炼钢、铸锭过程中产生非金属夹杂物的原因
非金属夹杂的成因是钢中含有硫化物和氧化物等杂质。

非金属夹杂的成因是钢中含有硫化物和氧化
物等杂质。
钢是一种常用的金属材料,但它不可避免地含有一些非金属夹杂物,如硫化物和氧化物等。
这些夹杂物会对钢的性能产生负面影响,因此需要我们关注和解决。
硫化物是一种常见的非金属夹杂物之一。
它主要来自于原料中的硫化物和钢的生产过程中难以避免的氧化作用。
硫化物会在钢中形成硫化夹杂物,这些夹杂物会使钢的塑性和韧性降低,甚至会导致脆性断裂。
因此,在制造钢的过程中,需要采取合理的预防和控制措施来减少硫化物的含量。
氧化物也是一种常见的非金属夹杂物。
它通常来自于钢的生产过程中的氧气和其他氧化性物质。
氧化物会在钢中形成氧化夹杂物,这些夹杂物同样会降低钢的性能,如塑性、韧性和强度等。
因此,在钢的生产过程中,我们应该尽量避免或减少氧化作用,以降低氧化物的含量。
在制造钢的过程中,除了采取预防和控制措施,我们还可以通过加入一些有益元素来优化钢的性能,如添加微量元素、调整合金比例等。
这些措施有助于减少非金属夹杂物的含量,提高钢的性能,使其更符合各种应用场合的要求。
总之,非金属夹杂物是钢制品中不可避免的存在。
我们应该通过
采取合理的措施,来预防和控制夹杂物的产生,优化钢的组织和性能,使其能更好地服务于各种工业应用。
铸铁非金属夹杂物的形成原因与应对措施
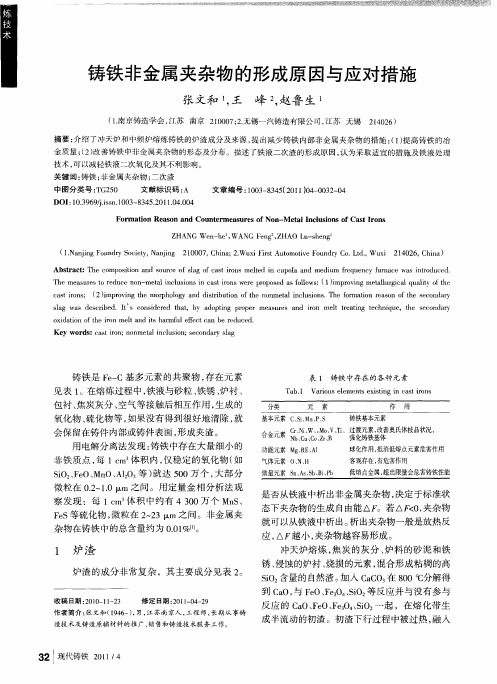
、
用电解分离法发现 : 铸铁中存在大量细小的
非铁 质 点 , 1c 3 每 m 体积 内 , 稳定 的氧化 物 ( 仅 如 SO 、e Mn A , ) 达 50万个 , i, O、 O、1 等 就 F O 0 大部 分
微 粒 在 02 1 m之 问 。用 定 量金 相 分 析 法 观 .~ . I 0x
Fo m a i n Re s n a u t r a u e fNo — e a n l so so s r n r t a o nd Co n e me s r so n M t l c u i n fCa tI o s o I Z HA NG e — e , ANG F n , HAO L — h n W n h W e Z u seg
功能元素 M ,E、l gR A 气体元素 O N、 、 i t 微量元素 s 、ss 、i b nA 、 B、 b P
钢中非金属夹杂物的分类
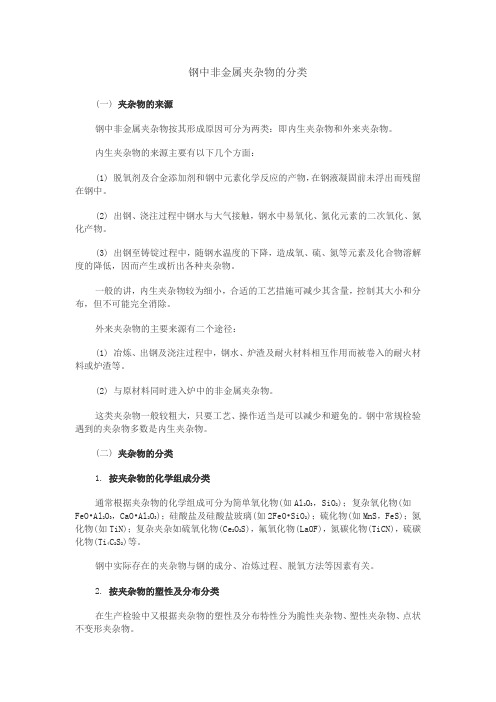
(4)半塑性夹杂物指各种复相的铝硅酸盐夹杂。基底铝硅酸盐有范性,热加工时延伸变形,但其中包含着的析出相如Al2O3等是脆性的,加工时保持原状或只是拉开距离。
除此之外,夹杂物还可根据化学稳定性的不同,分为易溶于稀酸,甚至在水中就能分解的不稳定夹杂物和在热的浓酸中才能溶解的稳定夹杂物。或按照钢的类型和成分分类等。
钢中非金属夹杂物的分类
(一)夹杂物的来源
钢中非金属夹杂物按其形成原因可分为两类:即内生夹杂物和外来夹杂物。
