液压系统课程设计专用双行程铣床
专用机床液压系统课程设计

专用机床液压系统课程设计一、课程目标知识目标:1. 学生能理解专用机床液压系统的基本组成、工作原理及功能。
2. 学生能掌握专用机床液压系统的主要参数计算方法及其在实际应用中的选用原则。
3. 学生能了解专用机床液压系统的设计流程,包括系统方案设计、元件选型、系统仿真等。
技能目标:1. 学生具备分析机床液压系统需求的能力,能根据具体工况设计合适的液压系统。
2. 学生能运用相关软件对机床液压系统进行仿真分析,优化系统性能。
3. 学生具备一定的机床液压系统故障诊断与维修能力。
情感态度价值观目标:1. 培养学生严谨的科学态度和良好的团队协作精神,激发学生对液压技术的学习兴趣。
2. 增强学生对我国机床行业发展的信心,提高学生的社会责任感和使命感。
3. 引导学生关注环保和节能,培养绿色设计理念。
课程性质:本课程为专业核心课程,以实践性、应用性为主,结合理论教学,培养学生的实际操作能力和设计能力。
学生特点:学生具有一定的液压基础,具有较强的学习能力和动手能力,对实际应用有较高的兴趣。
教学要求:注重理论与实践相结合,强调实际操作和设计能力的培养,提高学生的综合素质。
将课程目标分解为具体的学习成果,便于后续教学设计和评估。
二、教学内容1. 机床液压系统概述:包括机床液压系统的基本组成、工作原理、功能及在机床行业中的应用。
参考教材章节:第一章 液压与气压传动概述2. 机床液压系统主要参数计算:涉及压力、流量、功率等参数的计算方法及选用原则。
参考教材章节:第二章 液压系统的基本参数与计算3. 机床液压系统设计流程:讲解系统方案设计、元件选型、系统仿真等步骤。
参考教材章节:第三章 液压系统设计4. 液压元件的选用与性能分析:学习各类液压元件的原理、性能及选型方法。
参考教材章节:第四章 液压元件5. 液压系统仿真与优化:运用相关软件对机床液压系统进行仿真分析,优化系统性能。
参考教材章节:第五章 液压系统仿真与优化6. 机床液压系统故障诊断与维修:介绍故障诊断方法、维修技巧及注意事项。
专用铣床液压系统设计课程设计
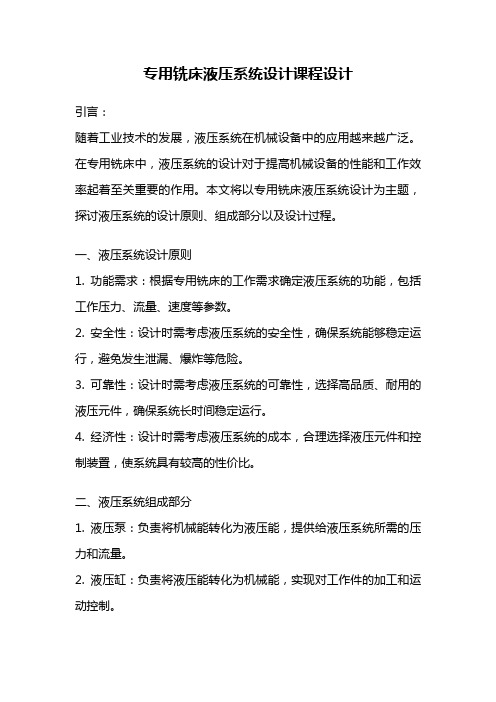
专用铣床液压系统设计课程设计引言:随着工业技术的发展,液压系统在机械设备中的应用越来越广泛。
在专用铣床中,液压系统的设计对于提高机械设备的性能和工作效率起着至关重要的作用。
本文将以专用铣床液压系统设计为主题,探讨液压系统的设计原则、组成部分以及设计过程。
一、液压系统设计原则1. 功能需求:根据专用铣床的工作需求确定液压系统的功能,包括工作压力、流量、速度等参数。
2. 安全性:设计时需考虑液压系统的安全性,确保系统能够稳定运行,避免发生泄漏、爆炸等危险。
3. 可靠性:设计时需考虑液压系统的可靠性,选择高品质、耐用的液压元件,确保系统长时间稳定运行。
4. 经济性:设计时需考虑液压系统的成本,合理选择液压元件和控制装置,使系统具有较高的性价比。
二、液压系统组成部分1. 液压泵:负责将机械能转化为液压能,提供给液压系统所需的压力和流量。
2. 液压缸:负责将液压能转化为机械能,实现对工作件的加工和运动控制。
3. 液压阀:用于控制液压系统的压力、流量和方向等参数。
4. 油箱:贮存液压油,保证液压系统的正常运行。
5. 滤清器:用于过滤液压油中的杂质和污染物,保护液压系统的元件。
6. 液压管路:将液压能传输到不同的液压元件中。
