钢中夹杂物分析方法探讨
钢中非金属夹杂物分析可行性研究报告
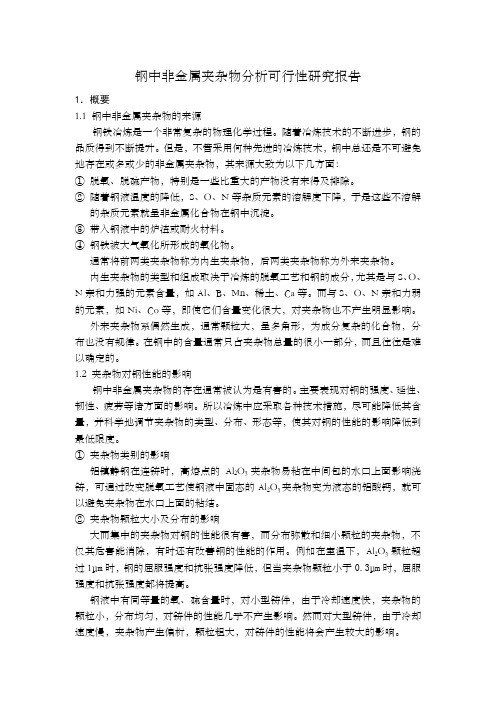
钢中非金属夹杂物分析可行性研究报告1.概要1.1 钢中非金属夹杂物的来源钢铁冶炼是一个非常复杂的物理化学过程。
随着冶炼技术的不断进步,钢的品质得到不断提升。
但是,不管采用何种先进的冶炼技术,钢中总还是不可避免地存在或多或少的非金属夹杂物,其来源大致为以下几方面:① 脱氧、脱硫产物,特别是一些比重大的产物没有来得及排除。
② 随着钢液温度的降低,S 、O 、N 等杂质元素的溶解度下降,于是这些不溶解的杂质元素就呈非金属化合物在钢中沉淀。
③ 带入钢液中的炉渣或耐火材料。
④ 钢铁被大气氧化所形成的氧化物。
通常将前两类夹杂物称为内生夹杂物,后两类夹杂物称为外来夹杂物。
内生夹杂物的类型和组成取决于冶炼的脱氧工艺和钢的成分,尤其是与S 、O 、N 亲和力强的元素含量,如Al 、B 、Mn 、稀土、Ca 等。
而与S 、O 、N 亲和力弱的元素,如Ni 、Co 等,即使它们含量变化很大,对夹杂物也不产生明显影响。
外来夹杂物系偶然生成,通常颗粒大,呈多角形,为成分复杂的化合物,分布也没有规律。
在钢中的含量通常只占夹杂物总量的很小一部分,而且往往是难以确定的。
1.2 夹杂物对钢性能的影响钢中非金属夹杂物的存在通常被认为是有害的。
主要表现对钢的强度、延性、韧性、疲劳等诸方面的影响。
所以冶炼中应采取各种技术措施,尽可能降低其含量,并科学地调节夹杂物的类型、分布、形态等,使其对钢的性能的影响降低到最低限度。
① 夹杂物类别的影响铝镇静钢在连铸时,高熔点的Al 2O 3夹杂物易粘在中间包的水口上面影响浇铸,可通过改变脱氧工艺使钢液中固态的Al 2O 3夹杂物变为液态的铝酸钙,就可以避免夹杂物在水口上面的粘结。
② 夹杂物颗粒大小及分布的影响大而集中的夹杂物对钢的性能很有害,而分布弥散和细小颗粒的夹杂物,不仅其危害能消除,有时还有改善钢的性能的作用。
例如在室温下,Al 2O 3颗粒超过1μm 时,钢的屈服强度和抗张强度降低,但当夹杂物颗粒小于0.3μm 时,屈服强度和抗张强度都将提高。
钢中非金属夹杂实验报告

实验报告姓名:班级:冶金1401班学号: 20142019实验名称:钢中非金属夹杂物观察与分析实验实验日期: 2017.11.7实验:钢中非金属夹杂物观察与分析实验一、实验目的1.掌握钢的磨制方法。
2.了解球磨机的使用方法。
3.了解金相显微镜的原理及使用。
4.对钢中的非金属夹杂物进行分析。
二、实验原理。
A钢中夹杂物的分类分类方法很多,但常见的有以下四种:1.按来源分类,可分为两类:(1)外来夹杂物:耐火材料、熔渣或两者的反应产物混入钢中并残留在钢中的颗粒夹杂称为外来夹杂。
包括从炉衬或包衬、或从汤道砖、中包绝热板、保护渣进入钢水中的夹杂物(有人还将钢水二次氧化生成的夹杂物包括在内)。
这类夹杂颗粒较大,易于上浮,但在钢中,它们的出现带着偶然性且不规则。
