粉末冶金在刀具上的应用
上千种粉末冶金材料化学成分

上千种粉末冶金材料化学成分
摘要:
一、粉末冶金材料概述
二、粉末冶金材料的分类
三、粉末冶金材料的应用领域
四、粉末冶金材料的发展趋势与前景
正文:
粉末冶金材料是一种以金属粉末或金属与非金属粉末的混合物为原料,通过成形和烧结等工艺制造的金属材料或复合材料。
粉末冶金材料因其独特的化学成分和物理、力学性能,在新材料的发展中起着举足轻重的作用。
粉末冶金材料可以分为以下几类:
1.粉末冶金结构材料:这类材料能承受拉伸、压缩、扭曲等载荷,具有良好的力学性能。
包括烧结结构材料、粉末冶金高速钢等。
2.粉末冶金工模具材料:包括硬质合金、粉末冶金高速钢等。
这类材料具有较高的硬度、韧性和耐磨性,可用于制造切削刀具、模具和零件的坯件。
3.多孔粉末冶金材料:这类材料具有孔隙度可控的特点,如多孔过滤材料、多孔含油轴承等。
4.粉末冶金磁性材料:如铁氧体磁性材料、永磁合金等。
这类材料具有较高的磁性能,广泛应用于磁性器件、磁力矫治等领域。
5.粉末冶金功能材料:如电催化材料、导电材料、热管理材料等。
这类材料具有独特的功能特性,可在电子、能源等产业中发挥重要作用。
粉末冶金材料广泛应用于航空航天、汽车、摩托车、家电、能源、电子、通讯、仪器仪表等领域。
随着科技的进步和产业的发展,粉末冶金材料在新能源、节能减排、环保等领域将发挥越来越重要的作用。
四大材料刀具的性能与选择
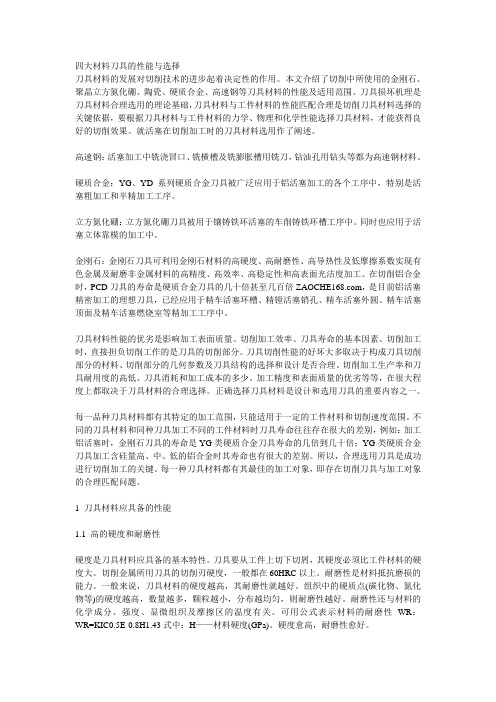
四大材料刀具的性能与选择刀具材料的发展对切削技术的进步起着决定性的作用。
本文介绍了切削中所使用的金刚石、聚晶立方氮化硼、陶瓷、硬质合金、高速钢等刀具材料的性能及适用范围。
刀具损坏机理是刀具材料合理选用的理论基础,刀具材料与工件材料的性能匹配合理是切削刀具材料选择的关键依据,要根据刀具材料与工件材料的力学、物理和化学性能选择刀具材料,才能获得良好的切削效果。
就活塞在切削加工时的刀具材料选用作了阐述。
高速钢:活塞加工中铣浇冒口、铣横槽及铣膨胀槽用铣刀,钻油孔用钻头等都为高速钢材料。
硬质合金:YG、YD系列硬质合金刀具被广泛应用于铝活塞加工的各个工序中,特别是活塞粗加工和半精加工工序。
立方氮化硼:立方氮化硼刀具被用于镶铸铁环活塞的车削铸铁环槽工序中。
同时也应用于活塞立体靠模的加工中。
金刚石:金刚石刀具可利用金刚石材料的高硬度、高耐磨性、高导热性及低摩擦系数实现有色金属及耐磨非金属材料的高精度、高效率、高稳定性和高表面光洁度加工。
在切削铝合金时,PCD刀具的寿命是硬质合金刀具的几十倍甚至几百倍,是目前铝活塞精密加工的理想刀具,已经应用于精车活塞环槽、精镗活塞销孔、精车活塞外圆、精车活塞顶面及精车活塞燃烧室等精加工工序中。
刀具材料性能的优劣是影响加工表面质量、切削加工效率、刀具寿命的基本因素。
切削加工时,直接担负切削工作的是刀具的切削部分。
刀具切削性能的好坏大多取决于构成刀具切削部分的材料、切削部分的几何参数及刀具结构的选择和设计是否合理。
切削加工生产率和刀具耐用度的高低、刀具消耗和加工成本的多少、加工精度和表面质量的优劣等等,在很大程度上都取决于刀具材料的合理选择。