7. 液压控制装置:包括液压控制阀、传感器等,用于控制和监测液压系统的工作状态。
三、液压系统设计过程1. 确定工作需求:根据专用铣床的加工要求和工作条件,确定液压系统的工作压力、流量和速度等参数。
2. 选择液压元件:根据工作需求选择合适的液压泵、液压缸、液压阀等液压元件,确保其性能和质量符合要求。
3. 设计液压管路:根据专用铣床的结构和工作方式,设计合理的液压管路,确保液压能够传输到各个液压元件中,并满足工作需求。
4. 安全措施:在设计过程中,需考虑液压系统的安全性,采取相应的安全措施,如设置泄压阀、安装压力传感器等。
5. 控制系统设计:根据专用铣床的工作要求,设计液压控制系统,包括液压控制阀、传感器等,实现对液压系统的精确控制。
液压专用铣床课程设计
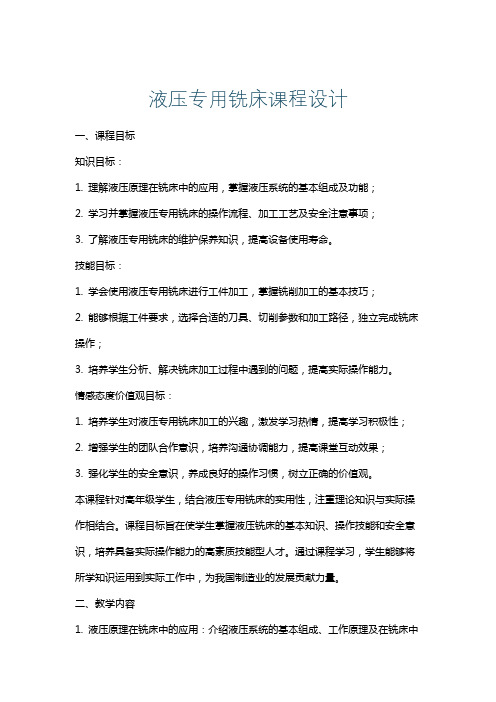
液压专用铣床课程设计一、课程目标知识目标:1. 理解液压原理在铣床中的应用,掌握液压系统的基本组成及功能;2. 学习并掌握液压专用铣床的操作流程、加工工艺及安全注意事项;3. 了解液压专用铣床的维护保养知识,提高设备使用寿命。
技能目标:1. 学会使用液压专用铣床进行工件加工,掌握铣削加工的基本技巧;2. 能够根据工件要求,选择合适的刀具、切削参数和加工路径,独立完成铣床操作;3. 培养学生分析、解决铣床加工过程中遇到的问题,提高实际操作能力。
情感态度价值观目标:1. 培养学生对液压专用铣床加工的兴趣,激发学习热情,提高学习积极性;2. 增强学生的团队合作意识,培养沟通协调能力,提高课堂互动效果;3. 强化学生的安全意识,养成良好的操作习惯,树立正确的价值观。
本课程针对高年级学生,结合液压专用铣床的实用性,注重理论知识与实际操作相结合。
课程目标旨在使学生掌握液压铣床的基本知识、操作技能和安全意识,培养具备实际操作能力的高素质技能型人才。
通过课程学习,学生能够将所学知识运用到实际工作中,为我国制造业的发展贡献力量。
二、教学内容1. 液压原理在铣床中的应用:介绍液压系统的基本组成、工作原理及在铣床中的功能,对应教材第3章第1节;2. 液压专用铣床操作流程:详细讲解铣床的操作步骤、加工工艺及安全注意事项,对应教材第4章第2节;3. 铣削加工技巧:教授铣削加工的基本技巧,包括刀具选择、切削参数设置、加工路径规划等,对应教材第5章;4. 液压专用铣床的维护保养:介绍铣床的日常维护、保养方法及故障排除,对应教材第6章;5. 实际操作训练:安排学生进行液压专用铣床的实操练习,巩固所学知识,提高操作技能。
教学内容根据课程目标进行科学、系统地组织,确保理论与实践相结合。
教学大纲明确教学内容、进度安排及教材章节,旨在帮助学生全面掌握液压专用铣床的知识与技能。
在教学过程中,教师应关注学生的实际操作能力培养,确保教学内容与实际工作需求紧密结合。
专用铣床液压系统设计课程设计

专用铣床液压系统设计课程设计专用铣床液压系统设计课程设计一、引言在现代机械加工领域,铣床是一种常用的机床设备。
为了提高铣床的运行效率和精度,液压系统被广泛应用于铣床中。
本课程设计旨在通过对专用铣床液压系统的设计,使学生掌握液压系统的原理和设计方法。
二、液压系统基础知识1. 液压系统概述液压系统是利用流体传递能量的一种动力传动系统。
它由液压泵、执行元件、控制元件和辅助元件等组成。
2. 液压传动基本原理液体在容器中形成封闭的流体传递介质,通过液压泵产生的高压油将能量传递到执行元件上,从而实现工作机构的运动。
