脱硫塔计算
氨法脱硫计算过程

氨法脱硫计算过程风量(标态):,烟气排气温度:168℃:工况下烟气量:还有约5%得水份如果在引风机后脱硫,脱硫塔进口压力约800Pa,出口压力约—200Pa,如果精度高一点,考虑以上两个因素、1、脱硫塔(1)塔径及底面积计算:塔内烟气流速:取D=2r=6、332m即塔径为6。
332米,取最大值为6、5米。
底面积S=πr2=3.14×3、252=33、17m2塔径设定时一般为一个整数,如6、5m,另外,还要考虑设备裕量得问题,为以后设备能够满足大气量情况下符合得运行要求。
(2)脱硫泵流量计算:液气比根据相关资料及规范取L/G= 1.4(如果烟气中二氧化硫偏高,液气比可适当放大,如1.5、)①循环水泵流量:较高,脱硫塔喷淋层设计时应选取为4层设计,每层喷淋设计由于烟气中SO2安装1台脱硫泵,476÷4=119m3/h,泵在设计与选型时,一定要留出20%左右得裕量。
裕量为:119×20%=23.8 m3/h, 泵总流量为:23。
8+119=142.8m3/h,参考相关资料取泵流量为140 m3/h。
配套功率可查相关资料,也可与泵厂家进行联系确定。
(3)吸收区高度计算吸收区高度需按照烟气中二氧化硫含量得多少进行确定,如果含量高,可适当调高吸收区高度、2。
5米×4层/秒=10米,上下两层中间安装一层填料装置,填料层至下一级距离按1米进行设计,由于吸收区底部安装有集液装置,最下层至集液装置距离为3。
7米-3。
8米进行设计、吸收区总高度为13.7米—13、8米。
(4)浓缩段高度计算浓缩段由于有烟气进口,因此,设计时应注意此段高度,浓缩段一般设计为2层,每层间距与吸收区高度一样,每层都就是2.5米,上层喷淋距离吸收区最下层喷淋为3、23米,下层距离烟气进口为5米,烟气进口距离下层底板为2。
48米。
总高为10、71米。
(5)除雾段高度计算除雾器设计成两段、每层除雾器上下各设有冲洗喷嘴。
双碱法烟气脱硫计算

双碱法计算过程标态:h Nm Q /4000030=65℃:h m Q /49523400002736527331=⨯+= 还有约5%的水份如果在引风机后脱硫,脱硫塔进口压力约800Pa ,出口压力约-200Pa ,如果精度高一点,考虑以上两个因素。
1、脱硫塔⑴ 塔径及底面积计算:塔内流速:取s m v /2.3=m v Q r r v vs Q 17.12.314.33600/49532121=⨯==⇒⋅⋅==ππ D=2r=2.35m 即塔径为2.35米。
底面积S=∏r 2=4.3m 2塔径设定为一个整数,如2.5m⑵ 脱硫塔高度计算:液气比取L/G= 4,烟气中水气含量设为8%SO 2如果1400mg/m3,液气比2.5即可,当SO2在4000mg/m3时,选4① 循环水泵流量:h m m l HG Q G L Q /1821000)08.01(495324)/(100033=-⨯⨯=⨯⨯= 取每台循环泵流量=Q 91m 。
选100LZ A -360型渣浆泵,流量94m 3/h ,扬程22.8米, 功率30KW ,2台② 计算循环浆液区的高度:取循环泵8min 的流量,则H 1=24.26÷4.3=5.65m如此小炉子,不建议采用塔内循环,塔内循环自控要求高,还要测液位等,投资相应大一点。
采用塔外循环,泵的杨程选35m ,管道采用碳钢即可。
③ 计算洗涤反应区高度停留时间取3秒,则洗涤反应区高度H2=3.2×3=9.6m④除雾区高度取6米H3=6m⑤脱硫塔总高度:H=H1+H2+H3=5.65+9.6+6=21.3m塔体直径和高度可综合考虑,直径大一点,高度可矮一点,从施工的方便程度、场地情况,周围建筑物配套情况综合考虑,可适当进行小的修正。
如采用塔内循环,底部不考虑持液槽,进口管路中心线高度可设在2.5m,塔排出口设为溢流槽,自流到循环水池。
塔的高度可设定在16~18m2、物料恒算每小时消耗99%的NaOH 1.075Kg。
氨法脱硫
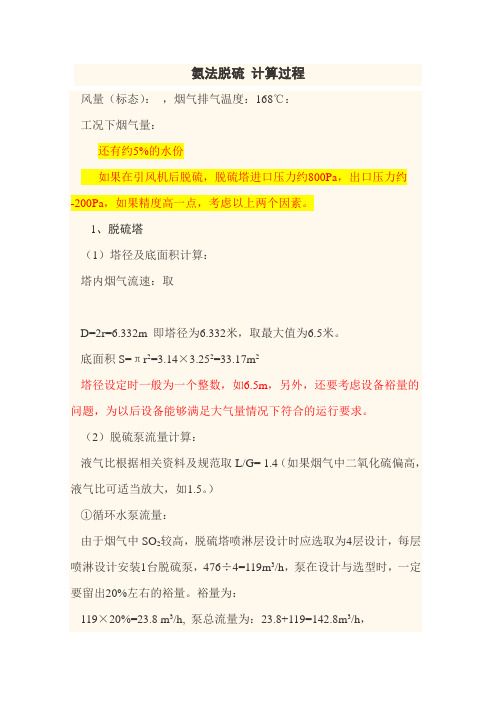
