内外饰DFMEA-29 汽车仪表板手套箱总成
汽车内外饰结构设计讲解

门护板下本体,通常作为门护板骨架,连接和安装门护板总成的其他零件,并且设计有与 门内板钣金的主要安装定位结构。通常采用注塑工艺成型,需要有足够的刚度和强度,以 保持门护板总成的形状。安装点要分布均匀。
地毯的典型结构、工艺和材料
地毯主要有簇绒地毯、针刺地毯和PVC地毯等。 簇绒地毯一般由尼龙簇绒软面、EVA重涂层和无纺布3层构成,(如下图所示)。其 制作工艺一般是将尼龙和涤纶丝织成簇绒毯面,再将尼龙簇绒软面、EVA重涂层和无纺 布放入模具热压成型。高档簇绒地毯背面还有PU发泡层,其主要作用是为了提供舒适的 感觉和良好的隔声\吸音性能,这要求地毯在热压成型后增加模具内发泡的工艺。 尼龙针刺地毯没有EVA重涂层和无纺布,采用热压工艺成型。 PVC地毯没有EVA重涂层和无纺布,同样采用热压工艺成型。 目前簇绒地毯和针刺地毯在成型后多采用水切割工艺来加工边界和开口。
目前主流汽车厂,大量采用钣金焊接型仪表台横梁。根据其断面形状,又可分为盒形 横梁和管柱型横梁。管柱型横梁,由于有比较明显的价格及性能优势,因而被广泛应 用。 管柱形横梁又分为直管型和弯管型。 直管型横梁对结构和安全性能非常有利,成本较低,但受仪表台总成系统中个零件布 置有较大限制。 弯管型横梁对仪表台总成零件布置相对有利,但会削弱结构和安全性能,制造相对复 杂一些,尺寸稳定性较差。
比较简单的门护板,如左图,由门护板 本体加必要功能件:内扣手、扶手面板、 地图袋、玻璃升降开关等组成。这类门 护板一般在经济型轿车和货车中较常见, 甚至比左图中的更简单。 这类门护板本体,通常采用注塑成型。
内外饰验收标准
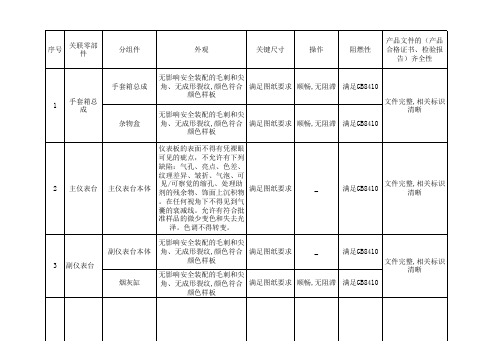
样板
无影响安全装配的毛刺和尖
清晰
序批准的色板或样品,其表面不应有毛刺、裂纹、污点、皱纹、凹凸及松弛等缺陷
泡沫对载体或表层的粘附力。
M:\试验大纲\
仪表板型式试验大纲.doc
枕强度要求和实验方法
(GB15083-2006)、汽车座椅头枕性能要求和实验方法(GB 抗拉强度、延伸率、剥离强度、耐磨性、缩水率、耐低温、抗褶皱、耐褪色牢度、压缩弹(GB 14167-2006)、汽车安全带动态性能要求和试验方法
(QC 244-1997)、乘用车正11551-2003)、汽车侧面碰撞
摩擦织物的评判、装饰材料抗洗涤性、饰件的耐摩擦色牢度
摩擦织物的评判、装饰材料抗洗涤性、饰件的耐摩擦色牢度
、表面抗刮伤性、相对光照的QCT 629-2005、弯曲刚度试验、折叠耐久性试验、摆动耐久性试验、抗高低温试验、抗温
度交变试验、镜盖翻转和开关
防夹力、安全性、滑动承载强度、面板保持强度、继电器烧
损、电机烧损、工作噪音、防水性(只试验天窗)、误操作M:\试验大纲\
天窗试验大纲.doc M:\试验大纲\
TEST\顶棚试验大纲.xls
屈服应力、球压硬度、缺口冲击韧性、老化温度、耐寒性、
温度存放试验、静态负载试验、回位时间及啪嗒声功能试验相应级别
M:\试验大纲\
TEST\试验大纲_遮阳板.doc。
汽车内外饰产品装配流程

2-A柱上饰板; 5-B柱上饰板; 8-C柱上饰板; 11-前侧饰板;
3-A柱上饰板堵盖; 6-B柱上饰板堵盖; 9-C柱上饰板堵盖; 12-前门槛踏板;
螺钉堵盖
