轮毂锻造工艺(全)
轮毂制造工艺

日本轮毂先进的制造工艺相信对于很多汽车消费者而言,轮毂基本上只有两种,那就是钢制轮毂和铝合金轮毂,而铝合金轮毂更好。
那么在铝合金轮毂之中,是否都是一样的?如果不是,那么哪一种才更好?更好的轮毂可以为您带来什么好处呢?今天我们就为您浅析一下不同的铝合金轮毂的种类,以及除铝合金轮毂之外,是否还有更好的产品?铝合金轮毂种类现在我们虽然知道了铝合金轮毂比钢轮毂更好,更适用于乘用车,但您知道铝合金轮毂也有不同的种类吗?从制造工艺上我们所见过的铝合金轮毂基本有三种,第一种是铸造,也就是绝大多数家用车或者部分豪华车所用。
另一种是锻造,多被用于高性能车、高级跑车,还有很多汽车轮毂改装品牌的高端产品也是锻造产品。
除上述两种原有的工艺之外,现在还有一种新的工艺形式,叫做MAT旋压铸造。
铸造铝合金轮毂铸造成型的铝合金轮毂是如何生产的呢,简单的说,是将被铸造的金属物质加热至液态,然后将极高温的液态金属倒入不同样子的铸模,然后再通过打磨、抛光等精加工来做出最终成品。
铸造一般分为两种,一种是重力铸造,另一种是低压铸造。
重力铸造是比较原始的铸造工艺,就是依靠铝水自身的重力倾注到铸模之中,铝水通过自身压力充满至整个铸模各个角落。
这种工艺的方法比较简单而且成本也更低,但产品质量可控性不高,并且容易出现瑕疵,在汽车轮毂制造业中几乎已经完全被低压铸造取代。
低压铸造顾名思义,就是将铝水通过设备施加压力灌注到铸模之中,铝水整个凝固过程都处在有一定压力的状态下。
这样的好处是铝水因为压力会产生更大的密度,凝固后成品的强度更高。
在造型比较复杂的铸模中也可以保证完全充满铸模,很多样式比较复杂的铸造铝合金轮毂只能通过低压铸造方式制造。
低压铸造的过程全部由机械完成,并且铸造成型的良品率高,非常适合大批量生产,所以目前汽车厂商指定的铸造铝合金轮毂都是由这种工艺生产出来的。
锻造铝合金轮毂锻造是一种比铸造更加高级的工艺,因为成品价格昂贵,所以一般的家用车甚至中高级车都不会采用锻造铝合金轮毂。
《7A04高强铝合金轮毂锻造成形工艺研究》范文

《7A04高强铝合金轮毂锻造成形工艺研究》篇一一、引言随着汽车工业的快速发展,轻量化、高强度和高耐久性的轮毂材料已成为市场的重要需求。
7A04高强铝合金以其优良的机械性能、加工性能和抗腐蚀性能,成为制造汽车轮毂的理想材料。
本文针对7A04高强铝合金轮毂的锻造成形工艺进行深入研究,探讨其成形过程中的关键技术和影响因素,以提高轮毂的成形质量和生产效率。
二、7A04高强铝合金的特性7A04高强铝合金是一种以铝为基础的合金,通过添加适量的合金元素(如铜、镁、锰等)提高其强度和耐腐蚀性。
该合金具有优良的加工性能、抗腐蚀性能和高强度,广泛应用于航空、航天、汽车等工业领域。
三、锻造成形工艺7A04高强铝合金轮毂的锻造成形工艺主要包括原材料准备、模具设计、锻造过程和后续处理四个部分。
(一)原材料准备选用合格的7A04高强铝合金锭料,进行熔炼、精炼和均匀化处理,以获得纯净、组织均匀的合金材料。
同时,对材料进行热处理,以提高其成形性能。
