涂装工艺技术参数
汽车零部件涂装喷漆工艺(参数)监控与记录要求
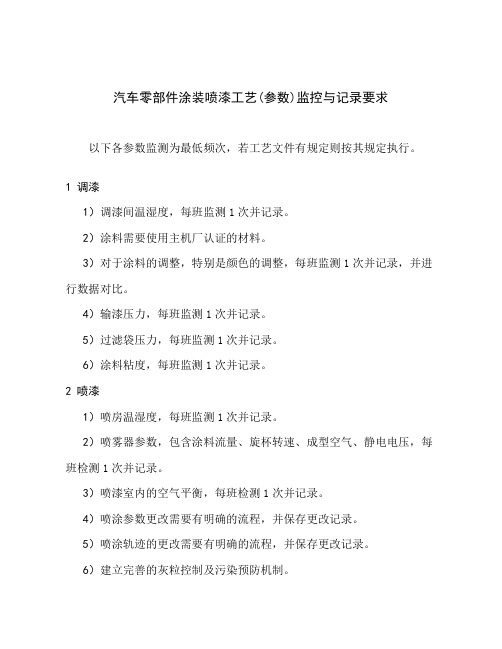
汽车零部件涂装喷漆工艺(参数)监控与记录要求以下各参数监测为最低频次,若工艺文件有规定则按其规定执行。
1调漆
1)调漆间温湿度,每班监测1次并记录。
2)涂料需要使用主机厂认证的材料。
3)对于涂料的调整,特别是颜色的调整,每班监测1次并记录,并进行数据对比。
4)输漆压力,每班监测1次并记录。
5)过滤袋压力,每班监测1次并记录。
6)涂料粘度,每班监测1次并记录。
2喷漆
1)喷房温湿度,每班监测1次并记录。
2)喷雾器参数,包含涂料流量、旋杯转速、成型空气、静电电压,每班检测1次并记录。
3)喷漆室内的空气平衡,每班检测1次并记录。
4)喷涂参数更改需要有明确的流程,并保存更改记录。
5)喷涂轨迹的更改需要有明确的流程,并保存更改记录。
6)建立完善的灰粒控制及污染预防机制。
7)定期检查和更换喷漆室空调动压室及静压室过滤袋,每班监测1次并记录。
3固化
1)烤炉内空气温度应有自动控制和监视,并有高低超温报警功能,每班监测1次并记录;若无自
动报警功能,每2h监测1次并记录。
.
2)定期对温度传感器(或热电偶)进行检定或校准,每年校准1次并记录。
3)定期验证零件在烤炉中的表面温度和持续时间(炉温曲线),确认是否满足涂料供应商推荐的烘烤规范,每3个月1次并记录。
4)定期对固化后的零件上的涂膜用白布涂上丙酮或丁酮或甲基异丁酮擦拭十个来回,检验是否固化充分,每班监测1次。
涂装车间技术规格及要求.

