喷丸综述
激光喷丸表面强化技术的研究综述

杨启 大连理工大学博士研究生,许昌
学院讲师,研究方向为航空钛合金的 微动疲劳损伤及表面强化技术、金属 材料的失效分析及强韧化处理。
随着世界工业领域的不断发展, 各种极端和复杂条件下的工程需求 日益增加,人们对机械装备构件的综 合性能提出了更高要求。尤其在关 乎国家安全与发展的重大领域,如航 空、航天、航海、石化、电力等,尺寸超 大或精密的关键零部件具有举足轻 重的地位,其性能要求也愈发严苛。 此类构件大多造价不菲且不易更换, 如何进一步提升其机械性能,延长服 役期限,是世界科研工作者面临的共 同问题。学者们研究发现,在实际应 用中,材料的失效大多发生在表面或 亚表面。因此,表面强化的理念开始 出现并被逐步认可,现已成为众多机 械产品,尤其是关键零部件制造过程 中的关键工序,直接催生了各类表面 强化技术的蓬勃发展 。 [1–3]
观结构和硬度产生影响。1972 年, Benjamin Wilcox 团队 [20] 采用功率 密度为 1.2~2.2GW/cm2、脉宽 32ns 的
米量级,其诱导的冲击波峰值压力可 达吉帕(GPa)量级。超高压力引起的 靶材应变速率可达到 107s–1 量级,较之
所产生的反冲压力。1964 年,美国 国家航天局(NASA)的 Neuman[17] 研究发现,采用 50ns 的激光脉冲所
吸收层(又称烧蚀层,常用铝箔、黑 面的选择性定域化处理。
得显著的冲击压力。这一突破性成
漆)的工件表面,如图 1 所示 [14]。吸
总体上看,激光喷丸技术具有良 果为后续几年探索激光诱导冲击波
收层受激光辐照迅速气化、电离,形 好的柔性和适应性,在宏、微观表面 作为材料加工工具的研究打开了大
成等离子体。等离子体持续吸收能 工程领域具有广泛的应用前景。本 门。不久后,学者们就开始关注激光
(完整版)喷丸综述

喷丸综述铝合金做为一种在工业中广泛使用的金属材料,以其优良的力学强度和相对较低的密度,在航空工业中也有广泛的应用。
在使用过程中,随着使用时间的延长材料的性能总会发生变化,从而影响其使用寿命。
最主要的的失效形式为材料的断裂,引起材料发生断裂的原因主要是在使用过程中受到载荷的循环作用,使其抗疲劳性能降低,从而在高的循环载荷作用下使材料发生断裂。
材料处理不当或者材料表面完整性不好,表面凸凹不平,都会导致材料在使用过程中容易发生失效。
表面完整性是指表面形貌、表面粗糙度、表面硬度、残余应力、表面显微组织结构等内在表面状态的完好程度。
金属材料表面改性的主要目的是通过改善表面完整性来提高材料抗疲劳、抗应力腐蚀以及磨损的能力。
当前提高材料表面完整性的方法主要有物理方法、化学方法、机械方法等。
物理方法主要是采用表面淬火的方式,化学方法主要是采用渗碳或者渗氮的方式,机械方法主要有挤压、滚压、抛光、喷丸、干涉配合等方式。
与其他表面强化技术相比,喷丸表面强化技术具有强化效果显著、适用面广、耗能低、实施方便等优点,目前在航空航天、国防工业、汽车、船舶、石油化工和农业部门等重要领域得到了广泛应用。
喷丸表面强化技术就是大量高速弹丸(多为球体)重复撞击工件表面,并在其表层受弹丸撞击及附近区域形成弹塑性变形区,如图1所示。
