真空辅助RTM成型技术的研究[1]
复合材料管道连接件真空辅助成型工艺树脂流动研究

王长春 工程师, 主要从事复合材料制造及 数值仿真、 复合材料结构强度计算与分 析工作。
航空航天一直是各国竞相发展 的热点。近年来, 随着各重大科技专 项的实施, 我国航空航天事业获得快 速发展。航空航天建设领域中需要 用到大型管道结构进行有效传输, 这 就要求管道结构在服役环境下具有 良好的力学性能。传统的管道结构 通常采用金属材质制造, 工艺成熟、 易于批量生产, 但由其制造所得管道 结构具有比重大、 制造工艺复杂且耐 腐蚀性能差等缺点 [1-2]。图 1 给出了 传统金属管道在工程服役环境下典 型腐蚀图, 并且这种管道腐蚀破坏不 易排查, 通常会造成重大经济损失。 如何有效基于低成本制造工艺制造 出轻质高性能的大直径管道结构具 有显著的工程意义 [3-5]。 先进复合材料以优异的比强度、 耐疲劳和抗腐蚀等性能被广泛用于 航空航天等高技术领域 [6-8]。已有研 究采用缠绕工艺制造复合材料管道, 并研究了预紧力和缠绕温度对复合
120mm×360mm 的长方形, 并将裁剪 好的单层织物按照设计铺层方式叠 放, 接着将具有复杂曲面的金属芯模 放置在预制体上方; 第二步, 将位于 芯模下方的纤维织物沿着芯模上表 面包覆铺放, 使芯模包埋在其中; 第 三步, 为保持上表面织物沿着芯模曲 面具有良好接触, 将与芯模上表面相 匹配的硬性金属模具覆盖在芯模上 方织物上表面, 以保持预制体织物在 浸润树脂前, 其形状与金属芯模表面 贴合良好; 第四步, 将注射口和出射 口的位置按采用模拟所得树脂注模 方式进行设置, 注模前将树脂注射口 采用密封夹密封; 第五步, 树脂注模 前, 将其置于真空烘箱内进行除气泡 操作, 在真空压力梯度下进行注模。 3 试验件注模方式设计 本文进行的技术攻ห้องสมุดไป่ตู้是采用 VARTM 工艺制造长度 6m、 直径 1.5m 的复合材料管道, 其关键是如何解
RTM成型学习资料
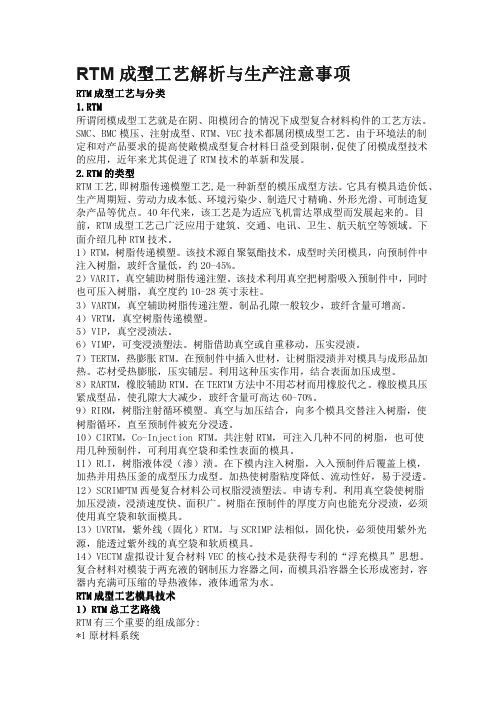
RTM成型工艺解析与生产注意事项RTM成型工艺与分类1.RTM所谓闭模成型工艺就是在阴、阳模闭合的情况下成型复合材料构件的工艺方法。
SMC、BMC模压、注射成型、RTM、VEC技术都属闭模成型工艺。
由于环境法的制定和对产品要求的提高使敞模成型复合材料日益受到限制,促使了闭模成型技术的应用,近年来尤其促进了RTM技术的革新和发展。
2.RTM的类型RTM工艺,即树脂传递模塑工艺,是一种新型的模压成型方法。
它具有模具造价低、生产周期短、劳动力成本低、环境污染少、制造尺寸精确、外形光滑、可制造复杂产品等优点。
40年代来,该工艺是为适应飞机雷达罩成型而发展起来的。
目前,RTM成型工艺己广泛应用于建筑、交通、电讯、卫生、航天航空等领域。
下面介绍几种RTM技术。
1)RTM,树脂传递模塑。
该技术源自聚氨酯技术,成型时关闭模具,向预制件中注入树脂,玻纤含量低,约20-45%。
2)VARIT,真空辅助树脂传递注塑。
该技术利用真空把树脂吸入预制件中,同时也可压入树脂,真空度约10-28英寸汞柱。
3)VARTM,真空辅助树脂传递注塑。
制品孔隙一般较少,玻纤含量可增高。
4)VRTM,真空树脂传递模塑。
5)VIP,真空浸渍法。
6)VIMP,可变浸渍塑法。
树脂借助真空或自重移动,压实浸渍。
7)TERTM,热膨胀RTM。
在预制件中插入世材,让树脂浸渍并对模具与成形品加热。
芯材受热膨胀,压实铺层。
利用这种压实作用,结合表面加压成型。
8)RARTM,橡胶辅助RTM。
在TERTM方法中不用芯材而用橡胶代之。
橡胶模具压紧成型品,使孔隙大大减少,玻纤含量可高达60-70%。
9)RIRM,树脂注射循环模塑。
真空与加压结合,向多个模具交替注入树脂,使树脂循环,直至预制件被充分浸透。
10)CIRTM,Co-Injection RTM。
共注射RTM,可注入几种不同的树脂,也可使用几种预制件,可利用真空袋和柔性表面的模具。
11)RLI,树脂液体浸(渗)渍。
RTM技术工艺详解
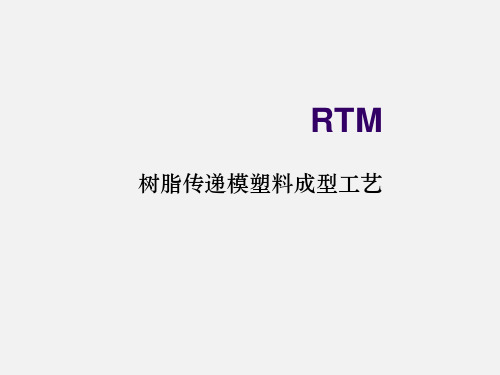
增强材料
由于在RTM成型过程中,增强材料在模具型腔 中要经过带压树脂流动充模过程,会带动或充 散纤维,造成制品出现“冲浪”或“跑道”现 象。因此,为保证制品质量,RTM工艺适用于 采用长纤维和连续纤维织物作为增强材料