内生夹杂物的来源主要有以下几个方面:
(1) 脱氧剂及合金添加剂和钢中元素化学反应的产物,在钢液凝固前未浮出而残留在钢中。
(2) 出钢、浇注过程中钢水与大气接触,钢水中易氧化、氮化元素的二次氧化、氮化产物。
钢中实际存在的夹杂物与钢的成分、冶炼过程、脱氧方法等因验中又根据夹杂物的塑性及分布特性分为脆性夹杂物、塑性夹杂物、点状不变形夹杂物。
(1)塑性夹杂物热变形时具有良好的范性,沿变形方向延伸成条带状。属于这类的夹杂物有硫化物及含SiO2量较低的铁锰硅酸盐等。
(2)脆性夹杂物热加工时形状和尺寸都不变化,但可沿加工方向成串或点链状排列。属于这类的夹杂物有Al2O3,Cr2O3等。
(3) 出钢至铸锭过程中,随钢水温度的下降,造成氧、硫、氮等元素及化合物溶解度的降低,因而产生或析出各种夹杂物。
一般的讲,内生夹杂物较为细小,合适的工艺措施可减少其含量,控制其大小和分布,但不可能完全消除。
外来夹杂物的主要来源有二个途径:
(1) 冶炼、出钢及浇注过程中,钢水、炉渣及耐火材料相互作用而被卷入的耐火材料或炉渣等。
(2) 与原材料同时进入炉中的非金属夹杂物。
金属冶炼过程中的非金属夹杂物控制

扫描电镜(SEM)
总结词
扫描电镜是一种高分辨率的显微镜,能够观察金属材料表面和内部的微观结构,适用于非金属夹杂物的检测和表 征。
详细描述
扫描电镜利用电子束扫描金属材料的表面,通过收集和分析反射回来的电子信号,形成高分辨率的图像。该方法 能够观察夹杂物的形貌、大小、分布和成分等信息,具有较高的精度和分辨率。
对金属材料性能的影响
力学性能
非金属夹杂物会降低金属的力学性能,如强度、韧性、疲劳寿命等 。夹杂物的存在会导致应力集中,降低材料的抗拉强度和疲劳极限 。
物理性能
非金属夹杂物对金属的物理性能也有显著影响。例如,夹杂物会降 低金属的导电性、导热性和磁性等。
工艺性能
非金属夹杂物还会影响金属的加工性能,如焊接、热处理、塑性加工 等。夹杂物的存在可能导致焊缝开裂、热处理时组织不均匀等问题。
X射线衍射(XRD)
总结词
X射线衍射是一种用于分析金属材料 晶体结构和相组成的检测方法,可以 用于非金属夹杂物的鉴别和定量分析 。
详细描述
X射线衍射利用X射线照射金属材料, 通过分析衍射图谱来判断材料的晶体 结构和相组成。该方法能够鉴别夹杂 物的矿物组成和含量,具有较高的精 度和可靠性。
04
非金属夹杂物的控制技术与实践
金属冶炼过程中的非金属 夹杂物控制
汇报人:可编辑 2024-01-06
目录
• 非金属夹杂物的基本概述 • 非金属夹杂物的来源与控制策略 • 非金属夹杂物检测与表征技术 • 非金属夹杂物的控制技术与实践 • 非金属夹杂物控制的效果评估与优化建议 • 案例分析:某钢厂非金属夹杂物控制实践
01
非金属夹杂物的基本概述
定期检查熔炼炉内衬,确保其完 好无损,防止剥落物混入金属溶 液。
钢中非金属夹杂物 冶金工程学术语

