管道系统吹洗施工工艺标准
管道吹洗作业技术程序(标准)

管道吹洗作业技术程序(标准)目录前言 (I)1适用范围 (1)2规范性引用文件 (1)3一般规定 (1)4管道吹洗 (2)5环保措施 (5)6质量检验 (5)7检查与评价..................................................................................... 错误!未定义书签。
前言本标准由广东火电工程总公司工程管理部归口管理。
本标准起草单位:广东火电工程总公司工程管理部本标准主要起草人:林泰石本标准主要审定人员:李华钧、潘润锋、李忠信、丰斌、古伟华、张文本标准批准人:丁毅本标准以编号QB/GPEC11105006-2009于2009年1月首次发布。
2011年10月第一次修订,并重新确定编号为QB/GPEC11105006-2011。
管道吹洗作业技术程序(标准)1 适用范围适用于按《压力管道安全管理与监察规定》中所指压力管道工程安装过程中系统管线的水冲洗、空气吹扫、蒸汽吹扫、油冲洗、化学清洗等内容。
2 规范性引用文件2.1 《质量管理体系基础和术语》(GB/T19000-2008)2.2 《质量管理体系要求》(GB/T19001-2008)2.3 《工程建设施工企业质量管理规范》(GB/T50430-2007)2.4 《职业健康安全管理体系要求》(GBT28001-2011)2.5 《环境管理体系要求及使用指南》(GBT24001-2004)2.6 GB50235-2010《工业金属管道工程施工规范》2.7 SH3501-2011《石油化工有毒、可燃介质管道工程施工及验收规范》2.8 SH3505-1999《石油化工施工安全技术规程》3 一般规定3.1 施工条件验收:3.1.1 系统管线已安装完成,焊口、支吊架经检验合格,对于进行蒸汽吹扫、化学清洗的管道系统需经管线试验(强度、严密性试验)合格后方可进行。
3.1.2 系统管线清洗作业措施、施工技术方案、安全措施编写完成并经相关单位、部门的审查批准。
管道吹扫规范(新)
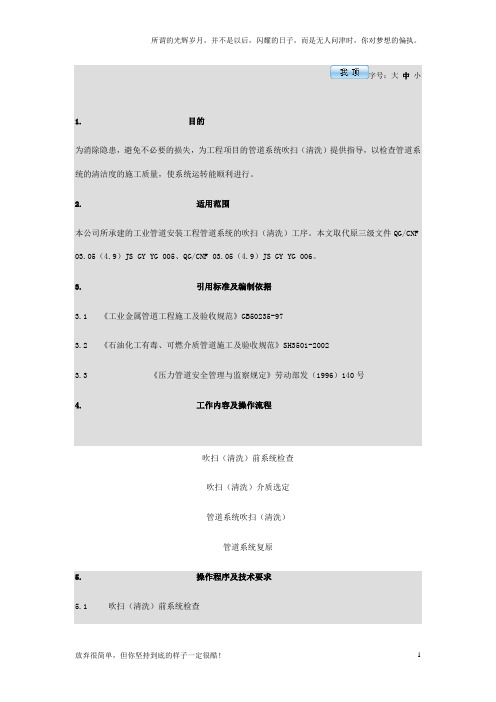
字号:大中小1. 目的为消除隐患,避免不必要的损失,为工程项目的管道系统吹扫(清洗)提供指导,以检查管道系统的清洁度的施工质量,使系统运转能顺利进行。
2. 适用范围本公司所承建的工业管道安装工程管道系统的吹扫(清洗)工序。
本文取代原三级文件QG/CNF 03.05(4.9)JS GY YG 005、QG/CNF 03.05(4.9)JS GY YG 006。
3. 引用标准及编制依据3.1 《工业金属管道工程施工及验收规范》GB50235-973.2 《石油化工有毒、可燃介质管道施工及验收规范》SH3501-20023.3 《压力管道安全管理与监察规定》劳动部发(1996)140号4. 工作内容及操作流程吹扫(清洗)前系统检查吹扫(清洗)介质选定管道系统吹扫(清洗)管道系统复原5. 操作程序及技术要求5.1 吹扫(清洗)前系统检查吹扫(清洗)前,经监检部门、建设部门及施工单位对系统的实体及资料进行全面检查,确认合格后方可进行。
