金属表面化学热处理技术与应用
金属材料的热处理和表面处理
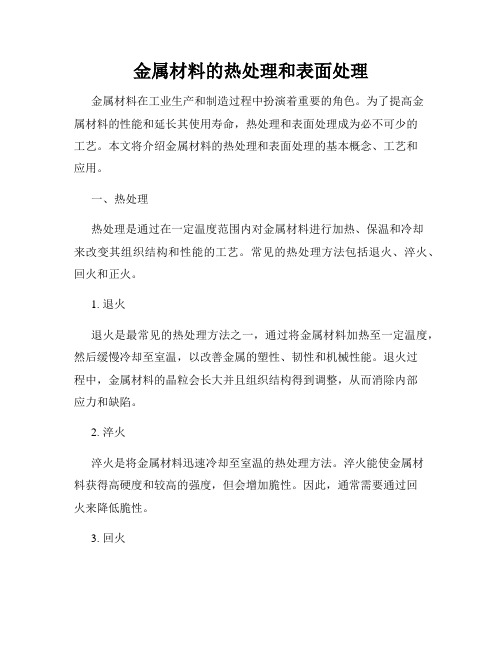
金属材料的热处理和表面处理金属材料在工业生产和制造过程中扮演着重要的角色。
为了提高金属材料的性能和延长其使用寿命,热处理和表面处理成为必不可少的工艺。
本文将介绍金属材料的热处理和表面处理的基本概念、工艺和应用。
一、热处理热处理是通过在一定温度范围内对金属材料进行加热、保温和冷却来改变其组织结构和性能的工艺。
常见的热处理方法包括退火、淬火、回火和正火。
1. 退火退火是最常见的热处理方法之一,通过将金属材料加热至一定温度,然后缓慢冷却至室温,以改善金属的塑性、韧性和机械性能。
退火过程中,金属材料的晶粒会长大并且组织结构得到调整,从而消除内部应力和缺陷。
2. 淬火淬火是将金属材料迅速冷却至室温的热处理方法。
淬火能使金属材料获得高硬度和较高的强度,但会增加脆性。
因此,通常需要通过回火来降低脆性。
3. 回火回火是将淬火后的金属材料加热至一定温度,然后以适当速度冷却的过程。
回火旨在降低金属材料的硬度和脆性,提高其韧性和塑性,以适应不同的使用要求。
4. 正火正火是将金属材料加热至临界点以上,然后冷却至室温的热处理过程。
正火能改善金属材料的硬度、强度和韧性,并且能提高金属材料的耐磨性能。
二、表面处理表面处理是通过对金属材料表面进行物理、化学或电化学处理,以提高金属材料的耐腐蚀性、耐磨性、装饰性和功能性。
常见的表面处理方法包括电镀、喷涂、热喷涂和阳极氧化。
1. 电镀电镀是利用电解质溶液中的金属离子,通过电解沉积在金属材料表面,形成一层金属膜的过程。
电镀可以改善金属材料的外观,提高其耐腐蚀性和耐磨性,同时也可以增加金属材料的导电性和焊接性。
2. 喷涂喷涂是将涂料通过喷枪均匀地喷洒在金属材料表面的过程。
喷涂能够形成一层保护膜,提供金属材料防锈、防腐蚀和装饰的功能。
常见的喷涂涂料有涂胶、烤漆和粉末涂料等。
3. 热喷涂热喷涂是将金属粉末或陶瓷粉末加热至熔点,然后通过喷枪喷射在金属材料表面形成涂层的过程。
热喷涂能够提高金属材料的抗腐蚀性、耐磨性和耐高温性,常用于航空航天和化工等领域。
金属表面处理及热处理加工与表面处理的区别
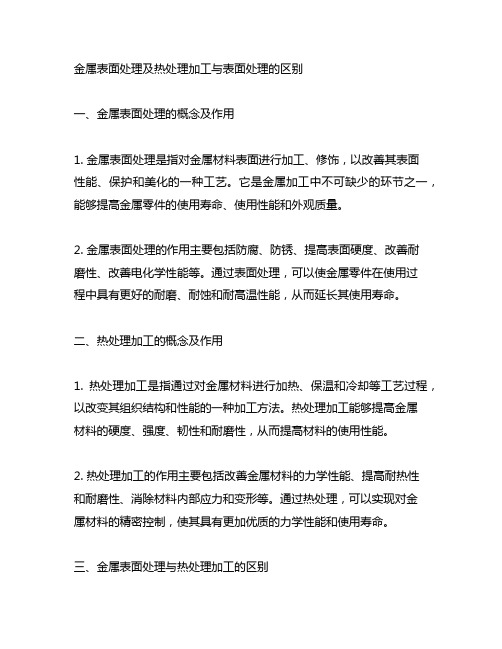
金属表面处理及热处理加工与表面处理的区别一、金属表面处理的概念及作用1. 金属表面处理是指对金属材料表面进行加工、修饰,以改善其表面性能、保护和美化的一种工艺。
它是金属加工中不可缺少的环节之一,能够提高金属零件的使用寿命、使用性能和外观质量。
2. 金属表面处理的作用主要包括防腐、防锈、提高表面硬度、改善耐磨性、改善电化学性能等。
通过表面处理,可以使金属零件在使用过程中具有更好的耐磨、耐蚀和耐高温性能,从而延长其使用寿命。
二、热处理加工的概念及作用1. 热处理加工是指通过对金属材料进行加热、保温和冷却等工艺过程,以改变其组织结构和性能的一种加工方法。
热处理加工能够提高金属材料的硬度、强度、韧性和耐磨性,从而提高材料的使用性能。
2. 热处理加工的作用主要包括改善金属材料的力学性能、提高耐热性和耐磨性、消除材料内部应力和变形等。
通过热处理,可以实现对金属材料的精密控制,使其具有更加优质的力学性能和使用寿命。