工艺因素
影响RTM工艺的因素
VARTM(真空辅助RTM)工艺
一般RTM工艺在树脂注入时,模具型腔内可积起几吨压力。 通过使用了真空,模具内形成这种压力的趋势得到了减少, 因而增加了使用更轻模具的可能性,真空的使用也可提高 玻璃纤维的含量,而且有助于树脂对纤维的浸渍。纤维含 量可达65%以上,空隙率小于2%。
VARTM工艺过程
ห้องสมุดไป่ตู้合模
注射树脂
RTM – 脱模
RTM的优点
无需胶衣涂层即可为 构件提供光滑表面, 能制造出具有良好表 面的高精度复杂制品
模具制造及选材灵 活性大,设备及模 具投资小,产品只 需做小的修边
产品铺层过程中 可加入嵌件及对 局部进行加强
制品纤维含量高, 空隙率低(<0.2%)
成型过程中挥发物少, 车间环境及气味较好
在制作高质量RTM制品时,会让出口流出一定 量的树脂以后才结束充模。
目的是改善树脂对纤维的浸渍程度及排出微观 气泡。即改善了纤维与树脂的物理结合强度, 又改善了制品的密实程度。
一般浪费树脂量可达模制品重量的1/3~2/3。
注胶压力
压力的高低决定模具的材料要求和结构设计, 高压力需要高强度、高刚度和大的合模力。
基体树脂
室温或工作温度下具有低的粘度(小于1.0Pas) 及一定长的适用期
树脂对增强材料具有良好的浸润性、匹配性、 粘附性
树脂在固化温度下具有良好的反应性且后处理 温度不应过高
RTM工艺及模具

轻质RTM工艺及模具制作一.轻质RTM成型工艺原理及技术特点1.工艺原理轻质RTM就是真空辅助带压低粘度树脂在闭合模具中流动浸润增强材料并固化成型的一种工艺技术,其成型压力不足1kg/cm2。
树脂和固化剂通过注射机计量泵按配比输出带压液体在静态混合器中混合均匀,然后在真空辅助下注入已合理铺放好的纤维增强体的闭合模中,模具用真空对周边进行密封和合模,并保证树脂流动顺畅,然后进行固化。
该工艺需要二级真空,第一级真空(真空度为667毫米汞柱)完成上下模的闭合动作,第二级真空(真空度为376毫米汞柱)在树脂注射过程中辅助树脂的流动和对增强材料的浸润。
2.技术特点轻质RTM具有很多传统RTM相似的优点,比如生产效率和产品质量可以得以提高;可以得到两面光,大尺寸的产品;减少树脂有害成份对人体和环境的毒害。
由于轻质RTM是低压真空辅助成型工艺,所以与传统RTM相比,模具制作工艺大大简化,既方便又快捷。
模具无需如传统RTM那样进行钢结构的加强,下模为三明治夹芯结构,具有较高的刚度以防止树脂在注射过程中模具产生任何变形,同时三明治夹芯结构可以有效保存产品固化时产生的热量,有利于后续产品的快速固化,缩短生产周期。
而上模更为简单,可作成轻质、半刚性的结构,这样非常有利于频繁的脱模、合模的操作。
二.模具的制作1.模具制作环境的要求以及原料的选择a.环境环境温度:理想的范围为25±3℃。
相对湿度:不能大于60%。
制作车间:应保持比产品生产区更高的清洁度与日常维护。
b.材料对于该工艺所需要的材料我们推荐如下:①主要材料胶衣:ccp-071(具有优良的耐热能力,HDT为160-173℃)模具树脂:RM2000(快速固化,快速制造模具,低收缩,降低模具成本)F-010(环氧改性乙烯基树脂,良好的强度和耐热性,以及低收缩率)表面毡:300g/m2无碱短切毡:450g/m2轻木:用于提高模具的刚性并减轻重量蜡片:用于控制模腔的厚度,良好的厚度均匀性。
RTM加工工艺存在的问题及研究现状

1 TM 工 艺 存 在 的 问题 R
RTM 工艺 主要 有两 个 关键环 节 : 浸渍 与聚 合 , 即树 脂 的充模 与 固
中 粉 工 22 o 国 体 业 0 .l 1N 2
化 。其 工艺 参数 和 材料 性能 对这 两 个 射 口和 溢料 ,从而 可 以提高 模 具设 计 性 差 。纤维 预 制体 边缘 与模 具表 面 不
II =. l 至加 工工艺存在的问题及研究 -
【 要 】 树 脂 传 递 模 塑 ( 罗 i T a se Mo d n 摘 sn l i g,RT 工 艺 是 M) 康 永 Re 红 r n f r
一
种 制造 高性 能纤 维增 强聚 合 物基 复合 材 料 的先进 技术陕 西榆林 1 1 。 陕西金泰 氯碱 化工有 限公司技术 部 , 因其成 型速 _ 0 ∞
模具 的优化设 计 、 新 RTM 专业软 件进 行工艺过 程模拟 可以 局 部纤 维体 积 分数 较低 或 较高 而形 成 过程 的在线监控 、 合 理 的 确 定 RTM 模 具 中 的 导 流 槽 、注 树 脂富 裕 区或 者贫 瘠 区 ,使成 品均 匀 型 工艺设 备 的开发 等。