3. 液压执行元件常见的液压执行元件包括油缸、马达和阀门等。
油缸通过受力面积差异实现线性运动,马达则通过转子与定子之间的摩擦力实现旋转运动。
三、专用铣床液压系统设计1. 设计目标专用铣床液压系统的设计目标是实现铣床的高效率、高精度和安全稳定的运行。
2. 系统组成专用铣床液压系统主要由液压泵、油缸、控制阀和辅助元件等组成。
液压泵负责产生高压油,油缸负责驱动工作台进行运动,控制阀则用于控制油液的流向和压力。
3. 液压系统参数选择根据铣床的工作要求和性能指标,选择合适的液压元件参数。
包括液压泵的流量、工作台的移动速度和承载能力等。
4. 液压系统布局设计根据铣床结构和工作台运动方式,合理布局液压元件。
保证油路畅通,减小能量损失和泄漏。
5. 液压系统控制策略设计根据铣床的工作过程,确定合理的控制策略。
可以采用手动控制或自动控制方式,实现对工作台运动的精确控制。
6. 液压系统安全保护设计在液压系统中添加安全保护装置,如过载保护阀、压力传感器和液压缸的行程限位装置等,以确保铣床的安全运行。
四、课程设计步骤1. 确定课程设计内容和目标明确课程设计的具体内容和目标,包括液压系统的基本原理、专用铣床液压系统的设计要求等。
2. 学习液压系统基础知识学生需要通过自学或教师讲解等方式,掌握液压系统的基本原理、执行元件和控制元件等知识。
液压双行程铣床课程设计

液压双行程铣床课程设计一、课程目标知识目标:1. 学生能理解液压双行程铣床的基本结构、工作原理及其在机械加工中的应用。
2. 学生能掌握液压系统在铣床中的作用,如速度调节、力矩控制等关键概念。
3. 学生能描述液压双行程铣床的操作流程,了解其安全操作规程。
技能目标:1. 学生能操作液压双行程铣床,进行简单的铣削加工,并正确调整铣床的各项参数。
2. 学生能通过实际操作,掌握液压系统的基本调试方法,确保铣床正常工作。
3. 学生能运用所学的知识和技能,解决铣床加工过程中出现的简单问题。
情感态度价值观目标:1. 学生能培养对机械加工职业的兴趣和热情,增强对液压双行程铣床操作的自豪感。
2. 学生能树立安全意识,养成遵守操作规程、爱护设备的好习惯。
3. 学生能在团队协作中发挥积极作用,提高沟通与协作能力。
课程性质:本课程为实践性较强的专业课,注重理论与实践相结合,通过实际操作培养学生的技能。
学生特点:学生具备一定的机械基础知识,动手能力强,对新鲜事物充满好奇。
教学要求:教师应结合学生特点,采用启发式、讨论式和现场教学等多种教学方法,引导学生掌握液压双行程铣床的相关知识和技能。
在教学过程中,注重培养学生的安全意识、团队合作精神和职业素养。
通过分解课程目标,确保教学设计和评估具有针对性和实效性。
二、教学内容1. 理论知识:- 液压双行程铣床的结构组成与工作原理。
- 液压系统在铣床中的应用,包括液压泵、液压缸、控制阀等元件的作用。
- 铣削加工的基本概念,如铣削速度、进给量、切削深度等。
2. 实践操作:- 液压双行程铣床的操作流程,包括开机、调试、加工、关机等步骤。
- 液压系统的调试与维护方法。
- 常见铣削加工工艺及操作要领。
3. 教学大纲:- 第一周:液压双行程铣床的基本结构与工作原理学习。
- 第二周:液压系统元件的认识及在铣床中的应用。
- 第三周:铣削加工的基本概念及参数设置。
- 第四周:液压双行程铣床的操作流程及实际操作。
机电液压课程设计专用铣床