(二)模具设计根据轮毂的形状和尺寸要求,设计合理的模具结构。
模具应具有良好的强度、耐磨性和热稳定性,以保证锻造过程的顺利进行。
(三)锻造过程锻造过程包括预处理、成形和后处理三个阶段。
预处理阶段主要对合金材料进行加热和保温,使其达到理想的锻造温度。
成形阶段通过模具将材料锻造成预定形状的轮毂。
后处理阶段包括冷却、去毛刺和热处理等工艺,以提高轮毂的机械性能和表面质量。
(四)后续处理对锻造后的轮毂进行表面处理,如喷涂、氧化等,以提高其耐腐蚀性和美观度。
同时,对轮毂进行质量检测,确保其符合设计要求。
四、关键技术和影响因素(一)模具设计及制造技术模具的设计和制造是锻造成形工艺的关键环节。
模具的结构应合理、尺寸应准确,以保证轮毂的成形质量和生产效率。
同时,模具的材料和热处理工艺也应考虑周全,以提高模具的使用寿命和降低制造成本。
(二)锻造温度及变形速率控制锻造温度和变形速率对轮毂的成形质量和机械性能有重要影响。
锻造工艺说明

铸造工艺阐明铸造重要工艺路线:6061铝棒切割→铝棒加热→预锻→锻成型→冲扩工艺孔→旋压→热处理→机加工→气密动平衡,跳动检查→涂装→包装入库。
铸造铝轮毂具有强度高、抗蚀性好,尺寸精确、加工量小等长处,一般状况其重量仅相称于同尺寸钢轮旳1/2或更低某些。
铸造铝轮毂旳晶粒流向与受力旳方向一致,其强度、韧性与疲劳强度均明显优于铸造铝轮毂。
同步,性能具有很好旳再现性,几乎每个轮毂具有同样旳力学性能。
铸造铝轮毂旳经典伸长率为12%-17%,因而能很好旳吸取道路旳震动和应力。
一般铸造轮毂具有旳相称强旳随压缩力旳能力,但承受冲击、剪切与拉伸载荷旳能力则远不如铸造铝轮毂。
铸造轮毂具有更高旳强度重量比。
此外,铸造铝轮毂表面无气孔,因而具有很好旳表面处理能力,不仅能保证涂层均匀一致,结合牢固,并且色彩也好,铸造铝轮毂旳最大缺陷是生产工序多,生产成本比铸造旳高得多。
铸造由于工序较为复杂,因而制导致本较为高昂,但铸造轮毂在生产过程中由于铝块通过不停冲压,因此在成型之后,其分子构造会变旳非常紧密,因此可以承受较高旳压力,因而在相似尺寸相似强度下,铸造轮毂也比铸造轮毂质量更轻。
二,改装铸造轮毂旳好处1.安全性能铸造轮毂材料强度比铸造轮高30%左右,有数据为证铸造轮铸造轮硬度 125HB 85HB延伸率 17% 12%抗拉强度 370兆帕 280兆帕铸造轮毂订制根据客户车型设计加工,完美匹配车型数据,不使用任何附件,譬如垫片,转接盘,中心套环等,有效减少了由于附件损坏带来旳安全隐患2.外观由于铸造式轮毂构造紧密,能承受高应力,因此在造型设计上,它可以设计出某些比较活泼旳细条辐,设计旳自由度也高。
可以根据客户需求设计,更能适合客户汽车整体外观,使您旳爱车更具个性化。
2:铸造:铸造旳制造工艺旳轮毂性能最高,重量最轻,硬度最高。
不过价格也比较高。