氨法脱硫计算过程风量(标态):,烟气排气温度:168℃:工况下烟气量:还有约5%的水份如果在引风机后脱硫,脱硫塔进口压力约800Pa,出口压力约-200Pa,如果精度高一点,考虑以上两个因素。
1、脱硫塔(1)塔径及底面积计算:塔内烟气流速:取D=2r=6.332m 即塔径为6.332米,取最大值为6.5米。
底面积S=πr2=3.14×3.252=33.17m2塔径设定时一般为一个整数,如6.5m,另外,还要考虑设备裕量的问题,为以后设备能够满足大气量情况下符合的运行要求。
(2)脱硫泵流量计算:液气比根据相关资料及规范取L/G= 1.4(如果烟气中二氧化硫偏高,液气比可适当放大,如1.5。
)①循环水泵流量:由于烟气中SO2较高,脱硫塔喷淋层设计时应选取为4层设计,每层喷淋设计安装1台脱硫泵,476÷4=119m3/h,泵在设计与选型时,一定要留出20%左右的裕量。
裕量为:119×20%=23.8 m3/h, 泵总流量为:23.8+119=142.8m3/h,参考相关资料取泵流量为140 m3/h。
配套功率可查相关资料,也可与泵厂家进行联系确定。
(3)吸收区高度计算吸收区高度需按照烟气中二氧化硫含量的多少进行确定,如果含量高,可适当调高吸收区高度。
2.5米×4层/秒=10米,上下两层中间安装一层填料装置,填料层至下一级距离按1米进行设计,由于吸收区底部安装有集液装置,最下层至集液装置距离为3.7米-3.8米进行设计。
吸收区总高度为13.7米-13.8米。
(4)浓缩段高度计算浓缩段由于有烟气进口,因此,设计时应注意此段高度,浓缩段一般设计为2层,每层间距与吸收区高度一样,每层都是2.5米,上层喷淋距离吸收区最下层喷淋为3.23米,下层距离烟气进口为5米,烟气进口距离下层底板为2.48米。
总高为10.71米。
(5)除雾段高度计算除雾器设计成两段。
每层除雾器上下各设有冲洗喷嘴。
脱硫计算公式比较全

湿法脱硫系统物料平衡计算基础数据(1)待处理烟气烟气量:1234496Nm3/h(wet)、1176998 Nm3/h(dry)烟气温度:114C烟气中SO2浓度:3600mg/Nm3烟气组成:石灰石浓度:96.05%平衡计算(1)原烟气组成计算(2)烟气量计算1、①-②(增压风机出口 T GGH 出口):取GGH 的泄漏率为0.5%,则GGH 出口总烟气量为1234496 Nm 3/h (1-0.5%)=1228324Nm 3/h=1629634kg/h泄漏后烟气组分不变,但其质量分别减少了 0.5%,见下表。
温度为70 C 。
2、⑥-⑦(氧化空气):假设脱硫塔设计脱硫率为95.7%,即脱硫塔出口二氧化硫流量为 3778 X(1-95.7%) =163 kg/h ,二氧化硫脱除量=(3778-163) /64.06=56.43kmol/ho取 O/S=4需空气量=56.43 4/2/0.21=537.14kmol/h 28.36 (空气分子量)=15499.60kg/h,约 12000Nm 3/ho其中氧气量为 537.14 kmol/h 0.21=112.80 kmol/h 32=3609.58kg/h 氮气量为 537.14 kmol/h 0.79=424.34 kmol/h 28.02=11890.02kg/h= 氧化空气进口温度为20r ,进塔温度为80^03、②-③(GGH 出口-脱硫塔出口):烟气蒸发水量计算:(40C)=0.2520 kcal/kg.r 。
Cp 烟气=(0.2536+0.2520) /2=0.2528 kcal/kg.C氧化空气进口温度为 80r ,其比热约为 0.2452 1)假设烟气进塔温度为70C ,在塔内得到充分换热, 由物性数据及烟气中的组分,可计算出进口烟气的比热约为出口温度为40^00.2536kcal/kg.r, Cpkcal/kg.r, Cp ( 40r)=0.2430kcal/kg.C 。
脱硫系统常用计算公式

1) 由于烟气设计资料,常常会以不同的基准重复出现多次,(如:干基湿基,标态实际态,实际O2 等),开始计算前一定要核算统一,如出现矛盾,必须找出正确的一组数据,避免原始数据代错。
