西气东输管道工程管道对接环焊缝全自动超声波检测规范
长输管线对接环焊缝自动相控阵超声波检测技术

图 4 T O FD 图与不检波 A 扫描波形 2006 年 第 28 卷 第 5 期
( 3) T OF D 的局限性有① T OF D 有盲区, 位于 表面下几毫米处。同样, 近内壁的 T OFD 信号也不
清晰。并 且 T OF D 有过分 强调中 壁信号 的倾 向。 ② T OF D 波幅很低, 可能会被漏掉。沿缺陷方向扫 查时操作者无法判定缺陷在焊缝轴向的位置, 但用 脉冲反射检测可以得到解决。③ T OF D 通常不是 被标准核准的工艺, 所有关于合格/ 判废的判定应根 据脉冲反射数据来定, 图像分析时应将带状图、B 扫 描和 T OFD 相结合才能达到最佳效果。
是指在扫查焊缝时仅沿焊缝做直线运动, 波束 的设置是检测整个焊缝区域, 与传统的锯齿形扫查 方式不同。线形扫查是在分区扫查法基础上使用相 控阵技术或多探头技术来实现的, 它具有运动方式 简单, 适于自动化, 检测效率高的特点, 但必须保证 不漏检。相控阵技术使用的每个发射器都有特定的 角度并聚焦到焊缝的每个小区域上。在熔合线处聚 焦尺寸一般为 2 m m 或更小。由于聚焦足够小, 所 以可以有效地检测各自的区域, 并且对邻近区域反 射体上的重叠, 即当主反射体的反射波在 80% F SH ( 满屏波高) 时, 邻 近反 射体 的反 射波 位于 5% ~ 40% F SH 。并且在检测坡口角度小、使用自发自收 扫查方式时, 往往效果较差。建议使用串联扫查的 方式。使用串列法时需要两个探头一发一收, 但在 相控阵系统中, 靠一个探头就可以实现。 2. 3 衍射时差法( TOFD)
全自动超声波检测技术在管道对接环焊缝检测中的应用

试验研究N DT 无损检测全自动超声波检测技术在管道对接环焊缝检测中的应用田国良(葫芦岛市特种设备监督检验所,辽宁葫芦岛 125001)摘 要:介绍了全自动超声波检测技术在管道对接环焊缝检测中的应用。
采用全自动超声波检测、手动超声波检测以及射线检测方法对预制缺陷进行了检测。
通过金相解剖对比三种检测方法的优劣,发现全自动超声波检测技术的优势和发展潜力,得出超声波衍射时差法结合超声脉冲反射法可有效检测管道对接环焊缝缺陷。
关键词:全自动超声波检测;手动超声波检测;射线检测;超声波衍射时差法;预制缺陷 中图分类号:T G115.28 文献标识码:A 文章编号:100026656(2007)0820472205Application of Automatic U ltrasonic T esting T echnology in the Inspectionof Butt G irth Welds of PipelineTIAN G uo2liang(Huludao Special Equipment Supervision and Inspection Institute,Huludao Liaoning125001,China)Abstract:The application of automatic ultrasonic testing for the inspection of butt girth welds of pipeline was introduced.Automatic ultrasonic testing,manual ultrasonic testing and radiographic testing techniques were used on the inspection of embedded parisons between existing testing results showed that automatic ultrasonic testing had great advantages and bright