真空辅助树脂传递模塑工艺
真空辅助树脂传递模塑工艺

真空辅助树脂传递模塑工艺真空辅助树脂传递模塑工艺(VARTM/SCRIMP)适用于质量要求高、小批量和尺寸较大的制品。
它和传统的热压罐成型工艺相比,具有模具低成本,树脂室温固化以及几乎不受限制的制品尺寸等突出的特点。
在国外VAR TM已成功地用于舰船、军事设施、国防工程、航空和民用工业等领域。
目前,真空辅助树脂传递注塑中应用最广泛的工艺之一,SCRIMP TM成型工艺,是在19世纪80年代后期在RTM 工艺基础上发展起来的以低成本、适合制作大型复合材料制品的成型工艺。
该加工工艺的成品有较好的品质,如:孔隙率低、纤维含量高,和良好的机械性能,并且可以将挥发性有毒气体的排放量控制在最小的程度。
SCRIMP真空辅助树脂传递注塑是利用薄膜将增强材料密封于单边模具上,完全借助于真空将低黏度树脂吸入,利用高渗透率介质沿增强材料的表面快速浸渍,并同时向增强材料厚度方向进行浸润的加工工艺。
用这种方法加工的复合材料,纤维含量高,制品力学性能优良,而且产品尺寸不受限制,尤其适合制作大型制品。
最近,由于树脂体系和纺织增强材料成型技术的不断发展,航空制造者们也对VAR TM表现出了浓厚的兴趣,主要表现为采用碳纤维-环氧树脂、碳纤维-双马来酰亚胺树脂的复合材料。
几种常用的纺织复合材料增强体和传统的开模成型工艺相比,SCRIMP成型工艺具有许多的优点。
SCRIMP工艺比手工铺放节约成本约50%,树脂浪费率低于5%,特别是加工过程的环保性,是SCRIM P工艺最突出的优点。
在同样原材料的情况下,与手糊构件相比,复合材料的强度、刚度或硬度及其它的物理特性可提高30%-50%以上。
产品质量不受操作人员影响,产品性能的均匀性和重复性比开模产品好得多,缺陷也少得多。
真空辅助树脂传递模塑成型工艺研究

第14期2020年5月No.14May ,2020作者简介:林涛(1984—),男,江西新余人,硕士;研究方向:风力发电机组叶片制造工艺。
真空辅助树脂传递模塑成型工艺研究江苏科技信息Jiangsu Science &Technology Information林涛,何明,陶生金(国电联合动力技术(连云港)有限公司,江苏连云港222002)摘要:为研究分析风力发电机叶片真空辅助树脂传递模塑成型(VARTM )工艺的影响因素,文章通过采用不同导流网密度、玻纤布型号、玻纤布尺寸、玻纤布铺层厚度研究了其对VARTM 工艺环氧树脂体系导流时间的影响,同时测量对应样品的含胶量,对比分析了VARTM 制品含胶量的影响因素。
关键词:风力发电机叶片;真空辅助树脂传递模塑成型;导流时间;含胶量中图分类号:TB33文献标志码:A 0引言目前应用较广的先进轻质的复合材料,如玻纤/碳纤铺层增强环氧树脂复合材料,因其相对其他材料具有更好的比强度和比模量,较好的抗腐蚀性和疲劳特性,特别是其层铺特性决定了其有非常灵活的材料力学性能设计性。
在风电叶片领域,玻纤/碳纤铺层增强环氧树脂复合材料已经成为叶片设计的主流[1]。
真空辅助树脂传递模塑成型(Vacuum Assisted Resin Transfer Molding ,VARTM )工艺作为一种典型的低成本热固性树脂流体成型工艺已广泛应用于风力发电机组复合材料叶片的制备[2]。
VARTM 工艺具有其他传统工艺无法比拟的优点:它能够用来制造超大型整体复合材料的单一部件,部件整体质量均一,质量控制好,成型时间短,设备要求低,成本低,VOC排放等污染少[3-5]。