5.1.1 完成管道的强度试验和严密性试验。
5.1.2 向参加吹扫工作的人员进行技术交底。
5.1.3 压力试验时,需要装设隔断盲板的地方,压力的导入口以及拆除的仪表、阀门等附件需装设临时短管的地方要考虑吹扫工作的需要,不宜马上复原,以免造成重复拆卸与安装。
5.1.4 吹扫时需要拆除的阀门、法兰、仪表等,事先拆除,并用临时短管接通。
对拆除下来的阀门、法兰等附件要密封好,妥善保管,以免丢失。
5.1.5凡用气体(如氮气、压空)和清水冲洗的管道,在吹扫前先用敲打法,使附着于管壁的杂物脱落下来,以达到彻底吹除的目的。
5.1.6金属管转子流量计、玻璃管转子流量计、电磁流量计、容积式流量计、调节阀、弹簧管压力表、视镜、流量孔板、过滤器、隔膜阀、聚四氟乙烯阀等拆除,用临时短管和孔板代替。
安全阀应拆除或插入盲板予以隔离。
5.1.7 仪表导压管、PH计主阀关闭,下方侧打开;铁壳温度计、液面开关不拆;液面调节计、液面计主阀关闭。
石油化工装置工艺管道系统吹洗技术

管道系统吹洗一、一般规定1.管道系统液压试验合格后气体泄漏性试验前,应进行管道系统吹洗。
2.管道系统的吹洗方法应根据管道的使用要求、工作介质及管道内表面的脏污程度确定。
公称直径大于或等于600mm的管道,宜采用人工清理;公称直径小于600mm的液体管道宜采用水冲洗;公称直径小于600mm的气体管道宜采用空气吹扫;蒸汽管道应以蒸汽吹扫;非热力管道应用空气吹扫。
对有特殊要求的管道,应按设计文件规定采用相应的吹洗方法。
3.管道系统吹洗前,应编制管道系统吹洗方案,并按经批准的吹洗方案进行。
方案应有下列内容:(1)吹洗程序、吹洗方法、吹洗介质、吹洗设备的布置;(2)吹洗介质的压力、流量、流速的操作控制方法;(3)检查方法、合格标准;(4)安全技术措施及其他注意事项。
4.管道系统吹洗前,应按下列要求做好准备工作:(1)将孔板、喷咀、滤网、调节阀、节流阀及止回阀阀芯等拆除,妥善保管,待吹洗合格后复位。
不需拆除阀芯的阀门,将阀芯提升,使其处于全开状态;(2)不允许吹洗的设备及管道应设置临时盲板,使其与吹洗系统隔离;(3)检查管道支、吊架的牢固程度,必要时应予以加固。
(4)吹洗介质进口管道上应有灵敏可靠的压力表和控制阀门。
5.管道系统吹洗应按下列规定分段依次进行:(1)设备、阀门、仪表件前应设置吹洗口,难以吹洗净的管段、急转弯、排空、倒淋等处也应设置吹洗口;(2)按主管──支管──疏排管的顺序吹洗;(3)吹洗主管时,应关闭支管阀门;(4)支管吹洗应先从介质前进方向的第一支管开始依次进行。
6.吹洗管道系统的介质,应满足下列要求:(1)保证有足够的流量和压力;(2)进气管与出气管的截面积应基本相同;(3)吹洗压力不得超过管道系统的设计压力;(4)吹洗流速不低于工作流速。
7.吹洗时,应不断敲打管子,对焊缝、死角、弯头和管底等部位宜重点敲打,但不得损坏管子。
不锈钢管道应用木锤或铜锤敲打。