application f uture.Final conclusion was drawn that the combination of both time of flight diffraction technique and pulse echo technique was effective for the butt girth welds testing of pipeline.K eyw ords:Automatic ultrasonic testing;Manual ultrasonic testing;Radiographic testing;Time of flight diffraction technique;Embedded defect 2006年伊朗IO EC公司在中国石油天然气管道局考察全自动超声波检测(以下简称AU T)应用于伊朗海上管道工程项目的效果时,提出在X70钢、<1016mm×21mm管件上用手工焊接预制11个缺陷(裂纹、未熔合、根部未焊透、夹渣及气孔等),分别采用AU T、手动超声波检测(以下简称MU T)以及射线检测(以下简称R T)进行对比试验,以验证AU T方法的可靠性[1,2]。
管道对接焊缝超声波检测作业指导书

管道对接焊缝超声波检测作业指导书6.1管径32-89mm对接焊缝的超声波检测6.1.1适用范围:本条适用于壁厚≥4 mm外径为32-159mm 管对接焊缝的超声波检测,适用于外径大于≥159mm,壁厚4-6 mm管对接焊缝的超声波检测,不适用于铸钢、奥氏体不锈钢管对接焊缝。
6.1.2检测工艺卡6.1.2.1检测工艺卡由具有II级UT资质人员编制,工艺卡的编制应与所执行的技术规范及本检测作业指导书相符。
6.1.2.2检测工艺卡由具有UTIII资质人员或UT检测责任师审核批准。
6.1.3检测仪器选用数字式超声波检测仪或A型脉冲反射式超声波检测仪,其工作频率范围为0.5-10MHz,水平线性误差不大于1%,垂直线性误差不大于5%。
6.1.3.1探头采用高阻尼、线聚焦斜探头或双晶探头,探头折射角应符合下表的规定:探头K值探头前沿,mm 管壁厚度(mm)4-8 2.5-3.0 ≤6>8-15 2.0-2.5 ≤8>15 1.5-2.0 ≤126.1.3.2试块a、应选用GS-1、GS-2、GS-3、GS-4专用试块。
b、当施工验收或设计文件另有规定时,也可以采用验收规范或设计文件要求的其他形式的标准试块和对比试块。
6.1.3.3耦合剂:化学浆糊或机油6.1.4工艺参数a、检测频率:2.5-5MHzb、扫描时基线调节:一般采用水平1:1调节。
c、检测灵敏度:φ2x20-16dB。
d、表面补偿:一般为4dB(当表面粗糙度Ra>6.3μm时应实测)。
E、检测位置:一般要求从焊缝两侧检测,因条件限制只能从一侧检测时,应采用两种不同折射角的探头检测,并在报告中注明。
6.1.5扫查灵敏度不低于最大声程处的评定线灵敏度。
6.1.6检测操作a、执行检测工艺卡的规定b、打开电源,连接仪器与探头,调节衰减器将检测灵敏度调整为评定线灵敏度。
c、将探头置于焊缝两侧作锯齿形移动扫查,探头的移动速度不得大于150mm/S,探头每次移动的距离不得超过晶片宽度,在保持探头移动方向与焊缝中心线垂直的同时,还要做小角度的摆动。
焊缝超声波探伤检验规程

焊缝超声波探伤检验规程1 目的指导本公司无损探伤人员工作,规范无损探伤的检验过程。
2 范围本程序适用于公司钢结构产品制造(包括外包外协件)中的无损检验工作。
3 职责3.1品保部探伤员Ⅰ、Ⅱ、Ⅲ级人员负责探伤工作的实施。
3.2品保部探伤员Ⅱ、Ⅲ级人员负责检验规程的编制、现场检测技术指导。
3.3品保部负责无损探伤的质量控制工作,对无损探伤中有争议的问题做出裁决。
3.4品保部负责自检报告的签发。