A采用圆柱状设计,直径龠大旳轮毂就是用较粗旳铝材去锻压,与铸造铝圈毂使用\"原材料\'旳制造措施愈然不一样.B.根据铝毂宽度所需旳J数切割铝材.C.先将铝锭加热至摄氏430上下,此时便可以准备进行锻压.D.热锻压成型,吨数愈高旳锻压机所需旳铝锭工作温度较低,所铸造出来旳产品晶粒较小,韧度也较高.E.通过高温高压成型旳粗胚温度非常高,表面充满黑色碳化物,必须使用叉动机来搬运.而通过酸洗表面处理之后旳粗胚已经具有轮毂旳雏型.F.在T4及T6两种热处理机旳长时间再加工热处理后,粗胚旳晶粒将更紧实,产品旳韧度也会提高.G.铸造铝毂必须靠着机械加工,将粗胚加工至轮毂成型,因此工作内容包括胎唇成型,螺丝孔钻洞,盘面车削,细部加工等等环节.H.在涂装之前,必须在检查一次轮毂表面与否有瑕疵.铝分子构造:铸铝合金轮毂旳铝分子已经破坏,锻铝合金轮毂没有破坏.[重量].铸铝轮毂重量很重,锻铝轮毂重量极轻:15寸4.3公斤/16寸6公斤/17寸7公斤/18寸7.5公斤. 锻铝轮毂旳长处:1.强度高,重量轻,安全性高.2.节省燃油。
汽车轮毂轴承生产工艺
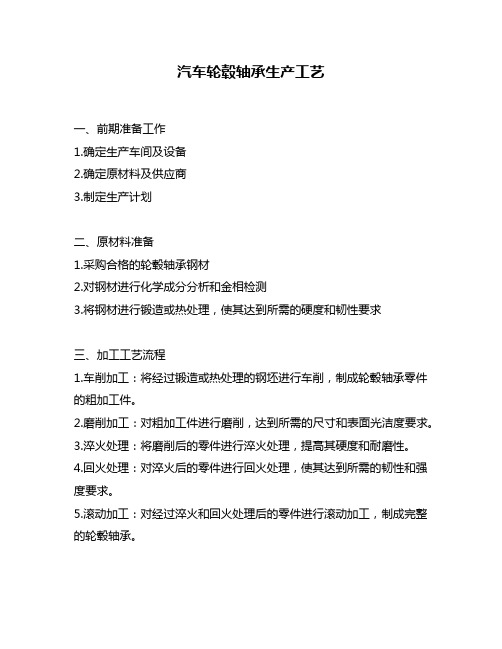
汽车轮毂轴承生产工艺
一、前期准备工作
1.确定生产车间及设备
2.确定原材料及供应商
3.制定生产计划
二、原材料准备
1.采购合格的轮毂轴承钢材
2.对钢材进行化学成分分析和金相检测
3.将钢材进行锻造或热处理,使其达到所需的硬度和韧性要求
三、加工工艺流程
1.车削加工:将经过锻造或热处理的钢坯进行车削,制成轮毂轴承零件的粗加工件。
2.磨削加工:对粗加工件进行磨削,达到所需的尺寸和表面光洁度要求。
3.淬火处理:将磨削后的零件进行淬火处理,提高其硬度和耐磨性。
4.回火处理:对淬火后的零件进行回火处理,使其达到所需的韧性和强度要求。
5.滚动加工:对经过淬火和回火处理后的零件进行滚动加工,制成完整的轮毂轴承。
四、检验及质量控制
1.采用金相显微镜等设备对零件进行金相检测,确保其组织均匀。
2.对零件进行尺寸、表面光洁度等质量检测,确保符合要求。
3.进行装配试验,确保轮毂轴承的性能符合要求。
五、包装及出厂
1.将轮毂轴承进行包装,防止受到损坏。
2.标注产品名称、型号、生产日期等信息。
3.按照客户要求进行发货。
六、设备清洁及维护
1.定期对车间设备进行清洁和维护。
2.对设备进行定期检修和更换易损件。
七、安全生产措施
1.建立安全生产责任制度和管理制度。
2.加强员工培训,提高安全意识。
3.对生产过程中的危险因素进行评估和控制。
以上是汽车轮毂轴承生产工艺的详细步骤。
在实际生产中,还需要根据具体情况不断优化工艺流程和质量控制措施,以确保产品的质量和稳定性。
汽车轮毂加工方法与工艺分析

本文以深槽轮辋为例,阐述兼具使用性能优点和加工成本优势的压力成形制造工艺。
通过分析轮毂的材料、结构及加工方法,详细介绍了轮辋生产过程及所用装备,并展望未来生产技术的特点和发展方向。
1 序言汽车作为现代化的交通工具,其数量越来越多。
车轮是汽车必须的、基本的和重要的部件,其安全性、经济性及外观质量是目前使用者关注的主要指标。
不同车辆的轮毂结构不同、材料不同,其加工工艺也不相同。
通过分析车辆轮毂常使用的材料及加工方法,着重介绍具有深槽结构的家用汽车铝合金轮毂加工工艺及其特点。
