蜗杆传动几何尺寸计算公式(3种类型)
蜗轮蜗杆计算公式(简洁版)

0
20 1.2004E-08 1.2E-08
中心距a(d1+d2+2*X2*m)/2 蜗杆分度圆导程角(γ)=atan(Z1/q) =atan(m*Z1/d1) 蜗杆齿顶高ha1(ha*=1)=m*ha*=(da1d1) 蜗轮齿顶高ha2=(ha*+X2)*m=(da2d2) 蜗杆齿根高hf1=(ha*+c*)m=(d1df1)/2 蜗轮齿根高hf2=(d2-df2)/2=m*(ha*X2+C*) 蜗杆分度圆直径d1=q*m 蜗轮分度圆直径d2=m*Z2=2a-d1-2*X2*m 蜗杆齿顶圆直径da1=(q+2) *m=d1+2*ha1=d1+2*m*h* 蜗轮喉圆直径da2= (Z2+2+2*X2)*m=d2+2*ha2 蜗杆齿根圆直径df1=d1-2*hf1
Z1大、 29.48
Z1小
Z1大、
33 29.48
普通圆柱螺杆L≥ X -1 -0.5 0 0.5 1
Z1=1~2 46
39.44 51.44 56.4 60.4
蜗杆螺纹部分长度L
圆弧圆柱蜗杆
Z1=3~4
X2
Z1
46
<1
1~2
49.16
1~1.5
1~2
61.16
<1
3~4
62.4
1~1.5
3~4
64.4
80
0
80
80
6.3434076 6.3434076 #DIV/0! 6.3434076
4
22
4
66
4
4.8
0
0
4.8
4.8
36 35.9999999
普通圆柱蜗杆传动的基本参数及几何尺寸计算
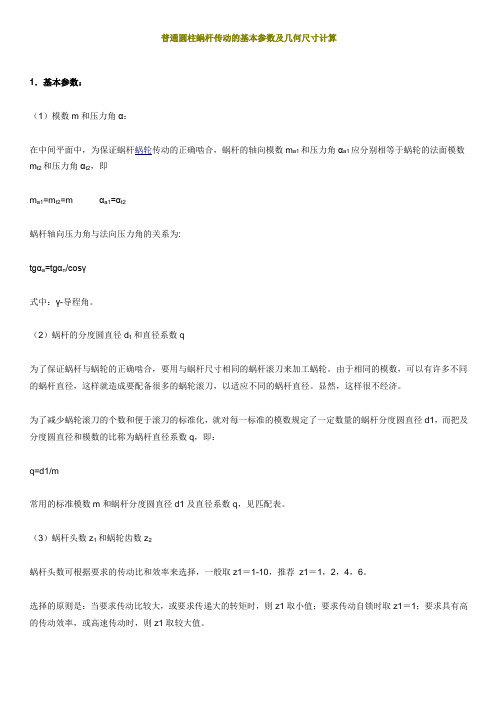
普通圆柱蜗杆传动的基本参数及几何尺寸计算1.基本参数:(1)模数m和压力角α:在中间平面中,为保证蜗杆蜗轮传动的正确啮合,蜗杆的轴向模数m a1和压力角αa1应分别相等于蜗轮的法面模数m t2和压力角αt2,即m a1=m t2=mαa1=αt2蜗杆轴向压力角与法向压力角的关系为:tgαa=tgαn/cosγ式中:γ-导程角。
(2)蜗杆的分度圆直径d1和直径系数q为了保证蜗杆与蜗轮的正确啮合,要用与蜗杆尺寸相同的蜗杆滚刀来加工蜗轮。
由于相同的模数,可以有许多不同的蜗杆直径,这样就造成要配备很多的蜗轮滚刀,以适应不同的蜗杆直径。
显然,这样很不经济。
为了减少蜗轮滚刀的个数和便于滚刀的标准化,就对每一标准的模数规定了一定数量的蜗杆分度圆直径d1,而把及分度圆直径和模数的比称为蜗杆直径系数q,即:q=d1/m常用的标准模数m和蜗杆分度圆直径d1及直径系数q,见匹配表。
(3)蜗杆头数z1和蜗轮齿数z2蜗杆头数可根据要求的传动比和效率来选择,一般取z1=1-10,推荐z1=1,2,4,6。
