汽车轮毂的制造工艺.
钢制轮毂生产工艺
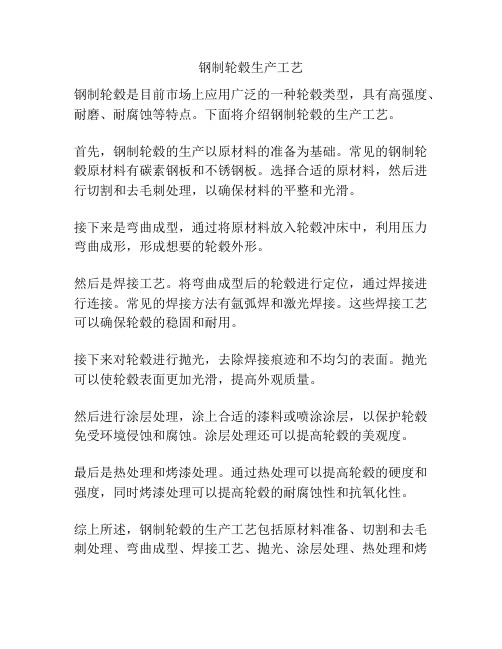
钢制轮毂生产工艺
钢制轮毂是目前市场上应用广泛的一种轮毂类型,具有高强度、耐磨、耐腐蚀等特点。
下面将介绍钢制轮毂的生产工艺。
首先,钢制轮毂的生产以原材料的准备为基础。
常见的钢制轮毂原材料有碳素钢板和不锈钢板。
选择合适的原材料,然后进行切割和去毛刺处理,以确保材料的平整和光滑。
接下来是弯曲成型,通过将原材料放入轮毂冲床中,利用压力弯曲成形,形成想要的轮毂外形。
然后是焊接工艺。
将弯曲成型后的轮毂进行定位,通过焊接进行连接。
常见的焊接方法有氩弧焊和激光焊接。
这些焊接工艺可以确保轮毂的稳固和耐用。
接下来对轮毂进行抛光,去除焊接痕迹和不均匀的表面。
抛光可以使轮毂表面更加光滑,提高外观质量。
然后进行涂层处理,涂上合适的漆料或喷涂涂层,以保护轮毂免受环境侵蚀和腐蚀。
涂层处理还可以提高轮毂的美观度。
最后是热处理和烤漆处理。
通过热处理可以提高轮毂的硬度和强度,同时烤漆处理可以提高轮毂的耐腐蚀性和抗氧化性。
综上所述,钢制轮毂的生产工艺包括原材料准备、切割和去毛刺处理、弯曲成型、焊接工艺、抛光、涂层处理、热处理和烤
漆处理等环节。
这些工艺都是为了生产出质量稳定、耐用且美观的钢制轮毂。
铝合金轮毂的8种典型生产工艺

铝合金轮毂的8种典型生产工艺轮毂,别名轮圈,即轮胎内廓用以支撑轮胎的圆桶形、中心装配在轴上的部件。
常见的汽车轮毂有钢质轮毂及铝合金质轮毂。
钢质轮毂的强度高,常用于大型载重汽车;但钢质轮毂质量重,外形单一,不符合如今低碳、时尚的理念,正逐渐被铝合金轮毂替代。
目前市场上乘用车的原厂轮毂基本都是铝合金轮毂。
铝合金轮毂的生产工艺主要有以下几种:1、重力铸造金属型重力铸造是指在常压下,液体金属靠重力作用充填金属铸型而获得铸件的一种铸造方法,这也是一种古老的铸造方法。
2、低压铸造低压铸造是将铸型放在一个密闭的炉子上面,型腔的下面用一个管(叫升液管)和炉膛里的金属液相通。
3、挤压铸造法4、铸造旋压铸旋分“低压铸造+旋压”和“重力铸造+旋压”两种工艺。
5、常规锻造锻造是铝轮毂应用较早的成形工艺之一。
6、铸造锻造法它是将铸件作为锻造工序的坯料使用,对其进行塑X加工的方法。
7、半固态模锻工艺所谓半固态模锻,就是将半固态坯料加热到有50%左右体积液相的半固态状态后一次模锻成形,获得所需的接近尺寸成品零件的工艺,这是一种介于固态成形和液态成形之间的崭新工艺。
近10年来,半固态成形技术在国外获得了广泛的应用,已逐步成为各先进工业国家竞相发展的一个新领域,被专家学者称为21世纪新一代新兴的金属成形技术。
预计在相当长的一段时期内,半固态成形的主要市场是汽车工业,应用最成功和最广泛的是汽车铝合金零件。
美国已建成数家铝合金半固态模锻工厂,其中美国的AEMP(Alumax Enginered metal Process)公司与Superior工业公司合作于1992年在阿肯色州建成了全球首家半固态模锻铝合金汽车轮毂厂。
用半固态模锻代替低压铸造生产ZL101铝合金车轮毂,不仅能减少机械加工量和提高生产率,而且还可以提高机械X能,减轻质量。