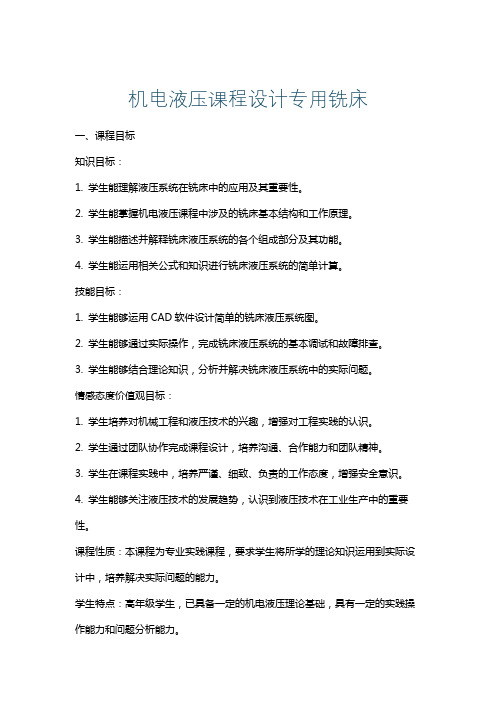
机电液压课程设计专用铣床一、课程目标知识目标:1. 学生能理解液压系统在铣床中的应用及其重要性。
2. 学生能掌握机电液压课程中涉及的铣床基本结构和工作原理。
3. 学生能描述并解释铣床液压系统的各个组成部分及其功能。
4. 学生能运用相关公式和知识进行铣床液压系统的简单计算。
技能目标:1. 学生能够运用CAD软件设计简单的铣床液压系统图。
2. 学生能够通过实际操作,完成铣床液压系统的基本调试和故障排查。
3. 学生能够结合理论知识,分析并解决铣床液压系统中的实际问题。
情感态度价值观目标:1. 学生培养对机械工程和液压技术的兴趣,增强对工程实践的认识。
2. 学生通过团队协作完成课程设计,培养沟通、合作能力和团队精神。
3. 学生在课程实践中,培养严谨、细致、负责的工作态度,增强安全意识。
4. 学生能够关注液压技术的发展趋势,认识到液压技术在工业生产中的重要性。
课程性质:本课程为专业实践课程,要求学生将所学的理论知识运用到实际设计中,培养解决实际问题的能力。
学生特点:高年级学生,已具备一定的机电液压理论基础,具有一定的实践操作能力和问题分析能力。
教学要求:结合学生特点,注重理论与实践相结合,提高学生的实际操作能力和创新能力。
通过课程目标的分解,使学生在完成设计任务的同时,达到知识、技能和情感态度价值观的全面提升。
二、教学内容1. 理论知识:- 液压基础知识:液压原理、流体力学基础、液压油性质等。
- 铣床液压系统组成:液压泵、液压缸、控制阀、油箱、管路等。
- 液压系统设计原理:系统压力、流量计算,元件选型,系统布局等。
2. 实践操作:- 铣床液压系统图设计:利用CAD软件绘制铣床液压系统图。
- 液压系统组装与调试:动手实践,完成铣床液压系统的组装、调试和故障排查。
3. 教学案例:- 分析典型铣床液压系统案例,理解液压系统在实际应用中的设计要点和优化方法。
4. 教学进度安排:- 理论知识学习:2课时。
- 液压系统图设计:3课时。
铣床液压课程设计

铣床液压课程设计一、课程目标知识目标:1. 理解铣床液压系统的基本原理和组成部分;2. 掌握铣床液压系统的主要参数及其对铣削加工的影响;3. 了解不同铣床液压系统的特点及其适用场景。
技能目标:1. 能够正确操作铣床液压系统,并进行基本的调试和故障排除;2. 能够根据加工需求,合理选择和调整铣床液压系统的参数;3. 能够运用铣床液压系统进行简单的铣削加工,并确保加工质量和效率。
情感态度价值观目标:1. 培养学生对机械加工和液压技术的兴趣,激发学习热情;2. 培养学生严谨的科学态度,注重实践操作的安全性和准确性;3. 培养学生的团队合作意识,学会在铣床液压系统操作中相互协作和沟通。
课程性质:本课程为实践性较强的技术学科,结合铣床液压系统的基础知识和操作技能,培养学生实际应用能力。
学生特点:学生为高年级中职或高职机械类相关专业的学生,具备一定的机械基础知识和动手能力。
教学要求:注重理论与实践相结合,强调操作技能的培养,同时关注学生情感态度价值观的引导。
将课程目标分解为具体的学习成果,以便进行有效的教学设计和评估。
二、教学内容1. 铣床液压系统原理:讲解液压系统的基本工作原理,包括液压泵、液压缸、控制阀等主要组成部分的功能和相互关系。
教材章节:第二章“液压系统基本原理”2. 铣床液压系统参数:学习液压系统的主要参数,如压力、流量、油温等,探讨这些参数对铣削加工的影响。
