第五章 离子注入低温掺杂
11-利用离子注入技术改善晶硅太阳能电池性能

个重要原因。
3 技术优势
3.1 低表面浓度发射极 低表面浓度发射极是改善电池光转化效率 的一个重要途径, 表面杂质浓度的大小直接 决定了表面复合速率 s 的大小。研究表明, 表面复合速率 s 是表面掺杂浓度的函数。在 表面浓度 2E15/cm3 到 1E18/cm3 范围内, s 随 着表面掺杂浓度增加呈亚线性增加趋势, 在 4E18/cm3 到 1E20/cm3 区间内是线性增加关 系[10]。因此降低表面掺杂浓度可以有效降 低太阳能电池的表面复合, 尤其对于较高表 面浓度的发射极。 采用离子注入的方式进行硅片前表面 掺杂, 该掺杂方式不受热扩散中所面临的固 溶度限制, 掺入杂质的浓度分布可以通过离 子注入的能量、剂量和退火工艺来调节,因 而可以实现低表面浓度掺杂。 为了说明这一 点,图 1 给出了 ECV 测量的不同注入剂量 和不同退火温度下的硅片表面的杂质浓度 分布。可以发现在同样的退火温度下(图中 的标准温度),发射极的表面浓度随着注入 剂量的降低而下降,对于注入剂量 2.3E15/cm2,其表面浓度为 3.4E20/cm3,远远 低于 POCl3 扩散形成的 8.5E20/cm3 的表面浓
图 1. ECV 测量的不同注入剂量和能量下的硅片表面的杂质浓度分布,如图曲线 1-5 所示。曲线 6 为热扩散后硅片表面的杂质浓度分布。
3.2 热氧钝化层 利用离子注入方法对半导体掺杂后, 需要高 温通氧的环境下退火激活杂质离子, 因此退 火后的硅片表面将会生长出较为致密的二 氧化硅钝化层, 从而进一步减少硅片表面的 复合。由于表面复合速率 s 是表征发射极反 向饱和电流 Joe 和少子有效寿命eff 的一个非 常重要的参数。由图 1 可以知道,随着注入 剂量的降低, 发射极的表面浓度也随之降低, 因此,反向饱和电流 Joe 也将随着降低,少 子寿命增加。 表 2 给出用 WCT-120 测量的双面离子 注入、退火、PECVD 氮化硅后的暗电压、 发射极反向饱和电流 Joe、和有效寿命eff。 通过对比可以发现,随着注入剂量的增加, 暗电压、有效寿命eff 逐渐降低、发射极反 向饱和电流 Joe 也逐渐增加,这主要是由于 发射极表面浓度增大导致表面复合增加的 缘故。对于 POCl3 扩散形成的发射极,由于 其较高的表面浓度并且没有热氧钝化层, 因 此相应的有效少子寿命eff、Joe 都会变差,
第五章 薄膜的化学气相沉积.
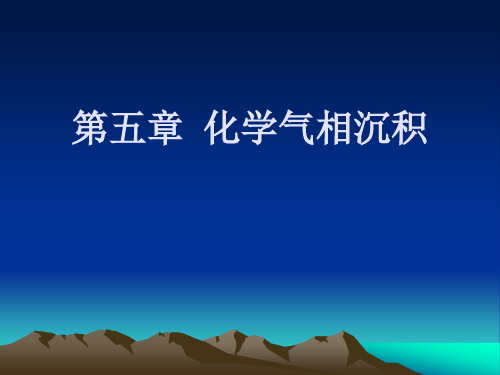
术中用来做发射极 4. 填充介质隔离技术中的深槽或浅槽。 5. 通过掺杂改变多晶硅的功函数,从而调整MOS器件的阈值
电压
5.3 CVD多晶硅的特性和制备方法
气体的流速分布和边界层,即泊 松流。
在化学气相沉积过程中,衬底表面的气体也要形成 相应的边界层,由于在边界层内,气体处于一种流 动性很低的状态,而反应物和反应产物都需要经过 扩散过程通过边界层,因此边界层的存在限制了沉 积的速度。根据
(x) 5x
Re( x)
Re(x) v0 x
(提高Re,降低边界层厚度)
4、化合反应:只要所需物质的先驱物可以气态存在并具有反 应活性,就可以利用化学反应沉积其化合物,如
SiCl4(g) + CH4(g) = SiC(s) + 4HCl(g) (1400℃) 3SiH4+4NH3=Si3N4+12H2 BCl3+NH3=BN+HCl
