#A and 0#B were different as well. In 0#B, a few white alundum (average diameter 1mm), barium sulfate, and chrome oxide were used as polishing additives, specially. After ground by 4#A (or 4#B) grinding wheel, the ceramic tiles were polished with 0#A (or 0#B). The processing combinations with 4# grinding wheels and 0#RESULTS AND DISCUSSIONSEffects of 2# and 3# Grinding WheelsSurface QualityIn rough grinding with a 2# grinding wheel, the surface roughness for all the tiles asymptotically decreases as the grinding time increases, see Fig. 1. The initial asymptote point of this curve represents the optimized rough grinding time, as continued grinding essentially has no effect on the surface roughness. In these tests, the surface roughness curves decrease with grindingtime and become smooth at ,120 sec. The final surface quality for different kinds of ceramic tiles is slightly different. In terms of the initial size of the tile, the surface roughness of ceramic tile A400 e £400 £5mm3T is lower than that of A500 e500 £500 £5mm3T: The surface roughness ofc e r a m i c t i l e B500r a p id l y d r o p s a s t he g r i n d i n g t i m e i n c r e a s e s.Thus, it is easier to remove surface material from the hardest of thethree kinds of the ceramic tiles (Table 1). However, as the final surface roughness of ceramic tile A500 is the same as that of ceramic tile C500, the hardness of theceramic tile does not have a direct relationship with the final surface quality.In the 3# grinding wheel step, all craters and cracks on the surface of ceramic tiles caused by the 2# grinding wheel must be removed. If residual cracks and craters exist, it will be impossible to get a high surface quality in the next step. The surface roughness obtained by the 2# grinding wheel willalso affect the surfaceFigure 1. Surface roughness of several ceramic tiles as a function of grinding time for 2# grindingwheel.quality of next grinding step by the 3# grinding wheel. In Fig. 2, the actions of the 3# grinding wheels are given using the ceramic tiles with different initial R a, which were ground by the 2# grinding wheel for 180 sec. The curves of surface vs. grinding time rapidly decrease in 60 sec. Asymptotic behavior essentially becomes constant after 60 sec. In general, the larger the initial surface roughness, the worse the final surface roughness. For example, for ceramic tile B500-1, the initial R a was 1.53mm, the finial R a was 0.59mm after being ground by the 3# grinding wheel. When the initial R a was 2.06mm for ceramic tile B500-2, the finial R a was 0.67mm. In Ref. [8], we studied the relations between abrasive mesh size and evaluation indices of surface quality, such as surface roughness and surface glossiness. In rough grinding, the ground surface of ceramic tile shows fracture craters. These craters scatter the light, so that the surface glossiness values are almost constant at a low level. It is difficult to improve the surface glossiness after these steps. Figure 3 shows the slow increase in surface glossiness with time by means of the 3# grinding wheel. It can be seen that the glossiness of ceramic tile B500-1 is the highest. The surface glossiness of ceramic tile A400-1 is better than that of A500-1 because the effective grinding times per unit area for former is longer than for latter. These trends are similar to those for surface r o u g h n e s s i nFig. 2.Wear of Grinding WheelsThe wear of grinding wheels is one of the factors controlling the machining cost. As shown in Fig.4, the wear of grinding wheels is proportional to grindingFigure 2. Surface roughness of several ceramic tiles as a function of grinding time for 3# grindingwheel.Figure 3. Surface glossiness of several ceramic tiles as a function of grinding time by 3# grindingwheel.time for both the grinding wheels and the three types of ceramic tiles. The wear rate of the 3# grinding wheel is larger than the 2# grinding wheel. It implies that the wear resistance of the 3# grinding wheel is not as good as 2# for constant grinding time of 180 sec. When the slope of thecurve is smaller, life of thegrinding wheels will be longer. Comparison of the ceramic tiles hardness (Table 1) with the wear resistance behavior in Fig. 4 does not reveal a strong dependency. Therefore, the hardness of the ceramic tile cannot be used to distinguish the machinability. The difference ofFigure 4. Wear of grinding wheels of several ceramic tiles as a function of grinding time for 2# and3# grinding wheels.initial surface roughness of ceramic tile will affect the wear of grinding wheel. In Fig. 4, the wear of the 3# grinding wheel for ceramic tile B500-1 is smaller than that for ceramic tile B500-2. The initial surface roughness of the latter is higher than that of the former so that additional grinding time is required to remove the deeper residual craters on the surface. Improvement of the initial surface roughness can be the principal method for obtaining better grinding quality and grinding wheel life during rough grinding.Effects of 4# Grinding Wheels and 0# Polishing WheelsSurface QualityThe combination and the performance of 4# grinding and 0# polishingwheels show different results for each ceramic tile. The grinding quality vs. grinding (polishing) time curves are presented in Fig. 5, where all the ceramic tiles were previously ground by 2# and 3# grinding wheels to the same surface quality.The surface glossiness is used to assess surface quality because the surface roughness is nearly constant as finishing or polishing time increases[8]. In this test, the ceramic tile A400 were fast ground by 4#A and 4#B grinding wheels [Fig. 5(a)]. The surface glossiness increased rapidly during the initial 90 sec and then slowly increased. The surface glossiness by grinding wheel 4#B is higher than by 4#A. Afterwards, polishing was done by four