8.吹洗时应采取措施防止管道的污物进入设备或设备的污物进入管道。
管道吹扫规范
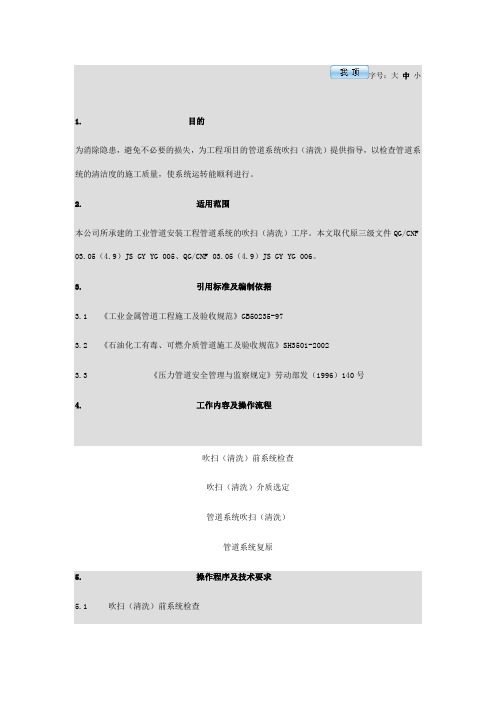
字号:大中小1. 目的为消除隐患,避免不必要的损失,为工程项目的管道系统吹扫(清洗)提供指导,以检查管道系统的清洁度的施工质量,使系统运转能顺利进行。
2. 适用范围本公司所承建的工业管道安装工程管道系统的吹扫(清洗)工序。
本文取代原三级文件QG/CNF 03.05(4.9)JS GY YG 005、QG/CNF 03.05(4.9)JS GY YG 006。
3. 引用标准及编制依据3.1 《工业金属管道工程施工及验收规范》GB50235-973.2 《石油化工有毒、可燃介质管道施工及验收规范》SH3501-20023.3 《压力管道安全管理与监察规定》劳动部发(1996)140号4. 工作内容及操作流程吹扫(清洗)前系统检查吹扫(清洗)介质选定管道系统吹扫(清洗)管道系统复原5. 操作程序及技术要求5.1 吹扫(清洗)前系统检查吹扫(清洗)前,经监检部门、建设部门及施工单位对系统的实体及资料进行全面检查,确认合格后方可进行。
5.1.1 完成管道的强度试验和严密性试验。
5.1.2 向参加吹扫工作的人员进行技术交底。
5.1.3 压力试验时,需要装设隔断盲板的地方,压力的导入口以及拆除的仪表、阀门等附件需装设临时短管的地方要考虑吹扫工作的需要,不宜马上复原,以免造成重复拆卸与安装。
5.1.4 吹扫时需要拆除的阀门、法兰、仪表等,事先拆除,并用临时短管接通。
对拆除下来的阀门、法兰等附件要密封好,妥善保管,以免丢失。
5.1.5凡用气体(如氮气、压空)和清水冲洗的管道,在吹扫前先用敲打法,使附着于管壁的杂物脱落下来,以达到彻底吹除的目的。
5.1.6金属管转子流量计、玻璃管转子流量计、电磁流量计、容积式流量计、调节阀、弹簧管压力表、视镜、流量孔板、过滤器、隔膜阀、聚四氟乙烯阀等拆除,用临时短管和孔板代替。
安全阀应拆除或插入盲板予以隔离。
5.1.7 仪表导压管、PH计主阀关闭,下方侧打开;铁壳温度计、液面开关不拆;液面调节计、液面计主阀关闭。
管道系统吹扫清洗施工方案

管道系统吹扫清洗施工方案管道系统吹扫清洗施工方案本方案适用于压力管道工程的系统吹扫、清洗(简称吹洗),包括人工清扫、水冲洗、空气吹扫、化学清洗、油冲洗等吹洗施工内容。
机器或设备的附属管道,其吹洗应按制造厂家的技术文件要求执行,但其质量标准应不低于本方案。
施工前应符合设计文件要求及国家现行有关标准、规范的规定。
施工准备:材料:用于管道系统吹扫施工的管材、管件、法兰、阀门、紧固件、支承件等临时材料,应具有质量合格证明书。
用于管道系统吹洗施工的橡胶管、橡胶石棉板、消防水带、塑料管,应采用质量优良、外观无缺陷的材料。
管道系统吹洗压力、温度较高时的临时连接材料,应根据吹洗系统的操作压力、温度要求进行材料选用。
用于化学清洗的化学药品,应符合相应标准的理化性能指标,并应设置专用库房进行存放。