4 检验规程4.1探伤准备工作a) 距离一波幅曲线:利用RB-1或RB-2试块测试距离一波幅曲线,评定线、定量线和判废线满足GB11345-89标准中9.2.1的B级要求。
b) 探伤灵敏度:不低于评定线,扫查灵敏度在基准敏度上提高6dB。
c) 探伤时机:碳素结构钢应在焊缝冷却到环境温度,低合金结构钢应在完成焊接24小时后进行探伤;另外,探测要经过打磨,外观检验合格后进行探伤。
d) 探伤方式和扫查方式:探伤方式见:扫查方式有锯齿形扫查、前后、左右、环绕、转角扫查等几种方式。
e) 检查部位:检查部位根据GB50205-2001《钢结构工程施工质量验收规范》及设计文件、工艺文件。
f) 抽检率:当设计和合同未对抽检率做出规定时,按GB50205-2001《钢结构工程施工质量验收规范》表5.2.4,当设计和合同对抽检率做出规定时,按设计和合同执行。
4.2探伤方法4.2.1平板对接焊缝a) 探头选择探头的K值选择如表1。
表1 探头的K值根据厚度不同按下表选择图1 平板对接焊缝的超声波探伤4.3.2 T型接头焊接的检验按T型焊缝的特点及GB11345-89标准要求,选择以下三种探伤方式组合实施检验。
4.3.2.1焊缝内部缺陷检测a) 探头选择见(表2)b) 根据不同检验等级要求选择探伤面,探伤面如图1所示。
表2 探头的K值根据腹板厚度不同按下表选择b) 探测位置c) 对所有反射波幅超过定量线的缺陷,均应确定其位置,最大反射波幅所在区域和缺陷指示长度。
管道对接焊缝的超声检测
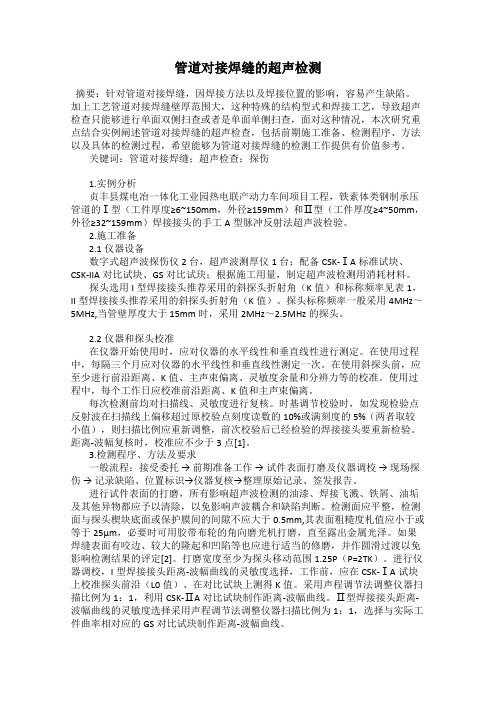
管道对接焊缝的超声检测摘要:针对管道对接焊缝,因焊接方法以及焊接位置的影响,容易产生缺陷。
加上工艺管道对接焊缝壁厚范围大,这种特殊的结构型式和焊接工艺,导致超声检查只能够进行单面双侧扫查或者是单面单侧扫查,面对这种情况,本次研究重点结合实例阐述管道对接焊缝的超声检查,包括前期施工准备、检测程序、方法以及具体的检测过程,希望能够为管道对接焊缝的检测工作提供有价值参考。
关键词:管道对接焊缝;超声检查;探伤1.实例分析贞丰县煤电冶一体化工业园热电联产动力车间项目工程,铁素体类钢制承压管道的Ⅰ型(工件厚度≥6~150mm,外径≥159mm)和Ⅱ型(工件厚度≥4~50mm,外径≥32~159mm)焊接接头的手工A型脉冲反射法超声波检验。
2.施工准备2.1仪器设备数字式超声波探伤仪2台,超声波测厚仪1台;配备CSK-ⅠA标准试块、CSK-IIA对比试块、GS对比试玦;根据施工用量,制定超声波检测用消耗材料。
探头选用I型焊接接头推荐采用的斜探头折射角(K值)和标称频率见表1,II型焊接接头推荐采用的斜探头折射角(K值)。
探头标称频率一般采用4MHz~5MHz,当管壁厚度大于15mm时,采用2MHz~2.5MHz的探头。
2.2仪器和探头校准在仪器开始使用时,应对仪器的水平线性和垂直线性进行测定。
在使用过程中,每隔三个月应对仪器的水平线性和垂直线性测定一次。
在使用斜探头前,应至少进行前沿距离、K值、主声束偏离、灵敏度余量和分辨力等的校准。
使用过程中,每个工作日应校准前沿距离、K值和主声束偏离。
每次检测前均对扫描线、灵敏度进行复核。
时基调节校验时,如发现检验点反射波在扫描线上偏移超过原校验点刻度读数的10%或满刻度的5%(两者取较小值),则扫描比例应重新调整,前次校验后已经检验的焊接接头要重新检验。
距离-波幅复核时,校准应不少于3点[1]。
3.检测程序、方法及要求一般流程:接受委托→ 前期准备工作→ 试件表面打磨及仪器调校→ 现场探伤→ 记录缺陷、位置标识→仪器复核→整理原始记录、签发报告。
西气东输管道环焊缝全自动超声波检测技术

防腐层 , 管线内有内涂层 。因此这 些管道是属于大 口 径厚壁管。对其焊缝 选用磁粉探伤 、 超声探 伤0 和射线探伤抽查 。本文
2 1 我 国管道环焊缝检测 主要采用手工超声波 和 .