钢中非金属夹杂物 冶金工程学术语钢中非金属夹杂物:一、定义:1、钢中非金属夹杂物,即钢中由于生产工序中所添加或引入的非金属材料,含有量小于1%且未熔融蒙皱的非金属材料。
2、根据夹杂物的外观与性质,可分为夹杂物胶质、韧性夹杂物、疲态的夹杂物,并可分为气泡、结晶等。
二、来源:1、主要来自钢坯冶炼过程中的熔法夹杂物,包括熔焊未熔化的冶金夹杂物、冷轧滚压的钢坯夹入的非金属晶体、熔炼用的除合金外的所有熔炼材料及冶炼布料溶解释放的夹杂物等。
2、熔融时引入,主要是调控钢坯成分时,所加入的金属合金元素中副产物(如小粒性铜);3、冶炼表面夹杂物:铸造时,冶炼表面有一定厚度熔融物膜沿着熔池表面顺着操作者加入熔坑时留下;4、熔焊夹杂物:发生在焊接结构中,其原因是熔接过程尚未完全焊接的金属件或者是熔接辅助材料及设备本身的一些杂物;5、冷轧夹杂物:冷轧过程中,加工物料之间产生的一些非金属物质和其它杂物,以及工艺仓内的尘埃等物质;6、其他:还有拉伸挤压、热处理、渗碳等工艺过程中,钢件表面所带有的夹杂物。
三、对钢的影响:1、影响钢的组织:夹杂物更像一个污染物,可以影响钢材的组织,使其产生不稳定性,影响到制品的力学性能。
2、影响钢的力学性能:夹杂物可以影响到钢材的形变构件的力学性能,减少它的抗弯强度。
3、影响钢的热强度:夹杂物颗粒本身比铁素体块大,它对整个模型的形变活动会造成一定影响,减少钢材热强度。
4、影响钢的变形性能:夹杂物颗粒之间空腔增加,会影响钢材的变形性能,减少制品在变形过程中的完整性。
5、可能会引起腐蚀:气泡、结晶夹杂物会对钢中各种合金元素的变迁和释放影响,加速钢材对溶液的吸收和溶解,从而损坏钢材表面的质量和尺寸精度,引起腐蚀缺陷。
四、检测方法:1、穿透式X射线:一种比较先进的非接触式检测方法。
它利用X射线通过物体穿透,经过X射线照射,把物体直接放入X射线管中,以检测不同物质对X射线的不同穿透率,以判断物体是否存在夹杂物。
非金属夹杂物

非金属夹杂物1概述在炼钢过程中,少量炉渣、耐火材料及冶炼中反应产物可能进入钢液,形成非金属夹杂物。
它们都会降低钢的机械性能,特别是降低塑性、韧性及疲劳极限。
严重时,还会使钢在热加工与热处理时产生裂纹或使用时突然脆断。
非金属夹杂物也促使钢形成热加工纤维组织与带状组织,使材料具有各向异性。
严重时,横向塑性仅为纵向的一半,并使冲击韧性大为降低。
因此,对重要用途的钢(如滚动轴承钢、弹簧钢等)要检查非金属夹杂物的数量、形状、大小与分布情况。
此外,钢在整个冶炼过程中,都与空气接触,因而钢液中总会吸收一些气体,如氮、氧、氢等。
它们对钢的质量也会产生不良影响。
钢中非金属夹杂物根据不源可分两大类,即外来非金属夹杂物和内在非金属夹杂物。
外来非金属夹杂物是钢冶炼、浇注过程中炉渣及耐火材料浸蚀剥落后进入钢液而形成的,内在非金属夹杂物主要是冶炼、浇注过程中物理化学反应的生成物,如脱氧产物等等。
常见的内在非金属夹杂物有以下几种;(a)氧化物,常见的为Al2O3;(b)硫化物,如FeS、MnS、(MnS·FeS)等;(c)硅酸盐,如硅酸亚铁(2FeO·SiO2)、硅酸亚锰(2MnO·SiO2)、铁锰硅酸盐(mFeO·MnO·SiO2)等;(d)氮化物,如TiN、ZrN等;点状不变形夹杂物等。
