常见纸板问题及解决方案
瓦楞纸板常见纸病的解决方案

瓦楞纸板常见纸病的解决方案一、开胶、假粘1、里纸开胶原因分析:1.1胶质量不符生产要求或腐败变质;1.2上胶量太小;1.3车速过快,瓦楞辊、压力辊热量不足;1.4压力辊压力不足;1.5瓦楞辊、压力辊的中高严重磨损。
解决方法:1.1更换合格胶液;1.2适量调大涂胶量;1.3提高瓦楞辊、压力辊温度,保证180℃以上开机,同时根据温度情况调整车速;1.4适当调整压力辊压力,以里、瓦纸粘合良好,里纸不露楞、瓦纸不碎为宜;1.5打磨或更换新压力辊、瓦楞辊。
1、面纸开胶、夹芯开胶原因分析:2.1胶量过小、烘干机速度过慢;2.2胶液稀薄,涂胶辊挂胶不足;2.3烘干机热板温度不足,胶液未充分糊化;2.4烘干机车速过快,纸板烘干不足;2.5烘干机传输带上面的压载辊没完全落下。
解决方法:2.1适当加大涂胶量,并酌情提高车速;2.2更换胶液或在原胶液中加入适量乳化剂;2.3升高烘干机热板温度至180℃以上开机;2.4减慢车速;2. 5落下压载浮辊。
原因分析:3.1瓦楞辊温度不足;3.2胶量过小,温度过高;3.3车速缓慢造成萃胶;3.4胶液黏度不够。
解决方法:3.1提高单面机工作温度;3.2调整涂胶量,关闭热源,待温度下降至180℃以下,160℃以上开机;3.3提高单面机速度;3.4适当增加胶液黏度。
2、面纸假粘原因分析:4.1烘干机热板温度不足;4.2胶液沉淀变质;4.3纸板在烘干机内停留时间过长。
解决方法:4.1待温度达到胶液能糊化时开机;4.2更换新胶;4.3尽量减少停机时间,换单换纸和断纸再续时动作要果断迅速。
二、倒楞1、单面纸板倒楞原因分析:1.1瓦楞辊磨损;1.2上下瓦楞辊间隙过大;1.3瓦楞纸定量太高且厚度太厚;1.4瓦楞纸水分过大;1.5瓦楞纸未经预热器,可塑性差。
解决方法:1.1磨削或更换瓦楞辊;1.2调整瓦楞辊间隙至0.5mm;1.3更换瓦楞纸;1.4调大预热包角,增大预热面积;1.5将瓦楞纸穿过预热器。
纸板强不高的原因和解决方法

书山有路勤为径;学海无涯苦作舟纸板强不高的原因和解决方法在纸板自动化生产过程中,几乎所有的厂家都希望纸板强度高、挺度好。
但往往事与愿违,不少厂家生产的纸板软、强度低,客户不满意,甚至达不到国家标准。
那幺,造成这些问题的原因是什幺呢?本文就此类原因作出分析并提出解决问题的办法,供广大纸板生产厂家参考。
一、纸板水分过高。
解决办法是降低纸板的水分。
造成纸板水分高的因素有很多,而且情况也比较复杂,具体分析及解决办法如下:1.纸板生产线所用胶水水分多。
解决办法:降低胶水中的水分。
2.涂胶量大。
造成涂胶一大有两种原因:一是涂胶辊之间的狭缝大。
解决办法是适当调小涂胶辊的狭缝。
二是狭缝不变的情况下,胶的粘度过大。
实际涂胶量会相对增大;胶的粘度小,实际涂胶量明显小。
粘度过小时,涂胶量很小,甚至涂不上胶。
解决办法:调整涂胶辊狭缝大小适中,确保涂胶量合适。
另外,在配胶时,保持胶的粘度大小基本一致。