形 成 气 泡 、干 斑 、脱 层 ,以 及 预 成 型 体 树 脂对 纤 维 的浸 润过程 均 不 可见 ,很 注 射 的树 脂冲 刷 而改变 其均 匀性 。纤
铺 敷 不 当 引 起 厚 度 不 均 和 褶 皱 等 。 难X R  ̄ TM工 艺过程进 行研究和 及时解 维预 制体 边缘 不 能与模 具 壁很 好地 吻 RT 技术在 国内外普遍 存在 的难关和 决实 际生 产 工 艺 过程 中 出现 的 问题 , 合 , 处容 易形成高渗 透区 ,导致树脂 M 该
. ( ) 格适 合 的 RTM 注射成 型分 2 2纤维预制体的可渗透性 5价
【doc】RTM成型工艺原理及其特点

RTM成型工艺原理及其特点诎拐,RTM成型工艺原理及其特点FRP的用途和成果,向材料工程师和制品设计工程师们介绍了许多有关制品设计,降低制品成本,提高生产效率的新概念.然而,环境保护法规的要求日益严格,这迫使复合材料制品制造者们努力寻求有害物质散发量最小的生产工艺.七十年代初期就发明了树脂注射模塑(Resininjectionmoulding)简称RIM的闭模成型工艺,但由于当时许多技术问题没有解决,如生产效率低,纤维织物浸润性差,气泡排不尽,树脂流动有死角,影响制品质量,故该工艺诞生不久即无人问津,材料专家们的注意力又转向SMC和BMC的模塑成型工艺.现在这二种成型工艺(sMC,BMC)发展已相当成熟,应用也非常广泛,但此二种成型工艺,其最大的缺点是设备投赍大,少则数百五多则数千万元一条生产线,增强材料多为短切乱纤维,不能按设计要求进行铺设.在此期间,由于热塑性塑料加工中的反应注射成型方法和工艺技术的发展,其英文缩写亦称为RIM.八十年代中期,由于FRP材料在汽车制造业中得到进一步的发展,用SMC或BMC成型FRP汽车配件虽然可得到二面光的美观的制品.生产效率也很高, 但材料强度低不适宜制造车身等大型构件, 而手糊成型生产效率低,环境污染严重,劳动强度太,急需发展一种无污染的'高效的闭模模塑成型技术,所以树脂注射模塑成型工艺又重新被人们提了出来.为了区别于热塑性塑料的反应注射成型.故改名为树脂传递模塑成型(ResintransfermoMing)简称RTM.它是所有闭模模辍工艺中功能最多盒,汽车保险杠引擎盖,到直径6米的天线反射罩,10米长的FRP游艇壳体;从简单的手推车车身,到复杂的小汽车,面包车整体车身及高性能复合材料绪构构件(如飞机辅翼托架,垂直尾翼.汽车主车架.底盘等)均可用RTM工艺制造.RTM工艺经过近五年的研究和发展.在工业发达国家如英,美,德.法,瑞典已发展到相当成熟的程度,应用也非常普遍.有取代手糊成型和SMC成型的趋势,该工艺系统目前正日趋完善.生产效率在不断提高的过程中,目前已达到每30分钟制造一个制品的程度,将来有可能实现FRP制品形状不受限制,铺层随意设计的机械化,自动化生产工艺线. 在我国该工艺的研究仅处于开始阶段,有些单位引进了RTM注射机,但预成型技术,原材料,FRP模具制造技术还不配套,亦未能发挥作用.二.RTM工艺原理树脂传递模塑(RTM)T艺是闭模模塑工艺之一,其工艺原理较为简单.如图所示:图1RTM工艺原理气口下模9在RTM工艺中.树脂(加引发剂和促进剂)注入已闭合.已铺放增强纤维织物的模具里,不需要加压.不需要外部加热,仅给模具内表面通电数分钟.待几十分钟固化后脱模,便成型双面光洁,尺寸稳定性好的FRP制品.制品脱模后稍加修整即可. RTM工艺最后成功的因素有:(1)RTM设备的有效性和简易性.(2)树脂配方的多样性,所有低粘度高韧性,快速固化树脂均可用于RTM工艺.(3)对模具要求的理解,可用FRP模具.(4)更多的可供选择的增强材料及预成型技术.(5)辅助设备的发展.RTM工艺不是简单的一种工艺方法或设备,它是一种新的成型工艺系统,根据发展,分为如下几个发展阶段:普通RTM工艺:它由注射机和对模组成,增强材料采用纤维毡纤维织物或预成型纤维型坯铺放在下模里,上模与下模闭合夹紧.模具一般采用FRP制造,可通电加热,树脂催化剂,促进剂在混合器中均匀混合后由泵输送注入模具内.注射压力一般为O.5~10?1.5kg/cm,注孔按制品形状和尺寸可由1个至多个.上下模具需用密封圈密封.关键部位开排气孔.要求模腔内的空气比树脂先从排气孔排出.这种普通RTM工艺目前有以下问题:用手工铺层,劳动强度大.