硫化原理
橡胶的硫化过程
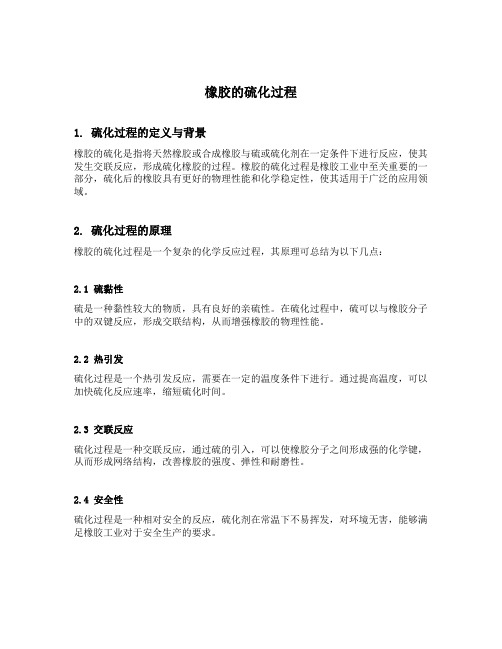
橡胶的硫化过程1. 硫化过程的定义与背景橡胶的硫化是指将天然橡胶或合成橡胶与硫或硫化剂在一定条件下进行反应,使其发生交联反应,形成硫化橡胶的过程。
橡胶的硫化过程是橡胶工业中至关重要的一部分,硫化后的橡胶具有更好的物理性能和化学稳定性,使其适用于广泛的应用领域。
2. 硫化过程的原理橡胶的硫化过程是一个复杂的化学反应过程,其原理可总结为以下几点:2.1 硫黏性硫是一种黏性较大的物质,具有良好的亲硫性。
在硫化过程中,硫可以与橡胶分子中的双键反应,形成交联结构,从而增强橡胶的物理性能。
2.2 热引发硫化过程是一个热引发反应,需要在一定的温度条件下进行。
通过提高温度,可以加快硫化反应速率,缩短硫化时间。
2.3 交联反应硫化过程是一种交联反应,通过硫的引入,可以使橡胶分子之间形成强的化学键,从而形成网络结构,改善橡胶的强度、弹性和耐磨性。
2.4 安全性硫化过程是一种相对安全的反应,硫化剂在常温下不易挥发,对环境无害,能够满足橡胶工业对于安全生产的要求。
3. 硫化过程的条件与方法橡胶的硫化过程需要一定的条件和方法,以确保硫化反应能够顺利进行。
3.1 温度温度是控制硫化反应速率和硫化时间的重要因素。
通常,硫化反应需要在高温条件下进行,一般为100-200摄氏度。
通过调节温度,可以控制硫化反应的速率和前进程度。
3.2 硫化剂硫化剂是触发硫化反应的重要因素,一般采用有机硫化剂或无机硫化剂。
常用的有机硫化剂有硫醇、硫胺等;无机硫化剂主要是硫。
不同的硫化剂对橡胶的硫化反应速率和效果有所差异,需要根据具体应用需求选择合适的硫化剂。
3.3 添加剂为了改善橡胶硫化过程的性能和效果,通常会添加一些辅助剂,如加速剂、活性剂、抗老化剂等。
这些添加剂可以提高硫化反应速率、改善硫化网络结构、延缓橡胶老化等,从而提高橡胶的物理性能和耐久性。
3.4 硫化方法橡胶的硫化方法主要有热硫化和冷硫化两种。
热硫化是在高温条件下进行的,常用于天然橡胶和低饱和度合成橡胶;冷硫化是在常温条件下进行的,常用于高饱和度合成橡胶。
硫化工艺技术

硫化工艺技术硫化工艺技术是一种常用的制造工艺,用于改善材料的性能和增加其使用寿命。
硫化是指在一定条件下,通过硫黄与材料反应,形成硫化物,并在材料中形成交联结构的过程。
硫化工艺技术广泛应用于橡胶、塑料和纤维等材料的生产中,下面我们来介绍一下硫化工艺技术的基本原理。
首先,硫化工艺技术的目的是通过交联结构的形成,增加材料的强度、耐磨性和耐老化性能。
硫化是通过硫黄与材料中的双键反应形成硫化物,从而将材料的分子间锁定在一起,形成交联结构。
硫黄在硫化过程中充当交联剂的角色,它能够与材料中的双键发生反应,将分子间的链断裂,并形成新的交联结构。
其次,硫化工艺技术的关键是控制硫化反应的温度和时间。
