模具的概念
模具的知识点总结

模具的知识点总结一、模具的基本概念1. 模具的定义:模具是用于生产制品的工艺装置,是一种工业生产中常用的辅助工具。
2. 模具的作用:模具是将原材料经过一定的加工和成型工序,制成具有一定形状和尺寸的制品的工具。
二、模具的分类1. 按成品类型分类:模具可分为塑料模具、压铸模具、橡胶模具、冲压模具等。
2. 按加工方式分类:模具可分为冷冲模、热冲模、复合模、硬模、软模等。
3. 按使用领域分类:模具可分为汽车模具、家电模具、日用品模具等。
三、模具的制造工艺1. 模具设计:模具设计是根据产品的要求和工艺特点,确定模具的结构形式、尺寸精度、加工工艺等内容。
2. 模具加工:模具加工包括模具零件的粗加工、精加工、装配以及热处理等工序。
3. 模具调试:模具调试是指将制造好的模具装配到设备上,进行成型工艺试验,验证模具的可用性和性能。
四、模具的材料1. 模具的零部件通常采用优质合金钢和工具钢制造。
2. 塑料模具的主要材料为45#钢、P20钢、718钢等。
3. 压铸模具的主要材料为H13钢、8407钢等。
4. 橡胶模具的主要材料为S50C钢、SKD61钢等。
五、模具的设计原则1. 模具设计应根据产品的使用要求,确定模具的结构和精度等技术参数。
2. 模具设计应根据材料特性和成本要求,合理选择材料和加工工艺。
3. 模具设计应遵循产品开发的原则,确保模具的可靠性和稳定性。
六、模具的使用与维护1. 模具使用过程中,应定期对模具进行检查和保养,确保模具的精度和可靠性。
2. 模具使用过程中,应注意控制模具的使用次数和工艺参数,减少模具的磨损。
3. 模具使用过程中,应按规定使用润滑剂,保证模具的正常工作。
总结:模具作为工业生产中不可或缺的一部分,对于提高产品质量和生产效率有着重要的作用。
通过对模具的相关知识点进行总结,可以更加深入地了解模具的制造工艺和使用原则,对于提高模具的设计和制造水平有一定的指导作用。
希望通过本文的介绍,能够对模具制造领域有所了解,为读者提供参考和借鉴的价值。
模具拆装知识点总结

模具拆装知识点总结一、模具拆装的基本概念1. 模具:模具是用于生产制品的工具或工装,其作用是将加工过的原材料通过压力、温度和其他作用力的作用,使得原材料充分充实模具中的造型腔内,从而得到产品的外表面和内部形状。
2. 模具拆装:当模具使用的一段时间后,需要清洗、维护或更换模具零件,就需要进行模具拆装。
模具拆装是模具维护保养的重要环节,也是为了确保模具使用安全和生产效率的需要。
二、模具拆装的原则1. 安全原则:模具拆装操作必须严格按照操作规程进行,严禁漫不经心、随意行事,保证操作安全。
2. 效率原则:模具拆装过程要迅速、有效地完成,避免生产线长时间停机,影响生产进度。
3. 严密原则:模具拆装后必须检查并确认所有零部件完好无损,确保没有遗漏,避免在使用过程中发生意外情况。
三、模具拆装的步骤1. 拆模前准备:对模具进行彻底的清洁,清理模具内的残留材料及异物,准备拆模所需的工具和辅助设备。
2. 拆模台车固定:使用拆模台车将模具升离设备或机床,并固定好,防止在拆卸过程中发生摇晃或倾倒事故。
3. 拆卸模具零部件:按照模具拆解图纸或操作规程,逐步拆卸模具零部件,并按规定进行标记和分类,以便后续组装时更加方便。
4. 清洁保养:拆卸下来的模具零部件需要进行清洁和保养,确保其表面光洁、无损,以便下次装配和使用。
5. 组装模具:待零部件清洁干净后,按照组装图纸或操作规程的要求,逐步进行模具的组装,注意细节,确保每个部位的连接牢固、无误差。
6. 调试检查:完成模具的组装后,对模具进行一次全面的调试检查,确认模具能够正常使用,确保在生产中无故障。
四、模具拆装的注意事项1. 拆装作业要在经过专业人员的指导和监督下进行,严禁操作人员擅自进行模具的拆装。
2. 在拆卸模具时,尽量避免使用过硬的工具和设备,以免划伤或损坏模具零部件。
3. 在拆装模具时,要注意承载能力,避免模具零部件的摔坏或受力过大而损坏。
4. 拆装模具时,要用专用设备和工具,以确保操作的精准性和安全性;严禁使用普通不合适的工具,以免造成不必要的损伤。
01-注塑 模具 基础

交口夹板
22
1. 模具的概念及构造
注塑 模具的动作顺序 2段模具
- PARTING面上 固定侧移动侧分开 - 成型品与交口 成型后分离开 (SLIDE GATE,DIRECT GATE) - 构造简单 取给容易 - 适合自由垂下 (submarline 交口; 不必要后加工) - 故障少价格低廉 料把, 交口及注塑交口和行腔在同一面上的 模具. 1个衔接面 上 可动侧与固定侧分离 料把, 交口, 成型品成一体进行脱模 23
15
⑤ Blow Molding
16
⑥ 熱成型(Thermoforming)---真空成型(Vaccum Mould): 热可塑性 塑料的 板及胶片加热后软解, 形和素材板之间 空气 向打头透的洞内 密封且进行成型, 把其冷却后得到理想的部品的方法 . 或压孔成型法是 形的相反方向 抽出压缩空气再把素材板向形上粘贴 成型的方法厚板及 变形抵抗大的热可塑性 塑料上适用 .
展延性(Malleability,
Ductility),
流動性(Fluidity) 等 性質把材料를加工成形, 作为製品 生産 道具 可叫‘模’或‘形’. 小范围意义 : 利用金屬材料 来作成的 模(形).
