滚齿机定数
滚齿机的数控编程与调试

滚齿机的数控编程与调试滚齿机是一种用于加工齿轮的机床,它具有高度自动化和精度高的特点,广泛应用于汽车、航空、航天等行业。
为了实现滚齿机的自动化加工,数控编程与调试是必不可少的环节。
本文将介绍滚齿机的数控编程与调试过程,并提供一些实用的技巧与经验。
一、数控编程的基本原理和步骤1. 数控编程原理数控编程是将加工过程中的运动轨迹、切削参数等信息转化为机床可以识别的指令,使机床按照指令进行加工的过程。
滚齿机数控编程的基本原理是基于齿轮的几何特征和切削理论,根据加工要求和滚齿机的功能特点,通过预先编写一系列指令,实现齿轮的精确加工。
2. 数控编程步骤(1)确定齿轮的尺寸和加工要求,包括模数、压力角、齿数等等。
(2)绘制齿轮的几何图形,计算出齿轮的几何参数,如齿顶圆直径、齿根圆直径、齿宽等。
(3)根据齿轮的几何参数,结合滚齿机的功能特点,编写数控程序并生成相应的G代码。
(4)将编写好的数控程序输入到滚齿机的数控系统中,进行调试和验证。
(5)根据加工过程中的实际效果对数控程序进行调整和优化,以获得更好的加工结果。
二、滚齿机数控编程的技巧和经验1. 合理选择滚齿机数控系统不同的滚齿机数控系统有不同的功能和性能,选择适合自己的滚齿机数控系统是提高编程效率和加工精度的关键。
在选择数控系统时,应考虑到滚齿机的加工要求、工作精度、稳定性等因素,并结合自身的实际情况做出决策。
2. 熟悉滚齿加工的基本原理和常见问题滚齿加工是滚齿机的核心任务,熟悉滚齿加工的基本原理和常见问题可以帮助我们更好地进行数控编程和调试。
例如,了解齿轮的齿形误差对加工的影响,了解滚齿刀具的选择和使用方法等等,都是提高编程和调试效果的重要因素。
3. 注意编写数控程序的细节在编写数控程序时,应注意以下细节:(1)合理调整刀具的进给速度和转速,避免过高或过低造成的加工质量问题。
(2)合理安排刀具的路径和切削方式,避免冲撞和切削过程中的问题。
(3)考虑到加工后的余量和切削力的影响,进行合适的切削参数的选择和调整。
滚齿加工操作流程

滚齿加工操作流程一、 本作业指导书适用于滚切法加工GB10095-88中规定的7、8、9级精度渐 开线圆柱齿轮直齿轮的加工。
二、 滚齿前挂轮的选择与安装1、 根据加工工件齿数计算分齿挂轮,对单头滚刀(我厂现使用滚刀均为单头滚刀),分齿挂轮计算式为a.c b.d =k 分 z(K 分为机床分齿定数),对YBA3120滚齿机,当5≤z ≤20时(e=56 f=28)a.c b.d =12 z , 当21≤z ≤142时(e=42 f=42)a.c b.d =24z,另可根据机床分齿挂轮表直接选取分齿挂轮.2、 根据被加工齿轮的技术参数、精度要求、材质和齿面硬度等情况选择合理的切削参数:(1) 切削速度V 切:在15-40m/min 范围内选取,根据工式n=1000.v 切 π.d 刀(d 刀为滚刀外径,我厂滚刀一般为55)计算出滚刀主轴转速,选取机床转速中最接近的一种转速,但选定的主轴转速应不高于机床说明书中规定的主轴允许最高转速,齿数越少,转速应越低,齿数少于20,转速应不高于250。
根据所选转速确定主轴的主速挂轮。
(2) 轴向进给量S轴:粗滚进给量在0.5-2.0mm/r 范围内选取,精滚进给量在0.6-1.50mm/r范围内选取,根据工式a1.c1 b1.d1=A1.S 轴(A1为机床轴向进给定数,对YBA3120滚齿机, A1=25 16π)计算出轴向进给挂轮(若S 轴=2,则a1.c1 b1.d1=1,若S 轴=1。