研究认为,表面强化层的存在不仅提高了结构件表面的硬度和耐磨性,更重要的是在结构件表层形成了残余压应力层,该残余压应力层可有效降低结构件服役过程中的有效工作应力(如图2所示),使得裂纹源萌生于结构件次表面,并减缓裂纹扩展速率,从而显著地提高结构件的抗疲劳性能。
图1 喷丸表面强化技术图2 喷丸强化后结构件有效的有效应力分布在经过喷丸强化以后,在结构件表面存在的应力分布有如图3所示的分布特征,表面及次表面的残余应力为压应力,随结构件深度的增加,残余应力由压应力转变为拉应力。
整个残余应力场包括以下四个特征参量:表面残余应力、最大残余压应力、最大残余压应力层深度和残余压应力层总深度。
喷丸强化基础知识ballshotpeening

喷丸强化工艺技术简介1强化喷丸概念在了解喷丸强化技术之前,有必要将抛丸、喷砂、喷丸的三个容易混淆的概念解释一下。
这三个概念其实就四个字:喷、抛、丸、砂,其中,喷抛是工艺方法,丸砂是使用的材料。
喷,是用高压空气将丸、砂吹到工件的表面,抛是用高速旋转的叶片抛射到工件表面,丸用的是钢丸,砂用的是石英砂等。
喷丸过程就是将大量弹丸喷射到零件表面上的过程,有如无数小锤对表面锤击,因此,金属零件表面产生极为强烈的塑性形变,使零件表面产生一定厚度的冷作硬化层,称为表面强化层,此强化层会显著地提高零件的疲劳强度。
测评强化丸质量有三个基本参数:强度、覆盖率、表面粗糙度。
2喷丸强度影响喷丸强度的工艺参数主要有:弹丸直径、弹流速度、弹丸流量、喷丸时间等。
弹丸直径越大,速度越快,弹丸与工件碰撞的动量越大,喷丸的强度就越大。
喷丸形成的残余压应力可以达到零件材料抗拉强度的60%,残余压应力层的深度通常可达0. 25mm,最大极限值为1mm左右。
喷丸强度需要一定的喷丸时间来保证,经过一定时间,喷丸强度达到饱和后,再延长喷丸时间,强度不再明显增加。
在喷丸强度的阿尔门试验中,喷丸强度的表征为试片变形的拱高。
3阿尔门(Almen)试验喷丸强度常用N试片(用于有色金属试验)、A试片(最常用)、C试片(更高强度)来进行测量,A试片和C试片之间关系为近似3倍关系。
如用C试片测得强度为0. 15~0.20Cmm就相当于0.45~0.60Amm。
图中厚的为C试片,薄的为A试片。
试验过程中,先测量试片原有变形,然后将卡好该试片的工装置于喷丸箱内,采用与工件相同的工艺进行喷射。
喷丸结束,取下试片,测量变形拱高。
4喷丸覆盖率覆盖率是指工件上每一个点被钢丸打到的次数,有人对喷丸覆盖率常这样认为:我的喷嘴1上1下喷工件2遍,不就可以满足200%的覆盖率了吗?乍一听觉得有道理,其实不是这样的。
覆盖率的测量是这样的:先在工件表面涂上一层彩釉或萤光釉,然后按工艺参数对工件进行喷丸,每喷表面一遍将工件取出,在显微镜(放大镜)下观察所残留的涂层在表面所占的比例,如还有20%残留,则覆盖率为80%。
基于有限元仿真的钛合金喷丸技术应用综述

基于有限元仿真的钛合金喷丸技术应用综述1. 有限元仿真基础及钛合金喷丸技术简介随着科技的不断发展,有限元仿真技术在各个领域得到了广泛的应用。
有限元仿真是一种通过计算机模拟的方法,对复杂结构进行分析和预测的技术。
它将实际问题抽象为一系列简单的数学模型,然后利用计算机求解这些模型,从而得到问题的解答。