2 汽车轮毂的材料及制造现状2.1 轮毂结构与材料轮毂是汽车支撑轮胎的圆形结构,由轮辋和轮辐组成,轮辋和轮辐可以是整体式的、永久联接式的和可拆卸式的。
轮辋常使用的结构有深槽轮辋和平底轮辋,并在此结构上有不同的改进,比如对开式轮辋、半深槽轮辋、平底宽轮辋及全斜底轮辋,用于不同的场合。
深槽轮辋如图1所示,断面中部呈凹槽形,有凸缘结构,用于安放轮胎,肩部向中间倾斜4°~6°。
该结构简单,刚度大,质量较小,对于尺寸小、弹性大的轮胎安装比较方便,因此适用于轿车及轻型越野车。
平底轮辋是货车常用的结构形式。
图1 深槽轮辋常见的汽车轮毂有钢质轮毂和铝合金轮毂。
钢质轮毂强度高,常用于大型载货汽车,质量较重;铝合金轮毂质量相较要轻很多,相同体积的铝合金轮毂比钢质轮毂轻2/3左右,符合如今低碳的使用理念,且导热快,散热性能好。
图2永久联接式轮毂结构2.2 轮毂常用加工方法目前铝合金轮毂的生产方法有铸造法、锻造法、冲压法和旋压法。
我国铝合金轮毂仍然以低压铸造为主,随着技术的发展,其加工工艺不断进行变革。
铝合金的铸造工艺主要有4种:重力铸造、低压铸造、反压铸造和挤压铸造。
大部分的铝合金车轮采用低压铸造生产,这是铝合金车轮铸造工艺中的主要技术。
铸造车轮需要准备铸型,熔炼金属,浇筑冷却凝固成形后取出铸件,工序多、设备大,产品容易出现缩孔、缩松等质量缺陷,特别是铸件尺寸较薄的情况下,更容易出现质量问题。
汽车轮毂轴管锻造余热淬火工艺研究
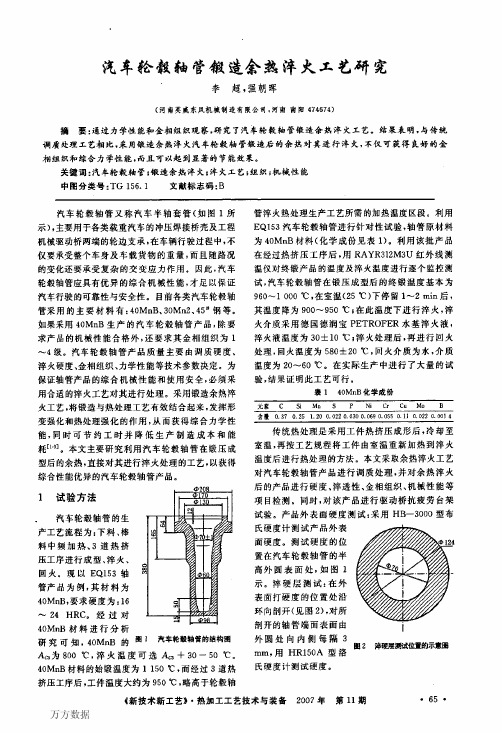
性及低摩擦系数“13等一系列的优异性能,多年来一 膜的沉积速率;另外,实验中还通过摩擦磨损仪对薄
直是国内外学者研究的热点,并且在精密仪器、光学 膜的机械性能进行了研究。
部件及宇宙导航领域有着广泛的应用前景E4 S]。 类金刚石薄膜通常分为2种,即含氢类金刚石
1试验部分
薄膜和无氢类金刚石薄膜。含氢的类金刚石薄膜主
了薄膜的沉积速率;另外,试验中还利用摩擦磨损仪对薄膜的机械性能进行了研究。试验结果表明,制备 的DLC薄膜比较致密均匀,粗糙度为8.1 nm,有较好的耐磨性能。
关键词:石墨;空。阴极等离子体放电;无氢DLC薄膜
中图分类号:TG 139.8
文献标志码:A
由于类金刚石(DLC)薄膜具有高硬度、高耐磨 分析了薄膜的表面形貌;通过表面轮廓仪测量了薄
距离为25 mm。用机械泵将真空室气压抽至8 Pa,
纯度为99.99%的Ar为辅助气体,用高纯石墨
然后向真空室通人Ar至20 Pa,换气5 min。之后,
(99.99%)为电极,利用空心阴极等离子体放电法在
减小Ar流量,使真空室气压稳定在20 Pa。将直流
载玻片上成功地制备了类金刚石薄膜。通过激光拉 稳压电源电压升高到500 V,空心阴极筒内产生明
其温度降为900~950℃;在此温度下进行淬火,淬 火介质采用德国德润宝PETROFER水基淬火液,
淬火液温度为30士10℃}淬火处理后,再进行回火
处理,回火温度为580土20℃,回火介质为水,介质
温度为20~60℃。在实际生产中进行了大量的试
验,结果证明此工艺可行。
表1 40MnB化学成份
元素 C
