石灰煅烧技术
石灰窑悬浮煅烧工艺流程

石灰窑悬浮煅烧工艺流程一、引言石灰窑悬浮煅烧是一种常见的工业生产过程,用于将石灰石转化为消化石灰。
本文将详细介绍石灰窑悬浮煅烧的工艺流程,包括原料准备、炉内反应过程、熟料处理和烟气处理等。
二、原料准备石灰窑悬浮煅烧的原料主要是石灰石。
在生产过程中,需要将石灰石进行破碎和粉碎,以确保粒度适合反应过程的需求。
破碎后的石灰石通过输送设备送入窑炉。
三、炉内反应过程炉内反应过程是石灰窑悬浮煅烧的核心环节。
在窑炉内,将石灰石暴露在高温环境中,通过煅烧将其转化为消化石灰。
具体步骤如下:1.预热区石灰窑的上部是预热区,石灰石在这个区域被逐渐预热至较高温度。
预热区的温度通常在800°C左右,预热的目的是提高石灰石的反应活性。
2.煅烧区煅烧区是石灰窑的主要部分,温度高达1300°C以上。
在这个区域,石灰石发生分解反应,将其转化为消化石灰。
石灰窑内部采用悬浮煅烧技术,即石灰石通过气流的作用悬浮在窑内,并与高温烟气进行充分接触,使反应更加充分。
3.冷却区冷却区是石灰窑的下部,用于冷却煅烧后的石灰石。
煅烧后的消化石灰通过输送设备进入冷却区,在与冷却气体的接触中逐渐降温。
冷却后的消化石灰成为最终产品,通过输送设备送至后续处理环节。
四、熟料处理熟料处理是将煅烧后的消化石灰进行研磨和加工,以满足不同工业领域的需求。
处理过程包括碎石机的破碎、筛分和分级等步骤,最终得到符合规格要求的消化石灰产品。
五、烟气处理石灰窑悬浮煅烧过程中会产生大量的烟气,其中含有二氧化硫等有害物质。
为减少对环境的影响,需要对烟气进行处理。
常见的处理方法包括烟气脱硫、脱尘和脱氮等技术,确保煅烧过程的环保合规。
结论石灰窑悬浮煅烧是一种重要的工业生产过程,通过将石灰石转化为消化石灰,为各个行业提供了重要的原材料。
在工艺流程中,原料准备、炉内反应、熟料处理和烟气处理等环节都起到至关重要的作用。
通过科学优化工艺流程,可以提高生产效率和产品质量,同时降低对环境的影响,实现可持续发展。
石灰回转窑煅烧技术

石灰回转窑煅烧技术石灰回转窑煅烧技术是一种常用于石灰生产的工艺。
通过将石灰石放入回转窑中进行煅烧,可以将其转化为高活性的石灰,广泛应用于建筑材料、冶金、化工等行业。
一、石灰回转窑的结构和原理石灰回转窑是一种圆筒形的设备,通常由筒体、支撑装置、传动装置、焚化装置、气体进出口等部分组成。
在石灰石进入回转窑后,通过传动装置将其慢慢旋转,使石灰石在高温下进行煅烧。
石灰石煅烧的过程中,主要经历以下几个阶段:预热阶段、分解阶段、石灰化阶段和冷却阶段。
在预热阶段,石灰石中的水分和部分游离二氧化碳会被释放出来。
随着温度的升高,石灰石会进入分解阶段,二氧化碳会被彻底释放出来。
接下来是石灰化阶段,石灰石中的钙氧化物会与二氧化碳反应生成石灰。
最后是冷却阶段,石灰会被冷却至合适的温度后取出。
二、石灰回转窑煅烧技术的优势石灰回转窑煅烧技术相比于其他石灰生产工艺具有以下优势:1. 温度控制精准:石灰回转窑可以通过控制回转速度和燃烧器的热量输出来控制煅烧温度,使其达到最佳值,从而保证石灰的质量稳定。