螺钉堵盖 B柱下饰板本体
前侧饰板总成
图一 内饰装配零件组成
图二 内饰装配流程图 前门槛踏板总成
螺钉堵盖
后门槛踏板总成
内外饰装配流程图——行李箱系统
1
2
3
4
6
5
1-背门饰板; 2-行李箱后饰板; 3-行李箱垫毯;
4-行李箱泡沫工具箱垫块;
5-行李箱左侧饰板;
6-行李箱右侧饰板
图一 行李箱装配零件组成
行李箱左侧饰板
行李箱右侧饰板
行李箱后饰板 行李箱泡沫工具箱垫块
行李箱垫毯
背门饰板
背门饰板单独安装
图二 行李箱装配流程图
内外饰装配流程图——前保系统 1
门饰板总成
盘头十字槽螺钉
车门钣金
图一 门护板装配零件组成
图二 门护板装配流程图
内外饰装配流程图——内饰系统
4
3
96
5
2
8
13
11
1
7 12
前围隔热垫 仪表板总成 顶棚总成
地毯总成
10
A柱上饰板本体 B柱上饰板本体
C柱上饰板本体
1-前围隔热垫; 4-顶棚总成; 7-B柱下饰板; 10-地毯总成; 13-后门槛踏板
内外饰装配流程图——CONSLE系统 1
2
3
4
1-副仪表总成; 3-堵盖;
2-后端盖总成; 4-前端护板总成
图一 副仪表板装配零件组成
副仪表总成 后端盖总成 前端护板总成
内外饰DFMEA-31 汽车仪表板出风口总成
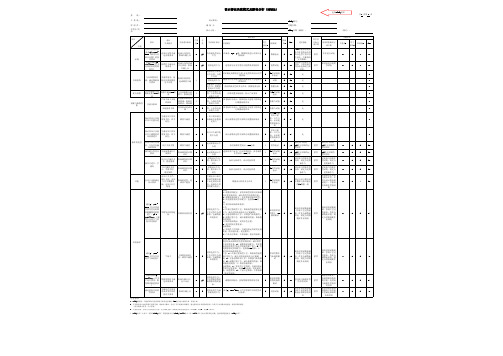
系 统 :子 系 统 :设计职责:零 部 件 :编 制 人:车型年/项目:
核心小组 :
3、严重度等级、分类与严重度对应关系、发生频度等级、探测度等级分别见附表一中图表1,图表2、图表3、图表4。
4“DFMEA清单”中每个“零部件DFMEA编号”需超链接至对应DFMEA的sheet表中,每个sheet表右上角中需附带返回键,返回键需超链接至“DFMEA清单”。
(修订):
1、DFMEA编制时,严格按照每个因素的填写说明进行编制,RPN值已输入函数关系,直接生成。
2、只有修改设计才能降低严重度等级,增加设计确认、验证工作只能减少探测度,通过修改设计来消除或控制一个或多个失效模式的起因、机理来降低频度。
一种失效模式仅有一个严重度。
关键日期:
DFEMA日期(编制):
设计潜在失效模式及影响分析(DFMEA)
共1 页第 1 页
DFMEA编号:。
DFMEA设计潜在失效模式及后果分析(Nanjing) 2013-09

G9
G8
G7
G6
G5
G4
G3
G2
G1
DFMEA策划 创建团队
输入
• 项目信息; • 项目时间进度; • 开发团队信息。
2013-9
输出
• DFMEA的零件清单; • 实施计划; • 核心团队的支持成员。
21
二. DFMEA策划及准备 STEP 2 – 创建团队 (G9-TG0)
牵头及负责人:DRE
设计潜在失效模式 设计潜在失效模式 及后果分析 DFMEA 及后果分析 DFMEA
2013-9
第一部分:FMEA发展和介绍 第二部分:DFMEA策划及准备 第三部分:DFMEA分析和实施 第四部分:注意事项和常见问题 第五部分:范例学习讨论
2013-9
2
一. FMEA发展和介绍 FMEA概念 Potential Failure Mode & Effect Analysis 潜在 “失效模式及后果分析”的首字母缩写 FMEA是一种普遍且重要的可靠性分策划及准备 DFMEA逻辑流程图:准备和实施