5则a1.c1b1.d1=37.5/50)若此时计算出的挂轮被占用,可用齿数相近的挂轮代替.3、 当分齿、速度、和走刀挂轮计算和校验后,便可进行挂轮架的调整。
调整中应注意以下问题:首先检查挂轮、挂轮架、轴、衬套、键以及垫圈、螺母等有无损坏,并仔细清洗;安装挂轮的齿侧间隙要适当,同时还应保证不歪斜。
机床启动前应用手扳转皮带轮,检查挂轮传动有无卡死现象和过大的松动。
三、根据滚刀安装与调整指导书安装与调整滚刀。
滚齿机在齿轮制造中的精度要求

滚齿机在齿轮制造中的精度要求齿轮是现代机械中常见的传动装置,广泛应用于各行各业。
而为了确保齿轮能够正常运转并具备良好的传动效果,其制造过程中的精度要求显得尤为重要。
在齿轮制造中,滚齿机是一种常用的加工设备,而滚齿机的性能和精度直接关系着齿轮的质量和传动效率。
首先,滚齿机在齿轮制造中的精度要求包括齿轮的几何精度和位置精度。
几何精度指的是齿轮的齿形、齿距、齿厚等几何参数的精确度。
而位置精度则是指齿轮齿槽与滚齿机滚子的相对位置的精确度。
这两者的精度要求直接影响着齿轮的传动性能以及工作时的噪声和寿命等重要指标。
对于齿轮的几何精度要求,滚齿机需要满足以下几个方面:1. 齿距精度:齿轮的齿距是指相邻两齿槽之间的距离,这个参数直接影响着齿轮的传动准确性。
滚齿机应确保齿距的相对误差小于规定的允许范围。
2. 齿厚精度:齿轮的齿厚是指齿轮齿槽的厚度,在传动中起到承载载荷的作用。
滚齿机需要确保齿厚的绝对误差在规定的范围内,并且各齿槽之间的齿厚误差需控制在一定的范围之内。
3. 齿高精度:齿轮的齿高是指齿槽顶和齿槽底之间的高度差,直接影响着齿轮的传动稳定性和噪声。
滚齿机应确保齿高的绝对误差和相对误差在规定的范围内。
对于齿轮的位置精度要求,滚齿机需要满足以下几个方面:1. 齿顶位置误差:齿顶位置误差是指齿轮齿顶相对于理想位置的偏离程度。
滚齿机应确保齿顶位置误差在一定的范围之内,以确保齿轮在传动中的定位精度。
2. 齿轮中心距误差:齿轮中心距误差是指齿轮齿槽中心与滚齿机滚子中心之间的距离偏差。
滚齿机应确保齿轮中心距误差在规定范围内,以确保齿轮的传动精度。
3. 齿轮螺纹高度误差:对于带内齿的齿轮而言,螺纹高度误差是指齿轮螺纹的高度与理想高度之间的差值。
滚齿机需要确保齿轮螺纹高度误差在规定的范围内,以保证齿轮和齿圈的连接性能。
总的来说,在齿轮制造中,滚齿机的精度要求是非常高的。
只有通过精确的加工,才能确保齿轮的传动效率、传动平稳性以及使用寿命。
滚齿机的齿量修正与矫正方法

滚齿机的齿量修正与矫正方法滚齿机是一种用于制造齿轮的重要工具,它通过将齿轮基体与齿轮轮廓滚刃接触,并通过滚切的方法完成齿轮齿面的加工。
在滚齿机的操作过程中,由于机器精度、材料特性等因素的影响,可能会出现齿量偏差或者齿形问题。
为了保证齿轮的质量和性能,需要对滚齿机的齿量进行修正与矫正。
齿量修正是指对齿形中的齿量进行微调,以使其满足设计要求。
齿量修正可以通过以下几种方法进行:1. 齿量修正切削:这是一种常用的方法,通过对齿轮齿面进行切削来改变齿量。
在滚齿机上,可以使用特殊的修形刀具进行齿量修正切削,以达到设计要求。
2. 齿量修正打磨:这是另一种常用的方法,通过对齿轮齿面进行打磨来改变齿量。