有限元仿真具有计算精度高、速度快、适用范围广等优点,因此在工程领域得到了广泛的应用。
钛合金喷丸技术是一种常见的金属表面处理方法,主要用于改善金属材料的表面性能和机械性能。
钛合金具有良好的力学性能、耐腐蚀性和生物相容性等特点,因此在航空航天、医疗器械等领域得到了广泛的应用。
由于钛合金的热稳定性较差,容易出现高温氧化现象,导致其性能下降。
为了解决这一问题,研究人员采用了喷丸技术对钛合金进行表面处理,以提高其抗高温氧化性能。
喷丸技术主要包括抛丸、喷丸和冲击三种形式。
抛丸是指通过高速旋转的金属颗粒对工件表面进行击打,使其产生塑性变形;喷丸是指通过高压气流将金属颗粒喷射到工件表面,使其产生塑性变形;冲击是指通过高速运动的金属块对工件表面进行撞击,使其产生塑性变形。
这三种形式的喷丸技术可以有效地改善钛合金的表面性能和机械性能。
基于有限元仿真的钛合金喷丸技术研究主要集中在以下几个方面:首先,通过对钛合金喷丸过程的有限元仿真分析,研究不同喷丸参数对材料表面形貌和性能的影响;其次,通过对钛合金喷丸过程的有限元仿真分析,研究不同喷丸方式对材料表面形貌和性能的影响;通过对钛合金喷丸过程的有限元仿真分析,研究喷丸后材料的组织演变规律和性能变化趋势。
这些研究成果有助于为实际工程应用提供理论依据和技术支持。
1.1 有限元仿真概述有限元仿真(Finite Element Simulation,简称FES)是一种通过计算机模拟工程结构在不同加载条件下的响应过程的方法。
它将复杂的结构问题转化为求解离散单元(如三角形、四边形等)的线性方程组的问题,从而实现对结构性能的预测和优化。
喷丸工艺

实践证明,强力喷丸工艺是提高齿轮齿部弯曲疲劳强度和接触疲劳强度的重要方法,是改善齿轮抗咬合能力、提高齿轮寿命的重要途径。
强力喷丸工艺最早产生于20世纪20年代,主要应用在军事领域。
随着应用范围的推广,强力喷丸工艺提高齿轮疲劳强度和寿命的能力已被很多企业所证实。
工作原理强力喷丸工艺主要是利用高速喷射的细小钢丸在室温下撞击受喷工件表面,使工件表层材料产生弹塑性变形并呈现较高的残余压应力,从而提高工件表面强度及疲劳强度。
喷丸一方面使零件表面发生弹性变形,同时也产生了大量孪晶和位错,使材料表面发生加工强化。
喷丸对表面形貌和性能的影响主要表现在改变零件的表面硬度、表面粗糙度、抗应力腐蚀能力和零件的疲劳寿命。
零件的材料表层在钢丸束的冲击下发生循环塑性变形。
根据材料的性质和状态的不同,喷丸后材料的表层将发生以下变化:硬度变化、组织结构的变化、相转变、表层残余应力场的形成、表面粗糙度的变化等。
喷丸强度的测量方法当一块金属片接受钢丸流的喷击时会产生弯曲。
饱和状态和喷丸强度是喷丸加工工艺中的两个重要概念。
饱和状态是指在同一条件下继续喷击而不再改变受喷区域机械特性时的状态。
所谓喷丸强度,就是通过打击预制成一定规格的金属片(即试片),在规定的时间使之达到饱和状态的强弱程度,并用试片弯曲的弧高值来度量其喷击的强弱程度。
目前,应用最广的美国机动车工程学会喷丸标准中采用阿尔曼提出的喷丸强化检验法——弧高度法,该方法由美国GM公司的J. O. Almen(阿尔门)提出,并由SAEJ442a和SAE 443标准规定的测量方法,其要点是用一定规格的弹簧钢试片通过检测喷丸强化后的形状变化来反映喷丸效果。