调研 以往的 失效模式 定义分析 范围: 方块图
准备 实施
潜在失效 后果 针对各 功能识 别潜在 失效模 式
严重度(S) 解决 问题 降低 风险
创建 DFMEA 团队
识别功能 需求
潜在失效 起因/机理
频度(O)
建议 措施
策划:确 定范围和 时间进度
G8 项目启动
G7 方案批准
G6 项目批准
G5 工程发布
G4
G3
G2
G1
战略立项
产品和 预试生产 试生产 正式投产 工艺验证
产品开发阶段:TG0 ~ TG2数据发布 工程发布 TG0发布 前期策划 DFMEA分析 确定 清单计划 DFMEA TG1版完成 DFMEA TG2版完成 DFMEA ESO版完成 TG1发布 失效分析和预防 TG2发布 根据验证结果更新 动态更新
DFMEA - 车身附件 - 车门内护板

快速件验 证
7
105
3
外观良 好,间 隙面差 均匀 边界与钣金不贴合 外观质量差, 用户抱怨
2
5
快速件验 证
7
70
3
3
快速件验 证
7
63
护板与内水切配合面 起波浪 护板与其他内饰色彩 有色差 护板表面包覆物包覆 效果不好
外观质量差, 用户抱怨 外观质量差, 用户抱怨 外观质量差, 用户抱怨
3 3 2
3 4 2 3 3 4 3
未进行人机工程 分析 未进行人机工程 分析 进行人机工程分 析 进行人机工程分 析 进行人机工程分 析 进行人机工程分 析 护板使用劣质材 料
2 3 2 4 4 3 4
人机工程 检查、快 速件验证 进行人机 工程分析 定义分模 线及模具 精度要求 进行人机 工程分析 数模结构 合理性检 查 进行人机 工程分析 严格定义 护板材料
2 护板与控制器盖板配 合间隙面差不好; 护板与内开启手柄配 合间隙面差不好; 护板与电器按钮配合 间隙面差不好;
6
按设计规 范要求检 查数模
快速件验 证
7
84
外观质量差, 用户抱怨 3
5
数模结构 合理性检 查 数模结构 合理性检 查 数模结构 合理性检 查 按设计规 范要求检 查数模 内饰整体 定义色彩 数模结构 合理性检 查
车型号/车辆类型: Model(s) 核心小组成员: FMEA Team Members
关键日期: Key Date
审核: Verification
序 号
项目 /功能
潜在失效模式
潜在失效后果
严 重 度
级 别
潜在失效原因
发 生 频 度
现行预防 控制
轿车手套箱总成技术条件
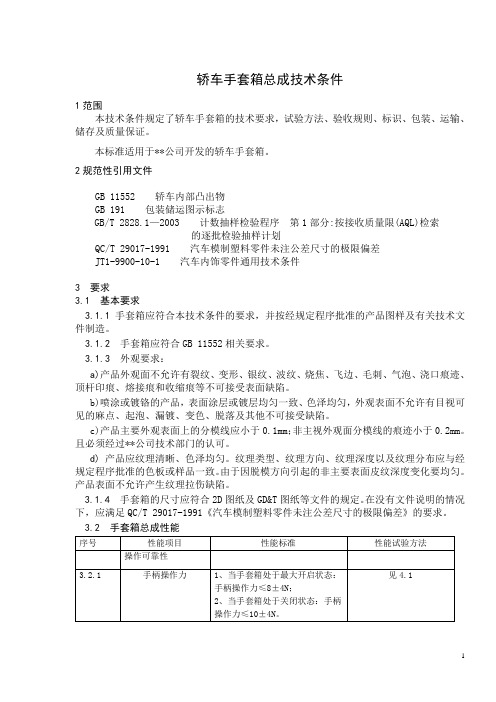
轿车手套箱总成技术条件1范围本技术条件规定了轿车手套箱的技术要求,试验方法、验收规则、标识、包装、运输、储存及质量保证。
本标准适用于**公司开发的轿车手套箱。
2规范性引用文件GB 11552 轿车内部凸出物GB 191 包装储运图示标志GB/T 2828.1—2003 计数抽样检验程序第1部分:按接收质量限(AQL)检索的逐批检验抽样计划QC/T 29017-1991 汽车模制塑料零件未注公差尺寸的极限偏差JT1-9900-10-1 汽车内饰零件通用技术条件3 要求3.1 基本要求3.1.1 手套箱应符合本技术条件的要求,并按经规定程序批准的产品图样及有关技术文件制造。
3.1.2 手套箱应符合GB 11552相关要求。
3.1.3 外观要求:a)产品外观面不允许有裂纹、变形、银纹、波纹、烧焦、飞边、毛刺、气泡、浇口痕迹、顶杆印痕、熔接痕和收缩痕等不可接受表面缺陷。
