机械制造工艺ppt 3第三章 机械加工表面质量
机械加工工艺基础课件中南大学完整版321页PPT

于基准之间位置的准确度。
02.04.2020
2.1 加 工 精 度
• 国家标准规定:常用的精度等级分为20级, 分别用IT01、IT0、IT1、IT2…IT18表示。 数字越大,精度越低。其中IT5-IT13常用。
2.4零件的加工精度与表面粗糙度的关系
提问
零件的加工精度与表面 粗糙度的关系如何?
• 精度:宏观几何参数的误差 • 表面粗糙度:微观几何参数的误差 • 加工精度高,必须采用一系列的高精度的加工方法,而
经过高精度的加工后零件表面粗糙度一定低,反之,表 面粗糙度低,零件必须采用一系列的降低表面粗糙度的 加工方法,而低表面粗糙度的加工方法不一定是高精度 的加工方法。 • 实例:各种机床上的手柄:表面粗糙度非常低,但精度 不高。
中南大学 Central South University
机械加工工艺基础
中南大学 工业训练中心
索引
第一章.切削加工的基础知识 第二章.金属切削机床 第三章.机械加工工艺过程 第四章.零件表面的加工方案 第五章.零件的结构工艺性 第六章.数控加工技术
第一章
切削加工的基础知识
返回索引
1.1 钳工与机械加工
02.04.2020
3.切削运动与切削用量
机器零件的基本表面包括:外圆、内圆 (孔)、平面和成型面
基本表面主要由如下的加工方法获得
3.1 切削运动
要完成零件表面的切削加工,刀具和 工件应具备形成表面的基本运动,即切削 运动
IT7~IT 6 IT5~IT2
Ra值范围 (μm) 25~12.5 6.3~3.2
机械加工质量培训课件PPT(共 104张)

2.1 机械加工精度
i工 机件 (蜗 床杆 丝) 杆 PP螺 1螺 ZZ距 距 21ZZ34
例1. 在公制车床上车模数为2mm蜗杆时,挂轮计算式为 :
z1 z2
z3 z4
P(P机 (1 床 蜗丝 杆杆 螺螺 距距 )) ,若P=6mm,
Z 1 1,1 Z 2 0 7,Z 0 3 8,Z 0 4 1,2 求加0 工后蜗杆螺距
误差是多少?
i
P1=2
P=6
解: i工 机件 (蜗 床杆 丝) 杆 PP螺 1螺 ZZ距 距 21ZZ34 P ห้องสมุดไป่ตู้iP Z Z2 1Z Z3 4P1 71 0 2 800 066.2857
1)主轴回转误差。 纯径向跳动误差 轴向窜动误差 纯角度摆动误差
①主轴纯径向跳动误差对加精度的影响。 产生的主要原因:主轴支承轴颈的圆度误差、轴承工作表面的
圆度误差等。 a. 切削力F的作用方向不变(见图2-5 车外圆的情形)
2
R
1
3
R3
R1 △R
o o′
理论位置
实际位置
R
4
车外圆时它使加工面产生圆度和圆柱度误差。
@加工质量与设备、工艺方法、工艺措施有关。
2.1 机械加工精度
2.1.1 概述 1、机械加工精度(简称加工精度):是指零件在机械加工后
的几何参数(尺寸、几何形状和表面间相互位置)的实际值和理 论值相符合的程度。
2、加工误差:实际参数与理论参数的差值
2.1 机械加工精度
2.1.2 影响加工精度的因素及其分析 在机械加工中,零件的尺寸、几何形状和表面间相互位置的
