回转窑技术参数与操纵制度
回转窑技术参数及工作原理

回转窑技术参数及工作原理回转窑是一种常用的烧结设备,广泛应用于水泥、冶金、化工等行业。
本文将介绍回转窑的技术参数及工作原理。
一、技术参数1. 窑体尺寸:回转窑的尺寸主要由窑筒直径和窑长两个参数决定。
一般窑筒直径为3-6米,窑长为30-150米,具体尺寸根据生产需求而定。
2. 转速:回转窑的转速是指窑筒每分钟旋转的圈数,通常为0.2-4.0转/分钟。
转速的选择应结合烧结物料的性质和生产工艺要求,以确保物料在窑内充分烧结。
3. 倾斜角度:回转窑的倾斜角度对物料的烧结效果有重要影响。
一般来说,倾斜角度为3-5度,过大或过小都会影响烧结效果。
4. 烧成温度:回转窑的烧成温度取决于生产工艺和物料的特性。
通常在1200-1500摄氏度之间,不同行业和产品的要求有所不同。
二、工作原理回转窑由筒体、带有轮圈的支撑装置、传动装置、密封装置等组成。
物料由窑头进料口进入回转窑,随着窑筒的旋转逐渐向窑尾移动。
在运动过程中,物料在重力的作用下沿着窑筒的倾斜方向逐渐下滑。
在回转窑内,物料经历了多个区域的热交换和化学反应。
首先是预热区,物料在此区域受到燃料燃烧产生的高温气体的预热作用,水分被蒸发,有机物被分解。
然后进入煅烧区,物料在高温区域中发生煅烧反应,形成熟料。
最后是冷却区,物料在此区域被冷却气体冷却,减少温度。
回转窑的工作原理可以简单概括为:物料在回转窑内受到高温气体和窑筒的作用,经过一系列的热交换和化学反应,最终形成所需的产品。
三、回转窑的优势1. 适应性强:回转窑适用于多种物料的烧结,如水泥熟料、石灰石、铁矿石等。
并且可以根据生产需要进行调整和改进。
2. 热能利用高效:回转窑内的物料与高温气体进行热交换,热能利用效率较高,有利于节能减排。
3. 产品质量好:回转窑能够实现物料的均匀受热和充分烧结,从而提高产品的质量。
4. 生产能力大:回转窑的生产能力大,适用于大规模生产。
回转窑是一种重要的烧结设备,具有广泛的应用前景。
石灰回转窑技术参数

石灰回转窑技术参数
石灰回转窑的技术参数包括以下方面:
1. 窑筒直径:一般在
2.5-6米之间,直径越大,生产能力越高。
2. 窑筒长度:一般在30-200米之间,长度越长,烧结时间越长,烧成的产品质量越好。
3. 倾角:一般在1%-5%之间,倾角越大,物料在窑筒中的停留时间越长,适合于生产精细产品。
4. 旋转速度:一般在0.5-3转/分钟之间,旋转速度越快,物料在窑筒中的停留时间越短,适合于生产大批量产品。
5. 石灰回转窑的主电机宜采用无级变速电动机,并需设置辅助传动,辅助传动应有备用电源。
6. 回转窑的烧成带筒体的冷却宜采用强制风冷,回转窑烧成带应有筒体温度的检测措施。
7. 窑体直径:400t石灰回转窑的直径一般为4-6米,根据生产需求和设备布局进行选择。
8. 窑体长度:窑体长度一般为30-60米,根据生产工艺和石灰石原料的特性来确定。