涂装车间技术规格及要求编制:制作日期:涂装车间技术规格及要求项目内容:1、小型结构件中途线2、大型结构件涂装线3、中大挖整机补漆线(SWE330)4、小挖整机补漆线(SWE130)5、自行葫芦输送系统(SWE330、SWE450)一、小型结构件中涂线(一)、设计依据1、生产任务:承担小型结构件中涂任务2、生产纲领:10000台/年3、生产节拍:10~25分钟/工位4、工件的尺寸以及重量:见附表一5、工作制度以及年时基数:(1)、工作制度:全年工作300天,每天两班制(2)、年时基数:工人年时基数600天,设备年时基数570天6、能源:(1)、动力电:380V 三相50HZ(2)、照明电:220V 单相50HZ7、供水:0.2~0.3MPa8、压缩空气:0.4~0.7MPa9、环境温度:-10℃~45℃10、涂装线布局:见附图11.运输方式:轨道加工艺车运输。
(二)、生产工艺流程(三)、中涂烘干室技术说明:因结构件的热容量大,烘干室温度应设计在60~120℃,为保证热效率高,运行成本低的原则,采用封闭式烘干结构,前后门为对开门,热风循环加热方式。
主要有室体、热风循环加热系统、废气处理系统以及电控系统等部分组成。
1、室体:采用钢结构骨架和彩钢保温板拼装制作,底部也需保温,材料为保温岩面,其厚度为100mm,壁板接缝处涂耐高温密封胶。
2、循环风管:采用1.5mm厚镀锌板制作,烘干室应设有废气处理和再利用装置。
3、加热系统:采用四元体燃气热风炉,带废气处理装置。
为保证循环空气的清洁度,热风循环系统中设有高温过滤装置。
燃烧机采用进口设备,保证加热设备的工作可靠性。
(四)、喷漆室技术要求:采用水旋式喷漆室结构,其结构由室体、送风系统、排风系统、水旋器装置、循环水系统以及电气控制系统组成。
1、室体:采用钢结构骨架以及EPS板拼装结构。
室体上部分为静压室,下部分为镀锌格栅板及水盆和水旋器装置。
静压室在室体顶部,有稳定气流的作用,使整个静压室到底部格栅板之间形成稳定的压差,保证漆雾最大量的被气流带走。
油漆喷涂工艺质量控制标准

油漆喷涂工艺质量控制标准1. 引言油漆喷涂是一种常用的表面处理方法,用于保护和美化物体表面。
为了确保油漆喷涂的质量,需要建立一套科学的工艺质量控制标准。
2. 工艺参数控制2.1 喷枪调节喷嘴尺寸:根据物体表面的大小和要求的涂层厚度,选择合适的喷嘴尺寸。
喷嘴角度:根据物体的形状和表面特征,调整喷嘴的角度,以达到均匀喷涂的效果。
喷涂距离:控制喷涂距离,保持适当的喷涂压力和喷涂效果。
喷涂速度:控制喷涂速度,保证涂层的均匀度和质量。
2.2 涂料稀释比例根据涂料的粘度和喷涂要求,确定涂料的稀释比例。
过高或过低的稀释比例都会影响喷涂效果和涂层的质量。
2.3 喷涂压力控制根据喷涂要求和涂料的性质,确定合适的喷涂压力。
过高或过低的喷涂压力都会导致喷涂质量不理想。
3. 工艺质量控制指标3.1 喷涂均匀度使用肉眼观察,检查涂层的颜色和光亮度是否均匀。
可以通过观察涂层的反光度和色差来评估喷涂的均匀度。
3.2 涂层厚度使用涂层厚度测量仪,测量涂层的厚度。
根据喷涂要求,确定合适的涂层厚度范围,并确保涂层的厚度在可接受范围内。
3.3 涂层附着力使用附着力测试仪,测试涂层的附着力。
根据要求,确定合适的附着力指标,并确保涂层的附着力符合要求。
3.4 涂层硬度使用硬度测量仪,测量涂层的硬度。