叶片制造的大型化和高成型质量、高生产效率要求非常适合采用VARTM 工艺进行生产[6]。
VARTM 工艺的一般实现方式为:首先,在叶片模具上铺设增强材料(包括纤维增强材料玻璃纤维、碳纤维或混编纤维、BALSA 芯材、PVC 或PET 芯材等),其次,铺设布置导流系统和抽气系统,再次用真空袋膜整体封闭再抽真空,最后将液态树脂体系从主导流管路导入,由真空形成的负压动力将流体树脂引入最终到达抽气系统侧,完成树脂对增强材料的完全浸润并固化成型[7]。
RTM技术工艺详解
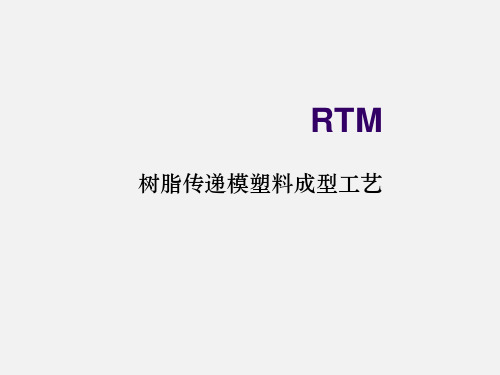
增强材料
由于在RTM成型过程中,增强材料在模具型腔 中要经过带压树脂流动充模过程,会带动或充 散纤维,造成制品出现“冲浪”或“跑道”现 象。因此,为保证制品质量,RTM工艺适用于 采用长纤维和连续纤维织物作为增强材料
工艺因素
影响RTM工艺的因素
VARTM(真空辅助RTM)工艺
一般RTM工艺在树脂注入时,模具型腔内可积起几吨压力。 通过使用了真空,模具内形成这种压力的趋势得到了减少, 因而增加了使用更轻模具的可能性,真空的使用也可提高 玻璃纤维的含量,而且有助于树脂对纤维的浸渍。纤维含 量可达65%以上,空隙率小于2%。
VARTM工艺过程
ห้องสมุดไป่ตู้合模
注射树脂
RTM – 脱模
RTM的优点
无需胶衣涂层即可为 构件提供光滑表面, 能制造出具有良好表 面的高精度复杂制品
模具制造及选材灵 活性大,设备及模 具投资小,产品只 需做小的修边
产品铺层过程中 可加入嵌件及对 局部进行加强
制品纤维含量高, 空隙率低(<0.2%)
成型过程中挥发物少, 车间环境及气味较好
在制作高质量RTM制品时,会让出口流出一定 量的树脂以后才结束充模。
目的是改善树脂对纤维的浸渍程度及排出微观 气泡。即改善了纤维与树脂的物理结合强度, 又改善了制品的密实程度。
一般浪费树脂量可达模制品重量的1/3~2/3。
注胶压力
压力的高低决定模具的材料要求和结构设计, 高压力需要高强度、高刚度和大的合模力。
基体树脂
室温或工作温度下具有低的粘度(小于1.0Pas) 及一定长的适用期
树脂对增强材料具有良好的浸润性、匹配性、 粘附性
树脂在固化温度下具有良好的反应性且后处理 温度不应过高
树脂传递模塑料成型工艺

胶衣准备
铺层
合模
模具 准备
脱模
固化
树脂 注射
后处理
检验
制品
RTM成型工艺流程图
树脂传递模塑料成型工艺
RTM-模具准备
1.检查模具有无缺损,并 2.
用压缩空气把模具表面的 疏
杂志清楚干净。注射口、 通
排气口设计是否合理。
进
料
口
和
排
气
口
是
重 点 树脂传递模塑料成型工艺
进料口
排气口
紧固的方式通常有两种 1.搭扣紧固 2.螺栓紧固
树脂传递模塑料成型工艺
搭扣紧固
树脂传递模塑料成型工艺
螺栓紧固
树脂传递模塑料成型工艺
合模类型
上下模完全靠螺栓锁 紧至上下定位销完全吻合
定位销完全吻合
树脂传递模塑料成型工艺
油缸或气缸举升下模与上模合模
半圆支架可以使 上模360度旋转
油缸举升上模, 并限位
树脂传递模塑料成型工艺
铰链式搭扣合模
铰链 搭扣紧固
树脂传递模塑料成型工艺
铰链
油缸举升上模, 并限位
注胶口和排气口的位置
1、中心注入 2、四周注入 四周浇注可以比中心浇注充模时间减少60%以上,孔隙率可 以比之降低25%以上,同时也能提高一定的力学性能。 另外还有真空辅助和充模时间的控制。
树脂传递模塑料成型工艺
模具的密封
