230KA导流结构电解槽混合料焙烧启动操作规程1
焙烧炉操作规程课件
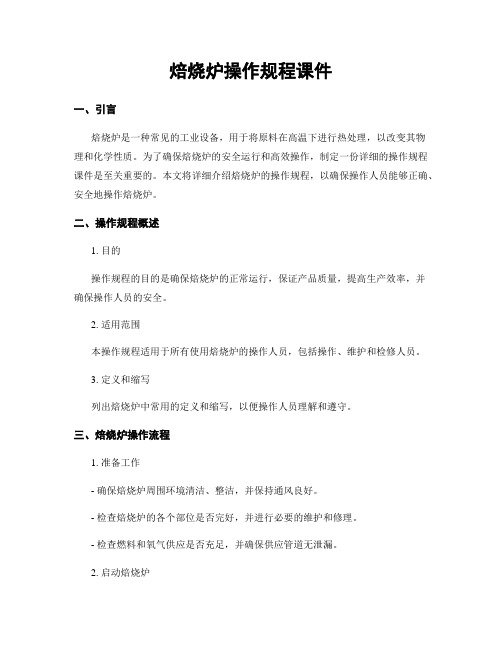
焙烧炉操作规程课件一、引言焙烧炉是一种常见的工业设备,用于将原料在高温下进行热处理,以改变其物理和化学性质。
为了确保焙烧炉的安全运行和高效操作,制定一份详细的操作规程课件是至关重要的。
本文将详细介绍焙烧炉的操作规程,以确保操作人员能够正确、安全地操作焙烧炉。
二、操作规程概述1. 目的操作规程的目的是确保焙烧炉的正常运行,保证产品质量,提高生产效率,并确保操作人员的安全。
2. 适用范围本操作规程适用于所有使用焙烧炉的操作人员,包括操作、维护和检修人员。
3. 定义和缩写列出焙烧炉中常用的定义和缩写,以便操作人员理解和遵守。
三、焙烧炉操作流程1. 准备工作- 确保焙烧炉周围环境清洁、整洁,并保持通风良好。
- 检查焙烧炉的各个部位是否完好,并进行必要的维护和修理。
- 检查燃料和氧气供应是否充足,并确保供应管道无泄漏。
2. 启动焙烧炉- 打开焙烧炉的主电源,并确保电压稳定。
- 按照操作面板上的指示,启动焙烧炉的主控制系统。
- 检查焙烧炉的各个传感器和仪表是否正常工作。
3. 加载原料- 根据生产计划和工艺要求,将待处理的原料准备好。
- 确保原料的质量和数量符合要求,并按照指定的方式将其装载到焙烧炉中。
4. 设置焙烧参数- 根据工艺要求,设置焙烧炉的温度、时间和其他相关参数。
- 在设置参数之前,确保操作人员已经了解和熟悉焙烧炉的控制系统和操作界面。
5. 启动焙烧过程- 按照操作面板上的指示,启动焙烧炉的加热系统和风机系统。
- 监控焙烧过程中的温度、压力和气体流量等参数,并及时调整控制系统以确保焙烧过程的稳定性。
6. 监控和记录- 持续监控焙烧炉的运行状态,包括温度、压力、气体流量和燃料消耗等。
- 定期记录焙烧过程中的关键参数,并进行必要的分析和比对。
7. 焙烧结束- 根据工艺要求和焙烧过程中的实际情况,判断焙烧是否已经完成。
- 在确认焙烧结束后,及时关闭焙烧炉的加热系统和风机系统,并将焙烧炉冷却至安全温度。
8. 清理和维护- 在焙烧结束后,及时清理焙烧炉的残留物和灰尘,并进行必要的维护和保养。
焙烧操作规程

13如果天车有异常现象本班未处理或未处理完,要做好记录,同时交班时必须向接班人员交待清楚。
14定期对天车各部位进行检查、维护、润滑,按国家有关规定进行起重设备管理。
第三章 编组站
3.1 编组的目的
按照一定标准通过炭块编组机使生阳极有序排列,以满足焙烧炉装炉的工艺要求。
天车的润滑系统分以下几个部分:集中润滑系统、外配套件的润滑和各单点润滑。
电动集中润滑系统的润滑点包括:平衡轮、定滑轮组。
外配套件的润滑详见其产品使用说明书。
其它各润滑点如大车车轮、大车水平轮、卷筒轴承座等处采用压注式油杯润滑,可定期或不定期加油。
2.3.1.8电控系统
电控系统包括配电系统、PLC控制系统、变频器、操作系统、保护系统、电控柜、电缆等。
4台
熟阳极炭块入库
运输机
BSL-00
L=16.5米;
运行速度:7.8m/min;
外形:16500×1800×770(L×W×H);
3台
熟阳极炭块出库
2.2炭块库工艺流程简图
合格生阳极炭块(来自成型)合格熟阳极炭块(入组装浇铸)
生阳极炭块(入焙烧装炉)合格熟阳极炭块(来自焙烧)
图1炭块库工艺流程简图
碳块库作为生、熟阳极碳块的储存和中转站,配合成型、焙烧、组装车间,使各车间的生产相对独立而又互相联系,是一个非常重要的生产环节。由堆垛天车和库内运输机共同完成来自成型车间的生阳极炭块的入库、焙烧装炉生阳极碳块的出库、来自焙烧合格和废熟阳极炭块的入库、组装浇铸熟阳极碳块的出库、废阳极生、熟碳块的定期出库。