对薄板试片进行单面喷丸时,由于表面层在弹丸作用下产生参与拉伸形变,所以薄板向喷丸面呈球面弯曲。
通常在一定跨度距离上测量球面的弧高度值,用其来度量喷丸的强度。
测定弧高度值是通过将阿尔门试片固定在专用夹具上,经喷丸后,再取下试片,然后用阿尔门量规测量试片经单面喷丸作用下产生的参与拉伸形变量(即弧高度值)。
关于激光喷丸运动控制系统方面的专题综述报告
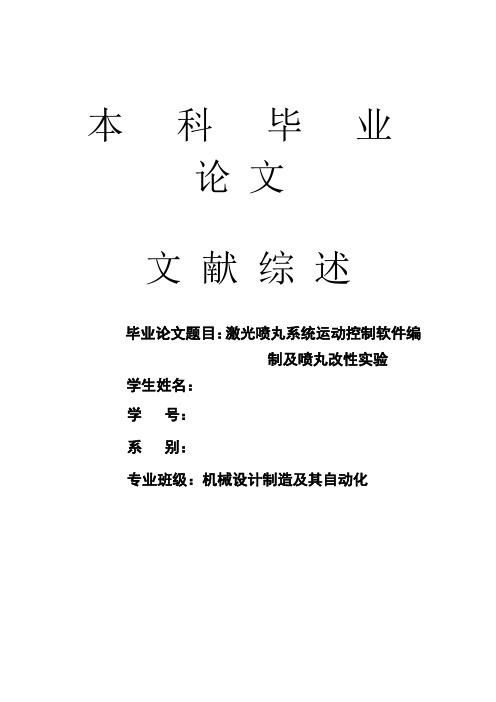
本科毕业论文文献综述毕业论文题目:激光喷丸系统运动控制软件编制及喷丸改性实验学生姓名:学号:系别:专业班级:机械设计制造及其自动化关于激光喷丸运动控制系统方面的专题综述报告机电一体化技术的发展状况是衡量一个国家机械工业发展水平的重要标志。
运动控制技术是机电一体化技术的核心部分。
因此,对运动控制技术作深入细致的研究,把握国内外运动控制技术的最新发展动态,开发运动控制类产品是摆在我们面前的一个重大课题。
在激光喷丸领域[1][2],激光喷丸工艺是利用高能脉冲激光在零件表面产生冲击波,冲击波作用于金属表面产生的机械“冷作”作用使表面金属材料达到压缩和塑性变形的效果;表面金属材料塑性变形的结果是在零件表面造成残余压应力,而残余压应力增强了零件材料对表面相关破坏(如疲劳、腐蚀疲劳和应力腐蚀裂纹)的抵抗能力。
激光喷丸工艺的最大优越性在于激光喷丸工艺可使飞机和航空发动机零部件在同一零件上的不同区域达到各自不同的抗疲劳性能。
当零件上的不同区域要求不同的抗疲劳性能时,激光喷丸工艺可以发挥其“点冷作”的优越性,通过调整工艺参数使零件不同的区域达到不同的残余应力强度和深度,从而实现不同的抗疲劳性能。
这是以往常规喷丸工艺所难以实现的,这一优越性赋予了飞机和航空发动机设计师更宽广的零件设计空间。
进行激光喷丸首先要具备激光喷丸机,由于航空零部件的结构特点和激光喷丸工艺的“点”工作特性,要求激光喷丸机具有较高的自动化程度。
利用目前成熟的三轴、四轴或五轴数控加工中心的控制系统将不难实现上述激光喷丸工艺的要求。
美国的激光喷丸设备处于相对成熟和工业应用推广阶段,但主要的应用领域还局限于航空发动机零部件,而激光喷丸设备存在的效率低是其最大的不足之处。
对国内而言现有的激光喷丸设备仅限于试验阶段,激光器的控制不成熟,这限制了激光喷丸工艺的应用和快速发展[3]。
在自动控制领域,开放式控制系统具有软件和硬件开放性,它能使人们自由的选择控制装置、伺服放大器、执行单元等,模块化开放式运动控制系统是当今运动精致技术的发展方向。
弹簧的喷丸处理技术

弹簧的喷丸处理技术
喷丸
喷丸或喷丸也被称为喷丸。
它是提高机械零件疲劳寿命的有效方法之一,在弹簧制造中得到了广泛的应用。
抛丸是用高速弹丸喷向弹簧表面,使弹簧表面发生塑性变形,从而形成一定厚度的表面强化层。
从应力状态看,补强层中形成较高的残余压应力。
由于材料表面上的残余压应力,当弹簧承受可变载荷时,它可以抵消可变载荷下的最大拉伸应力的一部分,从而提高弹簧的疲劳强度。
从组织的角度来看,强化层中形成了极高密度的位错。
在随后的应力、温度或二者的共同作用下,位错逐渐有序排列,形成多边形,即在增强层中逐渐形成较小的位错。
子粒度(子结构)。
由于表面层的冷硬化,它也有提高疲劳强度的作用。