密封是整个模具制作过程中较为关键的一步,根 据产品大小结构的不同大致分为以下7种方法: 矩形密封、半圆形密封、蘑菇形密封、半圆形+V 型两道密封、圆形真空密封、圆形充气密封、半 圆形两道密封。
树脂传递模塑料成型工艺
复合材料树脂渗透成型工艺(详细)
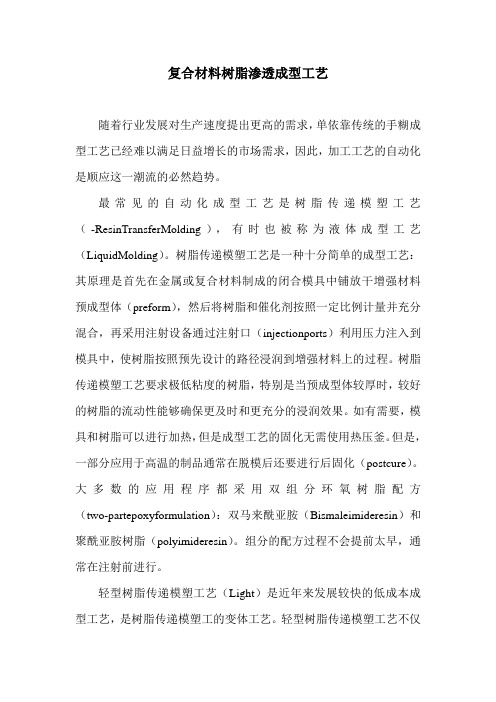
复合材料树脂渗透成型工艺随着行业发展对生产速度提出更高的需求,单依靠传统的手糊成型工艺已经难以满足日益增长的市场需求,因此,加工工艺的自动化是顺应这一潮流的必然趋势。
最常见的自动化成型工艺是树脂传递模塑工艺(-ResinTransferMolding),有时也被称为液体成型工艺(LiquidMolding)。
树脂传递模塑工艺是一种十分简单的成型工艺:其原理是首先在金属或复合材料制成的闭合模具中铺放干增强材料预成型体(preform),然后将树脂和催化剂按照一定比例计量并充分混合,再采用注射设备通过注射口(injectionports)利用压力注入到模具中,使树脂按照预先设计的路径浸润到增强材料上的过程。
树脂传递模塑工艺要求极低粘度的树脂,特别是当预成型体较厚时,较好的树脂的流动性能够确保更及时和更充分的浸润效果。
如有需要,模具和树脂可以进行加热,但是成型工艺的固化无需使用热压釜。
但是,一部分应用于高温的制品通常在脱模后还要进行后固化(postcure)。
大多数的应用程序都采用双组分环氧树脂配方(two-partepoxyformulation):双马来酰亚胺(Bismaleimideresin)和聚酰亚胺树脂(polyimideresin)。
组分的配方过程不会提前太早,通常在注射前进行。
轻型树脂传递模塑工艺(Light)是近年来发展较快的低成本成型工艺,是树脂传递模塑工的变体工艺。
轻型树脂传递模塑工艺不仅具备工艺的所有特点,还降低了成型工艺对一系列指标的要求,例如,注射压力,真空耦合(coupledwithvacuum),和模具的造价和刚性指标。
树脂传递模塑工艺具有许多显著的优点。
一般来说,在树脂传递模塑工艺过程中所使用的干预成型体和树脂材料的价格都比预浸料便宜,而且还可以在室温下存放。
利用这种工艺可以生产较厚的净成形零件,同时免去许多后续加工程序。
该工艺还能帮助生产尺寸精确,表面工艺精湛的复杂零件。
RTM相关资料

RTM相关资料1.前言所谓闭模成型工艺就是在阴、阳模闭合的情况下成型复合材料构件的工艺方法。
SMC、BMC模压、注射成型、RTM、VEC技术都属闭模成型工艺。
由于环境法的制定和对产品要求的提高使敞模成型复合材料日益受到限制,促使了闭模成型技术的应用,近年来尤其促进了RTM技术的革新和发展。
2.RTM的类型RTM工艺,即树脂传递模塑工艺,是一种新型的模压成型方法。
它具有模具造价低、生产周期短、劳动力成本低、环境污染少、制造尺寸精确、外形光滑、可制造复杂产品等优点。
40年代来,该工艺是为适应飞机雷达罩成型而发展起来的。
目前,RTM成型工艺己广泛应用于建筑、交通、电讯、卫生、航天航空等领域。
下面介绍几种RTM技术。
1)TM,树脂传递模塑。
该技术源自聚氨酯技术,成型时关闭模具,向预制件中注入树脂,玻纤含量低,约20-45%。
2)VARIT,真空辅助树脂传递注塑。
该技术利用真空把树脂吸入预制件中,同时也可压入树脂,真空度约10-28英寸汞柱。
3)VARTM,真空辅助树脂传递注塑。
制品孔隙一般较少,玻纤含量可增高。
4)VRTM,真空树脂传递模塑。