常用折算公式如下:烟气量(dry)=烟气量(wet) >(1-烟气含水量%)实际态烟气量=标态烟气量>气压修正系数x温度修正系数烟气量(6%02) = ( 21-烟气含氧量)/ ( 21 -6%)S02 浓度(6%02 ) = ( 21 - 6%) / (21 -烟气含氧量)S02 浓度( mg/Nm3 ) =S02 浓度( ppm) x2.857物料平衡计算1 )吸收塔出口烟气量G2G2= (G1 x (1 - mw1) X(P2/(P2-Pw2)) (X —mw2 )+ G3X (1- 0.21/K) ) >(P2/(P2-Pw2))G1: 吸收塔入口烟气流量mw1: 入口烟气含湿率P2:烟气压力Pw2 :饱和烟气的水蒸气分压说明: Pw2 为绝热饱和温度下的水蒸气分压,该值是根据热平衡计算的反应温度,由烟气湿度表查得。
(计算步骤见热平衡计算)2) 氧化空气量的计算根据经验,当烟气中含氧量为6%以上时,在吸收塔喷淋区域的氧化率为50 - 60 %。
采用氧枪式氧化分布技术,在浆池中氧化空气利用率n 02=25-30%,因此,浆池内的需要的理论氧气量为:S=(G1 x q1-G2 x q2) x(1-0.6)/2/22.41所需空气流量QreqQreq=S x22.4/(0.21 0.x3)G3= Qreq >KG3:实际空气供应量K :根据浆液溶解盐的多少根据经验来确定,一般在 2.0-3左右。
3) 石灰石消耗量计算W1=100x qs xnsW1: 石灰石消耗量qs: :入口S02 流量n S兑硫效率4) 吸收塔排出的石膏浆液量计算W2=172xx qs xn s/SsW2:石膏浆液量Ss石膏浆液固含量5) 脱水石膏产量的计算W3=172xx qs xn s/SgW3: 石膏浆液量Sg:脱水石膏固含量(1-石膏含水量)6) 滤液水量的计算W4=W3-W2W3: 滤液水量7) 工艺水消耗量的计算W5=18x (G4-G1-G3 x(1-0.21/K))+W3 (1x-Sg)+36x qs x n+W s WT蒸发水量石膏表面水石膏结晶水排放废水。
氨法脱硫计算过程

氨法脱硫计算过程风量(标态):,烟气排气温度:168℃:工况下烟气量:还有约5%的水份如果在引风机后脱硫,脱硫塔进口压力约800Pa,出口压力约-200Pa,如果精度高一点,考虑以上两个因素。
1、脱硫塔(1)塔径及底面积计算:塔内烟气流速:取D=2r=6.332m 即塔径为6.332米,取最大值为6.5米。
底面积S=πr2=3.14×3.252=33.17m2塔径设定时一般为一个整数,如6.5m,另外,还要考虑设备裕量的问题,为以后设备能够满足大气量情况下符合的运行要求。
(2)脱硫泵流量计算:液气比根据相关资料及规范取L/G= 1.4(如果烟气中二氧化硫偏高,液气比可适当放大,如1.5。
)①循环水泵流量:较高,脱硫塔喷淋层设计时应选取为4层设计,每层喷淋设计由于烟气中SO2安装1台脱硫泵,476÷4=119m3/h,泵在设计与选型时,一定要留出20%左右的裕量。
裕量为:119×20%=23.8 m3/h, 泵总流量为:23.8+119=142.8m3/h,参考相关资料取泵流量为140 m3/h。
配套功率可查相关资料,也可与泵厂家进行联系确定。
(3)吸收区高度计算吸收区高度需按照烟气中二氧化硫含量的多少进行确定,如果含量高,可适当调高吸收区高度。
2.5米×4层/秒=10米,上下两层中间安装一层填料装置,填料层至下一级距离按1米进行设计,由于吸收区底部安装有集液装置,最下层至集液装置距离为3.7米-3.8米进行设计。
吸收区总高度为13.7米-13.8米。
(4)浓缩段高度计算浓缩段由于有烟气进口,因此,设计时应注意此段高度,浓缩段一般设计为2层,每层间距与吸收区高度一样,每层都是2.5米,上层喷淋距离吸收区最下层喷淋为3.23米,下层距离烟气进口为5米,烟气进口距离下层底板为2.48米。
总高为10.71米。
(5)除雾段高度计算除雾器设计成两段。