5.2 边界层理论
一、流动气体的边界层及影响因素
质量输运控制的CVD 质量输运过程是通过气体扩散完成的,扩散速度 与气体的扩散系数和边界层内的浓度梯度有关。 质量输运速率控制的薄膜沉积速率与主气流速度 的平方根成正比,增加气流速度可以提高薄膜沉 积速率,当气流速率大到一定程度时,薄膜的沉 积速率达到一稳定值不再变化。沉积速率转变为 由表面反应速度控制
(一般是热壁型的)
维持低压
低压CVD装置图
2、PECVD和HDPCVD
(1)PECVD使用辉光放电等离子体的能量来产生并维 持化学反应。PECVD的反应气压与LPCVD的气压差不多 (5-500Pa),但PECVD的沉积温度比LPCVD的沉积温度 低 很 多 。 如 LPCVD 沉 积 Si3N4 的 温 度 800-900C , 而 用 PECVD只需350C。因为等离子体可以促进气体分子的分 解、化合、激发和电离过程,促进反应活性基团的形成, 因而显著降低了反应沉积温度。
现代半导体器件物理与工艺(杂质掺杂详解~)

现代半导体器件物理与工艺Physics and Technology of Modern Semiconductor Devices杂质掺杂杂质掺杂所谓杂质掺杂是将可控数量的杂质掺入半导体内。
杂质掺杂的实际应用主要是改变半导体的电特性。
扩散和离子注入是半导体掺杂的两种主要方式。
方式高温扩散:一直到20世纪70年代,杂质掺杂主要是由高温的扩散方式来完成,杂质原子通过气相源或掺杂过的氧化物扩散或淀积到硅晶片的表面,这些杂质浓度将从表面到体内单调下降,而杂质分布主要是由高温面杂质浓度将从表面到体内单降杂质分布由高与扩散时间来决定。
离子注入:掺杂离子以离子束的形式注入半导体内,杂质浓度在半导体内有个峰值分布,杂质分布主要由离子质量和注入能量决定。
扩散和离子注入两者都被用来制作分立器件与集成电路,因为二者互补不足,相得益彰。
基本扩散工艺杂质扩散通常是在经仔细控制的石英高温炉管中放入半导体硅晶片并通入含有所需掺杂剂的气体混合物。
硅的温度在800-1200℃;砷化镓的温6001000扩散进入半导体内部的杂质原子数量与气体混合物中度在600-1000℃。
扩散进入半导体内部的杂质原子数量与气体混合物中的杂质分压有关。
对硅而言型掺杂剂它们在硅中都有极对硅而言,B 、P 和As 分别是常用的p 型和n 型掺杂剂,它们在硅中都有极高的固溶度,可高于5×1020cm-3。
引入方式有:固态源(BN 、As2O3、P2O5);液态源(BBr3、AsCl3、POCl3);气体源(B2H6、AsH3、PH3 ),其中液态源最常用。
使用液态源的磷扩散的化学反应如下:3225243 26POCl O P O Cl +→+在硅晶片上形成层玻璃并由硅还原出磷氯气被带走P2O5在硅晶片上形成一层玻璃并由硅还原出磷,氯气被带走。
25225 45P O Si P SiO +→+对砷化镓的扩散工艺而言,因砷的蒸汽压高,所以需要特别的方式来防止砷的分解或蒸发所造成的损失。
Ion implantation

离子注入深度
2 M 1M 2 ∆R p ≈ Rp 3 M1 + M 2