可以使用砂轮或其他合适的磨削工具进行修正打磨,以达到设计要求。
无论是齿量修正切削还是齿量修正打磨,都需要根据实际情况和具体要求进行操作。
在进行修正时,需要注意以下几点:1. 充分了解齿量修正的要求:在进行齿量修正之前,需要明确齿量的目标值和允许范围。
只有明确了要求,才能有针对性地进行修正。
2. 选择合适的修正方法:齿量修正可以采取不同的方法,根据具体情况选择适合的修正方法。
例如,对于齿量较大的情况,可以使用切削来进行修正;对于齿量较小的情况,可以使用打磨来进行修正。
3. 控制修正量和修正位置:修正齿量时需要控制修正量和修正位置,避免过度修正或修正不足。
修正量过大或位置偏差都可能导致齿轮质量下降,因此需要谨慎操作。
除了齿量修正之外,滚齿机还需要进行齿量矫正。
齿量矫正是指在齿轮制造过程中发现齿量偏差或齿形问题时进行的一种矫正处理。
齿量矫正可以通过以下几种方法进行:1. 加工补偿:在加工齿轮时,可以在一定程度上通过加工补偿来矫正齿量。
例如,可以使用特殊成形刀具进行加工,通过切削加工来矫正齿量偏差。
2. 热处理矫正:在制造齿轮的过程中,可以通过热处理来改变齿轮的性能和形状。
通过控制热处理的温度和时间,可以矫正一定程度的齿量偏差。
滚齿机加工参数

Y38滚齿机技术规格工作台:直径 475mm 中心孔直径 80mm心轴直径 35mm心轴孔锥度莫氏5# 工作台中心至刀具主轴中心距离30—470mm加工最大圆柱直齿轮直径:不用后立柱时 800mm用后立柱时 450mm加工最大圆柱斜齿轮直径:当螺旋角为 30°时500mm当螺旋角为60°时190mm 加工工件:最大模数(钢/铸件) 6/8mm最大宽度 240mm 刀具最大垂直行程 290mm刀架最大回转角度 360°刀具中心至工作台面最小距离 205mm 可安装滚刀最大直120mm滚刀转速范围:(共分7级) 47.5—192r/min刀具心轴直径 22、27、32mm 轴向进给范围 0.25—3mm/r 径向进给范围0.03—0.36mm/r主电机:功率 3kw转速1430 r/min 快速移动电机:功率 1.1kw转速 1400 r/min机床重量 3.65 t切向进给范围 0.15—0.9mm/r 主电机:功率 3kw转速1430 r/min 快速移动电机:功率 1.1kw转速 1400 r/min 机床重量 3.65tY38A滚齿机技术规格工作台:直径 475mm 中心孔直径80mm心轴直径 35mm心轴孔锥度莫氏5# 工作台中心至刀具主轴中心距离30—470mm加工最大圆柱直齿轮直径:不用后立柱时 800mm用后立柱时 450mm加工最大圆柱斜齿轮直径:当螺旋角为 30°时500mm当螺旋角为60°时190mm 加工工件:最大模数(钢/铸件)6/8mm最大宽度240mm 刀具最大垂直行程 290mm刀架最大回转角度360°刀具中心至工作台面最小距离 205mm 可安装滚刀最大直径 120mm滚刀转速范围:(共分7级) 47.5—192r/min刀具心轴直径 22、27、32mm 轴向进给范围 0.25—3mm/r 径向进给范围0.03—0.36mm/r主电机:功率 3kw转速 1430 r/min 快速移动电机:功率 1.1kw转速 1400 r/min机床重量 3.65 tYW3180滚齿机床技术规格最大工件直径 800mm 最大工件模数 10mm 最小工件齿数8 刀具最大垂直行程 