核电站数字化仪控系统简介
核电站数字化仪控DCS
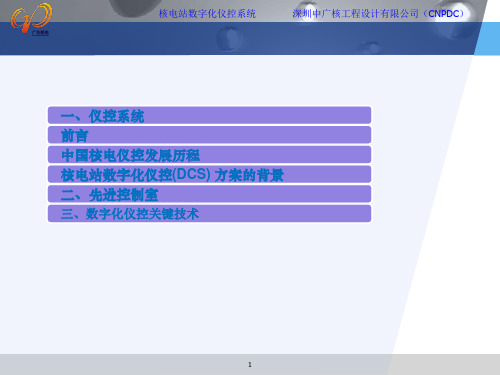
3
核电站数字化仪控系统
深圳中广核工程设计有限公司(CNPDC)
中国核电/仪控系统发展历程
FCD时间
1984
1987.8
1997.5 1999.12
2005.12 2007.8 2008.2 2009
商运时间
秦山一期 大亚湾 1991.12 1994.5
岭澳一期 田湾一期 2003.1 2007.5
7
核电站数字化仪控系统
深圳中广核工程设计有限公司(CNPDC)
核电站数字化仪控(DCS) 方案的背景
数字化仪控的应用和发展
计算机技术、网络技术快速发展和广泛应用,已有多种成熟、可靠的DCS 商业产品。国内火力发电机组已成功应用自主知识产权的DCS,国内、国 外DCS产品已形成了竞争的局面。
国内60万和30万火力发电机组已积累了使用DCS系统的经验,秦山一期/三 期,大亚湾/岭澳核电站一期也积累了使用某些数字技术(如数据采集,常 规岛控制)的经验。
常规模拟式仪控系统
岭澳二期 红沿河一期 宁德一期 台山EPR
2010.5
全部数字化仪控自主 化设计/国产化开始
主控室自主化设计
数字化仪控系统
4
核电站数字化仪控系统
深圳中广核工程设计有限公司(CNPDC)
继电器控制机柜—岭澳一期(数量大、检修靠人工)
5
Interruptor
核电站数字化仪控系统
深圳中广核工程设计有限公司(CNPDC)
8
核电站数字化仪控系统
深圳中广核工程设计有限公司(CNPDC)
核电站数字化仪控(DCS) 方案的背景
核电站仪控系统采用数字化已是一种迫切的需要和必然的趋势
法国N4 MCR示意图
方家山核电站数字化仪控系统浅析
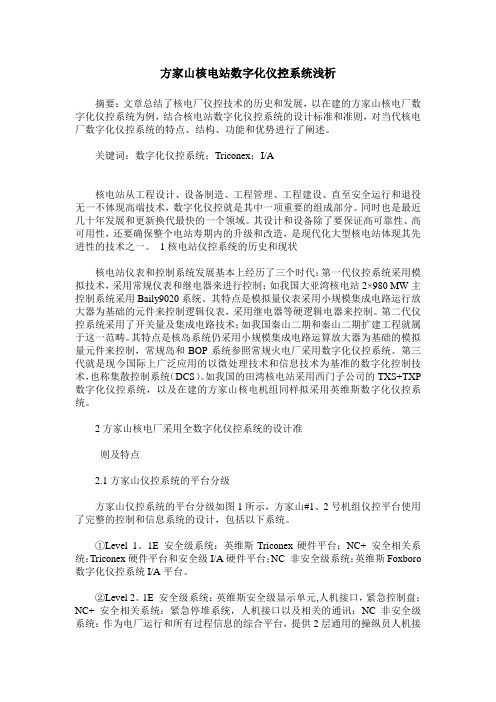
方家山核电站数字化仪控系统浅析摘要:文章总结了核电厂仪控技术的历史和发展,以在建的方家山核电厂数字化仪控系统为例,结合核电站数字化仪控系统的设计标准和准则,对当代核电厂数字化仪控系统的特点、结构、功能和优势进行了阐述。
关键词:数字化仪控系统;Triconex;I/A核电站从工程设计、设备制造、工程管理、工程建设、直至安全运行和退役无一不体现高端技术,数字化仪控就是其中一项重要的组成部分。
同时也是最近几十年发展和更新换代最快的一个领域。
其设计和设备除了要保证高可靠性、高可用性,还要确保整个电站寿期内的升级和改造,是现代化大型核电站体现其先进性的技术之一。
1核电站仪控系统的历史和现状核电站仪表和控制系统发展基本上经历了三个时代:第一代仪控系统采用模拟技术,采用常规仪表和继电器来进行控制;如我国大亚湾核电站2×980 MW主控制系统采用Baily9020系统。
其特点是模拟量仪表采用小规模集成电路运行放大器为基础的元件来控制逻辑仪表,采用继电器等硬逻辑电器来控制。
第二代仪控系统采用了开关量及集成电路技术;如我国秦山二期和秦山二期扩建工程就属于这一范畴。
其特点是核岛系统仍采用小规模集成电路运算放大器为基础的模拟量元件来控制,常规岛和BOP系统参照常规火电厂采用数字化仪控系统。
第三代就是现今国际上广泛应用的以微处理技术和信息技术为基准的数字化控制技术,也称集散控制系统(DCS)。
