陶粒生产实用技术样本
陶粒制备方法
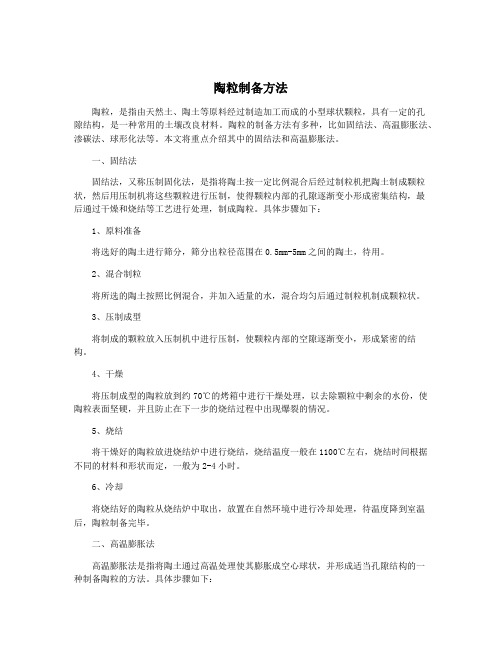
陶粒制备方法陶粒,是指由天然土、陶土等原料经过制造加工而成的小型球状颗粒,具有一定的孔隙结构,是一种常用的土壤改良材料。
陶粒的制备方法有多种,比如固结法、高温膨胀法、渗碳法、球形化法等。
本文将重点介绍其中的固结法和高温膨胀法。
一、固结法固结法,又称压制固化法,是指将陶土按一定比例混合后经过制粒机把陶土制成颗粒状,然后用压制机将这些颗粒进行压制,使得颗粒内部的孔隙逐渐变小形成密集结构,最后通过干燥和烧结等工艺进行处理,制成陶粒。
具体步骤如下:1、原料准备将选好的陶土进行筛分,筛分出粒径范围在0.5mm-5mm之间的陶土,待用。
2、混合制粒将所选的陶土按照比例混合,并加入适量的水,混合均匀后通过制粒机制成颗粒状。
3、压制成型将制成的颗粒放入压制机中进行压制,使颗粒内部的空隙逐渐变小,形成紧密的结构。
4、干燥将压制成型的陶粒放到约70℃的烤箱中进行干燥处理,以去除颗粒中剩余的水份,使陶粒表面坚硬,并且防止在下一步的烧结过程中出现爆裂的情况。
5、烧结将干燥好的陶粒放进烧结炉中进行烧结,烧结温度一般在1100℃左右,烧结时间根据不同的材料和形状而定,一般为2-4小时。
6、冷却将烧结好的陶粒从烧结炉中取出,放置在自然环境中进行冷却处理,待温度降到室温后,陶粒制备完毕。
二、高温膨胀法高温膨胀法是指将陶土通过高温处理使其膨胀成空心球状,并形成适当孔隙结构的一种制备陶粒的方法。
具体步骤如下:将所选的原料经过筛分,将粒径控制在1-5mm之间,在原料中加入化学添加剂,如氢氧化钠、碳酸氢钠等,调节陶土中的主要化学性质,使得烧后生成浮石的条件适宜。
2、高温处理将处理好的原料放入高温烧炉中进行高温处理,一般温度在1000℃以上。
在高温下,原料中的氢氧化钠或碳酸氢钠会分解放出大量气体,使得原料迅速膨胀成为球状,并形成适当的孔隙结构。
三、陶粒的应用陶粒是一种常用的土壤改良材料,主要应用于土壤改良、植物栽培、水利工程等领域。
它具有良好的透水性、透气性,能够增加土壤的孔隙度和通气性,促进植物生长。
自然养护法生产粉煤灰陶粒的配方和工艺流程
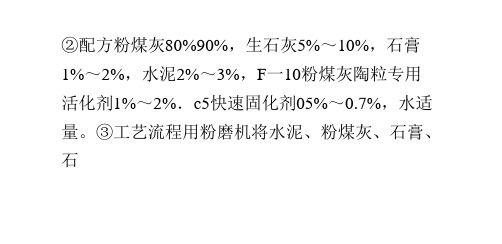
陈化仓,进行陈化反应。陈化时间2~4h.陈化温
度不能低于40℃,陈化仓相对湿度不能低于90%。
陈化结束后,将配台料重新输入轮碾搅拌机,补
充水分,继续轮碾搅拌3~4min。出料后,即可用 带式输送机将其送
人盘式成球机或辊式成球机。如果使用盘式成球
②配方粉煤灰80%90%,生石灰5%~10%,石膏
1%~2%,水泥2%~3%,F一10粉煤灰陶粒专用
活化剂1%~2%.c5快速固化剂05%~0.7%,水适
量。③工艺流程用粉磨机将水泥、粉煤灰、石膏、 石
石灰混合粉磨至0.08mm方孔筛筛余小于10%。若
使用湿排粉煤灰,需用烘干机将其烘干至含水量
小于2%,然后再混合粉磨。粉磨结束后,将混合
采用露天养护,一定要有防雨遮阳措施。陶粒要 用塑料布覆盖,塑料布外面再覆
盖草帘、棉被等保温。陶粒的堆放场地一定要比
周围地面高出30-50cm,以防雨水倒灌。如果条件
具备,可采用太阳能养护罩或太阳能养护仓对陶