三、金属表面处理与热处理加工的区别1. 目的不同:金属表面处理主要是为了改善表面性能,如耐腐蚀、耐磨等;而热处理加工旨在改善整体材料的力学性能,如硬度、强度等。
2. 方法不同:金属表面处理多采用化学处理、机械加工等方式,以在表面形成一层保护膜或改变表面状态;而热处理加工则通过加热、保温和冷却等工艺过程改变材料的组织结构和性能。
3. 范围不同:金属表面处理更偏向于表面的零部件加工和改良;热处理加工则涉及到整体材料的加工和性能提升。
四、个人观点及总结在金属加工领域,金属表面处理和热处理加工都扮演着十分重要的角色。
金属表面处理能够改善金属零件的表面性能,从而提高其使用寿命和稳定性;而热处理加工则能够提升整体材料的力学性能,使其在各种特殊条件下都能够保持优质的性能特性。
两者相辅相成,为金属加工领域的高质量发展提供了重要支撑。
在以后的工程实践中,我会更加注重金属材料的综合加工处理,同时加强对金属表面处理和热处理加工的深入学习和实践应用,以提高自己在金属加工领域的专业技能和水平。
金属材料表面处理工艺的研究与应用
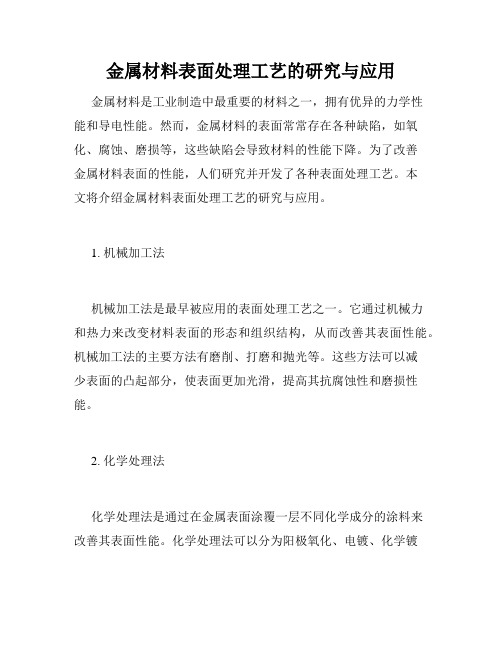
金属材料表面处理工艺的研究与应用金属材料是工业制造中最重要的材料之一,拥有优异的力学性能和导电性能。
然而,金属材料的表面常常存在各种缺陷,如氧化、腐蚀、磨损等,这些缺陷会导致材料的性能下降。
为了改善金属材料表面的性能,人们研究并开发了各种表面处理工艺。
本文将介绍金属材料表面处理工艺的研究与应用。
1. 机械加工法机械加工法是最早被应用的表面处理工艺之一。
它通过机械力和热力来改变材料表面的形态和组织结构,从而改善其表面性能。
机械加工法的主要方法有磨削、打磨和抛光等。
这些方法可以减少表面的凸起部分,使表面更加光滑,提高其抗腐蚀性和磨损性能。
2. 化学处理法化学处理法是通过在金属表面涂覆一层不同化学成分的涂料来改善其表面性能。
化学处理法可以分为阳极氧化、电镀、化学镀等多种方法。
这些方法可以形成一层保护膜,防止金属表面氧化、腐蚀和磨损。
3. 热处理法热处理法是通过在金属表面加热而改变其组织结构和性能。
常用的热处理方法有退火、正火、淬火和回火。
这些方法可以改善材料的硬度、强度和韧性等力学性能,同时也可以改善抗腐蚀性和耐磨性等表面性能。
4. 薄膜涂覆法薄膜涂覆法是在金属表面涂覆一层薄膜,这些薄膜可以分为有机薄膜和金属薄膜两类。
有机薄膜如聚合物、防护漆等可以保护金属表面免受腐蚀和磨损。
而金属薄膜如氧化铬膜和氮化硅膜可以提高材料表面硬度和耐磨性能。
总之,金属材料表面处理工艺的研究与应用对于提高材料表面性能和延长材料寿命具有重要意义。
随着科技的进步和工艺的发展,人们相信会有更多更高效的表面处理方法被应用到实际生产中,为各行各业的发展带来更多贡献。
常用金属表面处理工艺及技术

金属表面处理工艺一、表面热处理1、表面淬火 n 表面淬火是指在不改变钢的化学成分及心部组织情况下,利用快速加热将表层奥氏体化后进行淬火以 强化零件表面的热处理方法。
感火焰加热 应加 热n 表面淬火目的: n ① 使表面具有高的硬度、耐磨性和疲劳极限; n ② 心部在保持一定的强度、硬度的条件下,具有足够的塑性和韧性。
即表硬里韧。
n 适用于承受弯曲、扭转、摩擦和冲击的零件。
轴 的 感 应 加加 热 表 面 淬淬 火n ①表面淬火用材料 n ⑴ 0.4-0.5%C的中碳钢。
n 含碳量过低,则表面硬度、耐磨性下降。
