气烧石灰窑
石灰窑方案

(此文档为Word格式,下载后可以任意编辑修改!)石灰窑方案编制单位:编制人:审核人:批准人:编制日期:年月日1.1 工程概述安阳150m3气烧石灰窑工程包括以下设计内容:料场、原料筛分、上料系统、3×150m3气烧石灰窑、出料系统、破碎系统、贮料系统及煤气空气加压系统等。
项目建成后,年可产活性石灰8万吨。
1.2设计原则本工程设计按照采用成熟可靠技术、工艺布置合理、运行安全顺畅、力争节省工程投资、降低消耗、安全生产的原则进行。
1.3原料1.3.1石灰石150m3气烧石灰窑要求石灰石粒度为30-70mm,其化学成份按生产冶金石灰的国家标准由生产厂选定。
1.3.2燃料150m3气烧石灰窑燃料用热值大于3300KJ/Nm3的高炉煤气。
1.4成品150m3气烧石灰窑生生的活性石灰活性度>300ml,生过烧率<10%。
本工程炼钢块灰粒度30-70mm,烧结用石灰粉<3mm。
1.5工艺流程及特点1.5.1工艺流程图11.5.2工艺特点(1)窑体结构见表1-12窑体结构表1-1(2)窑体参数见表1-2窑体参数表1-2(3)竖窑的操作方式竖窑烧制生石灰工艺上主要控制物料及火焰的均匀性,为此工艺上石灰石的粒度控制在30-70mm,使窑内具有良好的透气性,温度分布均匀,减少生过烧现象。
在竖窑预热带、煅烧带、冷却带、等处设热电偶测温仪,严格控制各带温度,保证煅烧带温度控制在900-1100℃之间。
(4) 竖窑的送风方式150m3气烧石灰窑采用底风和侧风同时送风的方式,底风保证物料的冷及燃烧,侧风保证一次风的需求量。
(5) 竖窑的排烟方式150m3气烧石灰窑排烟方式为自然排烟方式。
本工程土建内容为矿石地仓部分;皮带机通廊;1#、2#、3#立窑;破碎室机成品仓。
矿石地仓为地下钢筋混凝土板壁结构;1#、2#皮带机通廊为敞开式,其基础为混凝土结构;3#、4#皮带机通廊为砖混结构;1#、2#、3#立窑基础为钢筋混凝土大块基础;立窑斗提机坑为钢筋混凝土板壁结构;振动筛、破碎机基础为钢筋混凝土基础;破碎室为钢筋混凝土框架结构,共两层;成品仓为钢筋混凝土框架结构,其内部漏斗为钢结构。
TGS活性白灰气烧窑

用高炉煤气做气源,日产750吨活性白灰工程三种可供选择方案对比表:
的三种白灰窑对比表
日 产 750 吨
石灰石粒度 优指标窑炉 TGS 活性白 圆形气
名称
灰气烧窑 烧窑
30-60或 助燃风预热 40-80毫米 温度 ℃
240-305 210-240
混合煤气热 单炉产量 吨/
值
天
180-200 110-130
它是将传统的140M3ND 型高炉煤气石灰窑不合理的地方进行了改进。窑体本身略有 变化,产量80—100吨/天。白灰质量提高了一些,整体投资没有大的变化约80—100万元。 技术成熟可靠,风险小。
四、关于中材水泥设备有限公司 河南中材水泥装备有限公司是专业从事白灰回转窑、环保石灰窑、水泥回转窑、磨粉机、
4、哑铃形炉型为国内兄弟厂家所开发的一种新型炉型,已有多年成功生产经验。延长 了预热和冷却时间,适应了白灰导热系数低的特点,减少了炉内气流阻力,有利于白灰 窑直接使用低压煤气。 5、简易排料抽尘器,充分利用高炉除尘旧布袋,投资低,可大大改善排料过程的漏气扬 尘问题。 6、入炉原料三道筛分,分级入炉,使入炉石灰石的粒度均匀性大大提高,可进一步提高 白灰窑的料柱透气性,改善产量和质量。 7、采用装载机和皮带供料,翻斗汽车直接排料,减少了扬尘过程和工人岗位定员,提高 了机械化程度。 8、采用一套计算机系统检测多座白灰窑,既提高了检测精度,又节省了投资。 9、由于采用前述技术方案,提高了 TGS 白灰窑的机械化程度,改善了环境,提高了白灰 的质量,生烧率低于10%,活性度达300ml 以上。并使 TGS 石灰窑在低煤气压力下(5Kpa), 仍然可达到日产90吨的正常生产状态。 