此外,喷丸可以消除弹簧表面的缺陷(小缺陷、脱碳),降低应力集中等,从而消除或减少疲劳源。
喷丸可以减少或增加表面粗糙度。
表面粗糙度的增加不利于疲劳强度的提高。
因此,无论如何,应避免由于喷丸处理而导致表面粗糙度显著增加。
过程弹丸加工参数包括弹丸材料、弹丸尺寸、弹丸硬度、弹丸速度、弹丸流量、弹丸角度、弹丸时间、喷枪或离心轮到弹丸表面的距离。
合理选择这些工艺参数可以达到良好的喷丸效果。
喷丸强化技术概论

2021/2/6
32
(3) 弧度测具
测量标准试片弧高 度值的标准测量工 具,应符合相关的技 术要求。
2021/2/6
基准面
33
(4) 喷丸强度
在其它喷丸强化工艺参数固定的条件下,试片的 弧高度值起初随着喷丸时间而迅速增高,但随 后逐渐变缓,最终达到饱和或准饱和。
2021/2/6
22
2、组织强化
喷丸应变层内的组织结构,包括位错密度及形态 、晶粒形状、亚晶粒尺寸、相转变等方面均发 生变化。
2021/2/6
23
对于多数材料,喷丸应变层内的位错密度增高 、晶体点阵畸变增大,亚晶粒细化。
这些因素,都可以阻碍疲劳裂纹在材料表面 和次表面的萌生,延长疲劳裂纹成核寿命。
上世纪八十年代以来,国际上一度兴起了喷 丸热,各种机械零件采用喷丸强化工艺的数量 与日俱增。
1981年9月在法国巴黎召开了第一届国际喷 丸强化会议,以后每三年即召开一次。
2021/2/6
9
我国的喷丸强化工艺,首先是在航空制造工业 中得到应用。
目前国内喷丸技术十分落后,许多单位是利 用喷砂来代替喷丸,强化效果较差。
2021/2/6
+σr
δc
残
余
应 δc
力
-σr
距表面
深度δ
14
当喷丸强度恒定 时,材料强度越高 则δc 值越小
当材料强度不变 时,喷丸强度越高 则δc 越大
通 常 情 况 下 , δc 在 0 . 1 ~ 0 . 8 mm 的 范围内
2021/2/6
15
下图是300M高强钢 (σb=1900MPa)喷丸残余应力 分布曲线,可见喷丸强度由 0.13Amm增高至 0.75Amm,导致δc由0.15mm增至0.55mm,但表 面残余应力和最大残余应力变化不明显。
- 1、下载文档前请自行甄别文档内容的完整性,平台不提供额外的编辑、内容补充、找答案等附加服务。
- 2、"仅部分预览"的文档,不可在线预览部分如存在完整性等问题,可反馈申请退款(可完整预览的文档不适用该条件!)。
- 3、如文档侵犯您的权益,请联系客服反馈,我们会尽快为您处理(人工客服工作时间:9:00-18:30)。
喷丸综述铝合金做为一种在工业中广泛使用的金属材料,以其优良的力学强度和相对较低的密度,在航空工业中也有广泛的应用。
在使用过程中,随着使用时间的延长材料的性能总会发生变化,从而影响其使用寿命。
最主要的的失效形式为材料的断裂,引起材料发生断裂的原因主要是在使用过程中受到载荷的循环作用,使其抗疲劳性能降低,从而在高的循环载荷作用下使材料发生断裂。
材料处理不当或者材料表面完整性不好,表面凸凹不平,都会导致材料在使用过程中容易发生失效。
表面完整性是指表面形貌、表面粗糙度、表面硬度、残余应力、表面显微组织结构等内在表面状态的完好程度。
金属材料表面改性的主要目的是通过改善表面完整性来提高材料抗疲劳、抗应力腐蚀以及磨损的能力。