外圆竺向T内侧每苎,:圈2潮嘱籼的示意图
mm,用HRl50A型洛。 氏硬度计测试硬度。
旋压轮毂制造过程
旋压轮毂制造过程
旋压轮毂是指利用金属板材经过多次冷压成型、成形而成的轮毂。
旋压轮毂生产过程分为以下几个步骤:
1. 制备原材料
旋压轮毂的原材料一般为钢板或铝板,生产前要对原材料进行切割、修整等加工处理,以确保原材料符合生产要求。
2. 压花成形
将原材料经过预处理后,放入轮毂成形机进行轮毂成形的第一步——压花成形。
将金属板材置于旋压成形机上,利用压力和模具对金属板材进行加工,使得轮毂表层产生纹路、沟槽等花纹,增加轮毂的美观度和摩擦力。
3. 半成型
经过压花成形后,轮毂表面产生了纹路和凹凸不平的情况。
此时需要进行半成型,通过特殊的金属加工工艺,使轮毂表面趋于光滑,易于后续的成型处理。
4. 旋压成型
经过半成型,金属板材经旋转并不断受力变形,最终形成圆周不一的几何形状。
整个过程需要调整旋转速度、压力大小等加工参数,以确保各部位成形程度统一。
5. 车削、磨削
经过旋压成型后,对于一些工艺要求较高的轮毂,还需要进行车削和磨削。
这是为了削除成品表面缺陷,提高表面质量和尺寸精度。
6. 轮毂裁剪
最后,将成型好的轮毂裁剪成合适的尺寸和形状,以便更好地适应不同车型和车辆行驶条件。
在整个旋压轮毂的制造过程中,需要严格控制各个制造工序的质量,以确保轮毂的强度、耐久性、质量等组合指标符合要求。
同时要选用合适的金属材料、采用高效率的机器设备,进一步提高轮毂的质量和生产效率。
汽车轮毂制造工艺
汽车轮毂制造工艺
汽车轮毂是汽车的一个重要零部件,它直接与轮胎接触并支撑汽
车的重量。
汽车轮毂制造工艺的质量直接影响到汽车行驶的安全和舒
适性,因此汽车轮毂的制造工艺十分重要。
首先,汽车轮毂制造的第一步是用沙模或金属模制作模具。
模具
的质量直接决定了轮毂的精度和质量,因此制作模具时必须要保证其
精度和质量。
接下来,制作轮毂前需要选用合适的轮毂材料,现在常用的材料
有铝合金、镁合金和锻钢等。
不同的材料具有不同的特点和适用范围,需要根据不同的车型和使用环境来选择适合的材料。
然后,根据模具设计与材料特性,选择合适的制造工艺方法,通
常有铸造、锻造和旋压等方法。
其中铸造是最常用的制造方法,根据
设计需要,将熔化的金属浇入模具中,冷却后将轮毂取出,并经过后
续的加工、调整和表面处理等工序制成成品。
在制造过程中,还需要对轮毂进行加工和处理,包括车削、磨削、机加工、表面处理和质量检查等环节。
其中质量检查是制造过程中最
重要的一个环节,只有确保质量的稳定和可靠,才能保障车辆行驶的
安全和可靠。
最后是轮毂的装配,将制造好的轮毂安装到汽车上,并针对其大小、尺寸和安装方式进行调整和校准,确保其符合设计要求和实际使
用情况,实现最佳的行驶性能。
总体来说,汽车轮毂制造工艺是一个复杂、系统的过程,需要严
格控制各个环节的质量和精度,以确保轮毂的稳定性和可靠性。
在未来,随着科技的不断发展和创新,汽车轮毂的制造工艺也将不断完善
和提高,以适应日益严格的市场需求和更加安全、舒适的技术标准。