根据要求,确定合适的硬度范围,并确保涂层的硬度符合要求。
3.5 涂层耐候性将喷涂的物体放置在不同的环境条件下,观察涂层的耐候性能。
根据要求,确定合适的耐候性指标,并确保涂层的耐候性符合要求。
3.6 其他指标根据具体要求,可以制定其他工艺质量控制指标,如涂层的耐腐蚀性、耐磨性等。
4. 工艺质量控制步骤4.1 调整喷枪参数根据喷涂要求和涂料的性质,调整喷枪的喷嘴尺寸、角度、喷涂距离和喷涂速度。
4.2 稀释涂料根据涂料的粘度和喷涂要求,确定合适的稀释比例。
4.3 控制喷涂压力根据喷涂要求和涂料的性质,调整喷涂压力,保证喷涂的质量。
4.4 喷涂样品测量随时测量涂层的均匀度、厚度和附着力,确保喷涂质量符合要求。
喷漆操作中的喷涂工艺参数与调整方法
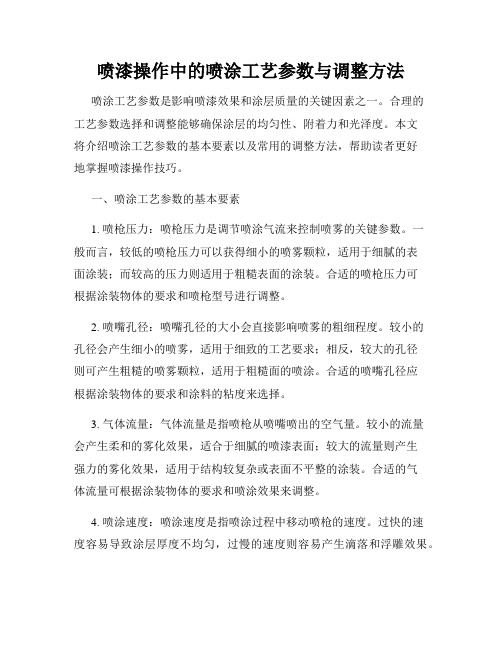
喷漆操作中的喷涂工艺参数与调整方法喷涂工艺参数是影响喷漆效果和涂层质量的关键因素之一。
合理的工艺参数选择和调整能够确保涂层的均匀性、附着力和光泽度。
本文将介绍喷涂工艺参数的基本要素以及常用的调整方法,帮助读者更好地掌握喷漆操作技巧。
一、喷涂工艺参数的基本要素1. 喷枪压力:喷枪压力是调节喷涂气流来控制喷雾的关键参数。
一般而言,较低的喷枪压力可以获得细小的喷雾颗粒,适用于细腻的表面涂装;而较高的压力则适用于粗糙表面的涂装。
合适的喷枪压力可根据涂装物体的要求和喷枪型号进行调整。
2. 喷嘴孔径:喷嘴孔径的大小会直接影响喷雾的粗细程度。
较小的孔径会产生细小的喷雾,适用于细致的工艺要求;相反,较大的孔径则可产生粗糙的喷雾颗粒,适用于粗糙面的喷涂。
合适的喷嘴孔径应根据涂装物体的要求和涂料的粘度来选择。
3. 气体流量:气体流量是指喷枪从喷嘴喷出的空气量。
较小的流量会产生柔和的雾化效果,适合于细腻的喷漆表面;较大的流量则产生强力的雾化效果,适用于结构较复杂或表面不平整的涂装。
合适的气体流量可根据涂装物体的要求和喷涂效果来调整。
4. 喷涂速度:喷涂速度是指喷涂过程中移动喷枪的速度。
过快的速度容易导致涂层厚度不均匀,过慢的速度则容易产生滴落和浮雕效果。
合适的喷涂速度应根据涂料的粘度、涂装物体的形状和表面要求来确定。
二、喷涂工艺参数的调整方法1. 喷枪调整:首先,根据涂装物体的尺寸和形状选择合适的喷枪型号。
然后,通过调整喷枪的喷枪压力、喷嘴孔径和气体流量,控制喷涂的雾化状态和喷涂效果。
调整时应注意逐步调整,观察液雾的均匀程度和涂层的质量,适时进行微调。
2. 涂料稀释:根据涂料的粘度和喷涂要求,适当稀释涂料。
过粘的涂料容易产生滴落和流挂现象,影响涂层的质量;过稀的涂料则会导致喷涂效果不佳。
应根据涂料厂家提供的使用指南,按比例稀释涂料至合适的粘度。
3. 喷涂距离:喷涂距离是指喷枪与涂装物体的距离。
喷涂距离过近会导致过度喷涂,涂层厚度不均匀;喷涂距离过远则会造成喷漆感观不佳。
电泳涂装工艺技术标准

电泳涂装工艺技术标准电泳涂装工艺技术标准电泳涂装是一种常用于车身和金属制品涂装的表面处理工艺,其工艺技术标准的制定对于保证涂装质量和提高生产效率至关重要。
下面介绍一下电泳涂装工艺技术标准的要点。
1. 电泳槽的准备电泳槽应选用耐腐蚀性好且具有较高绝缘性能的材料,如不锈钢或塑料等。
槽的尺寸和形状应符合涂装产品的尺寸和形状要求。
槽内需保持清洁,并定期更换电泳液,以确保涂装效果。