1. 离子注入靶中,其射程是一条十分曲折的路径; 离子注入靶中, 射程是一条十分曲折的路径 是一条十分曲折的路径; 2. 但在微电子工艺中,所关注的是射程在靶片法线方向上的 但在微电子工艺中, 则是投影射程的标准偏差 标准偏差, 投影长度, 投影射程R 投影长度,叫投影射程 p;△Rp则是投影射程的标准偏差, 反应了射程的分散宽度,也就是离子主要分布在Rp 反应了射程的分散宽度, 也就是离子主要分布在Rp±△Rp 范围内。 范围内。
微电子工艺学
第五章 离子注入 Ion Implantation
离子注入定义
定义:将掺杂剂通过离子注入机的离化、 定义 : 将掺杂剂通过离子注入机的离化 、 加速和质量分析, 加速和质量分析 , 形成一束由所需杂质 离子组成的高能离子流, 离子组成的高能离子流 , 打入半导体晶 片内部, 片内部 , 并通过逐点扫描完成对整块晶 片的注入。 片的注入。 离子注入的设想始于20世纪 年代, 世纪50年代 离子注入的设想始于 世纪 年代, 年代进入实用阶段。 于70年代进入实用阶段。 年代进入实用阶段
2 MVext 1 M r= 2 Vext ⇒ B = 2 B q q×r 2 × 28 ×1.67 ×10 × 20000 = −19 2 1.6 × 10 × 0.3 = 0.36T
−27
离子注入的过程
1. 从离子注入机中出来的高能离子投射到靶 的表面,绝大部分离子会进入靶内。 的表面,绝大部分离子会进入靶内。 2. 进入靶内的离子不断遭受靶原子的阻挡作 用而逐步损失能量,最终能量耗尽, 用而逐步损失能量,最终能量耗尽,停止 在靶内某处。 在靶内某处。
第五章 离子注入
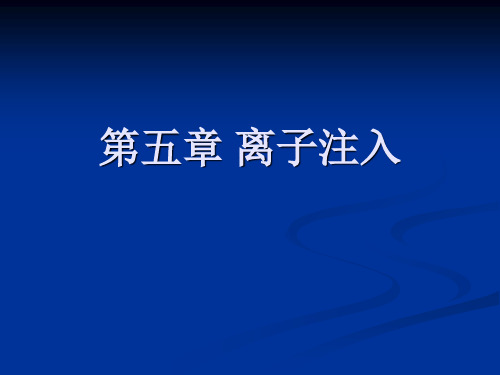
Distribution according to Gaussian function
x2 QT C x, t exp 4 Dt Dt
第五章 离子注入 实 际 工 艺 中 二 步 扩 散
第一步 为恒定表面浓度的扩散(Pre-deposition) (称为预沉积或预扩散) 控制掺入的杂质总量
电荷/动量交换导致入射离子运 动方向的改变(<核间作用)
把固体中的电子看成自由电子气,电子的阻止就类似于粘滞气 体的阻力(一阶近似)。电子阻止本领和注入离子的能量的平 方根成正比。 1/ 2 15 1/ 2 2
Se E Cvion kE , k 0.2 10 eV cm
第五章 离子注入
ETrans 4 m1m2 E 2 (m 1 m2 )
核阻止能力的一阶近似为:
m——质量, Z——原子序数 下标1——离子,下标2——靶 例如:磷离子Z1 = 15, m1 = 31 注入硅 Z2 = 14, m2 = 28, 计算可得: Sn ~ 550 keV-m2
Sn E 2.8 10
15
Z1Z 2
23 Z12 3 Z 2
m1 eV cm2 m1 m2
摘自J.F. Gibbons, Proc. IEEE, Vol. 56 (3), March, 1968, p. 295
第五章 离子注入
第五章 离子注入
电子阻止本领
第五章离子注入低温掺杂

• 当具有高能量的离子注入到固体靶面以后,这 些高能粒子将与固体靶面的原子与电子进行多 次碰撞,这些碰撞将逐步削弱粒子的能量,最 后由于能量消失而停止运动,形成一定的杂质 分布。
• 离子在硅体内的注入深度和分布状态与射入时 所加的电场强度、离子剂量、衬底晶向等有关
第五章离子注入低温掺杂
第五章离子注入ห้องสมุดไป่ตู้温掺杂
How can we form ultrashallow junction in today’s CMOS devices?