9. 倾角:一般为3-5度,它的选择与石灰石原料的性质有关。
这些参数的选择需要根据具体生产需求和设备布局等因素进行综合考虑。
回转窑操作规章制度

回转窑操作规章制度一、操作人员要求1.1 操作人员必须接受相关岗位培训,掌握回转窑的工作原理、操作流程和安全规范,经过考核合格方可上岗操作。
1.2 操作人员必须穿戴符合要求的劳动防护用品,如安全帽、安全鞋、防护眼镜等。
1.3 操作人员必须严格遵守操作规程,不得随意更改设备参数或进行未经许可的操作。
1.4 操作人员必须做好设备巡检工作,及时发现和报告设备故障,确保设备运行的正常。
1.5 操作人员必须具备应急处置能力,能够在突发情况下迅速做出正确反应,保障人员和设备的安全。
二、设备操作规范2.1 启动前检查2.1.1 操作人员在启动回转窑前必须进行设备的检查,包括轴承润滑情况、传动装置是否松动、电气线路是否正常等。
2.1.2 在检查过程中发现异常情况,必须及时停机处理,确保设备启动前的安全。
2.2 启动操作2.2.1 启动回转窑时,应按照操作规程逐步启动,不得急躁操作,以免造成设备故障。
2.2.2 启动过程中,操作人员必须密切关注设备运行状态,及时发现异常情况并做出处理。
2.2.3 启动后需要进行调试,检查设备各部位是否运转正常,是否有异常声音或振动。
2.3 运行操作2.3.1 在设备运行过程中,操作人员必须密切关注设备运行状态,保持设备的稳定运行。
2.3.2 运行中如发现异常情况,应及时停机处理,并及时报告相关部门。
2.3.3 对于运行中可能出现的风险,必须采取有效的措施进行控制,确保安全生产。
2.4 停机操作2.4.1 停机前必须先减小负荷,缓慢降低运行速度,确保设备平稳停机。
2.4.2 停机时必须先切断电源,清理设备周围杂物,然后关闭设备所有设备。
2.4.3 停机后还需对设备进行巡检,确认设备状态正常后方可离开现场。
三、安全管理规定3.1 安全防护3.1.1 操作人员在操作回转窑时必须穿戴符合要求的劳动防护用品,不得随意解除。
3.1.2 设备周围必须设置安全警示标志,防止他人误入作业区域。
3.1.3 设备运行时,不得有非设备操作人员靠近,严禁在设备周围玩耍。
回转窑的操作规程
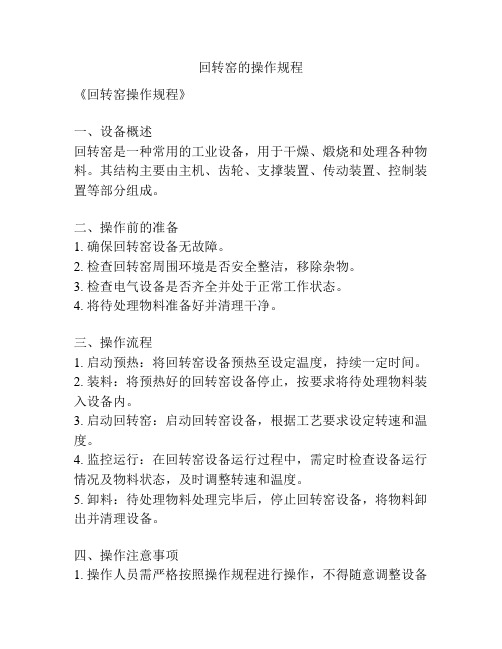
回转窑的操作规程《回转窑操作规程》一、设备概述回转窑是一种常用的工业设备,用于干燥、煅烧和处理各种物料。
其结构主要由主机、齿轮、支撑装置、传动装置、控制装置等部分组成。
二、操作前的准备1. 确保回转窑设备无故障。
2. 检查回转窑周围环境是否安全整洁,移除杂物。
3. 检查电气设备是否齐全并处于正常工作状态。
4. 将待处理物料准备好并清理干净。
三、操作流程1. 启动预热:将回转窑设备预热至设定温度,持续一定时间。
2. 装料:将预热好的回转窑设备停止,按要求将待处理物料装入设备内。
3. 启动回转窑:启动回转窑设备,根据工艺要求设定转速和温度。