5)VIP,真空浸渍法。
6)VIMP,可变浸渍塑法。
树脂借助真空或自重移动,压实浸渍。
7)TERTM,热膨胀RTM。
在预制件中插入世材,让树脂浸渍并对模具与成形品加热。
芯材受热膨胀,压实铺层。
利用这种压实作用,结合表面加压成型。
8)RARTM,橡胶辅助RTM。
在TERTM方法中不用芯材而用橡胶代之。
橡胶模具压紧成型品,使孔隙大大减少,玻纤含量可高达60-70%。
9)RIRM,树脂注射循环模塑。
真空与加压结合,向多个模具交替注入树脂,使树脂循环,直至预制件被充分浸透。
10)CIRTM,Co-Injection RTM。
共注射RTM,可注入几种不同的树脂,也可使用几种预制件,可利用真空袋和柔性表面的模具。
11)RLI,树脂液体浸(渗)渍。
在下模内注入树脂,入入预制件后覆盖上模,加热并用热压釜的成型压力成型。
树脂渗透工艺

复合材料的树脂渗透成型工艺树脂渗透工艺:随着行业发展对生产速度提出更高的需求,单依靠传统的手糊成型工艺已经难以满足日益增长的市场需求,因此,加工工艺的自动化是顺应这一潮流的必然趋势。
最常见的自动化成型工艺是树脂传递模塑工艺(-ResinTransferMolding),有时也被称为液体成型工艺(LiquidMolding)。
树脂传递模塑工艺是一种十分简单的成型工艺:其原理是首先在金属或复合材料制成的闭合模具中铺放干增强材料预成型体(preform),然后将树脂和催化剂按照一定比例计量并充分混合,再采用注射设备通过注射口(injectionports)利用压力注入到模具中,使树脂按照预先设计的路径浸润到增强材料上的过程。
树脂传递模塑工艺要求极低粘度的树脂,特别是当预成型体较厚时,较好的树脂的流动性能够确保更及时和更充分的浸润效果。
如有需要,模具和树脂可以进行加热,但是成型工艺的固化无需使用热压釜。
但是,一部分应用于高温的制品通常在脱模后还要进行后固化(postcure)。
大多数的应用程序都采用双组分环氧树脂配方(two-partepoxyformulation):双马来酰亚胺(Bismaleimideresin)和聚酰亚胺树脂(polyimideresin)。
组分的配方过程不会提前太早,通常在注射前进行。
轻型树脂传递模塑工艺(Light)是近年来发展较快的低成本成型工艺,是树脂传递模塑工的变体工艺。
轻型树脂传递模塑工艺不仅具备工艺的所有特点,还降低了成型工艺对一系列指标的要求,例如,注射压力,真空耦合(coupledwithvacuum),和模具的造价和刚性指标。
树脂传递模塑工艺具有许多显著的优点。
一般来说,在树脂传递模塑工艺过程中所使用的干预成型体和树脂材料的价格都比预浸料便宜,而且还可以在室温下存放。
利用这种工艺可以生产较厚的净成形零件,同时免去许多后续加工程序。
该工艺还能帮助生产尺寸精确,表面工艺精湛的复杂零件。
树脂传递模塑工艺
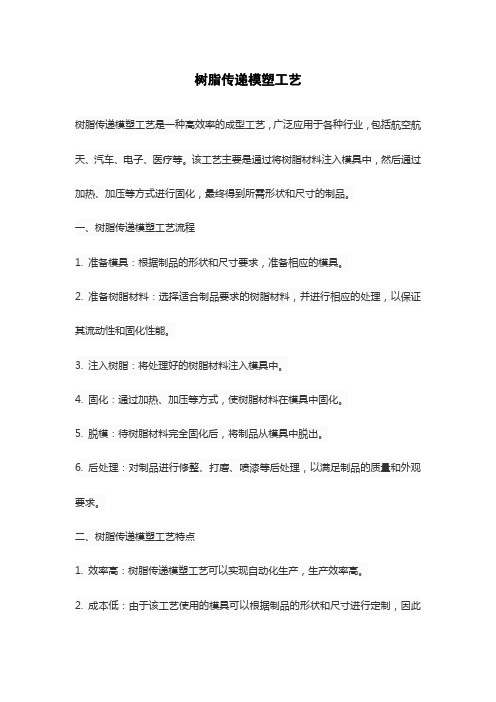
树脂传递模塑工艺树脂传递模塑工艺是一种高效率的成型工艺,广泛应用于各种行业,包括航空航天、汽车、电子、医疗等。
该工艺主要是通过将树脂材料注入模具中,然后通过加热、加压等方式进行固化,最终得到所需形状和尺寸的制品。
一、树脂传递模塑工艺流程1. 准备模具:根据制品的形状和尺寸要求,准备相应的模具。
2. 准备树脂材料:选择适合制品要求的树脂材料,并进行相应的处理,以保证其流动性和固化性能。
3. 注入树脂:将处理好的树脂材料注入模具中。