胶的粘度差别较大时,应随时调整狭缝大小,确保涂胶量适中。
3.开机速度过快。
纸板在烘干道中停留时间短,烘干时间不够。
解决办法,根据情况控制合理的开机速度。
4.蒸气压力低。
解决办法:升高蒸气压力;如果不能提高蒸气压力,只能适当降低开机速度。
5.纸板自身水分高。
同一纸厂的纸张不分不是恒定的,同一批进来的纸,水分也是有高有低。
解决办法:控制纸张的水分,纸张水分过高,不宜采用。
6.空气湿度高,水分挥发不出去。
解决办法:只能适当的降低开机速度,延长烘干时间,降低纸的水分。
专注下一代成长,为了孩子。
分析纸板爆线原因及解决方法
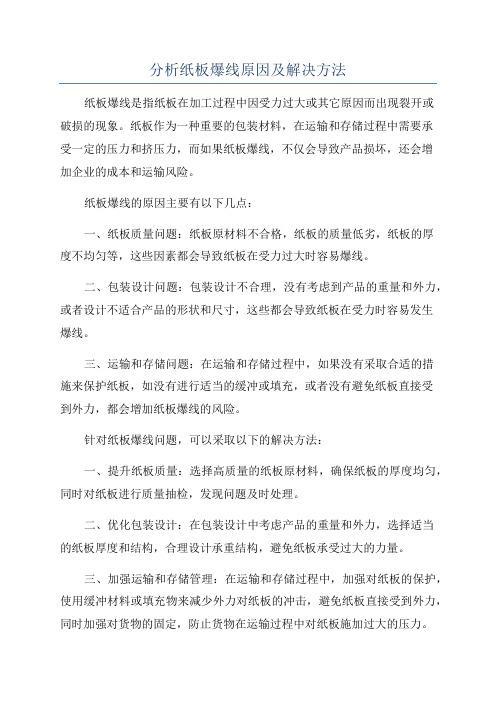
分析纸板爆线原因及解决方法纸板爆线是指纸板在加工过程中因受力过大或其它原因而出现裂开或破损的现象。
纸板作为一种重要的包装材料,在运输和存储过程中需要承受一定的压力和挤压力,而如果纸板爆线,不仅会导致产品损坏,还会增加企业的成本和运输风险。
纸板爆线的原因主要有以下几点:一、纸板质量问题:纸板原材料不合格,纸板的质量低劣,纸板的厚度不均匀等,这些因素都会导致纸板在受力过大时容易爆线。
二、包装设计问题:包装设计不合理,没有考虑到产品的重量和外力,或者设计不适合产品的形状和尺寸,这些都会导致纸板在受力时容易发生爆线。
三、运输和存储问题:在运输和存储过程中,如果没有采取合适的措施来保护纸板,如没有进行适当的缓冲或填充,或者没有避免纸板直接受到外力,都会增加纸板爆线的风险。
针对纸板爆线问题,可以采取以下的解决方法:一、提升纸板质量:选择高质量的纸板原材料,确保纸板的厚度均匀,同时对纸板进行质量抽检,发现问题及时处理。
二、优化包装设计:在包装设计中考虑产品的重量和外力,选择适当的纸板厚度和结构,合理设计承重结构,避免纸板承受过大的力量。
三、加强运输和存储管理:在运输和存储过程中,加强对纸板的保护,使用缓冲材料或填充物来减少外力对纸板的冲击,避免纸板直接受到外力,同时加强对货物的固定,防止货物在运输过程中对纸板施加过大的压力。
四、加强员工培训和意识提高:培训员工掌握正确的包装和操作方法,增强员工对纸板爆线问题的意识,提高操作技能和注意力,减少因操作不当导致纸板爆线的情况发生。
五、加强供应商管理:与供应商建立良好的合作关系,对供应商进行审核和监督,确保供应商提供的纸板符合标准和质量要求。
六、进行事故分析和改进:对纸板爆线问题进行事故分析,找出问题发生的原因和根本原因,制定改进措施,并及时进行改进,以减少纸板爆线问题的发生。
综上所述,纸板爆线问题虽然可能会导致产品损坏和运输风险增加,但通过提升纸板质量、优化包装设计、加强运输和存储管理、加强员工培训和供应商管理等方式,可以有效减少纸板爆线问题的发生,提高包装的质量和效果,为企业的运营和产品质量保驾护航。
纸板及纸箱制造常见问题解决方法
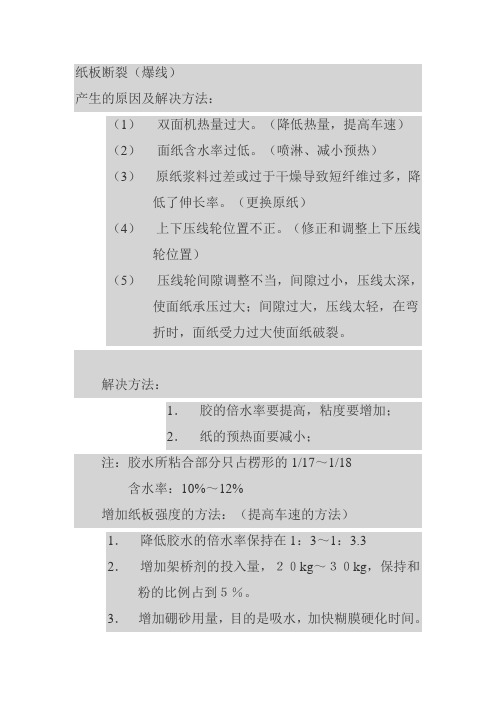