如我国的田湾核电站采用西门子公司的TXS+TXP 数字化仪控系统,以及在建的方家山核电机组同样拟采用英维斯数字化仪控系统。
2方家山核电厂采用全数字化仪控系统的设计准则及特点2.1方家山仪控系统的平台分级方家山仪控系统的平台分级如图1所示,方家山#1、2号机组仪控平台使用了完整的控制和信息系统的设计,包括以下系统。
①Level 1。
1E 安全级系统:英维斯Triconex硬件平台;NC+ 安全相关系统:Triconex硬件平台和安全级I/A硬件平台;NC 非安全级系统:英维斯Foxboro 数字化仪控系统I/A平台。
核电站数字化仪控系统简介
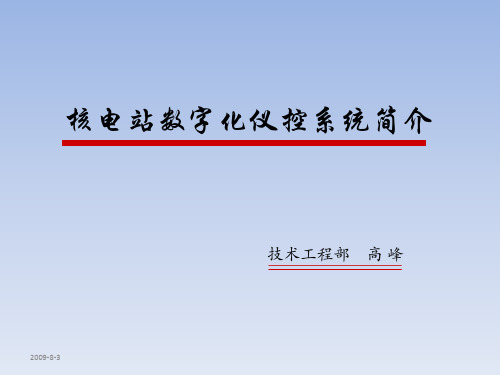
ECP 命令、ESFAS 命令、多样化系统(如果有)命令、来自 后备盘或安全VDU的1E 级单个手动(如果有)命令高于NC 级命令。
优先功能取决于I&C 的安全功能分级,并依照相应的可靠性进 行设计和实施。
2009-8-3
19
可试验性
保护系统:
(1)反应堆紧急停堆 RTS (2)专设安全设施 ESFAS 安全监测系统: (1)事故后监测系统 PAMS
2009-8-3
22
紧急停堆
系统结构及功能
紧急停堆所需自动监测的变量: 中子注量率
反应堆冷却剂温度 反应堆冷却剂系统压力(稳压器压力) 稳压器水位 反应堆冷却剂流量和反应堆冷却剂泵断路器断开 反应堆冷却剂泵转速 蒸汽发生器给水流量 蒸汽发生器水位 汽轮发电机运行状态(保护流体低压信号和低压缸截止
设计准则
系统自检:自检应包括但不限于RAM 和ROM 故障检查、运算处理单 元故障检查、数据链接存储器检查、CPU 看门狗定时器复位检查、通 讯状态检查、IO 模块和接线检查、外围模件检查等。
定期试验:试验范围应覆盖DCS 系统的如下部分:保护和安全监测系统、 ATWT 系统及其他有特殊要求的NC 系统,并且应进行全通道试验,从探 测器至驱动器。遵守IEC 60671。
在反应堆装置运行时以及停堆后一定时间内,由于辐 射的原因,对大部分设备来说人员是不能接近的;
系统安全性、可靠性要求高,运行质量直接与仪控系 统性能相关;
控制和监测核燃料裂变链式反应及堆芯状态监测的必 要性;
大量核物理、热工、水力及其它一些直接测量无法得 到的参数计算多,且精确性和实时性要求高。
2009-8-3
核电厂数字化仪表与控制系统的应用现状与发展趋势

核电厂数字化仪表与控制系统的应用现状与发展趋势随着科技的迅猛发展,核电厂数字化仪表与控制系统在核电行业中的应用越来越广泛,这些先进的技术不仅提高了核电厂的安全性和可靠性,还提高了核电厂的运行效率和经济性。
本文将介绍核电厂数字化仪表与控制系统的应用现状与发展趋势。
一、应用现状1. 数字化仪表与控制系统在核电厂中的应用数字化仪表是指使用数字技术替代原有的模拟仪表,数字化控制系统则是使用数字技术替代原有的模拟控制系统。
数字化仪表与控制系统的应用,使得核电厂的监测、控制和保护等功能更加可靠和高效。
数字化仪表具有抗干扰能力强、精度高、易于维护等优点,而数字化控制系统具有分布式、智能化、网络化等特点。