第一章 阳极焙烧工艺过程概述
成型分厂生产的生阳极炭块,存放于炭块库内。焙烧炉需要装炉时,用堆垛天车把21块为一组的生阳极炭块组吊运到链式输送机上,输送到焙烧厂房,经过炭块编组机编成7块一组,经多功能天车的夹运装入焙烧炉内,并装入填充料,由路面燃烧系统加热焙烧。
焙烧启动工艺技术标准
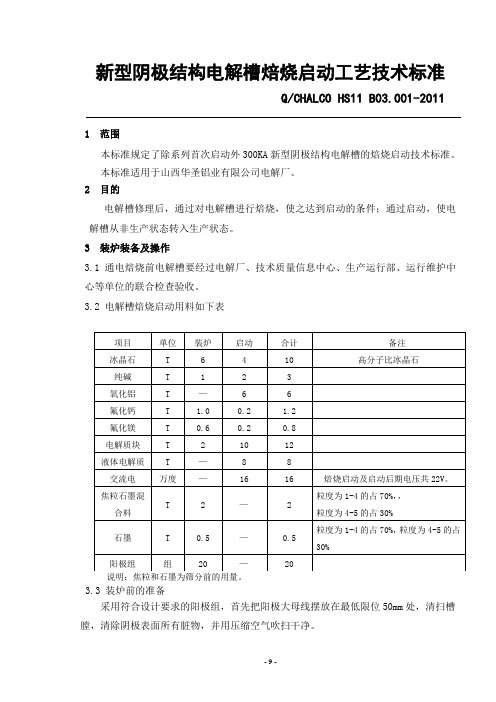
新型阴极结构电解槽焙烧启动工艺技术标准Q/CHALCO HS11 B03.001-20111 范围本标准规定了除系列首次启动外300KA新型阴极结构电解槽的焙烧启动技术标准。
本标准适用于山西华圣铝业有限公司电解厂。
2 目的电解槽修理后,通过对电解槽进行焙烧,使之达到启动的条件;通过启动,使电解槽从非生产状态转入生产状态。
3 装炉装备及操作3.1通电焙烧前电解槽要经过电解厂、技术质量信息中心、生产运行部、运行维护中心等单位的联合检查验收。
3.2 电解槽焙烧启动用料如下表说明:焦粒和石墨为筛分前的用量。
3.3 装炉前的准备采用符合设计要求的阳极组,首先把阳极大母线摆放在最低限位50mm处,清扫槽膛,清除阴极表面所有脏物,并用压缩空气吹扫干净。
3.4 铺设焦粒和挂极铺设前先用石墨将炉底找平,焦粒铺设及阳极的安放自A10、B10开始连续铺设至A1、B1结束,焦粒石墨混合料铺设厚度要求20-25mm,阳极与焦粒的压实面应大于80%,铝导杆和水平母线压接处的缝隙不大于6mm,安放阳极后用纸板封堵极间缝。
3.5 安放热电偶套管在A1-B1、A6-B6、A10-B10阳极中间对应的中缝处及A10、B10角部各装上一支热电偶保护管,热电偶套管斜放,下面封口不得与阴、阳极接触。
3.6 装炉在槽膛四周紧贴阳极的底掌边沿添加60-100mm冰晶石,在人造伸腿上均匀铺上1 T氟化钙,在氟化钙上均匀添加氟化镁0.6 T,紧靠阳极周边均匀添加纯碱1吨,在纯碱上装电解质块2T,要求紧靠侧砖,装到距槽上沿50mm,在电解质块上全部加冰晶石至满槽,阳极组表面冰晶石厚度不低于150mm,中缝添加100-150mm冰晶石,阳极中缝用不小于5mm厚的钢板盖严。
3.7 安装软连接器3.8 分流器的安装装炉结束后进行分流器的安装,末端槽采用钢带分流,钢带一端焊于阳极钢梁上,另一端焊于阴极钢棒处。
4 短路口操作及通电4.1 使用设备、工具、材料不停电开停槽装置、短路口绝缘板、绝缘套管、呆扳手、摇表工器具等。
电解槽焙烧启动标准

青海百河铝业公司240KA系列电解槽通电焙烧、启动操作标准生产技术部2015年3月3日240KA电解槽通电焙烧、启动操作标准- 3 -②铺设焦料:从A8、B8开始,在阳极正投影下方均匀铺设2cm厚焦粒至A1、B1,焦粒规格φ2mm-5mm;③铺设要求:将焦粒框平整地放在阳极组投影区域,然后将焦粒石墨粉混合料倒入框内,用刮尺沿着焦粒框的长度方向刮平。
2.安放阳极①安放阳极之前先检查阳极质量、检查阳极底掌是否平整有杂物,铝导杆是否与阳极垂直,磷生铁浇铸是否饱满,有无夹渣和裂纹等(质量不符合要求的阳极不准许装槽)。
②安放阳极要求a.将阳极坐在焦粒上的同时,检查其周边是否已与焦粒充分接触;如有明显未接触的地方,要重新安放或重铺焦粒再装阳极。
安放阳极时,大母线要与导杆接触面贴紧。
b.阳极挂好后,由专人负责检查软连接安装质量,并挂好小盒夹具。
③在阳极导杆与大母线下边沿对齐位置画好平行定位线。