生产效率低,模塑周期较长.用于汽车工业的高速R1M工艺要使RTM工艺用于高效的汽车工业中,其目标是生产效率达到每分钟1件,重量大于100kg的汽车构件,要达到此目标.(1)采用高性能低粘度快速固化树脂.(2)自动化铺层的预成型技术.(3)高效率的快速注射机.(4)fl动化机械式的闹模脱模装置.用于航天航空工业的RTM工艺用予航天航空领域的FRP制品有以下的特点:高强度高刚度,耐高温,重量轻等特点,RTM工艺要适用该工业,工艺系统作以下改变:①特种树脂开发;②特种模具设计,使它容易嵌入金属预埋件;③真空辅助装置,强制排气:④提高注射压力和模温,树脂加热注射.工艺流程如下:RTM工艺流程图三,RTM工艺系统组成部份及技术关键RTM成型工艺系统包括以下四大部份:1.增强材料预成型系统:当前世界上高效生产汽车.飞机,船体等大型高性能复合材料(FRP)构件最有前途的成型工艺是树脂传递模塑(RTM)T艺和结构反应注射模塑(SRIM)T艺.这两种工艺都要求需要高效率的成型增强材料型坯的铺层技术.这是RTM走上工业化,自动化生产的关键.增强材料预成型工艺大致有以下五种:(1)手工铺层(2)编织法(3)针织法(4)热成型连续原丝毡法(5)预成型定向纤维毡.从低成本高效率的角度分析,后二种方法适合RTM和SRIM,尤其是预成型定向纤维毡技术具有较好的渗透性和耐冲刷性.充模较容易.也是最经济的方}.普通定向纤维成型技术是通过具有水平轴的4站圆盘传送机组成.第一站短切纤维和粘结剂按一点方向一起喷射到预成型筛上.第二站烘干粘结剂.第三站型坯脱模.第四站型坯装人RTM模内.目前国外已实现用机器人操作的自动化增强材料预成型坯生产系统.2.树脂注射系统树脂注射系统通称为RTM机,它包括加热恒温系统.混合搅拌器.三种组份计量泵以及各种自动化仪表(如注射压力自控器.模塑周期计算器,树脂腔凝计时器等).整个注射系统装在有轮的平板上,非常小巧.移动方便.3.RTM的模具系统RTM所用的模具一般均采用自热式玻璃钢模,其内表面用高性能特种导热胶农树脂翻造,使用寿命可达1万次.模内有通电加热元件.接着绝热层.强度层.整体刚度结构组成.模具内预埋有多个注射孔,树脂流道和排气孔,密封圈等组成.对RTM模具的要求:(1)保证制品尺寸,形状的精度要求,以及上下模的匹配精度.表面达到A级光洁度.(2)具有夹紧和顶开上下模的装置及制品脱模装置.(3)具有足够的强度和刚度在0.5--1.5kg/cn1的注射压力下不损坯,不变形.(4)可通电加热,能经受85℃~I20℃,一万次的热冲击.不开裂,不变形.(5)具有较长使用寿命,至少安全生产三千只制品.(6)具有合理的注射孔,流道,排气孔,密封设计.保证树脂流满模腔.制品无气泡.无疵点,不溢出树脂.(7)上下模密封性能好,除制品边缘外.模内树脂漏损率<1‰能排尽模内空气.(8)成本要低廉.4.测量控制系统模具内预埋有各种探头和传感器,用以测量控制模具内温度分布.树脂流速及充满情况,树脂固化程度……等.四,RTM工艺特点1.树脂,引发剂,促进剂从储存罐经精确计量后密封输送到闭模中,对环境无污染,对工作者身体无伤害.2.对模成型,制品尺寸稳定.双面光洁.3.不需要庞大复杂的成型设备,就可以翻造复杂的大型构件,设备投资少.即使引进大流量(每分钟注射量达50kg)快速RTM机.仅5万美元左右,同样用SMC工艺.设备投资在100万美元以上.4.成型压力低.可用0.5--1.5kg/cm的注射压力,故可用玻璃钢模具.模具费低.仅为金属模的1/10~1/30.且容易预埋金属嵌件.5.在FRP模具内表层可夹人加热原件,通电加热,生产效率达到手糊的10 (下转第21页)】1?使用维纳斯一加斯默的RTM注射阀还可进行多口注射,与单口注射相比,它以更低的模压更快地充人模腔.维纳斯一加斯默的RTM注射阀是固定在模具上的,而泵送管又直接连在注射阀上.RTM注射阀可以进行遥控操作并正在取代以往用手动方式处理混合头和静态混合管的旧方法.使用这种注入阀不再需要操作人员攀爬模具或在操作时施加模压,它也允许操作人员在启动注人阀的时候监督泵送系统的工作情况.维纳斯一加斯默还研制了一种精密的微调控制系统,它可以显示树脂和催化剂的流量以及混合比例,同时还有模压和温度,而所有参数都可以输人到工艺统计控制软件中.一个设计良好的工艺统计控制程序可以在设备出故ll/~"及时发现,从而可以极大地避免由于产品返工造成的损失.装备上RTM的泵送系统.并配上正确的计算机控制程序,就基本上消除了影响产品质量的主要因素,从而达到零缺陷这一生产标准.