减少沟道效应的措施
目前常用的解决方法有三种 • (1)是将硅片相对注入的离子运动方向
倾斜一个角度,7度左右最佳; • (2)是对硅片表面铺上一层非结晶系的
(4)离子注入深度是随离子能量的增加而增加。 可精确控制掺杂浓度和深度
(5)根据需要可从几十种元素中挑选合适的N型或P型 杂质进行掺杂。能容易地掺入多种杂质
(6)离子注入时的衬底温度较低(小于600℃ ),这 样就可以避免高温扩散所引起的热缺陷。同时横向效 应比热扩散小得多。
(7)表面浓度不受固溶度限制,可做到浅结低浓度 或 深结高浓度。
• 通常,在离子剂量和轰击次数一致的前提下, 注入的深度将随电场的强度增加而增加。
• 用离子注入法形成的分布,其浓度最大值不 在硅片表面,而是在深入硅体一定距离。这 段距离大小与注入粒子能量、离子类型等有 关。
第五章离子注入低温掺杂
离子注入的杂质分布还与衬底晶向有关系。
离子注入的沟道效应
沟道效应(Channeling effect)
离子注入机分类
离子注入机按能量高低分为: 低能离子注入机 中能离子注入机 高能离子注入机 兆能离子注入机
电子行业半导体制造与封测方案

电子行业半导体制造与封测方案第一章:半导体制造概述 (2)1.1 半导体制造简介 (2)1.2 半导体制造流程 (3)1.2.1 设计与仿真 (3)1.2.2 硅片制备 (3)1.2.3 光刻 (3)1.2.4 刻蚀 (3)1.2.5 离子注入 (3)1.2.6 化学气相沉积 (3)1.2.7 热处理 (3)1.2.8 封装与测试 (3)1.3 半导体制造发展趋势 (4)1.3.1 制程技术升级 (4)1.3.2 设备更新换代 (4)1.3.3 材料创新 (4)1.3.4 封装技术升级 (4)第二章:半导体材料与设备 (4)2.1 半导体材料概述 (4)2.2 半导体设备分类 (5)2.3 半导体设备选型与评价 (5)第三章:光刻技术 (6)3.1 光刻技术原理 (6)3.2 光刻机种类及特点 (6)3.2.1 深紫外光(DUV)光刻机 (6)3.2.2 极紫外光(EUV)光刻机 (6)3.2.3 光刻机其他类型 (6)3.3 光刻工艺优化 (7)3.3.1 光刻胶优化 (7)3.3.2 曝光参数优化 (7)3.3.3 显影工艺优化 (7)3.3.4 设备维护与校准 (7)第四章:蚀刻与沉积技术 (7)4.1 蚀刻技术概述 (7)4.2 沉积技术概述 (7)4.3 蚀刻与沉积工艺控制 (8)第五章:掺杂与离子注入 (8)5.1 掺杂原理 (9)5.2 离子注入技术 (9)5.3 掺杂与离子注入工艺优化 (9)第六章:半导体器件制造 (10)6.1 器件制造流程 (10)6.1.1 设计与仿真 (10)6.1.2 硅片制备 (10)6.1.3 光刻 (10)6.1.4 刻蚀 (10)6.1.5 离子注入 (10)6.1.6 化学气相沉积(CVD) (10)6.1.7 热处理 (10)6.1.8 封装 (11)6.2 器件种类及特点 (11)6.2.1 晶体管 (11)6.2.2 二极管 (11)6.2.3 集成电路 (11)6.2.4 光电器件 (11)6.3 器件制造工艺控制 (11)6.3.1 环境控制 (11)6.3.2 设备控制 (11)6.3.3 工艺参数控制 (11)6.3.4 质量控制 (11)第七章:封装技术 (12)7.1 封装技术概述 (12)7.2 封装材料与工艺 (12)7.2.1 封装材料 (12)7.2.2 封装工艺 (12)7.3 封装技术的发展趋势 (12)第八章:测试与质量控制 (13)8.1 测试原理与方法 (13)8.2 质量控制策略 (13)8.3 测试与质量控制发展趋势 (14)第九章:半导体制造项目管理 (14)9.1 项目管理概述 (14)9.2 项目进度与成本控制 (15)9.3 项目风险管理 (15)第十章:半导体制造与封测产业发展 (16)10.1 产业发展现状 (16)10.2 产业政策与规划 (16)10.3 产业发展趋势与挑战 (16)第一章:半导体制造概述1.1 半导体制造简介半导体制造是指将半导体材料经过一系列加工处理,制成具有特定功能器件的过程。
5.4 离子注入的基本原理[13页]
![5.4 离子注入的基本原理[13页]](https://img.taocdn.com/s3/m/2fb09c5083c4bb4cf7ecd187.png)
§5.4 离子注入的基本原理
一. 离子注入的定义及特点
1. 定义
先使待掺杂的原子或分,然后经过退火使杂质激活,从 而达到掺杂目的。
2. 特点
比较项目 温度
扩散法 高温(800-1200℃)