正确选择刀具材料是设计和选用刀具的重要内容之一。
每一品种刀具材料都有其特定的加工范围,只能适用于一定的工件材料和切削速度范围。
不同的刀具材料和同种刀具加工不同的工件材料时刀具寿命往往存在很大的差别,例如:加工铝活塞时,金刚石刀具的寿命是YG类硬质合金刀具寿命的几倍到几十倍;YG类硬质合金刀具加工含硅量高、中、低的铝合金时其寿命也有很大的差别。
常用刀具材料分类特点及应用

常用刀具材料分类、特点及应用刀具材料的切削性能直接影响着生产效率、工件的加工精度、已加工表面质量和加工成本等,所以正确选择刀具材料是设计和选用刀具的重要内容之一。
1.刀具材料应具备的性能金属切削时,刀具切削部分直接和工件及切屑相接触,承受着很大的切削压力和冲击,并受到工件及切屑的剧烈摩擦,产生很高的切削温度,即刀具切削部分是在高温、高压及剧烈摩擦的恶劣条件下工作的。
因此,刀具切削部分材料应具备以下基本性能。
1.1 高的硬度和耐磨性硬度是刀具材料应具备的基本特性。
刀具要从工件上切下切屑,其硬度必须比工件材料的硬度大。
耐磨性是材料抵抗磨损的能力。
一般来说,刀具材料的硬度越高,耐磨性就越好。
组织中硬质点(碳化物、氮化物等)的硬度越高,数量越多,颗粒越小,分布越均匀,则耐磨性越高。
但刀具材料的耐磨性实际上不仅取决于它的硬度,而且也和它的化学成分、强度、纤维组织及摩擦区的温度有关。
1.2 足够的强度和韧性要使刀具在承受很大压力,以及在切削过程中通常要出现的冲击和振动的条件下工作,而不产生崩刃和折断,刀具材料就必须具有足够的强度和韧性。
1.3 高的耐热性耐热性是衡量刀具材料切削性能的主要标志。
它是指刀具材料在高温下保持硬度、耐磨性、强度和韧性的性能。
1.4 导热性好刀具材料的导热性越好,切削热越容易从切削区散走,有利于降低切削温度。
刀具材料的导热性用热导率表示。
热导率大,表示导热性好,切削时产生的热量就容易传散出去,从而降低切削部分的温度,减轻刀具磨损。
1.5 具有良好的工艺性和经济性既要求刀具材料本身的可切削性能、耐磨性能、热处理性能、焊接性能等要好,且又要资源丰富,价格低廉。
2.常用刀具材料分类、特点及应用刀具材料可分为工具钢、高速钢、硬质合金、陶瓷和超硬材料等五大类。
常用刀具材料的主要性能及用途见表2-1。
2.1 高速钢2.1.1 普通高速钢普通高速钢指用来加工一般工程材料的高速钢,常用的牌号有:(1)W18Cr4V(简称W18)。
陶瓷铣刀知识点归纳总结

陶瓷铣刀知识点归纳总结一、材料陶瓷铣刀采用氧化锆、氧化铝、碳化硅等陶瓷材料制成。
这些材料具有高硬度、耐磨损、耐高温等特点,能够有效提高刀具的耐磨性和加工精度。
1. 氧化锆陶瓷氧化锆陶瓷具有高硬度、高强度和耐磨损性能,适用于加工高硬度、高强度金属材料,如高速钢、硬质合金等。
氧化锆陶瓷铣刀具有较长的使用寿命和良好的加工精度。
2. 氧化铝陶瓷氧化铝陶瓷具有高硬度、耐腐蚀、耐磨损等特点,适用于加工铸铁、不锈钢、铝合金等金属材料。
氧化铝陶瓷铣刀具有良好的抗磨损性能和化学稳定性,适用于长时间加工。
3. 碳化硅陶瓷碳化硅陶瓷具有高硬度、耐高温、耐磨损等特点,适用于加工高温合金、钛合金等金属材料。