400mm 刀架最大回转角度±65°刀架回转角度最小读数 5´刀具轴向移动量80mm 刀具主轴锥孔锥度莫氏5#刀具心轴直径 27、32、40、50mm 刀具垂直快速移动速度580mm/min 刀具垂直移动每转移动量 0.47mm/r 允许安装刀具最大长度 200mm刀具主轴中心距工作台面距离:最大 680mm最小 280mm刀具主轴中心距工作心轴中心距离:最大 520mm最小50mm 工作台直径 690mm 工作台孔径130mm 工作台水平最大移动距离 470mm工作台水平快速移动速度 458mm/min 工作台水平手动每转移动量 0.5mm/r 工作台水平移动最小读数 0.01mm工件心轴锥孔莫氏5# 刀具主轴转速范围 45—280r/min 轴向进给范围 0.43—5.9mm/ r切向进给范围 0.14—1.96mm/r 径向进给范围0.1—26.5mm/min主电机:功率 7.5kw 转速 1450 r/min轴向快速电动机功率 1.5kw 转速 1410 r/min径向快速电机功率 0.8kw 转速 1380 r/min液压电机功率 1.1kw 转速 1410 r/min冷却电机功率 0.09kw1. 机床主要性能及用途Y3180H普通滚齿机,采用齿轮滚刀以展成法滚切圆柱直齿轮、斜齿轮及花键等。
滚齿机功能使用说明

滚齿机功能使⽤说明滚齿机功能使⽤说明⽤本功能加⼯(磨削/切削)齿轮时,可使⼯件轴的旋转与⼑具轴(砂轮/滚⼑)的旋转同步。
同步的⽐率可通过程序进⾏指定。
本功能下的⼑具轴与⼯件轴的同步,因为采⽤数字伺服直接控制的⽅式,所以⼯件轴可以不带误差地跟随⼑具轴的速度变动,可以实现⾼精度的齿轮加⼯。
●控制轴构成:第1轴:X轴第2轴:Z轴第3轴:Y轴(⼑具轴,主轴轴)第4轴:C轴(⼯件轴,从控轴)●指令格式:开始同步:G81 T__ L__ (Q__ P__)解除同步:G80T:⼯件齿数(指令范围:1~1000)L:⼑具的滚齿条数(指令范围:-1000~1000,且不能为0)通过L 的符号来指定⼯件轴相对⼑具轴的旋转⽅向。
L为正时,⼯件轴的旋转⽅向与⼑具轴的旋转⽅向相同L为负时,⼯件轴的旋转⽅向为⼑具轴的旋转⽅向相反Q:齿轮的模数或径节公制输⼊时,指定模数。
(单位:0.001mm,指令范围:0.01~100.0mm)英制输⼊时,指定径节。
(单位:0.001inch-1, 指令范围:0.01~254.0 inch-1)P:齿轮的螺旋⾓(单位:deg,指令范围:-90.0~90.0deg)注:Q为法⾯模数或法⾯径节注:加⼯直齿轮时,Q、P值可省略。
●相关定义:主控轴、从控轴:成为同步标准的轴称作主控轴,与主控轴同步移动的轴称为从控轴。
例如像滚齿机那样与旋转的⼑具同步⽽⼯件移动时,⼑具轴成为主控轴,⼯件轴成为从控轴。
同步控制:1、开始同步指令G81进⼊同步⽅式时,⼑具轴和⼯件轴之间的同步开始。
在同步中,⼑具轴和⼯件轴的旋转,⼀直保持T(齿数) : L (滚齿条数) 的⽐例关系。
同步过程中不管是⾃动运⾏还是⼿动运⾏,始终保持同步关系。
在同步中没有取消同步⼜重新指令G81时,可由参数ECN设置是否有效,当ECN设置有效时,将根据新指定的T、L系数重新同步,如果指定有Q、P,则将进⾏斜齿轮加⼯。
由此,可进⾏直齿轮和斜齿轮的连续加⼯。
滚齿工艺

滚齿工序过程作业指导书滚齿: 开齿槽,为齿轮热处理前做准备工作或直接滚齿成形。