2. 电泳液的配置电泳液的主要成分依据具体涂装产品的要求而定,一般包括树脂、溶剂、助剂等。
液体成分的配比要按照标准比例进行,以保证涂层的质量和均匀性。
3. 预处理在进行电泳涂装之前,需要对涂装产品进行适当的预处理。
通常包括清洗、除油、除锈等工序,以确保产品表面的干净和粗糙度的适宜。
4. 涂装工艺参数的设定涂装工艺参数的设定是确保电泳涂装效果的重要一环。
包括电泳液浓度、电压、时间等参数的合理设定。
不同的工艺参数对涂装产品的质量和外观有着直接的影响,需要根据具体情况来调整。
5. 电泳涂装的操作规范操作人员应熟悉电泳涂装设备的使用方法和操作流程,并按照操作规范进行操作。
包括泵的启停、涂装件的悬挂和取下等操作,以及对设备的日常维护和保养等。
6. 质量控制在电泳涂装过程中,需要进行适时的质量控制工作。
主要包括对涂装产品的干膜厚度、硬度、附着力等进行检测。
通过设定合适的质量控制指标,可以及时发现和解决涂装过程中的问题,并保证涂装产品的质量。
7. 设备维护和保养电泳涂装设备需要定期进行维护和保养,以确保其正常运转和延长使用寿命。
定期清洗设备,更换液体和滤网等配件,检查电源和泵的运行情况等都是重要的维护工作。
总之,电泳涂装工艺技术标准的制定对于确保涂装质量和提高生产效率非常重要。
只有按照标准要求进行涂装操作,设定合适的工艺参数,进行质量控制,同时做好设备维护和保养工作,才能获得高质量的电泳涂装效果。
涂装技术要求

架桥机、运梁车涂装技术要求1.1涂装前表面清理1.1.1涂装前表面等级要求1.1.1.1富锌防锈防滑底漆,钢梁表面清理应达到GB/T8923-1988规定的Sa3级。
1.1.1.2涂醇酸、酚醛、聚氨脂底漆,钢梁表面清理应达到GB/T8923-1988规定的Sa2.5级。
1.1.1.3 栏杆、扶手、人行道、吊篮等附属钢结构涂装防锈底漆钢表面清理应达到GB/T8923-1988规定的Sa2级。
1.1.2.涂装前钢梁表面粗糙度要求1.1.2.1.涂装涂料涂层时,钢梁表面粗糙度规定为Rz25~60μm,即符合JB/T6060.5-1998规定。
1.1.2.2.富锌防滑底漆钢梁表面粗糙度Rz50~100μm,即符合JB/T6060.5-1998规定。
1.1.2.3.涂装涂料涂层选用最大粗糙度不超过涂装体系干膜厚度的1/3,表面粗糙度超过规定时,需加涂一道底漆。
1.1.3.钢表面清理用磨料钢表面清理磨料应符合YB/T5149-1993和YB/T5150-1993标准规定的钢丸、钢砂或应使用无盐分和无沾污的石英砂。
1.2.钢梁的涂料涂装体系(见下表)1.3.高强螺栓连接部分摩檫面涂装1.3.1.采用无机富锌防滑防锈涂料,涂层厚度为80μm。
涂层抗滑移系数不小于0.55。
1.4.涂层质量要求1.4.1.涂层表面平整均匀,不允许有剥落、其泡、裂纹、气孔。
1.4.2.金属涂层表面均匀一致,不允许有起皮、股泡、大熔滴、松散粒子、裂纹、掉块。
1.4.3.涂层附着力按GB/T9286-1998规定作划格实验,附着力不底于一级。
1.5试验方法1.5.1表面粗糙度检验1.5.1.1.表面粗糙度采用GB/T8923-1988规定的比较样块进行粗糙度目视和触觉评定。
1.5.1.2.表面粗糙度可用触针式表面轮廓仪测量。
1.5.1.3.峰谷深度可用指针式千分尺。