(2)内生夹杂物:在冶炼、浇注和凝固过程中,钢液、固体钢内进行着各种化学反应,对于在冶炼过程中所形成的化合物、脱氧时产生的脱氧产物、或在钢水凝固过程产生的化合物,当这些化合物来不及从钢水中彻底排出而残存在钢中者,叫做内在的非金属夹杂物。
内生夹杂物形成的时间可分为四个阶段:①一次夹杂(原生夹杂):钢液脱氧反应时生成的脱氧产物;②二次夹杂:在出钢和浇注过程中温度下降平衡移动时生成的夹杂物;③三次夹杂(再生夹杂):凝固过程中生成的夹杂;④四次夹杂:固态相变时因溶解度变化生成的夹杂。
一般说来外来夹杂物颗粒较大,在钢中比较集中,而内生夹杂物则与此相反。
从组成来看,内生夹杂物可以是简单组成,也可以是复杂组成;可以是单相的,也可以是多相的。
在铸坯凝固以及随后的冷却过程中,夹杂物不仅与钢基体保持平衡,而且夹杂物本身也不断发生改变,例如析出新的化合物以趋于稳定状态。
在轧制或热处理时,每次加热都为夹杂物和钢基体之间趋向平衡提供了条件,在室温下所观察到的夹杂物,实际上是经过了一系列复杂变化的结果。
2.按化学成分分类,一般分三类。
(1)氧化物:如FeO, Si02 , Al2O3等,有时它们各自独立存在,有时形成尖晶石(如MnO.Al203)或固溶体 (如FeO 和MnO)。
钢中细小夹杂物的研究方法探讨
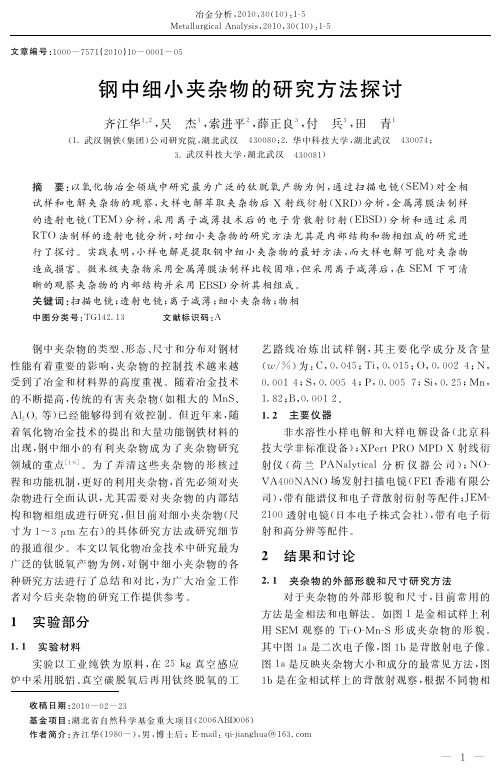
形态 & 尺寸和分布对钢材 !! 钢中夹杂物的类型 & 夹杂物的控制技术越来越 性能有着重要的 影 响 ! 受到了冶金和材料界的高度重视 ' 随着冶金技术 传统的有害夹 杂 物 " 如粗大的 ' 的不断提高 ! 2 :& 已经能够得到有效控制 ' 但 近年来 ! 随 1 + !A $ 等# 着氧化物冶金技术的提出和大量功能钢铁材料的 钢中细小的 有 利 夹 杂 物 成 为 了 夹 杂 物 研 究 出现 ! 领域的重点
' 通过
图 #! 非水溶液小样电解萃取的各种夹杂物外部形貌 ' ( " #!* + ,/ . : + . 4 . 6 ( 2 4 1 5 ( . 2< + : . 1 +5 / = 4 4 5 = / 4 ,, 4 , < : . 4 ? = < ( . 2. 62 . 2 7 = 1 , . 1 5 5 . 4 1 < ( . 2 ) 0 ) >. ) 0 > @
'了弄清这些夹杂物的形核过
程和功能机制 ! 更好的利用夹杂物 ! 首先必须对夹 尤其需要对夹杂物的内部结 杂物进行全面认 识 ! 构和物相组成进行研究 ! 但目前对细小夹杂物 " 尺 寸为 #"$# 的具体研究方法或研究细节 E 左右 # 的报道很少 ' 本文以氧化物冶金技术中研究最为 广泛的钛脱氧产 物 为 例 ! 对钢中细小夹杂物的各 种研究方法进行 了 总 结 和 对 比 ! 为广大冶金工作 者对今后夹杂物的研究工作提供参考 '
