动力电池自动化测试系统总体方案
中电瑞华推出电池EOL综合测试系统

中电瑞华推出电池EOL综合测试系统
中电瑞华(深圳)电子科技有限公司面向新能源汽车领域开发的电池EOL(End of Line Test/生产线下线测试应用)综合测试系统赢得市场的良好反响。
电池包EOL综合测试系统具备多项功能,诸如连接测试、短路测试、BMS通讯和错误码测试、绝缘检测、耐压检测等电气安规测试,以及程序烧录、充放电模拟、整车CAN报文模拟检测等功能。
是将众多测试仪器集成于一个设备,通过开关控制与软件集成,将众多测试项串联起来,达到连续测试的目的,优化下线的测试时间。
传统的电池包测试过程存在下线测试内容不完善,导致产品含有较大的安全与性能隐患的风险。
传统的测试方法主要依靠人工检测,但是由于数据量巨大,测试的工具和手段繁复不一,因此无法适应现今生产对产品测试高效率的要求并有效保障产品质量。
电池包EOL综合测试系统是一种全自动化的研发与生产测试平台:绝缘。
新能源汽车动力系统控制器硬件在环测试解决方案

新能源汽车动力系统控制器硬件在环测试解决方案相比较传统汽车,新能源电动汽车(包括纯电动汽车与混合动力电动汽车)动力系统增加了电机驱动系统、电池及其管理系统、整车控制器等关键零部件。
如图1所示,为一种常见的插电式混合动力汽车拓扑结构,与传统汽车相比,动力系统复杂程度增加,控制器数量增多,控制器测试的工作量与难度也相应增加。
图1 一种常见的插电式混合动力汽车拓扑结构新能源电动汽车对动力系统的动力性、经济性、制动性、排放性、可靠性等方面都有很高要求,需要对动力系统进行全面的测试,主要包括:动力性测试:最大输出功率最大扭矩加速时间最大爬坡度最高车速经济性测试:燃油消耗率平均燃油消耗量1 / 6电池能量消耗率平均电池能量消耗量制动性测试制动能量回收功能制动加速度制动距离制动时方向稳定性其它测试相关排放物含量安全防护通信故障诊断在传统的电动汽车动力系统测试中,需要使用大功率直流电源、测功机、功率分析仪、电池检测、数据采集等设备,并需要专门的配套实验室。
即使有了测试环境与测试工具,传统的测试方法还存在以下问题:耗费大量电能并产生废旧电池测试过程繁琐,耗费大量人力物力电机、电池等在极端运行环境下有较大的安全风险测试重现性较差,无法进行自动化测试使用硬件在环(HIL)测试方法,结合传统测试方法,将新能源电动汽车动力系统测试分成两个关键步骤:1.各个控制器的HIL测试,包括电池管理系统的HIL测试,电机控制器的HIL测试、整车控制器的HIL测试以及多个控制器的集成HIL测试,经过这个步骤,可以发现各个控制器存在的大部分问题,大幅降低后续大功率测试的风险与成本;2.整车动力系统的联合测试,利用HIL设备与传统测试台架相结合的联合测试台,对整车动力系统进行联合测试,用于验证动力系统的动力性、经济性、制动性、排放性、可靠性等指标,同时,对动力系统的通信、安全防护、故障诊断等进行全面测试。
相比较传统测试方法,联合测试方法可以更早地发现问题,降低风险与成本,使测试更加全面的同时缩短测试周期。
动力电池自动化测试系统总体方案修改

动力电池自动化测试系统总体方案修改一、引言随着电动汽车的普及,动力电池作为其核心组成部分之一,具有重要的功能和安全性要求。
因此,对动力电池进行准确、快速、稳定的自动化测试,是保证电池质量和性能的重要环节。
本文对现有的动力电池自动化测试系统进行修改和完善,提出了一套全新的总体方案。
二、系统概述本次修改的动力电池自动化测试系统主要包括硬件设备、测试流程和软件系统三个方面。
硬件设备包括测试平台、测试电路和相关传感器等;测试流程包括测试过程和测试指标等;软件系统包括测试控制、数据处理和报告生成等。
通过对这三个方面进行修改和优化,提高测试系统的准确性、效率和稳定性。
三、硬件设备方案修改1.测试平台方面:本次修改将原有的测试平台进行优化改造,增加电池固定装置、升降装置和可调整平台等功能,以适应不同尺寸、不同类型的电池测试需求。