n 含碳量过高,心部韧性下降; n ⑵ 铸铁 提高其表面耐磨性。
机床导轨表面淬火齿轮n ②预备热处理 n ⑴工艺: n 对于结构钢为调质或正火。
n 前者性能高,用于要求高的重要件,后者用于要求不高的普 通件。
n ⑵目的: n 为表面淬火作组织准备; n 获得最终心部组织。
回火索氏体 索氏体n ③表面淬火后的回火 n 采用低温回火,温度不高于200℃。
n 回火目的为降低内应力,保留淬火高硬度、耐磨性。
n ④表面淬火+低温回火后的组织 n 表层组织为M回;心部组织为S回(调质)或F+S(正火)。
感应加热表面淬火 感应淬火机床n ⑤表面淬火常用加热方法 n ⑴ 感应加热: 利用交变电流在工件表面感应巨大涡流, 使工件表面迅速加热的方法。
感应加热 表面淬火示意图n 感应加热分为: n 高频感应加热频率为250-300KHz,淬 硬层深度0.5-2mm火传 感动 应轴 器连续 淬感应加热表面淬火齿轮的截面图n 中频感应加热 频 率 为 25008000Hz , 淬 硬 层 深度2-10mm。
中频感应加热表面淬火的机车凸轮轴各种感应器n 工频感应加热 n 频率为50Hz,淬硬层深度10-15 mm感应穿透加热各种感应器n ⑵ 火焰加热: 利用乙炔火焰直接加 热工件表面的方法。
成本低,但质 量不易控制。
金属表面处理的工艺改进与技术应用
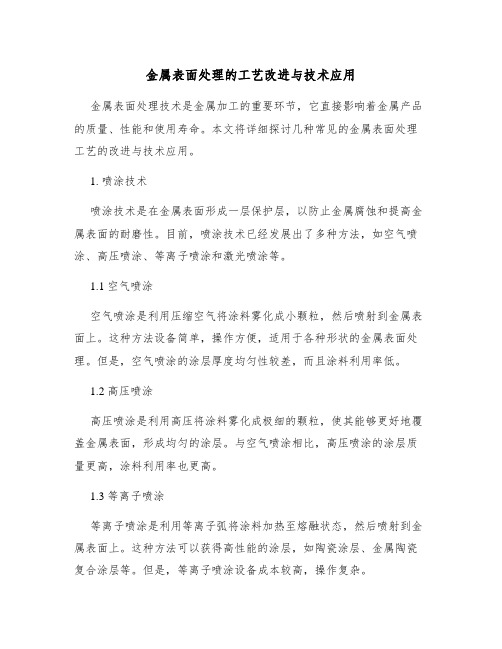
金属表面处理的工艺改进与技术应用金属表面处理技术是金属加工的重要环节,它直接影响着金属产品的质量、性能和使用寿命。
本文将详细探讨几种常见的金属表面处理工艺的改进与技术应用。
1. 喷涂技术喷涂技术是在金属表面形成一层保护层,以防止金属腐蚀和提高金属表面的耐磨性。
目前,喷涂技术已经发展出了多种方法,如空气喷涂、高压喷涂、等离子喷涂和激光喷涂等。
1.1 空气喷涂空气喷涂是利用压缩空气将涂料雾化成小颗粒,然后喷射到金属表面上。
这种方法设备简单,操作方便,适用于各种形状的金属表面处理。
但是,空气喷涂的涂层厚度均匀性较差,而且涂料利用率低。
1.2 高压喷涂高压喷涂是利用高压将涂料雾化成极细的颗粒,使其能够更好地覆盖金属表面,形成均匀的涂层。
与空气喷涂相比,高压喷涂的涂层质量更高,涂料利用率也更高。
1.3 等离子喷涂等离子喷涂是利用等离子弧将涂料加热至熔融状态,然后喷射到金属表面上。
这种方法可以获得高性能的涂层,如陶瓷涂层、金属陶瓷复合涂层等。
但是,等离子喷涂设备成本较高,操作复杂。
1.4 激光喷涂激光喷涂是利用激光束将涂料熔化,然后喷射到金属表面上。
这种方法可以获得高质量、高性能的涂层,但是设备成本极高,操作复杂,适用于小批量、高精度的金属表面处理。
2. 电镀技术电镀技术是在金属表面沉积一层金属,以提高金属的耐腐蚀性、耐磨性和装饰性。
电镀技术已经发展出了多种方法,如传统电镀、脉冲电镀和电化学镀等。
2.1 传统电镀传统电镀是在含有金属离子的溶液中,通过外加电流,使金属离子在金属表面上沉积形成金属层。
这种方法操作简单,成本低,但是镀层质量较差,生产效率低。
2.2 脉冲电镀脉冲电镀是在电镀过程中,通过改变电流的脉冲宽度和脉冲频率,以提高镀层的质量。
与传统电镀相比,脉冲电镀可以获得更均匀、更致密的镀层,提高生产效率。
2.3 电化学镀电化学镀是利用电化学反应,在金属表面沉积金属。
这种方法可以在复杂形状的金属表面上获得均匀的金属层,适用于小批量、高精度的金属表面处理。