教材章节:第三章“液压系统参数及其调整”3. 铣床液压系统操作与调试:介绍铣床液压系统的操作方法,包括启动、停止、调整等,以及系统调试的基本步骤和注意事项。
教材章节:第四章“铣床液压系统的操作与维护”4. 铣床液压系统故障排除:分析常见的铣床液压系统故障现象,学习故障诊断和排除方法。
教材章节:第五章“液压系统的故障诊断与排除”5. 铣床液压系统在实际应用中的选择与调整:根据加工需求,指导学生如何选择合适的铣床液压系统,并进行参数调整,以提高加工质量和效率。
专用铣床液压系统设计课程设计
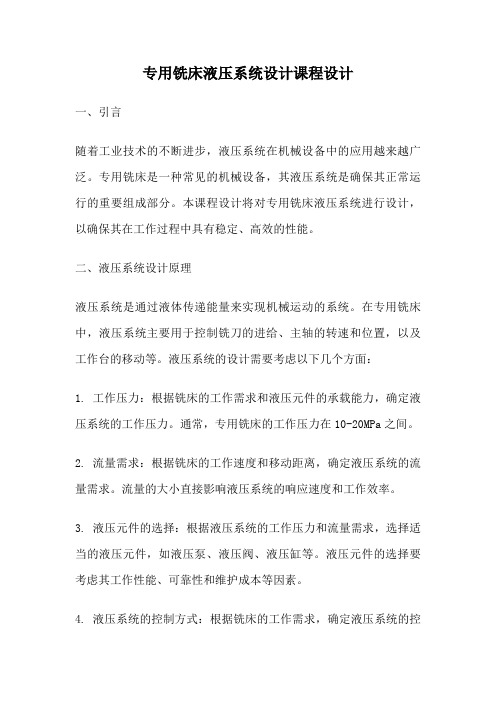
专用铣床液压系统设计课程设计一、引言随着工业技术的不断进步,液压系统在机械设备中的应用越来越广泛。
专用铣床是一种常见的机械设备,其液压系统是确保其正常运行的重要组成部分。
本课程设计将对专用铣床液压系统进行设计,以确保其在工作过程中具有稳定、高效的性能。
二、液压系统设计原理液压系统是通过液体传递能量来实现机械运动的系统。
在专用铣床中,液压系统主要用于控制铣刀的进给、主轴的转速和位置,以及工作台的移动等。
液压系统的设计需要考虑以下几个方面:1. 工作压力:根据铣床的工作需求和液压元件的承载能力,确定液压系统的工作压力。
通常,专用铣床的工作压力在10-20MPa之间。
2. 流量需求:根据铣床的工作速度和移动距离,确定液压系统的流量需求。
流量的大小直接影响液压系统的响应速度和工作效率。
3. 液压元件的选择:根据液压系统的工作压力和流量需求,选择适当的液压元件,如液压泵、液压阀、液压缸等。
液压元件的选择要考虑其工作性能、可靠性和维护成本等因素。
4. 液压系统的控制方式:根据铣床的工作需求,确定液压系统的控制方式。
常见的控制方式有手动控制、自动控制和数控控制等。
三、液压系统设计步骤1. 确定系统要求:根据专用铣床的工作特点和要求,明确液压系统的工作压力、流量需求和控制方式等。
2. 选择液压元件:根据系统要求,选择合适的液压元件。
液压泵的选择要考虑其流量和压力特性;液压阀的选择要考虑其控制特性和可靠性;液压缸的选择要考虑其负载能力和运动特性等。
3. 绘制液压系统图:根据系统要求和液压元件的选择,绘制液压系统图。
液压系统图应包括液压泵、液压阀、液压缸等液压元件的连接关系和管路布置。
4. 计算液压系统参数:根据系统要求和液压元件的特性,计算液压系统的参数,如泵的流量和压力、液压缸的负载和速度等。
5. 设计液压系统控制装置:根据系统要求和控制方式,设计液压系统的控制装置。
控制装置可以采用手动操作、电气控制或计算机控制等方式。
- 1、下载文档前请自行甄别文档内容的完整性,平台不提供额外的编辑、内容补充、找答案等附加服务。
- 2、"仅部分预览"的文档,不可在线预览部分如存在完整性等问题,可反馈申请退款(可完整预览的文档不适用该条件!)。
- 3、如文档侵犯您的权益,请联系客服反馈,我们会尽快为您处理(人工客服工作时间:9:00-18:30)。