2.测试电路方面:在测试电路方面,本次修改将引入更先进和精确的测试仪器和传感器,以提高测试的准确性和可靠性。
同时,加强对测试电路的防护和安全性设计,避免因测试过程中出现的电路问题对电池和操作人员造成伤害。
3.传感器方面:本次修改将增加一些新型传感器,如温度传感器、湿度传感器和振动传感器等,以获取更全面、准确的测试数据。
同时,优化传感器的布置方式,保证测试数据的高可靠性和再现性。
四、测试流程方案修改1.测试过程方面:本次修改将对现有的测试过程进行优化,增加多项测试指标,如内阻测试、电能密度测试、循环寿命测试等,以更全面地评估电池的性能和健康度。
2.测试指标方面:通过对测试指标的优化和调整,建立更合理、准确的测试标准,以确保测试结果的可靠性和一致性。
同时,加强对测试指标的数据库管理,方便后续数据分析和比对。
五、软件系统方案修改1.测试控制方面:本次修改将优化测试控制软件,增加自动化测试的稳定性和可靠性。
通过引入更高级的控制算法和自适应控制策略,提高测试系统对电池参数变化的适应能力,并能够自动调整测试参数,以获得更准确和稳定的测试结果。
星云动力锂电池组保护板测试系统BAT-NEHP36K-300

星云动力锂电池组保护板测试系统 BAT-NEHP36K-300简介星云动力锂电池组保护板测试系统 BAT-NEHP36K-300 是一种用于测试锂电池组保护板性能的设备。
该测试系统采用先进的测试技术,可以实时监测电池组的各项指标并进行全面的性能评估,帮助用户提高锂电池组的质量和可靠性。
功能特点1. 高精度测试星云动力锂电池组保护板测试系统 BAT-NEHP36K-300 采用高精度的测试仪器,能够准确测量电池组的电压、电流、温度和容量等参数,确保测试结果的准确性和可靠性。
2. 多项安全保护该测试系统具有多项安全保护功能,可以及时检测到电池组中的异常情况,并进行报警和保护措施。
例如,当电池组电压、温度超过安全范围时,系统会自动切断电池组与外部设备的连接,避免发生危险。
3. 自动化测试BAT-NEHP36K-300 具有自动化测试功能,可以根据用户的设定进行连续、定时或定量的测试,并自动生成测试报告。
这种自动化测试方式可以提高测试效率,节省时间和人力成本。
4. 多种接口该测试系统支持多种通信接口,包括USB、RS232、以太网等,方便与其他设备进行联接,实现数据的传输和管理。
同时,还具备远程控制和监测功能,用户可以通过网络远程监控测试状态和获取测试数据。
5. 易于操作BAT-NEHP36K-300 设计简洁,操作界面友好,具备用户友好的图形界面和操作指导。
即使对于没有专业电池测试经验的用户,也可以轻松上手,快速进行测试操作。
应用领域星云动力锂电池组保护板测试系统 BAT-NEHP36K-300 主要应用于锂电池组的生产、研发和质量控制过程中。
它可以对电池组的保护板进行全面测试和评估,确保电池组达到设计要求,并提供性能数据和分析报告,帮助用户改进产品质量,提高市场竞争力。
技术规格•测试通道数:36•测试电流范围:0~300A•测试电压范围:0~100V•测试温度范围:-10℃~60℃•测试精度:电流 0.1A,电压 0.01V,温度 0.1℃•通信接口:USB、RS232、以太网•输入电源:AC 220V•外形尺寸:400mm × 300mm × 200mm•重量:10kg使用说明注意:在操作之前,请确保已经详细阅读并理解用户手册中的操作规程和安全要求。
新能源汽车电池系统制造过程EOL自动检测方案研究

图1系统架构图2系统拓结构示意图2.1控制板设计图3控制面板图3中的控制板具有三路CAN通讯接口,可根据系统需求进行灵活配置,满足同一个测试系统,测量多种电池PACK的需求。
具备24路继电器高边驱动,16路继电器低边驱动。
多路继电器驱动,既能满足当前技术需求,也支持后期系统的功能扩展需求。