当前提高材料表面完整性的方法主要有物理方法、化学方法、机械方法等。
物理方法主要是采用表面淬火的方式,化学方法主要是采用渗碳或者渗氮的方式,机械方法主要有挤压、滚压、抛光、喷丸、干涉配合等方式。
与其他表面强化技术相比,喷丸表面强化技术具有强化效果显著、适用面广、耗能低、实施方便等优点,目前在航空航天、国防工业、汽车、船舶、石油化工和农业部门等重要领域得到了广泛应用。
喷丸表面强化技术就是大量高速弹丸(多为球体)重复撞击工件表面,并在其表层受弹丸撞击及附近区域形成弹塑性变形区,如图1所示。
研究认为,表面强化层的存在不仅提高了结构件表面的硬度和耐磨性,更重要的是在结构件表层形成了残余压应力层,该残余压应力层可有效降低结构件服役过程中的有效工作应力(如图2所示),使得裂纹源萌生于结构件次表面,并减缓裂纹扩展速率,从而显著地提高结构件的抗疲劳性能。
图1 喷丸表面强化技术图2 喷丸强化后结构件有效的有效应力分布在经过喷丸强化以后,在结构件表面存在的应力分布有如图3所示的分布特征,表面及次表面的残余应力为压应力,随结构件深度的增加,残余应力由压应力转变为拉应力。
整个残余应力场包括以下四个特征参量:表面残余应力、最大残余压应力、最大残余压应力层深度和残余压应力层总深度。
图3 喷丸残余应力场分布特征相比较传统的喷丸技术目前采用的新型喷丸技术有:预应力喷丸成形技术、数字化喷丸成形技术、激光喷丸成形技术、双面喷丸成形技术、超声喷丸成形技术、高压水喷丸成形技术等。
采用新型喷丸技术可以解决采用传统喷丸技术遇到的表面粗糙度大、喷丸强化层厚度不足等问题。
一、几种常见的喷丸强化工艺激光喷丸激光喷丸强化在材料表层诱导了高幅残余压应力,可有效降低金属构件承受交变载荷作用的拉应力水平,减小疲劳裂纹扩展的驱动力,从而有效降低疲劳裂纹萌生和扩展速率,实现疲劳寿命增益。
国内外的研究均表明,激光喷丸强化对各种招合金、镍基合金、不锈钢、钛合金、铸铁以及粉水冶金等均有良好的强化效果,除了在航空工业具有极好的应用前景外,在汽车制造、医疗卫生、海洋运输和核工业等都有潜在的应用价值。
激光喷丸工艺能够大幅度提高金属结构件的疲劳寿命,许多学者致力于研究不同激光工艺参数对金属材料疲劳性能的影响。
已有文献表明,不同激光喷丸工艺参数将诱导各异的残余压应力分布,通过合理选择工艺参数可获得所需的应力分布状态,从而实现预期的疲劳增益效果。
Rubio-Gonzalez等人实验研究了不同激光功率密度,6061-T6铝合金试样激光喷丸强化后的疲劳裂纹扩展特性。
结果表明,与未处理试样相比,激光喷丸强化可提升试样的疲劳裂纹扩展抗力。
激光喷丸后,试样表层显微硬度值增加,表层残余压应力大小及其影响层深度、断裂籾性随着激光功率密度的增加而增大,疲劳裂纹扩展速率随激光功率密度的增加而减小,当应力强度因子幅度超过20 MPa.m1/2时,激光喷丸强化对疲劳裂纹扩展速率的减缓效应较为明显。
美国休斯顿NASA研究中心的Hatamleh等人用脉冲激光喷丸7075-T7351铝合金振动摩擦挥接件,对比激光喷丸和机械喷丸对7075-T7351铝合金疲劳裂纹扩展方式的不同影响,结果表明机械喷丸使疲劳寿命提高123%,而激光喷丸大幅度降低了裂纹扩展速率,疲劳寿命增加了217%。