由于树脂处理和增强材料的预成型都实现了完全自动化,因此在年产20,000件至30,000件这一生产规模上,从规模成本角度看,RTM完全可以和sMc竞争.预计不远的将来,这一规模经济产量可以上升到5O.00o件/年.在以往的四十多年,维纳斯一加斯默倾尽全力追求工艺的完美,并欣然为众多成功的大型RTM模制厂家,如波音公司,洛克维克公司和DodgeViper汽车外壳的生产厂家等提供其优良设备和服务.九四年七月(上接第8页)7.J.S.Hayward.B RubberProcessing11(1989)191Harris,PlasticsandandApplications8.J.S.Hayward.B.Ha州s,SAMPEJour—hal,26(3)(1990)39--469.FrankC.Robertson,BritishPolymer Journal20r1988)4l7—42910.M.J.OWel1.V.Middleton,etal,Plastics andRubberProcessingandApplications 12(1989)22卜_225l1.Anon.,PlasticsTechno1.,(May1979)34 12.沈开猷编不饱和聚酯及其应用化学工业出版社】982(上接第l1贾)一15倍,为SMC的1/4倍,目前正在进一步改进工艺技术,以达到SMC的生产效率.模具不需要整个加热.节省成型能源. 根据目前生产汽车外壳和电视卫星天线,RTM成型工艺参数:成型温度:8O~12d℃注射压力:O.5~1.5kg/cm注射量:15kg/min~50kg/rain生产效率:20~50件/天.是当今制造结构复合材料大型异型构件,最好性能最有发展前途的成型工艺. 参考文献略21?。
复合材料真空灌注-RTM成型工艺及应用

复合材料真空灌注-RTM成型⼯艺及应⽤概述真空辅助树脂灌注成型⼯艺(VacuumAssisted Resin Infusion Molding)简称VARIM⼯艺,是在RTM(Resin Transfer Molding)⼯艺基础上发展起来的⼀种⾼性能、低成本的复合材料成型⼯艺。
⾃80年代末开发出来,VARIM⼯艺作为⼀种新型的液体模塑成型技术(Liquid Composite Molding,简称LCM),得到了航空航天、国防⼯程、船舶⼯业、能源⼯业、基础结构⼯程等应⽤领域的⼴泛重视,并被美国实施的低成本复合材料计划(Composite AffordabilityInitiative,简称CAI)作为⼀项关键低成本制造技术进⾏研究和应⽤。
如图1所⽰,VARIM⼯艺的基本原理是在真空负压条件下,利⽤树脂的流动和渗透实现对密闭模腔内的纤维织物增强材料的浸渍,然后固化成型。
VARIM⼯艺的基本流程包括:(a) 准备阶段。
包括单⾯刚性模具的设计和加⼯、模具表⾯的清理和涂覆脱模剂、增强材料(纤维织物、预成型件、芯材等)和真空辅助介质(脱模介质、⾼渗透导流介质、导⽓介质等)的准备等。
(b) 铺层阶段。
在单⾯刚性模具上依次铺设增强材料、脱模布、剥离层介质、⾼渗透导流介质、树脂灌注管道、真空导⽓管道等。
(c) 密封阶段。
⽤密封胶带将增强材料及真空辅助介质密封在弹性真空袋膜内,并抽真空,保证密闭模腔达到预定的真空度。
(d) 灌注阶段。
在真空负压下,将树脂胶液通过树脂灌注管道导⼊到密闭模腔内,并充分浸渍增强材料。
(e) 固化阶段。
继续维持较⾼的真空度,在室温或加热条件下液体树脂发⽣固化交联反应,得到产品预成型坯。
(f) 后处理阶段。
包括清理真空袋膜、导流介质、剥离层介质、脱模布等真空辅助介质和脱模修整等,最终得到制品。
图1 真空辅助模塑成型(VARIM)⼯艺⽰意图和传统的开模成型⼯艺以及RTM⼯艺相⽐,VARIM⼯艺具有以下优点:(1) 模具成本低。
真空辅助树脂传递模塑工艺
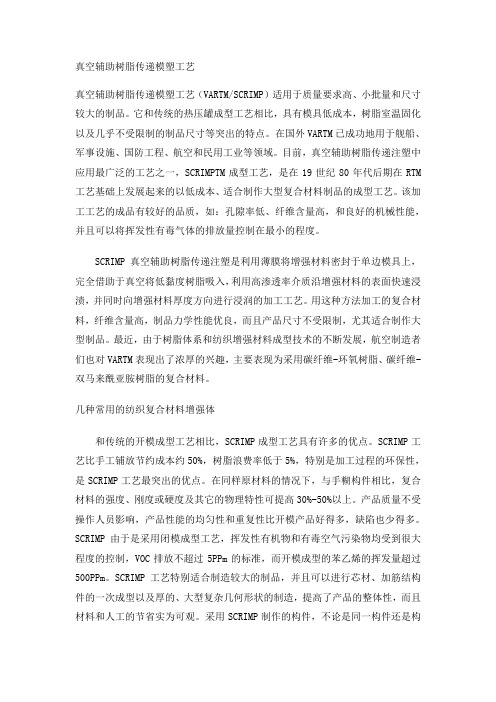
真空辅助树脂传递模塑工艺真空辅助树脂传递模塑工艺(VARTM/SCRIMP)适用于质量要求高、小批量和尺寸较大的制品。
它和传统的热压罐成型工艺相比,具有模具低成本,树脂室温固化以及几乎不受限制的制品尺寸等突出的特点。
在国外VARTM已成功地用于舰船、军事设施、国防工程、航空和民用工业等领域。
目前,真空辅助树脂传递注塑中应用最广泛的工艺之一,SCRIMPTM成型工艺,是在19世纪80年代后期在RTM 工艺基础上发展起来的以低成本、适合制作大型复合材料制品的成型工艺。