3.安放热电偶套管①装炉前在人造伸腿下部预埋“6-11根热电偶套管”,便于测量焙烧期间温度;②要求热电偶套管要斜放,并放置到焦粒层,并用冰晶石固定,上口用纸塞住,但不能接触到阳极。
4.加原、辅料①用石棉板堵住阳极的上部及四周缝隙,防止物料漏入阳极底下或阳极缝隙内;②在槽膛靠近阳极的地方添加5—10cm厚的冰晶石约0.6吨;③在冰晶石的上面均匀撒一层氟化钙约1.5吨;④用φ80mm的电解质块3吨垒在人工炉帮上,要求大块在外,小块在里;⑤在电解质上均匀倒入约1吨纯碱;⑥在纯碱上用冰晶石填满槽膛四周和阳极碳块上表面,防止在焙烧过程中发生阳极氧化。
要求阳极和中缝较高而边部较低。
5.装分流器、软连接①将4组分流器一端装置在前一台已启动槽的阳极平衡母线上,并紧- 5 -逐步升电压到2.5V-2.8V,保持1小时,可以每1小时点动一次,保持电压为 2.5-3.0V。
如果电压升幅过大时,应立即停止点动抬阳极,并延迟下一次点动抬阳极的时间;③在点动抬阳极的过程中,炉前工要不断地将极上保温料推入中缝火眼处,来增加槽中电解质数量及保温措施。
230KA导流结构电解槽混合料焙烧启动操作规程1讲解
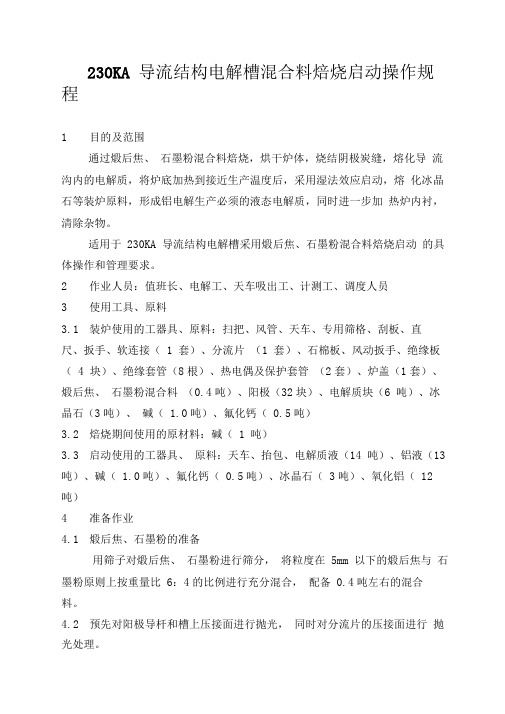
230KA 导流结构电解槽混合料焙烧启动操作规程1目的及范围通过煅后焦、石墨粉混合料焙烧,烘干炉体,烧结阴极炭缝,熔化导流沟内的电解质,将炉底加热到接近生产温度后,采用湿法效应启动,熔化冰晶石等装炉原料,形成铝电解生产必须的液态电解质,同时进一步加热炉内衬,清除杂物。
适用于230KA 导流结构电解槽采用煅后焦、石墨粉混合料焙烧启动的具体操作和管理要求。
2作业人员:值班长、电解工、天车吸出工、计测工、调度人员3使用工具、原料3.1装炉使用的工器具、原料:扫把、风管、天车、专用筛格、刮板、直尺、扳手、软连接(1 套)、分流片(1 套)、石棉板、风动扳手、绝缘板(4 块)、绝缘套管(8根)、热电偶及保护套管(2套)、炉盖(1套)、煅后焦、石墨粉混合料(0.4吨)、阳极(32块)、电解质块(6 吨)、冰晶石(3吨)、碱(1.0吨)、氟化钙(0.5吨)3.2焙烧期间使用的原材料:碱(1 吨)3.3启动使用的工器具、原料:天车、抬包、电解质液(14 吨)、铝液(13 吨)、碱(1.0吨)、氟化钙(0.5吨)、冰晶石(3吨)、氧化铝(12吨)4准备作业4.1煅后焦、石墨粉的准备用筛子对煅后焦、石墨粉进行筛分,将粒度在5mm 以下的煅后焦与石墨粉原则上按重量比6:4的比例进行充分混合,配备0.4吨左右的混合料。
4.2预先对阳极导杆和槽上压接面进行抛光,同时对分流片的压接面进行抛光处理。
4.3使用扫把等工具将电解槽阴极炭块表面清扫干净,再用风管将阴极表面吹干净。
4.4用冰晶石填充电解槽内的沟槽与阴极面平齐。
4.5铺设混合料、安装阳极4.5.1首先挂好A16处的阳极,确定阳极正投影位置,将专用筛格沿投影线摆好,要求筛格安放平整。
将混合料倒入筛格内,用刮板在筛格内来回刮混合料,使其沿筛眼漏至阴极面,待填满所有筛眼后,取出专用筛格。
沿阴极混合料处安放,在A、B两侧依次铺设混合料。
4.5.2铺设混合料后,安装阳极,装好卡具,但不拧紧,使阳极完全靠自重与混合料接触。
焙烧启动电解槽技术
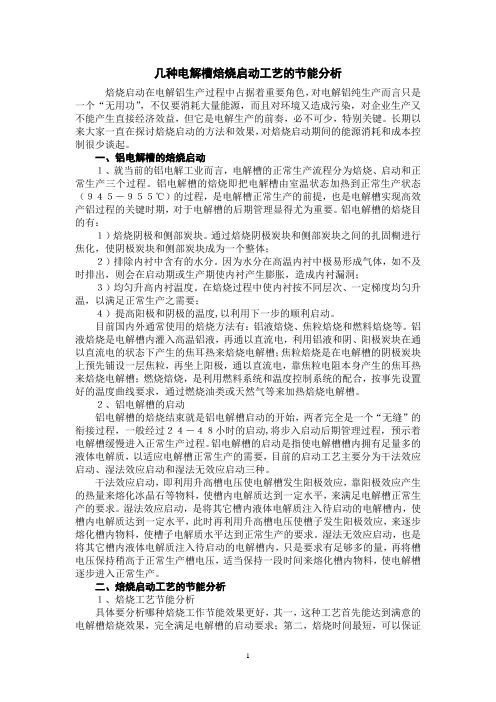
几种电解槽焙烧启动工艺的节能分析焙烧启动在电解铝生产过程中占据着重要角色,对电解铝纯生产而言只是一个“无用功”,不仅要消耗大量能源,而且对环境又造成污染,对企业生产又不能产生直接经济效益,但它是电解生产的前奏,必不可少,特别关键。
长期以来大家一直在探讨焙烧启动的方法和效果,对焙烧启动期间的能源消耗和成本控制很少谈起。