# " #! 夹杂物的内部结构和物相研究方法 # " # " !! 夹杂物 A B C 分析 ! 常用的 ! 种物相研究 方法是 < 衍 射 和 透 射 电 镜 下 的 选 区 电 子 衍 射 " ' 对于 钢 中 夹 杂 物 尤 其 是 细 小 夹 杂 物 来 : 1 ># 说! 要提取足 够 < 衍 射 分 析 的 样 品 ! 采用小样电 解的方法萃取十分困难 ' 本文尝试了通过大样电 置于光滑 解的方法提取了 钛 脱 氧 钢 中 的 夹 杂 物 ! 的玻璃片上 ! 采 用 < 微 区 衍 射 进 行 分 析! 结果如 图$ 所 示'研 究 结 果 表 明! 钛脱氧钢中生成产物 为? / A !' + ! +
钢中夹杂物的产生与去除途径
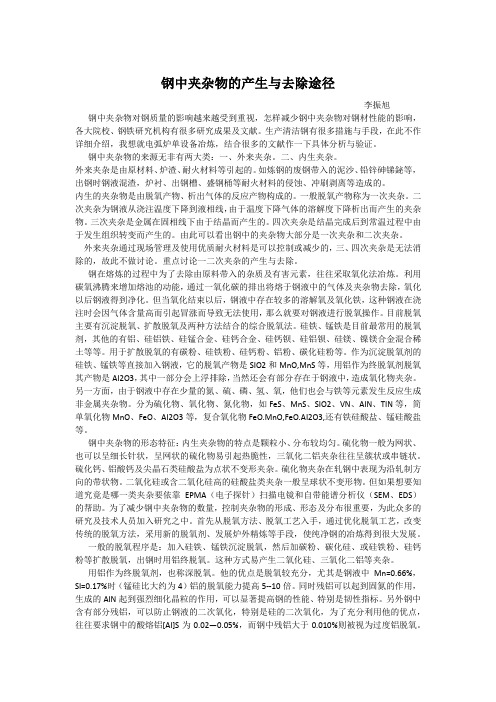
钢中夹杂物的产生与去除途径李振旭钢中夹杂物对钢质量的影响越来越受到重视,怎样减少钢中夹杂物对钢材性能的影响,各大院校、钢铁研究机构有很多研究成果及文献。
生产清洁钢有很多措施与手段,在此不作详细介绍,我想就电弧炉单设备冶炼,结合很多的文献作一下具体分析与验证。
钢中夹杂物的来源无非有两大类:一、外来夹杂。
二、内生夹杂。
外来夹杂是由原材料、炉渣、耐火材料等引起的。
如炼钢的废钢带入的泥沙、铅锌砷锑鉍等,出钢时钢液混渣,炉衬、出钢槽、盛钢桶等耐火材料的侵蚀、冲刷剥离等造成的。
内生的夹杂物是由脱氧产物、析出气体的反应产物构成的。
一般脱氧产物称为一次夹杂。
二次夹杂为钢液从浇注温度下降到液相线,由于温度下降气体的溶解度下降析出而产生的夹杂物。
三次夹杂是金属在固相线下由于结晶而产生的。
四次夹杂是结晶完成后到常温过程中由于发生组织转变而产生的。
由此可以看出钢中的夹杂物大部分是一次夹杂和二次夹杂。
外来夹杂通过现场管理及使用优质耐火材料是可以控制或减少的,三、四次夹杂是无法消除的,故此不做讨论。
重点讨论一二次夹杂的产生与去除。
钢在熔炼的过程中为了去除由原料带入的杂质及有害元素,往往采取氧化法冶炼。
利用碳氧沸腾来增加熔池的动能,通过一氧化碳的排出将熔于钢液中的气体及夹杂物去除,氧化以后钢液得到净化。
但当氧化结束以后,钢液中存在较多的溶解氧及氧化铁,这种钢液在浇注时会因气体含量高而引起冒涨而导致无法使用,那么就要对钢液进行脱氧操作。
目前脱氧主要有沉淀脱氧、扩散脱氧及两种方法结合的综合脱氧法。
硅铁、锰铁是目前最常用的脱氧剂,其他的有铝、硅铝铁、硅锰合金、硅钙合金、硅钙钡、硅铝钡、硅镁、镍镁合金混合稀土等等。
用于扩散脱氧的有碳粉、硅铁粉、硅钙粉、铝粉、碳化硅粉等。
作为沉淀脱氧剂的硅铁、锰铁等直接加入钢液,它的脱氧产物是SIO2和MnO,MnS等,用铝作为终脱氧剂脱氧其产物是AI2O3,其中一部分会上浮排除,当然还会有部分存在于钢液中,造成氧化物夹杂。
高铁车轮钢中TiN夹杂物析出的热力学分析
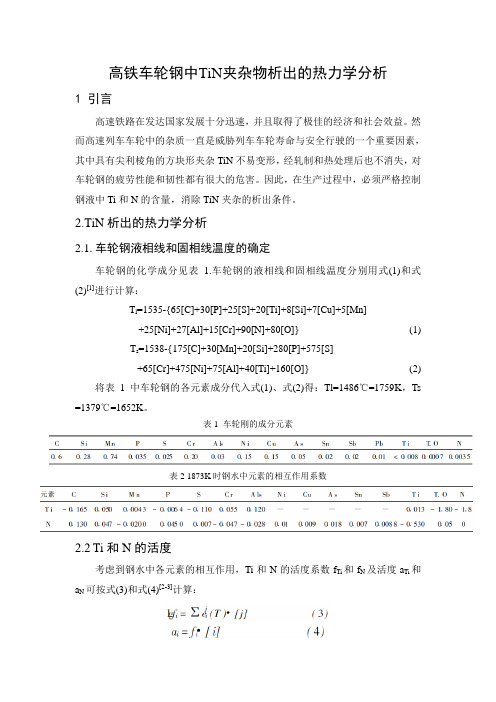
高铁车轮钢中TiN夹杂物析出的热力学分析1 引言高速铁路在发达国家发展十分迅速,并且取得了极佳的经济和社会效益。
然而高速列车车轮中的杂质一直是威胁列车车轮寿命与安全行驶的一个重要因素,其中具有尖利棱角的方块形夹杂TiN不易变形,经轧制和热处理后也不消失,对车轮钢的疲劳性能和韧性都有很大的危害。
因此,在生产过程中,必须严格控制钢液中Ti和N的含量,消除TiN夹杂的析出条件。