粒进行升温养护,缩短固化时间。陶粒成型后, ,导致下部物料互相粘连成团,可
。否则新制成的陶粒会黏结成团。成型后的陶粒
可用带式输送机送至养护室或养护场堆存养护。
为缩短养护时间,在成型时要使用热水配料,水
温不低于60℃。陶粒进入养护室以后,要覆盖保 温棉被,防止热量散失。养护室的
相对湿度要达到100%。养护室的墙壁要涂刷保温
涂料,其外墙最好能贴一层保温砖,以提升养护
室的反应温度。防止物料与热量过快散失。如果
在陶粒成型后喷洒224型防黏剂。陶粒在养护过程
中,要防止风吹、雨淋和太阳曝晒。陶粒的自然
养护期一般为7~10天,养护期结束后,陶粒已经 达到相当的强度。这时可以
陶粒的制造工艺及流程

陶粒的制造工艺及流程
陶粒是一种轻质、多孔、具有一定强度的微细颗粒材料,常用于制造混凝土、陶土制品、填充材料等。
下面是陶粒的制造工艺及流程:
1. 原料准备:选择质量好的陶粒原料,一般选用粘土、陶土、石英砂等作为主要原料。
2. 原料粉碎:将原料进行研磨,使之变成粉末状,通过球磨机、砂磨机等设备完成。
3. 混合:将不同原料的粉末按一定比例混合,并加入适量的水,使其形成均匀的糊状物。
4. 成型:将混合好的糊状物进行成型,常用的成型方法有挤出法、浇注法和压制法等,可根据需要选择。
5. 干燥:成型后的陶粒需要经过干燥处理,常用的干燥方法有自然风干、太阳晒干和蒸汽烘干等。
6. 烧结:将干燥后的陶粒放入窑炉中进行高温烧结,一般烧结温度为1000℃-1200℃,时间根据陶粒的厚度和尺寸有所不同。
7. 表面处理:经过烧结后的陶粒表面可能有些粗糙,可以根据需要进行表面处理,使其更为光滑。
8. 包装:经过表面处理后的陶粒进行质检,合格后进行包装,
常用的包装方式有袋装、散装等。
以上是一般陶粒的制造工艺及流程,具体制造工艺可能会根据不同的原料和产品要求有所差异。
陶粒的制作配方工艺流程

陶粒的制作配方工艺流程
陶粒是一种常见的园艺用土壤改良材料,可以提供良好的通气性和保水性。
以下是陶粒的制作配方和工艺流程:
一、材料准备:
1.粘土:选择适合的粘土作为原料,可以选择黏土、石灰土等。
2.硅藻土:硅藻土是一种常用的陶粒原料,可以增加陶粒的通气性和保水性。
3.煤渣或稻壳:煤渣或稻壳可以作为陶粒的燃料。
二、配方比例:
根据实际需求和材料性质,可以根据以下比例进行配方:
粘土:50-70%
硅藻土:30-50%
三、工艺流程:
1.材料预处理:将粘土和硅藻土分别进行筛选和清洗,去除杂质和颗粒。
2.混合:将粘土和硅藻土按照配方比例进行混合,可以使用搅拌机或手工搅拌,确保材料均匀混合。
3.成型:将混合好的材料进行成型,可以选择压制、挤压或滚压等方法。
可以使用模具来获得所需的陶粒形状和大小。
4.干燥:将成型的陶粒放置在通风干燥的环境中,进行自然干燥。
也可以使用烘干设备进行加热和加速干燥。
5.烧结:干燥后的陶粒进行煅烧,可以使用窑炉进行烧结。
烧结温度和时间根据具体材料和需求进行调整,一般在800-1200摄氏度之间。
6.冷却:烧结后的陶粒进行冷却,待完全冷却后即可使用。
7.检验和包装:对陶粒进行质量检验,检查是否存在瑕疵或裂纹。
合格的陶粒可以进行包装和存储。
粉煤灰陶粒生产工艺

粉煤灰陶粒生产工艺
嘿,朋友们!今天咱来聊聊粉煤灰陶粒生产工艺,这可真是个有意思的事儿呢!