汽车轮毂生产工艺
汽车轮毂生产工艺
汽车轮毂生产工艺分为铸造工艺、塑性加工工艺以及热处理工艺三个主要工艺环节。
首先是铸造工艺,铸造工艺是轮毂生产中最基础、最关键的工艺环节。
铸造工艺主要分为砂型铸造和压铸两种方式。
砂型铸造是一种传统的铸造方式,通过制作铁质砂型,将液态金属浇注到砂型中,经过凝固和冷却后,获得轮毂的基础形态。
而压铸则是将液态金属压入金属模具中进行成型,相比砂型铸造更加精细和高效。
在铸造工艺中,还需要进行砂型制作、充型、冷却、脱脆等环节,以确保轮毂的成型质量。
其次是塑性加工工艺,塑性加工工艺是对轮毂进行精细加工和成型的过程。
主要包括锻造和旋压两种方式。
锻造是将加热的金属料通过锻压设备,使其在一定的模具中受到压力和变形,最终获得所需的形状和尺寸。
旋压则是通过旋转和挤压的方式,将金属料塑成圆形的轮毂。
塑性加工工艺可以使轮毂具有更好的强度和耐久性,并且提高轮毂的整体质量。
最后是热处理工艺,热处理工艺主要通过对轮毂进行加热、保温和冷却等过程,以改变轮毂的组织结构和性能。
热处理工艺主要包括退火、淬火和回火等方式。
通过不同的热处理工艺,可以改变轮毂的硬度、强度、韧性和耐磨性等性能,以提高轮毂在使用过程中的性能和寿命。
综上所述,汽车轮毂的生产工艺包括铸造工艺、塑性加工工艺
和热处理工艺等环节。
通过这些工艺的精心设计和操作,可以生产出具有良好性能和质量的轮毂产品。
轮毂锻造工艺(全)
毂。
此后,便是钢轮毂和铝合金轮毂并驱 的时代。
关 于 材料
1,钢质轮 毂
1)钢轮毂的用钢是16Mn,16Mn叫低 合金高强度结构钢
低合金高强度结构钢:含碳量为0.1%0.25%,加入主要合金元素锰、硅、钒、
铌和钛等 2)钢制轮毂的优点: 制造工艺简单,成本相对较低,而且 抗金属疲劳的能力很强,也就是我们俗称 的便宜又结实。具有良好的综合力学性能、 低温冲击韧性、冷冲压、切削加工性、焊
游标 卡尺
车:
6 粗车阶梯面
半精车阶梯面
立 式 专用夹 车刀 游 标
倒角
车床 具
卡尺
车:
7 粗车下端面。
粗车下端面四分之一圆弧 立 式 专用夹 车 刀 游 标
半精车下端面
车床 具
( 陶 瓷 卡尺
半精车下端面四分之一圆
刀具)
弧
倒角。
车:
保证:表面与轴心
切断面
立 式 专 用 夹 车刀
激 光 垂直度
车床 具
铝轮毂锻造工 艺
(全)
轮 毂 的 故 事
轮 毂 的 历 史
汽车的轮毂最开始是继承马车的轮毂 而来。
1886年,世界上生产出的第一个轮 毂是由钢材制成。
20世纪30年代,德国人将钢制辐条 与铝质轧制轮辋相结合的车轮装载气车 上,为铝合金车轮的发展奠定了基础。
二战后,铝合金轮毂开始在普通汽车 上得到应用。
减少了油耗。 合金材质的导热性能又是钢的三倍左右,散热 性好,对于车辆的制动系,轮胎和制动系统的热衰减
2)铝合金轮毂一般用6061 铝合金, A365.2铝合金。 a)6061铝合金
- 1、下载文档前请自行甄别文档内容的完整性,平台不提供额外的编辑、内容补充、找答案等附加服务。
- 2、"仅部分预览"的文档,不可在线预览部分如存在完整性等问题,可反馈申请退款(可完整预览的文档不适用该条件!)。