每层除雾器上下各设有冲洗喷嘴。
脱硫塔基础计算模板

π
D1 2
2
HL
12
1.1
π
D1 2
+
a1 +
2
a2
+
LL
= 14.363
+
a1 +
2
a2
h2 +
π
D1 2
+
2
a1
( h1 +
0.1)
= 761.271
π
D1 2
2
HL
12 +
G+
G1 +
V
25 +
LL +
Fy +
Fv
...
F1 :=
+
π
D1 2
+
a1
+
a2
2
-
D1 2
+
a1
2
h1
18
π
D1 2
+
a1
+
2
a2
= 203.962
F0 = 220
风压高度系数:
顶出尺寸时产生竖向压力,
Fy :=
π
9 2
2
3
0
入口中心标高:H3 := 18.05 出口中心标高:H4 := 44.35
桁架时两柱脚荷载合计:
Fv :=
π 6.02 0.006 7.85 1.8
10 +
3.012 8
15 11 + 120 0 = 0
基础混凝土量:
V :=
π
D1 2
净烟道桁架活载M4:
D2 M4 := Fv = 0
氨法脱硫计算过程

氨法脱硫计算过程风量(标态):,烟气排气温度:168℃:工况下烟气量:还有约5%的水份如果在引风机后脱硫,脱硫塔进口压力约800Pa,出口压力约-200Pa,如果精度高一点,考虑以上两个因素。
1、脱硫塔(1)塔径及底面积计算:塔内烟气流速:取D=2r=6.332m 即塔径为6.332米,取最大值为6.5米。
底面积S=πr2=3.14×3.252=33.17m2塔径设定时一般为一个整数,如6.5m,另外,还要考虑设备裕量的问题,为以后设备能够满足大气量情况下符合的运行要求。
(2)脱硫泵流量计算:液气比根据相关资料及规范取L/G= 1.4(如果烟气中二氧化硫偏高,液气比可适当放大,如1.5。
)①循环水泵流量:较高,脱硫塔喷淋层设计时应选取为4层设计,每层喷淋设计由于烟气中SO2安装1台脱硫泵,476÷4=119m3/h,泵在设计与选型时,一定要留出20%左右的裕量。
裕量为:119×20%=23.8 m3/h, 泵总流量为:23.8+119=142.8m3/h,参考相关资料取泵流量为140 m3/h。
配套功率可查相关资料,也可与泵厂家进行联系确定。
(3)吸收区高度计算吸收区高度需按照烟气中二氧化硫含量的多少进行确定,如果含量高,可适当调高吸收区高度。
2.5米×4层/秒=10米,上下两层中间安装一层填料装置,填料层至下一级距离按1米进行设计,由于吸收区底部安装有集液装置,最下层至集液装置距离为3.7米-3.8米进行设计。
吸收区总高度为13.7米-13.8米。
(4)浓缩段高度计算浓缩段由于有烟气进口,因此,设计时应注意此段高度,浓缩段一般设计为2层,每层间距与吸收区高度一样,每层都是2.5米,上层喷淋距离吸收区最下层喷淋为3.23米,下层距离烟气进口为5米,烟气进口距离下层底板为2.48米。
总高为10.71米。
(5)除雾段高度计算除雾器设计成两段。
每层除雾器上下各设有冲洗喷嘴。
- 1、下载文档前请自行甄别文档内容的完整性,平台不提供额外的编辑、内容补充、找答案等附加服务。
- 2、"仅部分预览"的文档,不可在线预览部分如存在完整性等问题,可反馈申请退款(可完整预览的文档不适用该条件!)。
- 3、如文档侵犯您的权益,请联系客服反馈,我们会尽快为您处理(人工客服工作时间:9:00-18:30)。
地震影响系数最大值 场地土的特征周期 一阶振型阻尼比 基础标高
150 0.7 13300 12800 488 170 60 3 2 300 147 120 60 24 147
H 地脚螺栓座 下限 下限 16MnR δb [σ]bt d1 δG l2 Q235-A E
'
塔器高度
mm mm mm MPa mm mm MPa mm mm mm MPa
mihi
η1k αmax Tg ξ1 γ η2 α1 F1k
塔段号 h 1 2 3 4 5 6锥段 7 8 9 10 MEi-i
2.351E+00 基本振型参与系数