2.TiN析出的热力学分析2.1.车轮钢液相线和固相线温度的确定车轮钢的化学成分见表 1.车轮钢的液相线和固相线温度分别用式(1)和式(2)[1]进行计算:T l=1535-{65[C]+30[P]+25[S]+20[Ti]+8[Si]+7[Cu]+5[Mn]+25[Ni]+27[Al]+15[Cr]+90[N]+80[O]} (1)T s=1538-{175[C]+30[Mn]+20[Si]+280[P]+575[S]+65[Cr]+475[Ni]+75[Al]+40[Ti]+160[O]} (2) 将表1中车轮钢的各元素成分代入式(1)、式(2)得:Tl=1486℃=1759K,Ts =1379℃=1652K。
表1 车轮刚的成分元素表2 1873K时钢水中元素的相互作用系数2.2Ti和N的活度考虑到钢水中各元素的相互作用,Ti和N的活度系数f Ti和f N及活度a Ti和a N可按式(3)和式(4)[2-3]计算:式中,f i为元素i的亨利活度系数,e i j(T)为温度为T的钢液中元素j对i的相互作用系数,[i]为钢液中Ti或N的质量分数,[j]为钢液中溶质元素j的质量分数。
将车轮钢中各元素的质量分数(表1)和1873K时钢水中元素的相互作用系数[4-5](表2)代入式(3)计算得到下式:在本文讨论的车轮钢成分条件下,可得到1873K时钢液中Ti、N的活度如下:2.3车轮钢中TiN夹杂析出分析从文献[6]可查到:根据式(9)-(11)可导出[Ti]+[N]=TiN(s),△G=-314250+115.02T (12) 实际车轮钢中TiN 的生成反应吉布斯自由能的变化为G=G+RTlnJ,其中,J=aTiN/(aTiaN)。
钢中非金属夹杂物及其检测法

钢中非金属夹杂物及其检测法夹杂物的评级问题:不计较其组成成分和性能以及它们可能的来源等;只注意它们的数量、形状、大小和分布情况。
一般在明视场下放大100倍时检验即可。
现在采用的方法有:瑞典Jernkontoret(简称JK)夹杂物评级图。
美国试验及材料学会(ASTM)夹杂物评级标准亦采用JK评级图。
此外还有SAE(美国汽车工程师学会)夹杂物评级图等等。
中国冶金部YB25-59规定,夹杂物的评级有甲乙两种方法。
即:长度指数和与标准级别图对比评级法。
非金属夹杂的鉴定:(一)金相法:借助金相显微镜的明场、暗场及偏振光来观察夹杂物的形状、分布、色彩及各种特征,从而对夹杂物作出定性或半定性的结论。
但金相法不能获得夹杂物的晶体结构及精确成分的数据。
1.夹杂物的形状:鉴定夹杂物首先注意的是它们的形状,从它们的形状特点上,有时可以估计出它们属于那类夹杂物,这有利于考虑下一步应采取的鉴定方法。
如:玻璃质SiO2呈球形;TiN一般呈淡黄色的四方形。
在铸态时呈球形的夹杂物很多,但这些夹杂物有的具有一定的塑性,当钢在锻轧后,它们被压延拉长,如FeO 和2FeOSiO2共晶夹杂物,铸态时为球状,锻轧后被拉成长条状。
2.夹杂物分布:夹杂物的分布情况也有一定的特点,有的夹杂物成群,有的分散。
成群的夹杂物经锻轧后,即沿锻轧方向连续成串,Al2O3夹杂就属此类。