技術的 意味 : 为把同一 規格的 製品 大量进行 生産而作成的 母體性模. * 现如今大部分的 工業製品随着被 大量生産此种 所有 工業製品根据 量産成形来存在 * 模具正是 把这些变为可 量産 成形的 道具
로케이팅 링 디스크 스페이서
导柱 导管
sprue 부시
앵귤러 핀(12도) 테이퍼 록 핀
디스크 스페이서
顶杆
2段顶杆 2nd 스페이서 링
顶杆导柱
밀판 가이드 부시 스톱 핀
模具基本知识
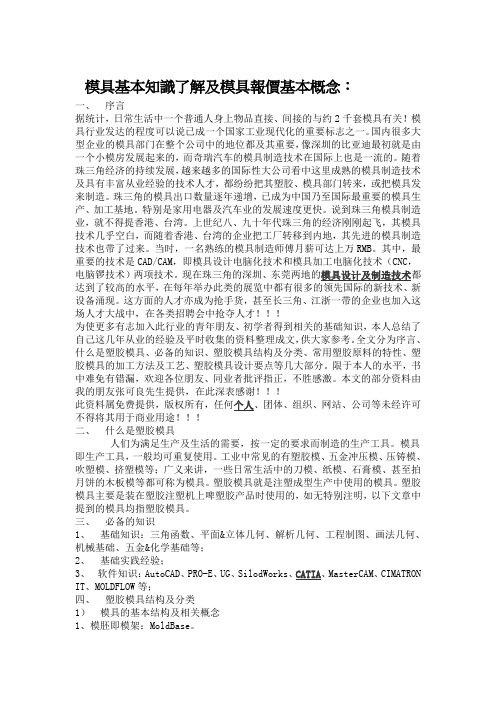
模具基本知識了解及模具報價基本概念:一、序言据统计,日常生活中一个普通人身上物品直接、间接的与约2千套模具有关!模具行业发达的程度可以说已成一个国家工业现代化的重要标志之一。
国内很多大型企业的模具部门在整个公司中的地位都及其重要,像深圳的比亚迪最初就是由一个小模房发展起来的,而奇瑞汽车的模具制造技术在国际上也是一流的。
随着珠三角经济的持续发展,越来越多的国际性大公司看中这里成熟的模具制造技术及具有丰富从业经验的技术人才,都纷纷把其塑胶、模具部门转来,或把模具发来制造。
珠三角的模具出口数量逐年递增,已成为中国乃至国际最重要的模具生产、加工基地。
特别是家用电器及汽车业的发展速度更快。
说到珠三角模具制造业,就不得提香港、台湾。
上世纪八、九十年代珠三角的经济刚刚起飞,其模具技术几乎空白,而随着香港、台湾的企业把工厂转移到内地,其先进的模具制造技术也带了过来。
当时,一名熟练的模具制造师傅月薪可达上万RMB。
其中,最重要的技术是CAD/CAM,即模具设计电脑化技术和模具加工电脑化技术(CNC,电脑锣技术)两项技术。
现在珠三角的深圳、东莞两地的模具设计及制造技术都达到了较高的水平,在每年举办此类的展览中都有很多的领先国际的新技术、新设备涌现。
这方面的人才亦成为抢手货,甚至长三角、江浙一带的企业也加入这场人才大战中,在各类招聘会中抢夺人才为使更多有志加入此行业的青年朋友、初学者得到相关的基础知识,本人总结了自己这几年从业的经验及平时收集的资料整理成文,供大家参考。
全文分为序言、什么是塑胶模具、必备的知识、塑胶模具结构及分类、常用塑胶原料的特性、塑胶模具的加工方法及工艺、塑胶模具设计要点等几大部分。
限于本人的水平,书中难免有错漏,欢迎各位朋友、同业者批评指正,不胜感激。
本文的部分资料由我的朋友张可良先生提供,在此深表感谢此资料属免费提供,版权所有,任何个人、团体、组织、网站、公司等未经许可不得将其用于商业用途二、什么是塑胶模具人们为满足生产及生活的需要,按一定的要求而制造的生产工具。
模具课教育训练教材

第一章模具概念一.概述模具具有非常广泛的应用,可以说各个行业都离不开模具.模具已成为生产各种工业产品不可缺少的重要工艺装备.在这里只介绍冷冲模具.冷冲压模具可以分为单工程模具和连续模具,而单工程模具又可以分为冲孔模,下料模,折弯模和复合模等.二.模具组成及结构每一套模具都由几块模板,冲头和入块等组成.下面我们来了解一下各个模板的名称: 上模座(USET),上垫板(UPHUB),固定板(UPH),背脱板(STRUB),脱料板(STR),母模(DIE),下垫板(DIEDB),下模座(DSET),冲头(P),小冲(SP),大冲(BP),内脱板(KO),下固定板(DPH)等.每一套模具都至少具有上模座,下模座,冲头,脱料板,母模,固定板等几块模板.我们组装的模具有冲孔模,下料模,复合模和连续模. 冲孔模是指经过机器加工以后落到下面的料是没用的那种模具.是整套模具生产中的一个环节,它只是加工模具的内孔.下料模是指经过机器加工以后落到下面的料是有用的那种模具,它也是整套模具生产中的一个环节,它是加工模具的外形.复合模是可以一次完成模具的外形和内孔加工的模具,它和上面的两组模具一样也不能做折弯的工程.如果模具有折弯的部分,那还需要折弯模的工序,在这里我也不作介绍了.而连续模则可以一次完成整套模具的加工,它一道一道的工序做,所以对准确度要求较高.三.模具配合间隙1.剪断间隙(GAP)=料厚(T)*6%2.活动间隙一般情况下为一条半(一条=0.01mm),但绝对不能大于剪断间隙.3.螺丝在模板中间隙缩放关系一般为单边放大0.5-0.1 mm.(铣床加工)4.固定销在模板中间隙缩放关系一般为单边放大0.004mm.(线割)5.导柱在模板中间隙缩放关系一般为单边放大0.002mm.(线割)6.在固定板(UPH)层中图形冲单边放0.008mm,异形冲单边放0.01mm.(线割)7.母模的大小=冲头的大小+剪断间隙. 脱料板(STR)的大小=冲头的大小+活动间隙.内脱板(KO)的大小=母模的大小—活动间隙8.在连续模中上垫板(UPHUB),背脱板(STRUB),下垫板(DIEDB)都只是起通过作用,所以缩放间隙为单边放大0.5-1mm.9.螺丝的头部或其它一些零件的头部所在的图层中要逃孔的大小为零件头部大小再单边加1mm.10.