化学清洗常用药剂的特性、用量详见表1.施工机具:常用设备有离心式清水泵、离心式油泵、滤油机、空气压缩机、氩弧焊机、电焊机、化学清洗加药循环装置等。
常用计量、检测器具有压力表、温度计、百分表、钢卷尺、钢板尺、黑光灯、YX—125萤光探伤仪。
技术准备:施工前应根据吹洗方法的选择、装置工艺流程、配管施工图和现场的具体条件组织编制吹洗施工技术方案,绘制系统吹洗流程图和清洗回路图,并根据吹洗施工技术方案要求,进行吹洗施工的各项准备工作。
管道吹洗流程的设置原则为先大系统,后小系统;先主干线,后支线;先高处,后低处,避免重复吹洗。
清洗流程应尽量简单、流畅,一般吹洗管道长度500m~1500m为宜,清洗液容量应30 m3~50m3为一回路。
清洗回路应尽量集中,以便于清洗液的重复利用。
酸钠是一种白色或微黄色粉末,具有特别强的清洗能力。
与苛性钠不同,酸钠没有碱腐蚀问题。
与磷酸氢钠配合使用,可以获得良好的脱脂效果。
此外,酸钠也可以用作中和防锈剂。
使用酸钠时,一般不单独使用,而是在1-2%的柠檬酸水溶液中加入氨,将pH值调整到3.5-5,以柠檬酸氨的形式使用。
管道系统吹洗工艺标准
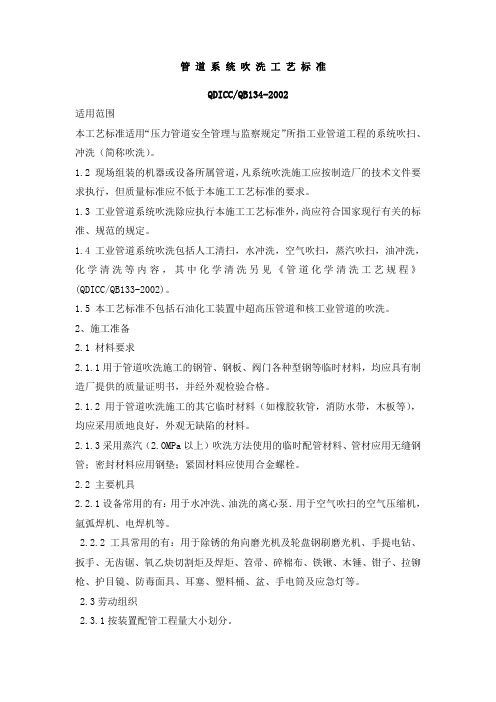
管道系统吹洗工艺标准QDICC/QB134-2002适用范围本工艺标准适用“压力管道安全管理与监察规定”所指工业管道工程的系统吹扫、冲洗(简称吹洗)。
1.2 现场组装的机器或设备所属管道,凡系统吹洗施工应按制造厂的技术文件要求执行,但质量标准应不低于本施工工艺标准的要求。
1.3 工业管道系统吹洗除应执行本施工工艺标准外,尚应符合国家现行有关的标准、规范的规定。
1.4 工业管道系统吹洗包括人工清扫,水冲洗,空气吹扫,蒸汽吹扫,油冲洗,化学清洗等内容,其中化学清洗另见《管道化学清洗工艺规程》(QDICC/QB133-2002)。
1.5 本工艺标准不包括石油化工装置中超高压管道和核工业管道的吹洗。
2、施工准备2.1 材料要求2.1.1用于管道吹洗施工的钢管、钢板、阀门各种型钢等临时材料,均应具有制造厂提供的质量证明书,并经外观检验合格。
2.1.2 用于管道吹洗施工的其它临时材料(如橡胶软管,消防水带,木板等),均应采用质地良好,外观无缺陷的材料。
2.1.3采用蒸汽(2.OMPa以上)吹洗方法使用的临时配管材料、管材应用无缝钢管;密封材料应用钢垫;紧固材料应使用合金螺栓。
2.2 主要机具2.2.1设备常用的有:用于水冲洗、油洗的离心泵.用于空气吹扫的空气压缩机,氩弧焊机、电焊机等。
2.2.2工具常用的有:用于除锈的角向磨光机及轮盘钢刷磨光机、手提电钻、扳手、无齿锯、氧乙炔切割炬及焊炬、笤帚、碎棉布、铁锹、木锤、钳子、拉铆枪、护目镜、防毒面具、耳塞、塑料桶、盆、手电筒及应急灯等。
2.3劳动组织2.3.1按装置配管工程量大小划分。
1)配管量在50Km以内,应有 12-16名管工, 2名电焊工和1名气焊工组成吹洗专业班组进行实施。
2)配管量在50Km-100Km之间,应有20-26名管工, 4名电焊工和2名气焊工组成两个吹洗作业班组,并配备适当辅助工。