有的夹杂物,如FeS 及FeS-FeO共晶夹杂物等。
因其熔点低,所以钢凝固时,这类夹杂物多沿晶界分布。
3.夹杂物的色彩和透明度:观察夹杂物的色彩及透明度一般应在暗场或偏振光下进行。
可分为透明和不透明两大类。
透明的还可分为透明和半透明两种。
透明的夹杂物在暗场下显得十分明亮。
如果夹杂物是透明的并有色彩,则在暗场下将呈现它们的固有色彩。
各种夹杂物都有其固有的色彩和透明度,再结合其它特征来进行判断。
如某种夹杂物,它们的分布及外形呈有棱的细小颗粒并沿轧制方向连续成群,在明场下这些夹杂物多呈深灰略带紫色,而在暗场下则为透明发亮的黄色。
20g钢中夹杂物研究精品

【关键字】质量、问题、充分、整体、制定、研究、措施、规律、关键、稳定、理想、能力、结构、水平、检验、分析、形成、保护、满足、严格、开展、优先、发挥、解决、优化、调整、改善、加强、实现、提高、显著改善、实施、改进20g钢中夹杂物研究闫卫兵1,2,杨海平2,任毅1,2(1.北京科技大学冶金学院,北京100083; 2.河北钢铁集团宣钢公司炼钢厂,河北宣化075100)摘要:20g钢在轧制过程中易发生表面纵裂,对钢水中氧、氮含量和纯净度要求严格。
研究了宣钢炼钢厂生产20g钢过程中各工序钢中全氧及氮含量的变化,夹杂物的种类及粒度分布,大型夹杂物的组成、分布及其来源。
介绍了非稳态浇铸对铸坯洁净度的影响,使用示踪剂追踪了夹杂物的来源,并制定了改进措施,20g钢铸坯质量得到显著改善。
关键词:20g钢;夹杂物;研究1 前言宣钢炼钢厂生产20g钢工艺流程为:120 t顶底复吹转炉→130t LF精炼→连铸。
选取了20g钢1个中包浇次的中间包前2炉取样。
在钢包和中间包钢液中取氧氮样、电解样,在连铸浇铸过程中切取铸坯样,取样前在钢包渣、中间包覆盖剂加入示踪元素,并利用结晶器保护渣中固有的示踪剂K和Na跟踪钢包渣、中间包覆盖剂、结晶器对钢液的污染。
根据铸坯样中夹杂物的示踪剂判定夹杂物的来源,对铸坯样进行夹杂物的检验,分析其夹杂物的种类、数量、形态、分布。
2 各工序钢中全氧及氮含量的变化钢中的氧、氮含量主要与转炉冶炼、炉外精炼及保护浇铸有关。
因此,分别在钢包、中间包及铸坯取样,精炼过程钢中平均T[O]和[N]的变化规律如图1所示,浇铸过程中间包钢液中平均T[O]和[N]的变化规律如图2所示,铸坯中平均T[O]和[N]的变化规律如图3所示。
由图1可知,20g 钢在精炼过程中的氧、氮含量变化为:在LF精炼过程中吹氩搅拌,钢液面波动较大,极易发生二次氧化,致使钢中氧氮含量升高;LF精炼末期,钢水通过弱氩气底吹,使钢水中氧氮含量降低。
底吹转炉钢中夹杂物的检测与鉴定技术

底吹转炉钢中夹杂物的检测与鉴定技术钢材是现代工业生产中不可或缺的材料之一,而钢材的质量则直接关系到产品的使用性能和安全性。
底吹转炉钢作为常见的一种钢材类型,其质量也备受关注。
其中,钢中的夹杂物是常见的一个质量问题,在生产过程和使用过程中可能导致钢材的性能下降甚至产生事故。
因此,底吹转炉钢中夹杂物的检测与鉴定技术显得尤为重要。
夹杂物是指分散分布在钢锭和钢坯中的非金属夹杂,它们可以是气体、氧化物、硫化物、碳化物等。