2.2系统功能与界面设计图4系统功能与界面系统测试主界面,如图4所示。
图形化显示电池包静态作电流和电池包总电压系统测试项目配置界面BMS系统CAN报文监测测试总报表,支持时段查询和权限分级测试报告自动生成。
2.3上位机系统设计上位机系统分登录、自动测试、系统配置、查询报表用户管理4大模块,如图5所示。
系统支持可视化、保密性以及后台参加可配置性等高兼容性;所有测试记录统一保存在SQL Server数据库服务器上。
3测试流程设计研究①测量电池包的静态工作电流:上位机通过CAN通讯控制工装板及扩展板切换将数字万用表串入电池包工作回路,读取数字万用表返回电流值并判断。
②快充CC、慢充CC、慢充CP信号读取:上位机通过CAN通讯控制工装板及扩展板分别输出快充CC、慢充CC和慢充CP信号,电池包报文返回收到的快充CC、慢充CC和慢充CP信号状态,上位机收到相关报文进行判断。
③快充电火信号、慢充点火信号和钥匙点火信号读取:上位机通过CAN通讯控制工装板及扩展板分别输出快充电火信号、慢充点火信号,电池包报文返回收到的快充电火信号、慢充点火信号状态,上位机收到相关报文进行判断。
④快充慢充指示控制:上位机通过CAN通讯控制工装板及扩展板分别输出快充、慢充信号,电池包报文返图5系统功能与界面自动化测试系统配置系统登录打印机用户管理SQL Server查询报表系统管理员管理员操作员。
SUNCH SPPT10-PCICH01动力电池测试系统 说明书

动力电池测试系统SPPT10-PCICH01一.应用领域动力电池电检柜主要用于组合电池的电性能测试,测试范围为1-4、1-7、1-12、1-15、5-14。
此系统是我公司推出的电池PCBA 性能检测的一种测试产品,各仪表采用目前国际先进的GPIB 通讯方式,主机采用先进的PXI (PCI )总线系统,基于虚拟测试平台上,其测试速度快,效率高,误测率低,性能稳定。
同时,还可根据客户自己的需要自行编辑测试脚本,操作简单,灵活,方便。
在如下行业得到广泛应用。
锂铁动力电池检测高铁动力电池检测十.应用案例天津力神电池股份有限公司二.特点系统模块化采用模块化设计,便于操作和控制;硬件组态:工控机、可编程直流电源、可编程负载、数据采集模块、内组表、数字式万用表、手动或自动电检工装等;可根据用户需求,合理选配各硬件单元,实现最高的性价比;高稳定性;高可靠性;高寿命;高精度:设备输出精度偏差控制在0.2%以内;软件组态:各测试项目设计成单元模块,可独立编辑,自由组合。
并可生成测试模板,提升管理、维护和升级的自动化程度,并极大的降低成本;显示系统配有17"液晶显示器,可以为操作者提供便捷、直观的运行情况报告;全中文操作界面,方便实用、降低使用门槛;操作软件调试、运行方便,系统可设置调试状态和自动状态两种;通讯各组成模块采用GPIB & RS232与上位机通讯,测试精度高,传输速率快;PCI总线工控主机配有网络接口,便于网络管理集中控制,实现数据实时查询、上传;丰富的其它接口:USB Device&Host、 RS232方便与外围设备连接。
测试接口采用快速拔插接头,便于测试夹具的连接;输出有GOOD与NG端口,便于夹具的声光报警装置设计;软件平台采用NI Labview软件平台,测试数据可生成多种格式,如: xls、.txt、access、sql server等,并能存档打印;智能化脚本编辑,简单的编辑方式;支持系统自动校验,可手动或自动完成设备上仪器的校验和确认;方便的MAX资源管理,便于设备中任何仪表、板卡的操作、维护;测试算法信息分类清楚、细致,能详细说明测试产品名称、测试时间、测试项目、测试状态、测试人员组别等信息;信息传输实时性强,能实时显示测试进度和数据,并用颜色区分显示测试结果,方便操作人员的测量、判断及操作;信息存储 可连续记录各电池组的测试数据,可自动按日期、电池版本号分别将测试数据存储为不同文件,方便用户管理和调用数据;信息统计分析 集成了强大的人性化统计分析功能,根据所测电池情况自动统计测试总数、合格率、各电池的测试时间及单项不合格率统计,并以柱状图显示;配件设备采用高精度可编程电源、负载集成,电子负载拉载电流平稳可靠,电流精度控制在±0.5‰以内。