2. 热能利用高效:石灰回转窑的结构设计使得煅烧过程中产生的余热可以被充分利用,用于预热石灰石和干燥原料,提高能源利用效率。
3. 适应性强:石灰回转窑可以适应不同种类的石灰石,且处理能力大,可以满足大规模生产的需求。
同时,还可以处理含有杂质的石灰石,提高了原料利用率。
4. 环境友好:石灰回转窑采用闭路燃烧方式,减少了烟气排放,对环境影响较小。
并且通过煅烧过程中产生的高温燃烧,可以将有害物质完全破坏,减少了对环境的污染。
三、石灰回转窑煅烧技术的应用石灰回转窑煅烧技术在建筑材料、冶金、化工等行业有着广泛的应用。
1. 建筑材料行业:石灰是制作砂浆、砖块、混凝土等建筑材料的重要原料,石灰回转窑煅烧技术可以生产出高活性的石灰,提高建筑材料的质量。
2. 冶金行业:石灰在冶金过程中有着重要的作用,可以用于炼钢、脱硫等工艺。
石灰回转窑煅烧技术可以生产出高纯度的石灰,满足冶金行业的需求。
石灰煅烧成套装备技术要求

石灰煅烧成套装备技术要求一、石灰煅烧成套装备概述石灰煅烧成套装备是指将天然石灰石进行加工处理,使其达到一定的物理和化学性质,以满足工业生产和建筑领域的需求。
该技术主要包括原料处理、炉体设计、加热方式、废气处理等方面。
二、原料处理1. 原料选择:选择纯度高、含杂质少的天然石灰石作为原料。
2. 破碎:采用颚式碎机或冲击式碎机对原料进行初步粉碎。
3. 磨粉:采用球磨机或立式辊式磨粉机对粉碎后的原料进行细化。
三、炉体设计1. 炉型选择:常见的有立式回转窑、水平回转窑和竖直加气道窑等,根据生产规模和产品要求选择合适的炉型。
2. 炉体材质:选用高温耐火材料制造,如耐火泥、高铝耐火材料等。
3. 炉壁厚度:根据不同的加工温度和物理性质,确定合适的炉壁厚度。
四、加热方式1. 直接加热:将燃料直接放入炉内,通过火焰和炉体的传导对原料进行加热。
2. 间接加热:采用电加热、蒸汽加热等方式对炉体进行加热,通过辐射和传导对原料进行加热。
五、废气处理1. 燃料选择:选择低排放的清洁能源,如天然气、液化气等。
2. 炉内减排:通过优化燃料配比和控制空气进量等方式减少废气排放。
3. 废气处理设备:采用除尘器、脱硫设备等对废气进行处理,达到环保要求。
六、技术要求1. 生产效率高:根据生产规模和产品要求,确定合适的生产线速度和产量。
2. 产品质量稳定:通过精确控制温度、时间等参数,保证产品质量稳定。
3. 能耗低排放少:采用先进的节能技术和环保措施,降低能耗和废气排放。
七、应用领域1. 建筑领域:用于生产建筑石灰、石膏等建筑材料。
2. 冶金领域:用于生产钢铁、铝等金属材料。
3. 化工领域:用于生产氧化钙、氢氧化钙等化工原料。
八、总结石灰煅烧成套装备技术要求高,需要在原料处理、炉体设计、加热方式和废气处理等方面进行精细控制。
能够满足不同领域的需求,为工业生产和建筑领域提供了重要的支持。
石灰煅烧工艺流程

石灰煅烧工艺流程
《石灰煅烧工艺流程》
石灰是一种常见的建筑材料,经过煅烧后可以得到石灰石、氧化钙和氢氧化钙等产品,广泛应用于建筑、冶金、化工等行业。
那么石灰的煅烧工艺流程是怎样的呢?