2.3.2吹洗工作应按装置工艺系统划分,并以吹洗方法、类别分工组织,按工序计划有序实施。
管道系统的吹扫和清洗
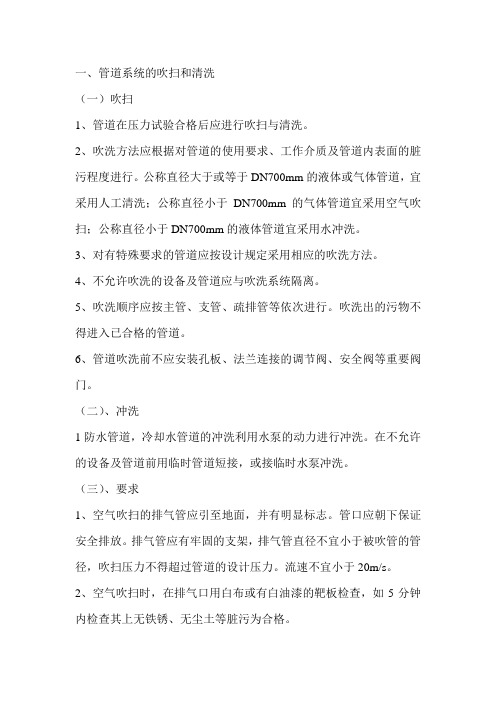
一、管道系统的吹扫和清洗
(一)吹扫
1、管道在压力试验合格后应进行吹扫与清洗。
2、吹洗方法应根据对管道的使用要求、工作介质及管道内表面的脏污程度进行。
公称直径大于或等于DN700mm的液体或气体管道,宜采用人工清洗;公称直径小于DN700mm的气体管道宜采用空气吹扫;公称直径小于DN700mm的液体管道宜采用水冲洗。
3、对有特殊要求的管道应按设计规定采用相应的吹洗方法。
4、不允许吹洗的设备及管道应与吹洗系统隔离。
5、吹洗顺序应按主管、支管、疏排管等依次进行。
吹洗出的污物不得进入已合格的管道。
6、管道吹洗前不应安装孔板、法兰连接的调节阀、安全阀等重要阀门。
(二)、冲洗
1防水管道,冷却水管道的冲洗利用水泵的动力进行冲洗。
在不允许的设备及管道前用临时管道短接,或接临时水泵冲洗。
(三)、要求
1、空气吹扫的排气管应引至地面,并有明显标志。
管口应朝下保证安全排放。
排气管应有牢固的支架,排气管直径不宜小于被吹管的管径,吹扫压力不得超过管道的设计压力。
流速不宜小于20m/s。
2、空气吹扫时,在排气口用白布或有白油漆的靶板检查,如5分钟内检查其上无铁锈、无尘土等脏污为合格。
3、空气吹扫时如压力和流速达不到要求时,则采用憋压对管道进行吹扫,憋气压力为0.3-0.4MPa,憋压吹扫的橡胶板厚度按计算结果选用。
4、试压时应注意安全,放气时不得面对放气孔,操作人员不准站在堵头、靶板的正前方,非操作人员不得在盲板、法兰、焊口等处停留。
任何人员不得在堵头、靶板等处停留。
压力高的管道,吹扫时应划出危险区域,禁止无关人员进入。
管道系统吹洗施工工艺

XXX有限公司工艺文件XXX/XXX 第A版管道系统吹洗施工工艺编制:审核:批准:2010-XX-XX批准2010-XX-X实施更改状态表XXX./XXX版本号修改号修改条款修改页码批准人实施日期第A版0 发布XXX 2010年XX月XX日主题:管道系统吹洗施工工艺第A版第0次修改1.操作工艺1.1吹洗施工工艺施工准备→吹洗系统连接→作业条件确认→吹洗→检查确认→系统封闭1.2施工准备1.2.1设备机具准备设备常用的有:用于水冲洗、油清洗的离心泵、用于空气吹扫的空气压缩机、移动式柴油发电机、电焊机、吊车等。
工具常用的有:切割砂轮机、磨光砂轮机、手提电钻、氧乙炔切割炬及焊炬、电焊钳、笤帚、铁锹、木锤、护目镜、钢丝刷等。
1.2.2材料准备消耗用料:氧气、乙炔、压缩空气、电焊条、砂轮片、水等。
措施用料:无缝钢管、钢板、法兰、螺栓、垫片、阀门、型钢、橡胶软管、消防水带、碎棉布、白布等。
1.2.3技术准备根据设计文件要求结合施工现场具体情况编制吹洗措施,明确海吹洗范围、吹洗介质、检验标准等。
根据吹洗系统绘制吹洗流程图,标明吹洗管线号、吹洗范围、需拆卸管道组成件、盲板位置及编号。