目前,全球大部分核电厂已经采用了数字化仪表与控制系统,并且很多核电厂正在进行数字化改造。
数字化仪表与控制系统在核电厂的安全中扮演着非常重要的角色。
它们可以实时监测核电厂的运行参数,保证核电厂的安全性。
在发生异常事件时,数字化仪表与控制系统能够迅速响应,及时采取措施,减小事故的危害程度。
数字化仪表与控制系统的应用大大提高了核电厂的安全性。
数字化仪表与控制系统的应用还提高了核电厂的经济性。
由于数字化技术的应用,核电厂的运行效率得到了提高,能够减少人力资源的消耗,减小能源损耗,提高了核电厂的经济效益。
二、发展趋势1. 智能化数字化仪表与控制系统将会向着智能化的方向发展。
随着人工智能技术的发展,数字化仪表与控制系统将会具备更加智能的功能。
智能化的数字化仪表与控制系统将会更加自动化、自适应、自修复,能够更好地满足核电厂对于安全、高效、经济的要求。
2. 网络化未来的数字化仪表与控制系统将会更加网络化。
这将使得核电厂的信息化水平得到进一步提高,能够实现远程监控、远程维护等功能。
通过互联网,数字化仪表与控制系统能够实现更加智能的运行。
3. 安全性数字化仪表与控制系统在安全性方面将会有更进一步的提升。
核电厂运行过程中,对于安全性的要求是非常高的,数字化仪表与控制系统将会向着更加安全可靠的方向发展,能够更好地保证核电厂的安全。
核电厂仪表和控制系统-精品文档47页

1)现场控制 2)远距离控制(遥控—把操纵员的指令传递到被 控设备,控制该设备响应操纵员的指令) 3)自动控制(使被控的输出量自动稳定在一个 整定值范围内,或者受控设备纽按规定条件或 时序动作)。
22.09.2019
15
为了完成控制功能,核电厂设置了很多必要的 控制系统,主要的控制系统有: ——反应堆功率控制系统: ——一次冷却剂过程参数监测及控制系统; ——二次冷却剂过程参数监测及控制系统: ——汽轮机控制及保护系统; ——发电机控制及保护系统; ——换料控制系统: ——核电厂信息处理系统等。
22.09.2019
13
8)监测反应堆及设备的事故状态(如冷却剂的 泄漏);
9)设备潜在故障的诊断及报警: 10)供电的监测与报警: 11)火灾的监测与报警 12)异常、故障或事故的声光报警: 13)系统间的信息传输; 14)计算机的信息处理及存贮: 15)环境监测。
22.09.2019
14
1.2.2 控制功能
专设安全设施系统为核电厂重大的事故提供必要的应急 冷却措施,并防止放射性物质的扩散。
22.09.2019
5
二回路系统由汽轮机、发电机、凝汽器、凝结水泵、 给水加热器、除氧器、给水泵、蒸汽发生器、汽水 分离再热器等设备组成。蒸汽发生器的给水在蒸汽 发生器吸收热量变成蒸汽,然后驱动汽轮发电机组 发电。做功后的乏汽在凝汽器内冷凝成水。凝结水 由凝结水泵输送,经低压加热器加热后进入除氧器, 除氧水由给水泵送入高压加热器加热后重新返回蒸 汽发生器,如此形成热力循环。为了保证二回路系 统的正常运行,二回路系统也设有一系列辅助系统。
22.09.2019
Ovation系统简介

仿真试验成为数字化仪控系统真正投入运行前原理样机、工程样机研制过程中非常重要的手段之一。
Ovatio n系统简介在核电站数字化仪控系统开发仿真试验中.采用的是西屋公司Ovation的最小配置系统。