夹杂物的存在会降低钢材的力学性能、加工性能和耐蚀性能,同时也会增加钢材的断裂风险。
因此,及时准确地检测和鉴定钢中的夹杂物,对于生产和应用安全至关重要。
底吹转炉钢中夹杂物的检测与鉴定技术涉及多个方面,以下是一些常见的技术方法和手段:1. 金相显微镜分析:使用金相显微镜对钢材进行观察和分析,能够直观地观察到夹杂物的形态、大小、分布等特征。
这种方法适用于较大夹杂物的检测和鉴定,但对于微小夹杂物的检测有一定局限性。
2. 扫描电子显微镜(SEM):SEM是一种高分辨率的显微镜,能够观察到微小夹杂物的形态和结构,并通过能谱分析技术确定其成分。
这种方法具有较高的检测灵敏度和分辨率,可准确检测到微小夹杂物。
3. 超声波检测:利用超声波传播的原理,对钢材进行扫描和检测,可以检测到夹杂物的存在和位置。
此外,超声波技术还可以评估夹杂物对钢材性能的影响程度,并预测其可能导致的破坏性行为。
4. 磁粉检测:利用磁粉法对钢材进行检测,通过观察磁粉的聚集和颜色变化等来确定夹杂物的位置和形态。
这种方法通常适用于表面的夹杂物检测,对于内部夹杂物的检测能力有一定限制。
5. 色谱分析:通过色谱技术对钢材中的夹杂物进行分离和分析,可以确定其组分和含量。
这种方法对于一些特定的夹杂物鉴定非常有效,但需要配合专业的分析仪器和技术人员进行操作。
在采用这些技术方法的同时,还需要建立一套完善的检测体系和标准,确保检测结果的准确性和可比性。
此外,在实际生产中,也需要对原材料、生产工艺和设备等方面进行控制,减少夹杂物的产生和污染。
- 1、下载文档前请自行甄别文档内容的完整性,平台不提供额外的编辑、内容补充、找答案等附加服务。
- 2、"仅部分预览"的文档,不可在线预览部分如存在完整性等问题,可反馈申请退款(可完整预览的文档不适用该条件!)。
- 3、如文档侵犯您的权益,请联系客服反馈,我们会尽快为您处理(人工客服工作时间:9:00-18:30)。
钢中夹杂物分析方法探讨
钢中夹杂物主要以非金属化合态存在,如氧化物、硫化物、氮化物等,造成钢的组织不均匀。
夹杂物的几何形状、化学成分、物理性能等不仅影响钢的冷热加工性能和理化性能,而且影响钢的力学性能和疲劳性能。
随着产品对夹杂物的分析提出更高的要求,需要建立适合生产现场的快速检测钢中夹杂的分析方法,以便降低钢中的夹杂含量,因此,对各种夹杂分析方法进行调研,并从单一和综合两方面进行分析。
单一方法
(1)金相显微镜观测法(MMO)。
金相显微镜观测法是一种传统的方法,用光学显微镜检测二维钢样薄片,并且用肉眼定量。
通过观察夹杂物的形状、光学特征或用化学法辅助,可以测定夹杂物类型,直接观测夹杂物的尺寸与分布情况,判断夹杂物的生成。
(2)图像扫描法(IA)。
采用高速计算机显微镜扫描图像,根据灰度的断续分辨明暗区,比肉眼观测的MMO法大有改进,容易测定较大面积和较多数量的夹杂物,自动化程度高,可获得体积分数、粒度分布直方图、定量等信息,但有时易将非金属夹杂物引起的划痕、麻点和凹坑分析错,且易受尘埃干扰,细小夹杂可能从磨面脱落。
(3)硫印法。