4. 监控运行:在回转窑设备运行过程中,需定时检查设备运行情况及物料状态,及时调整转速和温度。
5. 卸料:待处理物料处理完毕后,停止回转窑设备,将物料卸出并清理设备。
四、操作注意事项1. 操作人员需严格按照操作规程进行操作,不得随意调整设备参数。
2. 操作人员需时刻关注设备运行情况,发现异常情况立即报告。
3. 在操作过程中需遵守相关安全规定,穿戴好防护用具,确保人身安全。
4. 操作结束后,需对设备及周围环境进行清理和整理,确保设备安全。
五、设备维护1. 定期对回转窑设备进行清洗和维护,保持设备干净、整洁。
2. 定期对设备零部件进行检查和维修,确保设备运行正常。
3. 在使用过程中及时发现并解决设备故障,保障设备持续稳定运行。
六、操作记录每次操作结束后,需对设备操作过程进行记录,包括操作人员、操作时间、设备运行参数等,以备后续参考。
通过严格按照操作规程进行操作,可以确保回转窑设备的安全运行和物料处理质量,提高生产效率和产品质量。
回转窑技术参数
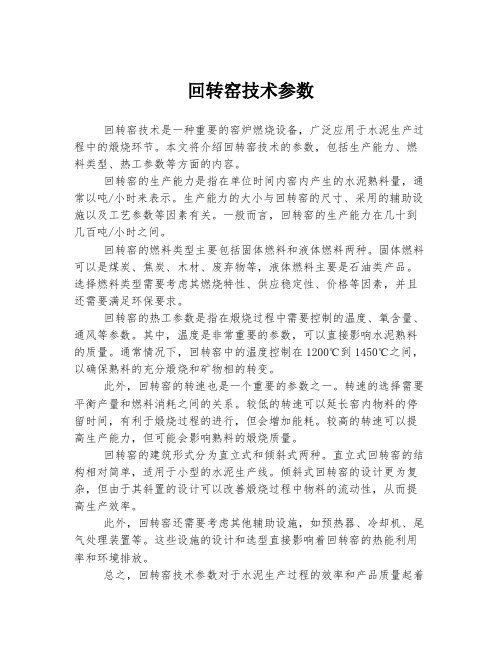
回转窑技术参数回转窑技术是一种重要的窑炉燃烧设备,广泛应用于水泥生产过程中的煅烧环节。
本文将介绍回转窑技术的参数,包括生产能力、燃料类型、热工参数等方面的内容。
回转窑的生产能力是指在单位时间内窑内产生的水泥熟料量,通常以吨/小时来表示。
生产能力的大小与回转窑的尺寸、采用的辅助设施以及工艺参数等因素有关。
一般而言,回转窑的生产能力在几十到几百吨/小时之间。
回转窑的燃料类型主要包括固体燃料和液体燃料两种。
固体燃料可以是煤炭、焦炭、木材、废弃物等,液体燃料主要是石油类产品。
选择燃料类型需要考虑其燃烧特性、供应稳定性、价格等因素,并且还需要满足环保要求。
回转窑的热工参数是指在煅烧过程中需要控制的温度、氧含量、通风等参数。
其中,温度是非常重要的参数,可以直接影响水泥熟料的质量。
通常情况下,回转窑中的温度控制在1200℃到1450℃之间,以确保熟料的充分煅烧和矿物相的转变。
此外,回转窑的转速也是一个重要的参数之一。
转速的选择需要平衡产量和燃料消耗之间的关系。
较低的转速可以延长窑内物料的停留时间,有利于煅烧过程的进行,但会增加能耗。
较高的转速可以提高生产能力,但可能会影响熟料的煅烧质量。
回转窑的建筑形式分为直立式和倾斜式两种。
直立式回转窑的结构相对简单,适用于小型的水泥生产线。
倾斜式回转窑的设计更为复杂,但由于其斜置的设计可以改善煅烧过程中物料的流动性,从而提高生产效率。
此外,回转窑还需要考虑其他辅助设施,如预热器、冷却机、尾气处理装置等。
这些设施的设计和选型直接影响着回转窑的热能利用率和环境排放。
总之,回转窑技术参数对于水泥生产过程的效率和产品质量起着重要的作用。
了解回转窑技术参数的基本原理,对于提高生产效率、降低能耗以及减少环境污染具有重要的意义。
(整理)回转窑技术参数.