你想想看,那粉煤灰就像一群等待变身的小精灵,通过一系列神奇的步骤,就能变成有用的陶粒啦!
首先呢,得把粉煤灰收集起来,这就像是给小精灵们建个营地。
然后啊,要给它们加上一些其他的材料,就像给小精灵们配备各种魔法道具。
接下来就是关键的一步啦,要把这些材料混合在一起,让它们充分交流融合,就好像小精灵们在开派对一样热闹。
然后呢,把混合好的材料送进专门的设备里,这个设备就像是一个魔法炉,在里面进行烧制。
烧制的过程可不能马虎,火候得掌握好,不然小精灵们可就变不出完美的形态啦!
烧制完成后,哇哦,那些原本灰扑扑的材料就变成了一颗颗圆滚滚的陶粒,就像是小精灵们华丽变身啦!
这陶粒用处可大了去了,它可以用来做建筑材料,让房子更坚固;还可以用来做园艺材料,让植物们长得更欢实。
你说神奇不神奇?
咱再回过头来想想这个生产工艺,不就跟咱做饭似的嘛,得准备食材,得掌握火候,还得有耐心。
这粉煤灰陶粒生产也是一样啊,每一步都得精心对待,才能生产出高质量的陶粒。
而且啊,这粉煤灰本来可能就是被人忽视的东西,通过这个工艺,却能变成宝贝,这不是很了不起吗?这就好像一个其貌不扬的人,通过自己的努力和才华,变得闪闪发光一样。
所以说啊,咱可别小瞧了这粉煤灰陶粒生产工艺,它里面蕴含的智慧和力量可大着呢!这可是人类智慧的结晶,让那些原本普通的材料有了新的生命和价值。
怎么样,朋友们,是不是对粉煤灰陶粒生产工艺有了更深的了解呢?是不是觉得很有意思呢?以后看到那些陶粒,可别忘了它们是怎么来的哟!。
免烧粉煤灰轻质陶粒生产方法

免烧粉煤灰轻质陶粒节省能源、工艺简便、成本
低、投资少;以粉煤灰为主要原料,降低环境负
荷,与环境协调性好,符合可持续发展的方向。
但这种陶粒的主要问题是表观密度偏高,一般为 800850kg/m3。而烧结粉
粉煤灰陶粒表观密度为800kg/m3左右。降低非烧
结粉煤灰陶粒的表观密度成为研究的重点。下面,
我们向读者介绍一种免烧粉煤灰轻质陶粒生产方
再喷人粉煤灰胶结料,喷雾成球。这个工艺方法
经试验证明,工艺复杂、打泡、吹泡的工艺不容
易操作,芯材的均匀性也较差。②铝粉发气的办 法将铝粉掺人粉煤灰、水泥、石灰料
浆中,搅拌均匀,铝粉与石灰反应产生氢气,使
粉浆膨胀,形成多孔料浆。初凝后,将多孔料浆
打碎成球,再投入成球盘中喷雾,喷入胶凝材料
成球,得到多孔陶粒坯体,经蒸养或自然养护而 得免烧粉煤灰轻质陶粒。试验结果证
及水雾成球,得到免烧粉煤灰陶粒坯料,经养护 得免烧粉煤灰陶粒。此工艺过程
比较简单,生产陶粒工艺过程容易控制,质量有
保证,而且可以利用白色垃圾为原料,使免烧粉
煤灰陶粒主要原料为两种工业废渣:白色工业垃
圾及黑色工业垃圾,有利于环保和工业废渣资源 化。(2)免烧粉煤灰轻质陶粒生产
实例①原材料a粉煤灰干排灰,含碳量低于10%。
明,这个工艺过程也比较复杂,多孔料浆初凝后
破碎成粒不容易控制,大小不均匀,粒形也不规
则。故生产上更难以控制。③硬质泡沫塑料颗粒
为芯材的办法将包装箱等硬质泡沫塑料,在高速 粉碎机中破碎成粒(粒度可根据要求
改变高速粉碎机的筛板来实现),一般5mm以下。