10 、TGS 白灰窑结构简单可靠,投资低、能耗低,维修和运行费用低。 二、TGS 活性白灰气烧窑投资 由于采用上述新技术,提高了活性白灰窑的产量和质量,一座白灰窑产量相当于别人两 座白灰窑产量,以一座日产200吨白灰窑和两座日产100吨白灰窑相比钢材可节省15%~20%, 耐材可节省约30%,可省一套上料系统、一套除尘系统,车间人员也略有减少,车间运行成 本每吨白灰可降低5~10元。如果产量相同,配置相同,TGS 白灰窑总投资可节省20%~30%, 而产品质量相对较好。 由于进口窑型不适合低热值煤气,比较适合高热值煤气。进口一座日产300~500吨白灰 窑投资高达4000万元以上;回转窑也不适应使用低热值煤气,不能作为低热值煤气的选择方 案。
石灰窑煅烧废气的原理

石灰窑煅烧废气的原理
石灰窑煅烧废气处理的原理是通过将石灰石放入石灰窑中,在高温的环境下进行煅烧。
煅烧过程中,石灰石中的碳酸钙经过分解反应,释放出二氧化碳气体和水蒸气。
废气处理的原理主要包括两个方面:
1. 煅烧过程中的脱硫:石灰石中可能含有一定的硫元素,高温下硫元素会与石灰石中的氧气发生化学反应生成二氧化硫气体。
为了减少二氧化硫对环境的污染,需要进行脱硫处理。
通常采用的方法包括喷射石灰石浆液或喷射活性炭等吸附剂,来吸附和捕集二氧化硫气体,减少其排放。
2. 废气净化处理:石灰窑煅烧过程中还会产生一些有害气体,如一氧化碳、氮氧化物等。
为了减少这些有害气体对环境的影响,常采用的方法是利用石灰窑排出的高温废气与空气进行充分混合,然后经过空气预热器等设备进行预热。
在预热过程中,通过喷洒水或白灼石灰石的方式,将有害气体进行吸附和洗涤,使其减少到允许排放标准以下。
气烧石灰窑操作手册
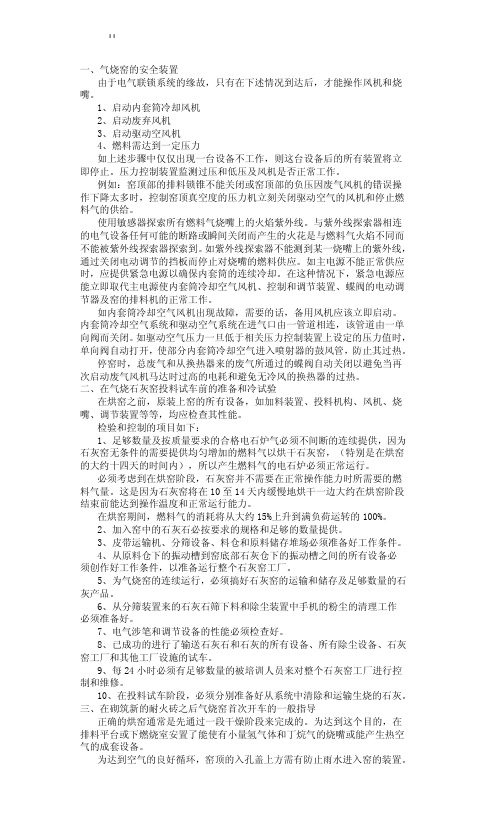
一、气烧窑的安全装置由于电气联锁系统的缘故,只有在下述情况到达后,才能操作风机和烧嘴。
1、启动内套筒冷却风机2、启动废弃风机3、启动驱动空风机4、燃料需达到一定压力如上述步骤中仅仅出现一台设备不工作,则这台设备后的所有装置将立即停止。
压力控制装置监测过压和低压及风机是否正常工作。
例如:窑顶部的排料锁锥不能关闭或窑顶部的负压因废气风机的错误操作下降太多时,控制窑顶真空度的压力机立刻关闭驱动空气的风机和停止燃料气的供给。
使用敏感器探索所有燃料气烧嘴上的火焰紫外线。
与紫外线探索器相连的电气设备任何可能的断路或瞬间关闭而产生的火花是与燃料气火焰不同而不能被紫外线探索器探索到。
如紫外线探索器不能测到某一烧嘴上的紫外线,通过关闭电动调节的挡板而停止对烧嘴的燃料供应。
如主电源不能正常供应时,应提供紧急电源以确保内套筒的连续冷却。
在这种情况下,紧急电源应能立即取代主电源使内套筒冷却空气风机、控制和调节装置、蝶阀的电动调节器及窑的排料机的正常工作。
如内套筒冷却空气风机出现故障,需要的话,备用风机应该立即启动。
内套筒冷却空气系统和驱动空气系统在进气口由一管道相连,该管道由一单向阀而关闭。
如驱动空气压力一旦低于相关压力控制装置上设定的压力值时,单向阀自动打开,使部分内套筒冷却空气进入喷射器的鼓风管,防止其过热。
停窑时,总废气和从换热器来的废气所通过的蝶阀自动关闭以避免当再次启动废气风机马达时过高的电耗和避免无冷风的换热器的过热。
二、在气烧石灰窑投料试车前的准备和冷试验在烘窑之前,原装上窑的所有设备,如加料装置、投料机构、风机、烧嘴、调节装置等等,均应检查其性能。
检验和控制的项目如下:1、足够数量及按质量要求的合格电石炉气必须不间断的连续提供,因为石灰窑无条件的需要提供均匀增加的燃料气以烘干石灰窑,(特别是在烘窑的大约十四天的时间内),所以产生燃料气的电石炉必须正常运行。
必须考虑到在烘窑阶段,石灰窑并不需要在正常操作能力时所需要的燃料气量。
气烧石灰窑知识问答
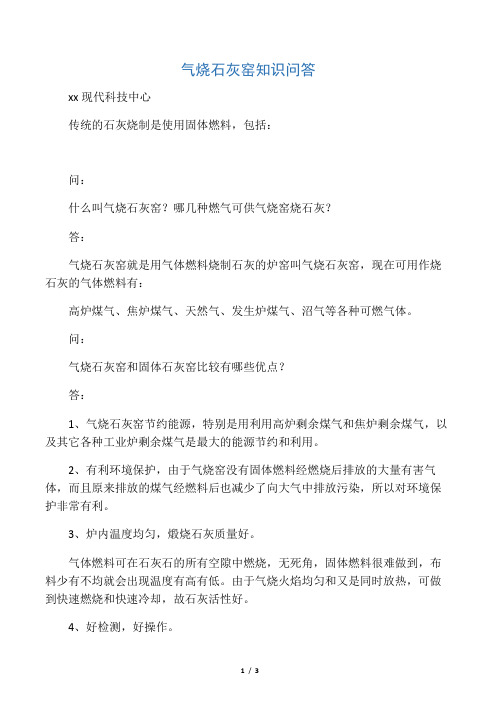