(整理)回转窑技术参数.回转窑是用于生产水泥、石灰、铁精矿和活性石灰等物料的重要设备。
它具有体积大、适用范围广、热量利用率高等特点,被广泛应用于建材、冶金、化工等行业。
回转窑的技术参数涉及到其结构、尺寸、能耗、生产能力等方面,下面我们来详细介绍一下。
1. 结构和尺寸:回转窑的结构主要包括筒体、轴承、齿轮环、轴承座等部件。
筒体通常采用直径较大的圆筒形状,长度根据生产需要而定。
一般来说,回转窑的直径在2.5米到7米之间,长度可以达到70米以上。
2. 制备能耗:回转窑的能耗主要包括燃烧燃料所需的热量和电力消耗。
不同的燃料和物料具有不同的热值和消耗量。
一般来说,燃烧煤粉需要的热量约为2800-3000千卡/千克,燃烧重油约为10000千卡/千克,燃烧天然气约为8300千卡/立方米。
而电力消耗根据生产能力和设备配置而定,一般为50-70千瓦时/吨物料。
3. 生产能力:回转窑的生产能力主要受到物料性质、窑筒尺寸和转速等因素的影响。
一般来说,水泥产线上的回转窑生产能力为1000-8000吨/天,石灰产线上的回转窑生产能力为100-1000吨/天。
生产能力还可通过改变生产线的运行时间和窑筒转速来调节。
4. 窑筒转速:回转窑的转速对于物料煅烧的均匀性和产量具有重要影响。
一般来说,水泥生产中回转窑的转速为0.3-2转/分钟,石灰生产中的回转窑转速为0.25-0.5转/分钟。
转速过高会导致物料不充分煅烧,转速过低则会影响生产效率。
5. 窑炉热效率:回转窑的热效率是评估其能耗高低和燃料利用率的重要指标。
热效率取决于回转窑的结构设计、燃料种类和燃烧系统的性能等因素。
一般来说,回转窑的热效率可达到60%-80%。
总结:回转窑是一种常见的重要工业设备,其技术参数包括结构和尺寸、能耗、生产能力、窑筒转速和热效率等方面。
了解这些参数可以帮助我们更好地使用和选择回转窑,提高生产效率和降低能耗。
同时,不同行业和不同生产要求可能会有一些特殊的技术参数,需要根据实际情况进行调整和优化。
回转窑技术参数

回转窑技术参数第一篇:回转窑是一种重要的热工设备,广泛应用于水泥、冶金、化工等工业领域,以下是其技术参数的详细介绍:1. 生产能力:回转窑的生产能力是指其单位时间内处理原料的能力,通常以吨/小时或立方米/小时来表示。
生产能力的大小与设备的形式、尺寸、结构、转速等因素有关。
2. 转速:回转窑的转速决定了其热交换能力和物料在窑内停留时间的长短。
不同类型的回转窑转速范围不同,通常在0.5-3.5转/分之间。
3. 倾角:回转窑的倾角一般在1-5度之间,也有些窑体采用类似于注塑机底座上垫角度铁的做法来调整倾角。
倾角的大小会影响窑内物料的流动和热交换,进而影响窑的生产效率和质量。
4. 窑体直径和长度:回转窑的直径和长度决定了其产能和各项工艺参数。
不同工业部门和工艺要求下,直径和长度范围不同,一般在3-6米之间,长度可达30-100米不等。
5. 窑内温度:回转窑的运行需要维持一定的工艺温度。
不同物料和生产工艺需要的温度不同,一般在900-1500℃之间,常见的水泥熟料窑温度一般为1300-1450℃左右。
6. 燃料类型:回转窑的燃料类型主要包括固体燃料和液态燃料,液态燃料可能会导致煤气化产物和燃烧产物混杂,影响窑内气流和物料质量。
回转窑技术参数的合理设计和可持续管理是保障生产质量和效益的重要保证。
下面将继续从其它方面介绍回转窑的技术参数。