选择的原则是:当要求传动比较大,或要求传递大的转矩时,则z1取小值;要求传动自锁时取z1=1;要求具有高的传动效率,或高速传动时,则z1取较大值。
蜗轮齿数的多少,影响运转的平稳性,并受到两个限制:最少齿数应避免发生根切与干涉,理论上应使z2min≥17,但z2<26时,啮合区显著减小,影响平稳性,而在z2≥30时,则可始终保持有两对齿以上啮合,因之通常规定z2>28。
另一方面z2也不能过多,当z2>80时(对于动力传动),蜗轮直径将增大过多,在结构上相应就须增大蜗杆两支承点间的跨距,影响蜗杆轴的刚度和啮合精度;对一定直径的蜗轮,如z2取得过多,模数m就减小甚多,将影响轮齿的弯曲强度;故对于动力传动,常用的范围为z2≈28-70。
对于传递运动的传动,z2可达200、300,甚至可到1000。
z1和z2的推荐值见下表(4)导程角γ蜗杆的形成原理与螺旋相同,所以蜗杆轴向齿距p a与蜗杆导程p z的关系为p z=z1p a,由下图可知:tanγ=p z/πd1=z1p a/πd1=z1m/d1=z1/q导程角γ的范围为3.5°一33°。
机械设计(7.2.1)--圆柱蜗杆传动主要参数和几何尺寸计算
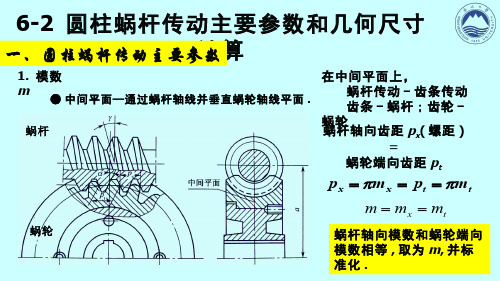
变 圆分离 ;
位 : 蜗杆分度线与蜗轮分度
中心距较标准值改 变;
位 , 减小 .
正变位 , 增大 ; 负变
(4) 变位后 , 蜗轮分度圆仍然与其节圆重 合,
但轮尺尺寸有变化 .
负变位 x2<0
标准 x2=0
正变位 x2>0 变位系数 , 过小 ,
( 变位后的 ) 实际中心距
a
a
a
1 2
(d1
● 蜗杆径向尺寸: d1= 按标准或自定 齿全高 , 齿顶高 , 齿根高及顶圆、
根圆同标准齿轮 , 无关变位 .
da1 d1 2ha1;ha1 ha*m d f 1 d1 2hf 1;hf 1 (ha* c* )m
ha* 1.0,0.8(短);c* 0.2,0.15,0.25
与链传动不同
7. 蜗轮齿数 表z26-3 给出了 z2 荐用值 ( 结合传动比和 蜗杆头数, z1=1,2,4,6) 。
为避免根切:
z1=1 , z2>17~18
z1=2 , z2>27
动力传动时,
z2<80, 根强度
避免尺寸过大 , 削弱齿
6-2 圆柱蜗杆传动主要参数和几何尺寸计算 一、圆柱蜗杆传动主要参 数
6-2 圆柱蜗杆传动主要参数和几何尺寸计算 一、圆柱蜗杆传动主要参 数
一、圆柱蜗杆传动主要参数
4. 蜗杆分度圆直径 d1(1) 为保证正确啮合,用蜗杆尺寸基
本相同的滚刀来加工蜗轮 .
(2) 为减少滚刀的数量和使之标准化 ,每个标准模数的规定了一定数量 的滚刀直径 ( 即蜗杆直径 ).
(3) 表 6-2 列出了 m 和 d1 常用标准 值.