机械制造工艺学(王先逵)第三章参考答案(部分)

3-1 机械加工表面质量包括哪些具体内容?机械加工表面质量,其含义包括两个方面的内容:1.加工表面层的几何形貌主要由以下几部分组成:⑴表面粗糙度;⑵波纹度⑶纹理方向⑷表面缺陷2.表面层材料的力学物理性能和化学性能表面层材料的力学物理性能和化学性能主要反映在以下三个方面:⑴表面层金属冷作硬化;⑵表面层金属的金相组织变化;⑶表面层金属的残余应力。
3-2为什么机器零件一般总是从表面层开始破坏的?加工表面质量对机器使用性能有哪些影响?一、机器零件的损坏,在多数情况下都是从表面开始的,这是由于表面是零件材料的边界,常常承受工作负荷所引起的最大应力和外界介质的侵蚀,表面上有着引起应力集中而导致破坏的微小缺陷,所以这些表面直接与机器零件的使用性能有关。
二、加工表面质量对机器的耐磨性、耐疲劳性、耐蚀性、零件配合质量都有影响(一)表面质量对耐磨性的影响1.表面粗糙度、波纹度对耐磨性的影响表面粗糙度值越小,其耐磨性越好;但是表面粗糙度值太小,因接触面容易发生分子粘接,且润滑液不易储存,磨损反而增加;因此,就磨损而言,存在一个最优表面粗糙度值。
2.表面纹理对耐磨性的影响圆弧状、凹坑状表面纹理的耐磨性好;尖峰状的表面纹理由于摩擦副接触面压强大,耐磨性较差。
在运动副中,两相对运动零件表面的刀纹方向均与运动方向相同时,耐磨性较好;两者的刀纹方向均与运动垂直时,耐磨性最差3.冷作硬化对耐磨性的影响加工表面的冷作硬化,一般都能使耐磨性有所提高。
(二)表面质量对耐疲劳性的影响1.表面粗糙度对耐疲劳性的影响表面粗糙度值越小,表面缺陷越少,工件耐疲劳性越好2.表面层金属的力学物理性质对耐疲劳性的影响表面层金属的冷作硬化能够阻止疲劳裂纹的生长,可提高零件的耐疲劳强度。
(三)表面质量对耐蚀性的影响1.表面粗糙度对耐蚀性的影响表面粗糙度值越大,耐蚀性能就越差。
2.表面层金属力学物理性质对耐蚀性的影响表面层金属力学物理性质对耐蚀性的影响当零件表面层有残余压应力时,能够阻止表面裂纹的进一步扩大,有利于提高零件表面抵抗耐蚀的能力。
机械加工表面质量
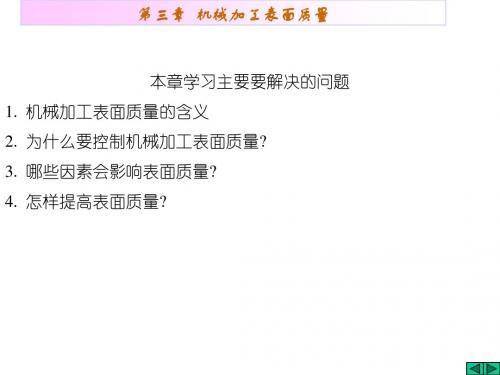
2.表面层物理 力学、化学性能
(1)表面粗糙度 (2)表面波度 (3)纹理方向 (4)伤痕——表面上一些个别位置 上出现的缺陷
(1)表面层加工硬化(冷作硬化)。 (2)表面层金相组织变化。
(3)表面层产生残余应力。
第一节 加工表面质量及其对使用性能的影响
第一节 加工表面质量及其对使用性能的影响
影响表层残余应力的因素
三、表层金属的残余应力——拉应力或者压应力
(一)残余应力产生的原因 1)冷塑性变形——使表层产生压缩残余应力,里层产生拉伸 残余应力。
原因:加工表面受刀具或砂轮磨粒的挤压和摩擦,产生拉伸塑性变形 ,此 时里层金属处于弹性变形状态,切削后里层金属趋于弹性恢复,但受 到已产生塑性变形的表层金属牵制
第三章 机械加工表面质量
本章学习主要要解决的问题 1. 机械加工表面质量的含义 2. 为什么要控制机械加工表面质量? 3. 哪些因素会影响表面质量? 4. 怎样提高表面质量?