这是一个可以扩展的快速以太网系统.其中的SUN Blade150工作站既作为工程师站,又作为操作员站,所有的控制组态都在SUN工作站上进行。
从而建立的最小配置核电站数字化仪控系统组成包括:I /O卡件、控制器、高速数据通信网络、系统服务器、操纵员控制台、工程师站、显示器、键盘、微机等。
该Ovati on系统的硬件配置如图7:(1)Sun Blade15O工作站一台,作为Ovation系统的操作员站和工程师站,主要用于完成监视以及组态等任务。
主要性能指标和配置为:600MHz Sparc处理器芯片;512M内存;36G内置硬盘;32M 显存的显示卡;20英寸纯平彩色CRT显示器;软盘驱动器、CD—ROM驱动器;外置SCSI硬盘盒和磁带驱动器。
(2)Ovatio n控制器一套.可实现从10ms~30 S五种不同频率的过程控制.并实现报警处理、冗余处理、控制状态和备份状态管理、以及故障自动切换等功能。
配备了VxWorks嵌入式实时操作系统。
两组控制器硬件,互为冗余:两组控制器电源.互为冗余。
CiSCO24口高速交换机,作为Ova t ion控制器和Sun工作站通信连接的桥梁.提供1 00M带宽的高速以太网通信条件。
4个I/o模块,主要是数据的采集和发送模块.包括模拟量和数字量的处理。
模拟量输入/输出模块,8路输入/输出信号互为隔离.每路有单独的A/D(D/A)转换器.O.4w低功耗.1 3位分辨力.正常时每秒刷新10次.每8 S自动校验一次.每路电流输入配有熔断保险丝。
核电站数字化仪控系统简介
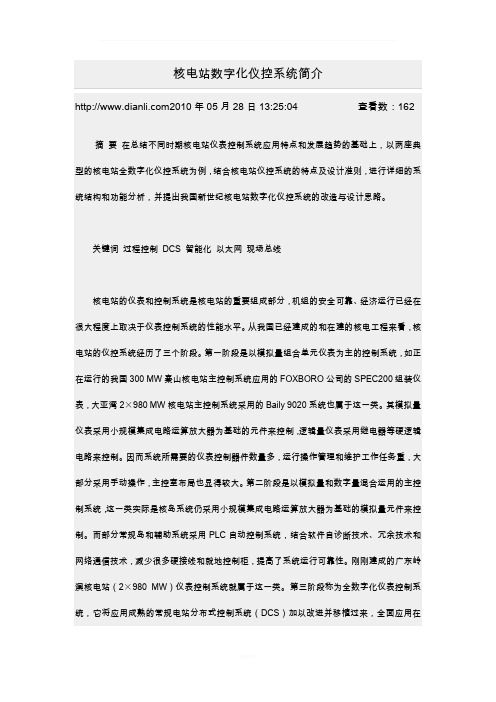
2010年05月28日13:25:04查看数:162 摘要在总结不同时期核电站仪表控制系统应用特点和发展趋势的基础上,以两座典型的核电站全数字化仪控系统为例,结合核电站仪控系统的特点及设计准则,进行详细的系统结构和功能分析,并提出我国新世纪核电站数字化仪控系统的改造与设计思路。
关键词过程控制DCS 智能化以太网现场总线核电站的仪表和控制系统是核电站的重要组成部分,机组的安全可靠、经济运行已经在很大程度上取决于仪表控制系统的性能水平。
从我国已经建成的和在建的核电工程来看,核电站的仪控系统经历了三个阶段。
第一阶段是以模拟量组合单元仪表为主的控制系统,如正在运行的我国300 MW秦山核电站主控制系统应用的FOXBORO公司的SPEC200组装仪表,大亚湾2×980 MW核电站主控制系统采用的Baily 9020系统也属于这一类。
其模拟量仪表采用小规模集成电路运算放大器为基础的元件来控制,逻辑量仪表采用继电器等硬逻辑电路来控制。
因而系统所需要的仪表控制器件数量多,运行操作管理和维护工作任务重,大部分采用手动操作,主控室布局也显得较大。
第二阶段是以模拟量和数字量混合运用的主控制系统,这一类实际是核岛系统仍采用小规模集成电路运算放大器为基础的模拟量元件来控制。
而部分常规岛和辅助系统采用PLC自动控制系统,结合软件自诊断技术、冗余技术和网络通信技术,减少很多硬接线和就地控制柜,提高了系统运行可靠性。
刚刚建成的广东岭澳核电站(2×980 MW)仪表控制系统就属于这一类。