备注工序内容: 滚齿,公法线留量(见表),差动挂轮计算到小数点后第六位,齿底粗糙度达Ra12.5以上。
例:机床: 按图纸(齿轮模数、齿顶圆直径、齿轮重量等)选取滚齿机床。
例: 刀杆:刀杆:刀杆安装后,悬臂检查刀杆径向和端面圆跳动,其跳动公差不得大于表1的规定。
表1 mm齿轮精度等级 圆跳动公差A B C7 0.005 0.008 0.005 8 0.008 0.010 0.008 90.0100.0150.010注:1、精度等级按第Ⅱ公差组要求。
2、表中B 点跳动是指L ≤100mm 时的数值,L 每增加100mm ,B 点跳动允许增加0.01mm例:滚齿刀具:按图纸选取滚齿刀具(根据加工工件的模数、压力角、精度等级和工艺要求来确定),通过滚齿直接成品时选用标准齿轮滚刀,滚齿后还需要磨齿时,应选用磨前齿轮滚刀。
下图为标准滚刀及磨前滚刀。
磨前滚刀 标准滚刀滚刀精度:滚刀通常分为AA 、A 、B 、C 四种精度等级,小模数齿轮滚刀分为AAA 、AA 、A 三种精度等级,滚刀的精度等级应根据工件的精度等级来确定。
按表2所示对滚刀进行选择。
表2齿轮精度等级滚刀精度等级粗滚齿精滚齿 7 B 或C AA 8 A 9CA注:精度等级按第Ⅱ公差组要求。
滚刀磨钝标准: 在滚齿时,如发现齿面有光斑、拉毛、粗糙度变坏等现象时,应立即停止使用并交给专人进行复磨滚刀。
滚刀头数: 滚刀头数分为单头及多头滚刀,我厂多采用单头滚刀滚刀旋向:为了切出准确的齿形,应使滚刀和工件处于正确的“啮合”位置,即保证滚刀刀齿的排列方向与齿轮齿槽方向一致齿槽方向一致,从而加工出一定螺旋角的齿轮齿槽。
为此,在加工齿轮前须将滚刀轴线相对于齿轮顶面偏转一定的角度进行安装,该偏转角称为滚刀安装角,滚刀安装角的大小与方向不仅与滚刀的螺旋升角有关,还与被加工齿轮的螺旋角有关。
滚齿机操作规程
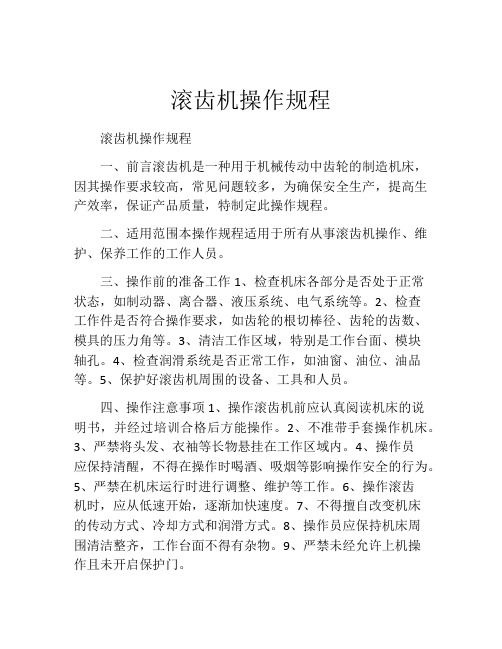
滚齿机操作规程滚齿机操作规程一、前言滚齿机是一种用于机械传动中齿轮的制造机床,因其操作要求较高,常见问题较多,为确保安全生产,提高生产效率,保证产品质量,特制定此操作规程。
二、适用范围本操作规程适用于所有从事滚齿机操作、维护、保养工作的工作人员。
三、操作前的准备工作1、检查机床各部分是否处于正常状态,如制动器、离合器、液压系统、电气系统等。
2、检查工作件是否符合操作要求,如齿轮的根切棒径、齿轮的齿数、模具的压力角等。
3、清洁工作区域,特别是工作台面、模块轴孔。
4、检查润滑系统是否正常工作,如油窗、油位、油品等。
5、保护好滚齿机周围的设备、工具和人员。
四、操作注意事项1、操作滚齿机前应认真阅读机床的说明书,并经过培训合格后方能操作。
2、不准带手套操作机床。
3、严禁将头发、衣袖等长物悬挂在工作区域内。
4、操作员应保持清醒,不得在操作时喝酒、吸烟等影响操作安全的行为。
5、严禁在机床运行时进行调整、维护等工作。
6、操作滚齿机时,应从低速开始,逐渐加快速度。
7、不得擅自改变机床的传动方式、冷却方式和润滑方式。
8、操作员应保持机床周围清洁整齐,工作台面不得有杂物。
9、严禁未经允许上机操作且未开启保护门。
五、操作流程1、机床开机前检查。
2、打开滚齿机的电源总闸,并进行手动试车调整。
3、加工前要进行机床的试车和试切。
4、开工前应正确调整好机床各部件和工件,特别要调整好送料器送丝装置,并用完成而不可退让的取向模具进行调整。