8、锻造旋压比较高端的成形工艺,目前国内只有10%左右企业采用该工艺进行生产,产品主要供应国内外的大巴、货车及高端轿车市场。
汽车轮毂制造工艺
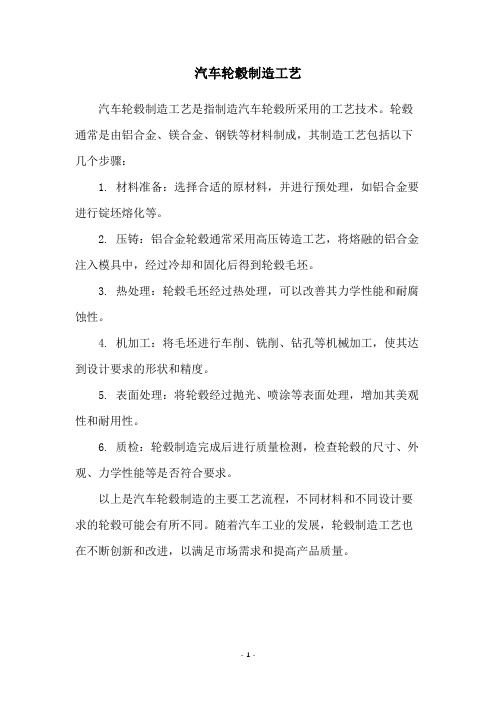
汽车轮毂制造工艺
汽车轮毂制造工艺是指制造汽车轮毂所采用的工艺技术。
轮毂通常是由铝合金、镁合金、钢铁等材料制成,其制造工艺包括以下几个步骤:
1. 材料准备:选择合适的原材料,并进行预处理,如铝合金要进行锭坯熔化等。
2. 压铸:铝合金轮毂通常采用高压铸造工艺,将熔融的铝合金注入模具中,经过冷却和固化后得到轮毂毛坯。
3. 热处理:轮毂毛坯经过热处理,可以改善其力学性能和耐腐蚀性。
4. 机加工:将毛坯进行车削、铣削、钻孔等机械加工,使其达到设计要求的形状和精度。
5. 表面处理:将轮毂经过抛光、喷涂等表面处理,增加其美观性和耐用性。
6. 质检:轮毂制造完成后进行质量检测,检查轮毂的尺寸、外观、力学性能等是否符合要求。
以上是汽车轮毂制造的主要工艺流程,不同材料和不同设计要求的轮毂可能会有所不同。
随着汽车工业的发展,轮毂制造工艺也在不断创新和改进,以满足市场需求和提高产品质量。
- 1 -。
钢轮毂生产工艺

钢轮毂生产工艺
钢轮毂生产工艺是指通过一系列的加工和生产过程,将原料制作成轨道车辆所需的钢轮毂产品的工艺过程。
首先,钢轮毂生产工艺的第一步是原料准备。
通常使用优质的合金钢作为原材料,并对原料进行检验和筛选,确保原料质量合格。
接下来,将筛选后的原料进行加热处理。
通过高温加热,将材料变得柔软且易于加工。
加热过程还可以降低材料的内应力,提高材料的耐磨性能。
然后,对加热后的原料进行锻造。
锻造是将原料置于机床上,通过压制和变形来改变其形状和尺寸的工艺过程。
通常使用液压或机械锻造设备进行锻造,以确保钢轮毂的均匀性和一致性。
完成锻造后,对锻造件进行热处理。
热处理是通过控制温度和时间来改善材料的力学性能和组织结构的过程。
常见的热处理方法包括淬火、回火和正火。
经过热处理后,对钢轮毂进行精加工。
精加工是通过切削、磨削和铣削等加工方法来加工和修整钢轮毂的工艺过程。
这一步骤旨在确保钢轮毂的尺寸精度和表面质量。
最后,进行钢轮毂的检测和质量控制。
通过尺寸检测、外观检测和性能测试等手段来检测钢轮毂的质量。
质量合格的产品将进行包装和存储,以备下一步的配送和应用。
总体来说,钢轮毂生产工艺包括原料准备、加热处理、锻造、热处理、精加工、检测和质量控制等步骤。
通过这些工艺过程,可以制造出质量合格的钢轮毂产品,以满足轨道车辆的使用需求。
轮毂模具制作工艺

轮毂模具制作工艺轮毂模具制作工艺是指将轮毂产品的设计图纸转化为实际零件的过程,它是制造高质量轮毂的关键环节。
以下为轮毂模具制作工艺的主要步骤及流程。
1. 设计轮毂模具:首先,需要根据轮毂产品的设计要求和图纸,设计轮毂模具的结构和形状。
这一步是制作工艺的基础,要根据轮毂的尺寸、形状、孔距和孔径等要求来确定模具的结构参数。
2. 材料准备:根据轮毂模具的设计要求,在选择合适的材料方面,需要考虑模具的耐磨性、强度和硬度等。
常见的材料有优质钢材、合金钢等,根据实际情况进行选择。
3. CNC加工模具:接下来,将轮毂模具的设计图纸输入到计算机数控(CNC)加工机器中,进行模具的加工。