纸板断裂(爆线)产生的原因及解决方法:(1)双面机热量过大。
(降低热量,提高车速)(2)面纸含水率过低。
(喷淋、减小预热)(3)原纸浆料过差或过于干燥导致短纤维过多,降低了伸长率。
(更换原纸)(4)上下压线轮位置不正。
(修正和调整上下压线轮位置)(5)压线轮间隙调整不当,间隙过小,压线太深,使面纸承压过大;间隙过大,压线太轻,在弯折时,面纸受力过大使面纸破裂。
解决方法:1.胶的倍水率要提高,粘度要增加;2.纸的预热面要减小;注:胶水所粘合部分只占楞形的1/17~1/18含水率:10%~12%增加纸板强度的方法:(提高车速的方法)1.降低胶水的倍水率保持在1:3~1:3.32.增加架桥剂的投入量,20kg~30kg,保持和粉的比例占到5%。
3.增加硼砂用量,目的是吸水,加快糊膜硬化时间。
随着瓦楞芯纸波纹的起伏,面纸在纸板的表面上做不平坦的蹦紧,形如“搓板”亦称“搓板状”纸板,它的成型原因是:■糊的粘度过大,或上糊量过多。
当楞峰与面纸粘合受到压力时,多余的浆糊被挤出而附到楞峰的两侧,在楞峰的宽度上形成一个比实际所需要宽得多的涂糊区域,随着糊液的干燥而收缩,使面纸在瓦楞峰两侧被拉下陷,形成“搓板”而在表面上露出楞痕。
克重较高的纸,其刚性较大,可抵抗这种收缩拉力,下陷量就要少些,故在使用较薄或克重较小的面纸时,要注意减少上糊量,即要将糊辘与刮糊辘的间隙调小一些,以减少“搓板”现象的发生。
■瓦楞辊磨损以后,其楞峰半径增大。
因而易吸收更多的粘合剂,就容易导致“搓板”现象的发生。
■糊辘与下瓦楞辊的速度不协调,因而粘合剂集中到楞肩的一侧,引起面纸在一侧收缩。
■面纸的含水率过高,在粘合剂干燥以后,引起面纸的收缩下陷。
纸板曲翘纸板曲翘是指纸板在较大的范围内凸起或凹下。
有一种纸板曲翘叫“正向曲翘”,又称“向上曲翘”,即纸板向面纸一侧凸起。
反之是“反向曲翘”。
一边凸起,另一边凹下,是“S型曲翘”,以纸板对角线为轴展开的弯翘为“扭曲曲翘”。
纸箱纸板各种常见不良的解决方案

纸箱纸板各种常见不良的解决方案纸箱纸板在使用过程中常会出现一些不良,如折痕、开胶、断裂等问题。
下面是纸箱纸板常见不良的解决方案。
一、折痕问题1.质量控制:加强材料的质量管理,确保纸板的强度和刚度满足要求。
2.设计优化:合理设计纸箱的结构,避免出现折痕问题。
比如在纸箱侧面加强支撑板等。
3.减少叠压:降低堆码的高度和层数,减少纸箱在运输和存储过程中的压力,以减少折痕问题的发生。
二、开胶问题1.使用优质胶水:选择质量好的胶水,确保胶水的黏性和耐久性。
2.加强胶线的密度:增加胶线的密度,使胶层更加紧密,提高胶线的附着力。
3.加强胶合工艺:在胶水施加和压合的过程中,合理控制压力和温度,确保胶水完全固化粘结。
三、断裂问题1.加强纸板的强度:控制纸浆浓度和纤维长度,增加纸板的强度。
2.加强纸板的厚度:增加纸板的厚度,提高其负荷能力和抗拉强度。
3.加强纸板的湿强度:通过调整纸板的湿度和环境温度等条件,提高纸板的湿强度,减少断裂问题的发生。