面, 我国在 16 年建成 了第一条大口径输气管道巴 93
技术相 比, 它具有更高 的缺 陷检出率 ( 特别是危 害性 缺陷) 。能较好地测出缺陷 自身高度 , 测量速度快也
安全。但它仍有 以下局 限性 。
() 1 由于装了 1 多个探头 , 0 因此探头盘大而重 ;
() 2 不能适应各种不同的焊缝型式 ;
() 3 当管道直径或壁厚变化时 , 重新调试工作 比
焊缝主要采用射线检测 。为了提高无损检测的工作
效率和准确性 , 美国、 加拿大研究 了新的全 自动超声
展 。长输管道建设已从陆地 向海洋、 中延伸, 沙漠 另
外, 输送介质领域也不断拓宽。它还可 以输送 工业 原料 、 粮食 、 水泥、 煤浆等 固体物料。 到 19 96年底…, 国 已建 成 长输 油 、 管道 全 气 35 , 中输油管道 18条; 9条 其 7 输气 管道 27 , 1 条 总 长度 1213 k 。 73 . i 7n
管道运输成本低 、 运量大 、 占地少、 安全可靠 、 建 设周期短、 动化程度高 、 自 设备简单 , 可在较恶劣 的 自 然环境下连续运输 , 与其它运输方法相 比, 有很大 的优势。而 目 前我国的长输管道长度只有全世界的
110 因此 , /2 , 我国的管道运输业前景广阔 , 大有发展
定义扫查方法来提高成象质量 , 或开发适用 于 自己 要求的特殊扫查 , 该技术还可 以实现声 束角度和聚
焦在很大范围内的变化 , 能精确控制声束 的角度和
全自动超声波检测管道焊缝缺陷的评判

摘 要 :根据 全 自动 超 声波检 测 ( U )评 判 的基 本原 理和 实践经验 ,结 合 实际检 测得 到 的 西 气 东 A T
输 二 线 工 程 中 管 道 焊 缝 A T的 扫 查 图 .按 照 焊 缝 的坡 口 分 区 ,依 次介 绍 了根 部 、 钝 边 、 热 焊 及 填 充 U
O 引 言
才 能进 行评 定 T F O D和 B扫描 的显示 方 式有 别 于
带 状 图 T F 实 际 上 是 焊 缝 的 侧 视 图 , 纵 轴 代 表 O D
当前 我 国正处 于石 油 天然气 管 道建 设 的第 四次
高潮 ,管 道 向大 口径 、大 壁厚趋 势 发展 ,管道 自动
6 1
图 1 AUT典 型 扫 查 图
的判 断 能 力来 评 定 .应 通 过 根 部 B扫 描 、体 积 通 道 以及 T F O D通 道 的相互 比较 、互 相 验证 得 出正确 结论 。 钝 边 、热 焊 和根 部 的缺 陷 在 图 l中都 有 反 映 。
角度 原 因造成 的。根 据对缺 陷产生 的原 因分析 ,可 以得 到在 热 焊部位 的缺陷性 质 和深度 ( 图 2所示 如
负值 .以后 为 正值 。每 个分 区 的阈 门长度 不 等 ,在
6mm 到 1 m 左 右 .根 据 熔 合 线 到 焊 缝 中 心 线 的 8m
对 于 长输管 道 的焊接 .根部 焊接 是关键 .所 以
在 评定 过程 中尤 其要 关 注根 部缺 陷 。根焊 缺 陷 的评 定 比较 复 杂 .从 扫查 图上看 ,仅从 一个 通 道难 以准
层 等 各个 区域缺 陷在 扫查 图 中的表现 特点及 对 其定性 定量 的评 判方 法。
全自动超声波检测实用标准

西气东输管道工程企业标准培训教材管道对接环焊缝全自动超声波检测(Q/SY XQ 7—2001)盘锦北方无损检测公司2001年9月8日一、概述1、编制背景和过程1.1 西气东输工程是将我国西部地区的天然气通过管道输往急需清洁能源的东部地区,既满足东部地区对天然气能源的要求,又发展了西部经济,是东西部经济发展的系统工程。
此输气管道全长4000多公里,材质X70,规格为Ф1016×14.6-26.2mm,工作压力10MPa,是“十五”期间规模最大的管道工程。
本工程向国际招标,使用国际上最先进的技术,最先进的设备和最先进的管理方式,建成世界一流工程。
目前国内长输管道都采用常规超声波检测标准,又处于待修订状态,难以满足此工程需要。