第三章 机械加工表面质量
第一节 加工表面质量及其对使用性能的影响
一、机械加工表面质量的含义
1.表面的几何特征
2)热塑性变形——表层产生拉伸残余应力,里层产生压缩残 余应力。
原因:切削和磨削过程中,表层的温度比里层高,表层的热膨胀较大;加 工后零件冷却至室温时,表层金属体积的收缩受到里层的牵制。
影响表层残余应力的因素
3)相变引起的体积变化 金相组织的变化引起表层金属的比容增大,则表层金属将产生 压缩残余应力,而里层金属产生拉伸残余应力; 金相组织的变化引起表层金属的比容减小,则表层金属产生拉 伸残余应力,而里层金属产生压缩残余应力 。
• 提高砂轮速度,降低工件转速,减小纵向进给速度——增大单位面 积的磨粒数
机械加工质量分析PPT31页

零件的耐腐蚀性在很大程度上取决于表面粗糙度。表面粗糙度值 越大,越容易积聚腐蚀性物质,凹谷越深,渗透与腐蚀作用越强烈。 故减小表面粗糙度值,可提高零件的耐蚀性。此外,残余压应力使零 件表面紧密腐蚀性物质不易进入,可增强零件的耐蚀性。
4.表面质量对配合性质的影响
在间隙配合中,如果配合表面粗糙,则在初期磨损阶段由于配合 表面迅速磨损,使配合间隙增大,改变了配合性质。在过盈配合中, 如果配合表面粗糙,则装配后表面的凸峰将被挤压,而使有效过盈量 减少,降低了配合强度。
➢ 解决办法是在工件和电磁吸盘之间垫入一薄橡皮
(0.5mm以下)。当吸紧时,橡皮被压缩,工件变形减小,
经几次反复磨削逐渐修正工件的翘曲,将工件磨平。
2021/9/23
13
4.1 机械加工精度
4.1.8 工艺系统受热变形引起的加工误差 1.工艺系统的热源 (1)内部热源:切削热 、摩擦热、派生热源 (2)外部热源:环境温度、热辐射 2.工艺系统的热平衡
2021/9/23
24
4.2 机械加工表面质量
4.2.3 影响表面粗糙度的因素 1. 切削加工中影响表面粗糙度的因素 (1)几何因素 (2)物理因素
➢ 积屑瘤 ➢ 刀具表面对工件表面的挤压与摩擦 ➢ 工件材料性质
2021/9/23
25
4.2 机械加工表面质量
2. 磨削加工中影响表面粗糙度的因素
(1)磨削用量砂轮速度对表面粗糙度的影响较大,提高有利于降低表 面粗糙度。磨削深度与进给速度增大时,将使工件表面塑性变形加剧, 因而使表面粗糙度值增大。
4.1 机械加工精度
• 教学重点:
– 掌握机械加工精度的概念; – 掌握获得加工精度的方法; – 掌握影响加工精度的因素; – 掌握提高加工精度的工艺措施
第三章外圆表面加工
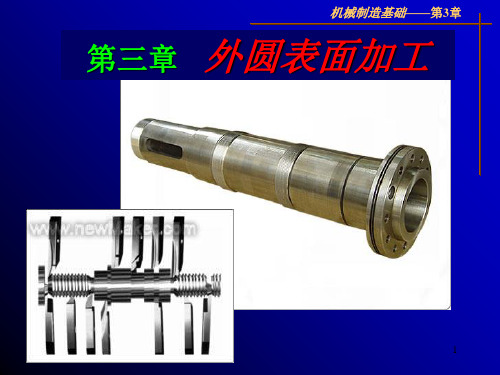
2021/3/15
13
2021/3/15
外圆磨削方式
14
• 提问:
上述中心磨削法是以轴的中心孔作定位基 准,它是怎样使该轴旋转的?在上图中 代表什 么?
2021/3/15
15
2021/3/15
16
• 问题
车削细长轴时,常采用哪些措施增加工件的刚性,提 高加工质量?
2021/3/15
17
答:
支承刚度好,刚度差的工件也可采 用较大的切削用量进行磨削
2021/3/15
25
容易实现工艺过程的自动化
前工序的形状误差会影响磨削的加工精 度,且不能改善加工表面与工件上其它表 面的位置精度,并有一定的棱圆度误差产
生,圆度误差一般不小于0.002mm
所能加工的工件有一定局限,不 能磨带槽的, 其加工余量很大且不均匀,荒车 可以切除大部分余量,减少其形 状和位置偏差,为保证后续加工 的加工精度作准备
粗车
2021/3/15
中小型铸锻件可直接进行粗车
粗车的主要任务是采用较大的背吃 刀量、较大的进给量和中等切削速 度,迅速切除毛坯上多余的金属层, 尽可能提高生产率
2021/3/15
18
2021/3/15
19
2021/3/15
20
• 问题:
磨削为什么能加工淬硬的材料?为什么磨削工件的 精度高、表面粗糙度低?