该加工工艺的成品有较好的品质,如:孔隙率低、纤维含量高,和良好的机械性能,并且可以将挥发性有毒气体的排放量控制在最小的程度。
SCRIMP真空辅助树脂传递注塑是利用薄膜将增强材料密封于单边模具上,完全借助于真空将低黏度树脂吸入,利用高渗透率介质沿增强材料的表面快速浸渍,并同时向增强材料厚度方向进行浸润的加工工艺。
用这种方法加工的复合材料,纤维含量高,制品力学性能优良,而且产品尺寸不受限制,尤其适合制作大型制品。
最近,由于树脂体系和纺织增强材料成型技术的不断发展,航空制造者们也对VARTM表现出了浓厚的兴趣,主要表现为采用碳纤维-环氧树脂、碳纤维-双马来酰亚胺树脂的复合材料。
几种常用的纺织复合材料增强体和传统的开模成型工艺相比,SCRIMP成型工艺具有许多的优点。
SCRIMP工艺比手工铺放节约成本约50%,树脂浪费率低于5%,特别是加工过程的环保性,是SCRIMP工艺最突出的优点。
在同样原材料的情况下,与手糊构件相比,复合材料的强度、刚度或硬度及其它的物理特性可提高30%-50%以上。
产品质量不受操作人员影响,产品性能的均匀性和重复性比开模产品好得多,缺陷也少得多。
SCRIMP由于是采用闭模成型工艺,挥发性有机物和有毒空气污染物均受到很大程度的控制,VOC排放不超过5PPm的标准,而开模成型的苯乙烯的挥发量超过500PPm。
SCRIMP工艺特别适合制造较大的制品,并且可以进行芯材、加筋结构件的一次成型以及厚的、大型复杂几何形状的制造,提高了产品的整体性,而且材料和人工的节省实为可观。
- 1、下载文档前请自行甄别文档内容的完整性,平台不提供额外的编辑、内容补充、找答案等附加服务。
- 2、"仅部分预览"的文档,不可在线预览部分如存在完整性等问题,可反馈申请退款(可完整预览的文档不适用该条件!)。
- 3、如文档侵犯您的权益,请联系客服反馈,我们会尽快为您处理(人工客服工作时间:9:00-18:30)。
真空辅助RTM成型技术的研究Ξ李柏松 王继辉 邓京兰(武汉工业大学材料复合新技术国家实验室,武汉430070)摘要: 本文详细介绍了目前RT M工艺中最先进的两种真空辅助成型技术高渗透介质辅助成型及引流槽辅助成型。
采用这两种技术的RT M工艺能够制造超厚超大的产品,适应更加广阔市场需求。
同时,真空辅助RT M成型技术也将RT M工艺的应用领域进一步扩大。
关键词: RT M 真空辅助成型 高渗透性介质 引流槽1 前 言树脂传递模塑成型(RT M)工艺自90年代以来,得到越来越广泛的应用。
传统的RT M工艺是将纤维增强材料铺放到闭合的模腔中,用压力将树脂注入模腔,树脂浸透纤维增强材料,然后固化,脱模成型制品。
这一方法受到材料品种及其性能的限制,很难适应大尺寸及厚壁制品的生产要求。
由于闭模操作,虽然人们采用各种各样的方法,也很难将制品的缺陷降到一个可以普遍接受的水平。
随着复合材料工业对成型工艺的要求越来越高,特别是对成型工艺的环保及成本方面的要求越来越高。
近年来,国外研制开发了真空辅助RT M成型技术(Vacuum-Assisted Resin Trans fer M olding)简称VART M。
与传统的RT M工艺相比,其模具成本可以降低50-70%,使用这一工艺在成型过程中有机挥发物(VOC)非常少,充分满足了人们对环保的要求,并且成型适应性好,因为真空辅助,可以充分消除气泡。
这一工艺制造的单件制品的最大表面积可以达到186m2,厚度150mm〔1〕,纤维重量含量最大可达75~80%〔2〕。
正因为这些优点,这一技术正迅速地得到推广。
2 VART M工艺VART M工艺是最近几年发展起来的一种改进的RT M工艺。
其基本方法是使用敞开模具成型制品。
这里所说的敞开模具是相对传统的RT M的双层硬质闭合模具而言的,VART M模具只有一层硬质模板,纤维增强材料按规定的尺寸及厚度铺放在模板上,用真空袋包覆,并密封四周,真空袋采用尼龙或硅树脂制成。
注射口设在模具的一端,而出口则设在另一端,注射口与RT M喷枪相连,出口与真空泵相连。
当模具密封完好,确认无空气泄漏后,开动真空泵抽真空。
达到一定真空度后,开始注入树脂,固化成型。
2.1 高渗透介质辅助VARTM工艺形状复杂的大型厚壁制品,在充模过程中,对于树脂胶液在模腔内的流动时间及流动模式的预测至关重要,准确的流动时间及流动模式对于调整树脂的凝胶时间,保证树脂对纤维增强材料的浸透起着关键作用。