四、印刷问题1.控制印刷压力:合理调整印刷机的压力,确保印刷品的清晰度和准确度。
2.提高油墨附着力:选择合适的油墨和印版,控制油墨的粘度和稠度,以提高油墨的附着力。
3.加强印刷技术培训:加强对印刷工人的技术培训,提高他们的专业素养和操作技巧。
五、包装问题1.加强包装材料的质量:选择优质的包装材料,提高其防潮、防震和防撞能力。
2.加强包装设计:合理设计包装结构,增加包装材料的厚度和缓冲层,提高纸箱的抗震能力。
3.加强包装测试:进行包装材料和纸箱的抗压试验,确保其在运输和储存过程中的安全性。
总之,要解决纸箱纸板的常见不良问题,需要从质量控制、设计优化、工艺改进和包装提升等多个方面入手,确保纸箱纸板的质量和性能满足使用要求。
纸板印刷常见问题

第二种涂上的油墨因为PH值太高或太低无法被印在承 印物上 因为承印物的质量问题,涂上的油墨不干
印迹模糊 印迹不干净
第二种涂上的油墨与第一种涂上的油墨互相不溶
由于油墨层太厚而油墨不干(涂墨层太多)
因承印物的表面质量问题导致油墨不干 油墨本身干燥功能不足 油墨配方问题 承印物上有油墨层不均(印迹旁边有晕圈或整体的印 刷颜色不均) 印版上有污点 带纸轮与印版原件不对齐 折带磨损或滑落 输纸导板或杆碰到印刷图案 堆纸机传送带碰到印刷图案 印刷机附件使印迹模糊 模切或折叠操作中,平台垫粗糙或磨损模切压力太大 印刷机上一个或多个辊或辊筒尺寸不当引起辊筒和瓦 楞纸板的线速度比率不准确,纸板进入印刷机前印板 上油墨太多
调整刮墨辊 调换刮墨辊 调整刮墨刀 调换刮墨刀 清除网纹辊上的污垢 调换网纹辊 减少网纹辊和印刷辊筒之间的距离 调换网纹辊 向造纸厂或油墨供应商技术代表寻求帮助 减少印刷辊筒和压印辊筒之间的距离或调换瓦楞纸板 增加新油墨或使用另一墨盒中的油墨 清除印版上的污垢或调换印版 咨询印版供应商,使用标准硬度计 增加印版在承印物上的压力 通过一些措施增加油墨层的厚度:增加油墨年度;降低网纹 辊的载墨量;增加网纹辊中油墨流量;根据承印物表面吸水 性质重新配方油墨 使用硬度小些的印版 添加剂的建议 加入溶解速度慢的溶剂,减少印版表面的气流或热流;提高 机器运行速度 检查并调整油墨的PH值至符合标准 填充印版凹点;调换印版 检查平行状况,必要时进行调整 如果可能调换墨色的印刷顺序 减少油墨的流量,用最小的油墨量达到最好的油墨覆盖效果 浅颜色的油墨必须先涂上而且粘度一定要比第二种颜色的油 墨高 通过以下方式,提高油墨变干速度:降低先涂上的油墨的粘 度;用较好的刮墨装置降低油墨层的厚度;改变油墨配方以 加快变干速度;降低印刷机的运转速度;减少网纹辊的油墨 流量;提高干燥器的温度 增加第二种油墨的粘度并使之比第一种油墨的粘度高 通过以下措施降低变干速度:加入降低变干速度的溶剂(慢 干剂);停止印版上的气流或热流;提高印刷机运转速度 调整油墨的PH值,使之符合油墨供应商推荐的规格或调换 油墨 调换承印物,降低油墨墨层厚度或加强油墨干燥系统功能
常见的瓦楞纸板缺陷及其解决方法