首先,原料的准备是煅烧工艺流程的第一步。
一般来说,石灰的原料主要是石灰石。
石灰石是一种含有高含量氧化钙的矿石,通过采矿、破碎和磨碎等流程,将石灰石制成符合生产需求的石灰石颗粒。
接下来就是石灰石的煅烧过程了。
石灰石在高温下煅烧,使得其中的氧化钙发生热分解反应,将氧化钙和二氧化碳分解开来,生成氧化钙和二氧化碳。
这个过程需要在高温下进行,一般需要在800°C以上的温度进行煅烧。
在石灰石煅烧完成后,得到的产物主要是氧化钙和二氧化碳。
在实际应用中,氧化钙可以继续加工成氧化钙粉、氢氧化钙等多种产品,而二氧化碳可以用于工业生产、农业生产等领域。
石灰煅烧工艺流程是一个能够将石灰石中的氧化钙释放出来的过程,通过这个过程,我们可以得到多种不同的产品,满足不同行业的需求。
而随着科技的不断进步,石灰煅烧工艺流程也在不断完善,带来更高效、环保的生产方式。
白灰窑的煅烧工艺流程

白灰窑的煅烧工艺流程白灰窑是一种重要的煅烧工艺,主要用于生产活性石灰。
煅烧是将石灰石等原料在高温下进行烧结反应,生成活性石灰的过程。
下面将介绍白灰窑的煅烧工艺流程。
首先,需要准备适当的石灰石原料。
通常情况下,白灰窑采用低硅石灰石作为原料,因为低硅石灰石的含硅量低,其中的杂质少,利于活性石灰的生成。
接下来,将石灰石原料送入白灰窑的进料口。
进料口是设置在白灰窑前部的一个开口,通过进料设备将石灰石原料从这个开口中送入白灰窑的炉膛内。
石灰石原料进入白灰窑后,首先经过预热段的处理。
预热段通常设置在白灰窑的前部,其主要功能是将石灰石原料加热至一定温度,以提高煅烧反应的速度和效率。
在预热段内,石灰石原料与高温燃烧气体进行传热和传质,实现石灰石原料的预热。
当石灰石原料通过预热段后,便进入到煅烧段。
煅烧段是白灰窑的核心部分,也是石灰石原料发生煅烧反应的地方。
在煅烧段中,石灰石原料受到高温燃烧气体的直接加热,从而使石灰石中的碳酸钙分解,产生石灰石的活性钙氧化反应。
在煅烧段内,石灰石原料经历不同的温度区域,以完成石灰石的分解反应。
首先是预分解区,温度在600-800之间,碳酸钙逐渐分解生成氧化钙和二氧化碳。
在此温度下,石灰石的结构开始松散,但是仍然存在颗粒与颗粒之间的一些物理连接。
然后是煅烧区,温度在900-1200之间,氧化钙继续分解产生更多的二氧化钙和氧化镁。
在这个温度范围内,石灰石原料的结构开始崩解,石灰石颗粒逐渐成为细小的颗粒。
最后是煅烧结束区,温度在1200-1300之间,石灰石原料的煅烧反应结束,形成活性石灰。
煅烧结束后,生成的活性石灰从白灰窑的出料口排出。
活性石灰具有较高的化学活性和强附着性,在建筑材料、环保行业、钢铁冶炼等领域有广泛的应用。
此外,为了提高白灰窑的煅烧效率和节能降耗,还可以采用一些技术措施。
例如,通过改善燃烧设备的设计和调节燃烧工艺参数,可以提高燃料的燃烧效率,减少燃料消耗量。