动力电池PACK充放电测试方案

费思电池PACK充放电测试方案绪论:.................................................... - 1 -多次充放电循环测试、老化、一致性测试 ..................... - 2 -界面及管理介绍:...................................... - 2 -主显示界面......................................... - 2 -副显示界面:....................................... - 3 -多次充放电分析及寿命分析.............................. - 4 -总体数据分析:..................................... - 4 -电池容量老化曲线:................................. - 4 -总体参数测试:(生产及产线) ............................. - 4 -1、电池内阻:总体直流放电内阻测试内阻,(0.000000Ω). - 4 -2、过流保护点:BMS的过流保护点........................ - 5 -3、电池放电容量:电池容值。
........................... - 6 -4、最大功率点:....................................... - 7 -费思电池PACK充放电测试方案费思最新推出动力电池充放电测试方案,针对动力电池包的整体参数和组成电池包电池芯参数测试的一体分析方案。
绪论:动力电池是一个新兴行业,其电气特征及普通锂电池等电池不一样,拘于普通电池测试方法,在动力电池行业一般测试如下:单节类测试:内阻测试,采用内阻测试仪来测试(交流内阻),但是交流内阻没有办法反应大电流放电状态下的极化内阻,从而使结果严重偏小于实际值。
电池管理系统全自动测试软件设计
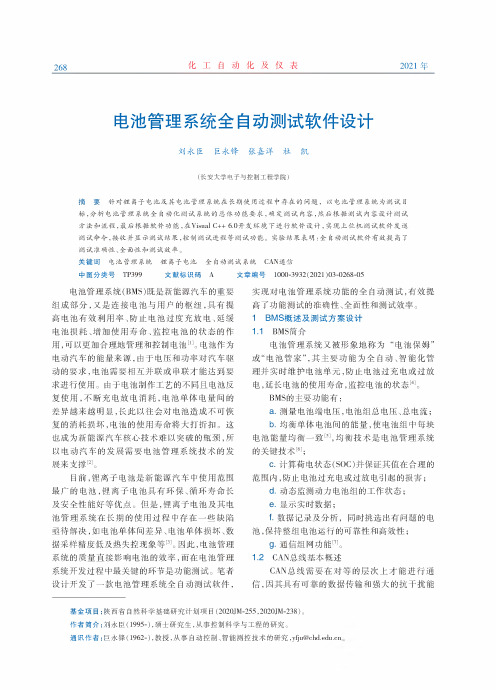
268化工自动化及仪表2021年电池管理系统全自动测试软件设计刘永臣巨永锋张嘉洋杜凯(长安大学电子与控制工程学院)摘要针对锂离子电池及其电池管理系统在长期使用过程中存在的问题,以电池管理系统为测试目标,分析电池管理系统全自动化测试系统的总体功能要求,确定测试内容,然后根据测试内容设计测试方法和流程,最后根据软件功能,在Visual C++6.0开发环境下进行软件设计,实现上位机测试软件发送测试命令,接收并显示测试结果,控制测试进程等测试功能"实验结果表明:全自动测试软件有效提高了测试准确性、全面性和测试效率。
关键词电池管理系统锂离子电池全自动测试系统CAN通信中图分类号TP399文献标识码A文章编号1000-3932(2021)03-0268-05电池管理系统(BMS"既是新能源汽车的重要组成部分,又是连接电池与用户的枢纽,具有提高电池有效利用率、防止电池过度充放电、延缓电池损耗、增加使用寿命、监控电池的状态的作用,可以更加合理地管理和控制电池[1]o电池作为电动汽车的能量来源,由于电压和功率对汽车驱动的要求,电池需要相互并联或串联才能达到要求进行使用。
由于电池制作工艺的不同且电池反复使用,不断充电放电消耗,电池单体电量间的差异越来越明显,长此以往会对电池造成不可恢复的消耗损坏,电池的使用寿命将大打折扣。
这也成为新能源汽车核心技术难以突破的瓶颈,所以电动汽车的发展需要电池管理系统技术的发展来支撑[2](目前,锂离子电池是新能源汽车中使用范围最广的电池,锂离子电池具有环保、循环寿命长及安全性能好等优点。