气烧石灰窑知识问答xx现代科技中心传统的石灰烧制是使用固体燃料,包括:问:什么叫气烧石灰窑?哪几种燃气可供气烧窑烧石灰?答:气烧石灰窑就是用气体燃料烧制石灰的炉窑叫气烧石灰窑,现在可用作烧石灰的气体燃料有:高炉煤气、焦炉煤气、天然气、发生炉煤气、沼气等各种可燃气体。
问:气烧石灰窑和固体石灰窑比较有哪些优点?答:1、气烧石灰窑节约能源,特别是用利用高炉剩余煤气和焦炉剩余煤气,以及其它各种工业炉剩余煤气是最大的能源节约和利用。
2、有利环境保护,由于气烧窑没有固体燃料经燃烧后排放的大量有害气体,而且原来排放的煤气经燃料后也减少了向大气中排放污染,所以对环境保护非常有利。
3、炉内温度均匀,煅烧石灰质量好。
气体燃料可在石灰石的所有空隙中燃烧,无死角,固体燃料很难做到,布料少有不均就会出现温度有高有低。
由于气烧火焰均匀和又是同时放热,可做到快速燃烧和快速冷却,故石灰活性好。
4、好检测,好操作。
因气烧窑的温度和煤气、空气流量、压力均可由仪表检测,司炉工可根据检测数据掌握炉况和调节炉况,不像固体燃料不好控制,即使该炉子还在继续燃烧,气烧窑调节周期短,固体燃料窑调节周期长。
问:气烧石灰窑烧石灰需要多少气体燃料?答:在气烧炉内煅烧一吨石灰大约需一百万千卡热量。
一般所需用不同燃料的数量则按它的最低热值换算:高炉煤气热值约850千卡故烧1吨石灰约需1200M3左右。
焦炉煤气热值约4000千卡故烧1吨石灰约需250M3左右。
发生炉煤气热值约1250千卡故烧1吨石灰约需800M3左右。
天然气热值约8000千卡故烧1吨石灰约需130M3左右。
问:气烧石灰窑都有哪几种炉型,每天能产多少石灰?答:气烧石灰窑的规格是按它的炉容体积公称的。
现在我们林州现代科技中心可设计的有26M3,50M3,120M3,140M3,甚至还有更大的。
具体规格应根据各企业的自身条件来确定,但气烧窑炉容越小越好操作。
26M3窑日(24小时)产灰在20吨左右。
气烧石灰窑热工计算
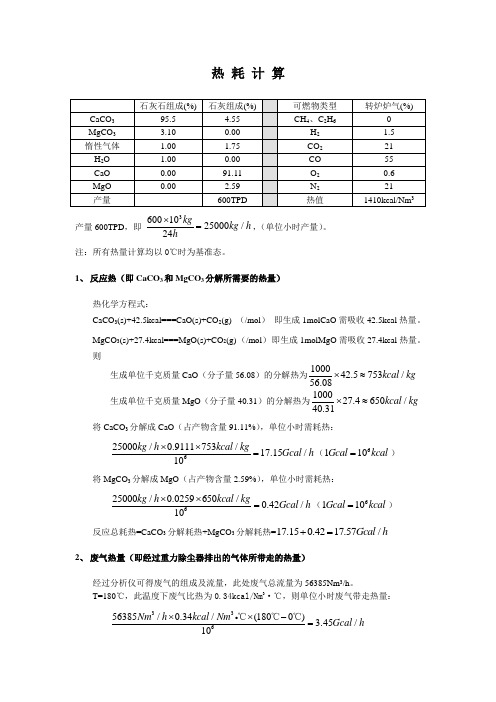
热 耗 计 算产量600TPD ,即 36001025000/24kgkg h h⨯=,(单位小时产量)。
注:所有热量计算均以0℃时为基准态。
1、 反应热(即CaCO 3和MgCO 3分解所需要的热量)热化学方程式:CaCO 3(s)+42.5kcal===CaO(s)+CO 2(g) (/mol ) 即生成1molCaO 需吸收42.5kcal 热量。
MgCO 3(s)+27.4kcal===MgO(s)+CO 2(g) (/mol ) 即生成1molMgO 需吸收27.4kcal 热量。
则生成单位千克质量CaO (分子量56.08)的分解热为100042.5753/56.08kcal kg ⨯≈生成单位千克质量MgO (分子量40.31)的分解热为100027.4650/40.31kcal kg ⨯≈将CaCO 3分解成CaO (占产物含量91.11%),单位小时需耗热:625000/0.9111753/17.15/10kg h kcal kgGcal h ⨯⨯=(6110Gcal kcal =) 将MgCO 3分解成MgO (占产物含量2.59%),单位小时需耗热:625000/0.0259650/0.42/10kg h kcal kg Gcal h ⨯⨯=(6110Gcal kcal =) 反应总耗热=CaCO 3分解耗热+MgCO 3分解耗热=17.150.4217.57/Gcal h += 2、 废气热量(即经过重力除尘器排出的气体所带走的热量)经过分析仪可得废气的组成及流量,此处废气总流量为56385Nm 3/h 。