此外,还可以利用余热回收技术,将煅烧产生的高温烟气的余热用于预热石灰石原料或产生蒸汽等工序,提高能源利用效率。
小粒度石灰石煅烧活性石灰研究

小粒度石灰石煅烧活性石灰研究石灰回转窑煅烧工艺对石灰石入窑粒度有着严格的要求,一般石灰石粒度比不宜大于3。
酒钢西沟矿供我公司石灰石粒度为10~65mm,石灰石粒度比大,如直接入窑煅烧,在煅炼过程中容易造成物料偏析,破坏物料塌落式运动轨迹;碎料被包裹在中间或和压在料层低端,影响分解速度,石灰石分解率下降,成品率降低[1];煅烧出的石灰中粉灰多,0~10mm 的粉灰占比20%~25%,石灰CaO 含量下降,不仅影响炼钢灰质量,还造成原料浪费。
为此,我们进行了小粒度石灰石煅烧试验,并在此基础上提出了三级筛分、分级煅烧的工艺方案。
一、煅烧试验试验采用西沟矿10~65mm 石灰石筛下10~20mm小粒度石灰石,其化学成分:CaO含量53%,MgO含量1.1%,SiO2含量1.3%。
(一)试验方法试验在马弗炉内进行,通过温度控制,在马弗炉内放入一定量的10~20mm 石灰石。
一般温度取1000℃、1050℃、1100℃、1150℃,煅烧时间取80min、120min、160min。
(二)试验结果及分析也随之由低到高;当温度达到1050℃并持续升高时,石灰活性度又呈下降趋势。
因此,最佳的煅烧温度在1000~1150 ℃之间,煅烧时间控制在2~2.3h,在此煅烧条件下生产出的石灰质量好、生烧率低、活性度能达到290ml 以上,完全能够满足烧结厂和炼钢厂使用要求。
试验结果表明,回转窑煅烧小粒度石灰石,进而实行石灰石分级煅烧的工艺方案是可行的。
二、原料预处理系统设备及预热器改造方案(一)原料预处理系统设备改造目前我公司上料系统配套有3台滚筒筛,滚筒筛无法实现分级筛分,故需要将滚筒筛分系统改为分级振动筛分系统。
在筛分设备的选型上,建议选择具备三级筛分效果的分级筛,将10mm以下粉料筛下入石灰石粉地仓,供烧结制粉用,10~20mm的入原料专用地仓,20~65mm 石灰石入原料专用地仓。
同时,配套安装相应的辅助设备及单机除尘、收尘管道等环保设施。
石灰煅烧机理

石灰煅烧机理石灰煅烧是指将石灰石(CaCO3)在高温下分解成氧化钙(CaO)和二氧化碳(CO2)的过程。
这个过程不仅在工业生产中广泛应用,也在冶金、建筑、环保等领域发挥着重要作用。
本文将详细介绍石灰煅烧的机理。
石灰煅烧的机理可以通过两个主要反应来解释:石灰石的分解反应和氧化反应。
首先是石灰石的热分解反应,化学方程式为CaCO3(s) → CaO(s) + CO2(g)。
这个反应在900~1000℃之间进行,需要输入大量的热量。
石灰石分解的主要原因是在高温下,CaCO3的分解活化能降低,使得分子内的化学键能够被破坏。
具体来说,随着温度的升高,CaCO3的晶格结构发生变化,相邻Ca和CO3离子之间的距离增加,石灰石颗粒内部的压力增大,导致材料发生脆性断裂。