第二篇:继上文介绍回转窑技术参数的生产能力、转速、倾角、窑体直径和长度、窑内温度、燃料类型后,以下将继续介绍其它参数:7. 窑头温度:回转窑的窑头部位温度主要决定了其燃烧效率和下料速度。
适当地提高窑头温度可以排除窑内积存物质,加快生产速度,但是过高的温度会导致窑头易损坏。
8. 窑尾温度:回转窑的窑尾部位温度决定了其烟气净化效果和生产设备的良好状态。
控制窑尾温度可以减少污染物排放,同时也有助于减少锅炉烟气中氮氧化物的生成。
9. 窑壳厚度:回转窑的窑壳部分的厚度主要影响其导热性能和结构强度。
回转窑工艺、操作要求及推荐参数
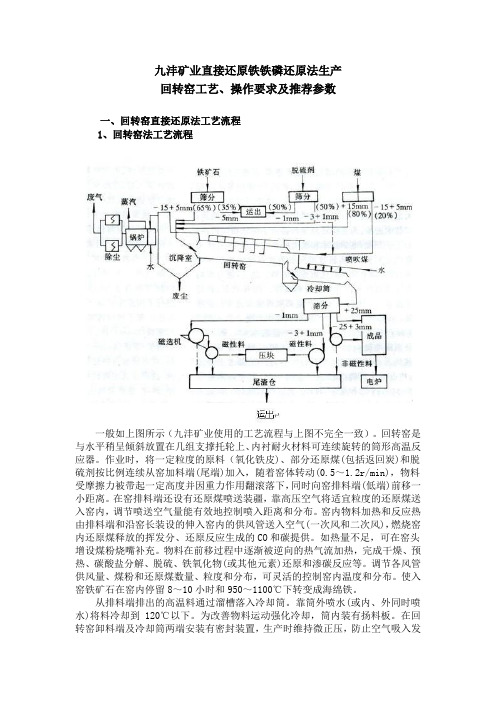
九沣矿业直接还原铁铁磷还原法生产回转窑工艺、操作要求及推荐参数一、回转窑直接还原法工艺流程1、回转窑法工艺流程一般如上图所示(九沣矿业使用的工艺流程与上图不完全一致)。
回转窑是与水平稍呈倾斜放置在几组支撑托轮上、内衬耐火材料可连续旋转的筒形高温反应器。
作业时,将一定粒度的原料(氧化铁皮)、部分还原煤(包括返回炭)和脱硫剂按比例连续从窑加料端(尾端)加入,随着窑体转动(0.5~1.2r/min),物料受摩擦力被带起一定高度并因重力作用翻滚落下,同时向窑排料端(低端)前移一小距离。
在窑排料端还设有还原煤喷送装疆,靠高压空气将适宜粒度的还原煤送入窑内,调节喷送空气量能有效地控制喷入距离和分布。
窑内物料加热和反应热由排料端和沿窑长装设的伸入窑内的供风管送入空气(一次风和二次风),燃烧窑内还原煤释放的挥发分、还原反应生成的CO和碳提供。
如热量不足,可在窑头增设煤粉烧嘴补充。
物料在前移过程中逐渐被逆向的热气流加热,完成干燥、预热、碳酸盐分解、脱硫、铁氧化物(或其他元素)还原和渗碳反应等。
调节各风管供风量、煤粉和还原煤数量、粒度和分布,可灵活的控制窑内温度和分布。
使入窑铁矿石在窑内停留8~10小时和950~1100℃下转变成海绵铁。
从排料端排出的高温料通过溜槽落入冷却筒。
靠筒外喷水(或内、外同时喷水)将料冷却到120℃以下。
为改善物料运动强化冷却,筒内装有扬料板。
在回转窑卸料端及冷却筒两端安装有密封装置,生产时维持微正压,防止空气吸入发生再氧化。
冷却后的物料经筛分分级、磁选分离得出磁性颗粒料(直接还原铁)、磁性粉料、非磁性颗粒料和非磁性粉。
非磁性颗粒料含较高固定碳,可作还原剂重新利用。
二、回转窑设备组成回转窑设备主要由筒体、滚圈、支承装置、传动装置、窑头罩、密封装置、集尘室、燃烧装置及热烟室等部分构成,详见上图。
(1)筒体。
回转窑的筒体由钢板卷成,从铆接已发展为全部焊接。
筒体应具有足够的刚度和强度,以保证在安装和运转中轴线的直线性和截面的圆度。
- 1、下载文档前请自行甄别文档内容的完整性,平台不提供额外的编辑、内容补充、找答案等附加服务。
- 2、"仅部分预览"的文档,不可在线预览部分如存在完整性等问题,可反馈申请退款(可完整预览的文档不适用该条件!)。
- 3、如文档侵犯您的权益,请联系客服反馈,我们会尽快为您处理(人工客服工作时间:9:00-18:30)。