第三阶段称为全数字化仪表控制系统,它将应用成熟的常规电站分布式控制系统(DCS)加以改进并移植过来,全面应用在常规岛、BOP、核岛部分,构成核电站全新数字化仪表控制系统。
现阶段应用比较典型的全数字化仪控系统有:日本日立等公司开发的NUCAMM-90系统、法国法马通公司N4控制系统、ABB公司的NUPLEX80 系统、美国西屋公司的Eagle21 WDPFⅡ系统以及我国在建的田湾核电站所采用的德国西门子公司的TELEPERM XP XS系统等。
核电站数字化仪控
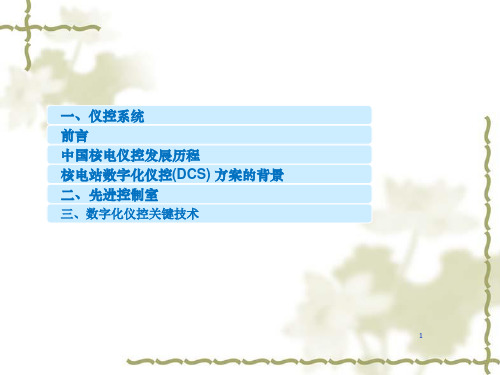
计算机化的核电厂专用设备产品开发与应用。诸如:核测系统、堆芯仪表系 统、棒控系统。
安全系统的软件研制、开发、鉴定已有相应的标准可使用并有多家公认的权 威认证机构 。
核电站数字化仪控(DCS) 方案的背景
核电站仪控系统采用数字化已是一种迫切的需要和必然的趋势
安全控制区
电厂概 貌
辅助控制区
主控制区
监视与交流区
田湾核电站主控室
11
核电站数字化仪控(DCS) 方案的背景
核电站仪控系统采用数字化已是一种迫切的需要和必然的趋势
12
核电站数字化仪控(DCS) 方案的背景
一、仪控系统 前言 中国核电仪控发展历程 核电站数字化仪控(DCS) 方案的背景 二、先进控制室
三、数字化仪控关键技术
1
一、仪控系统
2
前言
大型先进压水堆核电厂的数字化仪控系统是以计算机、网络通讯为基础 的分布式控制系统的系统,它进一步引入和开发面向状态的诊断技术、智能 化报警技术、数据库技术、符合人因工程要求的人机界面、先进的主控室等 现代技术,并采用系统化的控制室功能分析和分配、操纵员作业分析等设计 技术,以及面向核电厂运行安全状态的操作员支持系统包括智能诊断与智能 报警为基础的计算机化操作规程等。
7
核电站数字化仪控(DCS) 方案的背景
数字化仪控的应用和发展
计算机技术、网络技术快速发展和广泛应用,已有多种成熟、可靠的DCS 商业产品。国内火力发电机组已成功应用自主知识产权的DCS,国内、国 外DCS产品已形成了竞争的局面。
- 1、下载文档前请自行甄别文档内容的完整性,平台不提供额外的编辑、内容补充、找答案等附加服务。
- 2、"仅部分预览"的文档,不可在线预览部分如存在完整性等问题,可反馈申请退款(可完整预览的文档不适用该条件!)。
- 3、如文档侵犯您的权益,请联系客服反馈,我们会尽快为您处理(人工客服工作时间:9:00-18:30)。
2010年05月28日13:25:04 查看数:162摘要在总结不同时期核电站仪表控制系统应用特点和发展趋势的基础上,以两座典型的核电站全数字化仪控系统为例,结合核电站仪控系统的特点及设计准则,进行详细的系统结构和功能分析,并提出我国新世纪核电站数字化仪控系统的改造与设计思路。
关键词过程控制DCS 智能化以太网现场总线核电站的仪表和控制系统是核电站的重要组成部分,机组的安全可靠、经济运行已经在很大程度上取决于仪表控制系统的性能水平。
从我国已经建成的和在建的核电工程来看,核电站的仪控系统经历了三个阶段。
第一阶段是以模拟量组合单元仪表为主的控制系统,如正在运行的我国300 MW秦山核电站主控制系统应用的FOXBORO公司的SPEC200组装仪表,大亚湾2×980 MW核电站主控制系统采用的Baily 9020系统也属于这一类。