热处理方法、特点和应用
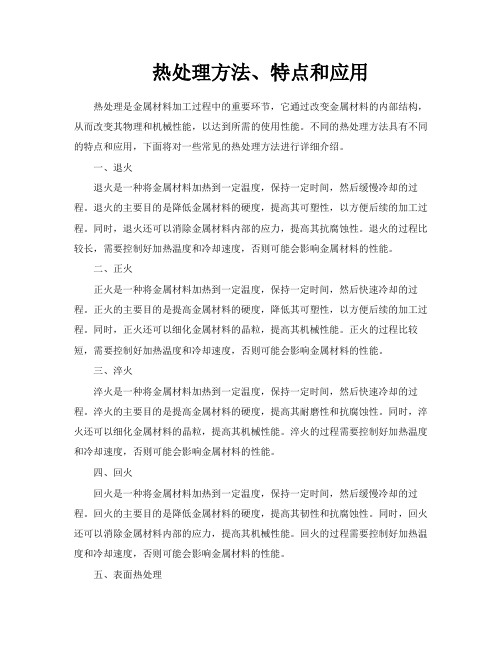
热处理方法、特点和应用热处理是金属材料加工过程中的重要环节,它通过改变金属材料的内部结构,从而改变其物理和机械性能,以达到所需的使用性能。
不同的热处理方法具有不同的特点和应用,下面将对一些常见的热处理方法进行详细介绍。
一、退火退火是一种将金属材料加热到一定温度,保持一定时间,然后缓慢冷却的过程。
退火的主要目的是降低金属材料的硬度,提高其可塑性,以方便后续的加工过程。
同时,退火还可以消除金属材料内部的应力,提高其抗腐蚀性。
退火的过程比较长,需要控制好加热温度和冷却速度,否则可能会影响金属材料的性能。
二、正火正火是一种将金属材料加热到一定温度,保持一定时间,然后快速冷却的过程。
正火的主要目的是提高金属材料的硬度,降低其可塑性,以方便后续的加工过程。
同时,正火还可以细化金属材料的晶粒,提高其机械性能。
正火的过程比较短,需要控制好加热温度和冷却速度,否则可能会影响金属材料的性能。
三、淬火淬火是一种将金属材料加热到一定温度,保持一定时间,然后快速冷却的过程。
淬火的主要目的是提高金属材料的硬度,提高其耐磨性和抗腐蚀性。
同时,淬火还可以细化金属材料的晶粒,提高其机械性能。
淬火的过程需要控制好加热温度和冷却速度,否则可能会影响金属材料的性能。
四、回火回火是一种将金属材料加热到一定温度,保持一定时间,然后缓慢冷却的过程。
回火的主要目的是降低金属材料的硬度,提高其韧性和抗腐蚀性。
同时,回火还可以消除金属材料内部的应力,提高其机械性能。
回火的过程需要控制好加热温度和冷却速度,否则可能会影响金属材料的性能。
五、表面热处理表面热处理是一种只对金属材料表面进行热处理的过程,主要目的是提高金属材料表面的硬度和耐磨性,同时不改变金属材料内部的性能。
表面热处理的方法包括火焰喷涂、等离子喷涂、电镀等。
这些方法可以有效地提高金属材料的表面性能,同时不改变金属材料内部的性能。
六、化学热处理化学热处理是一种通过化学反应改变金属材料表面的化学成分,从而提高其硬度、耐磨性和抗腐蚀性的过程。
表面化学热处理技术

化学热处理渗碳:为了获得高硬度、高耐磨的表面及强韧的心部,渗碳后必须进行淬火加低温回火处理。
按渗碳介质可分为:气体渗碳、液体渗碳、固体渗碳。
渗氮:①渗氮层具有高硬度、高耐磨性;②渗氮层比热容打,在钢件表面形成压应力层可显著提高耐疲劳性能,渗氮层的耐疲劳性优于渗碳层;③渗氮层表面有化学稳定性高的ε相,能显著提高耐腐蚀性。
渗氮能形成性能优越的渗氮层,但由于工艺时间太长,使得生产率太低,成本高,应尽量少采用。
渗氮一般用在强烈磨损、耐疲劳性要求非常高的零件,有的场合是除要求机械性能外还要求耐腐蚀的零件。
碳氮共渗(俗称“氰化”):按工艺温度分:低温碳氮共渗(520-580℃),工艺温度低,共渗过程是以氮原子为主、碳原子为辅的渗入过程,俗称“软氮化”;中温碳氮共渗(780-880℃);高温碳氮共渗(880-930℃)。
优点:①与渗碳相比处理温度低,渗后可直接淬火,工艺简单,晶粒不易长大,变形裂倾向小,能源消耗少,共渗层的疲劳性和抗回火稳定性好;②与渗氮相比,生产周期大大缩短,对材料适用广。
氮碳共渗:氮碳共渗起源于西德,是在液体渗氮基础上发展起来的。
早期氮碳共渗是在含氰化物的盐浴中进行的。