2危害不同形态的夹杂物混杂在金属内部,破坏了金属的连续性和完整性。
夹杂物同金属之间的结合情况不同、弹性和塑性的不同以及热膨胀系数的差异,常使金属材料的塑性、韧性、强度、疲劳极限和耐蚀性等受到显著影响,同时也常常影响加工零件的表面质量和加工工具的寿命。
非金属夹杂分塑性夹杂和脆性夹杂。
塑性夹杂如MnS等随金属变形而延伸轧薄。
脆性夹杂如Al:0。
等随金属变形而破碎。
另一些夹杂物软化点及硬度很高,热加工中不变形,不破碎,保持原来形状,如TIN、稀土硫氧化物等。
铜中氧化夹杂CuZO常分布在晶界上,Cu20是一种硬脆相,会降低金属的热塑性,还影响铜的导电能力。
圆钢 非金属夹杂物
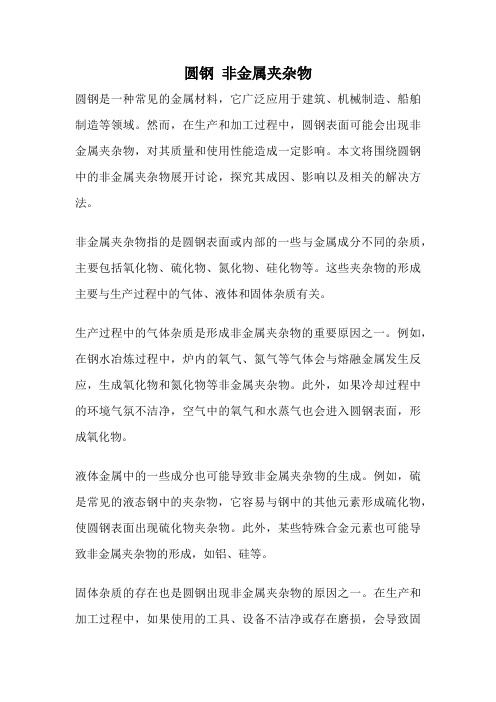
圆钢非金属夹杂物圆钢是一种常见的金属材料,它广泛应用于建筑、机械制造、船舶制造等领域。
然而,在生产和加工过程中,圆钢表面可能会出现非金属夹杂物,对其质量和使用性能造成一定影响。
本文将围绕圆钢中的非金属夹杂物展开讨论,探究其成因、影响以及相关的解决方法。
非金属夹杂物指的是圆钢表面或内部的一些与金属成分不同的杂质,主要包括氧化物、硫化物、氮化物、硅化物等。
这些夹杂物的形成主要与生产过程中的气体、液体和固体杂质有关。
生产过程中的气体杂质是形成非金属夹杂物的重要原因之一。
例如,在钢水冶炼过程中,炉内的氧气、氮气等气体会与熔融金属发生反应,生成氧化物和氮化物等非金属夹杂物。
此外,如果冷却过程中的环境气氛不洁净,空气中的氧气和水蒸气也会进入圆钢表面,形成氧化物。
液体金属中的一些成分也可能导致非金属夹杂物的生成。
例如,硫是常见的液态钢中的夹杂物,它容易与钢中的其他元素形成硫化物,使圆钢表面出现硫化物夹杂物。
此外,某些特殊合金元素也可能导致非金属夹杂物的形成,如铝、硅等。
固体杂质的存在也是圆钢出现非金属夹杂物的原因之一。
在生产和加工过程中,如果使用的工具、设备不洁净或存在磨损,会导致固体杂质进入圆钢表面或内部,形成非金属夹杂物。
此外,如果生产环境中存在灰尘、颗粒等固体杂质,也可能被带入圆钢表面,形成夹杂物。
非金属夹杂物对圆钢的质量和使用性能产生一定的影响。
首先,非金属夹杂物会降低圆钢的强度和韧性,使其易于断裂和变形。
其次,夹杂物的存在还会影响圆钢的导电性和导热性能,降低其传导效率。
此外,非金属夹杂物还会降低圆钢的耐腐蚀性能,使其易受到氧化、腐蚀等损害。
针对圆钢中的非金属夹杂物问题,可以采取一些解决方法来提高其质量。
首先,生产过程中应加强对气体、液体和固体杂质的控制,确保环境洁净。
其次,可以通过优化冶炼工艺和添加合适的合金元素来减少非金属夹杂物的生成。
此外,加强对工具、设备的维护和保养,防止固体杂质的污染也是很重要的一步。
钢中非金属夹杂物的起源和控制
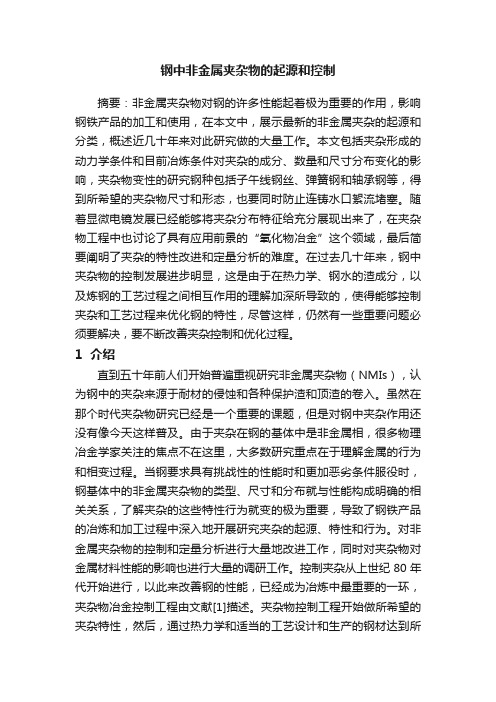