连续模中下垫板(DIEDB),下模座(DSET)中的冲头孔只是起漏料作用,每一层比上一层单边放大0.5-1mm.四.常见冲头尺寸计算:1.闭模高度的确认(UPH, STR, STRUB的高度组合).如UPH=20mm, STR=20mm, STRUB=15mm,则闭模高度=55mm.2.冲孔冲头必须隐藏于脱料板.所以冲孔冲头长度L=上闭合高(UPH+STRUB+STR)+料厚t+(2~3)mm例如:UPH厚度为20mm,STRUB为15mm,STR为20mm. t=0.8则L=20+15+20+0.8+2=58mm.3.成型冲的确认(即向下打凸1.0高) 则冲子=闭模高+1.0,母模入块向下降1.0.(成型冲=打凸N或V字型,卷弯,斜度,冲剪成凸,翻边打断差等.)均属成型.4. 抽芽冲,折弯冲的确认.(即:视抽芽长宽及折弯高度来决定冲子长度,一般抽芽长直升部位必须有3~4mm, 视抽芽高度而定,折弯冲一般如果成品超过8.0高,不含R角)方能使90°成型.5. 入块的确认(若为冲孔入块则必须下孔为锥度状(上模冲成型2.0,下模入块则必须刚好低于模面2.0)6.向上拆弯入块突出母模面高度一般应为折弯深度的一半,避免划伤),而压料入块应高出拆弯入块1mm以上.第二章模具课组立作业规范一.组立前置作业:1.在一组模具图纸到手后,首先认真分析产品图,模具结构图,将产品结构,生产工艺以及模具制造中会遇到的问题牢记于心.2.对照模板图,零件图以及五金零件申购单检查模板,零件是否齐全,是否正确,包括模板厚度,光洁度,有无倒角以及各孔位大小位置.若有不妥,要及时反应并追踪到位.3.对照图面及模板将冲头,入块挂台方向,挂台高度以及总高度标示好,以做研磨加工.4.模板导柱及刀口检对,模板到齐后可以将母模板与脱料板迭好,装入导柱,然后进行刀口对正,所有剪口冲头必须滑配,以手轻轻推入为准.检验好后再依此将夹板与脱料板对正,直至上下模板可以顺利配置.5.模板刀口OK后,最后需将各相关联模板迭对,以确保其孔位加工有准,特别是冲孔落屑一定要顺畅,以免在组立中反复拆卸.6.以上若有问题点需记录于组立日志,以便积累经验,以及核算成本.二.组立要点:1.等高套筒,弹簧的选用与计算.(1) 套筒计算方式=最长冲子-脱板厚+1~2.0的高度.(冲子内缩量)若等高套筒吊在上垫板,则冲子长+上垫板厚-脱板厚+1~2.0. (冲子内缩量)(2) 弹簧选用=一般视材料成型及模具结构而定.折弯弹簧一般使用红色或绿色,材料较薄0.6以下则用红色,0.6以上则用绿色.抽牙弹簧一般使用绿色或茶色;成型冲弹簧一般使用红色或绿色;冲孔冲弹簧一般使用绿色.(3) 弹簧压缩量计算方式为: DF—50%极轻荷重(黄色) DL—40%轻荷重(蓝色) DM—30%中荷重(红色) DH—24%重荷重(绿色) DB—20%极重荷重(茶色).2.五金零件的选择与制作:(1) 内外定位及其顶料销的制作: 外定位要比内定位的直身位高至少1t(t表示料带厚度),而内定位旁的顶料销要比内定位的直身位低1 t.(2)导正销(引导销)的制作: 导正销的直身位伸出脱料板的长度为料厚+0.5t,而其旁的顶料销的长度伸出脱料面大于导正销直身位1.0t,特别注意的是此顶料销用圆线弹簧,力度不要过大,一般用0.4~0.7线径即可.(3)定位销的使用: 定位销在装入模中之前,要试配合模板中的孔是否过紧,必要时要铰孔处理加油使其便利进入.(4)导柱,导套的运用: 辅助导柱在无脱背的情况下,要检查导柱末端部与上夹紧配合的长度看是否长于上夹的厚度,若有长出则要铣深逃孔,避免和脱板发生干涉;导柱与各模板在正常间隙下活动,其长度则要根据模具的结构作选择;外导柱装入模座中,最好用油压机置入,这样可以避免受力倾斜,外导套与模座孔的单边间隙为0.08mm.(5)制高块的制作: 制高块的高度为h(制高块)=t(母模)+(冲件材料厚度t-0.2mm)左右作制高块的目的主要是:A.连续模中刚送料时,避免整个脱料板的受力倾斜,不平衡.B.避免模板中字模,压线印等零件的损坏.(6)灌胶的注意事项: 灌胶时要把模座孔内擦干净,光洁,要让导套与滚珠,导柱在孔内便活动,用等高块置于上下模座之间,并测量是否等高,然后开始灌胶. 灌胶4小时后即可开模,做装弹簧等动作,装入的顶料销浮升块等零件用手压缩,不至于让弹簧打死,全部工作完成,等待试模.3. 冲子装配要点:冲子或入块装入模板前需先用卡尺量测挂位沉头深度及冲子挂位长度(一般为5mm),确认OK后方可将冲子入块置入模板中,冲子若凸出太高,则需将沉头铣至低于模面0.1之高度,不可用打磨机磨掉,亦不可猛砸使其凹下,若沉头太亦应立即反应(不得低于模式面0.5以下),否遇会使冲子被拉出脱板外造成脱料板不顺之现象.4.闭模及灌胶要点:组模时在配入刀口与成型块确定间隙OK,长度尺寸,螺丝孔,等高套筒,固定梢,导柱孔,定位梢,避位处均无干涉现象时即可进行闭模,外导柱灌胶或装独立导柱三作业.(灌胶间隙为导柱尾部大于内孔0.05). 