硫化反应需要一定的温度和时间才能完成。
温度过高或时间过长会导致硫化反应过度,使材料变硬、脆化甚至破裂。
温度过低或时间过短则无法完成硫化反应,材料性能改善效果不明显。
因此,在硫化工艺技术中,需要根据不同材料的特性和要求,合理选择硫化温度和时间,以达到最佳硫化效果。
此外,硫化工艺技术还需要使用一定的硫化助剂和适当的硫化条件。
硫化助剂有助于加快硫化反应速度,提高硫化效果。
常用的硫化助剂有活性剂、抗老化剂和加成剂等。
硫化条件主要包括硫化温度、硫化时间和硫化环境等,不同材料对硫化条件的要求也有所不同。
最后,硫化工艺技术在实际应用中还需要注意一些问题。
首先是硫化过程中产生的气体和有害物质的处理问题。
硫化反应会产生一些有害气体和污染物,需要通过适当的处理措施将其排出和处理,以保护环境和人体健康。
其次是硫化后材料的贮存和使用问题。
硫化后的材料需要避免日光直射和潮湿环境,以防止硫化物的分解和材料的老化。
总之,硫化工艺技术是一种重要的制造工艺,通过硫化反应能够改善材料的性能和增加其使用寿命。
在应用硫化工艺技术时,需要合理选择硫化条件、使用适当的硫化助剂,并注意硫化过程中产生的气体和有害物质的处理问题。
通过科学的硫化工艺技术,可以使材料的性能得到有效提升,推动工业的发展。
补胎抹胶硫化的作用与原理
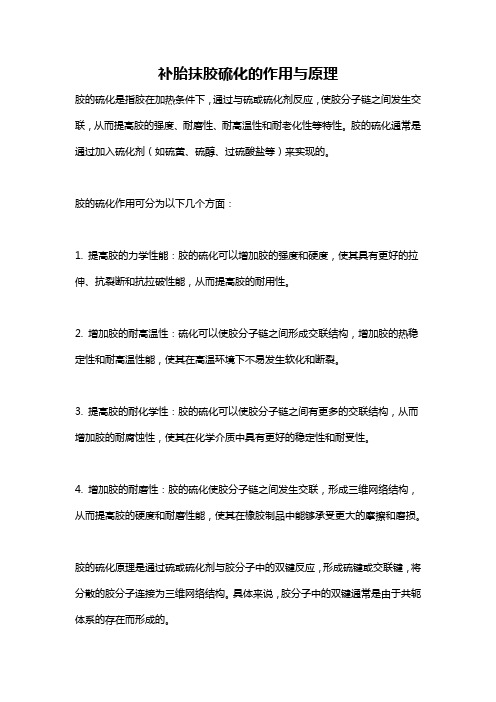
补胎抹胶硫化的作用与原理胶的硫化是指胶在加热条件下,通过与硫或硫化剂反应,使胶分子链之间发生交联,从而提高胶的强度、耐磨性、耐高温性和耐老化性等特性。
胶的硫化通常是通过加入硫化剂(如硫黄、硫醇、过硫酸盐等)来实现的。
胶的硫化作用可分为以下几个方面:1. 提高胶的力学性能:胶的硫化可以增加胶的强度和硬度,使其具有更好的拉伸、抗裂断和抗拉破性能,从而提高胶的耐用性。
2. 增加胶的耐高温性:硫化可以使胶分子链之间形成交联结构,增加胶的热稳定性和耐高温性能,使其在高温环境下不易发生软化和断裂。
3. 提高胶的耐化学性:胶的硫化可以使胶分子链之间有更多的交联结构,从而增加胶的耐腐蚀性,使其在化学介质中具有更好的稳定性和耐受性。
4. 增加胶的耐磨性:胶的硫化使胶分子链之间发生交联,形成三维网络结构,从而提高胶的硬度和耐磨性能,使其在橡胶制品中能够承受更大的摩擦和磨损。
胶的硫化原理是通过硫或硫化剂与胶分子中的双键反应,形成硫键或交联键,将分散的胶分子连接为三维网络结构。
具体来说,胶分子中的双键通常是由于共轭体系的存在而形成的。
普通胶可通过冷硫化、热硫化和辐射硫化等方式进行硫化,其中热硫化是最常用的方法。
热硫化是将胶料与硫或硫化剂混合,制成硫化胶,然后经过一定的时间和温度条件下加热,使硫化剂与胶料中的双键反应,从而实现胶的硫化。
在热硫化过程中,硫或硫化剂与胶料中的双键发生反应,形成硫键或交联键。
硫化过程一般分为三个阶段:1. 活化期:在低温下,硫或硫化剂与胶料中的双键反应生成活化的中间产物。