different combinations of finishing wheel and polishing wheel. By means of polishing wheels 0#A and 0#B, we processed the surface finished by 4#A grinding wheel (described as 4#A–0#A and 4#A–0#B in Fig. 5), and the surfacef i n i s h e d b y4#Bg r i n d i n g wh e e l (described as 4#B–0#A and 4#B–0#B in Fig. 5). The curves of surface glossiness vs. polishing timeshow parabolic behavior. After 60 sec of polishing, the surface glossiness reaches to ,508, then slowly increases. The polishing wheel 0#B gives a better surface quality than 0#A.In Fig. 5(a), the maximum surface glossiness of ceramic tile A400 is about ,75 by 4#B–0#B.The relation between initial surface glossiness and the final surface quality is not strong. The effect of pre-polishing surface glossiness can be observed by 0#B polishing wheel as polishing ceramictile A500 [Fig. 5(b)]. The maximum surface glossiness that can be achieved is 748 in 240 sec by4#A–0#B or 4#B–0#B. This value is lower than that of ceramic tile A400 [Fig. 5(a)].The final surface glossiness by 4#A grinding wheel is highly different from that by 4#B grinding wheel for ceramic tile B500, as shown in Fig. 5(c), but the final polishing roughness is the same when 0#A polishing wheel is used. The better performance of 0#B polishing wheel is shown because the surface glossiness canincrease from 17 to 228 in 30 sec. The maximum surface glossiness is 658 by 4#B–0#B. Thecurves of polishing time vs. surface glossiness in Fig. 5(d) present the same results as polishing of ceramic tile B500 [Fig. 5(c)]. With 0#A polishingFigure 5. Surface glossiness for ceramic tiles (a) A400, (b) A500, (c) B500, and (d) C500 as afunction of grinding (polishing) time for 4# grinding wheels and 0# polishing wheels.wheel, the action of pre-polishing surface glossiness is significant. The best value of surface glossiness in 240 sec is 708 by 4#B–0#B as polishing ceramic tile C500. The results discussed earlier describe that the surface glossiness by 0# polishing wheel will depend not only on the pre-polishing surface glossiness formed by 4# grinding wheel, but also on the characteristics of the ceramic tiles and the performance of 0# polishing wheel. The differences of initial surface glossiness and final surface glossiness are larger for 4#A and 4#B. If the prepolishing surfaceroughness is lower, the final surface glossiness will be higher.Figure 5. Continued.The polishing time taken to achieve the maximum surface glossiness will be also shorter. The initial surface quality will limit the maximum value of polishing surface glossiness that can be obtained. To reach a final surface glossiness of above 608, the minimum pre-polishing surface glossiness must be above 208.The performance of the polishing wheel is the key to good surface quality. The polishing ability of the polishing wheels depends on the properties of the ceramic tiles as well. Even if the same grinding and polishing wheels are used, on all four ceramic tiles, the maximum surface glossiness values of ceramic tiles are different. The ceramic tile A500 shows the best surface glossiness, and ceramictile B500 shows the worst, although it is easier to roughly grind ceramic tile B500. The peak valueof the surface glossiness is also limited by the properties ofWear of Grinding and Polishing WheelsThe life of 4# grinding wheels and 0# polishing wheels (Fig. 6) are longer than those of the rough grinding wheels (Fig. 4). For finer grinding (Fig. 6), it is impossible to distinguish the relation between grinding wheels and ceramic tiles. Polishing wheels have longer life because they produce more plastic deformation than removal.SUMMARY OF RESULTS(1) The performance of grinding and polishing wheels will affect its life and the surface quality of ceramic tiles.(2) In ceramic tile machining, the surface quality gained in the previous step will limit the final surface quality in the next step. The surface glossiness of pre-polishing must be higher than 208 inorder to get the highest polishing quality. The optimization of the combination of grinding wheels and polishing wheels for all the steps will shorten machining time and improve surface quality. Optimization must be determined for each ceramics tiles.Figure 6. Wear of grinding wheels 4# and polishing wheels 0# for several ceramic tiles as afunction of grinding time.(3) The effect of hardness of ceramic tiles is not direct, thus the hardness of ceramic tiles cannot be used for evaluating the machinability ofACKNOWLEDGMENTThe authors thank Nature Science Foundation of Guangdong Province and Science Foundation of Guangdong High Education for their financial support.REFERENCES1. Wang, C.Y.; Liu, P.D.; Chen, P.Y. Grinding Mechanism of Marble. AbrasivesGrinding 1987, 2 (38), 6–10, (in Chinese).2. Inasaki, I. Grinding of Hard and Brittle Materials. Annals of the CIRP 1987, 36 (2),463–471.3. Zhang, B.; Howes, D. Material Removal Mechanisms in Grinding Ceramics. Annalsof the CIRP 1994, 45 (1), 263–266.4. Malkin, S.; Hwang, T.W. Grinding Mechanism for Ceramics. Annals of the CIRP1996, 46 (2), 569–580.5. Black, I. Laser Cutting Decorative Glass, Ceramic Tile. Am. Ceram. Soc. Bull. 1998,77 (9), 53–57.6. Black, I.; Livingstone, S.A.J.; Chua, K.L. A Laser Beam Machining (LBM) Database for the Cutting of Ceramic Tile. J. Mater. Process. Technol. 1998, 84 (1–3), 47–55.7. Jiang, D.F. Mirror Surface Polishing of Ceramic Tile. New Building Mater. 1994, 20(11), 27–30, (in Chinese).8. Ma, J.F. Analysis on Man-Made Floor Brick and Manufacture of Grinding SegmentUsed for Floor Brick. Diamond Abrasive Eng. 1996, 6 (95), 35–46, (in Chinese). 9. Wang, C.Y.; Wei, X.; Yuan, H. Grinding Mechanism of Vitreous Ceramic Tile. Chin.J. Mech. Eng. 1998, 9 (8), 9–11, 46 (in Chinese).材料与制造工艺17(3), 401–413 (2002)抛光瓷砖王CY,* 魏X, 袁H制造技术研究所,广东工业大学科技,广州510090,中国P.R.摘要研磨和抛光,是装饰玻璃陶瓷砖的生产中的重要步骤。