T=180℃,此温度下废气比热为0.34kcal/Nm 3·℃,则单位小时废气带走热量:33656385/0.34/(1800)3.45/10Nm h kcal Nm Gcal h ⨯⨯-=℃℃℃3、 排放石灰热量(即窑底出灰热损,仅考虑主要成分CaO ,杂质忽略不计)CaO 比热:0.21 kcal/Nm 3·℃,温度T=80℃,则单位小时CaO 热损为:33625000/0.21/(800)0.42/10Nm h kcal Nm Gcal h⨯⨯-=℃℃℃4、 对流和辐射损失(即壁面对环境辐射+对流散热)总辐射面积=768m 2a)区域面积:219 m 2,内外温差△t=600℃,热传递系数:1kcal/hm 2·℃。
TGS石灰窑介绍7.10
TGS气烧石灰窑基本知识一、产品质量指标含义、检测方法、对转炉的影响。
1、活性度:表征生石灰水化反应速度的一个指标。
以10分钟内,搅拌条件下,在2000毫升(初温40℃)水中,用中和50克1mm ~5 mm生石灰消化时产生的Ca(OH)2所消耗的4mol/L盐酸的毫升数表示(此滴定过程始终保持水溶液处于中性)。
麦尔兹窑活性度一般在330———390 毫升(必需高热值燃料,可喷煤);回转窑活性度一般在330———390毫升(必需高热值燃料,可喷煤);套筒窑活性度一般在320—-—380毫升(必需高热值燃料);国外弗卡斯窑活性度一般在300—-—380毫升(必需高热值燃料,可喷煤,必须配有国外精确的燃料热值和流量分析计量仪表系统);国内梁式窑活性度一般在280-—-360毫升(多数在280—-—340毫升,偏重高热值煤气,低热值煤气指标差一些,特别是产量大于300吨/的窑型生产波动较大);ND140—180石灰窑活性度一般在220--—340毫升(波动较大,多数在230---320毫升,偏重低热值煤气,高热值煤气指标差一些)TGS180—--TGS350石灰窑活性度一般在280---340毫升(多数在300-——330毫升,高低热值煤气均可)TGS400--—TGS480石灰窑活性度一般在300——-360毫升(多数在320--—350毫升,高低热值煤气均可)2、在转炉中的作用:炼钢实践表明,高活性(≥280毫升)石灰融化快,在转炉内化渣快,可以提高脱磷脱硫效率和钢水品质,减少吨钢灰耗,减少渣量,减少喷溅,提高一次命中率,同时缩短冶炼时间2-3min,节省铁耗(5--—30Kg铁/t钢)、并节省氧气和铁合金的消耗。
在3—5min之内可以完全与钢水中酸性物质反应完毕,而一般石灰的反应时间至少要6-10min。
此外提高炉龄40%以上。
3、生过烧率 = 生烧率+过烧率。
(在石灰中MgO含量≤3%的情况下)生烧率 = CaO CaCO3 ÷ CaO全×100%过烧率=CaO过÷CaO全×100%CaO CaCO3-石灰中以CaCO3形式存在的CaO量CaO过—石灰中过烧部分的CaO量(遇水后一定时间还没消化的CaO。
气烧石灰竖窑的窑壁效应产生原因、预防与处理方法
气烧石灰竖窑的窑壁效应产生原因、预防与处理方法活性石灰在很多工厂生产过程中都有使用,而活性石灰的煅烧工作多采用气烧石灰竖窑,但是在实际生产中,由于窑内的气体流动难以控制,所以很容易出现垮边、掉洞等问题,这些其实都是由于窑壁效应导致的,那怎么解决气烧石灰竖窑的窑壁效应呢?一、气烧石灰竖窑产生窑壁效应的原因1、什么是窑壁效应物料在竖窑中堆积方式不同,将明显地影响气体流动过程的阻力损失。
在靠近窑璧处,物料堆积与窑壁之间的孔隙率与物料之间堆积的孔隙率相比较大,加之物料高温收缩造成环形缝隙,使得气流易于从周边通过,即在窑的同一断面上,周边空气和煤气的分配较*处为多,由于空气、煤气分配的不均匀,致使在同一断面温度不均匀,煅烧不均匀,这一现象就是窑壁效应。
2、产生原因(1)石灰窑内料层阻力不均匀,阻力小、通风很好的地方经常出现龇火风洞。
且由于通风过盛,底火越烧越浅,高温层越来越薄,加上散热严重,温度低,物料难以烧结。
当其下面料层松散有架空的空隙时,就会塌下去,造成垮边、掉洞。