华中科技大学机械学院液压系统课程设计专用双行程铣床机制0803班目录一、 设计内容 ......................................................... 2 二、 负载分析与计算 ................................................... 2 三、 液压系统原理图设计分析 ........................................... 4 1. 液压缸参数计算 ............................................... 5 2. 确定液压泵的流量、压力和选择泵的规格 ......................... 8 3. 液压阀,过滤器,油管及油箱的选择 ............................. 9 4. 液压系统的验算 .............................................. 11 四、 PLC 控制系统设计 ................................................. 13 1. 各电磁铁动作顺序表 .......................................... 13 2. PLC 控制连接图 ............................................... 14 3. 继电器-接触器控制梯形图 ..................................... 15 4. PLC 控制梯形图 ............................................... 16 5. 指令语句表 .................................................. 17 六、 感受与收获 ...................................................... 18 参考资料 . (18)一、设计内容设计一专用双行程铣床。
工件安装在工作台上,工作台往复运动由液压系统实现。
双向铣削。
工件的定位和夹紧由液压实现,铣刀的进给由机械步进装置完成,每一个行程进刀一次。
要求机床的工作循环为:手工上料——按电钮——工件自动定位、夹紧——工作台往复运动铣削工件若干次——拧紧铣削——夹具松开——手工卸料(泵卸载)。
工作台往复运动速度(m/min )v01/v02 (0.8~8)/(0.4~4)。
取快进、快退最快速度为16m/min 。
工作台往复运动的行程(100~270)mm ,最大行程定为500mm 。
定位缸的负载200N ,行程100mm ,动作时间1s ;夹紧的缸的负载2000N ,行程15mm ,动作时间1s 。
二、负载分析与计算取液压缸的机械效率m η为0.92。
计算液压缸驱动力0m F =F η(N ) 2-1根据公式2-1,计算液压缸驱动力得定位液压缸的驱动力为0F =2002170.92N = 得夹紧液压缸的驱动力为0F =200021740.92N = 切削负载(F 01/F 02):13000/6500N ;工作台液压缸总负载m f a F=F +F +F 2-2m F 为工作负载,a F 为惯性负载,f F 为摩擦阻力负载m F =13000/6500N ,a F 不作考虑,f F 设动摩擦为2500N ,静摩擦为5000N 。
由公式2-1,工作台液压缸的工作推力快进、快退时外负载F=2500N ,启动加速是外负载F=5000N ,工作缸的外负载为图1 工作循环图根据上述计算结果各工作阶段所受的外负载,并画出负载循环图。