导套为导套正尺寸小导套孔+0.1灌胶时需确认每一块模板均紧贴齐面.灌胶作业于4小时后拆模将弹簧及顶料浮升零件置入,完成组模程序.5.组模后再对照整组模具认真检查每块模板之外观及模具内部结构,如避位是否确实避开,所有紧固螺丝是否锁紧,关键部位有无润滑,定位是否有松动,落屑是否顺畅等现象.三.常见模具之对模方式:在完成各项组立前置工作,确保模具在结构上及装配上无误后,可进行模具组立装配工作.一般常见模具的对模方式及过程有以下几种:(一)下料模: 开始组立模具时,一般应由下模开始组立.1.将下夹板与下脱料板装入导柱,公模放入下夹板上定位梢.2. 上紧套筒待完成后将套筒顶至高出公模半块成品料厚(此为正常下料模下模套筒长度,若下模有上下成型冲则脱料板与成型冲平齐)3. 放入弹簧上螺丝不能完全锁紧,把定位梢固定下模板架构方能上紧螺丝.4.组装上模,将脱料板放入母模盖上夹板,开始组模.(※上模脱料板需超出母模1m/m长)(二)冲孔模:1.在组立模具之前最好将以往的试模经验加以溶合.如:脱料上的问题,如折弯脱料,凸点脱料,抽牙脱料,铆合抽孔脱料等,以上种种问题皆需顾及弹簧的弹力与压缩量.2.注意导柱长度是否在适当长度,下模导柱避位深度是否足够,上模座导柱挂台避位3.预估你组立的模具试模时会产生何种现象,当现象发生时你将作何处置.(三)折弯模: 一般向上折弯可区分为三种:1.线割外形向上折弯模2.利用下夹板精铣沟槽以定位折弯块之向上折弯模3.以90° V形成型之折弯模(1)线割外形向上折弯模最常见的线割外形折弯模,它通常做为公母模共享,故我们组立时需在留意公母模的料厚间隙问题.A.先将测量母模线割外形尺寸.不得小于成品外形.B.查出公模所要研磨的尺寸(预留精修)将公模配入夹板定位,再与母模利用导柱将两块模板定位,用间隙片测量折弯公模式与母模之间的间隙进行配刀,直到材料厚度(t)准时即可.(※注意间隙不可过紧)C.组立下模进注意,弹簧压缩量,预压量,是否在正常值下.( ※所谓正常值:即是弹簧力量过大于90°,),此时可用压线克服加强90°之稳定性;若弹簧力量过小则会产生90°内弯现象,此时则需测量产品高度,不可倒过大的角度,若产品折弯高度已在上限则以放开间隙,降低折弯深度或加强弹簧以相互利用,达成90°之需求.D.组立下模时需注意冲制品以三边成型,则需先折对称两边折弯约1.5~3 m/m(视素材t厚而改变);再折另外一边此种方式可避免产品拉料现象.E.组立上模时需注意,公模脱料的浮升梢跟刀口距离;其浮升梢四分点刀口不得超过3.5m/m;(一般料厚1.6 m/m以下皆可适用),再则留意弹簧力量.(以1.0 m/m素材而言,大约25m/m折线就需有2条绿色,直径为10;行程10m/m~12m/m弹簧).F.注意公模本身侧面的表面粗糙度,因为它将增强脱料的磨擦系数严重将使其脱节料不顺畅,其解决方式可用细目油刀石将表面推亮.(2)向上折弯模,其中若折弯块上割有滚轮时就必须注意,滚轮与折弯块装配后是不是可以很顺畅的滚动,若无法滚动时就必须利用砂布将沟槽拋光,直到滚坳顺畅.(3)测量,检测滚轮与折弯块装配后宽度,高度是否与入块同一尺寸,若侧割滚轮有偏位则心须做局部修整,再进一步将入块装入下夹键槽内,装入滚轮,测量两侧折刀尺寸,其尺寸可大于成品外形+N;--0.如:(4)折弯块之成型,当内脱料板厚为20mm;折弯块为35 mm时折弯块从底部算起23 mm以上的位置须让位0.1 mm以避免成品在折弯过程中被滚轮下端尖端锐角刮伤.(5)在组模时折弯块底部须做倒角约(0.3~0.5 mm)以避免下键槽壁刮伤损坏,如此即可准备组模动作.(内脱料板需高出下模折弯块1 mm)(6)上折弯公模虽然没有较具体的技巧性,但仍须注意下列三项A.压线问题考虑冲制的素材是否须要压筋;压筋的深度是否过深,因为将影响90°向上折弯与成品高度.B.脱料问题无论任何一种90°向上折弯皆需要装置浮升梢顶料,如:三面折弯;二面折弯甚至一面或四面折弯原理在于如何让冲制品在最佳平衡状态下脱模.C.滑块间隙问题滑块间隙不可过松或过紧,一般最大值间隙为0.05m/m若折弯成品0.1m/m~0.3m/m时其滑块间隙为0.03m/m以下.※滑块加有顶料梢时,顶料梢最佳放制点为滑块的1/3点.(接近公模位置的1/3~1/4点为最佳位置,但注意顶料梢浮升时不可撞击公模斜边.)四. 试模及模具维修:1.试模规范: 在模具组立及检查完毕后方可试模,新进员工由于对机床熟练程度可能不够,试模时请务必知会班组长.同时班组长在试模期间也需在现场做技术指导与监督,以免发生突发及意外事件,并做好试模报告记录.2.试模常见异常及维修:A连续模: (1)送料不顺: 发生原因多为浮升两用梢的送料宽度与试模料不符,或者所放间隙过小,再者下模浮升引导梢, 浮升块有无过高造成挡料.(2)上模带料: 发生原因多为: a上模导正梢直身过长或较为粗糙. b. 送料步距有误. C.上模冲头或向上折弯脱料不顺.