由于处理温度低,一般在500-600℃,过程以渗氮为主,渗碳为辅,所以又称为“软氮化”。
氮碳共渗工艺的优点如下:①氮碳共渗有优良的性能:渗层硬度高,碳钢氮碳共渗处理后渗层硬度可达HV570-680;渗氮钢、高速钢、模具钢共渗后硬度可达HV850-1200;脆性低,有优良的耐磨性、耐疲劳性、抗咬合性和耐腐蚀性。
②工艺温度低,且不淬火,工件变形小。
③处理时间短,经济性好。
④设备简单,工艺易掌握。
存在问题是:渗层浅,承受重载荷零件不宜采用。
渗硼:渗硼是一种有效地表面硬化工艺。
将工件置于能产生活性硼的介质中,经过加热、保温,使硼原子渗入工件表面形成硼化物层的过程称为渗硼。
金属零件渗硼后,表面形成的硼化物(FeB、Fe2B、TiB2、ZrB2、VB2、CrB2)及碳化硼等化合物的硬度极高,热稳定性。
零件加工中的表面处理技术

零件加工中的表面处理技术随着工业技术的不断进步,零件加工已不再是简单的机械生产过程,而是成为了具有高度技术含量的复合综合过程。
表面处理技术作为零件加工的重要环节,对于零件的质量、耐用性、外观等方面具有很大的影响。
本文探讨零件加工中常用的表面处理技术,分析各种技术的特点和适用范围,以期为零件制造业提供参考。
一、化学处理技术化学处理技术是利用酸、碱等化学物质将零件表面腐蚀、氧化或还原,以改善、修饰、保护、增强金属表面性能的方法。
其中最常见的化学处理技术包括镀铬、镀锌、磷化和阳极氧化等。
1. 镀铬:镀铬是目前最常见的表面处理技术之一,主要是利用电解沉积法将铬层沉积到零件表面,形成具有防腐、耐磨、光亮度高、色彩稳定等特点的铬层。
镀铬技术适用于各种金属材料,如铁、铜、铝等。
2. 镀锌:镀锌技术适用于镀锌零件的防锈、耐蚀等要求较高的场合。
主要原理是将锌层电沉积到钢材表面,形成具有良好耐腐蚀性的锌层。
对于冶金行业、建筑工程等领域,镀锌技术也已得到广泛应用。
3. 磷化:磷化技术的作用是通过在钢材表面形成一层磷酸盐膜,以降低钢材表面的摩擦系数、增强耐磨性和延长使用寿命。
适用于机械、汽车、电子等行业中对耐腐蚀性、耐磨性和硬度要求较高的部件。
4. 阳极氧化:阳极氧化是指在金属表面形成一层氧化铝薄膜,以提高金属零件的防腐蚀、保护和装饰效果。
适用于铝合金零件、电子元器件和汽车等领域。
二、机械处理技术机械处理技术是指采用机械加工的方式对零件表面进行加工处理的技术。
机械处理技术适用范围广,处理方法也比较多样,常见的有研磨、抛光、划痕、喷砂等。
1. 研磨:研磨是指通过研磨机将零件表面进行平整、光洁处理。
这种技术适用于对表面光洁度要求较高的零件加工。
2. 抛光:抛光技术是通过磨料对零件表面进行喷射和抛光处理,以便为其赋予镜面效果、提高表面硬度和耐腐蚀性等性能。
3. 划痕:划痕技术是一种通过磨料对零件表面进行切割,形成高亮晶体的表面加工方式。
- 1、下载文档前请自行甄别文档内容的完整性,平台不提供额外的编辑、内容补充、找答案等附加服务。
- 2、"仅部分预览"的文档,不可在线预览部分如存在完整性等问题,可反馈申请退款(可完整预览的文档不适用该条件!)。
- 3、如文档侵犯您的权益,请联系客服反馈,我们会尽快为您处理(人工客服工作时间:9:00-18:30)。
课程:学生姓名:学号:课程教师:金属表面化学热处理技术与应用姓名(南昌大学,机电工程学院,江西南昌330031)摘要:为提高金属表面机械强度和摩擦磨损性能,通常需要对材料表面进行化学热处理。