图2 速度循环图图3 负载循环图三、液压系统原理图设计分析(1) 确定供油方式:根据设计背景要求,供油方式采用限压式变量泵,变量泵选择用带压力反馈的限压式变量叶片泵。
(2) 调速方式的选择:调速阀调速。
(3) 速度换接方式的选择采用电磁阀的快慢速换接回路,特点是结构简单、调节行程比较方便,但速度换接的平稳性较差。
若要提高系统的换接平稳性,则可改用行程阀切速的速度换接回路。
(4) 夹紧回路的选择用二位四通阀来控制夹紧、松开换向动作时,为了避免工作时突然失电而松开,应该用失电夹紧方式。
考虑到夹紧时间可调节和当进油路压力瞬间下降时仍能保持夹紧力,所以接入节流阀调速和单向阀保压。
在该回路中还装有减压阀,用来调节夹紧力的大小和保持夹紧力的稳定。
图4 液压系统原理图1. 液压缸参数计算(1)参考GB2348-80,铣床液压系统的工作压力选为5MPa 。
(2)由于要求工作台双向移动速度相等,快进,快退速度相等,故工作液压缸选用单缸双杆式。
夹紧和定位缸均选单缸单杆式。
(3)计算工作液压缸内径D 和活塞杆直径d , 最大负载为16848N ,取背压2P 为0.5Mpa ,试取d/D =0.7。
将数据代入式得-29.6710m =⨯,根据液压缸内尺寸系列GB2348-80,液压缸内径圆整为标准系列直径D=100mm ,按d/D=0.7,取d=70mm 。
(4)计算夹紧缸和定位缸内径D 和活塞杆直径d 。
按工作要求的夹紧力由一个夹紧缸提供,考虑到夹紧力的稳定,夹紧缸的工作压力应低于进给液压缸的的工作压力,现取夹紧缸的工作压力为2Mpa ,回油背压力为0.5Mpa ,取液压缸的机械效率m η为0.92。
取d/D=0.7代入下式得-2D=3.984x10m ,按液压缸内尺寸系列GB2348-80,和活塞杆直径系列GB2348-80,取夹紧液压缸的D 和d 分别为40mm 及28mm 。
取定位缸工作压力为2Mpa ,回油背压力为0.5Mpa ,取液压缸的机械效率m η为0.92。
取d/D=0.7代入式3-2,得-2D=1.260x10m ,取定位液压缸的D 和d 分别为12mm 及8mm 。
(5) 按最低工进速度验算液压缸的最小稳定速度,min min minq A =v 3-3 A>min A ,min q 是由产品样本查得的最小稳定流量0.05L/min 。
min v 0.4/min m =得A>21.25cm ,调速阀安装在回油路上,液压缸的有效工作面积应选取液压缸有杆腔的实际面积,()222A=40.0354D d cm π-=,可见满足要求。
3)计算在各工作阶段液压缸所需要的流量2222Imax Imax 3.14q (D -d )v (10.7)8032.028L /min 44π==⨯-⨯=工进工进2222max max 3.14q (D -d )v (10.7)4016.014L /min 44π==⨯-⨯=工进Ⅱ工进Ⅱ, 223.140.1560q D v 0.4=1.130L /min 441π⨯==⨯⨯夹紧夹紧,223.14160q D v 0.12=0.678L /min 441π⨯==⨯⨯定位定位。
动时间为:快进1t ,工进一2t ,工进二3t ,快退4t 。
)图5 进油腔压力图图6 输入流量图图7 功率图2. 确定液压泵的流量、压力和选择泵的规格1)泵的工作压力的确定。
由于油管有一定的压降,所以泵的工作压力为p 1p p p =+∆∑ 3-4p ∆∑取为0.5Mpa ,故p p =5.21Mpa 。