其模拟量仪表采用小规模集成电路运算放大器为基础的元件来控制,逻辑量仪表采用继电器等硬逻辑电路来控制。
因而系统所需要的仪表控制器件数量多,运行操作管理和维护工作任务重,大部分采用手动操作,主控室布局也显得较大。
第二阶段是以模拟量和数字量混合运用的主控制系统,这一类实际是核岛系统仍采用小规模集成电路运算放大器为基础的模拟量元件来控制。
而部分常规岛和辅助系统采用PLC自动控制系统,结合软件自诊断技术、冗余技术和网络通信技术,减少很多硬接线和就地控制柜,提高了系统运行可靠性。
刚刚建成的广东岭澳核电站(2×980 MW)仪表控制系统就属于这一类。
第三阶段称为全数字化仪表控制系统,它将应用成熟的常规电站分布式控制系统(DCS)加以改进并移植过来,全面应用在常规岛、BOP、核岛部分,构成核电站全新数字化仪表控制系统。
现阶段应用比较典型的全数字化仪控系统有:日本日立等公司开发的NUCAMM-90系统、法国法马通公司N4控制系统、ABB公司的NUPLEX80 系统、美国西屋公司的Eagle21 WDPFⅡ系统以及我国在建的田湾核电站所采用的德国西门子公司的TELEPERM XP XS系统等。
1 核电站仪控系统的特点及全数字化仪控系统的功能设计原则核电站仪控系统的特点是由其工艺过程的特点决定的,一般来讲典型的核电站仪控系统特点可以归纳为以下几点:(1)控制对象的工艺流程复杂,监测和控制的参数多而且各种过程参数联系密切,1000 MW典型的核电站仪控系统的参数信息量和指令大约是7000~9000个。
(2)系统安全性、可靠性要求高,运行质量直接与仪控系统性能相关。
(3)反应堆工作或停堆后一段时间内,大部分设备人员无法接近。
(4)控制和监测核燃料裂变链式反应及堆芯状态监测的必要性。
(5)大量核物理、热工、水力及其它一些直接测量无法得到的参数计算多,且精确性和实时性要求高。
这些特性使核电站的控制对象变得十分复杂,必须采用先进的计算机技术使仪控系统的软硬件装置的设计功能满足生产工艺过程的需要和对过程设备在机组运行工况下的监督和控制,才能保证电站的安全、稳定、经济运行。
因此,核电站数字化仪控系统的功能设计应该遵循以下原则:(1)故障安全原则;(2)单一故障原则;(3)多样性原则;(4)独立性原则;(5)冗余性原则;(6)共模故障最小原则;(7)节能降耗原则;(8)经济性原则。
下面就以两种典型的核电站数字化仪控系统为例,进行详细的功能分析,以便进一步探讨现阶段核电站数字化仪控系统的设计思路和具体应用。
2 典型的核电站数字化仪控系统功能分析2.1 N4核电站的数字化仪控系统N4是法国法马通公司推出的1450 MW系列的最新一代压水堆核电站,分别在法国的Chooz和Civaux两个地方建造4台机组,其中Chooz的两台机组已投入运行。
N4的仪表控制系统也是在原来该公司1300 MW P4机组的仪控系统上进一步发展而来的。
从功能上分为4级,即:现场设备级、控制和保护系统级、人机接口级、远程和就地技术管理系统级。
其中前两级的安全系统由两条实体隔离的通道A和B组成,这样每条通道均能独立控制整个机组。