此项技术正逐步朝着能源消耗低、环境污染少的方向发展。
本文论述了渗硼、渗碳、真空化学热处理、催渗、等离子化学热处理等化学热处理技术在金属材料表面加工中的作用机理和应用;简介了复合处理新兴工艺并展望了化学热处理技术未来的发展方向。
关键词:化学热处理;金属材料;渗硼;电化学热处理Metal surface chemical treatment technology and applicationsZHANG Dan-ting(School of Mechatronics Engineering,Nanchang University,Nanchang 330031,China)Abstract:In order to improve the mechanical strength and the friction and wear propertiesof the metal surface,it usually requires chemical treatment of the material surface.This technology is developing toward low energy consumption,less environmental pollution and direction gradually.This article discusses applications and the mechanism of metallic material’s chemical heat treatment technologies such as boronizing,carburizing,vacuum heat chemical treatment,reminders infiltration and the plasma chemical treatment;Introduce the composite processing technology briefly and outlook development of chemical treatment technology in the future.Key Words:Chemical treatment;Metallic materials:Boriding;Electrochemical heat treatment金属材料表面化学热处理是表面合金化与热处理相结合的一种表面处理技术。
它是利用元素扩散性能,使合金元素渗人金属表面的一种热处理工艺。
其基本工艺过程是:首先将工件置于含有渗入元素的活性介质中加热到一定温度,是活性介质通过分解并释放出欲渗入元素的活性原子,活性原子被工件表面吸附并溶入表面,溶入表面的原子向金属表层扩散渗入形成一定厚度的扩散层,从而改变工件表层、组织和性能[1]。
根据渗入元素的活性介质所处状态不同,化学热处理可分为:固体法、液体法、气体法和等离子法。
通过一定的化学热处理工艺,金属表层、过渡层与心部,在成分、组织和性能上有很大差别。
强化效果不仅与各层的性能有关,而且还与各层之间的相互联系有关。
如渗碳表面层的碳含量及其分布、渗碳层深度和组织等均可能影响材料渗碳后的性能。
当前,我国热处理已有了不少重大的发展和进步,但与世界先进水平相比仍存在着很大的而且还在不断扩大着的差距,这种差距是深层次的。