这一步主要是利用机器自动控制削剪、刮削、铣削等工艺,将模具的外形和内部空腔进行加工成型。
4. 精细加工模具:在CNC加工完成后,有时还需要进行一些精细加工工艺,如磨削、抛光等。
这些工艺主要是为了提高模具的表面光洁度和尺寸精度,确保模具加工的质量。
5. 模具组装:模具加工完成后,需要根据设计要求进行模具的组装。
这一步主要是将模具的各个零部件进行拼装,确保模具的结构完整、刚性良好,并能满足后续的使用要求。
6. 模具热处理:某些情况下,为提高模具的硬度和耐磨性,还需要对模具进行热处理。
热处理一般包括淬火、回火、正火等工艺,以增强模具的耐用性和使用寿命。
7. 模具检验:模具制作完成后,需要对模具进行严格的检验。
主要包括尺寸检验、外观检查和功能测试等,以确保模具的质量和性能符合设计要求。
8. 模具调试:模具通过检验后,需要进行调试。
在模具调试过程中,需要根据实际的生产要求进行参数的调整,做好轮毂模具的准备工作。
9. 模具正式投产:经过调试和确认后,模具可以投入正式的生产使用。
在生产过程中,需要进行模具的定期维护和保养,以保证模具的使用寿命和工作效率。
10. 模具改进和优化:一旦模具投入使用,就需要不断对模具进行改进和优化。
根据轮毂产品的实际情况和用户的反馈,可以改进模具的结构和工艺,以提高轮毂产品的质量和效率。
轮毂生产工艺流程

轮毂生产工艺流程轮毂生产工艺流程是指将原材料经过一系列的加工和处理,最终制成轮毂的过程。
下面是一个典型的轮毂生产工艺流程,大致包括以下几个步骤:1. 原材料准备:轮毂的原材料一般是铝合金或钢材。
首先需要根据设计要求选择合适的原材料,并对原材料进行检测和质量验收。
2. 模具制作:根据轮毂的设计图纸,制作相应的模具。
这些模具一般由铸造模具、加工模具等组成,用于后续工序的操作。
3. 铸造:将铝合金或钢材熔化,并倒入铸造模具中进行注射或浇铸,形成初步的轮毂形状。
4. 精密加工:经过铸造得到的轮毂需要进行精密加工,包括修整外表面、铣削轮缘和孔径、钻孔或滚丝等操作。
5. 表面处理:对轮毂进行表面处理,包括喷砂、抛光、镀铬等工艺。
这些工艺可以改善轮毂表面的光洁度、耐腐蚀性和装饰性。
6. 精加工:经过表面处理的轮毂需要进行精加工,包括钻孔、搅拌轧辊、修整孔径和轮缘等操作。
这些工艺可以提高轮毂的尺寸精度和表面质量。
7. 色彩处理:一些轮毂需要进行涂装或喷涂,以增加产品的美观度和耐久性。
通常要经过底漆、涂装、烘干和固化等多个步骤。
8. 轮毂组装:如果轮毂是多部件组成的,需要进行组装。
这包括预装轮缘和中心盖、紧固螺栓和气门芯等。
9. 检测和质量控制:在各个工序中需要进行检测和质量控制,以确保产品符合设计要求和标准。
常见的检测方法包括外观检查、尺寸测量和材料质量检测。
10. 包装和出厂:经过检测和质量控制的轮毂可以进行包装,并准备出厂。
通常要将轮毂包装在适当的包装箱中,以保护产品免受损坏。
以上是一个典型的轮毂生产工艺流程,每个工艺流程都需要经过严格的操作和控制,以确保产品的质量和性能。
这个流程只是一个概述,并不具体说明每个步骤的细节和操作方法。
实际的轮毂生产过程可能会因不同的厂商和工艺而有所不同。
车轮是怎么制造的?