掩蔽氧化层
<100>晶向注入方向倾斜7° 先轻微的离子注入
确定Rp和⊿Rp
3. 注入分布的应用
A. 计算结深 例:用100Kev的B+注入到具有掺杂浓度为2*1016cm-3的硅靶中,注入剂量 为 5*1013cm-2,试计算结深为多少?
B. 确定注入能量E和注入剂量Φ 例:基区杂质为6*1018cm-3的硅样品中,用P+注入形成发射区,要求硅中的最 大杂质为8*1021cm-3,发射结结深为0.13 μm,试估算入射离子的能量和剂量。
离子注入 注入在中等温度下进行(小于125℃ )
浓度控制
均匀性 结特性
横向扩散 掺杂深度
受源温、气体流量、扩散温度、 能在很大范围内精确控制注入杂质浓度,从
时间等多种因素影 响
1010到1017个/cm2,误差 2%之间
用扫描的方式控制杂质的均匀性
适合作深结
通过控制注入能量控制注入深度,增大了设计 的灵活性
有横向扩散 受固溶度极限
很小,几乎没有 注入杂质含量不受硅片固溶度的限制
二、注入的基本原理
1. 主要参数
• 投影射程 Xp • 平均投影射程Rp • 标准偏差ΔRp • 注入剂量Φ
入射离子束
硅衬底
X Rt p Rp
2. 杂质分布公式
• Φ:注入剂量:单位面积注入进去的杂质粒子数 • 当注入杂质种类,注入能量,衬底确定后,就能
- 1、下载文档前请自行甄别文档内容的完整性,平台不提供额外的编辑、内容补充、找答案等附加服务。
- 2、"仅部分预览"的文档,不可在线预览部分如存在完整性等问题,可反馈申请退款(可完整预览的文档不适用该条件!)。
- 3、如文档侵犯您的权益,请联系客服反馈,我们会尽快为您处理(人工客服工作时间:9:00-18:30)。
分析磁体 粒子束
加速管
工艺腔 扫描盘
从离子源引出的离子经过磁分析器选择出需要的离子, 离子源引出的离子经过磁分析器选择出需要的离子, 经过磁分析器选择出需要的离子 分析后的离子加速以提高离子的能量,再经过两维偏转 离子加速以提高离子的能量 分析后的离子加速以提高离子的能量,再经过两维偏转 使离子束均匀的注入到材料表面, 扫描器使离子束均匀的注入到材料表面 扫描器使离子束均匀的注入到材料表面,用电荷积分仪 可精确的测量注入离子的数量 离子的数量, 可精确的测量注入离子的数量,调节注入离子的能量可 注入深度。 精确的控制离子的注入深度 精确的控制离子的注入深度。
16
How can we form ultrashallow junction in today’s CMOS devices?
减少沟道效应的措施
目前常用的解决方法有三种
(1)是将硅片相对注入的离子运动方向倾 斜一个角度, 度左右最佳; 斜一个角度,7度左右最佳; (2)是对硅片表面铺上一层非结晶系的 材料,使入射的注入离子在进入硅片衬底之前, 材料,使入射的注入离子在进入硅片衬底之前, 在非结晶层里与无固定排列方式的非结晶系原 子产生碰撞而散射,这样可以减弱沟道效应; 子产生碰撞而散射,这样可以减弱沟道效应; 表面用SiO2层掩膜) 层掩膜) (表面用
23
注入材料形态选择
材料 硼 磷 砷 锑 气态 BF3 PH3 AsH3 - 固态 红磷 固态砷,As2O3 Sb2O3
24
离子源( 用来产生离子的装置。 离子源(Ion Source) 用来产生离子的装置。 原理是利用灯丝 利用灯丝(filament)发出的自由电子在 发出的自由电子 原理是利用灯丝 发出的自由电子在 电磁场作用下,获得足够的能量后撞击分子或 电磁场作用下,获得足够的能量后撞击分子或 原子,使它们电离成离子,再经吸极吸出, 原子,使它们电离成离子,再经吸极吸出,由 初聚焦系统聚成离子束, 初聚焦系统聚成离子束,射向磁分析器
25