地震影响系数最大值 场地土的特征周期 一阶振型阻尼比 曲线下降段的衰减系数 阻尼调整系数 对应基本振型T1的地震影响系数 N 23557 1底面 0 5.89E+07 1.28E+08 4.14E+08 1.62E+09 2.26E+09 6.86E+08 1.13E+09 1.43E+09 1.79E+09 2.80E+09 1.23E+10 17016 2底面 5000 4.25E+07 2.48E+08 1.16E+09 1.76E+09 5.57E+08 9.47E+08 1.24E+09 1.59E+09 2.52E+09 1.01E+10
自支撑脱硫塔及烟囱设计计算
计算条件
q0 [σ]t ρ Ei C1 C2 δs1 δs2 ρs φ Dob Dib l [σ]b n n1 lk [ σ] G l3 d3 δc [ σ] z 基本风压 壳体材料 设计温度下壳体材料许用应力 壳体材料密度 壳体材料弹性模量 烟囱钢板附加量 塔体钢板附加量 烟囱保温层厚度 塔体保温层厚度 保温层材料密度 焊接接头系数 基础环外径 基础环内径 两相邻筋板最大外侧间距 基础环材料的许用应力 地脚螺栓个数 地脚螺栓腐蚀裕量 对应于一个地脚螺栓的筋板数 筋板长度(高度方向) 筋板材料的许用应力 筋板内侧间距 盖板上地脚螺栓孔直径 盖板厚度 盖板与垫板材料的许用应力 400 16MnR 162 7850 194000
9 41000 47250 0.7 1.6449
10 47250 53500 0.7 1.7116
备注
体型系数 风压高度变化系数
脉动增大系数 mm 5000 B类 0.7235 0.0943 0.0267 1.0486 5000 13500 19819.36
10000 0.7410 0.1887 0.0378 1.0694 5000 13500 20544.87
2 13000 16 5000 25680 6420 55000 0 150 15000 0
3 13000 14 5000 22466 5617 42000 0 12400 0
10000
4 13000 12 5000 19254 4813 120000 0 123000 12 5000 19254 4813 80000 0 12280 0 0
4.436E-05 2.212E-05
基本振型自振周期
T1 114 . 8 N 52 ( N 56 N 57 ) 10 3
计算地震载荷及地震弯矩-按JB/T4710-2005
塔段号 mi hi mihi
1.5 3
kg mm
1 735519 2500 9.194E+10 1.149E+16 2.638E-02
偏心质量标高 mmin=m01+0.2m02+m03+m04+ma+me 5 116347 22500 8901.8 33000 1.016E+13 6锥段 23422 26500 2927.8 28000 3.641E+12 7 25768 31125 5219.0 25000 1.816E+12
3 0.25 200
0
Pa MPa kg/m mm mm mm mm kg/m
3 3
设防烈度 设计地震分组 场地土类别 地面粗糙度类别
8度(0.1g) 第一组 Ⅱ B类 0.08 0.35 0.02 500 53000 s 查表8-1 查表8-2 无实测,可取0.01~0.03 mm mm
MPa
αmax Tg ξ1
mm 2500 塔器高度 77.2 53000 1.364E+13
塔顶至该段底截面
Hi /EiIi Hi /Ei-1Ii-1 T1
3
3
圆筒段 5.627E-05
Ii
( D i ei ) 3 ei 8
3.444E-05 3.005E-05 0.296 2.783E-05 2.377E-05 s 1.822E-05 1.822E-05
8 20675 37375 1.494E+11 1.079E+18 1.525E+00 第一组
9 17583 43625 1.602E+11 1.460E+18 1.923E+00
10 19703 49875 2.195E+11 2.444E+18