普通圆柱蜗杆传动基本几何尺寸计算关系式
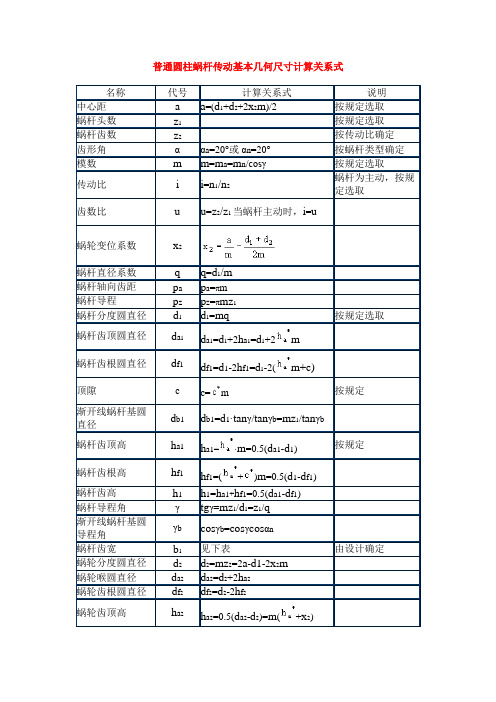
名称
代号
计算关系式
说明
中心距
a
a=(d1+d2+2x2m)/2
按规定选取
蜗杆头数
z1
按规定选取
蜗杆齿数
z2
按传动比确定
齿形角
α
αa=20°或αn=20°
按蜗杆类型确定
模数
m
m=ma=mn/cosγ
按规定选取
传动比
i
i=n1/n2
蜗杆为主动,按规定选取
齿数比
u
u=z2/z1当蜗杆主动时,i=u
经磨削的蜗杆,按左式所求的长度应再增加下列值:
当m<10mm时,增加25mm;
当m=10~16mm时,增加35~40mm;
当m>16mm时,增加50mm;
2
≤da2+1.5m
4
≤0.67da1
≤da2+m
0
-0.5
-1.0
0.5
1.0
≥(12.5+0.09z2)m
≥(9.5+0.09z2)m
≥(10.5+z1)m
蜗轮咽喉母圆半径
rg2
rg2=a-0.5da2
蜗轮齿宽
b2
由设计确定
蜗轮齿宽角
θ
θ=2arcsin(b2/d1)
蜗杆轴向齿厚
sa
sa=0.5πm
蜗杆法向齿厚
sn
sn=sa·cosγ
蜗轮齿厚
st
按蜗杆节圆处轴向齿槽宽ea'确定
蜗杆节圆直径
d1'
d1'=d1+2x2m=m(q+2x2)
蜗轮蜗杆的计算

蜗轮蜗杆的计算公司标准化编码 [QQX96QT-XQQB89Q8-NQQJ6Q8-MQM9N]蜗轮、蜗杆的计算公式:1,传动比=蜗轮齿数÷蜗杆头数2,中心距=(蜗轮节径+蜗杆节径)÷2 3,蜗轮吼径=(齿数+2)×模数 4,蜗轮节径=模数×齿数5,蜗杆节径=蜗杆外径-2×模数 6,蜗杆导程=π×模数×头数7,螺旋角(导程角)tg β=(模数×头数)÷蜗杆节径 一.基本参数:(1)模数m 和压力角α:在中间平面中,为保证蜗杆蜗轮传动的正确啮合,蜗杆的轴向模数m a1和压力角αa1应分别相等于蜗轮的法面模数m t2和压力角αt2,即 m a1=m t2=m αa1=αt2蜗杆轴向压力角与法向压力角的关系为: tgαa =tgαn /cosγ 式中:γ-导程角。
(2)蜗杆的分度圆直径d 1和直径系数q为了保证蜗杆与蜗轮的正确啮合,要用与蜗杆尺寸相同的蜗杆滚刀来加工蜗轮。
由于相同的模数,可以有许多不同的蜗杆直径,这样就造成要配备很多的蜗轮滚刀,以适应不同的蜗杆直径。
显然,这样很不经济。
为了减少蜗轮滚刀的个数和便于滚刀的标准化,就对每一标准的模数规定了一定数量的蜗杆分度圆直径d1,而把及分度圆直径和模数的比称为蜗杆直径系数q ,即: q=d1/m常用的标准模数m 和蜗杆分度圆直径d1及直径系数q ,见匹配表。
(3)蜗杆头数z 1和蜗轮齿数z 2蜗杆头数可根据要求的传动比和效率来选择,一般取z1=1-10,推荐 z1=1,2,4,6。
选择的原则是:当要求传动比较大,或要求传递大的转矩时,则z1取小值;要求传动自锁时取z1=1;要求具有高的传动效率,或高速传动时,则z1取较大值。
蜗轮齿数的多少,影响运转的平稳性,并受到两个限制:最少齿数应避免发生根切与干涉,理论上应使z2min≥17,但z2<26时,啮合区显着减小,影响平稳性,而在z2≥30时,则可始终保持有两对齿以上啮合,因之通常规定z2>28。