b)喷涂或镀铬的产品,表面涂层或镀层均匀一致、色泽均匀,外观表面不允许有目视可见的麻点、起泡、漏镀、变色、脱落及其他不可接受缺陷。
c)产品主要外观表面上的分模线应小于0.1mm;非主视外观面分模线的痕迹小于0.2mm。
且必须经过**公司技术部门的认可。
d)产品应纹理清晰、色泽均匀。
纹理类型、纹理方向、纹理深度以及纹理分布应与经规定程序批准的色板或样品一致。
由于因脱模方向引起的非主要表面皮纹深度变化要均匀。
产品表面不允许产生纹理拉伤缺陷。
3.1.4 手套箱的尺寸应符合2D图纸及GD&T图纸等文件的规定。
在没有文件说明的情况下,应满足QC/T 29017-1991《汽车模制塑料零件未注公差尺寸的极限偏差》的要求。
3.2 手套箱总成性能件》相关要求。
的试验方法进行。
3.2.21 气味满足《汽车内饰零件通用技术条件》相关要求。
按JT1-9900-10-1规定的试验方法进行。
4.试验方法4.1手柄操作力试验方法:a、开启手套箱处于最大开启状态,并固定。
内外饰基础知识培训-20200611

版权所有:janycamy
仪表板因其得天独厚的空间位置,使愈来愈多的操作功能分布于其中,除反映车辆行驶基本状态外,对风口、音响、空 调、灯光等控制也给予行车更多的安全和驾驶乐趣。.
仪表帽檐装饰罩
左前除霜格栅
仪表板上本体
左侧除霜格栅 左侧出风口 左端侧盖板 检修口杂物盒 发动机罩开启扣手
左下护板 转向管柱护罩 一键启动开关盖板
副仪表板左前延伸板 副仪表板左装饰板 副仪表板左装饰条 移动式烟灰缸
副仪表板上盖板 扶手箱
副仪表板后盖板
副仪表板下本体
版权所有:janycamy
仪表台横梁总成是为仪表台本体总成及其附件(收音机、DVD、空调控制模块、安全气囊、转向管柱、制动踏板、离合踏 板、空调箱、线束等)提供支撑结构,同时也是模块化仪表台总成装配过程中的辅助夹具和定位支撑件。直接与车身相接,承 受所支撑件和连接件传递的载荷,对成员安全性有较大的影响。
行李箱左轮罩
前地毯
前地毯左减震垫 中通道减震垫
前挡板隔热垫
前舱隔热垫
发盖隔热垫
行李箱右轮罩
行李箱地毯减震 垫
行李箱地毯
前地毯左减震垫
版权所有:janycamy
右前座椅总成
左前座椅总成
后排座椅总成
现代轿车已经不是一个单纯的 运载工具,它已经是“人、汽车 与 环境”的组合体。座椅作为 汽车使用者的直接支承装置,在 车厢部件中具有非同小可的重要 性。汽车座椅的主要功能是为驾 驶者提供便于操纵、舒适、安全 和不易疲劳的驾驶座位。
版权所有:janycamy
主仪表板总成
副仪表板总成
仪表板简称IP(Instrument panel).仪表板总成包括仪表板 和副仪表板两部分,是轿车车厢 内最引人注目的部件 ,仪表板总 成既有技术的功能又有艺术的 功能, 它集安全性、功能性、 舒适性与装饰性于一身。反映 出各国轿车制作工艺和风格上 的差异,是整车的特色典型代 表之一 。
- 1、下载文档前请自行甄别文档内容的完整性,平台不提供额外的编辑、内容补充、找答案等附加服务。
- 2、"仅部分预览"的文档,不可在线预览部分如存在完整性等问题,可反馈申请退款(可完整预览的文档不适用该条件!)。
- 3、如文档侵犯您的权益,请联系客服反馈,我们会尽快为您处理(人工客服工作时间:9:00-18:30)。