一、铝电解槽的焙烧启动1、就当前的铝电解工业而言,电解槽的正常生产流程分为焙烧、启动和正常生产三个过程。
铝电解槽的焙烧即把电解槽由室温状态加热到正常生产状态(945-955℃)的过程,是电解槽正常生产的前提,也是电解槽实现高效产铝过程的关键时期,对于电解槽的后期管理显得尤为重要。
铝电解槽的焙烧目的有:1)焙烧阴极和侧部炭块。
通过焙烧阴极炭块和侧部炭块之间的扎固糊进行焦化,使阴极炭块和侧部炭块成为一个整体;2)排除内衬中含有的水分。
因为水分在高温内衬中极易形成气体,如不及时排出,则会在启动期或生产期使内衬产生膨胀,造成内衬漏洞;3)均匀升高内衬温度。
在焙烧过程中使内衬按不同层次、一定梯度均匀升温,以满足正常生产之需要;4)提高阳极和阴极的温度,以利用下一步的顺利启动。
目前国内外通常使用的焙烧方法有:铝液焙烧、焦粒焙烧和燃料焙烧等。
铝液焙烧是电解槽内灌入高温铝液,再通以直流电,利用铝液和阴、阳极炭块在通以直流电的状态下产生的焦耳热来焙烧电解槽;焦粒焙烧是在电解槽的阴极炭块上预先铺设一层焦粒,再坐上阳极,通以直流电,靠焦粒电阻本身产生的焦耳热来焙烧电解槽;燃烧焙烧,是利用燃料系统和温度控制系统的配合,按事先设置好的温度曲线要求,通过燃烧油类或天然气等来加热焙烧电解槽。
2、铝电解槽的启动铝电解槽的焙烧结束就是铝电解槽启动的开始,两者完全是一个“无缝”的衔接过程,一般经过24-48小时的启动,将步入启动后期管理过程,预示着电解槽缓慢进入正常生产过程。
铝电解槽的启动是指使电解槽槽内拥有足量多的液体电解质,以适应电解槽正常生产的需要,目前的启动工艺主要分为干法效应启动、湿法效应启动和湿法无效应启动三种。
2-4电解槽焙烧与启动
三、铝电解槽非正常期生产管理
• 电解槽启动后24小时即可灌铝,灌铝后的电解槽即进入启动后期。 • 目的: • 这期间电解槽将逐渐转入正常运行: • 一是各项技术条件逐步过渡到正常生产控制范围; • 二是形成一定的槽膛内型; • 三是能量平衡、物料平衡逐渐建立、稳定。
• 当这些变化完成之后,电解槽即进入了正常。
一、目的和方法
• 电解槽预热焙烧的目的: • 1)加热并焙烧阴极 。提高阴极温度,对阴极碳块间缝和槽周边的扎
糊进行烧结焦化,以形成密实的炭素槽膛。 • 2)烘干电解槽内衬材料。通过一定时间的缓慢加热,以排除槽体内耐
火材料、保温材料、浇注材料等砌体的水分。 • 3)提高槽膛温度。使阴、阳极温度接近或达到电解槽生产温度,以能
天,低效高耗。
一、目的和方法
• 焦粒焙烧法: • 在阴、阳极之间铺上一层煅烧过的焦炭颗粒,其厚度为15一20mm 。焦粒粒
度在1一4mm之间。电解槽通电后,焦粒层作为电阻体在阴、阳极之间产生焦 耳热来预热电解槽,同时,阴极和阳极本身的电阻也产生热量,在其内部预 热。因阳极碳块直接坐在焦粒层上,为解决预热过程中产生的热应力,阳极 导杆与阳极母线之间用临时导电软母线联接,因为这种软连接可以使阳极碳 块有一定的活动自由度,以释放在焙烧时焦粒上抬的膨胀力,并使阳极重量 能全部压实在焦粒上,保证阳极与焦粒良好接触, 以获得均匀的阴阳极电流 分布。在启动前拆除临时导电软母线。
过快。
一、目的和方法
• 燃料预热法 • 加热采用燃烧喷嘴喷射火焰,在阳极上面加盖保温罩,使高温气体停留在
槽内,并防止冷空气窜入。火焰在阴`阳极之间燃烧,依靠传导、对流和 辐射,将热量传输到其他部位。 • 此法的最大优点为升温快,可以控制加热速度,使阴极表面均匀受 热,节省电能。 • 其缺点是操作比较复杂,只能控制表面温度,内部温度靠热传导, 温差较大,火焰燃烧时易使阴极和阳极表面烧损。