分子内的键被破坏后,CaO和CO2分开,形成氧化钙和二氧化碳。
其次是氧化反应,化学方程式为CaO(s) + 1/2 O2(g) → CaO(s)。
在空气中,氧化钙会与氧气发生反应,生成CaO。
这个反应是一个氧化还原反应,氧化钙失去电子生成Ca2+离子,氧气获得电子生成O2-离子。
由于氧化反应伴随着释放热量,所以这个反应是放热反应。
通过这个反应,氧化钙可以得到更加稳定的化学结构,使得石灰石的煅烧产物更加纯净。
在石灰煅烧的过程中,还有一些次要反应参与其中。
一方面,石灰石的分解反应是一个端头反应,需要从石灰石颗粒的表面开始进行。
因此,石灰石的分解速率也受到颗粒表面的条件和外界环境的影响。
另一方面,由于煅烧温度较高,石灰石颗粒中的杂质(如镁、铁、铝等)有可能发生固相反应或溶解反应。
这些反应可以改变石灰石的煅烧产物的性质,使得产物的纯度和质量发生变化。
石灰石的煅烧过程涉及到多个物理和化学因素的相互作用。
首先是温度的影响。
石灰石分解反应的速率随着温度的升高而增加,但反应速率也会受到温度过高时颗粒烧结的影响。
其次是氧气的影响。
较高的氧浓度可以提高氧化反应的速率,但过高的氧浓度会加剧石灰石颗粒的烧结现象。
石灰竖窑煅烧基础知识
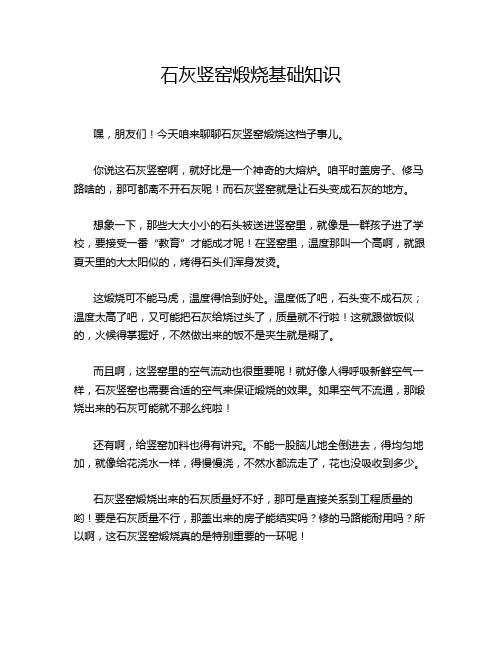
石灰竖窑煅烧基础知识
嘿,朋友们!今天咱来聊聊石灰竖窑煅烧这档子事儿。
你说这石灰竖窑啊,就好比是一个神奇的大熔炉。
咱平时盖房子、修马路啥的,那可都离不开石灰呢!而石灰竖窑就是让石头变成石灰的地方。
想象一下,那些大大小小的石头被送进竖窑里,就像是一群孩子进了学校,要接受一番“教育”才能成才呢!在竖窑里,温度那叫一个高啊,就跟夏天里的大太阳似的,烤得石头们浑身发烫。
这煅烧可不能马虎,温度得恰到好处。
温度低了吧,石头变不成石灰;温度太高了吧,又可能把石灰给烧过头了,质量就不行啦!这就跟做饭似的,火候得掌握好,不然做出来的饭不是夹生就是糊了。
而且啊,这竖窑里的空气流动也很重要呢!就好像人得呼吸新鲜空气一样,石灰竖窑也需要合适的空气来保证煅烧的效果。
如果空气不流通,那煅烧出来的石灰可能就不那么纯啦!
还有啊,给竖窑加料也得有讲究。
不能一股脑儿地全倒进去,得均匀地加,就像给花浇水一样,得慢慢浇,不然水都流走了,花也没吸收到多少。
石灰竖窑煅烧出来的石灰质量好不好,那可是直接关系到工程质量的哟!要是石灰质量不行,那盖出来的房子能结实吗?修的马路能耐用吗?所以啊,这石灰竖窑煅烧真的是特别重要的一环呢!
咱平时可能不太会注意到这些,但你想想,身边那么多建筑,哪一个离得开石灰呢?这石灰竖窑可不就是在默默地为我们的生活做贡献嘛!它就像是一个勤劳的工人,在自己的岗位上默默地工作着,为我们创造出更好的生活条件。
总之啊,石灰竖窑煅烧虽然看起来普普通通,但实际上它的作用可大啦!咱可不能小瞧了它哟!