(3)废料反弹: 连续模在快速冲压情况下多会发生废料反弹现象.原因常有几种: a.冲孔间隙过大. b. 冲头有磁性. C.冲入深度不够,此时可以适当调整间隙及冲孔深度.再者可以将冲头研磨斜面减小真空吸附力或者做子母冲.B.下料模: (1)脱料不顺: 检查模具内外脱板是否滑配,脱料弹簧力是否够大,是否均衡.(2)产品与料带或外脱夹料,难以取出,解决方法:a.降低外脱b.外脱脱料力量减弱(3)产品毛边过大检查对策: a.冲减间隙是否过大或过小. b. 刀口是否锋利 c.刀口配合是否有准.C.成型模: (1)脱料不顺: 原因应有多方面应针对实际情况解决,常见原因主要有:a. 脱料力不足b. 折弯入块光洁度不足c.脱料力不均衡,造成掊料不一致此时可增加顶料梢或增加弹簧预压量,或者将折弯入块用小油石或拋光砂轮拋光滑,再者就是调整脱料力所分布位置及大小使其均衡.(2)角度不准:常发生情况有:(一)角度过大: a.间隙过大 b.折弯直身过短 c.压料力量过大 d.外定位过紧 e模具闭合不良(二)角度过小: a.间隙过小 b.压线过深 c.压料力量过小 d.模具闭合不良(3)尺寸不准: 造成尺寸不准的原因可能有: a. 定位不准 b.展开错误 c. 折弯成型时拉料针对以上情况可用以下方法调整: a.增加定位或定位调整 b.展开计算检查 c.加强压料力(4)外观模痕: 改善对策: a.折块R角适当加大,拋光至圆滑过渡 b.适当放大折弯间隙 c.做滚轴式折块五.模具后期工作:模具后期工作主要是对模具外观及细节的检查,以免交模后发生不必要的错误,主要可以从以下方面着手:1.模具包观良好,上下模座必须研磨光亮,无明显刮痕,凹痕以及锈斑.2.冲小孔入块必须背面逃孔,所有冲孔处落屑检查,必须顺畅,以免废料堵孔造成爆模.3.下料模限位柱,上下模位置对正,大小一致,表面不应过于粗糙.4.模具闭合高度以及上模架模螺丝孔是否符合客户要求.内外导柱配合是否顺畅.5.模内清洁,关键部位必须加以润滑.另外案内梢使产品定位良好,不得太紧,且案内梢本身不得过松,以防生产过程中跳出造成爆模.所有模板及冲头,入块完全无磁性.附冲压操作规范 :使用冲床试模时﹐务必将安全检测器开启﹐方能试模﹐试模人数不能超过3人﹐操机者必须由组长或资深人员进行﹒操机人员身后不得站人及围观﹐每次冲压检查模料时安全开关一律按下﹐未按下时﹐头部﹑手部不得伸入模面﹐冲压进行中切勿让眼睛与母模面闭合同高度﹐以免异物弹出造成眼睛受损﹐试模时不得使用脚踏开关﹐如需用脚踏开关必需经理及组长在现场﹐非主管部任何人均不得用脚踏开关。
模具工艺制造实训报告
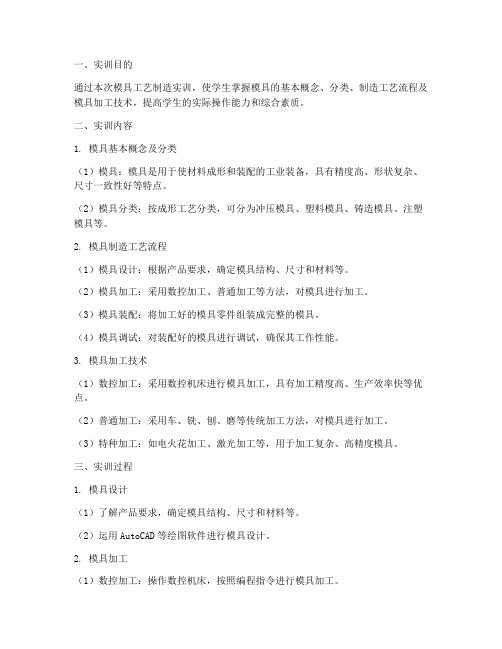
一、实训目的通过本次模具工艺制造实训,使学生掌握模具的基本概念、分类、制造工艺流程及模具加工技术,提高学生的实际操作能力和综合素质。
二、实训内容1. 模具基本概念及分类(1)模具:模具是用于使材料成形和装配的工业装备,具有精度高、形状复杂、尺寸一致性好等特点。
(2)模具分类:按成形工艺分类,可分为冲压模具、塑料模具、铸造模具、注塑模具等。
2. 模具制造工艺流程(1)模具设计:根据产品要求,确定模具结构、尺寸和材料等。
(2)模具加工:采用数控加工、普通加工等方法,对模具进行加工。
(3)模具装配:将加工好的模具零件组装成完整的模具。
(4)模具调试:对装配好的模具进行调试,确保其工作性能。
3. 模具加工技术(1)数控加工:采用数控机床进行模具加工,具有加工精度高、生产效率快等优点。
(2)普通加工:采用车、铣、刨、磨等传统加工方法,对模具进行加工。
(3)特种加工:如电火花加工、激光加工等,用于加工复杂、高精度模具。
三、实训过程1. 模具设计(1)了解产品要求,确定模具结构、尺寸和材料等。
(2)运用AutoCAD等绘图软件进行模具设计。
2. 模具加工(1)数控加工:操作数控机床,按照编程指令进行模具加工。
(2)普通加工:根据加工工艺,对模具进行车、铣、刨、磨等加工。
3. 模具装配(1)按照装配图,将加工好的模具零件组装成完整的模具。
(2)检查模具装配质量,确保装配精度。
4. 模具调试(1)对装配好的模具进行试模,观察模具工作性能。
(2)根据试模结果,调整模具结构,确保模具工作性能。
四、实训心得1. 通过本次实训,我深刻认识到模具制造工艺的重要性。
模具是工业生产的重要装备,其质量直接影响产品的质量和生产效率。
2. 模具设计、加工、装配和调试是模具制造的关键环节。
在设计阶段,要充分考虑产品要求、加工工艺和装配精度等因素;在加工阶段,要熟练掌握数控加工、普通加工和特种加工等技术;在装配阶段,要严格按照装配图进行操作,确保装配精度;在调试阶段,要观察模具工作性能,及时调整模具结构。
模具设计与制造专业描述
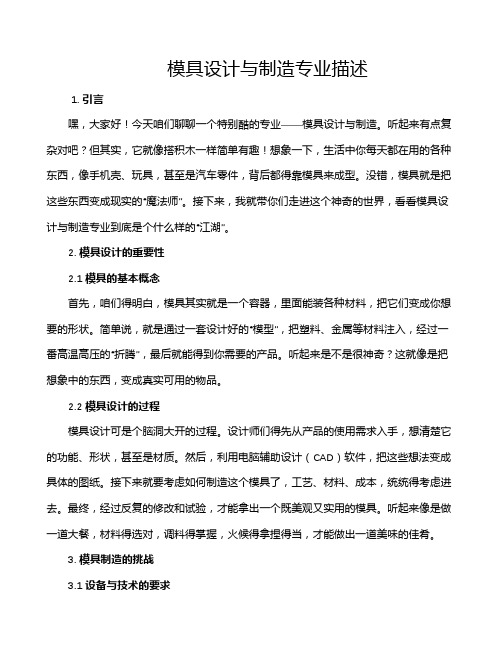
模具设计与制造专业描述1. 引言嘿,大家好!今天咱们聊聊一个特别酷的专业——模具设计与制造。