钢中非金属夹杂物的起源和控制摘要:非金属夹杂物对钢的许多性能起着极为重要的作用,影响钢铁产品的加工和使用,在本文中,展示最新的非金属夹杂的起源和分类,概述近几十年来对此研究做的大量工作。
本文包括夹杂形成的动力学条件和目前冶炼条件对夹杂的成分、数量和尺寸分布变化的影响,夹杂物变性的研究钢种包括子午线钢丝、弹簧钢和轴承钢等,得到所希望的夹杂物尺寸和形态,也要同时防止连铸水口絮流堵塞。
随着显微电镜发展已经能够将夹杂分布特征给充分展现出来了,在夹杂物工程中也讨论了具有应用前景的“氧化物冶金”这个领域,最后简要阐明了夹杂的特性改进和定量分析的难度。
在过去几十年来,钢中夹杂物的控制发展进步明显,这是由于在热力学、钢水的渣成分,以及炼钢的工艺过程之间相互作用的理解加深所导致的,使得能够控制夹杂和工艺过程来优化钢的特性,尽管这样,仍然有一些重要问题必须要解决,要不断改善夹杂控制和优化过程。
1 介绍直到五十年前人们开始普遍重视研究非金属夹杂物(NMIs),认为钢中的夹杂来源于耐材的侵蚀和各种保护渣和顶渣的卷入。
虽然在那个时代夹杂物研究已经是一个重要的课题,但是对钢中夹杂作用还没有像今天这样普及。
由于夹杂在钢的基体中是非金属相,很多物理冶金学家关注的焦点不在这里,大多数研究重点在于理解金属的行为和相变过程。
当钢要求具有挑战性的性能时和更加恶劣条件服役时,钢基体中的非金属夹杂物的类型、尺寸和分布就与性能构成明确的相关关系,了解夹杂的这些特性行为就变的极为重要,导致了钢铁产品的冶炼和加工过程中深入地开展研究夹杂的起源、特性和行为。
对非金属夹杂物的控制和定量分析进行大量地改进工作,同时对夹杂物对金属材料性能的影响也进行大量的调研工作。
控制夹杂从上世纪80年代开始进行,以此来改善钢的性能,已经成为冶炼中最重要的一环,夹杂物冶金控制工程由文献[1]描述。
夹杂物控制工程开始做所希望的夹杂特性,然后,通过热力学和适当的工艺设计和生产的钢材达到所希望的夹杂占其主导地位。
- 1、下载文档前请自行甄别文档内容的完整性,平台不提供额外的编辑、内容补充、找答案等附加服务。
- 2、"仅部分预览"的文档,不可在线预览部分如存在完整性等问题,可反馈申请退款(可完整预览的文档不适用该条件!)。
- 3、如文档侵犯您的权益,请联系客服反馈,我们会尽快为您处理(人工客服工作时间:9:00-18:30)。
炼钢、铸锭过程中产生非金属夹杂物的原因
摘要:论述钢中非金属夹杂物对钢锭质圣的影响,分析了非金属夹杂物在冶炼和铸锭过程中产生的原因,提出了控制夹杂物产生的几点行之有效的措施。
关键词:非金属夹杂物冶炼浇注电弧炉精炼炉质,控制
非金属夹杂物,一般是指钢锭在冶炼和浇注过程中产生或混人的非金属相,都是一些金属元素(Fe、Mn、Al等)及51与非金属元素(0、S、N、P、C 等)结合而生成的氧化物和硫化物(如Feo、Si02、Mno、A12O3、MnS、MnC)等。
非金属夹杂物按来源分为内生夹杂物和外来夹杂物。