因此对化学热处理技术发展历程及现状进行全面深入的了解显得十分必要,本文列举渗硼、渗碳、真空化学热处理、催渗、等离子化学热处理等表面处理技术来说明近年来工艺发展的趋势。
1渗硼技术1.1 渗硼技术发展现状渗硼是现代化学热处理方法之一,由于渗硼层极高的硬度和耐磨性远非一般表面硬化层可比,所以近年来渗硼工艺得到了国内外普遍重视[2]。
渗硼就是将工件置于高温状态的渗硼介质中,渗硼介质经化学反应析出活性硼原子,硼原子被工件表面吸收,在高温下逐步向工件内层扩散形成硼化层。
这种方法可用于钢铁材料,金属陶瓷和某些有色金属材料,如钛、钽和镍基合金。
渗硼工艺的历史已近百年,1895年莫桑(Moissan)发表了在钢铁材料表面进行气体渗硼的论文。
20世纪初期,前苏联、德国、美国等开始研究固体渗硼。
但由于得到的渗硼层薄、不均匀和疏松严重,没有实用价值,因此未能引起人们的重视。
20世纪60年代又重新重视固体渗硼。
G.Kartal,O.L.Eryilmaz,G.Krumdick[3]等人在研究中指出在低碳钢板基材,使用电化学渗硼在范围为850℃-1000℃的高温下,保温时间是从5分钟到120分钟,能得到一定致密度和厚度渗硼层硼化层,组织成分主要包括Fe2B和FeB相。
结果显示:电化学渗硼后硬度有了明显提高,从200±20HV提高到1700±200HV。
M.Keddam,R.Chegroune[4]使用以灰铸铁为渗硼试样,通过固体渗硼,从而得出渗硼层中Fe2B的增长与处理时间符合抛物线关系。
I.Campos-Silva,M.Ortiz-Dominguez[5]等研究以硼势和渗硼时间为主要因素,对灰铸铁试样进行渗硼试验,得出Fe2B形成动力学。
他们通过灰铸铁Fe2B层的增长动力学得到一个最佳渗硼的浓度,并与试验有很好的一致性,而且不同的渗硼源和渗硼媒介,可以不同程度促进和优化在不同金属的渗硼过程。
我国从1958年开始研究渗硼,首先研究了液体渗硼和膏剂渗硼。
今几年来在固体渗硼方面进展较大。
广大热处理工作者根据我国的具体条件研制了以硼铁为供硼剂的粉末渗硼剂、粒状渗硼剂,进而研究出硼砂石墨型渗硼剂。
从过去只能获得双相硼化层发展到可以稳定得到单相Fe2B的硼化层,使我国在固体渗硼方面步入世界前列[6]。
曲敬信,武晓丽,邵荷生[7]等对渗硼层磨料磨损特性的研究后指出:通过试验他们得出钢铁材料渗硼后由于可以大幅度提高硬度和耐磨性。
赵善中,曲敬信,邵荷生[8]等对几种常用热模具钢渗硼层进行磨损实验。
5CrMnMo,3Cr2W8V,4Cr5MoSi和40Cr钢的渗硼层在本实验条件下,从室温到500℃温度范围内,具有较低的磨损率,与同一成分未渗试样比较,其耐磨性提高3-7倍。
刘健健,陈祝平[9]等对膏剂渗硼进行研究,研究中指出膏剂渗硼的优点是可实现局部渗硼、渗剂消耗少和设备简单等优点;在膏剂渗硼中,影响渗硼层深度和质量的因素除选择合理的温度和时间外,主要是渗剂的成分;渗剂活性越强,渗硼层越厚,其中FeB含量越多;反之,渗硼层越薄,FeB含量越少。
1.2 渗硼技术的应用冷作模具主要的要求是抗磨损,故渗硼对于因磨损失效的模具非常合适。
对于只要求表面耐磨而基体强度要求不高的模具,渗硼后可不再进行热处理,这样既可保持模具的表面光洁度,又可保持基本不变形。
而对于热作磨具如:热冲压冲头、热引伸冲头等,经渗硼回火后使用寿命提高3~6倍。
另外在压铸模方面以普通碳素钢渗硼替代3Cr2W8V高合金钢取得了成功。