(2)操作中未注意压边风(因扩大角太小),边部上火快,二胁被压死,中间底火深,造成边风压不住,物料烧不结,连续出现龇火风洞,使底火被破坏而产生垮边。
(3)石料或燃料粉料比例过高,石料中二氧化硅含量高、熔剂或配煤量不够、煤料混合不匀,造成物料不易烧结。
二、解决气烧石灰竖窑窑壁效应的方法1、预防方法石灰石的分解速度与煅烧温度的关系取决于窑内高温空气的分布与走向,而高温空气的分布与走向主要取决于窑内石料粒度的分布,即石料与石料之间的空隙大小才是决定空气的流量和走向的关键,也是热能分配均衡的重要路径。
其关键点就在于如何把不同粒径的石料进行布置在不同区域内来达到,通过对小粒度石料之间因空隙小“风阻大”原理达到热风流速慢、热量少而缩短煅烧时间,同时增加大粒度石料区域的高温空气流量和流速加快煅烧时间,使窑内煅烧带热量均衡、阻力均衡,达到整个窑面“上火”均匀一致。
TGS石灰窑介绍7.10
4、生石灰的有效CaO含量(CaO有效):在炼钢过程中,炉渣碱度R2(R2=CaO/SiO2=2.5)一般为2.5,生石灰中每1%SiO2需有2.5%的CaO来中和,去掉此部分后的CaO为有效CaO含量。
CaO有效= CaO全–2.5×SiO2
国内大中企业吨钢灰耗多数在55---65 Kg灰/t钢,先进的宝钢、武钢、沙钢等在45---55 Kg灰/t钢,很多较落后的企业在60---80 Kg灰/t钢。
我们与文丰钢铁公司一起努力,使吨钢灰耗由2003至2005年的60--75 Kg灰/t钢,降到2008年至今的29.6---39.3Kg灰/t钢(中厚板钢种),2008年全年平均35.6 Kg灰/t钢,吨钢成本降低近40元/t钢。
2)、采用余热回收,空气(助燃风)预热。炉顶助燃风预热器,设于炉顶料面以上的慢速气流空间内,有效避开了炉料和含尘气体的磨损和热膨胀问题。可将助燃风预热至220-300oC,大大提高了石灰窑的热效率,同时保护了炉顶设备。还可根据用户的节能要求增设煤气预热器,实现双预热。
3)、日本国井式侧向石灰窑烧嘴。并使用了特种耐火材料,燃烧稳定可靠,寿命长且不易回火。另外,由于此种烧嘴的燃烧原理是扩散燃烧,其穿透能力较预混烧嘴强。在窑炉中部圆周均匀分布,大侧向烧嘴和小侧向烧嘴各2排,每排烧嘴的个数有10、12、14个,具体个数根据炉型和煤气压力而定。
在中厚板、螺纹、型材等钢种冶炼过程中,经统计分析,改善这三项指标,上述效果很显著,且有如下规律:活性度主要影响化渣速度,它对吨钢灰耗的影响类似一个倾斜的“厂”字形曲线,拐点范围大体在240---260毫升;当活性度小于240毫升时,提高活性度为主要矛盾,对炼钢影响最大,此时应以提高石灰活性度为主;当活性度大于260毫升时,化渣速度已经比较快,基本可以满足炼钢要求;特别是当活性度大于280毫升时,化渣速度已经相当快,活性度就转化为次要矛盾,此时有效CaO含量(与石灰中SiO2含量关系最大)和石灰中硫含量影响更大。因此,选择优秀的窑炉和优质石灰石(包括成分和粒度)对于钢铁企业的经济效益影响很大。
工业石灰窑价格,天然气烧石灰生产工艺和投建项目成本
工业石灰窑价格,天然气烧石灰生产工艺一、石灰窑投建成本价格价格环保石灰窑的建设成本我们要了解环保石灰窑的价格,就要先了解该设备的建设成本需要多少钱,以及回转窑项目建设需要考虑和准备的工作,整个项目下来需要多少费用等,这是关乎价格的决定因素,也是用户该考虑的问题。
很多的回转窑项目都会做前期的预估,在投资一条生产回转窑的生产线时,要考虑的问题有石灰生产后的销路、生产石灰的设备从哪里购买、购买环保石灰窑的费用、整个项目所需的费用等等,然后在选购合作厂家的时候才不会盲目投资多花钱。
环保石灰窑的价格环保石灰窑价格相对来说,在市场上是比较稳定的,一般100-200万也能买的来。
但是价格不同的环保石灰窑设备,其具体的配置是不一样的,具体的价格还是需要咨询厂家进行了解的,不过一条石灰窑系统至少要百万以上。