2. 交联期:中间产物通过自由基或离子机理进行互相反应,形成交联键,将胶分子连接在一起。
3. 稳定期:交联键的形成达到饱和,胶的硫化完成,形成交联胶。
热硫化的温度和时间是影响硫化效果的两个重要因素。
一般来说,提高硫化温度可以加快反应速度,缩短硫化时间;而延长硫化时间可以增加交联的程度和强度。
不同的胶料和硫化剂对温度和时间的要求不同,需要根据具体情况进行调整。
硫化反应的名词解释
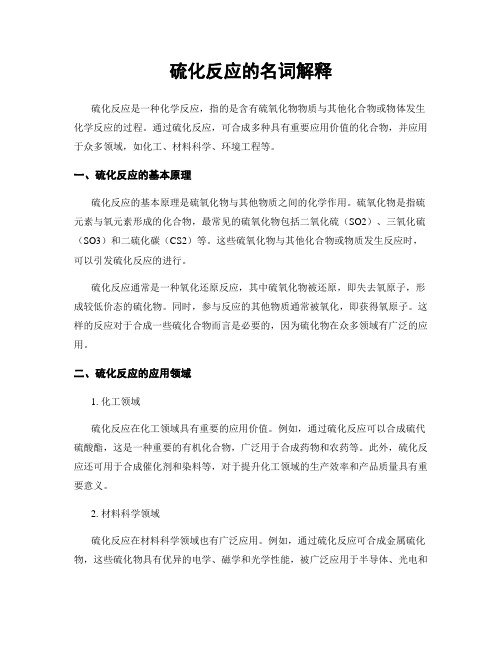
硫化反应的名词解释硫化反应是一种化学反应,指的是含有硫氧化物物质与其他化合物或物体发生化学反应的过程。
通过硫化反应,可合成多种具有重要应用价值的化合物,并应用于众多领域,如化工、材料科学、环境工程等。
一、硫化反应的基本原理硫化反应的基本原理是硫氧化物与其他物质之间的化学作用。
硫氧化物是指硫元素与氧元素形成的化合物,最常见的硫氧化物包括二氧化硫(SO2)、三氧化硫(SO3)和二硫化碳(CS2)等。
这些硫氧化物与其他化合物或物质发生反应时,可以引发硫化反应的进行。
硫化反应通常是一种氧化还原反应,其中硫氧化物被还原,即失去氧原子,形成较低价态的硫化物。
同时,参与反应的其他物质通常被氧化,即获得氧原子。
这样的反应对于合成一些硫化合物而言是必要的,因为硫化物在众多领域有广泛的应用。
二、硫化反应的应用领域1. 化工领域硫化反应在化工领域具有重要的应用价值。
例如,通过硫化反应可以合成硫代硫酸酯,这是一种重要的有机化合物,广泛用于合成药物和农药等。
此外,硫化反应还可用于合成催化剂和染料等,对于提升化工领域的生产效率和产品质量具有重要意义。
2. 材料科学领域硫化反应在材料科学领域也有广泛应用。
例如,通过硫化反应可合成金属硫化物,这些硫化物具有优异的电学、磁学和光学性能,被广泛应用于半导体、光电和磁性材料等领域。
另外,硫化反应还可用于合成一些高性能涂料和粘合剂等,为材料科学领域的研究和应用带来了诸多便利。
3. 环境工程领域在环境工程领域,硫化反应也扮演着重要的角色。
二氧化硫是燃烧过程中的产物之一,其排放会对环境和人体健康造成严重影响。
通过硫化反应,可以将二氧化硫转化为二硫化碳和硫酸,以减少其对环境的危害。
此外,硫化反应还可用于废气和污水处理中,将有害的硫化氢转化为较为稳定的硫酸盐和硫化物,从而减少环境污染。
综上所述,硫化反应是一种重要的化学反应,通过此反应可以合成多种具有重要应用价值的化合物。
硫化反应在化工、材料科学和环境工程等领域发挥着重要的作用,为这些领域的研究和应用带来了许多便利。
硅胶硫化原理

硅胶硫化原理
硅胶在硫化过程中,其分子链中的硅羟基被氧化成硅氧键,从而产生了极强的内聚力,使硅胶具有很高的机械强度。
硅胶硫化一般采用过氧化物硫化和催化剂硫化两种方法。