其中现场设备级的控制和保护系统主要有150个称为"Contronic E"的仪表控制单元组成,组成一个完全模块化的分布式控制系统,用于数据采集、传输和处理。
每个控制站由一个中央系统(CMX)和I/O单元组成。
中央单元执行控制、操作和诊断任务以及外围总线(P-Bus)和通信网络之间的数据传输。
该网络按功能可划分为控制总线(A-Bus)和操作总线(L-Bus)。
它支持数据在实时状态下在所有站之间进行传输。
控制和保护系统级由Sema Group集团负责提供以它自己的产品ADACS为基础的KIC操作系统。
整个系统由下面几个部分组成:(1)操作员工作站:操作员工作站是控制系统与用户进行信息交换的设备,其主要功能是为运行操作人员提供人机界面,使操作人员及时全面地了解系统运行情况,并对生产过程进行调节和控制。
该系统可向操作员提供正常控制程序的1500幅画面、事件和事故控制程序的1200幅画面,以及4000个事故警报数据表。
控制室布置有4个同类型操作台和一个提供机组状态全貌的墙式动态模拟显示屏。
当计算机控制系统失灵时,一个常规辅助控制台作为计算机控制备用,并备有紧急操纵时的常规操作仪器。
(2)中央服务器:所有的系统信息、报告及总数据库由中央服务器统一管理,以实现信息集中管理。
中央服务器用UNIX或WINDOWS NT为操作系统,配以系统应用软件,组态功能由中央服务器提供。
工程师可利用中央服务器的系统应用软件来修改或添加控制配置并下载至控制器中。
(3)控制器:控制器作为自动控制系统中的控制中枢主要包括处理器、内存、I/O接口和外部通讯接口。
采用模块化结构形式。
处理器模块、本地I/O模块、通讯接口模块等均插入同一框架中,通过数据总线相连,实现"软接线",另外,通过现场PLC还可扩展远程I/O模块。
(4)局域网(LAN)及外围总线:Ethernet(以太网)采用载波侦听/多路访问协议,具有10 Mbps及100 Mbps的通讯速度,但它不具备实时性;ARCNET采用令牌传输协议,具有2.5 Mbps的通讯速度,具有较好的实时性。
局域网的网络拓扑结构采用总线形、混合形。
其传输介质使用同轴电缆和光纤。
作为工厂网络底层的现场总线对现场环境有较强的适应性,不但减少了大量的隔离器、端子柜、I/O卡及I/O端口,节省了I/O装置及装置室的空间,同时还减少了大量电缆,节省了安装费用。
(5)输入/输出(I/O)模块:如模拟量/数字量、直流/交流、电压/电流及不同电压等级的I/O模块等。
将多个控制器及I/O框架分散后进行联网,一方面可将生产过程的全部信息通过网络传送至中央服务器以实现信息集中,另一方面避免因个别设备出现故障殃及整个系统而造成的危险,提高可靠性。
N4核电站的数字化仪控系统充分体现了"信息集中,控制分散"的设计思路。
随着计算机信息控制技术的不断发展,各生产厂商竞相研制各种丰富多样的自带处理器的智能型I/O 模块,如CRT模块、数控模块、计算模块、模糊模块等,这些I/O模块可与工业现场的按钮、变送器、传感器、电磁阀门及马达控制器等设备元件直接相连,在完成基本控制功能的同时还可以随时诊断设备的运行情况。