将塑料粒吹入喷胶机中,使颗粒表面涂卜有机黏
结荆,然后投入成球盘,同时喷入粉煤灰胶结料
实验室工作总结-陶粒配方研制
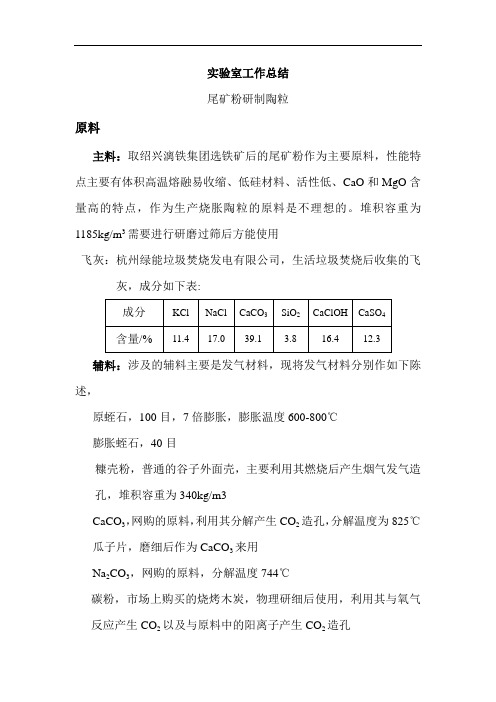
实验室工作总结尾矿粉研制陶粒原料主料:取绍兴漓铁集团选铁矿后的尾矿粉作为主要原料,性能特点主要有体积高温熔融易收缩、低硅材料、活性低、CaO和MgO含量高的特点,作为生产烧胀陶粒的原料是不理想的。
堆积容重为1185kg/m3需要进行研磨过筛后方能使用飞灰:杭州绿能垃圾焚烧发电有限公司,生活垃圾焚烧后收集的飞灰,成分如下表:辅料:涉及的辅料主要是发气材料,现将发气材料分别作如下陈述,原蛭石,100目,7倍膨胀,膨胀温度600-800℃膨胀蛭石,40目糠壳粉,普通的谷子外面壳,主要利用其燃烧后产生烟气发气造孔,堆积容重为340kg/m3CaCO3,网购的原料,利用其分解产生CO2造孔,分解温度为825℃瓜子片,磨细后作为CaCO3来用Na2CO3,网购的原料,分解温度744℃碳粉,市场上购买的烧烤木炭,物理研细后使用,利用其与氧气反应产生CO2以及与原料中的阳离子产生CO2造孔羟丙基甲基纤维素醚,保水作用配方及工艺第一阶段:初步试验是寻找尾矿粉的半熔融温度,制作陶粒的掺水量,并对发气材料的加量与造孔效果做初步性的研究,以便后续实验的加热至适当的温度,并选择合适的发气原料1.铁尾矿粉制成陶粒配方:铁尾矿粉100g,掺水至可以手工成球的水量是21g,手工搓成球,起初没有计量球体的重量工艺:分多次实验从常温分别加热到1200℃,1180℃,1160℃,1140℃,1120℃,1100℃,1080℃,忽略马蜂炉的温度不均匀等不利因素,得知如下结论结论: 球体体积收缩,铁尾矿粉在1080-1100℃左右处于固相、液相、气相三相交界点铁尾矿粉的掺水量在占铁尾矿质量的21%左右2.铁尾矿粉加糠壳粉制陶粒配方1:铁尾矿粉:糠壳粉体积比=1:1,掺水量至手工成球时总加水量占总料量的46%工艺:常温加热至1200℃,关闭电源不开炉子隔日开炉子现象:为粉碎,无强度配方2:铁尾矿粉:糠壳粉体积比=1:1.5,掺水量至手工成球时总加水量占总料量的50%工艺:500℃预热20min后加热至1200℃,关闭电源不开炉子隔日开炉子现象:全部熔融,体积收缩严重结论:加热温度过高3.铁尾矿粉加原蛭石制陶粒配方:分5组试验,分别占铁尾矿粉的质量的1%、2%、3%、4%、5%掺水量总料量的20%工艺:常温至1120℃,关闭电源不开炉子隔日开炉子结论: 五组试验区别不是很大,球体体积收缩,有孔隙,但是极不均匀,且极有可能孔洞是原料自身产生的4.对湿法直接焙烧的初步尝试配方1:铁尾矿粉掺水量21%配方2:铁尾矿粉额外加0.58%的羟基甲丙基纤维素醚,掺水量为总料量的28%配方3:原蛭石占铁尾矿粉的3%,额外加0.58%的羟基甲丙基纤维素醚,掺水量为总料量的28%工艺:250℃加热至1120℃,关闭电源不开炉子隔日开炉子结论:球体体积收缩,有孔隙,配方1与配方2烧制后无明显区别,羟基甲丙基纤维素醚的作用不明显5.