碳化硅陶瓷铣刀具有较高的切削速度和加工精度,适用于高速加工。
二、结构陶瓷铣刀的结构主要包括刃部和刀柄两部分。
刃部是用陶瓷材料制成的刀片,具有刀尖、刀身、刀脊等部分;刀柄则是用金属材料制成的刀柄,用于安装刀片和与加工设备连接。
1. 刀片陶瓷铣刀的刀片采用陶瓷材料制成,具有高硬度、耐磨损的特点。
刀片的刀尖采用超精密磨削工艺,保证刀尖的平整度和尺寸精度;刀片的刀身经过精密烧结工艺,保证刀片的整体性能和稳定性。
刀片的刀脊则采用特殊的设计,保证刀片的刚性和稳定性。
2. 刀柄陶瓷铣刀的刀柄采用金属材料制成,具有良好的机械性能和稳定性。
刀柄的设计考虑了切削力和加工稳定性,采用合理的结构,保证刀片的安全性和可靠性。
三、加工工艺陶瓷铣刀的制造工艺主要包括粉末冶金、成形工艺、烧结工艺、磨削工艺等。
通过这些工艺,可以保证刀具的整体性能和使用寿命。
1. 粉末冶金陶瓷铣刀的制造过程从粉末冶金开始,通过混合、压制等工艺,形成刀片和刀柄的原料。
2. 成形工艺陶瓷铣刀的刀片和刀柄经过成形工艺,通过模具成型、注射成型等工艺,形成刀具的初步形状。
3. 烧结工艺陶瓷铣刀的刀片和刀柄经过烧结工艺,通过高温烧结,形成致密的结构和良好的性能。
4. 磨削工艺陶瓷铣刀的刀片经过精密磨削工艺,通过超精密研磨、平面磨削等工艺,形成精确的刀尖和刀身。
粉末冶金高速钢刀具的特点及应用

粉末冶金高速钢刀具的特点及应用000内容摘要:近年来,随着粉末冶金高速钢(P/MI-ISS)刀具切削性能的提高,高速钢刀具的市场占有率有所回升。
与普通高速钢刀具相比,粉末冶金高速钢刀具硬度更高、韧性更好、更耐磨损,因此在某些应用领域(如高冲击性、大切除量的加工场合),粉末冶金高速钢刀具有逐渐取代脆性较大、在切削冲击下易发生碎裂的整体硬质合金刀具的趋势。
近年来,随着粉末冶金高速钢(P/MI-ISS)刀具切削性能的提高,高速钢刀具的市场占有率有所回升。
与普通高速钢刀具相比,粉末冶金高速钢刀具硬度更高、韧性更好、更耐磨损,因此在某些应用领域(如高冲击性、大切除量的加工场合),粉末冶金高速钢刀具有逐渐取代脆性较大、在切削冲击下易发生碎裂的整体硬质合金刀具的趋势。
粉末冶金高速钢制造工艺于20世纪60年代后期在瑞典开发成功,并于70年代初期进入市场。
该工艺可在高速钢中加入较多合金元素而不会损害材料的强韧性或易磨性,从而可制成具有高硬度、高耐磨性、可吸收切削冲击、适合高切除率加工和断续切削加工的刀具。
高速钢刀具材料主要由两种基本成分构成:一种是金属碳化物(碳化钨、碳化钼或碳化钒),它赋予刀具较好的耐磨性;二是分布在周围的钢基体,它使刀具具有较好的韧性和吸收冲击、防止碎裂的能力。
制备普通高速钢时,是将熔化的钢水从钢水包中注入铸模,使其缓慢冷却凝固。
此时,金属碳化物从溶液中析出,并形成较大的团块。
高速钢中添加的合金含量越多,碳化图I粉末冶金高速钢中的碳化物尺寸与碳化物含量无关;普通高速钢中的碳化物尺寸随碳化物含量的增加而急剧增大物团块就越大。
达到某一临界点时,可形成尺寸极大的碳化物团块(直径可达40mm)。