b)质量分析器(磁分析器magnet b)质量分析器(磁分析器magnet analyzer) 质量分析器 利用不同荷质比的离子在磁场下运动轨迹的 利用不同荷质比的离子在磁场下运动轨迹的 不同将离子分离,选出所需的杂质离子。 不同将离子分离,选出所需的杂质离子。被 选离子束通过可变狭缝,进入加速管。 选离子束通过可变狭缝,进入加速管。
18
5.3离子注入设备 5.3离子注入设备
Photograph courtesy of Varian Semiconductor, VIISion 80 Source/Terminal side
19
离子注入机分类
离子注入机按能量高低分为: 离子注入机按能量高低分为: 低能离子注入机 中能离子注入机 高能离子注入机 兆能离子注入机 离子注入机按束流大小分为: 离子注入机按束流大小分为: 小束流离子注入机 中束流离子注入机 强流离子注入机 超强流离子注入机
9
5.2
离子注入原理
在离子注入的设备中, 等离子体发生器” ♣在离子注入的设备中,用“等离子体发生器” 来制造工艺所要注入的离子。 来制造工艺所要注入的离子。 ♣因为离子带电荷,可以用加速场进行加速,并 因为离子带电荷,可以用加速场进行加速, 且借助于磁场来改变离子的运动方向。 且借助于磁场来改变离子的运动方向。
第五章 离子注入低温掺杂
离子注入(Ion Implantation) 离子注入
1
5.1 什么是离子注入
什么是离子注入
离化后的原子在强电场的加速作用下,注射进入靶材料的表层, 离化后的原子在强电场的加速作用下,注射进入靶材料的表层, 以改变这种材料表层的物理或化学性质
离子注入的基本过程
将某种元素的原子或携带该 元素的分子经离化变成带电 的离子 在强电场中加速, 在强电场中加速,获得较高 的动能后, 的动能后,射入材料表层 (靶) 以改变这种材料表层的物理 或化学性质
10
当具有高能量的离子注入到固体靶面以后, 当具有高能量的离子注入到固体靶面以后,这些 高能粒子将与固体靶面的原子与电子进行多次碰 这些碰撞将逐步削弱粒子的能量, 撞,这些碰撞将逐步削弱粒子的能量,最后由于 能量消失而停止运动,形成一定的杂质分布。 能量消失而停止运动,形成一定的杂质分布。 离子在硅体内的注入深度和分布状态 注入深度和分布状态与射入时所 离子在硅体内的注入深度和分布状态与射入时所 加的电场强度 离子剂量、衬底晶向等有关 电场强度、 加的电场强度、离子剂量、衬底晶向等有关
3
离子注入技术优点
是随离子能量的增加而增加。 (4)离子注入深度是随离子能量的增加而增加。 )离子注入深度是随离子能量的增加而增加 可精确控制掺杂浓度和深度 型或P型 (5)根据需要可从几十种元素中挑选合适的 型或 型 )根据需要可从几十种元素中挑选合适的N型或 杂质进行掺杂。 杂质进行掺杂。能容易地掺入多种杂质 温度较低( (6)离子注入时的衬底温度较低(小于600℃ ),这 )离子注入时的衬底温度较低 小于600℃ 样就可以避免高温扩散所引起的热缺陷。同时横向效 样就可以避免高温扩散所引起的热缺陷。同时横向效 避免高温扩散所引起的热缺陷 应比热扩散小得多。 应比热扩散小得多。 表面浓度不受固溶度限制, (7)表面浓度不受固溶度限制,可做到浅结低浓度 或 深结高浓度。 深结高浓度。
12
离子注入的杂质分布还与衬底晶向有关系。 离子注入的杂质分布还与衬底晶向有关系。 与衬底晶向有关系
离子注入的沟道效应
沟道效应(Channeling effect) 沟道效应( )
当离子沿晶轴方向注入时, 当离子沿晶轴方向注入时,大部分离子将沿沟道运 几乎不会受到原子核的散射,方向基本不变, 动,几乎不会受到原子核的散射,方向基本不变, 可以走得很远。 可以走得很远。
匀掺杂
温度低, (3)离子注入温度低,衬底一般是保持在室温或低于 )离子注入温度低 400℃。因此,像二氧化硅、氮化硅、光刻胶,铝等都可 ℃ 因此, 二氧化硅、氮化硅、光刻胶, 以用来作为选择掺杂的掩蔽膜。对器件制造中的自对准掩 以用来作为选择掺杂的掩蔽膜。对器件制造中的自对准掩 蔽技术给予更大的灵活性 这是热扩散方法根本做不到的。 给予更大的灵活性, 蔽技术给予更大的灵活性,这是热扩散方法根本做不到的。