通过对富硫区进行腐蚀,区分宏观夹杂和裂纹。
(4)电解(蚀)法。
该方法精确度高但费时,以钢样作为电解池的阳极,电解槽为阴极,通电后钢的基体呈离子状态进入溶液溶解,非金属夹杂物不被电解呈固相保留。
较大的钢样(2~3kg)被电解,然后对电解泥淘洗、磁选、氢气还原分离铁,最后称量分级;较小的钢样(50~120g)被电解或稀酸溶解,将残渣经碳化物处理、过滤、灼烧,得到氧化物总量。
马钢钢研所和北京科技大学成人教育学院运用大样电解法对钢样进行测定,并得到夹杂物不同粒度分布的百分含量。
(5)电子束熔炼法(EB)。
在真空条件下,用电子束熔化钢样,夹杂物上浮到钢水表面。
通常电子束熔炼查找的是上浮夹杂物特定区域。
电子束熔炼的升级法(EB-EV)用来评估夹杂物尺寸分布,根据测定区域的上浮夹杂物尺寸,推断所有夹杂物的上浮结果,从而计算夹杂物尺寸分布指数。
(6)水冷坩埚熔炼法(CC)。
在电子束熔炼的条件下,先将熔融钢样表面的夹杂物浓缩,冷却后,样品被分解,夹杂物被分离出来。
(7)扫描电子显微镜法(SEM)。
将电子束用电磁透镜聚焦照射于试样表面,同时用电子束扫描,在显像管上显示出试样发出的信号,可清晰地观测到各种夹杂物的主体像,了解其分布和形态,用电子探针分析仪(EPMA)测定其组成及含量,特别是鉴定夹杂物局部组成最有效,可分析的元素范围4Be~92U,对0.1μm以上的区域进行定性分析,对2μm以上的区域进行定量分析。
(8)单火花光谱分析法(SSA)即原位分析仪。
对被分析对象原始状态的化学和结构进行分析。
通过对无预燃、连续扫描激发的火花放电所产生的光谱信号进行高速的数据采集和解析,测定样品表面不同位置的原始状态下的化学成分分布、缺陷判别和夹杂状态分析,可获得夹杂物数量、组成、分布和粒度等多方面的信息;一次扫描即可得到元素成分、偏析、疏松和夹杂的定量分布结果,扫描范围达300mm×200mm,分析灵敏度优于常规火花光谱分析,样品无需抛光及处理,分析结果显示方式丰富,除了以列表方式显示各项分析数据和计数外,还同时以二维和三维多种图形显示成分、偏析、疏松和夹杂的分析结果,可直接应用于冶金炉前分析,实现临线快速分析,当样品太少时不能反映大型夹杂。
(9)曼内斯曼夹杂物检测法(MIDAS)。
又名LSHP法,先使钢样波动,以排除气泡,然后超声扫描检测固态夹杂物和固气复合夹杂物。
(10)激光衍射颗粒尺寸分析法(LDPSA)。
采用激光技术检测其他方法(如定泥法)已检测出夹杂物的尺寸分布。
(11)常规的超声波法(CUS)。
可确定固态钢样内大于20μm的夹杂物尺寸分布。
(12)锥形样品扫描法。
用螺旋运动检测仪自动扫描连铸产品的圆锥形样品表面每个位置的夹杂物。
(13)分级热分解法(FTD)。
利用不同氧化物夹杂可以在不同温度还原,如氧化铝基氧化物还原温度为1400℃或1600℃,耐火材料夹杂物还原温度为1900℃,总氧含量为每个加热步骤测出的氧含量之和。
(14)激光显微探针质谱分析法(LAMMS)。
用脉冲激光束照射每个颗粒,选择电离临界值之上最低激光度作为其化学状态特征光谱图。