出现大的碳化物团块的临界点根据钢锭的尺寸以及其它因素而略有不同,但一般是在碳化钒含量达到约4%时发生。
通过对钢锭进行锻造、轧制等后续加工,可以粉碎其中一部分碳化物团块,但不可能将其完全消除。
虽然增加钢材中金属碳化物颗粒的数量可以改善材料的耐磨性,但随着合金含量的增加,碳化物的尺寸及团块数量也会随之增加,这对于钢材的韧性会产生极其不利的影响,因为大的碳化物团快可能成为产生裂纹的起始点。
粉末冶金材料的应用
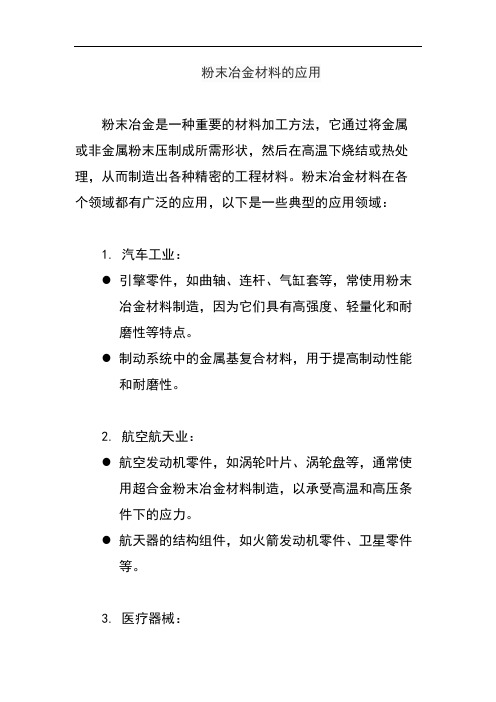
粉末冶金材料的应用粉末冶金是一种重要的材料加工方法,它通过将金属或非金属粉末压制成所需形状,然后在高温下烧结或热处理,从而制造出各种精密的工程材料。
粉末冶金材料在各个领域都有广泛的应用,以下是一些典型的应用领域:1. 汽车工业:●引擎零件,如曲轴、连杆、气缸套等,常使用粉末冶金材料制造,因为它们具有高强度、轻量化和耐磨性等特点。
●制动系统中的金属基复合材料,用于提高制动性能和耐磨性。
2. 航空航天业:●航空发动机零件,如涡轮叶片、涡轮盘等,通常使用超合金粉末冶金材料制造,以承受高温和高压条件下的应力。
●航天器的结构组件,如火箭发动机零件、卫星零件等。
3. 医疗器械:●人工关节、牙科植入物和医用工具等医疗器械中,粉末冶金材料常用于制造耐腐蚀、生物相容性好的部件。
4. 电子和电气工程:●电子电路板上的金属化连接器、封装材料和导电粘合剂中常使用粉末冶金材料。
●用于磁性元件、电感器和传感器的软磁材料,如铁氧体粉末。
5. 工具和刀具:●刀片、铣刀、钻头、齿轮和锯片等切削工具常使用粉末冶金材料制造,因为它们具有高硬度、耐磨性和耐热性。
●硬质合金(碳化钨等)用于制造切削刀具。
6. 磁性材料:●用于电机、变压器、传感器和磁盘驱动器的永磁体材料。
●电感线圈和电子元件的软磁材料。
7. 能源产业:●用于太阳能电池和燃料电池的材料。
●用于储能系统中的电池材料。
总的来说,粉末冶金材料在制造业中发挥着重要作用,因为它们具有高度可控性、高精度和多种定制化特性,可以满足各种应用的要求。
由于粉末冶金材料的广泛适用性和优越性能,它们在现代工程和科学领域中扮演着不可或缺的角色。
铣削粉末冶金高温合金的刀具优选试验

Q A a g I ig L U Z a qa g Z A u I O Y n ,A n , I h n i , H O Jn X n ( e a oa r o H g fc nya dCenMeh ncl n f tr , ns yo E u a o , K yL brt y f ihE i c n la c aia Ma ua ue Mii r f d ct n o i e c t i D p r n f c a i l n ier g S a d n n es y J a 5 0 ,C N) e at t h n a E gnei , h n o gU i r t, i n2 0 6 me o Me c n v i n 1 H
目前 系统 研究 粉末 冶金 高 温合 金不 同加 工条件 和
2 杨 有 君 . 控 技 术 [ . 京 : 械 工 业 出版 社 ,0 5 数 M] 北 机 20 .