2021/3/15
21
答:
因为
1)磨床的结构刚性好;
2)砂轮切入运动机构可以精密调节,因而可精密控制切削 深度ap ;
3)砂轮的磨粒微细、锐利、分布稠密且高速运动,每一磨 粒只从工件表面切下极薄的一层切屑。
2021/3/15
机械加工表面质量

第三章机械加工表面质量第一节概述评价零件是否合格的质量指标除了机械加工精度外,还有机械加工表面质量。
机械加工表面质量是指零件经过机械加工后的表面层状态。
探讨和研究机械加工表面,掌握机械加工过程中各种工艺因素对表面质量的影响规律,对于保证和提高产品的质量具有十分重要的意义。
一机械加工表面质量的含义机械加工表面质量又称为表面完整性,其含义包括两个方面的内容:1.表面层的几何形状特征表面层的几何形状特征如图3-1所示,主要由以下几部分组成:⑴表面粗糙度它是指加工表面上较小间距和峰谷所组成的微观几何形状特征,即加工表面的微观几何形状误差,其评定参数主要有轮廓算术平均偏差R a或轮廓微观不平度十点平均高度R z;⑵表面波度它是介于宏观形状误差与微观表面粗糙度之间的周期性形状误差,它主要是由机械加工过程中低频振动引起的,应作为工艺缺陷设法消除。
⑶表面加工纹理它是指表面切削加工刀纹的形状和方向,取决于表面形成过程中所采用的机加工方法及其切削运动的规律。
⑷伤痕它是指在加工表面个别位置上出现的缺陷,如砂眼、气孔、裂痕、划痕等,它们大多随机分布。
2.表面层的物理力学性能表面层的物理力学性能主要指以下三个方面的内容:⑴表面层的加工冷作硬化;⑵表面层金相组织的变化;⑶表面层的残余应力。
二表面质量对零件使用性能的影响1.表面质量对零件耐磨性的影响零件的耐磨性是零件的一项重要性能指标,当摩擦副的材料、润滑条件和加工精度确定之后,零件的表面质量对耐磨性将起着关键性的作用。
由于零件表面存在着表面粗糙度,当两个零件的表面开始接触时,接触部分集中在其波峰的顶部,因此实际接触面积远远小于名义接触面积,并且表面粗糙度越大,实际接触面积越小。
在外力作用下,波峰接触部分将产生很大的压应力。
当两个零件作相对运动时,开始阶段由于接触面积小、压应力大,在接触处的波峰会产生较大的弹性变形、塑性变形及剪切变形,波峰很快被磨平,即使有润滑油存在,也会因为接触点处压应力过大,油膜被破坏而形成干摩擦,导致零件接触表面的磨损加剧。
机械制造技术ppt课件(完整版)

机械制造技术课件
汇报人:
目录
01 02 03 04 05 06
机械制造概述 传统机械制造技术 现代机械制造技术 机械制造工艺流程 机械制造质量控制 机械制造的未来发展
01
机械制造概述
机械制造的定义
机械制造是将原材料转化为成品的生产过程。 机械制造包括产品设计、工艺设计、加工制造、检测和质量控制等环节。 机械制造广泛应用于各个领域,如航空、汽车、机床等。 机械制造的核心目标是提高生产效率、降低成本、保证产品质量。
05
机械制造质量控制
质量控制的方法
统计过程控制 测量系统分析 过程能力分析 质量改进方法
质量检测的步骤
检测计划制定 检测工具准备 样品选择与制备 检测数据记录与分析
质量问题的解决
确定问题:明确机械制造过程中出现的质量问题
分析原因:分析问题产生的原因,如材料、工艺、设备等
制定措施:根据分析,制定相应的解决措施,如改进工艺、更换材料、 调整设备等 实施方案:按照制定的措施实施方案,并对实施过程进行监控和调 整
精密加工技术
定义:使用精密机床和精细加工刀具进行加工 分类:超精加工、镜面加工、纳米加工等 应用:航空航天、医疗器械、光学仪器等领域 发展趋势:高精度、高效率、智能化