电解槽启动操作规程
电解槽启动操作规程
《电解槽启动操作规程》
电解槽是用于电解金属的重要设备,在启动操作过程中需要按照规程进行操作,以确保安全和高效运行。
以下是电解槽启动操作规程的主要内容:
1. 确保设备完好:在启动操作前,需要对电解槽及相关设备进行检查,确保各项设备完好无损,不存在故障或漏电的情况。
2. 准备电解液:根据工艺要求,准备适量的电解液,并确保电解槽内的电解液浓度和温度符合工艺要求。
3. 打开电源:在确认设备完好且电解液准备就绪后,可以打开电源,对电解槽进行通电操作。
4. 控制电流:启动操作后,需要逐步增加电流,控制电解过程的进行,确保电解槽内的电流与工艺要求相符。
5. 监测运行情况:在启动操作过程中,需要持续监测电解槽运行情况,注意观察电解液的浓度、温度和电流等参数,及时发现并解决异常情况。
6. 完善记录:启动操作结束后,需要完善电解槽的操作记录,包括启动时间、电解液参数、电流变化等,以便于后续的运行管理和维护。
以上是关于电解槽启动操作规程的主要内容,通过严格按照规程操作,可以确保电解槽的安全、稳定和高效运行。
电解槽焙烧启动标准
青海百河铝业公司240KA系列电解槽通电焙烧、启动操作标准生产技术部2015年3月3日240KA电解槽通电焙烧、启动操作标准③铺设要求:将焦粒框平整地放在阳极组投影区域,然后将焦粒石墨粉混合料倒入框内,用刮尺沿着焦粒框的长度方向刮平。
2.安放阳极①安放阳极之前先检查阳极质量、检查阳极底掌是否平整有杂物,铝导杆是否与阳极垂直,磷生铁浇铸是否饱满,有无夹渣和裂纹等(质量不符合要求的阳极不准许装槽)。
②安放阳极要求a.将阳极坐在焦粒上的同时,检查其周边是否已与焦粒充分接触;如有明显未接触的地方,要重新安放或重铺焦粒再装阳极。
安放阳极时,大母线要与导杆接触面贴紧。
b.阳极挂好后,由专人负责检查软连接安装质量,并挂好小盒夹具。
③在阳极导杆与大母线下边沿对齐位置画好平行定位线。
3.安放热电偶套管①装炉前在人造伸腿下部预埋“6-11根热电偶套管”,便于测量焙烧期间温度;②要求热电偶套管要斜放,并放置到焦粒层,并用冰晶石固定,上口用纸塞住,但不能接触到阳极。
4.加原、辅料①用石棉板堵住阳极的上部及四周缝隙,防止物料漏入阳极底下或阳极缝隙内;②在槽膛靠近阳极的地方添加5—10cm厚的冰晶石约0.6吨;③在冰晶石的上面均匀撒一层氟化钙约1.5吨;④用φ80mm的电解质块3吨垒在人工炉帮上,要求大块在外,小块在里;⑤在电解质上均匀倒入约1吨纯碱;⑥在纯碱上用冰晶石填满槽膛四周和阳极碳块上表面,防止在焙烧过程中发生阳极氧化。
要求阳极和中缝较高而边部较低。
5.装分流器、软连接①将4组分流器一端装置在前一台已启动槽的阳极平衡母线上,并紧螺丝,另一端卡在要启动槽立柱母线上卡紧,连接方式采用压板连接,紧固好螺丝,再次复紧;眼处,来增加槽中电解质数量及保温措施。
7.干法无效应启动①随着物料的加入和不断的熔化,可逐渐将电压提升到6.0—8.0V(以不发生效应为准)。
待物料全部融化后,电解质高度达到26~30cm,中缝温度达到950~9700C以上时,将槽中碳渣捞干净,开始通知净化NB作业,24小时后开始通知电算站微机操作,准备灌铝。
焙烧启动作业程序表
阴极钢棒、侧壁温度使用红外线测温仪,测量位置于侧壁拉筋中心点处
电压巡视记录及要求
焙烧期间二小时记录一次,拆卸分流器前后各记录一次
启动后每半小时记录一次
抬电压
抬电压前有25CM以上电解质,每半小抬一个回转计读数,抬电压过程要注意阳极电流分布、注意钢爪发红及脱极。
测量
按第六项内容做好测量。
8
通电96-120小时