4. 固化:通过加热、加压等方式,使树脂材料在模具中固化。
5. 脱模:待树脂材料完全固化后,将制品从模具中脱出。
6. 后处理:对制品进行修整、打磨、喷漆等后处理,以满足制品的质量和外观要求。
二、树脂传递模塑工艺特点1. 效率高:树脂传递模塑工艺可以实现自动化生产,生产效率高。
2. 成本低:由于该工艺使用的模具可以根据制品的形状和尺寸进行定制,因此可以大大降低生产成本。
3. 适用范围广:树脂传递模塑工艺可以用于各种形状和尺寸的制品生产,适用范围广。
4. 环保:该工艺使用的树脂材料可以循环使用,对环境友好。
三、树脂传递模塑工艺的应用1. 航空航天领域:在航空航天领域,树脂传递模塑工艺被广泛应用于制造各种形状和尺寸的轻量化制品,如飞机零部件、卫星零部件等。
2. 汽车领域:在汽车领域,树脂传递模塑工艺被广泛应用于制造各种零部件,如汽车车门、汽车发动机罩等。
3. 电子领域:在电子领域,树脂传递模塑工艺被广泛应用于制造各种电子元器件,如电路板、电池等。
4. 医疗领域:在医疗领域,树脂传递模塑工艺被广泛应用于制造各种医疗器材,如医疗器械外壳、医疗容器等。
树脂传递模塑工艺是一种高效、环保、低成本的成型工艺,具有广泛的应用前景。
随着科技的不断发展,该工艺将会不断创新和完善,为各行各业的发展提供更加优质的技术支持。
- 1、下载文档前请自行甄别文档内容的完整性,平台不提供额外的编辑、内容补充、找答案等附加服务。
- 2、"仅部分预览"的文档,不可在线预览部分如存在完整性等问题,可反馈申请退款(可完整预览的文档不适用该条件!)。
- 3、如文档侵犯您的权益,请联系客服反馈,我们会尽快为您处理(人工客服工作时间:9:00-18:30)。
真空辅助树脂传递模塑工艺
真空辅助树脂传递模塑工艺(VARTM/SCRIMP)适用于质量要求高、小批量和尺寸较大的制品。
它和传统的热压罐成型工艺相比,具有模具低成本,树脂室温固化以及几乎不受限制的制品尺寸等突出的特点。
在国外VARTM已成功地用于舰船、军事设施、国防工程、航空和民用工业等领域。
目前,真空辅助树脂传递注塑中应用最广泛的工艺之一,SCRIMPTM成型工艺,是在19世纪80年代后期在RTM 工艺基础上发展起来的以低成本、适合制作大型复合材料制品的成型工艺。
该加工工艺的成品有较好的品质,如:孔隙率低、纤维含量高,和良好的机械性能,并且可以将挥发性有毒气体的排放量控制在最小的程度。
SCRIMP真空辅助树脂传递注塑是利用薄膜将增强材料密封于单边模具上,完全借助于真空将低黏度树脂吸入,利用高渗透率介质沿增强材料的表面快速浸渍,并同时向增强材料厚度方向进行浸润的加工工艺。
用这种方法加工的复合材料,纤维含量高,制品力学性能优良,而且产品尺寸不受限制,尤其适合制作大型制品。
最近,由于树脂体系和纺织增强材料成型技术的不断发展,航空制造者们也对VARTM表现出了浓厚的兴趣,主要表现为采用碳纤维-环氧树脂、碳纤维-双马来酰亚胺树脂的复合材料。
几种常用的纺织复合材料增强体
和传统的开模成型工艺相比,SCRIMP成型工艺具有许多的优点。
SCRIMP工艺比手工铺放节约成本约50%,树脂浪费率低于5%,特别是加工过程的环保性,是SCRIMP工艺最突出的优点。
在同样原材料的情况下,与手糊构件相比,复合材料的强度、刚度或硬度及其它的物理特性可提高30%-50%以上。
产品质量不受操作人员影响,产品性能的均匀性和重复性比开模产品好得多,缺陷也少得多。