因此,2000年6月西气东输项目经理部委托编写本企业标准。
编制的指导思想是即要与国际标准接轨,又要结合国情。
1.2 接受任务后各级领导重视,立即组成编写班子,搜集国内外长输管道检测标准和相关资料,并从加拿大R/D tech公司引进目前世界上最先进的多通道、声聚焦、分区扫查的全自动超声波检测系统,并在涩宁兰工程西气东输试验段成功演示,为标准的编制提供了一些有价值的数据。
同年12月份写出标准征求意见初稿,发给专家审查。
汇总专家意见,于2001年1月份写出征求意见稿。
2001年2月20日-21日,在廊坊招开了标准初评会,与会专家经过认真细致的讨论、分析、比较和决断,对标准条文进行修改,特别是强调了缺欠自身高度和缺欠位置的重要性,对标准验收部分做了大量的修改。
按初评会专家意见于2001年2月底整理出标准送审初稿。
此稿于2001年4月22日~24日又经西气东输施工技术标准评审会的专家们再次修订,形成送审稿。
2001年6月5日至7日经西气东输施工技术标准审定会的专家们的修订,形成报批稿。
2、编制依据标准的检测方法部分参照ASTM E1961-98,验收部分参照API1104-99、CSAZ-662、ALLIANCE和EN25817-92(D级)等(见表1)。
- 1、下载文档前请自行甄别文档内容的完整性,平台不提供额外的编辑、内容补充、找答案等附加服务。
- 2、"仅部分预览"的文档,不可在线预览部分如存在完整性等问题,可反馈申请退款(可完整预览的文档不适用该条件!)。
- 3、如文档侵犯您的权益,请联系客服反馈,我们会尽快为您处理(人工客服工作时间:9:00-18:30)。
目次前言 .........................................................................1 范围 ........................................................................2 规范性引用文件...............................................................3 检测人员.....................................................................4 超声设备.....................................................................5 检测准备.....................................................................6 检测系统的调试...............................................................7 现场检测.....................................................................8 缺陷显示的评定...............................................................9 验收标准.....................................................................10 报告和存档..................................................................附录A(资料性附录)典型的探头结构.............................................附录B(规范性附录)钢管中声速的测定...........................................