但是,锂离子电池及其电池管理系统在长期的使用过程中存在一些缺陷亟待解决,如电池单体间差异、电池单体损坏、数据采样精度低及热失控现象等[3](因此,电池管理系统的质量直接影响电池的效率,而在电池管理系统开发过程中最关键的环节是功能测试。
笔者设计开发了一款电池管理系统全自动测试软件,实现对电池管理系统功能的全自动测试,有效提高了功能测试的准确性、全面性和测试效率。
- 1、下载文档前请自行甄别文档内容的完整性,平台不提供额外的编辑、内容补充、找答案等附加服务。
- 2、"仅部分预览"的文档,不可在线预览部分如存在完整性等问题,可反馈申请退款(可完整预览的文档不适用该条件!)。
- 3、如文档侵犯您的权益,请联系客服反馈,我们会尽快为您处理(人工客服工作时间:9:00-18:30)。
动力电池自动化测试系统总体方案湖北德普电气股份有限公司第一部分:模组来料OCV检测系统方案一、简述本系统首先导入模组出厂数据到本地数据库,测试时通过条码扫描枪读取电池包的条码信息,按照预设好的测试方案,通过CAN总线读取BMS的电池OCV信息,并将电池OCV信息与出厂数据进行比对,按照预设的条件进行产品合格判定。
并把相关信息记录在数据库中,同时将不合格结果进行标签打印。
二、组成模组来料OCV检测系统主要由以下设备组成,系统原理框图如图1所示。
1)研华工控机2)Honeywell条码扫描枪3)NI PCI CAN通讯卡4)明纬开关电源5)NI PCI I/O板卡6)Zebra标签打印机7)扫描枪伺服系统8)附属组件图1 模组来料OCV检测系统原理框图三、功能实现技术方案图2 来料OCV检测系统示意模组来料OCV检测系统由工控机通过软件进行设备集成。
用户登录后,根据权限编写测试流程,测试流程包含扫描枪伺服系统的控制、DBC文件的选择、不合格条件的设定等,并将测试流程与条码进行模糊绑定。
在进行具体测试过程中,当完成线束连接后,可以点击启动按钮,模组来料OCV 检测系统自动按照测试方案驱动扫描枪伺服系统,扫描枪到预设位置后读取相应的条形码填入对应位置。
条形码读取完毕后自动从数据库中搜索电池的相应出厂OCV值,并根据DBC文件,自动通过PCI CAN通讯卡读取并解析相应的电池OCV信息,按照预设的判定条件进行结果判定。
完成测试后,将不合格的测试结果按照预设格式进行打印。
同时出于满足手动调试的需要,所有的操作均可以单步手动操作。
工控机内安装PCI接口的CAN通讯卡、I/O板卡。
工控机通过PCI I/O板卡控制的接触器对BMS上电、下电控制。
工控机通过PCI CAN通讯卡与BMS进行通讯,完成数据的读取与解析。
按照功能划分,软件具备如下功能:3.1人机界面提供用户的登入登出、新用户的建立、管理等功能。
软件提供了测试流程的编辑、检查、载入等功能。
并提供测试方案的启动、停止、暂停、回复等按钮,用于测试流程控制。
软件提供了电池条码信息、接触器状态、BMS信息、测试流程的状态等信息。
界面大致如下:图3 模组来料测试系统主界面示意图3.2测试流程控制软件能根据预先编制好的测试方案,按照用户的命令启动测试方案,并能按照测试方案自动的执行测试流程,并完成结果判定。
图4系统及流程3.3数据存储、管理、查询功能记录用于对电池包设备的OCV测试信息,并存储在数据库中,并提供查询界面,用于用户查询。
图5 数据管理功能示意3.4标签打印通过以太网接口,将电池包的测试结果按照定制好的格式用标签打印机打印出来,粘贴在流程卡上,便于直接查看电池包状态。
打印格式由客户定制。
四、接口及形式◆对MES的以太网通讯接口◆对电池包的CAN通讯接口◆对电池包的12VDC电源接口第二部分:绝缘测试系统方案一、简述本系统通过条码扫描枪读取电池包的条码信息,按照预设好的测试方案,依次闭合电池包引线与耐压测试仪之间的连线,并启动高压绝缘测试仪对电池包进行绝缘测试,并根据测试结果进行产品合格判定。