- 3、如文档侵犯您的权益,请联系客服反馈,我们会尽快为您处理(人工客服工作时间:9:00-18:30)。
此后,便是钢轮毂和铝合金轮毂并驱的时代。
精品课件
关 于 材料
精品课件
1,钢质轮毂
1)钢轮毂的用钢是16Mn,16Mn叫低合金高强度结构钢 低合金高强度结构钢:含碳量为0.1%-0.25%,加入主要 合金元素锰、硅、钒、铌和钛等
觉效果好。 在高速转动时的变形小,惯性阻力小,有利于提高汽车的直线行驶性能,减轻轮胎滚
动阻力,从而减少了油耗。 合金材质的导热性能又是钢的三倍左右,散热性好,对于车辆的制动系,轮胎和制动
系统的热衰减都能起到一定的作用。
b)缺点:制造工艺复杂,成本高。
精品课件
2)铝合金轮毂一般用6061 铝合金,A365.2铝合金。
精品课件
1)工序
工序 号
1 2
工序名称
备料 锻造毛坯
设备名称及编 夹辅具及编号 切 削 工 具 量具及编号
号
及编号
3
退火
镗: 工位1:粗镗轴承孔 Ф69。 4 工位2:粗镗轴承孔 Ф70。 工位3:粗镗轴承孔 Ф71。 工位3:粗镗轴承孔 Ф72。 工位4:半精镗轴承孔 Ф72.4。 工位5:半精镗轴承孔 Ф72.5。
a)6061铝合金 经热处理预拉伸工艺生产的高品质铝合金产品,韵贤金属特性多,具有加工性能
极佳、优良的焊接特点及电镀性、良好的抗腐蚀性、韧性高及加工后不变形、材料致密无 缺陷及易于抛光、上色膜容易、氧化效果极佳等优良特点。
力学性能 6061的极限抗拉强度为124 MPa 受拉屈服强度 55.2 MPa 延伸率25.0 % 弹性系数68.9 GPa 弯曲极限强度228 MPa Bending Yield Strength 103 MPa 泊松比0.330 疲劳强度 62.1 MPa
立式车床 专用夹具 车刀
游标卡尺
立式车床 专用夹具 车刀(陶 游标卡尺 瓷刀具)
精品课件
2,合金轮毂
1)合金轮毂: 镁和铝是最适宜制造车轮的理想轻合金材料。
它有着传统钢车轮所无法比拟的许多优点,更 能适应整车高速化、节能化、现代化高档次发展的需 要。
尤其是镁合金有着极高的比强度、疲劳强度和 比弹性模量。是极为理想的车轮制造材料。使用镁合 金制造的车轮具有极佳的减震性能。
a)优点: 合金材质轮毂可以弥补钢质轮毂的缺点,较轻的重量,惯性阻力小,制作精度高,视
铝轮毂锻造工艺 (全)
精品课件
轮毂 的 故事
精品课件
轮毂 的 历史
精品课件
汽车的轮毂最开始是继承马车的轮毂而来。
1886年,世界上生产出的第一个轮毂是由钢材制 成。
20世纪30年代,德国人将钢制辐条与铝质轧制轮 辋相结合的车轮装载气车上,为铝合金车轮的发展奠 定了基础。
二战后,铝合金轮毂开始在普通汽车上得到应用。
3,热处理:
1)提高铸件的力学性能,改善合金的切削性能;消除内应力;稳定铸件的尺寸 和组织,改善合金的组织和力学性能。 2)本工序控制要点:退火时间和温度(60-85℃,3min)。
精品课件
4,机加工流程