过氧化物硫化是利用硫化剂和被硫化材料(填料、填充剂等)发生化学反应生成不饱和化合物,从而达到硫化目的。
硅胶在空气中自然失水干燥,失去水分子后其内部的分子链被破坏而形成的一种胶状物质。
当硅胶处于室温下时,由于其分子链间作用力很大,不易流动,在外力作用下,可迅速恢复原来的形状。
如果将硅胶放在空气中干燥一段时间后,分子链被破坏,失去了与周围介质的接触性,分子链间作用力减弱或消失,使硅胶在空气中失水后形成不稳定的凝胶状态。
当硅胶处于高温环境时(如在烘箱中),由于环境温度高于其老化温度(如70℃)使硅胶中的分子链间作用力增大,从而使不稳定的凝胶。
—— 1 —1 —。
硫化工艺
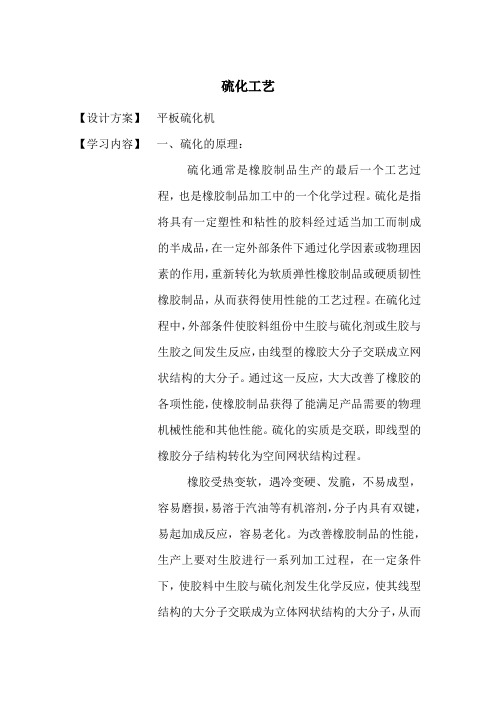
硫化工艺【设计方案】平板硫化机【学习内容】一、硫化的原理:硫化通常是橡胶制品生产的最后一个工艺过程,也是橡胶制品加工中的一个化学过程。
硫化是指将具有一定塑性和粘性的胶料经过适当加工而制成的半成品,在一定外部条件下通过化学因素或物理因素的作用,重新转化为软质弹性橡胶制品或硬质韧性橡胶制品,从而获得使用性能的工艺过程。
在硫化过程中,外部条件使胶料组份中生胶与硫化剂或生胶与生胶之间发生反应,由线型的橡胶大分子交联成立网状结构的大分子。
通过这一反应,大大改善了橡胶的各项性能,使橡胶制品获得了能满足产品需要的物理机械性能和其他性能。
硫化的实质是交联,即线型的橡胶分子结构转化为空间网状结构过程。
橡胶受热变软,遇冷变硬、发脆,不易成型,容易磨损,易溶于汽油等有机溶剂,分子内具有双键,易起加成反应,容易老化。
为改善橡胶制品的性能,生产上要对生胶进行一系列加工过程,在一定条件下,使胶料中生胶与硫化剂发生化学反应,使其线型结构的大分子交联成为立体网状结构的大分子,从而使胶料具备高强度、高弹性、抗腐蚀等优良性能。
二、硫化的方法1、温室硫化法温室硫化法用于需求在室温及不加压的条件下进行硫化的场合。
室温硫化通常将硫化剂与溶剂、惰性配合剂等配成一个组份,橡胶、树脂等与其他配合剂配成另一组分,使用是进行混合。
2、冷硫化法把制成品浸入2%-5%的一氯化硫的溶液中,时间从几秒到几分钟不等。
3、热硫化法⑴、间歇式硫化①、热水槽硫化法此法为直接常压硫化法,把需要硫化的产品浸于热水或盐水,适于乳胶薄膜制品的硫化。
②、烘房、烘箱热空气硫化法此法也为直接常压硫化法,该方法有两种方式,一是把半成品放在加热室中加热硫化;另一种是烘箱硫化,适用于某些特种橡胶制品的二次硫化。
③、硫化罐硫化硫化罐硫化工艺借助飞的硫化设备为硫化罐。
根据硫化介质的不同,硫化罐硫化工艺又有如下几种主要硫化方法:A、直接饱和蒸汽硫化法a、开放式硫化法b、包层硫化法c、埋粉硫化法d、模型硫化法B、热空气硫化法C、热空气-蒸汽混合硫化法⑵、外加压式硫化工艺①、平板硫化机模压硫化法采用这种方法可同时进行胶料在模具型腔内加压流动成型和胶料在硫化温度及硫化压力下发生硫化反应这两个过程。