如果在系统应用软件中采用智能控制算法或利用人工智能技术进行自诊断和故障的早期预测,并通过优化过程控制来提高系统的工作可靠性和控制水平,使系统更具有开放性、互操作性和互用性。
将使现在的数字化仪控系统更加完善。
但是目前由于计算机软硬件水平的限制,有些功能模块的功能还不是很强,品种也不够齐全,只能组成一般的控制回路如单回路、串级、比例控制等,对于复杂的、先进的控制算法还无法在仪表中实现;对于单回路内有多输入、多输出的情况缺乏良好的解决方案,成功的应用实例不多,难以评估其实际应用的效果。
所以有的用户借鉴上述仪控系统中的局部设计思路,尝试将现场已经应用成熟PLC设备连接到独立的现场总线网络服务器,与操作站直接通信。
尤其在旧的核电站仪控系统改造方案中,可以直接利用现场原有的电缆和一次测量元件及执行机构,只是对监测和控制部分用先进的I/O模块和PLC设备对原来的控制柜或控制仪表进行改造或替换。
根据现场的实际情况,选用适当的以太网PLC、现场总线PLC以及远程智能I/O设备更换现场的老式控制柜和辅助继电器柜,甚至利用先进的小型分布式控制网络替代原来的第一代模拟量组装仪表和控制盘台,使原先第一代或第二代的核电站仪控系统重新焕发了生命力,不但解决了原有老系统卡件老化严重且没有备品备件的问题,而且对机组的安全、稳定、经济运行起到至关重要的作用。
2.2 西门子TELEPERM XP XS系统西门子TELEPERM XP XS分布式控制系统是集计算机技术、信号处理技术、测量控制技术、通讯网络技术、CRT技术、图形显示技术及人机接口技术于一体,对生产过程进行集中监测、控制、操作、管理的一种新型数字化仪控系统。
从系统安全和系统硬件角度看,结构图划分为安全系统、正常运行系统以及和安全相关的正常运行系统。
其中TELEPERM XS用于安全系统,TELEPERM XP用于正常运行系统。
而且由这两个控制系统共同完成核电站中全部的自动控制任务。
图中的标识分别表示:AP 为自动处理器;APF为故障安全自动处理器;AS620为自动控制系统;ES/DS为工程设计及调试诊断系统;ET/DT为工程师诊断终端;FUM为功能模件;M为电动机;MSI为监测和服务接口;OM为操作和监测系统;OT为操作终端;PU为数据处理单元;SU为数据存储单元;TXP为TELEPERM XP系统;TXS为TELEPERM XS系统;XU为外部网络连接装置。
根据系统功能可分为:(1)过程控制级(包括电站控制级和机组控制级):它提供在主控室(MCR)对工艺过程的控制、监测和观察。
行程仪控系统和主控操作员之间的接口,包括操作终端、显示器及主控室和应急控制室的备用监测控制设备。
备用设备同TXS和TXP直接相连。
此控制级同样具有执行仪控工程师要求的功能,并处理文件和保存归档。
(2)通信级(终端总线):它是在操作和监测系统(OM690)框架内部的通讯级,完成过程控制级和处理级之间的连接。
(3)处理级:包括OM650系统的信号处理计算机(PU/ET/DT等),用于完成各种信息信号的处理。
(4)通信级(电厂总线):通过它和其它总线将整个系统和分布式控制系统连接起来。
所有的总线都采用光纤。
其中TXP系统的电厂总线保证所有的自动化处理器之间的通信,以及过程操作和监测系统(OM650)、工程设计和调试诊断系统(ES/DS)部件之间的通信。