听起来有点复杂对吧?但其实,它就像搭积木一样简单有趣!想象一下,生活中你每天都在用的各种东西,像手机壳、玩具,甚至是汽车零件,背后都得靠模具来成型。
没错,模具就是把这些东西变成现实的“魔法师”。
接下来,我就带你们走进这个神奇的世界,看看模具设计与制造专业到底是个什么样的“江湖”。
2. 模具设计的重要性2.1 模具的基本概念首先,咱们得明白,模具其实就是一个容器,里面能装各种材料,把它们变成你想要的形状。
简单说,就是通过一套设计好的“模型”,把塑料、金属等材料注入,经过一番高温高压的“折腾”,最后就能得到你需要的产品。
听起来是不是很神奇?这就像是把想象中的东西,变成真实可用的物品。
2.2 模具设计的过程模具设计可是个脑洞大开的过程。
设计师们得先从产品的使用需求入手,想清楚它的功能、形状,甚至是材质。
然后,利用电脑辅助设计(CAD)软件,把这些想法变成具体的图纸。
接下来就要考虑如何制造这个模具了,工艺、材料、成本,统统得考虑进去。
最终,经过反复的修改和试验,才能拿出一个既美观又实用的模具。
听起来像是做一道大餐,材料得选对,调料得掌握,火候得拿捏得当,才能做出一道美味的佳肴。
3. 模具制造的挑战3.1 设备与技术的要求说到模具制造,那就得提到一大堆高精尖的设备。
比如,数控机床、激光切割机等,都是现代模具制造的好帮手。
这些设备可不简单,操作起来需要一定的技术和经验。
要不然,搞不好就会把一块金属材料切成几块废铁!不过,别担心,经过系统的学习和实践,这些操作都能成为“驾轻就熟”的事儿。
3.2 质量与成本的平衡再来说说模具制造中的另一个大挑战——质量和成本的平衡。
大家都知道,便宜没好货,贵的也未必是最好的。
在模具设计与制造过程中,设计师和制造商需要不断权衡这两者。
要保证模具的质量,让产品使用得长久,同时又不能让成本高得离谱。
模具制造知识点总结大全

模具制造知识点总结大全一、模具的基本概念模具是用来制造特定形状的产品的工具。
它通常包括两个部分,一是模具本体,它是用来制造产品形状的部分;二是模具座,它是用来安装和固定模具本体的部分。
模具的制造可以分为设计、加工和装配三个阶段。
二、模具的主要分类根据模具的用途和制造工艺的不同,模具可以分为塑料模具、压铸模具、冲压模具、橡胶模具、玻璃模具等多种类型。
1. 塑料模具塑料模具主要用于生产塑料制品,包括注塑模具、挤出模具、吹塑模具等。
2. 压铸模具压铸模具主要用于生产金属制品,包括铝合金压铸模具、锌合金压铸模具、镁合金压铸模具等。
3. 冲压模具冲压模具主要用于生产金属板材制品,包括冲压拉伸模具、冲裁模具、弯曲模具等。
4. 橡胶模具橡胶模具主要用于生产橡胶制品,包括硅胶模具、橡胶压模具、橡胶注塑模具等。
5. 玻璃模具玻璃模具主要用于制造玻璃制品,包括玻璃成型模具、玻璃切割模具、玻璃磨削模具等。
三、模具的设计与制造模具的设计与制造是一个复杂的过程,需要集成材料、结构、工艺、热流等多学科知识,下面是几个重要的知识点:1. 材料选择模具材料的选择对模具的寿命、精度和成本都有很大影响。
常用的模具材料包括工具钢、硬质合金、特殊合金钢等。
2. 结构设计模具的结构设计要考虑产品的形状、尺寸、材料、生产工艺等因素,设计出合理的结构,保证产品的精度和质量。
3. 工艺设计模具的工艺设计要考虑加工工艺和装配工艺,确定合适的加工方法和工艺流程,保证模具能够满足产品的要求。
4. 热流分析对于热流模具,要进行热流分析,确定冷却系统和加热系统的布局,保证产品的成型质量。
5. 制造工艺模具的制造工艺包括数控加工、电火花加工、线切割加工、磨削加工等多种工艺,要根据模具的材料和结构设计合理的制定制造工艺。
6. 装配与调试模具制造完成后需要进行装配和调试,保证模具的正常使用。
以上是模具的设计与制造的一般知识点,不同类型的模具还有各自特定的知识点,需要根据实际情况进行具体研究。
- 1、下载文档前请自行甄别文档内容的完整性,平台不提供额外的编辑、内容补充、找答案等附加服务。
- 2、"仅部分预览"的文档,不可在线预览部分如存在完整性等问题,可反馈申请退款(可完整预览的文档不适用该条件!)。
- 3、如文档侵犯您的权益,请联系客服反馈,我们会尽快为您处理(人工客服工作时间:9:00-18:30)。
1.模具的概念,以及模具在现代工业中的作用。
概念:模具是用来成型各种工业产品的一中重要工艺装备,是机械制造工业成型毛坯或零件的一种手段。
作用:①用模具成型产品的工艺应用非常广泛;②模具成型制件可实现少、无切削的加工;③模具成型具有优质、高产、低消耗和低成本等特点。
2.模具工业发展趋势①发展精密、高效、长寿命模具;②发展高效、精密、数控自动化加工设备,提高模具制造水平;③发展各种简易模具技术;④完善、改进现有模具钢性能,开发新型模具钢种;⑤发展专业化生产。