Ding等人研究了试样几何尺寸对激光喷丸强化效果的影响,当板材厚度不同时采用相同的工艺进行喷丸发现。
当板材厚度增加时材料表面的残余压应力增加,但是残余应力的影响深度并没有显著增加。
Ivetid等人对试样含有预制小孔的材料进行研究发现,进行激光喷丸后,材料表面以及内层残余应力的分布与其它喷丸方式没有什么太大的区别。
只是在小孔出现的时间方面有些区别,当先喷丸再钻孔的话试样的疲劳强度提高了近3倍,而先钻孔再喷丸试样的疲劳强度降低了近2倍。
该研究表明,相比于激光喷丸改性相比,激光喷丸技术更适合于加工源头制造领域。
Cudlar等人采用了四种不同的激光喷丸路径对小孔试样进行了处理,结果表明,激光喷丸路径对于试样的疲劳性能有较大的影响,因此需要根据实际情况设计合理的喷丸路径,若喷丸路径选取不当,激光喷丸会对材料的疲劳性能产生不利的影响,如仅对高应力集中附近区域进行激光喷丸,则疲劳性能改善并不明显,而对开口小孔沿圆周方向进行环状喷丸,则可获得较为明显的疲劳寿命增益。
同时对于断裂来说,一些研究发现在观察端口形貌时发现,经过喷丸处理后的材料其疲劳条带间距减小,表明经过喷丸处理后疲劳裂纹扩展速率降低。
由于影响激光喷丸的因素很多,目前研究的主要方面集中在激光频率、温度以及激光喷丸的工艺等方面。
目前采用单一的实验方法选择工艺参数相对来说比较困难,目前多数的实验过程中都会采用数值模拟技术,模拟喷完过程中应力场的变化,随后在疲劳分析软件模块中进一步进行疲劳裂纹扩展性能、疲劳寿命设计分析。
与传统基于实验的产品设计方法相比,有限元模拟仿真不仅可以计算相关结构件表面的应力、应变以及疲劳寿命分布云图,而且可以在设计阶段判断出结构件的最大应力区域和疲劳寿命薄弱位置,进而通过避免不合理的应力分布获得相对理想的疲劳寿命。
从总体上来看,相比较传统的机械喷丸来说采用激光喷丸可以大幅度提高材料抗疲劳能力,具体原因表现在采用激光喷丸,激光束并没有直接作用在材料表面,因此对表面粗糙度的影响不大,降低了应力在表面尖锐部分形成应力集中,使材料表面的残余压应力可以更好的抵消材料所受到的拉应力,从而可以大幅提高材料的抗疲劳性能。
虽然激光喷丸强化延长裂纹结构件的疲劳寿命技术得到了国内外学者的高度关注,但现阶段主要集中于试验阶段方面研究,对共性的机理方面的研究相对匮乏。
有关激光喷丸诱导残余应力场下裂纹扩展规律及其延寿机理的研究还鲜有报道,仍未形成系统的激光喷丸抗疲劳延寿的基本理论;同时,激光喷丸强化抗疲劳制造的关键技术,即强化效果的预测和控制方法也迫切需要进一步发展。
对于喷丸以后在循环应力作用下或者高温作用下应力松弛规律的研究还鲜有报道。
超声喷丸超声波喷丸技术以千瓦以上功率和大于20kHz 频率的超声波作为加工力的初始形式,通过变换能器将高频正弦波转换成纵向振动的机械能,再由变幅杆将4μm 的小微振幅放大至20~80μm,使具有高能量密度的撞针或丸粒流持续撞击成形板材,在板材表面制造极大的撞击力。
该力远超材料本身的动态屈服极限,表层材料随即发生较强的塑性变形,其微观组织得到极大碎化,板材表层受冲击区域晶粒破碎,产生细晶(甚至达到纳米级别)及稳定均匀且密集的位错,生成硬化层,同时内部诱导生成高幅的残余压应力。