原创不易,请尊重原创,谢谢!。
- 1、下载文档前请自行甄别文档内容的完整性,平台不提供额外的编辑、内容补充、找答案等附加服务。
- 2、"仅部分预览"的文档,不可在线预览部分如存在完整性等问题,可反馈申请退款(可完整预览的文档不适用该条件!)。
- 3、如文档侵犯您的权益,请联系客服反馈,我们会尽快为您处理(人工客服工作时间:9:00-18:30)。
《山东冶金》2003年炼钢增刊石灰竖窑高效化技术改造与工艺创新付博,武光君,马霄,孟召来(莱芜钢铁股份有限公司炼钢厂,山东莱芜 271126)摘要:在活性石灰煅烧理论研究的基础上,对传统石灰竖窑进行高效化技术改造,并改进生产工艺,使石灰窑平均利用系数和石灰活性度等各项指标大幅提高,优化了炼钢工艺,吨钢石灰单耗由59.67kg降低至45.05kg。
关键词:石灰竖窑;利用系数;活性度中图分类号:TQ175.6+53.6 文献标识码:BHigh Efficiency Technical Transformation and ProcessInnovation of Lime Shaft-kilnFU Bo, WU Guang-jun, MA Xiao, MENG Zhao-lai(The Steel-making Plant of Laiwu Iron and Steel Group Co. Ltd., Laiwu 271126 , China)Abstract:On the basis of studying on calcinations theory of active lime, the conventional lime shaft kiln is technical transformed for higher efficiency purpose and the industrial process is improved. As the result the average utilization factor and lime activity of the lime is greatly improved, the process of steel making is optimized and the consumption of the lime is decreased from 59.67kg to 45.05kg.Keywords:lime shaft-kiln;utilization coefficient;activity1 前言冶金石灰是转炉炼钢的主要熔剂,其质量高低直接影响到炼钢的质量、消耗和成本等主要技术经济指标。
莱芜钢铁股份有限公司炼钢厂(简称莱钢炼钢厂)有3座焦炭机械化石灰竖窑,其中2座传统的150m3竖窑、1座170m3改进型石灰竖窑。
竖窑有效利用系数0.7~0.8t/(m3.d);石灰活性度为220~270mL。
随着钢产量的大幅递增和“四炉对四机”全连铸生产技术的应用,石灰产质量已不能满足现代转炉炼钢高强度、快节奏、高质量的生产需要。
2001~2002年,借大修之机对2座传统石灰竖窑进行高效化技术改造,并改进传统的生产工艺,极大地提高了石灰窑有效利用系数和石灰活性度,取得了良好的效果和经济效益。
2 高效石灰煅烧理论研究竖窑有效利用系数和石灰活性度,除了与原燃料的物理和化学性能有关外,还与石灰的煅烧工艺与控制水平密切相关。
煅烧工艺主要包括窑内气相压力(分解压)、煅烧温度和煅烧时间的控制。
2.1 CaCO3的分解压力与分解温度、速度的关系CaCO3的分解过程是一个吸热、多相反应,它的平衡常数表达式为:CaCO3(s)= CaO(s) +CO2(g)其平衡常数为:Kp=PCO2/P (1)式中P—标准大气压。