1)数控机床加工工序划分的特点为:先粗后精,先面后孔,刀具集中 。 2)加工顺序: 按由内到外、又粗到精、由近到远的原则确定。毛坯——孔加工粗加工——孔半精加工— —孔精加工——外圆面加工——外圆面半精加工——阶梯面粗加工——阶梯面半精加工— —内圆加工——退刀面加工——不规则孔加工——型孔加工——气门孔加工——去毛刺— —零件最终热处理——清洗——终检 重点控制项目:中心孔直径、PCD位置度、端径跳、动平衡。
精镗
镗床
专用夹具
精品课件
镗刀
塞规
备注
阶梯面(靠近内 圆)足够加工余 量
保证:轴承孔 Ф72.5表面粗 糙度为R1.6,上 极限为-0.028, 下极限为-0.058。
车:
工位1:粗车上端面。
5 工位2:粗车上端面四分之一圆弧。
工位3:半精车上端面。
工位4:半精车上端面四分之一圆弧。
工位5:半精车外圆。
精品课件
3)A356.2合金锭
a) 性能与特点: 具有流动性好,无热裂倾向,线收缩小,
气密性好等良好的铸造性能,比重小,耐蚀性良 好,易气焊,随铸件壁厚增加强度降低的程度小, 铸态下使用,变质后机械性能提高。 铸锭断口致 密,无熔渣和非金属夹杂物。
精品课件
结构 结 构
精品课件
精品课件
1,轮毂的结构
1)轮毂技术要求: 孔与外圆一般具有 较高的同轴度要求; 端面与孔轴线的垂 直度要求;内孔表 面本身的尺寸精度、 形状精度及表面粗 糙度要求;外圆表 面本身的尺寸、形 状精度及表面粗糙 度要求等。
精品课件
台阶面
2) 轮毂零件组成: 外圆表面,
内圆表面, 型孔,中心孔, 台阶面, 退刀槽, 内、外倒角, 气门孔。
2)钢制轮毂的优点: 制造工艺简单,成本相对较低,而且抗金属疲劳
的能力很强,也就是我们俗称的便宜又结实。具有良好 的综合力学性能、低温冲击韧性、冷冲压、切削加工性、 焊接性能等,
3)钢质轮毂的缺点: 外观丑陋(可以说没什么外观可言),重量较大
(相同的轮毂钢材质要比铝合金材质重很多),惯性阻力 大,散热性也比较差,而且非常容易生锈。
台阶面
轮毂结构组成: 外圆表面, 内圆表面, 型孔,中心孔, 台阶面, 退刀槽, 内、外倒角, 气门孔。
内圆表面
精品课件
外圆表面
型孔 中心精品课件
3,审美
精品课件
4,轮毂受力
结构决定造型,结构决定受力,轮毂受力主要在轮辐上
精品课件
加 工工 艺
精品课件
1,加工结构及技术要求
退刀槽 内圆表面
精品课件
外圆表面
型孔 中心孔 外倒角
2,加工流程
胚料
锻造
热处理
喷涂
精品课件
机加工
1)进料与切料: 铝棒材质为6061,将铝棒切 割成锻造轮毂所需的大小。
精品课件
2)锻压成胚: 以超过8000吨的锻压机 将预热的铝材,以锻压 方式,锻压成毛胚(保 留加工余量)。
精品课件
精品课件
立式车床 专用夹具
车刀
保证:上极限为0,下极 限为-0.6。
游标卡尺
车: 6 粗车阶梯面
半精车阶梯面 倒角 车: 7 粗车下端面。 粗车下端面四分之一圆弧 半精车下端面 半精车下端面四分之一圆弧 倒角。 车: 切断面
铣:粗铣上端面不规则孔。 8 精铣上端面不规则孔。
9 钻:钻4 xФ12 孔 钻4 xФ12.5孔 攻螺纹。