3 洪如瑾. X5设_‘ UGN i 基础 培训教 程 [ . f M] 北京 : 清华 大学 出版社 ,
c r i e g a e wa ee t d.Opt lb a d a d g o ti a a tr fi e twe e s l ce h o g o — a b d r d ss l ce i r n n e merc p r me e so ma ns r r ee t d t r u h c n
ta te pe i n ft o a e it n ea d to i r s x rme to lwe rr ssa c n o ll e. I i h wn t a h o td c r i e i h o e o l o f t ss o h tt e c ae a b d st epr p rto ma e ilfr t e m il g o wde eal r y s p r lo tra o h li fpo n r m t l g u e al y, a d t e we r mo p o o y a d me h n s f u n h a r h lg n c a ims o c a e a b d o l r n e t ae o td c r i e t os a e iv si t d. g Ke ywo d r s:Po e ea l r u e aly; Opt a ee tng; Co t d wd rM tlu g S p r lo y i lS lci m ae Ca b d o ; Cu tn e f r n e; W e r r i e To l ti g P ro ma c a Me h n s c a m
车床常用的刀具材料及其用途
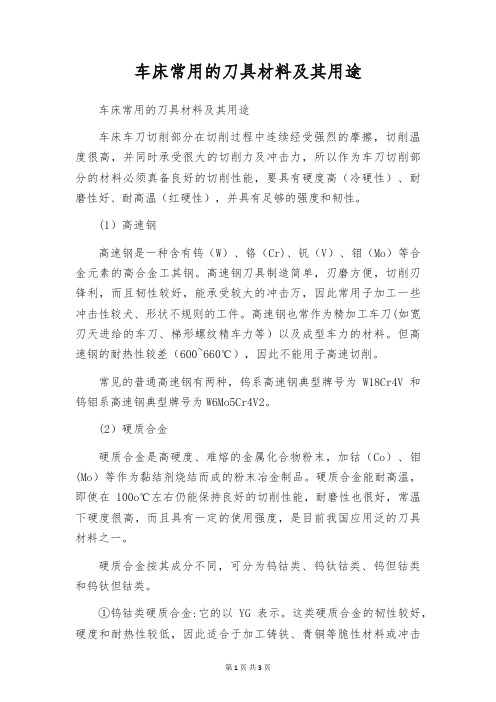
车床常用的刀具材料及其用途车床常用的刀具材料及其用途车床车刀切削部分在切削过程中连续经受强烈的摩擦,切削温度很高,并同时承受很大的切削力及冲击力,所以作为车刀切削部分的材料必须真备良好的切削性能,要具有硬度高(冷硬性)、耐磨性好、耐高温(红硬性),并具有足够的强度和韧性。
(1)高速钢高速钢是一种含有钨(W)、铬(Cr)、钒(V)、钼(Mo)等合金元素的高合金工其钢。
高速钢刀具制造简单,刃磨方便,切削刃锋利,而且韧性较好,能承受较大的冲击万,因此常用子加工一些冲击性较犬、形状不规则的工件。
高速钢也常作为精加工车刀(如宽刃天进给的车刀、梯形螺纹精车力等)以及成型车力的材料。
但高速钢的耐热性较差(600~660℃),因此不能用子高速切削。
常见的普通高速钢有两种,钨系高速钢典型牌号为W18Cr4V和钨钼系高速钢典型牌号为W6Mo5Cr4V2。
(2)硬质合金硬质合金是高硬度、难熔的金属化合物粉末,加钴(Co)、钼(Mo)等作为黏结剂烧结而成的粉末冶金制品。
硬质合金能耐高温,即使在100o℃左右仍能保持良好的切削性能,耐磨性也很好,常温下硬度很高,而且具有一定的使用强度,是目前我国应用泛的刀具材料之一。
硬质合金按其成分不同,可分为钨钴类、钨钛钴类、钨但钴类和钨钛但钴类。
①钨钴类硬质合金:它的以YG表示。
这类硬质合金的韧性较好,硬度和耐热性较低,因此适合于加工铸铁、青铜等脆性材料或冲击性较大的工件。
钨钴类硬质合金按不同的含钴量,分为YG3、YG6、YG8等多种牌号。
YG8适合于粗加工,YG6适谷子半精加工,YG3适合于精加工。
②钨钛钴类硬质合金:它的以YT表示。
这类硬质合金的耐磨性较好,能承受较高的切削温度,所以适合于加工碳钢、合金钢等塑性金属或其他韧性较大的塑性材料。
因为它性脆,不耐冲击,所以不宜加工脆性材料。