橡胶硫化原理

橡胶硫化原理
橡胶硫化是一种将天然橡胶或合成橡胶转化为具有较好弹性和耐磨性的过程。
它的原理是通过将硫元素添加到橡胶分子链中,从而形成交叉链结构。
硫化剂通常是硫或含有硫的化合物,如硫醇、硫含量较高的化合物和多硫化物。
在硫化过程中,硫与橡胶中的双键发生反应,使橡胶链之间形成交联。
这种交联结构能够增强橡胶的强度、耐磨性和耐老化性。
硫化反应需要在适当的温度和压力下进行。
通常,使用硫化机或硫化炉将橡胶制品置于高温和压力下进行硫化。
在硫化过程中,硫与橡胶中的双键发生加成反应,形成硫醇中间体,然后再与其他硫醇或橡胶分子链发生反应,形成交链结构。
交联结构的形成使橡胶变得坚固耐用。
交联结构可以限制橡胶分子链的自由运动,从而提高橡胶的强度和弹性。
另外,交联还能够使橡胶对温度、化学品和老化等外界环境的变化具有更好的耐性。
橡胶硫化是橡胶工业中一项重要的工艺,它使橡胶制品具有更广泛的应用。
硫化过程中的交联结构为橡胶制品提供了优良的性能,使其能够在汽车、轮胎、皮革制品、密封件和电气绝缘材料等领域发挥重要作用。
硫化基本原理及硫化过程中常见的问题资料

Page 9
1.3 硫化三要素
硫化三要素
硫化温度 硫化压力
硫化时间
硫化三要素对产品硫化质量有决定性的影响
Page 10
1.3 硫化三要素—硫化的温度
直接影响到硫化速度和产品质量。硫化温度高,硫 化速度快,生产效率高,易生成较多的低硫交联键; 反之,硫化速度慢,生产效率低,易生成较多的多 硫交联键。
硫 化的定 义 硫 化的四个阶段 硫 化的三要素
第二部分:常见问题及解决办法
橡胶与金属粘接不牢 气泡 炸边 缺胶、硫 痕 缩孔
Page 2
第一部分 硫化的基本原理
1.1 硫化的定义
通俗的说法 硫化就是从生胶变成熟胶的过程;
教科书上的定义 硫化是指橡胶线型结构的大分子链通过化
学交联而构成三维网状结构的大分子的化学变 化过程,并使胶料的物理机械性能及其他性能 随之发生根本变化的过程。也就是从塑性胶变 成弹性胶的过程。
通常在硫化时,随着硫化压力的增大,硫化胶的很多物理 机械性能,如强度、动态模数、耐疲劳性、耐磨性及与骨 架材料的粘着性等相应提高。但过高的压力反而使橡胶的 某些性能降低,是因为高压同高温一样会加速橡胶分子的 热解作用。
一般来说,对硫化压力的选取根据胶料的配方、可塑性和产品 结构等来决定,在工艺上遵循的原则是:塑性大,压力宜小; 产品厚、层数多、结构复杂,压力宜大;薄制品压力宜低,甚 至可用常压。
硫化效应可以简单的理解为在给定的硫化温度、 压力和时间的条件下橡胶硫化所达到的效果;
一般来说,要达到相同的硫化效应,提升硫化温 度,则必须减少硫化时间,这也就是我们现在实 行的高温快速硫化;
- 1、下载文档前请自行甄别文档内容的完整性,平台不提供额外的编辑、内容补充、找答案等附加服务。