铁尾矿粉加CaCO3制陶粒配方1:CaCO3占铁尾矿粉的5%,采用瓜子片磨细后作CaCO3使用配方2: CaCO3占铁尾矿粉的10%,采用瓜子片磨细后作CaCO3使用工艺: 400℃加热至1110℃,关闭电源不开炉子隔日开炉子结论:球体体积收缩,发气造孔效果不明显,CaCO3作用不明显6.铁尾矿粉加Na2CO3制陶粒配方1:Na2CO3占铁尾矿粉1%,配方2:Na2CO3占铁尾矿粉3%工艺:400℃加热至1070℃,关闭电源不开炉子隔日开炉子结论: 球体体积收缩,造孔效果不佳,更换造孔材料7.湿法直接焙烧工艺的改进尝试配方1:铁尾矿粉+CaCO3(占原料量的5%)+水配方2:铁尾矿粉+原蛭石(占原料量的8%)+水工艺:900℃加热至1110℃关闭电源不开炉子隔日开炉子结论:配方1球体体积收缩,有孔隙但不均匀,配方2直接爆裂8.尾矿粉加碳粉制作陶粒配方1:铁尾矿粉+碳粉(5%铁尾矿粉的量)配方2: 铁尾矿粉+碳粉(10%铁尾矿粉的量)工艺:400℃加热至1110℃,直接将陶粒取出结论:球体收缩,孔隙明显但不是均匀,配方2比配方1的孔隙多且大,质地坚硬9.尾矿粉与HZ、SZ混合后加碳粉制作陶粒配方1:铁尾矿粉:HZ料质量比=1:1,碳粉占总料量的10%配方2:铁尾矿粉:SZ料质量比=1:1,碳粉占总料量的10%工艺1:400℃加热至1110℃,直接将陶粒取出工艺2:900℃加热至1112℃,直接将陶粒取出结论:球体收缩,孔隙有但不明显,配方1与配方2无明显差异,质地较硬。
页岩制作陶粒生产工艺
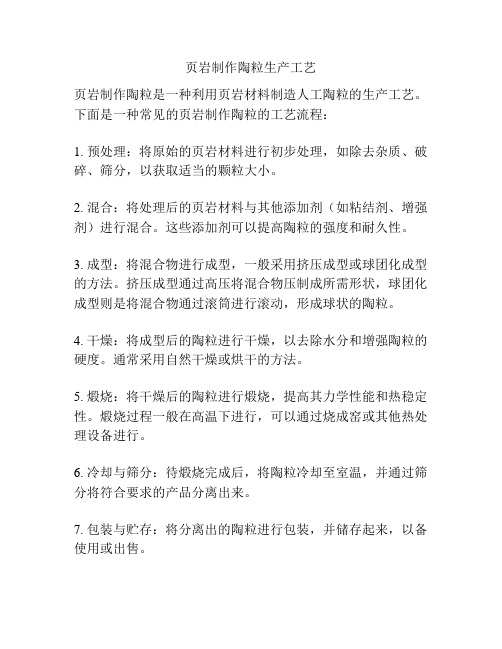
页岩制作陶粒生产工艺
页岩制作陶粒是一种利用页岩材料制造人工陶粒的生产工艺。
下面是一种常见的页岩制作陶粒的工艺流程:
1. 预处理:将原始的页岩材料进行初步处理,如除去杂质、破碎、筛分,以获取适当的颗粒大小。
2. 混合:将处理后的页岩材料与其他添加剂(如粘结剂、增强剂)进行混合。
这些添加剂可以提高陶粒的强度和耐久性。
3. 成型:将混合物进行成型,一般采用挤压成型或球团化成型的方法。
挤压成型通过高压将混合物压制成所需形状,球团化成型则是将混合物通过滚筒进行滚动,形成球状的陶粒。
4. 干燥:将成型后的陶粒进行干燥,以去除水分和增强陶粒的硬度。
通常采用自然干燥或烘干的方法。
5. 煅烧:将干燥后的陶粒进行煅烧,提高其力学性能和热稳定性。
煅烧过程一般在高温下进行,可以通过烧成窑或其他热处理设备进行。
6. 冷却与筛分:待煅烧完成后,将陶粒冷却至室温,并通过筛分将符合要求的产品分离出来。
7. 包装与贮存:将分离出的陶粒进行包装,并储存起来,以备使用或出售。
需要注意的是,不同的工艺会有一些细微的差异,具体的工艺流程也会根据生产厂家的不同而有所差异。
上述只是一种常见的工艺流程,供参考。
- 1、下载文档前请自行甄别文档内容的完整性,平台不提供额外的编辑、内容补充、找答案等附加服务。
- 2、"仅部分预览"的文档,不可在线预览部分如存在完整性等问题,可反馈申请退款(可完整预览的文档不适用该条件!)。
- 3、如文档侵犯您的权益,请联系客服反馈,我们会尽快为您处理(人工客服工作时间:9:00-18:30)。