5、在加工时严禁超载,主軸负荷不得超过机床规定范围,划线部分加工时,要加强刀具与齿轮的协作。
6、刚开始的加工时,应手动推动滚轮到合适位置,逐步增快速度,以最终用自动循环完成,操作速度控制在当类加工性能及机床精度允许的范围内。
六、操作结束后的事项1、停机后,应将机床及时清洁,特别是滚制部位应严密保护。
2、关闭机床电源,并清理现场。
3、定期检修润滑系统,并更换润滑油。
4、加工结束后,操作者应在加工记录清单上逐项记录工件名称、数量、质量、时间等内容。
- 1、下载文档前请自行甄别文档内容的完整性,平台不提供额外的编辑、内容补充、找答案等附加服务。
- 2、"仅部分预览"的文档,不可在线预览部分如存在完整性等问题,可反馈申请退款(可完整预览的文档不适用该条件!)。
- 3、如文档侵犯您的权益,请联系客服反馈,我们会尽快为您处理(人工客服工作时间:9:00-18:30)。
分齿定数
滚齿机型号差动定数差动轴向值
直齿斜齿
YC3132(南京第二机床厂)8mm12126
YZ3132(南京第二机床厂)8mm12126
YBA3132(重庆机床厂)6mm1818 61/12
YB3120(重庆机床厂)6mm1616 27/4
YBA3120(重庆机床厂)4mm24243
YBA3112(重庆机床厂)2mm2424 1.006944
YB3112(上海第一机床厂)2mm1515 2.03718
FQ-2520.6265
Y3131540
Y3150050
Y361258
Y3610030
Y35015.91546
Y33024
W1Y3J25
5370 5.431162
ZWF-30 6.366198
OF-108.25059
53279.81456
Y3109.8145319
KF213.47515
URF5 6.0638
ZWF15 6.73756
RF1057.639443
RF758.08572
RF58.5943
Y31512.1276
Y31611.9637
Y37-19.81456
Y38-1(青岛机床厂)8mm 6.96301
Y37 5.96831
RF2 4.491882
RF0 2.15615
Y31125 4.7746371
Y304 1.617
Y350Z 3.81972
Y310.95493
Y35-1 5.57042
YM32B 3.9788812.5 Y32020或4020或401515π
Y3180E242466π
Y36100(武汉重型机床厂)25mm151530
Y36100(齐齐哈尔第一机床厂)24mm202025
Y3663A(齐齐哈尔第一机床厂)16mm202025
YMA3180(重庆机床厂)8mm24246
YM3180H(重庆机床厂)10mm36369
YM3150E(重庆机床厂)8mm36369
YA3180(重庆机床厂)10mm24246
Y3180(南京第二机床厂)10mm242499π
YB3180H(重庆机床厂)10mm242499π
Y3180E(上海第一机床厂)10mm242499π
Y3180E(重庆机床厂)10mm242499π
Y3150E(重庆机床厂)8mm242499π
YB3150E(重庆机床厂)8mm242499π
Y3150(上海第一机床厂)6mm24488.355615 105/4 Y32b2424 3.97888 25/2
Y3824247.9577525