钨钛钴类硬质合金按不同的含碳化钛量,分为YT5、YT15、YT3o等几种牌号。
YT5适合子粗加工,YT15适合于半精加工和精加工,YT3o适合于精加工。
- 1、下载文档前请自行甄别文档内容的完整性,平台不提供额外的编辑、内容补充、找答案等附加服务。
- 2、"仅部分预览"的文档,不可在线预览部分如存在完整性等问题,可反馈申请退款(可完整预览的文档不适用该条件!)。
- 3、如文档侵犯您的权益,请联系客服反馈,我们会尽快为您处理(人工客服工作时间:9:00-18:30)。
粉末冶金在刀具上的应用性能优异的粉末冶金高速钢刀具随着汽车、航天、航空、军工、信息技术产业及机械制造业的迅速发展,现代的机械加工越来越追求“高精度、高效率、高可靠性和专业化”目标,这就需要工具行业提供高切削性能的刀具,为此开发用于制造刀具的优质材料更显得十分重要。
粉末冶金高速钢于20世纪60年代后期开始研制生产,并在70年代投入应用。
粉末冶金高速钢特殊而先进的冶炼方法是高速钢冶炼的一种创新,它造就了性能介于硬质合金和普通高速钢之间的新钢种,使机械制造加工业的刀具用材有了新的突破。
作为一种性能优异的新钢种,粉末冶金高速钢正逐渐被人们认识和接受,在机械加工业中发挥越来越大的作用。
1. 粉末冶金高速钢的冶炼特性与普通高速钢的冶炼相比,粉末冶金高速钢的冶炼更具有其特殊性和先进性。
普通高速钢通过电弧炉或感应熔炼炉熔炼后,直接将钢液浇注成钢锭,然后再通过锻造、轧制加工成钢材,但由于钢液浇注冷凝成钢锭时,凝固速度十分缓慢,从钢液中析岀大量的金属碳化物,形成鱼骨状的莱氏体和团块状的粗大共晶碳化物,并产生碳化物偏析,直接影响到钢的各种力学性能,特别是钢的韧性。
而粉末冶金高速钢的冶炼则不同,经过电弧炉或感应熔炼炉熔化的钢液不是直接浇注成钢锭,而是将熔化的钢液通过喷嘴,喷入到高压氮气流中,钢液被迅速雾化冷却成细小的钢粒,其直径一般小于1mm。
再将这样制成的钢粉装入钢桶,对钢桶抽真空,使桶中钢粉间的空气抽净成真空状态,然后焊合钢桶,再在高温高压下将钢桶中的钢粉压制成形,形成热等静压烧结制备工艺。
由此可生产岀致密度几乎为100 % 的粉末冶金高速钢坯料,然后接下来再锻造、轧制成钢材由于粉末冶金在喷雾制粉过程中,钢液冷却速度十分快,避免了普通高速钢铸锭过程中的许多缺陷,雾化的钢液中碳化物来不及聚集长大形成团块状,因此碳化物颗粒细小而均匀,一般为1〜3卩m (最大尺寸不超过6卩m),这就大大提高了钢的强度和韧性。
2. 粉末冶金高速钢的性能和特点粉末冶金高速钢性能十分优越,它具有高强度、高硬度、高韧性、高耐磨性,以及可加工性好的特点,是一种介于硬质合金和高速钢之间的新材料。
由于粉末冶金高速钢制造的刀具的切削性能在所有切削加工领域内全面超越了原来的高速钢,其韧性优于整体硬质合金刀具而越来越受到工具行业的青睐。
3. 粉末冶金高速钢的应用粉末冶金高速钢因具有极佳的韧性和机加工性能、良好的红硬性、较高的抗压强度和高的耐磨性,具有高合金含量、高纯度无偏析、细小的碳化物颗粒和各向同性同质的特点,而得到广泛的应用。
它被用作加工钛和铝合金等有色金属的刀具,用作加工齿轮铣刀、滚刀、插齿刀、剃齿刀等刀具,也可用作侧面铣刀、成形铣刀和拉刀,也常用于麻花钻、机用丝锥、铰刀等制造。
在锯条行业用作带锯双金属钢带,还用作精密冲切工具和冲头冲模的制造、以及其他模具制造。
由于粉末冶金价格较贵(一般是普通高速钢的4〜8倍),所以考虑成本因素,粉末冶金高速钢通常用于制造精密复杂刀具或数控机床用刀具。
粉末冶金高速钢制造的切削刀具性能优于普通高速钢,使用寿命高于普通高速钢(一般2〜3倍),在冲击负荷大的切削场合又可替代硬质合金刀具,因此粉末冶金高速钢刀具在工具行业的应用前景十分看好,越来越受到人们的关注。