确定吹洗方法:吹洗方法应根据管道的使用要求、工作介质及管道内表面的脏污程度确定。
对公称直径大于或等于600mm的管道宜用人工清理,对公称直径小于600mm的管道及工作介质为液体的管道宜用水冲洗或空气吹扫,对工作介质为气体的管道宜用空气吹扫,对工作介质为蒸汽的管道宜用蒸汽吹扫。
对有特殊要求(如禁水、禁油机器或设备内部管道等)管道,应按设计文件或制造厂技术文件要求,采用相应的吹洗方法。
对参与吹洗的施工人员进行详细的技术交底。
1.3吹洗系统连接1.3.1在管道吹洗前,对不应安装的孔板、法兰连接的调节阀、安全阀等管道组成件,按系统或装置单元划分组织拆除,并妥善保管,对于焊接的上述阀门和仪表,应采取流经旁路,卸掉阀头或阀座加保护套等保护措施,将管道系统中弹簧支架、膨胀节锁定牢固。
- 1、下载文档前请自行甄别文档内容的完整性,平台不提供额外的编辑、内容补充、找答案等附加服务。
- 2、"仅部分预览"的文档,不可在线预览部分如存在完整性等问题,可反馈申请退款(可完整预览的文档不适用该条件!)。
- 3、如文档侵犯您的权益,请联系客服反馈,我们会尽快为您处理(人工客服工作时间:9:00-18:30)。
管道系统吹洗施工工艺标准
QJ/JA0622-2006
1.目的
为了规范我公司工业管道系统吹洗的施工工艺过程,保障施工质量,特制定本工艺标准。
2.使用范围
适用于冶金、石油、化工、机械、电力、轻工等行业的碳素钢、合金钢、不锈钢、有色金属管道的系统吹洗施工。
3.参考文件或引用标准:
《化工金属管道工程施工及验收规范》 HG20225-95 《工业金属管道工程施工及验收规范》 GB50235-97 《工业金属管道工程质量检验评定标准》 GB50184-93 4.施工准备:
4.1熟悉设计要求,审查图纸,确定系统吹洗方法,编制技术交底;进行人员、材料、机具的准备;
4.3.2准备必须的劳动保护用品和施工防护。
5.操作工艺:
5.1水冲洗
5.1.1冲洗管道应使用洁净水,冲洗奥氏体不锈钢管道时,水中氯离子含量不得超过25×10-6(25ppm)。
5.1.2冲洗时,宜采用最大流量,流速不得低于1.5m/s。
5.1.3排放水应引入可靠的排水井或沟中,排放管的截面积不得小于被冲洗管截面积的60%。
排水时,不得形成负压。
5.1.4管道的排水支管应全部冲洗。
5.2空气吹扫
5.2.1空气吹扫应利用生产装置的大型压缩机,也可利用装置中的大型容器蓄气,进行间断性的吹扫。
吹扫压力不得超过容器和管道的设计压力,流速不宜小于20m/s。
5.2.2吹扫忌油管道时,气体中不得含油。
5.4蒸汽吹扫
5.4.1为蒸汽吹扫安设的临时管道应按蒸汽管道的技术要求安装,安装质量应符合本规范的规定。
5.4.2蒸汽管道应以大流量蒸汽进行吹扫,流速不应低于30m/s。
5.4.3蒸汽吹扫前,应先行暖管、及时排水,并应检查管道热位移。
5.4.4蒸汽吹扫应按加热一冷却一再加热的顺序,循环进行。
吹扫时宜采取每次吹扫一根,轮流吹扫的方法。
5.4.5通往汽轮机或设计文件有规定的蒸汽管道,经蒸汽吹扫后应检验靶片。