渗硼技术也应用到了石油机械上,如用于超低碳铬镍不锈钢制的阀杆、耐热钢制分离器壳体等均获得成功。
渗硼工艺还成功地应用于饲料粉碎机的锤片、泥浆泵钢套和可锻铸铁制件,以及纺织机械导板配件。
2渗碳技术2.1 渗碳方法与研究现状渗碳可提高材料表面硬度、耐磨性和疲劳强度,在工业中应用十分广泛。
结构钢经渗碳后,能使工件表面活动高的硬度、耐磨性、耐侵蚀磨损性、接触疲劳强度和弯曲疲劳强度,而心部具有一定强度、塑性、韧性的性能。
除了常规的气体渗碳、液体渗碳、固体渗碳,当前已经开发了许多新的渗碳工艺,有效的提高表面渗碳效率,缩短工艺周期,提高生产率获得高质量的工件,如高温渗碳、等离子渗碳、真空渗碳、放电与电解渗碳等。
从相应的比较出发,国外的渗碳和渗氮工艺在近二十多年来的进展已形成具有明显特色的一些先进工艺技术。
德国Clausen等2001年发表的高温渗碳论文中介绍渗碳温度从950℃提高至1050℃可使渗碳周期缩短50%。
日本学者S.Nakamura等[10],I.Machida 等[11]和T.Moritov等[12]分别在2002、2008和2010年在美国申请高浓度渗碳专利(US2002/0050307A1,US2008/0156399A1和US2010/0126632A1),都能获得在常规渗碳淬火的马氏体基体上分布着细小弥散的碳化物粒状。
国内实施的高浓度渗碳工艺,一般采用在Ac1~Ac3或Ac1~Ac cm之间的温度下进行。
工件表面均处于[γ+(Fe,Cr,Mo)3C]两相区,以便形成细小、均匀的合金渗碳体颗粒,并保持在不聚集长大的状态。
有的采用循环加热渗碳工艺,有利于形成细小球形颗粒。
渗碳气氛碳势高于渗碳温度下奥氏体的饱和碳浓度值。
刘志儒等[13]采用稀土催渗的高浓度气体渗碳方法和(860±5)℃,8h(气氛碳势C p=1.2%)油淬工艺得到含大量细小弥散颗粒碳化物的渗层,表面硬度高于1000HV0.1,具有高耐磨性,试样的冲击韧度还高于常规渗碳工艺。
石巨岩等[14]对20CrMnTi钢在双室结构的滴控箱式气体渗碳炉上采用的工艺为:830℃(碳势C p=1.2%)预渗1h→925±5℃(C p=1.1%)1h,油冷→925±5℃(C p=1.1%)2h,油冷→925±5℃(C p=0.9%)1h,降温至880℃(C p=0.9%)1h,油冷,获得高饱和渗碳层的组织,表面硬度1057HV0.1,该值和耐磨性分别比常规渗碳的值提高13%和20%。
2.2 渗碳技术的应用高温渗碳周期短,生产效率高,使得高温渗碳齿轮钢的研发非常有意义。
但是由于高温渗碳速率快,易发生过渗现象,渗层深度过大,渗碳层残余应力就会下降,反而使材料的疲劳极限下降。
还需做更多工艺控制研究,使之成为成熟的渗碳技术。
深层渗碳对大模数重载齿轮的生产十分适用,这一技术要求除对基体材料的成分和强度有要求外,还对齿轮的渗层深度和碳浓度分布提出特殊规定。
许多工业发达国家,如瑞士、德国和日本都采用渗碳淬火和磨齿工艺技术。
低压真空渗碳在商用和军用飞机和航天器的应用包括制动系统、传动装置、飞行控制和导航系统、液动力设备、降落齿轮箱部件和轴承、球螺栓螺母、行星齿轮、小齿轮和轴等众多的零部件等领域广泛应用。
我国现在也制订了“航空发动机用高温渗碳轴承钢”相关标准,材料牌号为G13Cr4Mo4Ni4V。
要获得优良的渗碳硬化层性能和显微组织,只有采用真空渗碳才易于达到。