手指伸入扣手困难
顾客不满意
5
B
结构设计不合理
组织经验丰富的技术人员对结构进行评价,参考成 熟车型的结构设计
3
RP样件 试装验
证
3
45
无
与仪表板配合
与仪表板配合
安装点布置不合
RP件试
配合间隙 间隙满足整车 间隙不满足DTS要求 间隙大,影响 4
理,卡扣等安装结
合理布置安装结构,防止产品变形
3 制装车 3 36
无
DTS要求
美观
构不合理
验证
外板和内板是通过
配合
满足零部件本 身设计要求
手套箱外板与内板 脱开(脱焊)
影响使用,造 成客户抱怨,
投诉
5
摩擦焊工艺焊接
B
的,内板焊接筋高 组织经验丰富的技术人员对结构进行评价,参考成
度较低,焊接量较
熟车型的结构设计
பைடு நூலகம்
3
样件验 证
3
少,连接强度较
45
无
低,容易脱开;
操作力和耐久 操作力过大或过小 影响功能件的
RP样件
3 试装验 3 45
无
证
储物功能
提供足够的储 物空间
杂物盒过小
取物不便,影 响人机功能, 5 导致顾客不满
B 杂物盒布置区域空 间小。
对油泥模型进行扫描,进行验证评审
RP样件
3 试装验 3 45
无
证
杂物盒开启角度设 计小
多方评审,DMU分析
RP样件
3 试装验 3 45
无
证
方便性
操作空间合 理,操作方便
无
证
RP样件
3 试装验 3 45
无
证
阻尼过大,杂物箱 开启缓慢
顾客不满意
5
B 结构设计不合理
标杆分析研究,设计经验积累
RP样件
3 试装验 3 45
无
证
阻尼过小,杂物箱 开启过快
顾客不满意
5
B 结构设计不合理
标杆分析研究,设计经验积累
RP样件
3 试装验 3 45
无
证
材料:
1)调整材料配方,采用环保型材料及环保助剂代
RP样件
人机工程校
核,CAE分析
3 试装验 3
81 核,CAE分析 附件 校核,RP件试 8
2
3
48
证
校核
验验证,满足
能布置硬物,
设计要求
如分缝线、开
关等
与内饰整体协 表面质量差;装配 影响外观效
外观装饰 调,满足图纸 后外观间隙段差不 果,造成顾客 4
相关要求
合理
不满
间隙段差方案定义 不合理,分块不合
3
阻燃试 验
3
他车型材
81
料,与供应 商共同协商
原材料进行阻
附件
燃性试验
9
2
1
18
选择适当的
材料。
膝部与IP间隙
要求在100mm
以上(混三假
人的尺寸要
人机工程校
安全性
求),撞击中 心 50mm半径 范围内要求不
碰撞试验中膝部受 损严重
造成人身伤 害,影响车辆
上市
9
A
杂物箱外板设计不 合理,有硬物
对油泥模型进行扫描,进行验证评审
要求
扣手等安装可靠性 不足,间隙和面差
不能保证
碰撞时安装结 构失效;间隙 和面差不均匀
影响外观
5
安装点不足,间隙 B 和面差控制结构不
合理
增加限位和面差控制结构
RP样件
3 试装验 3 45
无
证
0
给装配和维修
装配与维修性 能
安装及拆卸
产品不易于安装和 带来困难;拆
拆卸
卸时易损坏,
增加维护成本
5
B
结构设计不合理; 与周边件的搭接不
合理
参考标杆车设计;组织经验丰富的工程师进行数据 结构评审
3
用RP件 试装验
证
3
45
无
0
安装强度不够
容易松动造成 异响
5
B
安装点布置不合 理,卡扣等安装结
构不合理
参考标杆车设计;组织经验丰富的工程师进行数据 结构评审
3
拔脱力 试验