启动过程
启动前复紧小盒卡具,电压抬到8V后再次复紧;启动过程注意物料喷出烧伤,按要求管理好电压,下好电压及氧化铝接通计划表,做好物料等记录。注意槽底及侧部
9
通电120―192时
120小时灌铝及三天电压管理
灌铝过程注意电压保持,小心铝液伤人。灌铝结束注意电压调整,做好记录。
鑫业分公司电解槽焙烧启动作业程序表
槽号:
焙烧、启动期间测量要求
测量项目
测量要求
责任人签字
焙烧温度测量
每两小时测量一次
阳极电流分布测量
四小时测量一次
偏高和偏低值要重点标出
阳极电流分布异常的处理时间、处理措施及处理结果都要有记录
测量使用数字式毫伏表,测量位置于水平母线下沿的铝导杆上
钢爪温度重点巡视测量
结合阳极电流分布对阳极电流分布每半小时巡、测一次
发现有钢爪发红或其它异常时要及时汇报并进行相应的处理
测量使用红外线测温仪
炉底钢板温度测量
每8小时测量一次(整个炉底面巡视测量,记录超过100℃的点并在相应位置作出标示)
灌电解质以后测量一次,然后每8小时测量一次。启动槽炉底钢板温度变化较大,要注意加强巡视和监控
此项测量时间范围自焙烧开始至灌铝后48小时后结束,对异常槽要继续测量和监控
- 1、下载文档前请自行甄别文档内容的完整性,平台不提供额外的编辑、内容补充、找答案等附加服务。
- 2、"仅部分预览"的文档,不可在线预览部分如存在完整性等问题,可反馈申请退款(可完整预览的文档不适用该条件!)。
- 3、如文档侵犯您的权益,请联系客服反馈,我们会尽快为您处理(人工客服工作时间:9:00-18:30)。
230KA导流结构电解槽混合料焙烧启动操作规程1目的及范围通过煅后焦、石墨粉混合料焙烧,烘干炉体,烧结阴极炭缝,熔化导流沟内的电解质,将炉底加热到接近生产温度后,采用湿法效应启动,熔化冰晶石等装炉原料,形成铝电解生产必须的液态电解质,同时进一步加热炉内衬,清除杂物。
适用于230KA导流结构电解槽采用煅后焦、石墨粉混合料焙烧启动的具体操作和管理要求。
2作业人员:值班长、电解工、天车吸出工、计测工、调度人员3使用工具、原料3.1 装炉使用的工器具、原料:扫把、风管、天车、专用筛格、刮板、直尺、扳手、软连接(1套)、分流片(1套)、石棉板、风动扳手、绝缘板(4块)、绝缘套管(8根)、热电偶及保护套管(2套)、炉盖(1套)、煅后焦、石墨粉混合料(0.4吨)、阳极(32块)、电解质块(6吨)、冰晶石(3吨)、碱(1.0吨)、氟化钙(0.5吨)3.2 焙烧期间使用的原材料:碱(1吨)3.3 启动使用的工器具、原料:天车、抬包、电解质液(14吨)、铝液(13吨)、碱(1.0吨)、氟化钙(0.5吨)、冰晶石(3吨)、氧化铝(12吨)4 准备作业4.1 煅后焦、石墨粉的准备用筛子对煅后焦、石墨粉进行筛分,将粒度在5mm以下的煅后焦与石墨粉原则上按重量比6:4的比例进行充分混合,配备0.4吨左右的混合料。
4.2 预先对阳极导杆和槽上压接面进行抛光,同时对分流片的压接面进行抛光处理。
4.3 使用扫把等工具将电解槽阴极炭块表面清扫干净,再用风管将阴极表面吹干净。
4.4 用冰晶石填充电解槽内的沟槽与阴极面平齐。
4.5 铺设混合料、安装阳极4.5.1 首先挂好A16处的阳极,确定阳极正投影位置,将专用筛格沿投影线摆好,要求筛格安放平整。
将混合料倒入筛格内,用刮板在筛格内来回刮混合料,使其沿筛眼漏至阴极面,待填满所有筛眼后,取出专用筛格。
沿阴极混合料处安放,在A、B两侧依次铺设混合料。
4.5.2 铺设混合料后,安装阳极,装好卡具,但不拧紧,使阳极完全靠自重与混合料接触。
在阳极中缝、间缝铺设10mm厚的石棉板。