SCRIMP由于是采用闭模成型工艺,挥发性有机物和有毒空气污染物均受到很大程度的控制,VOC排放不超过5PPm的标准,而开模成型的苯乙烯的挥发量超过500PPm。
SCRIMP工艺特别适合制造较大的制品,并且可以进行芯材、加筋结构件的一次成型以及厚的、大型复杂几何形状的制造,提高了产品的整体性,而且材料和人工的节省实为可观。
采用SCRIMP制作的构件,不论是同一构件还是构
件与构件间,制品都有保持着良好的重复性。
SCRIMP成型时树脂的消耗量可以进行严格控制,纤维体积比可高达60%,制品孔隙率小于1%。
国内外复合材料生产厂家,特别是一些造船厂、游艇工厂和风力发电叶片厂,目前已经有不少已经采用SCRIMP方法,但多数的制造技术在使用上都是以“试误(TrialandError)”的方式来积累加工经验的,这样就使得制品的品质受到很大的影响。
而要充分发挥采用SCRIMP工艺制品的特点,达到高水平的品质,生产企业应该注意诸如:浸渍时的真空度的选择、增强材料的特性、树脂黏度、树脂种类、浸渍程度、树脂的凝胶及固化情况等。
LCM工艺用纺织增强材料目前,常用的增强材料主要是玻璃纤维、碳纤维、芳纶和高密度聚乙烯纤维等等。
而增强材料的结构可以有许多种类可供选择,图1为常用的增强材料的结构形式,如机织的方格布、三维正交机织物、经编多轴向织物、2D和3D的编织织物以及缝编织物。
在复合材料加工过程中,增强材料的结构、材质和铺放形式都直接影响到树脂浸润和加工工艺。
LCM工艺技术的应用SCRIMP工艺的高纤维含量、优异的制品性能、良好的生产重复性、特别是低成本的快速成型,使其制品性能可以与航空、宇航等领域广泛采用的热压釜工艺相媲美。
随着SCRIMP技术从早期的海军军事和国防军工领域应用向民用工业的拓展,SCRIMP工艺已经大量地应用于制造船体、船舶甲板、巡逻艇、风机叶片、桥梁、运输壳体以及其它民用和海洋基础工程。
目前SCRIMP工艺可成型面积达185m2、厚度达700mm、纤维重量含量达70~80%、孔隙率低于1%的制品,其树脂浪费率低于5%,与手工铺放相比,节约劳动成本50%以上。
SCRIMP制品的主要应用领域是是船体结构,瑞典海军的隐型护卫舰Visby,艇长72m,是目前建造的最大的FRP夹芯结构,舰上的部件如船体、甲板和上层建筑都也都是用SCRIMP法制造的。
图2为作者在美国特拉华大学复合材料中心主持的《低成本制造大型流体动力表面》项目所完成的复合材料船舵的计算机模型和实际的增强体铺放。
图中模型,高38”,宽42”,为真实船舵大小的1/4。
SCRIMP工艺的另一个主要应用领域是风机叶片的制造。
国内目前的我国风机叶片制造厂家由于受市场、技术、材料及资金等方面的影响,大多采用湿法手
糊工艺,常温固化。
能够实现600KW和750KW机组叶片的批量生产。
湿法手糊工艺工艺相对简单,不需要加温加压装置,不需要昂贵的工装设备。
成型工艺具有生产效率低、劳动强度大、劳动卫生条件差、产品质量不易控制、性能稳定性不高、产品力学性能较低等的缺点,该工艺通常只用于生产叶片长度比较短和批量比较小的时候。
但对于大型的兆瓦级风力机叶片,由于叶片体形庞大,最宽处达300cm左右,最高处大于200cm,手糊成型工艺是无法胜任的。
目前,国外采用闭模的真空辅助成型工艺用于生产大型叶片(叶片长度在40m以上时)和大批量的生产。
这种工艺适宜一次成型整体的风力发电机叶片(纤维、夹芯和接头等可一次模腔中共成型),而无需二次粘接。
世界著名的叶片生产企业LM公司开发出56M的全玻纤叶片就是采用这种工艺生产的。