2
30
无
0
杂物盒前期尺寸定 义偏小。
对油泥模型进行扫描,进行验证评审
理
评审确定间隙段差方案,在造型阶段设计时严格控 制
RP件试 3 制装车
验证
3
36
无
材料选用不当
根据零件的安装位置和表面处理工艺选择合适的材 料
3
试装
3
36
无
表面皮纹/色差设 计不当,拔模角度
设计不合理
皮纹样板及色彩多方评审,拔模角度分析
3
拔模分 析
3
36
无
0 0 0
外观装饰
提供安装平 台,间隙段差 满足图纸相关
替常规材料,减少挥发性有机物含量;
2)调整胶粘剂配方,变更胶粘剂溶剂类型;
3)优化搪塑表皮材料配方,选择低VOC材料;
满足Q/ 7124-
2018《车内零
部件挥发性有
机物和醛酮物 质的限值》, GB/T 27630-
甲醛等有机物超标
对乘客身体有 害
9
2011 《乘用
车内部空气质
量评价指南》
4)采用环保油漆和胶带。
操作力及耐久
试验不满足零 部件技术要
造成手感欠佳;不 满足耐久试验要求
使用,造成顾 客的不满或抱
5
求;
在使用过程中损坏
怨
B
结构设计不合理或 借鉴成熟车型的成熟结构,组织经验丰富的工程师
材料选用不当
评审
3
RP件试 制装车
验证
3
45
无
扣手开启关闭力 大,开启困难
影响顾客的后 期评价
5
B 结构设计不合理
标杆分析研究,设计经验积累
设计潜在 失效模式
系 统:
子系统:
零部件:
车型年/项目:
设计职责: 编 制 人: 核心小组 :
DFMEA 编 号 关: 键 日 期 DF: EMA日期(编 制):
返回DFMEA清单
共1 页第 1页
(修订):
项目
要求
潜在 失效模式
失效潜在影响
严重 度S
类分
失效潜在原因 控制预防
现行设计
探测 度D
RPN
建议措施
职责和 目标完
实施结果
发生 控制探 频度O 测
采取的措施和 严重 发生 完成日期 度S 频度O
探测度D
RPN
在NC数据冻
内部凸出物要
结前的各个
求满足GB 11552-2009《 乘用车内部凸 出物》的技术
内部凸出物不满足 法规要求
造成人身伤 害,影响车辆
上市
9
AR
外表面造型设计不 在油泥、CAS、A面、数据阶段进行内部凸出物校核
当
。
3
数据验 证
3
阶段将该内
81
容列入造型 工程可行性
分析,不断
附件 实车进行试验 9
2
1
18
法规
要求
修改完善数 据。
对比海马其
阻燃性满足GB 8410-2006《 汽车内饰材料 的燃烧特性》
阻燃性不满足法规 要求
造成人身伤害 或火灾事故, 影响车辆上市
9
AR
材料选用不当
选用海马历史车型符合阻燃要求的材料
工艺:
AR
材料选用不当、工 艺过程不合理添加 、仓储物流环境恶
劣
1)改善注塑成型工艺,降低成型温度和注射压 力,减少材料高温高压分子链破裂; 2)完善前期烘料工序;以增强气味的散发; 3)调整注塑工艺,减少脱模剂用量,降低脱模剂 残留;
4)取消表面喷涂,采用本色注塑;
RP样件
3 试装验 3 45
无
证
舒适性
关闭力过小,杂物
箱锁止结构失效, 影响顾客的后 车辆颠簸时自动打 期评价
5
操作力适中,
开
舒适性好,阻 尼适中
扣手开启角度太 大,舒适性差
影响顾客的后 期评价
5
B 结构设计不合理 B 结构设计不合理
标杆分析研究,设计经验积累 标杆分析研究,设计经验积累
RP样件
3 试装验 3 45