并把相关信息记录在数据库中,同时将结果进行标签打印。
二、组成绝缘测试系统主要由以下设备组成,系统原理框图如图1所示。
1)研华工控机2)Honeywell条码扫描枪3)Chroma 绝缘耐压测试仪4)NI PCI I/O板卡5)Zebra标签打印机6)附属组件图1 绝缘测试系统原理框图三、功能实现技术方案绝缘测试系统由工控机通过软件进行设备集成。
用户登录后,根据权限编写测试流程,测试流程包含绝缘耐压仪的参数设定、辅助接触器的闭合与断开、绝缘测试的启动停止、绝缘测试结果的判定条件等,并将测试流程与条码进行模糊绑定。
在进行具体测试过程中,当完成线束连接后,可以点击启动按钮,绝缘测试系统自动按照测试方案闭合对应的接触器、完成对绝缘耐压仪参数的设定后,自动启动绝缘耐压仪对电池包进行绝缘测试,并将测试结果按照预设好的条件进行判定。
完成测试后,将测试结果按照预设格式进行打印。
同时出于满足手动调试的需要,所有的操作均可以单步手动操作。
工控机内安装PCI接口的I/O板卡。
工控机通过PCI I/O板卡控制的接触器实现对绝缘耐压仪输出正对电池包主正、电池包主负、MSD In、MSD Out引线的互锁与切换,并利用接近开关及PC I/O板卡判定线束是否在位,进行操作命令的锁定。
工控机通过RS232口实现对绝缘耐压仪参数的传递、启停的控制等功能。
按照功能划分,软件具备如下功能:3.1人机界面提供用户的登入登出、新用户的建立、管理等功能。
软件提供了测试流程的编辑、检查、载入等功能。
并提供测试方案的启动、停止、暂停、回复等按钮,用于测试流程控制。
软件提供了电池条码信息、接触器状态、绝缘耐压仪状态及信息、测试流程的状态等信息,用于用户掌握绝缘测试系统的实时状态。
图2 测试流程设置示意3.2测试流程控制软件能根据预先编制好的测试方案,按照用户的命令启动测试方案,并能按照测试方案自动的执行测试流程,并完成结果判定。
图3 结果判定示意3.3数据存储、管理、查询功能记录用于对电池包设备的绝缘耐压测试信息,并存储在数据库中,并提供查询界面,用于用户查询。
查询方式同第一部分。
3.4标签打印通过以太网接口,将电池包的测试结果按照定制好的格式用标签打印机打印出来,粘贴在流程卡上,便于直接查看电池包状态。
四、接口及形式◆对MES的以太网通讯接口◆对电池包的耐压测试接口◆对电池包的12VDC电源接口第三部分:软件刷写测试系统方案一、简述本系统通过条码扫描枪读取电池包的条码信息,控制电源对设备上电后,调用预设好的用户程序完成对电池包的控制器应用层程序的刷写,刷写完成后控制电源重新对电池包BMS上电,检查确认系统基本参数,并将物流信息写入控制器中。
并把相关信息记录在数据库中,同时将结果进行标签打印。
二、组成软件刷写测试系统主要由以下设备组成,系统原理框图如图1所示。
1)研华工控机2)Honeywell条码扫描枪3)NI PCI CAN通讯卡4)明纬开关电源5)NI PCI I/O板卡6)Zebra标签打印机7)附属组件图1 软件刷写测试系统原理框图三、功能实现技术方案软件刷写测试系统由工控机通过软件进行设备集成。
用户登录后,根据权限编写测试流程,测试流程包含选择需要刷写的用户程序、用于解析BMS协议的DBC文件、系统基本参数的合理性的判定条件、需要写入的物流参数的设定,并将测试流程与条码进行模糊绑定。
在进行具体测试过程中,当完成线束连接后,可以点击启动按钮,软件测试系统自动完成软件的刷写、BMS的重上电、系统基本参数的判定、物流参数的写入等功能,完成测试后,将测试结果按照预设格式进行打印。
同时出于满足手动调试的需要,所有的操作均可以单步手动操作。
工控机内安装PCI接口的CAN通讯卡、I/O板卡。
工控机通过PCI I/O板卡控制的接触器对BMS上电、下电控制。
工控机通过PCI CAN通讯卡与BMS进行通讯,完成程序刷写、系统基本参数读取、物流参数的写入等功能。