4.6 安装软连接4.6.1 安装软连接前确认软连接完好,无断裂情况。
4.6.2 用风动抛光机打磨软连接的接触面。
4.6.3 用风动抛光机打磨与软连接接触处的铝导杆和阳极水平母线,将软连接的两端分别与铝导杆和阳极水平母线连接。
(如图1所示)4.6.4 安装软连接必须使软连接与母线、导杆连接的螺帽扭紧,通电前进行最后确认(复紧)。
4.7 安装分流片4.7.1 安装分流器前先确认分流器完好,无断裂、缺片。
4.7.2 将分流器安装面、母线接触部位用抛光机进行抛光处理。
4.7.3 安装分流器,必须扭紧分流器与母线连接的螺帽,通电前进行最后确认(复紧)。
采用立柱分流(如图2所示),将分流器的一端安装在焙烧槽的B侧阳极横母线上,另一端安装在下一台槽的立柱母线上,安装时,每组分流片两端的连接必须紧固。
图2 分流器安装示意图4.8 砌炉4.8.1 用纸板挡住阳极间缝外侧,在侧部人造伸腿上均匀撒上1.0吨冰晶石和0.5吨氟化钙。
4.8.2 先在人造伸腿处堆砌小于10cm的电解质块,大块在外,小块在内,然后在砌好的电解质块上撒1.0吨碱。
4.8.3 在砌好的人工炉帮上和阳极上均匀地铺设剩余的冰晶石。
4.9 设置热电偶在电解槽的出铝端和烟道端阳极1、2及15、16中缝处预埋2个热电偶保护套管,并用纸等制成栓塞塞住套管口。
4.10 检查确认具备通电条件后,安装2个热电偶进入保护套管内。
5 通电5.1 联系5.1.1 与生产控制中心调度联系预定通电的时间、槽号。
5.1.2 与计算机联系预定通电的时间、槽号。
5.1.3 与浓相联系预定通电的时间、槽号,确定氧化铝的打料时间。
5.2 采用不停电装置通电,具体操作按《230KA电解槽不停电开停槽操作规程》执行。
5.3 焙烧期间温度控制要求及升温曲线5.3.1 焙烧期间温度控制要求焙烧期间按下表控制焙烧温度:5.3.2 升温曲线如图3所示10020030040050060070080090006121824303642485460667278849096时间(h )温度(℃)图3 升温曲线5.4 通电后的测试5.4.1 通全电流30分钟测量一次阳极电流分布,以后每8小时测量一次阳极电流分布。
测量值小于3mv 时,用大锤敲击阳极钢梁,使阳极与混合料充分接触。
5.4.2 通电后2小时测量一次阴极电流分布。
阴极电流分布修正值大于10mv 时,结合对应处阳极电流分布的情况进行分析,调整阳极电流分布,保证阴极焙烧温度均匀上升。
以后每24小时测量一次。
5.4.3 通电后每隔两小时用红外线测温仪测量一次软连接温度,温度<250℃,视为正常温度;测量温度≥250℃,视为异常温度;测量温度≥300℃,视为危险温度。
发现异常,作如下处理:5.4.3.1先复紧软连接两个连接面的螺帽,直至温度<250℃。
5.4.3.2检查该阳极电流分布的大小,观察是否存在阳极发红,如阳极电流分布大于20mv ,或存在阳极发红,应对阳极问题进行处理。
5.4.3.3对处理后的温度异常软连接要进行重点跟踪,要求每小时测量一次,直到温度<250℃为止。
5.4.3.4 当软连接异常温度处理后仍然大于250℃,用风管冷却处理。
5.4.4 通电后4小时测量焙烧温度,以后每4小时测量一次焙烧温度。
5.4.5 通电后4小时测量软连接处的接触压降,以后每班测量一次,测量值大于25 mv时,用扳手复紧该处螺杆,使其接触完好。
5.4.6 通电后出现分流器螺帽部位发红,首先对螺帽进行复紧,继续发红可用铁锤轻轻敲打发红部位,使螺帽与螺杆良好接触,同时对分流片进行吹风冷却直至发红情况消除。
5.4.6 启动前测量一次炉底钢板温度。