内生夹杂物是钢内部发生的反应产物或者因为温度降低而形成夹杂析出。
外来夹杂物是由炉料带人,耐火材料及炉渣混人的颗粒。
内生夹杂物可以以外来夹杂物为核心聚集到后者的颗粒上。
外来夹杂物也可能与钢液反应被还原。
钢中如果有非金属夹杂物的存在,即使在钢中含量极少(通常是小于万分之一)也会给钢的质量带来极为有害的影响。
从2002年1~7月份重点产品的投料统计情况看,锻钢支承辊共生产68支,经探伤发现其中2支因有密集夹杂物缺陷而报废,有4支因有夹杂物等缺陷造成锻造裂纹。
电站锻件钢共生产41支,经探伤发现其中4支有严重的条状缺陷,缺陷性质为夹杂物。
半钢辊钢共生产27支,其中14支因夹杂物造成不同程度的裂纹。
可见夹杂物对钢锭质量造成的经济损失是非常巨大的。
1 冶炼过程中产生非金属夹杂物的原因
造渣材料碱性电弧炉常用的造渣材料采用石灰、萤石。
石灰,主要成份为CaO,其含量不应小于85%,SiO2含量不大于2%,硫含量应小于0.15%。
石灰易吸收水分而变成粉末,所以,造渣时要使用刚烧好的、烧透的石灰,或对石灰进行预热后再使用,这样能防止石灰给钢液带人过多的水分,否则就会使钢液氢含量增加,影响钢的质量,严重时会使钢报废。
萤石,主要成份为CaF2,含量为85%、95%, SiO2含量约为6%。
石中若掺杂硫化物矿石,必须将这种萤石排除掉,否则会降低炉渣的脱硫能力,易造成硫化物(MnS)夹杂。
铁合金在冶炼时,如果使用烘烤时间短、烘烤温度低、甚至根本未经烘烤的铁合金材料,势必会增加外来夹杂物和气体带人钢液中的机会。
经过烘烤的铁合金上到炉台,在寒冷的冬季,露天摆放的铁合金会很快凉下来,将这些凉的铁合金
加人到炼钢包内,不可能很快熔化并且在钢液中分布均匀,它们得经过一段时间的熔化和搅拌的过程。
对于精炼炉来说,钢水在真空结束后,有时还要补加一些铁合金调整钢液元素含量,如果没在工艺规定的时间内出钢,势必影响真空除气、去杂质的效果,又增加了外来夹杂物进人钢液中的机会,影响钢水质量。
精炼炉真空操作精炼炉冶炼的大都是重点钢种,精炼炉的真空操作起到了画龙点睛之功效。
钢水经真空处理是为了脱氢、脱氧和排除非金属夹杂物。
精炼炉冶炼的钢水是由电弧炉提供的初炼钢水,有些初炼钢水在初炼过程中没有一定的脱碳量,脱碳速度也达不到要求,这样就造成钢液去气速度小于吸气速度,不利于排出钢中气体和使夹杂物充分上浮。
把这种劣质钢水兑人精炼炉,全都依靠精炼真空处理去除夹杂物,不可能达到最佳的效果。
真空脱氧过程中钢水、熔渣激烈沸腾使钢包内衬的耐火材料受到强烈冲刷,耐火材料的熔融混人产生的夹杂物如果不能充分上浮便进人钢液,因此对精炼包内衬的耐火材料应该进行严格的控制。
氮气氢气是一种惰性气体,在钢液中不发生化学反应和变化。
炼钢时,将氢气通过精炼包底部的多孔透气砖不断吹人熔池中,氢气形成大量的小气泡,对于钢水中的有害气体如氢、氧、氮来说,相当一个“真空室”,这个小“真空室”内其它气体的分压几乎等于零。