陶粒生产技术
1、烧胀陶粒与烧结陶粒的不同:
烧结陶粒在焙烧过程中不发生较大的体积膨胀, 内部只有少量气孔, 而且有许多是联通或开放性的。
而烧胀陶粒会发生较大的体
积膨胀, 内部有大量的气孔, 这些气孔多是密闭的, 互补连通的, 开放性气孔较少。
2、烧胀陶粒的主要性能特点
由于是密闭微孔结构, 气孔率非常高, 一般要占陶粒总体积的
48%-70%, 因此它除具有陶粒的共同特征外, 又具有了这种孔结构
所赋予的都有特征。
①具有更加优异的保温性能, 热导率一般只有0.08-0.15w( m·k)
②更低的堆积密度, 堆积密度大多为300-500kg/m3
③优异的吸声隔声性能
3、膨胀气体产生的基本原理
膨胀的物质基础是气体, 这些气体是由一些原料成分在高温下发
生反应而产生的, 而非外加的
当前中国生产膨胀陶粒主要是利用如下四大类能够产生气体的成分: 碳酸盐类、硫化物类、氧化铁类、碳类。
最常见的碳酸盐
为碳酸钙和碳酸镁, 最常见的硫化物为硫化铁、硫等, 最常见的氧化铁为Fe2O3
4、主要化学反应
( 1) 碳酸钙的分解反应
①碳酸钙的发起反应
CaCO3→CaO+CO2↑( 850-900℃)
②碳酸镁的发起反应
MgCO3→MgO+CO2↑(400-500℃)
( 2) 氧化铁的分解与还原反应
2Fe2O3+C→4FeO+ CO2↑
2Fe2O3+3C→4Fe+ 3CO2↑
Fe2O3+C→2FeO+ CO↑
Fe2O3+C→2Fe+ 3CO↑
( 3) 硫化物的分解与氧化反应
Fe2O3===FeS+S↑
S+O2===SO2
4FeS2+11O2===2Fe2O3+8SO2↑
( 4) 碳的化合反应
C+O2→CO2↑
2C+O2→2CO↑(缺氧条件下)
5、在氧化气氛下, CO从600℃左右开始产生, 当温度超过1000℃时, CO溢出量增多, 由于CO是氧化铁与碳之间反应的产物, 它的出现不但消耗未燃尽的煤, 而且消耗氧化铁, 因此经600℃以上温度长时间预热, 膨胀会受到影响, 另外在膨胀温度范围内, 逸出的气体主要是CO, 说明CO是主要膨胀气体。
6、膨胀原理
陶粒的膨胀实际就是发泡, 发泡物质在高温下释放气体, 产生气体压力才能使陶粒坯体膨胀, 但没有气体她就无法得以保存, 因此还必须有能束缚住气体的溶体, 经过加热产生的熔体包围并防止气体外溢, 膨胀才能成功。
早期的动态平衡膨胀过程有利于坯体的膨胀使陶粒实现轻质化, , 少量多余的溢出减压, 为后期陶粒坯体的膨胀收缩创造了良好的条件。
后期的静态平衡膨胀过程可经过早期的气体释放减压和后期的降温增加来实现, 致使陶粒表层开孔气孔减少或损失, 同时内部气孔细化、封闭。
7、膨胀模式理论对生产陶粒的指导意义
①发气量是陶粒膨胀的最基本因素, 对它的正确把握至关重要。
膨胀模式理论可使我们在配方设计或工艺控制时, 能够更为准确地把握陶粒坯体的发气量, 是之既不会完全被液相始终抑制, 达到要求的膨胀力, 又能有一定的释放量, 形成减压收缩, 而且不造成大量气体的逸出, 使液相对其的抑制难以进行。