1.5.2.涂层表面质量检查采用目视法1.5.3涂层厚度检测方法1.5.3.1涂层干膜厚度和湿膜厚度测量,按GB/T13452.2-1992规定进行。
涂装自动线工艺参数表[空白模板]
位置 喷枪喷距cm 喷枪高度 喷枪气压kg
版本:V02
记录保管期限:5年
制作:
审核:
核准:
批量生产烘烤时间
底漆喷枪 喷枪一 喷枪二 喷枪三 喷枪四 喷枪五 喷枪六 喷枪七 喷枪八
位置
PU/橡胶漆 喷枪喷距cm
PU/3.H 注意:
喷枪高度
喷枪气压 kg
中漆枪数 喷枪一 喷枪二 喷枪三 喷枪四 喷枪五 喷枪六 喷枪七 喷枪八
位置
备注: 1.膜厚达标后才能进行小批量试产,小批量试产成功后必须要先填写参数表方可上线. 2.产品头部,侧边,底部,表面,都必须贴膜厚,并都要达到规定膜厚。 2.uv能量上中下最低保证在1000mj/CM²±200mj。
线别/粘度
膜厚 滤网目数
文件编码
产 品 示 图
壳体名称 版次
泵浦压力 (KG)
UV能量
顶灯 侧灯 低灯
第一组灯 强光 中光 弱光
强光
第二组灯
中光
弱光
UV能量控制范围:
加油房 卫生状
况
喷房/喷枪 卫生状况 (OK/KG)
喷房温度 (℃)
喷房湿度 (%)
线体链速(m/min)
喷枪喷距cm
喷枪高度 喷枪气压kg 面漆喷枪 喷枪一 喷枪二 喷枪三 喷枪四 喷枪五 喷枪六 喷枪七 喷枪八
线体:
涂装自动线工艺参数表
日期:
客户 素材颜色
涂层
油漆编号
油漆颜色
机型名称 喷涂颜色 供应商 开油比例
底漆
固化剂
助剂
底漆稀释剂
中漆
固化剂
中漆稀释剂
助剂
面漆光油
面漆哑油
固化剂
水性涂料涂装工艺参数标准
10min
流量计 压力表 压力表 pH计 电导率仪 细菌棒 pH计 电导率仪 压力表 流量计 分析天平,烘箱 细菌棒 压力表 pH计 分析天平,烘箱 压力表 细菌棒 分析天平,烘箱 细菌棒 压力表 电导率仪 pH计 压力表 电导率仪 pH计 压力表
目视 炉温跟踪仪 炉温跟踪仪
100%
100%
100%
30000~65000/min 50~550L/min
(2.3:1)~(2:1.2) 0.4~0.6m/s 21~28℃ 55%~75%RH 5~6.5bar
100~200mL/min (2.3:1)~(2:1.2)
见烘烤数据 20~55μm
制造商数据表
制造商数据表
>80/20°
测定仪 系统压力表 系统压力表 系统压力表 系统压力表 系统压力表
系统仪表 目视
系统压力表 见附着力测试规范/批
次样板 测定仪 系统压力表 系统压力表 系统仪表 系统仪表 系统仪表 系统仪表
目视 系统压力表 见附着力测试规范/批
次样板 测定仪 系统压力表 系统压力表 系统压力表
目视 见附着力测试规范/批
机器人
烘房窗口 压缩空气
温度 湿度 向下风速 向下风速 温度 湿度 油漆流量 电流 旋杯转速 成型空气
烘烤温度
脱水率
湿度 向下风速
温度 湿度 油漆流量 旋杯转速
30
自动喷涂内表面色 漆
机器人
成型空气
向下风速
喷房
温度
31
自动喷涂外表面色 漆
机器人
湿度 油漆流量
电流 旋杯转速
成型空气
向下风速
喷房
温度
32
涂装工艺标准
3 操作工艺3.1 工艺流程:作业准备基面清理防火涂料配料、搅拌底漆涂装检查验收喷涂面漆涂装3.2 钢结构防腐涂料涂装3.2.1 基面清理3.2.1.1 建筑钢结构工程的油漆涂装应在钢结构安装验收合格后进行。