04
机械制造工艺流程
零件的定位与装夹
定位原理:六点 定位原理,限制 工件的自由度
装夹方法:如三 爪卡盘、四爪卡 盘等,固定工件
定位元件:如V 形块、定位销等, 限制工件的自由 度
焊接工艺及 设备
焊接种类及 特点
焊接应用及 发展
切削加工技术
定义:利用切削 工具从工件上切 除多余材料的加 工方法
分类:车削、铣 削、钻孔、刨削、 磨削等
- 1、下载文档前请自行甄别文档内容的完整性,平台不提供额外的编辑、内容补充、找答案等附加服务。
- 2、"仅部分预览"的文档,不可在线预览部分如存在完整性等问题,可反馈申请退款(可完整预览的文档不适用该条件!)。
- 3、如文档侵犯您的权益,请联系客服反馈,我们会尽快为您处理(人工客服工作时间:9:00-18:30)。
刀具材料、 刀具材料、刃磨质量
•刀具材料强度↑→ Ra↓ •刃磨质量↑→ Ra↓ •冷却、润滑↑→ Ra↓
18
二、磨削加工表面粗糙度
外圆磨削
磨削用量:砂轮转速、工件 转速、轴向进给量(f)、 砂轮纵向进给量(ap) 砂轮的六因素:磨料,粒度, 结合剂,硬度,组织,形状 尺寸
3
3.1 加工表面质量及其对使用性能的影响
一、加工表面质量的概念 加工表面质量(或表面完整性)包含的内容:
表面粗糙度 表面 几何学 已加工 表面质量 表面层 材质变化 表面波度 纹理方向 表面缺陷(伤痕 表面缺陷 伤痕) 伤痕 表面层冷作硬化 表面层金相组织的变化 表面层残余应力
4
微观几 何轮廓 宏观几 何轮廓
2. 砂轮粒度
磨粒在砂轮上的分布越均匀、 磨粒在砂轮上的分布越均匀、 磨粒越细,刃口的等高性越好。 磨粒越细,刃口的等高性越好。 则砂轮单位面积上参加磨削的 磨粒越多, 磨粒越多,磨削表面上的刻痕 就越细密均匀, 就越细密均匀,表面粗糙度值 就越小。 就越小。
3. 砂轮修整
砂轮修整除了使砂轮具有正 确的几何形状外, 确的几何形状外,更重要的是 使砂轮工作表面形成排列整齐 而又锐利的微刃。因此, 而又锐利的微刃。因此,砂轮 修整的质量对磨削表面的粗糙 度影响很大。 度影响很大。
•砂轮粒度。磨粒太细,砂轮易 砂轮粒度。磨粒太细,
2. 砂轮的选择
被磨屑堵塞, 被磨屑堵塞,使表面粗糙度值增 若导热情况不好, 大,若导热情况不好,还会烧伤 工件表面。 工件表面。 •砂轮硬度。太硬,磨粒脱落 表 砂轮硬度。太硬,磨粒脱落↓,表 面粗糙度增大;太软,磨粒脱落↑, 面粗糙度增大;太软,磨粒脱落 使表面粗糙度值增大 硬度合适、 增大。 使表面粗糙度值增大。硬度合适、 自励性好↑→Ra↓ 自励性好 •砂轮组织。紧密组织在精密磨获 砂轮组织。 得高精度和较小的表面粗糙度值; 得高精度和较小的表面粗糙度值; 疏松组织不易堵塞。 疏松组织不易堵塞。
12
加工表面质量对零件使用性能的影响
粗糙度太大、 粗糙度太大、太小都不耐磨 对耐磨性影响 适度冷硬能提高耐磨性 粗糙度越大, 粗糙度越大,疲劳强度越差
零件表面质量
对疲劳强度的 影响
适度冷硬、 适度冷硬、残余压应力能提高疲 劳强度 粗糙度越大、 粗糙度越大、工作精度降低 残余应力越大, 残余应力越大,工作精度降低 粗糙度越大, 粗糙度越大,耐腐蚀性越差 压应力提高耐腐蚀性, 压应力提高耐腐蚀性,拉应力反 之则降低耐腐蚀性
加工表面的冷作硬化,一般能提高零件的耐磨性。 因为它使磨擦副表面层金属的显微硬度提高,塑性 降低,减少了摩擦副接触部分的弹性变形和塑性变 形。 并非冷作硬化程度越高,耐磨性就越高。这是因 为过分的冷作硬化,将引起金属组织过度“疏松”, 在相对运动中可能会产生金属剥落,在接触面间形 成小颗粒,使零件加速磨损。 图3-5