车轮是怎么制造的?
制造车轮是一项复杂的工程,要求制造精度极高。
它的过程是对精密制造技术的生动诠释,以下是其制造的步骤:
一、锻造
锻造是制造车轮的第一步,通过高温,高压将原料合金铸造,使钢质比较细腻,形成为几何形式的轮毂模具。
通过轮辋等组装完成后,此车轮就形成,并试验其负荷能力等特殊性能。
二、机加工
机加工是指将锻造后的机械零件加工成轮毂,使轮毂具有高精度、光滑表面,以确保能同轮辋接轨或同机械元件接轨。
机加工包括内外车轮的铣削、镗孔、攻丝等加工技术。
三、淬火
淬火是对车轮的一项特殊处理,主要是对凸台、螺旋等机械零件整体进行高热、低热等浸渍处理,使车轮坚硬耐磨,具有良好的强度、刚性和可靠性。
四、贴心外表面
贴心外表面是指将陶瓷、金属或其它材料涂层在车轮内外表面进行涂装,为轮毂增加耐磨性及其它化学稳定性,增强耐腐蚀性,提高车轮外形审美程度,改善车轮的绝缘性能,增加其抗腐蚀性。
五、贴标
贴标是一项必须的步骤,即将产品的生产日期、售后保修等信息印刷在车轮内外表面,以便客户使用时能及时知晓产品的情况,同时可以用于长期管理车轮使用状态。
从以上五项工艺可以看到,制造车轮流程复杂,要求对精密制造技术实施的过程严格把关,以保证车轮质量及性能可靠稳定。
只有完成了所有流程,车轮才能够遵守印度汽车标准,且满足用户高度要求,健康安全可靠地投入使用。
铝合金轮毂制造工艺
铝合金轮毂制造工艺铝合金轮毂是现代汽车制造中常用的一种轮毂材料,它具有轻质、高强度、耐腐蚀等优点,因此被广泛应用于汽车制造中。
本文将介绍铝合金轮毂的制造工艺。
一、铝合金轮毂的材料选择铝合金轮毂的材料选择非常重要,它直接影响到轮毂的质量和性能。
目前常用的铝合金材料有A356、A357、A356.2、A357.2等。
其中,A356和A357是最常用的两种材料,它们具有良好的铸造性能和机械性能,可以满足轮毂的要求。
二、铝合金轮毂的铸造工艺铝合金轮毂的制造工艺主要包括铸造、热处理、机加工等环节。
其中,铸造是最关键的一步,它直接影响到轮毂的质量和性能。
1.模具制造模具是铸造的关键,它的制造质量直接影响到铸造件的质量。
模具的制造需要根据轮毂的形状和尺寸进行设计,然后制造出模具。
模具的制造需要考虑到铸造过程中的收缩率和变形,以保证铸造件的尺寸精度和形状精度。
2.熔炼铝合金铝合金轮毂的铸造采用熔炼铝合金的方法。
首先将铝合金料放入熔炉中加热,使其熔化。
然后加入一定量的熔剂和精炼剂,以去除杂质和气泡。
最后将熔融的铝合金倒入模具中进行铸造。
3.铸造铸造是铝合金轮毂制造的关键环节。
在铸造过程中,需要控制铝合金的温度、流速和压力等参数,以保证铸造件的质量和性能。
铸造完成后,需要进行冷却和固化,以保证铸造件的尺寸精度和形状精度。
三、铝合金轮毂的热处理工艺铝合金轮毂的热处理工艺是为了改善轮毂的性能和耐腐蚀性。
常用的热处理工艺有T6、T7、T8等。
其中,T6是最常用的一种热处理工艺,它可以提高铝合金轮毂的强度和硬度,同时保持良好的韧性和耐腐蚀性。
四、铝合金轮毂的机加工工艺铝合金轮毂的机加工工艺是为了加工轮毂的表面和孔洞等部位。
常用的机加工工艺有车削、铣削、钻孔等。
机加工工艺需要根据轮毂的形状和尺寸进行设计,以保证加工精度和表面质量。
五、铝合金轮毂的质量检测铝合金轮毂的质量检测是为了保证轮毂的质量和性能。
常用的质量检测方法有外观检查、尺寸检查、硬度检测、化学成分分析等。
轮毂制造工艺流程
轮毂是汽车上最重要的平安零件之一,有钢制轮毂和铝制轮毂之分,轮毂承受着汽车和载物质量作用的压力,受到车辆在起动、制动时动态扭矩的作用,还承受汽车在行驶过程中转弯、凹凸路面、路面障碍物冲击等来自不同方向动态载荷产生的不规那么交变受力。