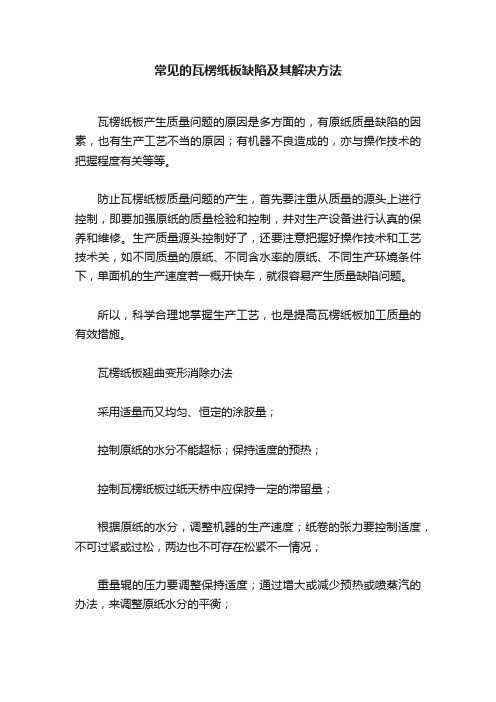
常见的瓦楞纸板缺陷及其解决方法瓦楞纸板产生质量问题的原因是多方面的,有原纸质量缺陷的因素,也有生产工艺不当的原因;有机器不良造成的,亦与操作技术的把握程度有关等等。
防止瓦楞纸板质量问题的产生,首先要注重从质量的源头上进行控制,即要加强原纸的质量检验和控制,并对生产设备进行认真的保养和维修。
生产质量源头控制好了,还要注意把握好操作技术和工艺技术关,如不同质量的原纸、不同含水率的原纸、不同生产环境条件下,单面机的生产速度若一概开快车,就很容易产生质量缺陷问题。
所以,科学合理地掌握生产工艺,也是提高瓦楞纸板加工质量的有效措施。
瓦楞纸板翘曲变形消除办法采用适量而又均匀、恒定的涂胶量;控制原纸的水分不能超标;保持适度的预热;控制瓦楞纸板过纸天桥中应保持一定的滞留量;根据原纸的水分,调整机器的生产速度;纸卷的张力要控制适度,不可过紧或过松,两边也不可存在松紧不一情况;重量辊的压力要调整保持适度;通过增大或减少预热或喷蒸汽的办法,来调整原纸水分的平衡;控制单面机或双面机生产环境保持稳定的温湿度;瓦楞辊、压力辊、活动辊和预热辊要调整保持平衡状态;对使用磨损厉害的瓦楞辊应更换新辊;切忌将含水率高低悬殊过大的瓦楞纸、面纸或里纸(箱板纸)进行配套成型加工。
瓦楞纸板出现搓衣板状变形的原因瓦楞纸板由于受到温度、黏合剂和机器张力和原纸质量等方面的作用,就容易出现搓衣板状变形。
产生原因:1、原纸的纤维组织的伸缩率差异较大;2、面纸或里纸的定量偏低和原纸的纤维组织过于柔软的话,成型后其挺度相应也就差;3、黏合剂涂布量过多或不均匀时,使瓦楞楞顶两侧边缘也有胶液,当其与面纸或里纸黏结干燥后,由于收缩作用导致对面纸或里纸构成一定扭力;4、黏合剂的黏度偏低,与里纸或面纸的纤维组织没有很好地黏结成坚固的整体;5、单面机或双面机的瓦楞辊、压力辊间隙不适、不平衡;6、瓦楞辊楞齿顶磨损严重时,由于楞齿顶面积增大而加大胶的涂布量,使面纸或里纸黏结后容易变形;7、瓦楞辊、压力辊或预热辊的温度过高或过低等情况存在时,都容易使瓦楞纸板成型后出现搓衣板状变形现象。
纸箱、纸板存在质量问题解决方法

纸箱、纸板存在质量问题解决方法纸箱、纸板质量的好坏是企业的生命,也那时各企业各项管理工作的综合反映,必须加强领导、加强管理、坚持质量第一。
纸箱质量的好坏主要取决于瓦楞纸板、纸箱和高质量的成型工艺――印刷、开槽、压线、钉箱等。
随着纸箱行业竞争的日益激烈,客户对纸箱质量要求越来越高,这就是要求纸箱生产厂家不断提高产品质量,杜绝各种质量事故的发生,力争质量零缺陷,适应市场要求,争取良好的经济效益和社会效益。
一、纸箱、纸板存在的质量问题及产生的原因根据我们多年对纸箱质量问题的调查研究和行业统计资料分析发现,纸箱、纸板经常出现以下质量问题:1、纸箱尺寸不准确纸箱的设计、加工都离不开尺寸。
纸箱尺寸分内径尺寸、外径尺寸、加工尺寸。