¢4.3X70M回转窑技术参数及操作规程文章来源:徐州龙圣建材机械制造有限公司添加人:admin 添加时间:2008-11-18 15:38:20 点击:2518回转窑操作规程1.设备技术性能筒体内径: 4.3m筒体长度:70m斜度: 3.5[wiki]%[/wiki]支承数:3档生产能力:100t/d转速:用主传动:0.40-1.3r/min用辅助传动:7.9r/h传动电动机(单传动):主传动辅助传动型号功率(Kw)转速(r/min)型号功率(Kw)转速(r/min)YPT400-8 250 750 Y225S-4 37 1480减速器:主传动辅助传动型号速比型号速比ZSY630-71-I 71 ZSY280-22.4-Ⅱ22.42.结构及工作原理概述回转窑的筒体由钢板卷制而成,筒体内镶砌耐火衬,且与水平线成规定的斜度,由3个轮带支承在各挡支承装置上,在入料端轮带附近的跨内筒体上用切向弹簧板固定一个大齿圈,其下有一个小齿轮与其啮合。
正常运转时,由主传动电动机经主减速器向该开式齿轮装置传递动力,驱动回转窑。
物料从窑尾(筒体的高端)进入窑内煅烧。
由于筒体的倾斜和缓慢的回转作用,物料既沿圆周方向翻滚又沿轴向(从高端向低端)移动,继续完成其工艺过程,最后,生成熟料经窑头罩进入冷却机冷却。
燃料由窑头喷入窑内,燃烧产生的废气与物料进行交换后,由窑尾导出。
本设计不含燃料的燃烧器。
该窑在结构方面有下列主要特点:1简体采用保证五项[wiki]机械[/wiki]性能(σa、σb、σ%、αk和冷弯试验)的20g及Q235-B钢板卷制,通常采用自动焊焊接。
筒体壁厚:一般为25mm,烧成带为32mm,轮带下为65mm,由轮带下到跨间有38mm厚的过渡段节,从而使筒体的设计更为合理,既保证横截面的刚性又改善了支承装置的受力状态。
在筒体出料端有耐高温、耐磨损的窑口护板,筒体窑尾端由一米长1Cr18Ni9Ti钢板制作。
其中窑头护板与冷风套组成分格的套筒空间,从喇叭口向筒内吹冷风冷却窑头护板的非工作面,以有利该部分的长期安全工作,在筒体上套有三个矩形实心轮带。
轮带与筒体垫板间的间隙由热膨胀量决定,当窑正常运转时,轮带能适度套在筒体上,以减少筒体径向变形。
3传动系统用单传动,由变频电动机驱动硬齿面三级圆柱齿轮减速器,再带动窑的开式齿轮副,该传动装置采用胶块联轴器,以增加传动的平稳性,设有连接保安电源的辅助传动装置,可保证主电源中断时仍能盘窑操作,防止筒体弯曲并便利检修。
4窑头密封采用罩壳气封、迷宫加弹簧刚片双层柔性密封装置。
通过喇叭口吹入适量的冷空气冷却护板,冷空气受热后从顶部排走;通过交迭的耐热弹簧钢片下柔性密封板压紧冷风套筒体,保证在窑头筒体稍有偏摆时仍能保持密封作用。
5窑尾密封采用钢片加石墨柔性密封。
该装置安装简单方便,使用安全可靠。
三安装要求安装前应熟悉有关图纸和技术文件,了解设备结构,明确安装要求;根据具体条件确定安装顺序、方法,准备必要的安装工具与设备;编制组织和安装计划,然后精心施工。
核对基础,划基准线1.修正图纸。
实测筒体各段节长度,考虑每个接口的间隙量和焊接收缩量等,一般可按每个为2mm,算出筒体上每两轮带间的实际尺寸,再计及相应热膨胀量,得出相邻两档支承装置最后的斜向间距尺寸和水平间距尺寸,以修正图纸上的相关尺寸。
2.根据修正的图纸,核对窑基础尺寸,特别是基础中心距尺寸,如不符合,应采取下列措施:(1)修正后图纸尺寸与相应基础尺寸偏差小于5mm时,不必采取措施;(2)偏差5~10mm时,适当增缩筒体段节间接合面的间隙,每一接合面间隙调整范围为1~3mm;(3)偏差大于10mm时,除调整筒体段节接合面的间隙外,还必须调整支承装置的位置,根据调整后的实际尺寸,再次修正图纸上各挡支承装置斜向间距尺寸,算出其水平间距尺寸;实测托轮及其轴承尺寸,修下托轮工作表面顶部母线的标高尺寸。