苏联Y5322424 5.96831 75/4 YM3180H24或3624或3699π
Y3180H24或3624或3699π
YB3120121299π
Y3150A242466π
Y3180B242466π
Y31125A(南京第二机床厂)16mm
Y31125E(重庆机床厂)16mm48481010π
YM31125E(重庆机床厂)12mm48481010πYGA31125(重庆机床厂)8mm606015
YM31200H(重庆机床厂)16mm24247
Y31200H(重庆机床厂)20mm242410
Y31200G(武汉重型机床厂)20mm202015
YQ31315G(武汉重型机床厂)20mm202015
YQ31315(武汉重型机床厂)24mm202015
Y31315B(武汉重型机床厂)30mm404015
Y31500A(武汉重型机床厂)30mm505015
Y31800(武汉重型机床厂)30mm505015
捷克F061212 5.96831 75/4
苏联Y533015或30或6015或30或6015.2788848或24 Y3120024241010π
Y3131540402424π
YG36121616 2.38732 15/2 RWF2卧30或1530或1512.1275838.1
西德RFW16卧15153030π
有差动滚齿机202095.49296300
苏联有差动滚齿机1515285.8649812573/14苏联马拉特(MOPAT)161630.5577596
Y35J2424 Y36082424无差动高效立式滚齿机2424无差动机构无差动机构无差动机构
无差动机构无差动滚齿机2020
YG3780
走刀定数出处
齿轮手册
齿轮手册
齿轮手册
齿轮手册
齿轮手册
齿轮手册
齿轮手册
通用比值挂轮表
通用比值挂轮表
通用比值挂轮表
通用比值挂轮表
通用比值挂轮表
通用比值挂轮表
通用比值挂轮表
通用比值挂轮表
通用比值挂轮表
通用比值挂轮表
通用比值挂轮表
通用比值挂轮表
通用比值挂轮表
通用比值挂轮表
通用比值挂轮表
通用比值挂轮表
通用比值挂轮表
通用比值挂轮表
通用比值挂轮表
通用比值挂轮表
通用比值挂轮表
通用比值挂轮表
通用比值挂轮表
通用比值挂轮表
通用比值挂轮表
通用比值挂轮表
通用比值挂轮表
通用比值挂轮表
通用比值挂轮表
通用比值挂轮表
通用比值挂轮表
通用比值挂轮表
通用比值挂轮表
齿轮手册
齿轮手册
齿轮手册
齿轮手册
齿轮手册
齿轮手册
齿轮手册
齿轮手册
齿轮手册
齿轮手册
齿轮手册
齿轮手册
齿轮手册
1齿轮手册M6Φ500 10/3M4Φ200 3/4M8Φ800 32/9M8Φ750 32*π/125或1248*π/3125或2016*π/3125M10Φ800 32*π/125或1248*π/3125或2016*π/3125M10Φ800πM6Φ200 54*π/125M8Φ500无级M10Φ800
齿轮手册
π/4齿轮手册M16Φ1250π/4齿轮手册M16Φ1250
齿轮手册
齿轮手册
齿轮手册
齿轮手册
齿轮手册
齿轮手册
齿轮手册
齿轮手册
齿轮手册
312/119M8Φ800
M20Φ1500
M20Φ2000
M30Φ3150 16/15M1.5Φ125
M16Φ1000
M30Φ1600 3/2
381/180
8/5
4
0.397M1Φ80。