受冲击后的板材成形面浅层材料由于塑性变形产生相对移动,部分下压、部分向四周延展,残余压应力不断积累,板材逐步向成形面弯曲,渐渐达到预定曲率,实现板材成形。
由此可以看出超声喷丸不仅可以实现对材料表面处理还可以实现微细精密加工。
该过程可以通过改变超声波喷丸成形技术的不同参数来实现,如撞针直径、电流强度等。
超声波喷丸技术由一开始的单弹丸撞击试验、理论研究,到现在大型板材成形与数字化模拟,经历了从理论到实践,再到产业化应用的过程,成形工艺日趋完善。
而成形之后的抗疲劳破坏、抗腐蚀性能和表面性能研究方面成为研究不同材料成形的侧重点,从国内外高水平的研究论文中发现,其中表面性能研究是主要部分,它包括表面形貌、残余压应力、表面粗糙度和表面硬度等。
太原理工大学刘海英、轧钢等人用单个弹丸撞击试样来简化超声波喷丸过程,并对此过程用ANASYS/LS-DYNA 软件进行有限元仿真,观察了残余应力的产生过程。
通过改变弹丸的材料和直径,分析残余应力在不同弹丸材料和直径下的分布情况,通过总结得出结论:材料残余应力伴随弹丸规格尺寸的变大,表面值和深度均呈增加趋势,进一步的研究表明弹丸流密度增强,也会导致相同的结果。
温爱玲,通过直径较大的撞针处理纯钛材料的表面,使得表面产生纳米晶粒层用以提高抗疲劳破坏的能力,最后用直径相对很小的丸粒修平原先坑凹状态的表面。
结果表明:疲劳强度得到极大提高,与比没有喷丸处理件提高了约52.3%,比单纯高能喷丸的试件的提高了13.6%。
产生这种现象的主要原因是在大直径撞针的作用下,材料的表面粗糙度较大而且会有显微裂纹存在,采用小直径撞针可以有效修复这些缺陷,从而使得材料表面更加光滑,有利于提高材料的表面完整性。
Katarína Miková通过采用高能喷丸的方式与普通喷丸进行对比发现,采用高能喷丸可以获得更高的残余应力值,虽然在高能喷丸的情况下材料的表面质量不高,但是依旧比普通喷丸有更好的性能。
可以进行预测,采用更高的覆盖率和喷丸强度可能可以进一步提高材料的抗疲劳强度。
提高覆盖率即对相同的区域进行重复喷丸,在这个过程中对于凸起的部分进行再次喷丸可以使其变的平整,从而降低了表面粗糙度,提高表面质量。
二、表面质量影响因素无论对于传统喷丸还是先进喷丸技术来说人们关注的重点是喷丸后的表面质量,材料的表面质量越好那么材料的性能就会越好。
目前关于表面完整性关注的主要是以下几个方面:表面粗糙度、残余应力、显微组织结构、表层致密度和表层硬度等。
因为这些因素是影响材料抗疲劳和抗腐蚀的主要原因。
因此研究的重点也是通过研究喷丸后表面质量的好坏来观测其对性能的影响。
但是在一般情况下在同一参数下想要使所有的指标都合理基本上是不可能的,因为这些指标之间会有一种对应关系,从而起到一定的限制作用。
残余应力对于残余应力来说,普遍认为残余压应力是提高工程材料抗疲劳性能和抗应力腐蚀性能的重要强化机制,而且残余压应力值大小、压应力层深度对工件疲劳强度或寿命影响显著。
因此,如何实现残余应力分布特征的调控是该领域重要研究内容之一。
残余应力的大小和分布特征受到喷丸强化工艺类型、工艺参数及材料自身属性等诸多因素影响。
残余应力数值主要取决于受喷材料自身的屈服强度、晶体结构和加工硬化率。
喷丸强化工艺参数,如喷丸强度、喷丸时间、弹丸介质和弹丸流量的选取对残余应力值大小与分布的影响明显。