因此,CaCO3的分解温度就是其分解压(PCO2)等于气相中CO2分压(PCO2)时的分解温度。
用化学反应等温方程式表示如下:△G=-RTlnKp +RTLnQP=RTlnQP/Kp(2)式中QP—非平衡时的比例常数。
只有QP <Kp,△G<0时,分解反应才能自动进行。
据此创造条件来满足石灰石的煅烧气氛:(1)减少产物[WTBZ]CO2气体的压力,即采用风机不断抽出窑气混合物,从而使QP降低。
(2)提高温度,增大Kp。
根据CaCO3的分解反应,CaCO3的分解压PCO2与分解温度T的关系可用热化学方程式表示如下:lgPCO2=-8920/T+7.54 (3)式中T—分解温度,K。
此方程可知,CaCO3在一定温度下要对应一定的分解压,并随着温度的升高而升高,而且升高的速率相当快,因此升高温度是加速CaCO3化合物分解的有效措施。
在实际生产中,石灰在窑炉内煅烧并不是理想状态下,石灰石表层在810~850℃开始分解,而内层由于分解表层CaO的气孔中充满分解析出的CO2,石灰石内层的CO2分压比窑气中高,分解温度也相应要高。
因此可通过引风机不断抽出窑气,采取负压操作,加快CaCO3的分解速度,可缩短石灰石在窑内烧成带的停留时间。
2.2 煅烧工艺对石灰活性度的影响石灰的活性度取决于它的组织结构,石灰的组织结构与煅烧温度和煅烧时间密切相关。
影响石灰活性度的组织结构包括体积密度、气孔率、比表面积和CaO矿物的晶粒尺寸。
晶粒越小,比表面积越大,气孔率越高,石灰活性就越高,化学反应能力就越强。
2.2.1煅烧时间的影响图1为石灰体积密度与煅烧时间及温度的关系。
由图1可以看出,随着煅烧时间的延长,石灰的体积密度逐渐增大,从而使石灰气孔率降低,比表面积缩小,CaO晶粒长大,石灰活性降低。
石灰石在受热分解时,放出了CO2,使石灰的晶粒上出现了空位,CaO晶粒处于不稳定状态,CaO分子比较活泼,因而活性高,这时快速冷却,把石灰这种不稳定的组织结构固定下来,石灰活性就会提高。
图1 石灰体积密度与煅烧时间和煅烧温度的关系2.2.2煅烧温度的影响煅烧温度与石灰的性质关系见表1。
由表1可知,石灰石在1000~1100℃左右的温度下生产的石灰疏松多孔,CaO晶粒高度弥散,排列杂乱且晶格有畸变,使其具有大的比表面积和高的自由能(活性度高)。
随着温度的升高,CaO晶体结构不断发育,由杂乱排列逐渐排列紧凑,结构致密,石灰体积收缩,气孔率下降,比表面积降低,石灰活性降低。
因此煅烧石灰的温度应控制在1200℃以下,最佳煅烧温度为1000~1150℃。
表1 石灰的煅烧温度与石灰性质的关系温度/℃结晶粒度/μm体积密度/g.cm-3比表面积/cm2.g-1气孔率/% 收缩率/% 过烧率/%800 0.3 1.59 19.5 52.5 0900 0.5~0.7 1.52 21.0 535.5 -2.0 5 1000 1.8 1.55 18.0 52.0 4.2 10注:表中数据引用日本住友金属株式会社测定数据。
3 传统石灰竖窑高效化改造提高设备工艺技术性能和自动化控制水平,是优化、改进传统石灰生产工艺的前提。
根据高效石灰煅烧工艺的要求,进行了高效化、自动化和智能化设计与改造。
3.1 窑衬改造,减少截面,增大高径比传统的机械化竖窑截面大,窑径比小,一般H 有效:D 内径为5~6,易造成布料、出灰不均,为此进行了设计改造。
原炉壳直径不变,加厚窑衬,内径由原来的3.4m 减少到2.9m ;有效高度由原来的18m 增加到18.2m ,使窑径比由原来的5.29提高到6.27,有效容积由原来的150m 3变为120m 3。