3. 基础划线(1)在基础侧面离地面约1m处划出水平基准线,燕在基础四角埋设标高板。
基准面标高偏差不得大于0.5mm;(2)划出纵向中心线,偏差不得大于0.5mm;(3)根据修正后图纸,在水平基础线主划出各基础的横向中心线,相隔两基础的中心距偏差不得大于1.5mm,首尾两基础的中心距偏差不得大于1.5mm首尾两基础的中心距偏差不得大于3mm。
四、支承装置安装窑筒体中心线能否在运转时保持直线,首先取决于支承装置的定位,因此要高度重视支承装置的安装,安装时必须满足下列要求:1.底座经精确找正后应满足如下要求:底座纵向中心线允许偏差0.5mm相邻两底座中心距允许偏差 1.5mm首尾两底座中心距允许偏差3mm相邻两档底座标高允许偏差0.5mm首尾两档底座标高允许偏差1mm底座加工表面斜度运行偏差0.05mm/m2.装配托轮轴承组时,必须检查轴承座,球面瓦及衬瓦编号,确认是同一号码才进行组装。
用涂色方法进行检查。
衬瓦的接触斑点应均匀,沿母线全长等宽,并主要在中部区域连续颁。
否则必须进行现场刮研。
球面瓦与衬瓦间接触点在10×10mm上应不小于1点;球面瓦与轴承底座间接触点在25×25mm三不小于1点。
但边缘50mm左右的圈环地带允许有0.1mm左右的间隙;用塞尺检查衬瓦与轴颈的两侧间隙,在塞入100mm处一般要保持0.24mm,测隙不够时要加以刮削。
3.把托轮轴承组装于底座上,经过调整后应满足下列要求:(1)托轮轴高端(靠近料端)的止推圈应与衬瓦的端面接触,而低端则留有约4mm间隙;两托轮在高端的轮缘侧面应在同一平面内,用直尺检查,允许误差为0.5mm。
(2)两托轮中心线与底座纵向中心线的距离应符合图纸要求,允许不得超过0.5mm。
(3)用斜度规和水平仪检查全窑各个托轮工作表面,其铅垂直径上端母线的倾斜度应一致,允许误差不得超过0.05mm/m,同一档两托轮上述母线中心点边线应呈水平,允许误差不得超过0.05mm/m,超过允许误差时,可以在轴承底座下加薄垫片调整。
(4)测量各档托轮铅垂直径上端母线中心点的标高。
各档标高差应修正后图纸各档底座上表面中心的高差相对应,相信两档的允许偏差不得超过0.5mm,首尾两档的允许偏差不得超过1mm,(5)用经纬仪检查,所有托轮铅垂直径上端母线都应位于与水平成3.5%的倾斜平面内。
如果标高或倾斜度有误差,应通过调节螺栓进行调整,将底座略为升降,直至完全符合上述各项要求。
五、筒体安装和焊接1.准备工作:(1)按出厂标示的接口字码(或接口连续直线标志)在地面上初步试组装。
(2)检查每节筒体段节两边接口,其圆周长公差为6mm,圆度公差为8mm,当圆度超过允许值时,必须用筒体安装工具校正。
(3)测量轮带内径和各档垫板外径,其间隙是否符图纸要求。
(4)清除窑筒体段节接口处的飞边,毛刺,油污,铁锈等,保持其清洁和干燥。
2.组装和找正筒体:筒体段节的组装顺序由现场决定,为了保证筒体各段节接口间隙在1~3mm的范围内,可在接口处沿周围均匀分布的插入16块长约100mm,厚为1~3mm的方钢板。
焊接时,方钢板必须逐个除去,不得整周同时去掉。
注意检查轮带与托轮的相对位置是否和图纸上冷态的相对位置符合,其允许偏差为5mm。
筒体测量和调整后,必须符合下列要求:(1)筒体径向偏摆:窑头、窑尾处不得大于5mm;齿圈处不得大于2mm,其他各处不得大于6mm。
(2)筒体焊接口处,内壁应先保证平齐且圆周任何位置上最大错边量不得大于2mm。