这对于原料中发气成分的控制尤为重要。
②正确把握液相量及液相粘度
如果液相量不足, 她就无法包裹坯体产生的大量气体, 如果液相量过大, 就会使她的抑制作用过强, 而使气体的膨胀力被过分地抑制。
液相的粘度也对气体的膨胀有极大的影响, 粘度越大, 对气体的控制力就越强。
③正确地把握不同膨胀端的技术特点
8、气孔率对陶粒性能的影响
大孔的直径大于1mm, 小孔直径小于1mm, 微孔直径小于0.5mm a: 陶粒密度
陶粒的气孔率越大, 她的堆积密度就越低, 轻质性能就越优异。
当她的表观密度为500kg/m3左右时, 其气孔率均在48%左右。
b:陶粒强度
陶粒的强度随着气孔率的提高而降低。
气孔率为10%时, 其强度
会比无气孔时降低40%左右, 气孔率在10%以下时, 强度下降不太明显, 当气孔率超过10%时, 强度下降就十分明显。
c:陶粒吸水率
陶粒的吸水率随气孔率的提高而提高。
气孔率越高, 吸水率就越高, 但这是一般情况。
在气孔细化、封闭、开口孔的连通孔均少或没有的情况下, 高气孔率的陶粒也具有很低的吸水率。
9、气孔的尺寸、形状、均匀性对陶粒性能的影响
气孔的尺寸越大, 在密度相等时, 逃离的强度就越差, 保持陶粒的总孔隙率不变, 气孔尺寸越小, 强度就越高。
减小气孔的尺寸, 能够提高陶粒的强度。
气孔的形状对强度和吸水率均具有重大的影响。
闭口型状的圆孔, 会使陶粒强度高, 而且吸水率低。
开口形状的气孔、连通形状的气孔都会使强度下降。
10、烧胀陶粒的孔间壁对陶粒性能的影响
①陶粒强度
孔间壁是陶粒内部结构的骨架, 是承受压应力的主体。
孔间壁的厚度越大, 孔间壁占陶粒体积的比例越大, 孔间壁上的孔隙越小, 陶粒的强度就越高。
孔间壁的物相成分对陶粒的强度影响也非常大。
孔间壁若以玻璃相为主, 陶粒的强度就差, 若以结晶体针状
莫来石晶体网络为主, 陶粒的强度就越好。
因为针状莫来石晶体呈网络状分布与玻璃相中, 形成坚固的骨架结构, 对玻璃相起到了支撑和加固作用, 可提高陶粒的强度并提高其断裂强度。
②陶粒吸水率
要烧制出优质的膨胀陶粒, 就要满足
( 1) 在保证不降低陶粒强度的情况下, 尽量提高陶粒的气孔率, 以降低陶粒的堆积密度, 使其轻质的特性更加突出。
( 2) 在保证不降低套利的孔隙率的情况下, 经过优化孔结构来实现高孔隙率下的理想强度和低吸水率。
这些油画孔结构的手段包括细化气孔, 使气孔以封闭圆球孔为主, 尽量减少或不形成连通孔和开口孔。
( 3) 优化陶粒孔结构的孔间壁, 使之减少或不生成能够使气孔相连或开口的孔隙。
并使组成孔间壁的物相以针状莫来石晶体为主。
不能以莫来石为主的, 也要尽量提高莫来石的数量, 以使孔间壁形成坚固的骨架网络。
11、气体的释放主要是CO2、 CO、 SO2.在粘性状态的粘土内部形成了类似球形的孔洞, 因而具有蜂窝状结构。
其原因主要有二: 一方面是材料的粘度和材料在熔融过程中所发生的表面张力; 另一方面时从这种材料的内部释放出一些气体, 而产生膨胀的必要条件时在材料内部具有足够量的矿物成分和有机物。
这些矿物成。