3.我国模具制造与国外相比的落后之处主要表现为以下几个方面:①标准化程度较低;②模具品种少、效率低;③模具制造精度低、周期长;④模具寿命短、材料利用率低;⑤技术力量落后,管理水平较差4.模具成型工艺有哪些?①普通模锻;②挤压;③拉拔;④冲压;⑤压铸;⑥塑料成型5.模具寿命的定义是什么?定义:模具因为磨损或其他形式的失效、终至不可修复而报废之前所加工的产品的件数,称为模具的使用寿命,简称模具寿命。
6.模具寿命与失效的术语及其定义①模具服役:模具安装调试后,正常生产合格产品的过程叫模具服役;②模具损伤:模具在使用过程中,出现尺寸变化或微裂纹、腐蚀等现象,但没有立即丧失服役能力的状态称为模具损伤;③模具失效:模具受到损坏,不能通过修复而继续服役时称为模具失效;④正常失效:模具经大量的生产使用,因缓慢塑性变形或较均匀地磨损或疲劳断裂而不能继续服役时,称为模具的正常失效;⑤模具正常寿命:模具正常失效前生产出的合格产品的数目称为模具正常寿命。
7.简述我国模具技术的发展趋势。
针对当前模具寿命的现状,我国提出了中长期模具技术发展要点。
为提高模具寿命综合技术,近期的目标是:①对精密、复杂、大型、长寿命模具进行失效分析;②研究综合性能优良的模具钢,形成系列,淘汰老钢种;③研制高耐磨冷作模具钢,硬化精密热作模具钢,复合系易切削镜面塑料模具钢,新型硬质合金,钢结硬质合金模具材料;④研究真空热处理及表面热处理技术;⑤研制新型模具润滑剂和涂料、黏结剂;⑥研制新型喷镀、刷镀等新强化堆焊技术,提高模具维修技术,提供综合性措施,大幅度提高模具使用寿命。
到2020年的目标是:①研制高性能优质模具钢;②开发新型超硬合金钢、金属陶瓷、合成纤维等新型模具材料;③研究应用激光等新型热处理强化技术。
1、解释模具失效的意义是什么?P16答:提高模具的寿命其实就是延缓模具的失效。
失效总是从模具对服役条件最不适应的环节开始,而且失效模具的残骸上必然会留有失效过程的信息,总体而言,失效分析是对事物认识的一个复杂过程。
2、在什么条件下会失效?答:引起模具失效的因素有内因和外因,内因即材料方面,包括材料品质及加工工艺方面的各种因素;外因及环境方面,包括受截条件、时间、温度及环境介质多个因素。
任何模具失效都是在材料的强度、韧性与应力因素和环境条件不相适应的条件下发生的。
3、影响失效的因素有哪些?答:内因和外因。
模具失效的影响因素包括:模具的结构、模具工作条件、模具材料、模具制造。
其中模具结构、材料和制造属于内因,即材料方面,包括材料品质及加工工艺方面的各种因素;模具工作条件属于外因,即环境方面,包括受载荷条件、温度及环境介质镀铬因素。
4、按失效形式和机理课分为哪几类?答:磨粒磨损、粘着磨损、疲劳磨损、其他形式磨损。
P17磨粒的概念:工作表面的硬突出物或外来硬质颗粒存在共工作与模具接触表面之间,刮擦模具表面,引起模具材料脱落的现象称为磨粒磨损。
P9粘着磨损的概念:工作于模具表面相对运动时,由于表面凹凸不平,某些接触点局部压力超过了材料的屈服强度发生粘合,粘合的结点发生剪切断裂而开,使得模具表面材料转移到工作上或脱落的现象称为粘着磨损。
P21疲劳磨损的概念:两接触表面相互运动时,在循环应力的作用下,使表层金属疲劳脱落的现象称为疲劳磨损。
P23解释模具材料过量变形失效主要有哪些?是含义是什么?答:过量变形失效主要有:过量弹性变形失效;材料受外力作用是产生变形,去掉外力是即消失变形消失后材料的变形的形式和尺寸完全全恢复原样,这样的变形为弹性变形。
塑性变形失效;模具在使用过程中,由于发生苏习惯变形改变了几何形状或尺寸,而不能通过修复继续服役的现象称为塑性变形失效。
P24断裂时效的分类及其特征:韧性断裂特征:断裂是没有明显的塑性变形,断口形貌是光亮的结晶体。
脆性断裂特征:断裂是没有塑性变形,断口形貌是暗色纤维状沿晶断裂特征:裂纹沿晶界发展穿晶断裂特征:裂纹穿过晶粒内部混晶断裂特征:在准解理小平面内向四周放射的河流花样,小平面间存在大量短而弯曲的撕裂棱一次性断裂特征:断口呈结晶状疲劳断裂特征:疲劳扩展区是裂纹自裂纹源向纵深逐渐发展形成的,具有光亮的“贝纹”状的痕迹正断和切断特征:断层的宏观表面垂直、平行于方向1 冷冲裁模工作过程,分析变形受力情况,失效形式及对模具寿命的影响。
P28 答:①工作过程:冷冲裁模用于冷冲压加工的分离工序,主要是使各种板料冲切成型。
冲裁模的主要工作部位是凸模(或冲头)刃口和凹模刃口,在冲压力作用下,凸模引入凹模时,对板料施加一定压力,通过锋利的刃口使板料产生弹性变形、塑性变形,直至被剪裂。
②变形受力情况:在板料弹性变形阶段,冲头端面的中央部位与板料脱离接触,压力集中于刃口附近的狭小范围内,使刃口上的单位面积压力增大。
在板料塑性变形和剪裂阶段,凸模切入板料,板料挤入凹模内孔,使模具刃口的端面和侧面产生挤压和摩擦。
因此,模具在工作过程中刃口受到的力主要有正压力、侧压力、摩擦力和弯曲力等。
③失效形式:其失效的主要形式是磨损,除此之外,还能发生崩刃或局部断裂。
当比值d/t较小时,还会引起冲头的宏观塑性变形或折断。