对此美国俄亥俄大学的L.James Lee〔1〕等人采用高渗透介质辅助的VART M工艺,借助高渗透介质对流动的帮助可以预测树脂在模腔内的流动情况。
高渗透介质辅助VART M工艺中,纤维增强材料直接铺放在硬质模板上,在纤维增强材料顶上铺设一层剥离层,剥离层通常是一层很薄的低孔隙率、低渗透率的纤维织物,剥离层上铺放高渗透介质,然后用其真空袋包覆、密封、结构形式如图1所示。
图1 高渗透介质辅助VART M结构对于单纯的平面流动,高渗透介质的渗透率可以用下面的方程来描述:t=μ<2kP0s2(1)这里,s是从注射口到流动前缘的距离,t是相应的时间,μ是树脂胶液的粘度,P o是注射口处的压力,<是高渗透介质的孔隙率,采用的高渗透介质孔隙率一般为0.85-0.88。
树脂胶液在高渗透介质中的流动时间可以决定纤维织物在充模过程中的渗透率。
这是因为真空辅助RT M工艺过程中树脂胶液是在两种截然不同的多孔介质内造成的。
模腔内树脂胶液的流动行为可以用如下达西定理和连续方程进行控制: ・ V=0(2)71 2001年1月Ξ国家自然科学基金资助项目(19872051)和高等学校骨干教师资助计划资助项目玻璃钢/复合材料FRP/C M 20011No.1V =-Kμ P(3)这里, K 是渗透率张量,是一个三维坐标函数。
对于纤维织物部分和高渗透介质部分,它的数值是不同的.上述控制方程可以用变系数有限元方法求解。
在树脂注射过程中,由于高渗透介质的渗透率远远高于剥离层和纤维增强材料的渗透率,高渗透介质层内树脂流动前缘迅速超前于纤维层,进入纤维增强材料的树脂胶液大部分是从高渗透介质中流出的。
L.James Lee 通过有限元分析确定了在VART M 充模过程中树脂胶液的流动模型,如图2所示。
图2 树脂胶液流动模型图树脂胶液在高渗透介质中的流动可以看作是一种存在渗漏的平面流动。
这种渗漏是沿着高渗透介质厚度方向流入剥离层和纤维增强材料。
剥离层和纤维增强材料看作是渗漏树脂的接收器。
树脂胶液在高渗透介质中渗漏流动区域可以由三节点三角形有限元模型来处理,如图3所示。
渗漏量可以用方程(4)计算。
图3 有限元模型Q leak =κSK lump μPL dS (4)其中:dS 是控制体积分;L 是树脂胶液在剥离层和纤维增强材料部分的流动前缘的距离;K lump 是剥离层和纤维增强材料部分在厚度方向上的总的渗透率。
L.James Lee 通过实验研究得出结论:高渗透介质的渗透率直接决定着充模流动时间,而纤维增强材料的渗透率不起决定作用。
因此高渗透介质可以提高充模速度。
2.2 引流槽辅助VARTM 工艺虽然采用高渗透介质辅助VART M 工艺可以较大地提高充模流动速度,但是这种提高相对于某些特殊性能(比如凝胶时间难以调控)的树脂来讲还是不够的,并且高渗透介质辅助成型还带来了固体废物的问题。
废弃的高渗透介质及剥离层不但会造成环境污染,还提高了制作成本,因此对于厚壁制品,采用引流槽辅助VART M 工艺有着更加实际的意义。
该工艺要求制品厚度达到能够在单面或中间加入低密度材料(如泡沫)夹层。
当然这种夹层可以更有效地降低制品重量,并有可能提高某些方面的应用性能。
引流槽辅助VART M 工艺结构由图4所示。
图4 真空辅助VART M 结构引流槽的数量及其尺寸与制品规格有关。
引流槽的设计直接决定树脂胶液对纤维增强材料的浸润程度。
在该工艺中,注射流道直接与引流槽入口相连,但是排气槽和引流槽出口要保持一定距离。
对于薄壁制品排气槽和引流槽出口的距离应为2倍的引流槽间距,对厚壁制品,这个距离与制品厚度和纤维增强材料横向渗透率有关。
树脂胶液的粘度直接决定着充模时间。
高粘度树脂胶液的充模流动行为遵从达西定理。
树脂胶液粘度与流动时间成线性关系,低粘度树脂胶液的充模流动行为不符合达西定理.这是因为低粘度树脂胶液在注射口和引流槽中流动速度非常快,表面张力起着主要作用。
树脂胶液在引流槽中的流动可看作是一维孔隙中的流动,单个引流槽及其所对应的纤维增强材料的渗透率用等价渗透率K eq 来计算:K eq=1HW ∑n =1,3,5 (8)n πβ3nW -sin (βn W )βn-1-K β2n -Kαβn sinh (βn W )-cosh (βn W )sinh (βn W )+Kαβn cosh (βnW )cosh (βn W )-1βn (5)(下转第23页)812001年1月真空辅助RT M 成型技术的研究FRP/C M 20011No.1产。