亘]自20世纪70年代以来,高速钢刀具的市场份额逐渐被硬质合金刀具所蚕食。
但近年来,随着粉末冶金高速钢(P/M HSS )刀具切削性能的提高,高速钢刀具的市场占有率又有所回升。
与普通高速钢刀具相比,粉末冶金高速钢刀具硬度更高、韧性更好、更耐磨损,因此在某些应用领域(如高冲击性、大切除量的加工场合),粉末冶金高速钢刀具有逐渐取代脆性较大、在切削冲击下易发生碎裂的整体硬质合金刀具的趋势。
粉末冶金高速钢制造工艺于20 世纪60 年代后期在瑞典开发成功,并于70 年代初期进入市场。
该工艺可在高速钢中加入较多合金元素而不会损害材料的强韧性或易磨性,从而可制成具有高硬度、高耐磨性、可吸收切削冲击、适合高切除率加工和断续切削加工的刀具。
高速钢刀具材料主要由两种基本成分构成:一种是金属碳化物(碳化钨、碳化钼或碳化钒),它赋予刀具较好的耐磨性;二是分布在周围的钢基体,它使刀具具有较好的韧性和吸收冲击、防止碎裂的能力。
制备普通高速钢时,是将熔化的钢水从钢水包中注入铸模,使其缓慢冷却凝固。
此时,金属碳化物从溶液中析出,并形成较大的团块。
高速钢中添加的合金含量越多,碳化物团块就越大。
达到某一临界点时,可形成尺寸极大的碳化物团块(直径可达40mm )。
出现大的碳化物团块的临界点根据钢锭的尺寸以及其它因素而略有不同,但一般是在碳化钒含量达到约4%时发生。
通过对钢锭进行锻造、轧制等后续加工,可以粉碎其中一部分碳化物团块,但不可能将其完全消除。
虽然增加钢材中金属碳化物颗粒的数量可以改善材料的耐磨性,但随着合金含量的增加,碳化物的尺寸及团块数量也会随之增加,这对于钢材的韧性会产生极其不利的影响,因为大的碳化物团快可能成为产生裂纹的起始点。
粉末冶金高速钢的制备工艺与普通高速钢的制备工艺不同,熔化的钢水不是直接注入铸模,而是通过一个小喷嘴将其吹入氮气流中进行雾化,喷出的雾状钢水迅速冷却为细小的钢粒(直径小于1mm )。
由于钢水溶液中的碳化物在快速冷却过程中来不及沉淀和形成团快,因此获得的钢粒中碳化物颗粒细小且分布均匀。
将这些钢粉过筛后置入一个钢桶中,并将钢粉中间的空气抽净形成真空状态,然后在高温、高压下将钢桶中的钢粉压制成型,即可得到致密度为100%的粉末冶金高速钢毛坯。
这一制备工艺被称为热等静压(hot isostatic pressing, HIPing )成型。
然后可对毛坯进行锻造、轧制等后续加工.利用热等静压成型工艺制备的粉末冶金高速钢中的碳化物颗粒非常细小,而且不管其合金含量为多少,这些碳化物颗粒都可均匀分布于整个高速钢基体中。
虽然不同的生产商制备粉末冶金高速钢的工艺细节可能略有不同,但其基本工艺原理(氮气雾化制粒和热等静压成型)都是相同的。
十分重要的一点是不能将这种制备工艺与热压烧结工艺(用加热到熔点温度的钢粉压制和烧结工件)相互混淆,虽然这两种工艺在名称上有一些相似,但其工艺原理却完全不同。
典型的热压烧结工艺是在模具中逐个压制出工件,且通常在原材料粉末中加入了粘结剂,因此烧结后的材料中会形成微孔结构。
采用粉末冶金高速钢制备工艺,钢材生产商可以充分增加钢中的金属碳化物含量,而不会对材料的韧性或易磨性造成有害影响。
虽然一些偏爱粉末冶金高速钢的人喜欢将其誉为高速钢与整体硬质合金的“混血儿”,但实际上它只是一种具有尺寸微小的碳化物颗粒和细化的钢基体粒子结构的高速钢。
不过,它确实将高速钢良好的韧性与硬质合金的高耐磨性很好地结合于一身。
由于粉末冶金高速钢中碳化物颗粒细小且分布均匀,因此与碳化物含量相同的普通高速钢相比,其强韧性大大提高。
凭借这一优势,粉末冶金高速钢刀具非常适合用于切削冲击大和金属切除率高的加工场合(如挠曲切削、断续切削等)。