5.5 分流片的拆除通电后分流率不再变化,槽电压在2.5伏时拆除分流片,四根立柱不能同时进行,先拆除2、3立柱,8小时内拆除另外两组。
开始拆除分流片和拆完分流片时,记录电压、电流值。
5.6 软连接的拆除通电96小时后,炉底钢板温度平均值达到50℃以上,焙烧温度达到800℃以上,并且焙烧温度均匀后,启动电解槽。
启动电解槽前,将阳极卡具拧紧,拆除软连接。
6 启动6.1 电解槽具备启动条件后,取出阳极中缝的石棉板,使用溜槽往槽内灌入14吨电解质液,分三次进行。
第一次灌入5吨电解质,上抬阳极,确保阳极不脱离电解质,电压不超过6伏。
最后一次灌入电解质液后,电压保持10—12伏,效应持续约30分钟。
6.2 灌完电解质后,扒开中缝,在出铝端和烟道端同时打捞碳渣。
6.3 效应达到目的后,用木棒插入阳极底掌的方法熄灭效应,若效应不易熄灭,可投入一定量的氧化铝、增加插入木棒帮助熄灭,效应熄灭后,电压保持5.5伏。
6.4 效应熄灭后,再次打捞碳渣。
6.5 效应熄灭24小时内,采用手动调整电压,每30分钟调整一次电压,灌铝前电压保持5.0伏。
6.6 测量槽内电解质水平,当电解质水平小于30cm时,视具体情况适当补充冰晶石。
6.7 根据灌入电解质量及灌入电解质的分子比情况,往槽内适当补充部分碱。
6.8 熔料过程中,电压保持5.0伏,边熔料边捞碳渣。
物料熔化完毕,彻底打捞碳渣,并用小钩子清理阳极底掌的碳渣。
6.9 效应熄灭后24小时,采用溜槽灌入第一包铝液7吨,视槽温情况确定灌入第二包铝的时间,当槽温低于970℃,严禁灌第二包铝。
6.10 灌铝时,要有专人抬阳极,在灌铝的过程中电压的控制相应比灌铝前高0.4伏。
6.11灌完铝后,让槽电压高出灌铝前0.2伏,30分钟后恢复到灌铝前的电压。
6.12 灌铝后一周内,每24小时取样分析一次电解质成分,根据分子比及氟化钙含量决定碱和氟化钙的补充量。
6.13 灌铝后到RC接通前的电压调整灌铝结束1小时后,由值班长手动降电压,灌铝24小时后,电压降至4.75伏。
灌铝48小时后,电压降至4.5伏。
(电压控制曲线如图4所示)6.14 联机6.14.1 启动过程中第一个效应熄灭后,联系计算机接通NB、AEB,确定NB、AEB间隔,同时将电解槽运行状态变更为运行。
6.14.2 灌铝后AE间隔设置为13小时,第一个效应后设置为24小时,10天后设置为48小时,20天后设置为72小时,30天后设置为120小时。
6.14.3 灌铝完毕,槽电压降至4.5伏以下时,接通RC氧化铝模糊控制。
6.15 电解质表面结成薄壳后,由当班操炉人员指挥天车向阳极上添加氧化铝作保温料,并进行整形。
7 记录7.1 记录通电、拆分流片、拆软连接以及启动的时间,原材料的添加量。
7.2 记录阴、阳极电流分布测量值、炉底钢板温度、焙烧温度测量值、槽电压、效应电压、效应持续时间。
7.3 记录焙烧、启动过程中的异常情况和处理措施。
8 启动后工艺参数的控制范围启动后第一个月工艺参数控制9 降电压的步骤9.1 第一个长时间效应结束后,电压保持在5.5V左右,每班逐步下降电压,在启动后24小时时降至5V左右。
9.2 灌铝之后电压保持在4.75 V左右,灌铝48小时后,电压降至4.5伏。
9.3 启动后电压在4.30V之前,根据电解槽温度、稳定性每天降电压50~100mV,能降则降;9.4 降到4.30V后根据电解槽的稳定情况和铝水平、电解质水平的情况电压下降放缓,具体为:● 4.20~4.30V之间每天降20mV;● 4.06~4.20V之间每天降10mV;● 4.00~4.06V之间每天降5mV;● 4.00V以下根据电解槽槽况试探性下调电压。