20
离子注入系统的组成
离子源 (Ion Source) 磁分析器 (Magnetic analyzer) 加速管 (Accelerator) 聚焦和扫描系统 (Focus and Scan system) 工 艺 腔 ( 靶 室 和 后 台 处 理 系 统 Target Assembly)
21
离子源 等离子体 吸出组件
2
离子注入技术优点
离子注入技术主要有以下几方面的优点: 离子注入技术主要有以下几方面的优点: 主要有以下几方面的优点 (1)注入的离子是通过质量分析器选取出来的,被选取的 )注入的离子是通过质量分析器选取出来的, 离子纯度高,能量单一,从而保证了掺杂纯度不受杂质源 离子纯度高,能量单一,从而保证了掺杂纯度不受杂质源 即掺杂纯度高。 纯度的影响即掺杂纯度高 纯度的影响即掺杂纯度高。 离子/ 的较宽范围内, (2)注入剂量在 11一1017离子/cm2的较宽范围内,同一 )注入剂量在10 平面内的杂质均匀度可保证在 杂质均匀度可保证在± 的精度。 平面内的杂质均匀度可保证在±1%的精度。大面积均
8
退火处理
通常,离子注入的深度较浅且浓度较大, 通常,离子注入的深度较浅且浓度较大, 必须使它们重新分布。同时由于高能粒子的撞 必须使它们重新分布。同时由于高能粒子的撞 导致硅结构的晶格发生损伤 晶格发生损伤。 击,导致硅结构的晶格发生损伤。
为恢复晶格损伤, 为恢复晶格损伤,在离子注入后要进行 退火处理。在退火的同时, 退火处理。在退火的同时,掺入的杂质同 时向半导体体内进行再分布 再分布。 时向半导体体内进行再分布
6
离子注入掺杂分为 两个步骤 两个步骤: 离子注入掺杂 ---离子注入 离子注入 ---退火再分布 退火再分布。 退火再分布
7
离子注入
在离子注入中,电离的杂质离子经静电场加速 离子注入中 打到晶圆表面。在掺杂窗口处, 打到晶圆表面。在掺杂窗口处,杂质离子被注入裸 露的半导体本体, 露的半导体本体,在其它部位杂质离子则被半导体 上面的保护层屏蔽。 上面的保护层屏蔽。 通过测量离子电流可严格控制剂量 测量离子电流可严格控制剂量。 通过测量离子电流可严格控制剂量。 通过控制静电场可以控制杂质离子的穿透深度 控制静电场可以控制杂质离子的穿透深度。 通过控制静电场可以控制杂质离子的穿透深度。
13
沿 <110> 轴的硅晶格视图
Used with permission from Edgard Torres Designs
Figure 17.28
14
110
111
100
倾斜旋转硅片后的无序方向
15
沟道效应的存在, 沟道效应的存在,将使得对注入离子在深度 上难以控制, 上难以控制,尤其对大规模集成电路制造 更带来麻烦。 更带来麻烦。如MOS器件的结深通常只有 器件的结深通常只有 0.4um左右,有了这种沟道效应万一注入距 左右, 左右 离超过了预期的深度,就使元器件失效。 离超过了预期的深度,就使元器件失效。 因此,在离子注入时, 因此,在离子注入时,要考虑到这种沟道 效应,也就是说要抑止这种现象的产生 抑止这种现象的产生。 效应,也就是说要抑止这种现象的产生。
11
通常,在离子剂量和轰击次数一致的前提下, 通常,在离子剂量和轰击次数一致的前提下, 注入的深度将随电场的强度增加而增加。 注入的深度将随电场的强度增加而增加。 用离子注入法形成的分布, 浓度最大值不在 用离子注入法形成的分布,其浓度最大值不在 硅片表面,而是在深入硅体一定距离。 硅片表面,而是在深入硅体一定距离。这段距 离大小与注入粒子能量、离子类型等有关。 离大小与注入粒子能量、离子源 吸出 组件 分析磁体 粒子束 较轻离子