假如经检测后,由于工艺控制不严等原因造成模腔不符合要求,就此报废,重新开模未免太可惜。
按照我们的经验,可以有两种补救办法,①可以报废其中一片模具,再重新开一片;②可以利用RT M 工艺自身的特点进行修补,一般可以把其中一片模具表面胶衣层凿掉,然后铺上玻璃纤维增强材料,另一片模具则贴上蜡片,喷涂胶衣,然后合模注射,待固化后脱模处理,即可交付使用。
METH OD OF FRP MOU LD SIZE AN D CAVIT Y THICKNESS CONTR OL IN RTMY uan Hauizhou Abstract : This paper introduces how to manu fac 2ture the FRP m ould for RT M and the size and the thickness of m ould cavity is quite accurate through choosing raw materials and controlling process technology.K eyw ords : RT M raw materials process technology m ould 收稿日期:2000Ο06Ο21(上接第18页)这里βn =n πH,H 和W分别为引流槽的深度和宽度,K 为纤维增强材料的渗透率。
引流槽内的树脂胶液浸透纤维增强材料的流动从图5中能清楚的看到,依据质量守恒关系,单个引流槽中树脂胶液的分配按下面方程计算:Q in =Q out +Q leak(6)Q out 和Q in 分别代表流出和流入的树脂胶液,遵从达西定理:Q out =K eq μP i +1,n -P i ,ndlA n(7)图5 渗流模型Q in =K eq μP i ,n -P i -I ,ndlA n(8)A n 是树脂胶液在相邻引流槽对应纤维增强材料中交叉流动面积,P i -1,n ,P i ,n ,P i +1,n 代表注射压力。
Q leak 代表从引流槽相纤维增强材料浸透树脂胶液量。
Q leak =K x μP i ,n d fill hdl(9)d fill 为树脂胶液流动前缘到引流槽形心的距离。
由于这种引流槽的渗透率远远大于任何一种高渗透性介质,因此树脂总是先注满这些引流槽,然后才从引流槽注入纤维增强材料。
大型制品整个注射过程就可以被看作是被引流槽分解了的数个(与引流槽数量有关)小的注射过程。
因此对于厚壁制品而言,充模流动时间几乎等于单个引流槽内树脂在纤维增强材料厚度方向的浸透时间。
这大大地缩短了充模周期。
相对于高渗透介质辅助VART M 而言,引流槽辅助VART M 工艺充模速度可以提高17倍。
3 结束语我国玻璃钢工业处于蓬勃发展时期。
在国防、船舶、桥梁、航空工业等领域,这种低成本、高性能的VART M 制品会越来越受到青睐,因此研制或引进类似工艺方法,一定能促进我国玻璃钢工业的发展。
参考文献1 Plastics T echnology.M arch ,19952 X iu D ong Sum ,shoujie Li and L James Lee.P olymer C om posites ,1998;19:807STU DY ON VACUU M -ASSISE D RESIN TRANSFER MOLDINGLi Bais ong Wang Jihui Deng Jinglan(State Material Synthesis K ey Lab.,Wuhan University of T echnology )Abstract : The Study introduced tw o kinds of vacuum -assisted resin trans fer m olding ,one based on high -perme 2able medium ,the other based on grooves.The tw o kinds of vacuum -assisted resin trans fer m olding will find m ore uses in the com posite production.K eyw ords : RT M vacuum -assisted high -permeable medium grooves 收稿日期:2000Ο05Ο2232 2001年1月玻璃钢/复合材料FRP/C M 20011No.1。