④对模具寿命的影响:模具刃口受力的大小与板料的厚度和硬度有关。
冲头的压力通常大于凹模,尤其是在厚板上冲制小孔时,冲头的单位压力很大。
冲头受力越大,其寿命就越低。
2 弹性变形的抗力指标和塑性变形的抗力指标分别有哪些?P44-45答:弹性变形的抗力指标:用弹性模量E和切变模量G作为材料的刚度指标,衡量材料抵抗弹性变形的能力。
塑性变形的抗力指标:①冷作模具钢的碳含量一般较高,且在淬火和低温回火状态使用,其塑性较低、脆性较大,适宜用压缩试验测定其压缩屈服点。
②脆性较大的材料常用试验测定其抗弯屈服点。
③热作模具的工作温度较高,模具材料的塑变抗力不仅取决于材料室温下的屈服强度,还取决于材料的回火抗力及高温下的屈服强度。
3 疲劳断裂的定义是什么?快速断裂的类型有哪些?如何判断脆性断裂、韧性断裂、正断、切断?影响脆性断裂的因素有哪些?P46答:疲劳断裂:模具在循环应力的作用下经过一定周次所发生的断裂失效。
快速断裂的类型:韧性断裂和脆性断裂。
判断方法:脆性断裂特征:断裂时没有明显的塑性变形,断口形貌是光亮的结晶体;韧性断裂特征:断裂时有塑性变形,断口形貌是暗灰色纤维状;正断特征:断层的宏观表面垂直于方向;切断特征:断层的宏观表面平行于方向。
影响因素:取决于材料本身的性质和健全度以及模具的工作条件,如应力状态、工作温度、加载速度、环境介质等外界因素。
模具疲劳断裂的特点有哪些?1、失效抗力低;2、脆性断裂;3、对材料表面及内部的缺陷高度敏感;4、塑性变形的高度局部性和不均匀性;5、试验数据分散;6、疲劳断口有明显特征低周疲劳的特点是什么?最大循环应力接近或高于材料的屈服强度,它足以使材料的应力集中处等薄弱部位发生塑性变形,因而材料在每一周次的循环应力作用下,均产生一定幅度的塑性变形。
低周疲劳寿命较短,一般在10的二次方到10的五次方次的范围内。
影响疲劳强度的因素有哪些?1、应力集中的影响;2、表面状态的影响;3、尺寸因素的影响;4、材料本身的影响影响模具寿命的因素是什么?哪些是内因?哪些是外因?影响模具寿命的因素是:模具结构设计、模具工作条件、模具材料、模具的热加工和冷加工、模具使用状况内因:主要指模具的结构、模具的材料和模具的加工工艺。
外因:包括模具的工作条件和使用维护、制品的材质和形状大小等。
模具圆角半径对模具工艺、受力情况及寿命的影响是什么?采用圆角结构可以获得良好的工艺效果,同时,也可避免拐角处产生应力集中。
不同拐角形式产生的应力集中源不同,圆角半径越大应力分布越均匀,越不容易产生应力集中,拐角为尖角结构时应力集中最严重。
模具的圆角半径可分为外(凸)圆角半径和内(凹)圆角半径,凸圆角半径主要影响模具的工艺,过小的凸圆角半径在板料拉深中增加成型力;在模锻中,易造成锻件折叠等缺陷。
凹圆角半径主要影响模具的寿命。
小的凹圆角半径会使局部受力恶化,在四角半径处产生较大的应力集中,易萌生裂纹,导致断裂。
大的凹圆角半径使模具受力均匀,不易产生裂纹。
P82判断下列哪个模具寿命高①凹圆角半径主要影响模具寿命。
小的圆角半径会使局部受力恶化,在四角半径处产生较大的应力集中,易萌生裂纹,导致断裂。
大的圆角半径使模具受力均匀,不易产生裂纹。
从图中可以看出,在采用同一模具条件下,过渡半径R由 2.3增大到3.2,模具寿命就从1.5万件提高到2万件;②模具工作角度对成型过程中坯料的流动、成型力及模具寿命有很大的影响。
从图中可以看出,圆角过渡处加了过渡角、半径R增大到5,模具寿命就可以从1.5万件提高到30万件。
所以以上四个图最后一个图的模具寿命最高。
27.P83 5-5哪个图的寿命高及其原因?28.P86模具的工作间隙?1.冲裁模具凸、凹模的刃口间隙是工作间隙也叫冲裁间隙,不仅影响冲裁过程和冲裁质量,也影响模具的寿命。
2.当刃口间隙由板料厚度的5%加大到15%时,模具的一次刃磨寿命显著增加。
3.当间隙过大(>15%)时,料板的弯曲变形增大,凸、凹模端面与板料的接触面积减少,冲裁力集中于刃口处,使刃口处,使刃口塑变钝化。
4.刃口变钝又导致冲裁力增大,使模具的刃磨寿命降低。
5.实际中,获得高质量冲裁断面的最佳间隙值和保证模具较高寿命的最佳间隙值不是完全一致的,设计时应综合考虑作出最优的选择。
29.P110模具热处理一般缺陷有哪些?1.过热和过烧2.氧化和脱碳3.热处理裂纹4.硬度不足和软点5.黑色断裂6.脆性7.表面腐蚀(麻点)8.热处理变形30.p112产生表面腐蚀的原因有哪些?1.在箱式炉中防护剂使用不良,引起氧化、脱碳。
2.在盐浴炉中加热,盐浴校正剂选用不当,或校正剂中带有腐蚀性杂质,或脱氧后未捞渣。
3.模具进行空冷淬火,或在空气中预冷时间过长。
4.硝盐浴中存在大量氯离子,使模具产生电化学腐蚀5.模具淬火后没有及时清洗,使得残余盐腐蚀模具或模具淬火后虽及时清洗,但放置时间过长,没有采取防锈措施时,也将产生麻点。
防止表面腐蚀的措施是什么?:1.装箱保护(使用保护剂前烘干)2.盐浴及时脱氧、捞渣;尽量不进行空冷淬火。