轮毂的质量和可靠性不但关系到车辆和车上人员物资的平安性,还影响到车辆在行驶中的平稳性、操纵性、舒适性等性能,这就要求轮毂动平衡好、疲劳强度高、有好的刚度和弹性、尺寸和形状精度高、质量轻等,铝轮毂以其良好的综合性能满足了上述要求,在平安性、舒适性和轻量化等方面表现突出,博得了市场青睐,正逐步代替钢制轮毂成为最正确选择。
铝轮毂的制造设备、技术及趋势汽车铝轮毂的最主要的生产工艺流程是:熔化→精炼→材料检验→低压铸造→X 射线探伤→热处理→机械加工→动平衡检验→气密性检验→涂装。
1、熔化轮毂铝合金的熔化设备,按炉型分为塔式炉、感应炉、倾转炉、固定炉,按能源形式分为柴油、天然气、煤制气、电能。
塔式炉熔化速度快、烧损少、能耗低;感应炉熔化速度快、合金成分均匀、生产环境好;倾转炉可以配料也可以做保温炉使用、使用平安、维护方便;固定炉可以配料也可以做保温炉使用、使用和维护简便;燃油热值高、熔化效率高、使用维护方便,燃气生产环境好、清洁、使用维护方便;煤制气经济实惠,电能容易控制、生产环境好。
其中以燃油或燃气的塔式快速熔化炉为佳,同时配以铝屑熔化室使用更加方便,是主选设备。
熔化设备的关键在于炉温的控制,由于需要现场制造,故以国产为宜,而且,施工维护便利。
由于轮毂铝合金对Fe 〔铁〕含量要求严格〔≤0.15%〕,因此炉衬必须采用非金属材料制作,配料时选用高牌号的纯铝,回炉料的比例要严格控制。
国内已有少数厂家采购生产用液态铝合金,并将液态铝合金直接运送到生产现场,采用液态铝合金直接铸造铝轮毂这种工艺方式,大大减少了原材料熔化时的烧损及二次熔化时能源的消耗,是铝轮毂制造技术开展的新方向。
铸造生产现场2、精炼铝液的精炼方法有气体法和熔剂法,处理方式有通入管路法、钟罩压入法、精炼机等。
钢轮毂制造工艺流程
钢轮毂制造工艺流程一、原材料准备。
咱就说啊,这钢轮毂制造,那第一步肯定得把原材料准备好呀。
这原材料呢,主要就是钢材啦。
就像咱做菜得先准备好食材一样,制造钢轮毂的钢材那可得好好挑选呢。
这钢材的质量就直接影响着后面造出来的轮毂咋样。
一般来说呢,会选择那种强度比较合适、质量比较可靠的钢材。
这些钢材可能是从专门的钢铁厂运过来的,刚运来的时候,它们就像一群等待被训练的小士兵,整整齐齐地堆在那儿,就等着被加工成帅气的钢轮毂呢。
二、切割工序。
接下来就到切割这一步啦。
想象一下啊,那些钢材就像一块大蛋糕,咱们得按照一定的尺寸把它切成小块呢。
这个切割可不是随便切切的哦,得用专门的切割设备。
这些设备就像是超级精准的大厨刀,一下下去,就能把钢材按照设计好的尺寸完美地切下来。
切割的时候呢,还会有一些小火花冒出来,就像小烟花一样,还挺好玩的。
切割出来的小钢材块,就初步有了钢轮毂的样子啦,不过这时候还很粗糙呢,就像一个刚捏出来的小泥人,还得经过好多工序才能变成精美的艺术品。
三、冲压成型。
再然后就是冲压成型啦。
这个过程可神奇了呢。
把切割好的钢材块放到冲压机下面,冲压机就像一个大力士,“哐当”一下,就把钢材块压成了钢轮毂的大致形状。
这时候的钢轮毂就像从一个丑小鸭开始向白天鹅转变啦。
冲压的时候呢,压力得控制得特别好,如果压力太大,那钢材可能就被压坏了,如果压力太小呢,又不能把形状完全压好。
就像咱们吹气球,气吹得太多或者太少都不行呢。
冲压成型后的钢轮毂,已经有了轮毂的基本轮廓,但是它的边缘啊、表面啊,还是不够光滑,还得继续加工。
四、加工中心工序。
下面就是加工中心工序啦。
这个工序就像是给钢轮毂做精细的美容手术一样。
在这个工序里,会对钢轮毂的一些关键部位进行加工,比如轮毂的孔啊,还有一些安装螺丝的地方。
这些地方的精度要求可高了,如果加工得不好,那后面轮毂安装到车上的时候就会出问题。