备注 操作重 质心高度 求和N63 求和N64 1.814E+12 8.596E+18
2 ie 2 if
ma=0.25m01
计算基本自振周期-按JB/T4710-2005
kg 1 735519 2 102249 7500 289.7 48000 1.364E+13 3 92483 12500 53000 1213.3 43000 1.190E+13 4 156467 17500 mm 5632.6 38000 1.016E+13 8 20675 37375 7250.3 18750 1.411E+12 9 17583 43625 9805.4 12500 1.007E+12 10 19703 49875 16419.0 6250 1.007E+12 备注 操作重 1310216 质心高度 求和N52 57736.0
mm N.mm N.mm N.mm N.mm N.mm N.mm N.mm N.mm N.mm N.mm N.mm
8.28E+07 6.96E+08 1.26E+09 4.27E+08 7.66E+08 1.05E+09 1.38E+09 2.24E+09 7.90E+09
2.32E+08 7.55E+08 2.98E+08 5.85E+08 8.56E+08 1.18E+09 1.96E+09 5.86E+09
1.20E+08 3.85E+08 8.79E+08 1.38E+09
1.28E+08 5.27E+08 6.55E+08
1.76E+08 1.76E+08
计算风载荷及风弯矩-按JB/T4710-2005
塔段号 起点标高 终点标高 k1 fi q1 T 1 ξ Hit υi hit/H φzi k2i li Dei Pi mm mm N 1型
2 2
5 20500 25500 0.7 1.3503 查表8-4 25000 0.8500 0.4717 0.2788 1.4423 5000 13500 36809.05
6锥段 25500 28500 0.7 1.3992
7 28500 34750 0.7 1.4909
8 34750 41000 0.7 1.5719
2.52E+08 1.68E+08 4.03E+08 6.65E+08 9.70E+08 1.68E+09 4.14E+09
3.88E+07 2.22E+08 4.74E+08 7.65E+08 1.40E+09 2.90E+09
1.13E+08 3.59E+08 6.41E+08 1.23E+09 2.34E+09
2 102249 7500 6.641E+10 4.314E+16 1.371E-01
3 92483 12500 1.292E+11 1.806E+17 2.950E-01 0.08 0.35 0.02 0.95 1.3191 0.1238 33116 3底面 10000
4 156467 17500 3.622E+11 8.386E+17 4.886E-01 s
t
l4 d2 δz Q235-A
主要计算结果
m0 mmax mmin Mmax 塔器操作重量 塔器最大重量 塔器最小重量 塔壳底最大弯矩 1310216 1310216 374816 1.488E+10 kg kg kg N.mm T1 基本振型自振周期 0.296 s
计算质量-按JB/T4710-2005
28000 0.8644 0.5283 0.3692 1.5747 3000 9800 18138.02
34250 0.8772 0.6462 0.5060 1.7503 6250 5500 25115.98
40500 0.8872 0.7642 0.6830 1.9714 6250 5500 29827.07
10 8000 8 6250 9874 2469 0 4840 2520 0 0
备注 内径 厚度 总高 53000 壳重 174784 附件重 内件重 保温重 平台梯子 液重 偏心质量 43696 338000 22867 55870 665000 10000