按照功能划分,软件具备如下功能:3.1人机界面;提供用户的登入登出、新用户的建立、管理等功能。
软件提供了测试流程的编辑、检查、载入等功能。
并提供测试方案的启动、停止、暂停、回复等按钮,用于测试流程控制。
软件具备电池包基本参数显示、刷写过程显示、物流参数显示等,提供刷写过程中的一些必要信息。
3.2测试流程控制软件能根据预先编制好的测试方案,按照用户的命令启动测试方案,并能按照测试方案自动的执行测试流程,并完成结果判定。
3.3数据存储、管理、查询功能;记录用于对电池包设备的操作信息,并存储在数据库中,并提供查询界面,用于用户查询。
查询功能同第一部分。
3.4标签打印;通过以太网接口,将程序的刷写结果与电池包的测试结果,按照定制好的格式用标签打印机打印出来,粘贴在流程卡上,便于直接查看电池包状态。
打印内容用户定义。
四、接口及形式◆对MES的以太网通讯接口◆对电池包的CAN通讯接口◆对电池包的12VDC电源接口第四部分:电池包EOL测试系统方案一、简述电池包EOL综合测试系统是针对目前电池Pack测试过程自动化程度较低,记录分析能力较差的问题,开发的一种全智能化测试平台。
将电池充放电测试、电池安规检测、电池参数测试、BMS测试、辅助功能测试等多种功能,通过设备集成的方式,实现整个工作流程全智能化、自动化,以达到减少操作人员、提高测试效率的目的。
测试范围包含电池本体及相关辅件、BMS系统等。
二、功能、组成测试功能EOL系统的主要测试功能及分配如下表所示。
表1 EOL系统测试功能及分配列表注:开路电压测试根据精度要求不同,可用充放电测试仪或仪表进行测试组成EOL综合测试平台主要由以下设备组成,系统原理框图如图1所示。
1)充放电测试仪2)Pack自动测试柜3)研华工控机(含触摸屏显示器等)4)可编程五位半高性能数字万用表5)标准电阻模块6)NI PCI CAN通讯卡7)NI PCI AI/DI/DO接口板卡8)NI cDAQ数采板卡9)Honeywell条码扫描枪10)标签打印机11)线束在位传感器12)明纬开关电源13)附属组件如图1所示,EOL综合测试系统主要由上位机、充放电测试仪及Pack测试柜组成,其中PACK自动测试柜主要包含工控机、五位半高性能数字万用表、NI cDAQ数采板卡和标准电阻模块等。
图1 EOL系统原理图三、功能实现技术方案总体设计方案电源系统EOL综合测试平台主要由上位机、充放电测试仪及Pack自动测试柜组成,总体设计方案如下:3.1.1 上位机方案上位机作为系统控制中心,完成人机界面功能、工艺流程编制及指令的下发、数据显示和保存等功能。
设计方案如下:a)上位机硬件方案上位机采用研华工控机,其硬件配置不低于下列要求:1)CPU:Intel 双核3.0G 以上Dual core above2)硬盘:≥1T GB Hard drive abo ve 1TGB3)RAM:≥4 GB4)有相应的接口与电池测试系统通讯,PCI插槽≥2通道,RS232接口≥1通道。
PCI SLOT >=2 Channel, RS232 Connector >=1Channel5)键盘:US-ASCII Keyboard: US-ASCII6)鼠标:Mouse USB7)PCI网卡:100MB/10MB PCI Network adapter 100MB/10MB8)显示器:19英寸及以上彩色触摸屏显示器。
b)上位机软件方案按照功能划分,上位机软件具备如下功能:1)人机界面;提供用户的登入登出、新用户的建立、管理等功能;软件提供了测试流程的编辑、检查、载入等功能;并提供测试方案的启动、停止、暂停、回复等按钮,用于测试流程控制;系统软件能导入国际标准DBC文件,便于与BMS对接,并解析各种基本参数在主界面显示;软件具备电池包基本参数显示、测试过程显示、测试过程实时数据显示等,能够实时显示测试柜每一步骤的电压、电流、时间、容量、电池表面温度、能量等参数。