蜗杆传动基本尺寸计算公式
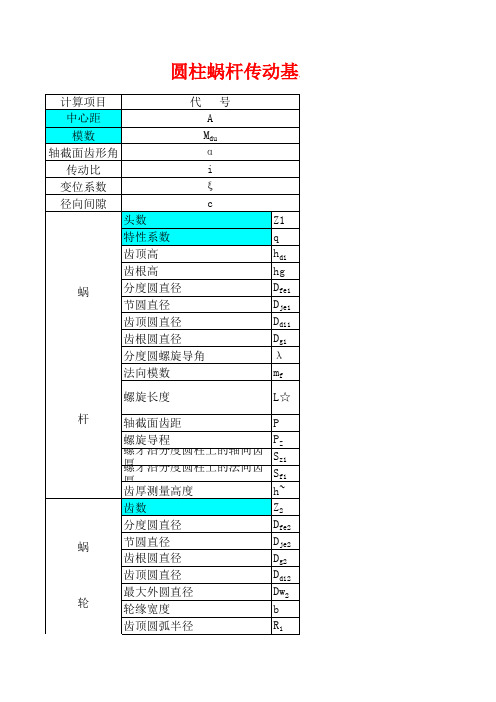
计算项目中心距模数轴截面齿形角传动比变位系数径向间隙头数Z1特性系数q 齿顶高h di 齿根高hg 分度圆直径D fe1节圆直径D je1齿顶圆直径D di1齿根圆直径D g1分度圆螺旋导角λ法向模数m f 轴截面齿距P螺旋导程P Z 螺牙沿分度圆柱上的轴向齿厚S z1螺牙沿分度圆柱上的法向齿厚S f1齿厚测量高度h~齿数Z 2分度圆直径D fe2节圆直径D je2齿根圆直径D g2齿顶圆直径D di2最大外圆直径Dw 2轮缘宽度b 齿顶圆弧半径R 1代 号A M du α螺旋长度L☆蜗 轮圆柱蜗杆传动基本几i ξc蜗杆齿根圆弧半径R 2轮基本几何尺寸计算公式公 式计算结果备注A=0.5M du(Z2+q+2ξ)175.00Mdu=2A/(Z2+q+2ξ) 3.15α=20°20.00i=Z2/Z1=n1/n297.00ξ=(A/Mdu)-0.5(q+z2) 2.06C=0.25Mdu0.79Z1=1,2,4 1.00q=Dfe1/Mdu10.00hdi=Mdu 3.15hg=1.25Mdu 3.94Dfe1=qMdu31.50Dje1=Dfe1+2Mduξ=Mdu(q+2ξ)44.45Ddi1=Mdu(q+2)37.80Dg1=Mdu(q-2.5)23.63λ=arctgZ1/q0.10mf=Mducosλ 3.13L=(12+0.1z2)Mdu68.36Z1=1,2 L=(13+0.1z2)Mdu71.51Z1=4 P=πMdu9.90PZ=πMduZ19.90Sz1=0.45πMdu97.00Sf1=Sz1cosλ96.52h~=Mdu 3.15Z2=iZ197.00Dfe2=MduZ2305.55Dje2=Dfe2=MduZ2305.55Dg2=2(A-0.5Ddi1-0.25Mdu)310.63Ddi2=2(A-0.5Dfe1+Mdu)324.80Dw2=Ddi2+Mdu327.95b=0.65Ddi124.57R1=0.5Dfe1-Mdu12.60R1=0.5Ddi1+0.25Mdu19.69。
蜗轮蜗杆的计算
蜗轮、蜗杆的计算公式: 1,传动比=蜗轮齿数÷蜗杆头数 2,中心距=(蜗轮节径+蜗杆节径)÷2 3,蜗轮吼径=(齿数+2)×模数 4,蜗轮节径=模数×齿数 5,蜗杆节径=蜗杆外径-2×模数 6,蜗杆导程=π×模数×头数7,螺旋角(导程角)tg β=(模数×头数)÷蜗杆节径 一.基本参数:(1)模数m 和压力角α:在中间平面中,为保证蜗杆蜗轮传动的正确啮合,蜗杆的轴向模数m a1和压力角αa1应分别相等于蜗轮的法面模数m t2和压力角αt2,即 m a1=m t2=m αa1=αt2蜗杆轴向压力角与法向压力角的关系为: tgαa =tgαn /cosγ 式中:γ-导程角。
(2)蜗杆的分度圆直径d 1和直径系数q为了保证蜗杆与蜗轮的正确啮合,要用与蜗杆尺寸相同的蜗杆滚刀来加工蜗轮。
由于相同的模数,可以有许多不同的蜗杆直径,这样就造成要配备很多的蜗轮滚刀,以适应不同的蜗杆直径。