于是溶解在钢液中的气体不断地向氨气泡中扩散,氢和氮在氢气泡中的分压力随着气泡上浮而增加,气泡在钢液中上浮时受热膨胀,因而氢和氮的分压力仍能保持较低的水平,所以继续吸收氢和氮,最后随氢气泡上浮溢出钢液而被去除。
氢气上浮时引起钢液搅动,提供了夹杂颗粒碰撞的机会,故烤时间要在4h以上。
有利于夹杂的排除。
可见,炼钢过程中,如果未调整好合适的气体参数(氢气压力、流量、气泡大小等),势必影响精炼的效果,增加产生非金属夹杂物的趋势。
2 铸锭过程中产生非金属夹杂物的原因
中间包的包衬和包底如果清洁不合格,有残钢、残渣将直接造成外来夹杂物的进人。
底盘、导流管、中间包盖板:在铸锭准备工作中,底盘、导流管的清洁工作最易被忽视,它们表面的铁锈及残钢、残渣也是带人外来夹杂物的直接因素。
中间包盖板使用前必须吹扫干净,否则在真空浇注时,盖板上覆盖物有可能落人
中间包丙,直接生成外来夹杂物,严重影响钢水质量。
3 降低非金属夹杂物的途径
提高原材料纯洁度对原材料必须加强管理,分类保存,达到清洁干燥的要求,冶炼电站钢、热壁加氢反应器钢、军工、核电产品等重点钢种时要求废钢、生铁和铁合金清洁无锈,铁合金要烤红、烤透。
对石灰、萤石、矿石等所含杂质要严格限制,冶炼重点钢种最好使用活性石灰以利于起到脱磷去除杂质的作用。
加强氧化操作,加强真空操作不进行真空精炼的钢种,冶炼时要加强氧化操作,保证一定的脱碳量和脱碳速度,造成一个良好沸腾的熔池,有利于夹杂物上浮及排除。
精炼炉真空操作时,真空度一定要达到工艺规定的要求,保证真空时间,提高真空效果。
精炼包、中间包包底不准砸砂子,包底、包衬不准换砖,必须清除残钢、残渣,烤红使用。
包要使用过一次或一次以上方可,以减少MgO外来夹杂。
钢锭模、底盘、导流管使用前必须清除内表面的残钢、残渣,打磨掉铁锈。
新模烘烤温度要高于120℃,烘时间在4h以上。
提高浇注系统的内在质量为减少耐火材料颗粒夹杂,应选用热稳定性强,耐火度高于其使用温度的耐火材料,以保证浇注系统清洁干燥,保证钢锭质量。
保持正常浇注浇注温度和浇注速度的良好配合能使钢液在浇注系统中处于正常的流动状态,从而减少了空气的卷人与钢液的裸露(除真空浇注外),也减轻了钢液对砖的冲刷,对降低夹杂十分有利。
执行吹氢工艺氨气的压力、流量、气泡大小直接影响精炼的效果。
应在保持较低压力下,尽量加大氢气的流量,特别是真空后出钢前,将氢气流量调到80l/min。
氢气泡的大小由透气砖的气孔尺寸决定,孔隙直径为0.1~0.26mm较好。
加强钢液的脱氧、脱硫操作对脱氧剂的种类、用量及加入方法要严格执行操作工艺。
冶炼重点钢种,应选用含硫低的炉料,控制好炉渣的碱度R,R=2.5~3.5时脱硫效果最好,减少硫所造成的夹杂。
4 结语
要提高钢水的质量,最大限度地减少非金属夹杂物对钢水质量的影响,必须控制好非金属夹杂物的两个来源,即内生夹杂物和外来夹杂物。
在实际生产中要加强冶炼准备、钢水熔炼、浇注等过程的质量控制,正确认识非金属夹杂物产生
的原因,采取有效的控制措施,严肃工艺纪律,提高操作者的技能和责任心。
质检人员严格把关,密切配合生产,一定会提高产品质量。