加工的时候呢,那些小刀具就像一个个小工匠,在钢轮毂上精心雕琢着,一点一点地把那些地方做得又精准又漂亮。
- 1、下载文档前请自行甄别文档内容的完整性,平台不提供额外的编辑、内容补充、找答案等附加服务。
- 2、"仅部分预览"的文档,不可在线预览部分如存在完整性等问题,可反馈申请退款(可完整预览的文档不适用该条件!)。
- 3、如文档侵犯您的权益,请联系客服反馈,我们会尽快为您处理(人工客服工作时间:9:00-18:30)。
汽车轮毂制造技术班级:机电1302班学号:13221045姓名:师世健指导教师:邢书明目录一、摘要 (3)二、汽车轮毂的选材 (3)1. 钢铁材料 (3)1.1 球墨铸铁 (3)1.2 其他钢铁材料 (3)2.合金材料 (3)3.复合材料 (3)三、铸造方法 (3)1.压力铸造 (3)2.金属型铸造 (4)3.熔模铸造 (4)4.低压铸造 (5)5.离心铸造 (5)四、工艺方案 (6)1.零件图 (6)2.浇注位置 (6)3.分型面 (7)4.砂芯 (7)5.浇注系统 (7)6.主要工艺参数的确定 (7)7.冒口 (7)8.铸造工艺图 (8)汽车轮毂制造技术一、摘要轮毂,作为汽车一个重要组成结构,起着支撑车身重量的作用,对汽车节能、环保、安全性、操控性都有着极其重要的影响。
对其工作环境及使用要求予以充分分析,对其结构进行合理设计,选取性能优良的材料及适当的加工方法,都是汽车轮毂制造中不可或缺的环节。
二、汽车轮毂的选材1.钢铁材料1.1 铸铁、铸钢球墨铸铁以其优良的综合力学性能应用在轮毂上,如铁素体球墨铸铁、高韧性球墨铸铁等。
但是,由于类似碳素钢轮毂的缺点,以及铸造过程的复杂性和铸造模型所限,轮毂形状难于控制,限制了其应用。
1.2 其他钢铁材料一些合金钢如加入钛元素的低合金钢,合金元素可以细化晶粒,提高钢的力学性能,使钢具有强度高、塑韧性好、加工成形性和焊接性良好,可以作为轮毂用钢;此外,低合金高强度双相钢,如低碳含铌钢,提高贝氏体含量,可以提高屈服强度,提高扩孔率,也可以用作轮辐和轮辋用钢。
在实际应用中的多数钢制轮毂是通过已成型的轮缘和轮盘焊接而成,尽量使自重降低。
2.合金材料汽车采用铝合金轮毂后减重效果明显,轻型车使用铝合金轮毂比传统钢制轮毂轻30%-40%,中型汽车可轻30%左右。
美国森特来因·图尔公司用分离旋压法制出的整体板材(6061合金)车轮,比钢板冲压车轮重量减轻达50%,旋压加工时间不到90s/个,不需要组装作业,适宜大批量生产。
另外,相同外径尺寸的轮毂使用铝合金轮毂抗压强度还有所提高。
3.复合材料复合材料是应现代科学技术发展而出现的具有强大生命力的材料。
由于复合材料具有特殊的振动阻尼特性,可减振和降低噪声、抗疲劳性能好,损伤后易修理,便于整体成形,故可用于制造汽车车身、受力构件、传动轴、发动机架及其内部构件。
三、铸造方法1.压力铸造压力铸造的实质是使液态金属在高压作用下以极高的速度充填型腔,并在压力作用下凝固而获得铸件的一种方法。
采用压铸工艺生产的铸件组织致密、机械性能好、强度和表面硬度较高、铸件的尺寸精确、表面光洁。
但传统压铸工艺生产的铝轮毂最大的缺点是不能通过热处理来进一步提高性能,由于液体金属充型速度极快,型腔中的气体很难完全排除,常以气孔形式存留在铸件中,这些铸件孔隙中的气体在热处理过程中会发生膨胀,使得铸件“起泡”。
为使压铸件也能适用于汽车保安件。
近年来出现了一些无气孔压铸新工艺,最有代表的是充氧压铸法。
充氧压铸法是使压室和压型型腔内的金属液相间的空间充氧置换,并在高速高压下进行压铸,当液体金属充填时,一方面通过排气槽排出氧气,另一方面喷散的铝液与未排出的氧气发生反应,形成氧化铝小微粒,分散在铸件内部,使铸件内不产生气孔。