减少截面,有利于均匀布料和窑内气流的均匀分布,缩短在烧成带的停留时间,减少石灰生烧,预防过烧。
3.2 风帽及出灰结构创新设计传统机械化石灰窑鼓风系统由高压离心风机和圆柱形风帽组成,气流在窑内的分布趋向于四周炉壁,中间单位面积流量小,加剧了窑壁效应,易发生粘瘤。
通过窑内气流分布研究和优化设计,改为层式风帽,如图2所示。
图2 风帽及出灰结构示意图1 层式风帽2 出灰漏斗3 圆盘出灰机4 竖窑窑衬采用半径大小不同、具有三种导向角的层式风帽和容积回转式罗茨风机,使窑体统一截面上气流分布趋于一致。
同时将原拖板出灰机改造为圆盘出灰机,并由传统的双层改为单层结构出灰流量调节范围宽,且可调整圆盘出灰机正反转,保证了物料在窑内均匀流动下沉和窑内气流的合理分布。
3.3 混配设备工艺性能改进原设计混配设备中,石灰石、焦炭是靠电磁振动给料机给料,磅秤称量通过溜槽直接进入料车。
称量误差和落下误差可达1%,且物料在料车内严重偏析。
改为变频控制电极振动给料后,称量后的物料进入中间斗,通过调节中间斗出料口的大小和石灰石、焦炭给料速度,保证了焦石混配的均匀性。
3.4 电气仪表自动化、智能化控制技术的应用控制系统采用西门子可编程控制器进行控制,使现场所有信号(温度、压力、流量、控制)全部进入PLC,按生产工艺流程进行集中监视和控制。
同时,上料卷扬主令控制器由传统的LK系列的机械触点式主令改为ZNLK智能主令,形成配套的PLC控制技术,提高了设备运行的可靠率和自动化控制水平。
对窑体上二次风口、检修门、温度监测点进行了合理配置和优化,在窑体各部位安装19个测温点,可显示、贮存和打印,随时观察分析窑内各带的温度及变化趋势,有利于对窑况进行有效的控制与调节。
3.5 增设二次风与引风除尘系统对原3座竖窑的3台风机和其中1台备用风机进行联网改造,将另一台备用风机改为二次风,并与3座竖窑联网共用。
在冷却带下部设置送风管道,沿炉体周围均匀分布8只吹入边风喷嘴和流量控制。
同时,在预热带上部增设抽气引风系统,由抽气梁、袋式除尘器、引风机构成。
抽气梁为φ800mm的管道,中间接φ1000mm的风口,抽气梁高度设置在料面500mm以下。
并根据炉顶负压要求,布料器上部增设闸板密封式储料斗。
4 石灰煅烧工艺改进与新技术应用4.1 快烧快冷煅烧工艺的应用传统石灰生产工艺采用“八进八出”进出料制度和废气直排式“正压”控制,窑内物料循环慢,窑内透气性差,造成窑内通风阻力大,石灰石分解压力大,煅烧速度慢。
经过试验探索,研究应用浅进浅出、快烧快冷石灰煅烧工艺,进出料制度采用周期性上料,周期288s,日上石量300t,不停风连续作业,每0.5h出灰一次;采用废气调控式“微负压”控制,由200~250Pa改为-100~0Pa;煅烧区温度控制在1000~1100℃。
实施后,窑内物料循环由原来27h缩短到16h。
4.2 竖窑偏烧调控技术的应用偏烧是竖窑石灰生产中易发生、难处理的工艺事故。
发生偏烧时,一是窑内预热带和冷却带两头高,灰温高,出灰量减少,必须减产;二是窑内一边温度高,一边温度低,造成大量的生烧石灰和过烧石灰。
针对炉况偏烧难题,利用二次风进行炉况调控。
根据热电偶的显示温度,发现窑内煅烧带温度偏差大,有偏烧征兆时,及时打开炉内上火慢方向的二次风阀门,通过补偿风量,加速燃烧、促其上移,避免偏烧问题的出现。
4.3 竖窑粘窑预防控制技术的应用石灰窑正常生产条件下,三带位置长期稳定在某一位置,这对稳定炉况、提高质量起到较好的作用。
但也使煅烧带所挂壁瘤充分熔融长大,导致因粘瘤引起偏烧。
为了遏制所挂壁瘤充分熔融长大,通过定期性降料面操作,受到热涨冷缩作用和石料冲刷,定期清理窑壁挂瘤,预防大面积粘瘤。