油漆涂刷前,应将需涂装部位的铁锈、焊缝药皮、焊接飞溅物、油污、尘土等杂物清理干净。
3.2.1.2 基面清理除锈质量的好坏,直接关系到涂层质量的好坏。
因此涂装工艺的基面除锈质量分级达到要求。
3.2.1.3为了保证涂装质量,根据不同需要可以分别选用以下除锈工艺。
3.2.1.3.1 喷砂除锈,它是利用压缩空气的压力,连续不断地用石英砂或铁砂冲击钢构件的表面,把钢材表面的铁锈、油污等杂物清理干净,露出金属钢材本色的一种除锈方法。
这种方法效率高,除锈彻底,是比较先进的除锈工艺。
3.2.1.3.2 酸洗除锈,它是把需涂装的钢构件浸放在酸池内,用酸除去构件表面的油污和铁锈。
采用酸洗工艺效率也高,除锈比较彻底,但是酸洗以后必须用热水或清水冲洗构件,如果有残酸存在,构件的锈蚀会更加厉害。
3.2.1.3.3 人工除锈,是由人工用一些比较简单的工具,如刮刀、砂轮、砂布、钢丝刷等工具,清除钢构件上的铁锈。
这种方法工作效率低,劳动条件差,除锈也不彻底。
3.2.2 底漆涂装:3.2.2.1 调合红丹防锈漆,控制油漆的粘度、稠度、稀度,兑制时应充分的搅拌,使油漆色泽、粘度均匀一致。
3.2.2.2 刷第一层底漆时涂刷方向应该一致,接槎整齐。
3.2.2.3 刷漆时应采用勤沾、短刷的原则,防止刷子带漆太多而流坠。
3.2.2.4 待第一遍刷完后,应保持一定的时间间隙,防止第一遍未干就上第二遍,这样会使漆液流坠发皱,质量下降。
3.2.2.5 待第一遍干燥后,再刷第二遍,第二遍涂刷方向应与第一遍涂刷方向垂直,这样会使漆膜厚度均匀一致。
3.2.2.6 底漆涂装后起码需4~8h 后才能达到表干、表干前不应涂装面漆。
3.2.3 面漆涂装:3.2.3.1 建筑钢结构涂装底漆与面漆一般中间间隙时间较长。
涂装前处理工艺参数
脱脂工艺参数工作时间:15-20分钟
温度:50-55度
总碱度:80-90
PH 值:PH>14
提升批次:3-4次
水洗工艺参数
(脱脂后)
工作时间:2-3分钟(保持溢流状态)温度:常温
PH 值:7-8
提升批次:2-3次
酸洗工艺参数工作时间:8-10分钟
温度:常温
PH 值:1<PH
提升批次:2-3次
水洗工艺参数
(酸洗后)
工作时间:2-3分钟(保持溢流状态)温度:常温
PH 值:6-7
提升批次:2-3次
中和工艺参数工作时间:2-3分钟
温度:常温
PH 值:9-10
提升批次:2-3次
水洗工艺参数
(中和后)
工作时间:2-3分钟(保持溢流状态)温度:常温
PH 值:7-8
提升批次:2-3次
表调工艺参数工作时间:2-3分钟
温度:常温
PH 值:8-9
提升批次: 2-3次
磷化工艺参数工作时间:15-20分钟
温度:35-40度
总酸度:40-50
游离酸度:2.5
PH 值:2-3
提升批次:2-3次
水洗工艺参数
(磷化后)
工作时间:2-3分钟(保持溢流状态)温度:常温
PH 值:6-7
提升批次:2-3次
钝化工艺参数工作时间:3-5分钟
温度:常温
PH 值:6-7
提升批次:2-3次。
- 1、下载文档前请自行甄别文档内容的完整性,平台不提供额外的编辑、内容补充、找答案等附加服务。
- 2、"仅部分预览"的文档,不可在线预览部分如存在完整性等问题,可反馈申请退款(可完整预览的文档不适用该条件!)。
- 3、如文档侵犯您的权益,请联系客服反馈,我们会尽快为您处理(人工客服工作时间:9:00-18:30)。
涂装工艺技术参数