用充氧压铸法生产的铸件,含气量为只有普通压铸法的1/10,可进行固溶处理和焊接。
与传统压铸法相比,充氧压铸的铝轮毂具有成品率高,组织致密,良好的拉伸强度和耐疲劳性能等优点。
国外该方法已广泛用于铝轮毂的生产,日本轻金属株式会社于1983年开始用此方法大批量生产轿车铝合金轮毂,较采用其它铸造方法生产的同类产品重量减少了15%机加工切削量由原来的2~3mm减少到0.75mm,轮毂价格降低了10%。
美国铸锻公司于1982年开始用充氧压铸法生产汽车铝合金轮毂,代替了原来的低压铸造法,并使铝轮毂的重量减轻了18%。
由于有较高的机械性能和较轻的重量,充氧压铸铝轮毂用于紧急救援车和高级车辆是十分理想的。
2.金属型铸造金属型铸造又称硬模铸造,它是将液体金属浇入金属铸型,以获得铸件的一种铸造方法。
铸型是用金属制成,可以反复使用多次(几百次到几千次)。
金属型铸造目前所能生产的铸件,在重量和形状方面还有一定的限制,如对黑色金属只能是形状简单的铸件;铸件的重量不可太大;壁厚也有限制,较小的铸件壁厚无法铸出。
与砂型铸造比较:在技术上与经济上有许多优点。
金属型生产的铸件,其机械性能比砂型铸件高。
同样合金,其抗拉强度平均可提高约25%,屈服强度平均提高约20%,其抗蚀性能和硬度亦显著提高;铸件的精度和表面光洁度比砂型铸件高,而且质量和尺寸稳定;铸件的工艺收得率高,液体金属耗量减少,一般可节约15~30%;不用砂或者少用砂,一般可节约造型材料80~100%;此外,金属型铸造的生产效率高;使铸件产生缺陷的原因减少;工序简单,易实现机械化和自动化。
金属型铸造虽有很多优点,但也有不足之处。
如:金属型制造成本高;金属型不透气,而且无退让性,易造成铸件浇不足、开裂或铸铁件白口等缺陷;金属型铸造时,铸型的工作温度、合金的浇注温度和浇注速度,铸件在铸型中停留的时间,以及所用的涂料等,对铸件的质量的影响甚为敏感,需要严格控制。
解决这些缺陷可以尽量选用成本较低的金属制造模型,并在型腔内留出透气孔,但因为其制造成本太高,还是不宜应用于汽车轮毂的制造。
3.熔模铸造熔模铸造又称失蜡法。
失蜡法是用腊制作所要铸成器物的模子,然后在蜡模上涂以泥浆,这就是泥模。
泥模晾干后,在焙烧成掏模。
一经焙烧,蜡模全部熔化流失,只剩陶模。
一般制泥模时就留下了浇注口,再从浇注口灌入铜液,冷却后,所需的器物就制成了。
熔模铸件尺寸精度较高,当然由于熔模铸造的工艺过程复杂,影响铸件尺寸精度的因素较多,例如模料的收缩、熔模的变形、型壳在加热和冷却过程中的线量变化、合金的收缩率以及在凝固过程中铸件的变形等,所以普通熔模铸件的尺寸精度虽然较高,但其一致性仍需提高。
压制熔模时,采用型腔表面光洁度高的压型,因此,熔模的表面光洁度也比较高。
此外,型壳由耐高温的特殊粘结剂和耐火材料配制成的耐火涂料涂挂在熔模上而制成,与熔融金属直接接触的型腔内表面光洁度高。
所以,熔模铸件的表面光洁度比一般铸造件的高。
熔模铸造最大的优点就是由于熔模铸件有着很高的尺寸精度和表面光洁度,所以可减少机械加工工作,只是在零件上要求较高的部位留少许加工余量即可,甚至某些铸件只留打磨、抛光余量,不必机械加工即可使用。
由此可见,采用熔模铸造方法可大量节省机床设备和加工工时,大幅度节约金属原材料。
熔模铸造方法的另一优点是,它可以铸造各种合金的复杂的铸件,特别可以铸造高温合金铸件。
如喷气式发动机的叶片,其流线型外廓与冷却用内腔,用机械加工工艺几乎无法形成。
用熔模铸造工艺生产不仅可以做到批量生产,保证了铸件的一致性,而且避免了机械加工后残留刀纹的应力集中。