通过与标样比较,激光显微探针质谱分析的强度峰值与每个化学元素对应。
(15)X射线衍射法(XPD)。
采用X射线对夹杂中的未知物定性、定量,并对其结构进行测定。
(16)X射线光电子光谱法或X射线光电子能谱法(XPS)。
对被分析表面进行定性及定量元素分析,采用X射线检测尺寸大于10μm的夹杂物化学状态。
(17)俄歇电子光谱法(AES)。
采用电子束检测夹杂物化学状态,以电子束照射固体表面,分析借俄歇过程从固体表面放射出来的二次电子的动能,从而进行元素测定的方法。
最大特点是对微小区域或表面进行分析,得到合金元素的组成变化信息,如根据AES分析可以证实钢中夹杂物硫在加热温度达到500℃左右时就会从表面析出,但检测的灵敏度不太高,获得信息的深度浅(0.5~10μm)。
(18)光电扫描法。
分析用其他方法分离出来的夹杂物的光电扫描信号,以检测其尺寸分布。
(19)库尔特计数分析法。
与LIMCA法相似,可检测电蚀法分离出来的夹杂物尺寸分布。
(20)液态金属洁净度分析法(LIMCA)。
用传感器在线直接检测钢液中的夹杂物,由于穿过空隙进入传感器的夹杂物颗粒能改变空隙断面的电导率,检测电导率的变化便可检测夹杂物。
(21)钢水超声技术。
吸收超声脉冲反射信号,在线检测钢中夹杂物,在钢样的超声技术方面,高频超声波对于氧化物夹杂能产生很强烈的缺陷波反射,高频探伤仪可检测>30μm夹杂物的近似形状和尺寸。
(22)热差抽取(DTE)。
可快速给出几类氧化夹杂含量,适合探讨工艺过程对某类夹杂的影响,而对于无形态粒度信息,加热过程可导致夹杂物发生变化。
综合方法
(1)电解抽取+化学分析(EE+CA)。
无铁水预处理和炉外精炼设施的钢厂,也未采取全封闭浇铸,夹杂物含量高且大型夹杂(>50μm)比例大,需大量采样才能反映各类夹杂存在状况,用此方法测定总量,试样量约40~80g,分析时间5~6d。
优点是取样量大,对大小颗粒都有代表性,含量和组成分析精度较好;缺点是费时,要求试剂及环境纯度高,不稳定夹杂物被溶解而测不到。
(2)电解抽取+电镜/能谱(EE+SEM/EDS)。
对钢中复合夹杂物的形态、组成和分布等细节进行精细的研究。
试样量约50~250g,分析时间8~10d。
优点是取样量及信息量大,适合考察聚合或外来的大型夹杂;缺点是费时,不稳定夹杂物被破坏。
(1)、(2)两种方法中,由于电解抽取和化学分离(除去渗碳体)会损伤部分对酸性试剂不稳定的夹杂物,必要时须直接对钢样磨面作能谱分析,补充组成分析结果。
(3)抽取+激光衍射和散射(PSM)。
试样量约50~100g,分析时间2~3d,3~5min测定,粒度0.1~1000μm;缺点是抽取(电解或酸溶)及除去碳化物均费时且可能损失目的物。
(4)电子束重熔+电镜/能谱(ESR+SEM/EDS)。
当考察大型夹杂时,常需电解2~3kg钢样,并用淘洗法除去碳化物和小夹杂,EBR重熔可使夹杂上浮富集于钢样表面供分析综合信息。
(5)高频超声探测(HE-US)。
试样量由探测面与深度估计,分析时间3~4h。
不分解试样,联合SEM/EDS可作原位分析;缺点是仅能探测到30μm以下的颗粒。