此外,由于粉末冶金高速钢的强韧性不会因金属碳化物含量的增加而削弱,因此钢材生产商可以在钢中添加大量合金元素,以提高刀具材料的性能。
以丝锥为例,由于攻丝加工中丝锥切削刃不断与工件接触和分离,切削冲击较大,因此需要用高强韧牌号的耐碎钢制造丝锥,同时,为了提高丝锥的耐磨损性能,要求刀具材料中的碳化物含量较高。
原来常用的丝锥材料为普通高速钢牌号M-2 ,现在则可用粉末冶金高速钢牌号M-4 替代。
这两种牌号中的中硬碳化物含量大致相同(M-4 为8%,M-2 为7%),但粉末冶金高速钢牌号中的高硬碳化物含量却远远高于普通高速钢(M-4 为6%,M-2 仅为2%),因此M-4 丝锥的耐磨性得到显著增强,加工效率和刀具寿命提高,同时M-4 丝锥的强韧性也大大优于M-2 丝锥,在攻丝加工中不易碎裂。
粉末冶金高速钢的缺点是价格较贵,约为普通高速钢的2〜5倍(不同牌号有所差异)。
因此,刀具制造商必须在刀具性能的提高与额外增加的刀具制造成本之间进行权衡。
对于小型复杂刀具而言,由于材料费用只占刀具总成本的一小部分,因此采用粉末冶金高速钢十分划算。
而对于大尺寸的简单刀具而言,是否选用粉末冶金高速钢则需要仔细斟酌。
不过,粉末冶金高速钢易磨性的显著改善通常可使增加的材料费用得到部分(或全部)补偿。
影响钢材易磨性的主要因素是钢中碳化钒的含量水平,由于碳化钒的硬度要高于磨轮中氧化铝磨粒的硬度,因此在磨削钒含量较高的普通高速钢时,磨粒容易钝化,产生磨削热较多,磨轮磨损较快,所需磨削工时也较长。
而粉末冶金高速钢中碳化物细小且分布均匀,与普通高速钢相比,对磨轮的损耗较小,可大大缩短磨削工时,节省磨削加工费用。
小型复杂刀具通常需要进行大量精密磨削加工,即其磨削/材料成本比率(grinding-to-material- cost ratio )较高,因此增加的材料费用支出很容易在磨削加工环节全部收回(甚至可有盈余)。
而大规格刀具所需磨削加工较少,磨削/材料成本比率较低,因此材料易磨性的改善通常只能部分补偿材料成本的提高。
虽然采用粉末冶金高速钢的经济性因不同刀具制造商的生产工艺而异,但一般而言,刀具材料易磨性的改善可使磨削工时缩短约30%。
如今,粉末冶金高速钢刀具已成为整体硬质合金刀具的有力竞争者。
虽然整体硬质合金刀具硬度很高,但脆性也很大,因此多用于车削加工,而不太适合切削冲击较大的加工和粗加工。
由于粉末冶金高速钢中含有大量硬质碳化物,因此其耐磨性可达到与整体硬质合金相当的水平,而其韧性则优于整体硬质合金,更能胜任要求刀具兼具耐磨性和强韧性的切削加工(如攻丝、立铣加工等)。
粉末冶金高速钢制备技术的最新进展进一步提高了其竞争力。
电渣加热(electro-slag heating, ESH )精炼工艺的应用对于粉末冶金高速钢具有里程碑式的重大意义。
该工艺可以去除钢中几乎所有杂质,进一步提高材料的韧性,显著改善刀具的抗崩刃能力。
此外,由于钢中杂质减少,生产商可以进一步增加钢中的合金含量,例如,某种粉末冶金高速钢牌号的碳化钒含量可达到14%,而普通高速钢牌号碳化钒的最大含量仅为约4%。
虽然钢中添加了大量合金,但并不会影响其韧性和易磨性。
需要注意的是,有许多粉末冶金高速钢生产商为了降低成本,没有采取提高材料纯度的工艺措施,他们生产的钢材中可能含有许多会引起刀具微崩刃的杂质。
但是,仅仅根据生产商提供的产品资料是很难辩别其质量优劣的,用户必须要求生产商说明采取了何种去除杂质的工艺措施,或进一步要求其提供有关钢中杂质大小的详细技术数据。
粉末冶金工艺改变了传统高速钢的材料特性,尤其是采用新开发的提纯技术,使粉末冶金高速钢可以达到极高的合金含量而又能保持其韧性。
因此,粉末冶金高速钢刀具的切削性能在几乎所有切削加工领域全面超越了传统高速钢刀具,并在高切除率、高冲击性切削加工中优于整体硬质合金刀具。