熔模铸造的缺点是工序繁杂,生产周期长,原辅材料费用比砂型铸造高,生产成本较高,铸件不宜太大、太长,一般限于25kg以下。
而且铸造出来的零件强度不高,所以该方法不适合制造汽车轮毂。
4.低压铸造低压铸造是用干燥、洁净的压缩空气将保温炉中的铝液自下而上通过升液管和浇注系统平稳地向上压到铸造机模具型腔中,保持一定压力,一般为20~60kPa 直到铸件凝固后释放压力。
因在压力下充型和凝固,所以充填性好、铸件缩松少、致密性高。
该法中,坩埚表面的氧化膜不会被破坏,与其它铸造方法比较,气孔和夹渣缺陷少,产品内部质量好。
由于低压铸造利用压力充型和补充,大大简化了浇冒系统的结构,使金属液收得率大大提高,一般可达90%,而金属型重力铸造仅40%~60%。
目前低压铸造已成为铝轮毂生产的首选工艺、日本的丰田汽车公司、东京轻合金制作所、美国福特汽车公司等均采用此工艺生产铝轮毂,国内的铝合金轮毂制造企业多数也采用此工艺生产,现有数十家企业用低压铸造工艺生产铝合金汽车及摩托车轮毂。
低压铸造法的缺点是铸造时间较长、加铝料、换模具费时间、设备投资大、低压铸造机使用的升液管成本较高且易损坏。
5.离心铸造离心铸造是将液体金属注入高速旋转的铸型内,使金属液在离心力的作用下充满铸型和形成铸件的技术和方法。
离心力使液体金属在径向能很好地充满铸型并形成铸件的自由表面;不用型芯能获得圆柱形的内孔;有助于液体金属中气体和夹杂物的排除;影响金属的结晶过程,从而改善铸件的机械性能和物理性能。
优点是几乎不存在浇注系统和冒口系统的金属消耗,提高工艺出品率;生产中空铸件时可不用型芯,故在生产长管形铸件时可大幅度地改善金属充型能力,降低铸件壁厚对长度或直径的比值,简化套筒和管类铸件的生产过程;铸件致密度高,气孔、夹渣等缺陷少,力学性能高;便于制造筒、套类复合金属铸件,如钢背铜套、双金属轧辊等;成形铸件时,可借离心力提高金属的充型能力,故可生产薄壁铸件。
缺点是用于生产异形铸件时有一定的局限性。
铸件内孔直径不准确,内孔表面比较粗糙,质量较差,加工余量大;铸件易产生比重偏析,因此不适合于合金易产生比重偏析的铸件(如铅青铜),尤其不适合于铸造杂质比重大于金属液的合金。
所以不适合汽车轮毂的制造。
四、工艺方案1.零件图:2.浇注位置:为了保证铸件质量,必须把最重要的加工面在浇注时向下或直立状态。
由于零件内部安装轴承,尺寸精度比较高,因此,应将两圆柱面呈直立状态,同时从顺序凝固的原则出发,将厚大部位放在上面,以便于安放冒口,得到顺序凝固。
所以本件的浇注位置如图所示。
冷却位置与浇注位置一致。
3.分型面:如图所示铸件大部分在同一铸型内,能够保证其尺寸精度,下芯也便于检查,同时满足合箱,浇注,冷却位置一致,采用侧浇,切向引入改善了浇注时的充型不平稳,减少了冲击,防止了冲砂缺陷的产生,上、下箱相差不大,造型简单。
缺点是有一个砂芯复杂,要求高,模样加工困难。
4.砂芯:根据铸件结构和已选定的分型面,必用两个5.主要工艺参数的确定:根据实际生产情况,确定该件的收缩率为2%。
由于铸件的精度要求较高,确定该件的精度为Ⅰ级,尺寸偏差为±2.5mm,重量偏差8%。
按一级精度铸件并考虑实际情况,确定加工余量,具体数值见铸件工艺图。
按零件图尺寸采用增厚法,确定拔模斜度为1º30'-2º。
6.浇注系统:浇注系统由浇口杯、直浇道、横浇道和内浇道组成。
浇注系统截面积大小对铸件质量影响很大,截面积太小,浇注时间长,可能产生浇不足、冷隔、砂眼等缺陷;截面积过大,浇注速度快,又可能收起冲砂,带入熔潭和气体,使铸件产生渣孔、气孔等缺陷。
为了使金属液以适宜的速度充填铸型,就必须合理确定浇注系统的面积。
7.冒口:铸件法兰与轮毂体交接处形成热节,容易产生分散性的缩松,严重降低铸件的机械强度。