附录C(规范性附录)报告格式...................................................III前 言本标准由范围、规范性引用文件、检测人员、检测准备、检测系统的调试、现场检测、缺欠本标准的检测方法部分参照ASTM E1961-1998《配备聚焦装置分区扫查的环焊缝全自动超声本标准验收部分按目前各国管道线路检测验收标准,不仅考虑缺欠的长度,还考虑了缺欠的本标准缺欠的长度参考API std 1104-1999《管道及有关设施的焊接》并结合我国长输管道环焊缝检测的实践确定,缺欠的自身高度参考美国ALLIANCE 管线验收标准和欧洲共同体EN25817-1992《钢电弧焊焊接接头缺陷质量分级指南》(D本标准代替Q/SYXQ-2002《西气东输管道工程管道对接环焊缝全自动超声波检测》,本标准本标准的附录A 为资料性附录,附录B 、附录C本标准主要起草单位:盘锦北方无损检测公司、中国石油天然气管道局生产技术处、中国石本标准主要起草人:张历成、赵 斌、袁少山、徐1西气东输管道工程管道对接环焊缝全自动超声波检测规范1 范围本标准适用于壁厚等于或大于7mm 、管径大于150mm的西气东输管道工程对接环焊缝检测与2 规范性引用文件下列文件中的条款通过本标准的引用而成为本标准的条款。
凡是注明日期的引用文件,其随后所有的修改单(不包括勘误的内容)或修订版均不适用于本标准,然而,鼓励根据本标准达成协议的各方研究是否可使用这些文件的最新版本。
凡是不注日期的引用文件,其最新版本适用于ASTM E-3173 检测人员3.1检测人员必须进行培训,经理论和实际考试合格,取得锅炉压力容器无损检测人员资格证3.2检测公司对从事全自动超声波检测人员进行设备性能、调试、评定等培训,经考试合格,4 超声设备 4.1该系统应该提供足够数量的检测通道,保证仅在管道环向扫查一周,即可对整个焊缝厚度方向的分区(见图1)进行全面检测;仪器的线性应按照ASTM E-317确定,每6个月校准一次,垂直线性误差小于等于满幅度的5%,水平线性误差小于等于满刻度的1%;闸门的位置和宽度任意可调,闸门内的信号电平不低于满幅度的20%4.2 记录系统4.2.1 通常用编码器记录焊缝环向扫查的位置。
编码器配置一个校正系统,保证显示记录的圆周距离与管道外表面标记的位置一致。
记录或标记系统应清楚地指示出缺欠相对于扫查起始点的位置,误差为 ±10mm;焊缝中的每个缺欠应有扫查记录;在显示记录上有声耦合4.2.2 焊缝缺欠扫查记录可用A 扫描、B 扫描或其它图象显示方式,也可增加衍射波时差(TOFD)4.2.3 TOFD 扫查装置的记录系统为256级灰度显示并且能够记录全R-F4.34.3.1聚焦探头应标出厂家的名称、探头类型、入射点、入射角或折射角、焦柱尺寸、频率及4.3.24.3.3 应准确布放探头与焊缝中心位置,探头楔块表面形状应与管道表面曲率相匹配,保证探头楔块与管表面吻合,保持稳定扫查。
4.4 试块4.4.14.4.1.1 试块的材料由业主提供该项目管线超声检测管道的一段,试块材料与受检材料的声速差不应超过±50m/s 。
业主应向检测公司提供检测项目的焊接工艺及试块的附加要求。
2图1 焊缝分区及缺陷简图4.4.1.2 根据焊缝坡口形式及焊接填充次数来分区,每个区高度一般为2-3mm ,设置两个对应的人工反射体用来调节灵敏度和缺欠定位,这两个反射体对该区探头来讲,称为主反射体(邻近区反射体对该区反射体来讲,不能称为主反射体)。
焊缝两侧各一个探头来完成一个区的检测。
4.4.1.3人工反射体在深度方向的布置应使显示信号达到独立的程度,但邻近区反射体不得互4.4.1.4a) 在坡口面上设置人工反射体,直径为2mm 的平底孔。
平底孔的中心线垂直于坡口面且在坡口面长度方向等分(见图2c 、db) 在外表面的熔合线上设置一个槽,深1mm 、宽2mm 、槽长10-20mm ,用来显示管道外表面的咬边或向表面延伸的未熔合等。
槽也可设在根焊区,根部槽长10-20mm ,其深度和角度与被检焊缝根部坡口形式一致(见图2c 、ec) 钻一个Ф2mm 的通孔(见图2b ),孔中心线与焊缝截面中心线相重合且垂直于管壁。