内径尺寸必须保证内装物的最大尺寸再加3-5mm;外径尺寸也必须满足集装箱、火车车厢、卡车装运的要求;加工尺寸与内径尺寸、外径尺寸、纸板厚度有关。
尺寸大小马虎不得,搞错了,加工出的纸箱也就成了一批废品,造成经济损失。
2、版面印刷质量差纸箱表面印刷,一般采用文字、数字印刷较对多,很容易产生字母、数字排列不整齐,大小不一、上下歪斜、不规范、不标准,出现问题又未得到及时纠正和版面校对、勘误,让产品带着质量问题流入市场,导致整批纸箱报废。
版面印刷模糊,颜色深浅不一和跑版,也直接影响纸箱美观及质量。
跑版颜色深浅不一,主要是对水墨的粘度控制不好,传墨状态、送纸状态不稳定,纸板的平整度不好所造成。
版面模糊,大部分是由于印刷压力过大,版面上多余的印刷痕迹所致,需要在印刷工序中重点进行控制。
好的印刷纸板,其产品整体效果好,也会得到用户的好评。
3、纸箱摇盖撕裂纸箱摇盖耐折度是纸箱质量的一个重要指标,在使用中客户要求非常严格,摇盖向里、外下折180度5次,里、外面纸都不得有折裂。
这就需要控制好原材料的质量,不使用粗糙和抵挡瓦楞原纸,因为这样的瓦楞原纸可能会导致摇盖折叠时发生断裂,令纸和纸板不平,也是造成摇盖断裂的主要原因,因此在生产中一定要控制好纸和纸板的含水率,防止摇盖断裂。
- 1、下载文档前请自行甄别文档内容的完整性,平台不提供额外的编辑、内容补充、找答案等附加服务。
- 2、"仅部分预览"的文档,不可在线预览部分如存在完整性等问题,可反馈申请退款(可完整预览的文档不适用该条件!)。
- 3、如文档侵犯您的权益,请联系客服反馈,我们会尽快为您处理(人工客服工作时间:9:00-18:30)。
书山有路勤为径;学海无涯苦作舟
常见纸板问题及解决方案
现在瓦楞纸箱的制作工艺越来越精良,但是在实际生产中还是存在很多品质问题。
对于广大纸箱生产厂家,解决纸板问题是提高纸箱成品质量的关键。
“搓板状”纸板
随着瓦楞芯纸波纹的起伏,面纸在纸板的表面上做不平坦的蹦紧,
形如“搓板”亦称“搓板状”纸板,它的成型原因是:
糊的粘度过大,或上糊量过多。
当楞峰与面纸粘合受到压力时,多
余的浆糊被挤出而附到楞峰的两侧,在楞峰的宽度上形成一个比实际所需要宽得多的涂糊区域,随着糊液的干燥而收缩,使面纸在瓦楞峰两侧被拉下陷,形成“搓板”而在表面上露出楞痕。
克重较高的纸,其刚性较大,
可抵抗这种收缩拉力,下陷量就要少些,故在使用较薄或克重较小的面纸时,要注意减少上糊量,即要将糊辘与刮糊辘的间隙调小一些,以减少“搓板”现象的发生。
瓦楞辊磨损以后,其楞峰半径增大。
因而易吸收更多的粘合剂,就
容易导致“搓板”现象的发生。
糊辘与下瓦楞辊的速度不协调,因而粘合剂集中到楞肩的一侧,引
起面纸在一侧收缩。
面纸的含水率过高,在粘合剂干燥以后,引起面纸的收缩下陷。
纸板曲翘
纸板曲翘是指纸板在较大的范围内凸起或凹下。
有一种纸板曲翘叫“正向曲翘”,又称“向上曲翘”,即纸板向面纸一侧凸起。
反之是“反向
曲翘”。
一边凸起,另一边凹下,是“S型曲翘”,以纸板对角线为轴展开
专注下一代成长,为了孩子。