p p 是系统的静态压力,考虑到系统在各种工况的过渡阶段出现的动态压力往往超过静态压力。
另外考虑到一定的压力储备量,并确保泵的寿命,因此选泵的额定压力n p p (1.25~1.6)p ≥。
选取1.25p p =6.25Mpa 。
2)泵的流量确定。
液压泵的最大流量应为()p L max q K q ≥∑,L K 为泄漏系数,一般取为1.1~1.3,现取为L K =1.1。
p q =64.06x1.1=70.466L/min 。
3)选择液压泵的规格。
根据以上计算的p p 和p q 查阅《机械设计手册》,按照需求选用YBX-D50(V3)限压式变量叶片泵,该泵的基本参数为:每转排量50ml/min ,泵的额定压力为10Mpa ,电动机额定转速1450r/min ,流量为72.5L/min ,驱动功率10kW ,总效率10.72η=。
4)与液压泵匹配的电动机的选定。
泵的机械效率为10.72η=,电机的工况条件下,取机械效率为20.75η=。
电机所需功率为11112111212()p p Q p p p Q P ηηηη+∆+∆== 3-5快退和快进时,进油腔压力为 1.18Mpa ,其中1p ∆=0.5MPa 是进油路压力损失,2p ∆=0.5MPa 是压力继电器可靠动作需要的压力差,3333164.0610/60/ 1.0710/Q m s m s --=⨯=⨯,推出,14320P W =;Ⅰ工进时,电机所需功率,根据公式3-5,其中1p ∆=0.5MPa 是调速阀所需最小压力,2p ∆=0.5MPa 是压力继电器可靠动作需要的压力差,3333232.0310/60/0.53410/Q m s m s --=⨯=⨯,得,25647P W =;由以上计算可知,最大功率出现在Ⅰ工进阶段,P max =5647W ,则电动机的功率应为N p >5912W 。
据此查样本选用Y2-132M-4三相异步电动机,电动机额定功率为7.5Kw ,额定转速为1440/min r 。
3. 液压阀,过滤器,油管及油箱的选择1)液压阀及过滤器的选择根据液压系统的最高工作压力和通过各个阀类元件和辅助元件的最大流量,可选出这根据选定的液压阀的连接油口尺寸确定管道尺寸。
由于系统在液压缸工进速度最快时,流量最大,实际最大流量约为:max 64/min Q L =,则泵的流量为额定流量72.5/min L ,连接液压缸的进出油路油管的直径选择公称通径为20mm 。
所以,按产品样本标准JB827-66,JB/Z95-67,选用公称通径为20mm 的管件。
3)油箱容积的选择中压系统的油箱容积一般取液压泵额定流量的5~7倍,这里取6倍,即6r V Q =,其中r Q 为液压泵每分钟排出压力油的体积。
得,V=400L 。
4. 液压系统的验算(1 ) 系统压力损失验算由于系统的具体管路布置尚未清楚,整个回路的压力损失无法估算,仅只有阀类元件对压力损失所造成的影响可以看得出来,供调定压力值时参考。
由于快进时的油液流量比快退时的流量大,所以其压力损失也就比快退时的大。
因此必须计算快进时进油路与回油路的压力损失。
假定液压系统选用N32号液压油,考虑最低工作温度为15℃,由手册查出此时油的运动粘度21.5 1.5st cm s ν==,,油的密度3900Kg m ρ=,液压元件采用集成块式的配置形式,Q 取64.06/min L ,即30.00107Q m =。