显然,这样很不经济。
为了减少蜗轮滚刀的个数和便于滚刀的标准化,就对每一标准的模数规定了一定数量的蜗杆分度圆直径d1,而把及分度圆直径和模数的比称为蜗杆直径系数q,即:q=d1/m常用的标准模数m和蜗杆分度圆直径d1及直径系数q,见匹配表。
(3)蜗杆头数z1和蜗轮齿数z2蜗杆头数可根据要求的传动比和效率来选择,一般取z1=1-10,推荐 z1=1,2,4,6。
选择的原则是:当要求传动比较大,或要求传递大的转矩时,则z1取小值;要求传动自锁时取z1=1;要求具有高的传动效率,或高速传动时,则z1取较大值。
蜗轮齿数的多少,影响运转的平稳性,并受到两个限制:最少齿数应避免发生根切与干涉,理论上应使z2min≥17,但z2<26时,啮合区显着减小,影响平稳性,而在z2≥30时,则可始终保持有两对齿以上啮合,因之通常规定z2>28。
另一方面z2也不能过多,当z2>80时(对于动力传动),蜗轮直径将增大过多,在结构上相应就须增大蜗杆两支承点间的跨距,影响蜗杆轴的刚度和啮合精度;对一定直径的蜗轮,如z2取得过多,模数m 就减小甚多,将影响轮齿的弯曲强度;故对于动力传动,常用的范围为z2≈28-70。
蜗轮蜗杆的计算
蜗轮蜗杆的计算(总4页) -CAL-FENGHAI.-(YICAI)-Company One1-CAL-本页仅作为文档封面,使用请直接删除蜗轮、蜗杆的计算公式:1,传动比=蜗轮齿数÷蜗杆头数2,中心距=(蜗轮节径+蜗杆节径)÷2 3,蜗轮吼径=(齿数+2)×模数 4,蜗轮节径=模数×齿数5,蜗杆节径=蜗杆外径-2×模数 6,蜗杆导程=π×模数×头数7,螺旋角(导程角)tg β=(模数×头数)÷蜗杆节径 一.基本参数:(1)模数m 和压力角α:在中间平面中,为保证蜗杆蜗轮传动的正确啮合,蜗杆的轴向模数m a1和压力角αa1应分别相等于蜗轮的法面模数m t2和压力角αt2,即 m a1=m t2=m αa1=αt2蜗杆轴向压力角与法向压力角的关系为: tgαa =tgαn /cosγ 式中:γ-导程角。
(2)蜗杆的分度圆直径d 1和直径系数q为了保证蜗杆与蜗轮的正确啮合,要用与蜗杆尺寸相同的蜗杆滚刀来加工蜗轮。
由于相同的模数,可以有许多不同的蜗杆直径,这样就造成要配备很多的蜗轮滚刀,以适应不同的蜗杆直径。
显然,这样很不经济。
为了减少蜗轮滚刀的个数和便于滚刀的标准化,就对每一标准的模数规定了一定数量的蜗杆分度圆直径d1,而把及分度圆直径和模数的比称为蜗杆直径系数q ,即: q=d1/m常用的标准模数m 和蜗杆分度圆直径d1及直径系数q ,见匹配表。
(3)蜗杆头数z 1和蜗轮齿数z 2蜗杆头数可根据要求的传动比和效率来选择,一般取z1=1-10,推荐 z1=1,2,4,6。
选择的原则是:当要求传动比较大,或要求传递大的转矩时,则z1取小值;要求传动自锁时取z1=1;要求具有高的传动效率,或高速传动时,则z1取较大值。
蜗轮齿数的多少,影响运转的平稳性,并受到两个限制:最少齿数应避免发生根切与干涉,理论上应使z2min≥17,但z2<26时,啮合区显着减小,影响平稳性,而在z2≥30时,则可始终保持有两对齿以上啮合,因之通常规定z2>28。