5.5化学清洗
5.5.1需要化学清洗的管道,其范围和质量要求应符合设计文件的规定。
5.5.2管道进行化学清洗时,必须与无关设备隔离。
5.5.3化学清洗液的配方必须经过鉴定,并曾在生产装置中使用过,经实践证明是有效和可靠的。
5.5.4化学清洗时,操作人员应着专用防护服装,并应根据不同清洗液对人体的危害佩带护目镜、防毒面具等防护用具。
5.5.5化学清洗合格的管道,当不能及时投入运行时,应进行封闭或充氮保护。
5.5.6化学清洗后的废液处理和排放应符合环境保护的规定。
5.6油清洗
5.6.1润滑、密封及控制油管道,应在机械及管道酸洗合格后、系统试运转前进行油清洗。
不锈钢管道,宜用蒸汽吹净后进行油清洗。
5.6.2油清洗应以油循环的方式进行,循环过程中每8h应在40-70℃的范围内反复升降油温2-3次,并应及时清洗或更换滤芯。
5.6.3管道油清洗后应采用滤网检验,应符合6.4的规定。
6.质量标准
6.1设计有规定检验标准的,应按设计规定的标准检验。
6.2空气吹扫过程中,当目测排气无烟尘时,应在排气口设置贴白布或涂白漆的木制靶板检验,5min内靶板上无铁锈、
尘土、水分及其他杂物,应为合格。
6.3水冲洗应连续进行。
以排出口的水色和透明度与入口水目测一致为合格。
6.4蒸气吹扫质量标准
注:靶片宜采用厚度5mm ,宽度不小于排汽管道内径的8%,长度略大于管道内径的铝板制成。
蒸汽管道还可用刨光木板检验,吹扫后,
木板上无铁锈、脏物时,应为合格。
6.4油清洗合格标准
7.成品保护:
7.1当管道经水冲洗合格后暂不运行时,应将水排净,并应
及时吹干。
7.2油清洗应采用适合于被清洗机械的合格油,清洗合格的管道,应采取有效的保护措施。
试运转前应采用具有合格证的工作用油。
8.施工注意事项:
8.1管道在压力试验合格后,建设单位应负责组织吹扫或清洗(简称吹洗)工作,并应在吹洗前编制吹洗方案。
8.2 吹洗方法应根据对管道的使用要求、工作介质及管道内表面的脏污程度确定。
公称直径大于或等于600mm的液体或气体管道,宜采用人工清理;公称直径小于600mm的气体管道宜采用空气吹扫;蒸汽管道应以蒸汽吹扫;非热力管道不得用蒸汽吹扫;对有特殊要求的管道,应按设计文件规定采用相应的吹洗方法。
8.3 不允许吹洗的设备及管道应与吹洗系统隔离。
8.4管道吹洗前,不应安装孔板、法兰连接的调节阀、重要阀门、节流阀、安全阀、仪表等,对于焊接的上述阀门和仪表,应采取流经旁路或卸掉阀头及阀座加保护套等保护措施。
8.5吹洗的顺序应按主管、支管、疏排管依次进行,吹洗出的脏物,不得进入已合格的管道。
8.6吹洗前应检验管道支、吊架的牢固程度,必要时应予以加固。
8.7清洗排放的脏液不得污染环境,严禁随地排放。
8.8吹扫时应设置禁区。
8.9蒸汽吹扫时,管道上及其附近不得放置易燃物。
8.10管道吹洗合格并复位后,不得再进行影响管内清洁的其他作业。
8.11管道复位时,应由施工单位会同建设单位共同检查,并应填写“管道系统吹扫及清洗记录”及“隐蔽工程(封闭)记录”。