在这里建议广大投资者还是购买质量可靠、生产实力强的厂家生产的回转窑设备,这样的回转窑设备投入成本会比较高,但是回报也会很大的。
二、新型节能环保石灰回转窑生产线工艺改进成果石灰回转窑生产线工艺的改进亮点很多,其中最重要的就是保温和热交换,其中保温我们就不在老生常谈,我们主要讲一下热交换的问题。
热交换是保障石灰窑不浪费多余的热量,使用热冷传递的原理进行冷热交换,在石灰窑从喂料机到冷却器出来,这其中一共有两次换热。
预热器换热:预热器的一侧是冷石灰石物料从给料机进入,另一侧是从石灰回转窑中煅烧过来的1150摄氏度左右的热风,然后在预热器中热冷相互传递之后可以把冷石灰石加热到600-800摄氏度,然后热风降温到200-300摄氏度,所以这一个换热的过程既没有让高温给除尘器系统增加压力,也可以让需要煅烧的冷石灰石得到提前预热反应,不但保存了热量实现节能的效果,还可以进一步的提高产量。
冷却器换热:冷却器换热则是经过煅烧的高温石灰,另一侧则是由冷风机运行吹过来的助燃冷风,所以在冷却器中经过换热之后可以把冷风温度提升到600-900摄氏度,石灰的温度则降到100摄氏度以下,这样既保留了热量又可以不给高温传送带造成高温压力,可谓是一举两得的结果。
- 1、下载文档前请自行甄别文档内容的完整性,平台不提供额外的编辑、内容补充、找答案等附加服务。
- 2、"仅部分预览"的文档,不可在线预览部分如存在完整性等问题,可反馈申请退款(可完整预览的文档不适用该条件!)。
- 3、如文档侵犯您的权益,请联系客服反馈,我们会尽快为您处理(人工客服工作时间:9:00-18:30)。
亿利4*300t/d石灰窑培训资料一、生产基本知识介绍及注意事项1.原料系统,主要设备依次为原料地坑振动给料机,倾角皮带,高效振动筛,过渡皮带,可逆皮带,分料小车。
主要注意事项:a,逆向启动,顺向停止。
b,拉绳开关和跑偏开关,拉绳开关在停止位皮带不能启动。
c,各设备转换开关需在自动。
d,原料启动前要打开除尘。
e,石灰石的成分要求:CaCO3≥95%,MgCO3≤1%,Fe2O3≤1%,Al2O3≤1%,SiO2≤1%,S≤0.1%,P≤0.008%。
粒度要求30-60mm。
2.上料系统注意事项:a,主控要时刻关注小车上料情况,避免小车撒料、冲顶。
b,主控要观察每次上料周期料钟,翻版的动作情况,以防料偏。
c,保证小车轨道、钢丝绳、卷扬机齿轮、车轮轴承、窑顶绳轮轴承的润滑。
均为普通黄油。
3.出灰系统注意事项:a,中间储灰仓灰温度高于100度时尽量不出灰,避免烧毁成品皮带。
b,出灰时可采用勤放少放的原则。
4.煤气系统注意事项:a,送气时阀门开关顺序为:电动盲板阀,蝶阀,调节阀,快切阀。
原则上送气时先开盲板阀,停气时最后关盲板阀,也可不关。
b,快切阀切断时主控要及时通知司窑关闭旋塞阀。
5.导热油系统注意事项:a,刚开窑时油温上升较快主控要注意膨胀罐油位。
b,油温超过100度时司窑要及时在排气阀处排气。
c,主控要观察每根燃烧梁导热油温度,是否基本平衡。
导热油型号HD-3206.窑体尺寸a,窑壳是由18段窑壳组成,截面积为椭圆形,外围最大尺寸为7044*5444mm,段高为1500 mm,窑壳总高25500 mm,窑壳截面积约为23 ㎡,窑底到下燃烧梁为8300mm,上下梁间距为2600mm,上燃烧梁到上吸气梁间距为12100 mm,上吸气梁到窑顶距离为2500mm。
由此可计算出灰周期:23*11*1.1(石灰堆比重)÷产量=时间。
b,保温材料,65%高铝砖(煅烧带75%高铝砖)——粘土砖——硅藻土保温砖——硅钙板——保温石棉。
(高镁砖-高铝砖-轻质保温砖-保温石棉)7.窑体共分为四个带,分别为:储料带、预热带、煅烧带、冷却带。
冷却带作用:使煅烧未完全反应的石灰可以继续利用脱碳后的石灰热量,完全煅烧成cao。
预热带的作用:使石灰石提前预热并初步分解,未煅烧带做好准备。