主要d) 必要时,钝边处设一个平底孔(见图2ae) 当设置人工反射体不能满足6.2.1.2要求时可增加其它的反射体,它们不得与规定的反f) 人工反射体允许误差不应超过下列数值,加工精度应符合ASTM E1961-1998孔直径:±0.1mm槽长度:±1mm 槽深度:±0.2mm所有相关角度:±1反射体中心位置:±0.1mmg)h) 试块上人工反射体的布置见图335 检测准备 5.1 受检表面制备5.1.1 探头移动区的宽度按检测设备而定,一般为焊缝两侧各不小于150mm5.1.2 焊缝两侧各150mm 范围内,管子制管焊缝(如螺旋焊缝、直焊缝)应用机械方法打磨至与母材齐平,打磨后焊缝余高应不大于0.5mm5.1.3 在管子防腐时,应在管端预留出150mm 的探头移动区,不得有涂层(如环氧粉末)。
5.1.45.2 每条焊缝应有编号标记,在平焊位置还应有起始标记和扫查方向标记,起始标记用“O ”表示,起始点为管线正上方中心点,即12点位置,扫查方向标记用箭头表示,通常沿介质流动方5.3 参考线5.3.1 参考线用于安装扫查器轨道。
在焊接之前,应在管子表面画一个参考线,参考线在检测区一侧距两坡口中心线的距离,应根据检测公司的检测设备而定,一般不小于40mm。
画参考线5.4 耦合剂5.4.1应选用适当的液体作为耦合剂,耦合剂应具有良好的透声性和适宜的流动性,对材料和5.4.25.4.36 检测系统的调试6.1 本检测系统是将焊缝沿厚度方向近似相等地分成几个区,分别覆盖根焊区、热焊区、填充区和盖面区,典型的分区方法见图1,每个区用一对探头检测。
要实现在管子上移动一周完成整6.2 检测系统的设置(分区调试)6.2.1a) 在试块的模拟焊缝中心线两侧,根据反射体的位置,将探头排布在轨道上的扫查器中(见附录Ab)移动扫查器,分别调整探头的位置,使每个探头对应的主反射体信号均达到峰值,即为(a )钝边处设置Φ2mm 的平底孔(b) 设置Φ2mm 的通孔4(c) 填充区设置Φ2mm 的平底孔(d) 热焊区设置Φ2mm 的平底孔(e) 根焊区设置Φ2mm 的平底孔或槽图2图3c) 将每个探头的峰值信号调整到满幅度的80%6.2.26.2.2.15a) 先用一侧探头的声束对准一个主反射体,在该反射体声束的路径上设置一个闸门,闸门的起点在坡口前至少3mm ,闸门终点至少超过焊缝中心线1mm ;该区另一侧闸门的设置与上述同; b) 熔合区的其它闸门按6.1.2.1a6.2.2.2填充区体积型缺欠居多,其显示信号幅度较垂直声束的未熔合缺欠反射信号弱且填充区比熔a) 当管子壁厚等于或大于12mm 时,在填充区的焊缝中心线上设置附加反射体,闸门的起点在探头侧坡口前至少1mm ,闸门终点至少覆盖熔合线(盖面区);该区另一侧闸门的设置与上述b) 当管子壁厚小于12mm ,可用熔合区的反射体调节填充区检测灵敏度,填充区检测灵敏度在熔合区基准灵敏度的基础上适当提高约8dB-14dB,6.2.2.3用槽对侧探头的声束对准该区的槽,在该槽声束路径上设置闸门,闸门的起点在探头侧坡口前3mm6.2.2.4用一侧探头的声束对准主反射体,在该反射体声束路径上设置闸门,闸门的起点在坡口前至少3mm6.2.3闸门电平不低于满幅度的20%,超过此幅度的信号按第8章评定。
检测气孔应采用B 扫描、TOFD6.2.4每个通道的输出信号均应在显示器上显示,对于每个主反射体,应在焊缝中心线两侧对称显示,也可用图象(B 扫描、TOFD6.2.5圆周扫查速度用公式1Vc ≤Wc ²PRF/3 (1)Wc ——PRF ——6.3 检测系统的总体调试6.3.16.3.1.1a) 每个主反射体的信号达到满幅度的80%b) 显示器上显示的编码位置精度:记录反射体间的显示编码位置相对于实际圆周位置的误差为±2mm6.3.1.2扫查过程中试块上主反射体的波幅达到满幅度80%时,其两侧邻近反射体的显示波幅应在5~40%(不包括40%)之间,低者覆盖不良,易漏检;高者可能产生干扰。