二、加工表面质量对机器零件使用性能的影响
(一)表面质量对零件耐磨性的影响 1. 表面粗糙度对耐磨性的影响
表面粗糙度太大和太小都不耐磨 表面粗糙度太大,接触表面的实际压强增大,粗 糙不平的凸峰相互咬合、挤裂、切断,故磨损加剧; 表面粗糙度太小,也会导致磨损加剧。因为表面 太光滑,存不住润滑油,接触面间不易形成油膜, 容易发生分子粘结而加剧磨损。
8
(二)表面质量对零件疲劳强度的影响 1. 表面粗糙度对疲劳强度的影响
表面粗糙度越大,抗疲劳破坏的能力越差。 对承受交变载荷零件的疲劳强度影响很大。在交 变载荷作用下,表面粗糙度的凹谷部位容易引起应 力集中,产生疲劳裂纹。 表面粗糙度值越小,表面缺陷越少,工件耐疲劳 性越好;反之,加工表面越粗糙,表面的纹痕越深, 纹底半径越小,其抗疲劳破坏的能力越差。 材料对应力集中敏感程度。钢,铸铁、非铁金属
2. 非几何因素 (1)工件材料的影响 )
韧性材料:工件材料韧性愈好, 韧性材料:工件材料韧性愈好,金属塑性变 形愈大,加工表面愈粗糙。故对中碳钢和低碳 形愈大,加工表面愈粗糙。 钢材料的工件,为改善切削性能, 钢材料的工件,为改善切削性能,减小表面粗 糙度, 糙度,常在粗加工或精加工前安排正火或调质 处理。 处理。 脆性材料:加工脆性材料时, 脆性材料:加工脆性材料时,其切削呈碎粒 状,由于切屑的崩碎而在加工表面留下许多麻 使表面粗糙。 点,使表面粗糙。
16
(2)切削速度的影响 )
加工塑性材料时, 加工塑性材料时,切削速度对表 面粗糙度的影响( 积屑瘤和鳞刺的 面粗糙度的影响(对积屑瘤和鳞刺的 影响)。加工脆性材料, )。加工脆性材料 影响)。加工脆性材料,切削速度影 响不大。 响不大。 此外,切削速度越高, 此外,切削速度越高,塑性变形 越不充分, 越不充分,表面粗糙度值越小 选择低速宽刀精切和高速精切, 选择低速宽刀精切和高速精切, 可以得到较小的表面粗糙度。 可以得到较小的表面粗糙度。 减小进给量f固然可以减小 减小进给量 固然可以减小 表面粗糙度值, 进给量过小, 表面粗糙度值,但进给量过小, 表面粗糙度会有增大的趋势。 表面粗糙度会有增大的趋势。 此外,合理使用冷却润滑液, 此外,合理使用冷却润滑液, 冷却润滑液 适当增大刀具的前角 提高刀具 增大刀具的前角, 适当增大刀具的前角,提高刀具 的刃磨质量等 质量等, 的刃磨质量等,均能有效地减小 表面粗糙度值。 表面粗糙度值。振动
1. 磨削用量
砂轮的转速↑ →材料塑性变形↓ → 表面粗 糙度值↓ ; 磨削深度↑工件速度↑ → 塑性变形↑ →表面 粗糙度值↑ ; 为提高磨削效率, 为提高磨削效率,通常在开始磨削时采用 较大的径向进给量, 较大的径向进给量,而在磨削后期采用较小 的径向进给量或无进给量磨削, 的径向进给量或无进给量磨削,以减小表面 粗糙度值。 粗糙度值。 22
1. 表面粗糙度对耐腐蚀性的影响 零件表面越粗糙,越容易积聚腐蚀性物质,凹谷越 深,渗透与腐蚀作用越强烈。减小零件表面粗糙度, 可以提高零件的耐腐蚀性能。 2. 表面金属的力学物理性质对耐腐蚀性能的影响 零件表面残余压应力使零件表面紧密,腐蚀性物质 不易进入,可增强零件的耐腐蚀性,而表面残余拉应 力则降低零件耐腐蚀性。 表面质量对零件使用性能还有其它方面的影响:如