【方案】蜗轮蜗杆的计算.doc
蜗轮、蜗杆的计算公式:1,传动比=蜗轮齿数÷蜗杆头数2,中心距=(蜗轮节径+蜗杆节径)÷23,蜗轮吼径=(齿数+2)×模数4,蜗轮节径=模数×齿数5,蜗杆节径=蜗杆外径-2×模数6,蜗杆导程=π×模数×头数7,螺旋角(导程角)tgβ=(模数×头数)÷蜗杆节径一.基本参数:(1)模数m和压力角α:在中间平面中,为保证蜗杆蜗轮传动的正确啮合,蜗杆的轴向模数m a1和压力角αa1应分别相等于蜗轮的法面模数m t2和压力角αt2,即m a1=m t2=mαa1=αt2蜗杆轴向压力角与法向压力角的关系为:tgαa=tgαn/cosγ式中:γ-导程角。
(2)蜗杆的分度圆直径d1和直径系数q为了保证蜗杆与蜗轮的正确啮合,要用与蜗杆尺寸相同的蜗杆滚刀来加工蜗轮。
由于相同的模数,可以有许多不同的蜗杆直径,这样就造成要配备很多的蜗轮滚刀,以适应不同的蜗杆直径。
显然,这样很不经济。
为了减少蜗轮滚刀的个数和便于滚刀的标准化,就对每一标准的模数规定了一定数量的蜗杆分度圆直径d1,而把及分度圆直径和模数的比称为蜗杆直径系数q,即:q=d1/m常用的标准模数m和蜗杆分度圆直径d1及直径系数q,见匹配表。
(3)蜗杆头数z1和蜗轮齿数z2蜗杆头数可根据要求的传动比和效率来选择,一般取z1=1-10,推荐z1=1,2,4,6。
选择的原则是:当要求传动比较大,或要求传递大的转矩时,则z1取小值;要求传动自锁时取z1=1;要求具有高的传动效率,或高速传动时,则z1取较大值。
蜗轮齿数的多少,影响运转的平稳性,并受到两个限制:最少齿数应避免发生根切与干涉,理论上应使z2min≥17,但z2<26时,啮合区显著减小,影响平稳性,而在z2≥30时,则可始终保持有两对齿以上啮合,因之通常规定z2>28。
另一方面z2也不能过多,当z2>80时(对于动力传动),蜗轮直径将增大过多,在结构上相应就须增大蜗杆两支承点间的跨距,影响蜗杆轴的刚度和啮合精度;对一定直径的蜗轮,如z2取得过多,模数m就减小甚多,将影响轮齿的弯曲强度;故对于动力传动,常用的范围为z2≈28-70。
蜗杆与蜗轮主要参数及几何计算
蜗杆与蜗轮主要参数及几何计算
普通圆柱蜗杆传动的基本尺寸和参数列于下表。
设计普通圆柱蜗杆减速装置时,在按接触强
后,一般应按表中的数据确定蜗杆与蜗轮的尺寸和参数,并度或弯曲强度确定了中心距a或 m2d
1
按表2值予以匹配。
表2:普通圆柱蜗杆传动的基本尺寸和参数与蜗轮参数的匹配
(200) (225) (250) 2
11 o
18’36’’
(41)
(47)
(52)
(-0.500)
(-0.375)
(+0.250) 4
21 o
48’05’’
6
30 o
57’50’’
注:1)本表中导程角γ小于3 o30’的圆柱蜗杆均为自锁蜗杆。
2)括号中的参数不适用于蜗杆头数z
1
=6时。
3)本表摘自GB10085-88。
蜗杆传动的几何尺寸及其计算公式见图1及表3表4。
图1 普通圆柱蜗杆传动的基本几何尺寸
图2:普通圆柱蜗杆传动
表3 普通圆柱蜗杆传动基本几何尺寸计算关系式
表4 蜗轮宽度B、顶圆直径d
e2及蜗杆齿宽b
1
的计算公式。