一、施工环境条件
1. 最佳施工环境条件为环境温度10-40℃,湿度30-70% 。
2. 空气湿度不得大于80%。
在湿度大于80%气候情况下,喷漆前需对工件进行烘烤,温度70-80℃(工件基体温度),保温时间30分钟。
3. 要求在配漆和施工环境中配置温度计和湿度计。
二、涂料调配(指加入固化剂后)
1.按涂料技术参数进行调配。
2.涂料调配好后需进行过滤除去涂料中杂质,底漆用180目、中涂用180-240目、面漆用300-320目滤布过滤。
3.涂料调配后放置8-10分钟,使涂料熟化后再喷涂。
(此点需严格执行)
4.涂料调配后应在4小时内使用完。
三、喷涂前准备工作
1.工件在喷涂前应做到干净、干燥;施工场地保持清洁干净,喷漆室每天进行清扫,定期对喷漆室送风过滤棉清理干净。
2.采用空气喷涂时必须安装冷干机(或油水分离器),每天上午和下午各排放一次油、水,湿度大的季节,还需增加排放油、水次数,保证压缩空气无油和水份等杂质。
3.喷漆工和相关接触人员在工作中应做好劳动安全保护,穿戴防毒口罩、手套、工作服等劳保用品,防止吸入有毒溶剂、尘埃等。
四、底、面漆技术参数
1. 大光黄底漆
(1)稀释剂:茸康大光黄底漆稀释剂;
(2)固化剂:进口固化剂;
(3)配比:进口固化剂=4:1(重量比);
(4)粘度:16-25秒;
2. SPU70815P-Y黄色聚氨酯中涂
(1) 稀释剂:RUT-085稀释剂(快干型,在15℃以下气温情况使用)或XPS90018溶
剂(慢干型,15℃以上<含15℃>气温情况下使用);
(2) 固化剂:GXH63417聚氨酯固化剂;
(3) 配比: GXH63417聚氨酯固化剂=7:1(重量比);
(4) 粘度:14-25秒;
3. SPU70806T-Y聚氨酯面漆(或SPU70807T-GY聚氨酯面漆)
(1) 稀释剂:RUT-085稀释剂(快干型,在15℃以下气温情况使用)或XPS90018溶
剂(慢干型,15℃以上<含15℃>气温情况下使用);
(2) 固化剂:GXH63417聚氨酯固化剂;
(3) 配比: GXH63417聚氨酯固化剂=4:1(重量比);
(4) 粘度:14-25秒;
4.干燥:
(1) 烘干温度需达到70-80℃(工件基体温度),保温时间30分钟;
(2) 工件进烘干室前需流平8-10分钟;
(3) 如常温自然干燥,干燥时间应大于24小时后才能开始涂刮腻子或喷涂面漆;
5.漆膜厚度要求:
(1) 底漆的干膜厚度应达到20- 35um;
(2) 面漆的干膜厚度应达到40- 60um;
(3) 涂膜总厚度:70μm≤磷化件≤100μm ,80μm≤抛丸喷砂件≤110μm;
五、腻子刮磨
1. 腻子桶打开后,观察腻子表面有无结皮,如有则去掉,然后将整桶腻子搅拌均匀;
2. 严格按原子灰配比(一般为原子灰:固化剂=100:2-3)要求调配腻子,在气温高情况下,不能减少固化剂用量,而应适当减少每次原子灰调配量,并充分搅拌均匀颜色一致;
3. 在刮涂腻子时应以工件表面为基准,刮平凹处,尽量使腻子薄而平整;
4. 如存在较大凹坑,应分多次填刮,每次刮涂厚度不应超过1mm,且需在上道腻子干燥后进行;
5. 腻子经干燥打磨后,整个表面应平整光滑,线角分明,腻子与涂层表面连接处不得有明显接痕,无漆粒等杂质附在工件表面上;
6. 擦净:用压缩空气全面擦吹净后再用粘性纱布按一个方向擦净工件表面;。