3.筒体焊接筒体焊接是回转窑安装工作的重要环节,其质量好坏直接影响窑的正常运转与工作寿命,必须给予高度重视,特别要注意下列事项:(1)焊工必须经考试合格后才能上岗。
(2)视现场条件,筒体焊接可采用内部手工封底,外部自动焊或手工焊。
自动焊时,采用相当于08A的焊丝;手工焊时,采用相当于E4815(GB5117-85)的焊条。
焊条使用前在250℃温度下干燥2小时,以确保干燥。
(3)焊接筒体时,窑内不得同时进行任何其他作业。
(4)下雨、大风、飘雪时,不应进行筒体焊接。
在温度低于5℃时,坡口要预热,焊后要保温,焊接工艺要相应调整。
筒体受日光曝晒时,“阴阳”两面的温差引起筒体中心线的弯曲,此时不宜焊接。
筒体单侧受热窑辐射也会引起欲焊筒体中心线的弯曲,此时,应采用石棉板墙防护等隔热措施后,再进行焊接。
(5)焊缝各层间起、熄弧点不得重叠。
焊缝不得有夹肉、咬边、夹渣、气孔、裂纹等外观缺陷。
每条焊缝都必须进行探伤检验,纵、环焊缝汇交处及其他可疑部位必须进行射线探伤或超声波探伤检验。
检验结果,射线探伤必须符合GB3323-87种Ⅲ级的要求;超声波探伤必须符合JB1152中Ⅱ级的要求。
不符合者必须返修,检验规则按JC333-91执行。
(6)筒体焊接完后,再次检查轮带与托轮的实际相对位置是否符合图纸上冷态的尺寸要求,允许偏差5㎜。
轮带与两侧挡块应按图纸要求留有均匀的间隙。
(7)整修窑体按上述要求调整安装完毕后,以Ⅰ、Ⅱ两挡轮带下的筒体横断面中心为连线,第Ⅱ档轮带下的筒体横断面中心宜稍低,降低量不小于1.5mm,但不得大于2mm。
六、传动装置安装筒体组安装成整体后,应即安装传动装置。
允许先临时固定以便盘窑进行筒体的找正和焊接。
安装传动装置时,必须符合下列要求:1.齿圈下筒体段节的纵焊缝必须用砂轮打平,宽度应比弹簧板两侧各宽50mm。
2.借助于安装工具的调整螺栓精细找正,以符合齿圈外圈径向跳动公差1.5mm,基准面端面跳动公差1mm的要求。
3.弹簧板的安装方向应满足当窑正常运转时,它只受拉力的要求。
弹簧板与齿圈联接的铰孔螺栓装上后,其一侧的垫圈与弹簧板轭板间应先塞入0.3mm垫片,待拧紧开槽螺母,装好开口销后,再撤去该垫板,以保持规定的间隙0.3mm。
4.传动装置底座的横向位置应根据窑中心线决定,轴向位置应根据热膨胀来决定齿圈中心位置(注意此时窑尾轮带宽度中心应与托轮宽度中心重合),其表面标高由窑尾档支承装置的标高决定,表面斜度应与支承装置底座相同。
5.以齿圈为基准安装小齿轮装置,其位置尺寸应符合图纸要求,允许偏差为2mm。
用斜度规找正斜度,允许误差不得超过0.05mm/m。
冷态转窑一圈时,小齿轮与齿轮圈的齿顶隙应为9~10mm。
窑体达到正常工作温度后,其齿顶隙不得小于7mm。
检查齿轮与小齿轮的尺面接触情况,接触面积沿齿高应在40%以上;沿齿长50%以上。
6.主减速器的低速轴与小齿轮的轴同轴度公差Φ0.2mm,在减速器机体与机盖的剖分面上测量其横向水平偏差、轴向斜度偏差均不得大于0.05mm/m。
七、铅丝试验法调整托轮装置维护回转窑先要调整好拖轮装置,经常观察托轮的运转,根据经验,判定托轮受力以及托轮与轮带的接触情况。
通常可借助铅丝试验法来调整托轮装置。
采用铅丝试验法要求托轮及轮带表面光滑平整,试验时,将Φ0.2mm铅丝(通常是15A保险丝)沿托轮母线平直地放在轮带与托轮之间,如图1所示,然后对辗出的铅丝开头进行分析。