减小表面粗糙度可提高零件的接触刚度、密封性和测量精度; 对滑动零件,可降低其摩擦系数,从而减少发热和功率损失。 11
(四)表面质量对零件配合质量的影响
(1)表面粗糙度对零件配合精度的影响 表面粗糙度较大,则降低了配合精度。 对间隙配合、对过盈配合影响。 (2)表面残余应力对零件工作精度的影响 表面层有较大的残余应力,就会影响它们精度 的稳定性。
机械加工后的零件表面实际上不是理想的光滑表面, 机械加工后的零件表面实际上不是理想的光滑表面,它 存在着不同程度的表面粗糙度、冷硬、裂纹等表面缺陷。 存在着不同程度的表面粗糙度、冷硬、裂纹等表面缺陷。 虽然只有极薄的一层(几微米~几十微米), ),但都错综复杂 虽然只有极薄的一层(几微米~几十微米),但都错综复杂 地影响着机械零件的精度、耐磨性、配合精度、 地影响着机械零件的精度、耐磨性、配合精度、抗腐蚀性 和疲劳强度等,从而影响产品的使用性能和寿命, 和疲劳强度等,从而影响产品的使用性能和寿命,因此必 须加以足够的重视。 须加以足够的重视。
21
(二)物理因素的影响-表面层金属的塑性变形 物理因素的影响 表面层金属的塑性变形
磨削速度比一般切削速度高得多,且磨粒大多数是负前角, 磨削速度比一般切削速度高得多,且磨粒大多数是负前角,切 削刃又不锐利,大多数磨粒在磨削过程中只是对被加工表面挤压, 削刃又不锐利,大多数磨粒在磨削过程中只是对被加工表面挤压, 没有切削作用。加工表面在多次挤压下出现沟槽与隆起, 没有切削作用。加工表面在多次挤压下出现沟槽与隆起,又由于磨 削时的高温更加剧了塑性变形,故表面粗糙度值增大。 削时的高温更加剧了塑性变形,故表面粗糙度值增大。
(3)进给量的影响 )
(4)其它因素的影响 )
17
影响加工表面粗糙度的因素
刀具几何形状 •残留面积↓ →Ra↓ •前角↑→ Ra↓ •后角↑→摩擦↓→Ra↓ •刃倾角会影响实际工作前角 • v↑→ Ra↓ •f↑→ Ra↑ •ap对Ra影响不大,太小会 打滑,划伤已加工表面
切削用量 影响切削加工表面 粗糙度的因素
砂轮材料。 砂轮材料。氧化物(刚玉)砂轮磨钢类零件;碳化物(碳 化硅、碳化硼)砂轮磨铸铁、硬质合金等;高硬材料(人 造金刚石、立方氮化硼)砂轮可获极小表面粗糙度值,成 本高。 磨削液。 磨削液。
23
影响磨削加工表面粗糙度的因素
砂轮粒度
•粒度↓→Ra↓ • 金刚石笔锋利↑,修正导程、 径向进给量↓→ Ra↓ •磨粒等高性↑→Ra↓ •硬度↑→钝化磨粒脱落↓→ Ra↑ •硬度↓→磨粒脱落↑→Ra↑ •硬度合适、自励性好↑→Ra↓ •砂轮V↑→ Ra↓ •ap、工件V↑→ 塑变↑→ Ra↑ •粗磨ap↑→生产率↑ •精磨ap↓→ Ra↓(ap=0 ) ap↓→ Ra↓(ap=0光磨) •太硬、太软、韧性、导热性差
14
残留面积高度的计算: 当刀尖圆弧半径rε=0时,残留面积高度H为 f H= ctgk r + ctgk r′
f:进给量, K r 主偏角, K r 副偏角
'
残留面积高度的计算: 当刀尖圆弧半径rε>0时,残留面积高度H为
f2 H= 8rε rε 刀尖圆弧半径
减小进给量f、减小主偏角kr和副偏角kr’、 增大刀尖圆弧半径rε,都能减小理论残留面积的 15 高度H,也就减小了零件的表面粗糙度
机械制造工艺学
第三章 机械加工表面质量
主讲: 主讲:胡大超
1
本章内容
3.1 加工表面质量及其对使用性能的影响 3.2 影响加工表面粗糙度的工艺因素及其改善措施 3.3 影响表层金属力学物理性能的工艺因素及其改 善措施 3.4 机械加工中的振动