煅烧带为上梁以上1.5m±0.5m到下梁1m±0.5m。
二、生产操作部分1.点窑操作步骤:a,各岗位工到位,巡检检查设备,如冷却水、引风机风门,导热油系统是否正常。
电磁振动给料机出灰5—10分钟,产量6t/h 左右,以活动窑内料面(由于停窑期间,高温区石灰可能有轻微粘接,影响透气性。
出灰使窑内料层松散,提高透气性)b,启动引风机,风门打开20%左右,5Hz启动助燃风机,根据窑内压力调整引风机开口度及助燃风。
c,煤气备妥后,打开调节阀10%,打开蝶阀,然后打开快切阀,同时司窑打开放散阀。
d,置换20分钟后司窑开始点火,先点上梁,再点下梁,最后点周边烧嘴。
主控要注意煤气压力和窑内负压,及时调整引风和助燃风。
e,火全部点着后主控要将快切阀、助燃风机投入连锁,上料系统大自动,注意导热油膨胀罐的液位。
f,刚点火时火不能太大,待燃烧稳定后(约20—30分钟),再将火调整均匀,同时主控配合司窑调整引凤和助燃风,保证下梁为微负压,并调整产量。
冷窑时要注意导热油的排气。
2.停窑操作步骤:a,通知生产调度停窑,通知司窑准备关闭旋塞阀,同时主控将连锁解除,配合司窑慢慢降低电动调节阀的开度,降低助燃风和引风。
b,待司窑关闭完所有旋塞阀后,主控切断快切阀,关闭电动蝶阀,电动调节阀。
(司窑打开放散)以及助燃风机。
c,助燃风停止10-15分钟后关闭引风机,停止出灰。
d,根据停窑时间的长短,以1、2、4、8、12、18、24、32、40、48小时的时间间隔进行出灰,每次出灰时间为10分钟。
d,顶温高于100度时,拆除料位计。
3.突发事件处理:①快切阀突然切断:a,主控马上通知司窑关闭所有旋塞阀。
b,主控马上降低引风频率,防止回火爆炸。
②导热油泵停止后的处理:启动备用油泵。
③上料小车、出灰称重。
④出灰口全部停止出灰应急处理:a,降低煤气流量,但要保证窑前压力;b,人工捅料出灰。
4.产量调整:调整产量前先调燃料,10分钟后调产量。
每次调整产量应以500Kg,或200 Kg为宜,且调整间隔为4小时左右为宜,否则会影响炉况波动,造成产品质量波动。
原则为先降煤气再降产量,先加产量再加煤气。
5.司窑工看火的主要要点:a,看窑内石灰颜色,橘红色为最好(1100左右)暗红色大约750度,红色大约850度,白红色大约1300度。
b,观察石灰石的流动性。
c,作料(窑振)是否有规律,大约10分钟一次。
d,观察燃烧梁两侧是否都有料。
三、工艺部分1.生过烧的原因及处理办法:a,生烧原因:供热不足,煤气量小;原料问题,杂质太多;产量高或窑况不好,窑壁有结遛,石灰石在煅烧带停留时间短。
处理办法:增大供热,加强进料粒度管理,降低产量。
b,过烧原因:煤气量大,原料问题,产量低。
处理办法:(略)2.悬料的产生及处理:a,悬料产生的原因:1)石灰石的筛分不正常。
在石灰石的表面有夹杂物(特别是粘土)或石灰石细粒,它们在约1000℃时会使石灰石块表面粘结导致悬料。
(原料粒度较小,大小不均匀,硅铝含量高,含土量大;配气或风量大,局部气量大或局部风量大)2)废气温度过高或煤气热值过高,波动较大,而引起竖窑操作不正常,过量的供给热量会导致物料过热,废气温度过高时会促使石灰石料块表面粘结。
3)长时间停窑过程中未能充分出料,导致形成坚固的石灰石料柱。
b,处理悬料的方法1)窑内悬料可利用短时间人工快速卸料来冲击石灰石料柱,使悬料移动,出窑活性石灰温度不能升得太高,短时间最高温度不要超过150℃,悬料下方的料柱也不能下沉得太多。
(浇水也可以)2)观察孔处及烧咀处的悬料可利用钢钎将其捅碎。
出料口部位可直接砸碎。
3. 结砣的产生及处理a,结砣产生的原因1)石灰石料块带有夹杂物(主要是粘土)或石灰石细粒。
2)石灰石含低熔点物质,质量较差。
3)加入的石灰石中碳酸盐含量较少而供入的热量过多。
或燃料的热值增加而没有减少燃料的供给量。
4)窑操作不正常,导致热输入和热需求量不平衡,窑内温度分布不均,局部温度过高。
5)加入的石灰石料中细粒的比例太高,减少了窑内物料的堆积空隙,导致料流状态不稳定。
b,表明形成结砣的迹象1)窑内压力无规律2)顶温升高偏差大,热电偶温度有较大的偏差。
3)窑内料柱跳动下落,料流不稳定,间断性的窑振,振动特别大。
4)出料机上的活性石灰质量不均匀5)窑顶料斗内原料不下沉(此时结砣已经十分严重)。
c,处理结砣的方法1)当已结砣时,要停止供给煤气,只向窑内供入助燃空气,利用热冲击可使结砣与窑墙胶离或开始破裂而向下移动。
结砣下面的料位每位不能下沉得太多,以避免损坏窑体。
2)当结砣到达出料机时,一般需停窑,采用机械方法打碎结砣,以避免阻塞出料机,为了安全起见要有预防措施,以预防结砣突然下沉所造成粉尘波和热量的上升而伤人。
4.出红灰的原因及解决办法:a)原因:窑内有结块;产量大,冷却风量小;主引风频率低,负压小(导致窑底冷却风上不去,冷却带缩短);b)解决办法:适当加大负压;增加冷却风量;减少煤气量和产量。
5.煤气量、助燃风及产量的配比:a,(煤气流量*热值)/热耗=产量煤气热值大概在2300-2800大卡之间,热值=co%*30.4,热耗约等于1150Kal。
1m³煤气可煅烧(2400÷1150=2.1Kg。
)b,2CO+O2=2CO2 计算煤气:助燃风=2.2,如果废气化验co含量超过1.5%时,应适当增大助燃风或降低煤气流量。
c,CaCO3=高温=CaO+CO2( 理论吨灰耗石量1.786)实际上1吨石灰石÷1.8=石灰重量。
随着温度的升高,产生的二氧化碳增多,窑内负压会变小。
d,上下梁的助燃风比例大约为5:4,例如煅烧温度为1200度时反应最快,当上梁温度为1080度,下梁为1200度,煅烧带缩短,预热带也缩短,因此煅烧时间短,生烧高;当上梁温度为1200度,下梁温度为1200度时,煅烧带长,预热带也常,煅烧时间长,生烧低;当上梁1200度,下梁1250度时,煅烧带长,预热带长,冷却带也长,煅烧时间过长,生烧少,但过烧增多,易结窑。
e,废气温度在200——350度之间,进除尘温度在100——220度之间(布袋耐温260度)e,煤气燃点650度。
f,石灰分解温度及速度:900度,约3.4mm/h ;1000度,约6.6 mm/h ;1200度,约14 mm/h 。
3.温度分布:4.a,热量的传递方式:介质传导;真空热辐射;介质对流。
窑壁效应:由于窑壁处的间隙率大(圆面于平面的接触),透气性好,气体走捷径,使热量从窑壁处上行顺畅,导致气流速度快,使窑壁散热。
b,上梁的四根梁距离窑壁较近,所以中间温度高,气量应小一点,两头及周边气量应大一点,一克服窑壁效应。
c,下梁同上梁不同的是外侧的两根梁的气量应大一点,他距离窑壁较远,而周边烧嘴不能开得太大。
(开得太大后煤气的冲击力使煤气不能顺窑壁向上于边壁空气燃烧,且一般不配风)d,当上梁的温度达到要求1150度左右,下梁气量给到总气量的35%-40%即可,保持和上梁温度相同后果:影响窑壁寿命;废气温度高。
5.作料(窑振)产生的原因:a,石料在经过煅烧高温膨胀后,增大了石料体积,等石灰到达冷却带时体积变小,会产生缝隙,到达一定程度后,所有石灰会自动落下,产生作料,次过程中会导致窑顶负压和煅烧带负压瞬间增大。
b,作料经常作为判断窑况的重要依据。
6.石灰存储时间对活性度的影响:7.一般热电偶测得温度壁实际温度低300-350度,原因是热电偶在窑墙内一半处(大约350mm)大概一毫米减少一度。
8.各种燃气与助燃风的配比:a,焦炉煤气与风配比1:4-5,热值4200——4500。
b,电石炉尾气与风配比1:1.9-2.5。
热值2000-2500Kcal。
c,转炉煤气与风配比1:1-2热值1200-1600.d,高炉煤气与风配比1:0.6-0.8,热值600(炼铁炉)经验公式:热值÷900=配风比。