- 2、"仅部分预览"的文档,不可在线预览部分如存在完整性等问题,可反馈申请退款(可完整预览的文档不适用该条件!)。
- 3、如文档侵犯您的权益,请联系客服反馈,我们会尽快为您处理(人工客服工作时间:9:00-18:30)。
1140液压硫化机液压原理的设计随着我国交通运输事业的迅速发展,高速公路不断铺设,这就对对汽车轮胎的均匀性提出了越来越高的要求,因此对硫化机的工作精度要求也随之提高。
目前我国轮胎行业广泛应用的是50年代发展起来的机械式硫化机,由于本身结构的原因,机械式硫化机存在如下问题:1. 上下热板的平行度、同轴度、机械手卡爪圆度和对下热板内孔的同轴度等精度等级低,特别是重复精度低;2. 连杆、曲柄齿轮等主要受力件上的运动副,是由铜套组成的滑动轴承,易磨损,对精度影响较大。
3. 上下模受到的合模力不均匀,对双模轮胎定型硫化机而言,两侧的受力,大于两内侧的受力;4. 合模力是在曲柄销到达下死点瞬间由各受力构件弹性变形量所决定的,而温度变化使受力构件尺寸发生变化,合模力也随之发生变化,因此,生产过程中温度的波动将造成合模力的波动。
由于机械式轮胎硫化机存在的不可克服的弱点,已不能满足由于高速公路的发展,对汽车轮胎质量要求的日益提高。
因而世界上主要轮胎公司已逐步采用液压式硫化机代替传统的机械式硫化机,这是因为液压式硫化机结构上具有如下特点:1. 机体为固定的框架式,结构紧凑,刚性良好。
虽然液压式硫化机也是双模腔,但从受力角度看,只是两台单模硫化机连结在一起,在合模力作用下,机架微小变形是以模具中心线对称的;2. 开合模时,上模部分仅作垂直上下运动,可保持很高的对中精度和重复精度;另一方面,对保持活洛模的精度也较为有利;3. 上下合模力均匀,不受工作温度影响;4. 整机重量减轻,仅为机械式硫化机的1/3;5. 由于取消了全部蜗轮减速器、大小齿轮、曲柄齿轮和连杆等运动部件和易损件,使维护保养工作量减少。
一、液压式轮胎定型硫化机的工作程序液压硫化机工作时,升降油缸带动上模沿导向柱上升,在机架内形成空腔,装胎装置转进装胎,中心机构的上下环上升,胎胚定位,装胎装置卸胎后退出,升降油缸带动上模沿导向柱下降合模,胎胚定型后合模到位,在模座下面的4个短行程加力油缸作用下,产生要求的合模力。
轮胎硫化结束后,加力油缸卸压,升降油缸带动上模上升,轮胎脱出上模,上模上升到位后,中心机构囊筒上升,轮胎脱下模,中心机构的上下环下降,胶囊收入囊筒中,同时,卸胎机构转进,囊筒下降,卸胎机构将轮胎翻转而出,送至后充气冷却。
从各国实践经验看,液压式硫化机在升降驱动装置、活络模装置、加力装置、中心机构、囊筒升降装置上采用液压驱动。
可以说除卸胎装置和装胎装置采用气动控制外,其它均采用液压驱动。
因此,作为动力源的液压系统设计十分重要。
二、硫化机液压动力源的设计1140液压式轮胎硫化机硫化胎圈直径范围12”~18”,最大合模力为1360KN。
合模力的获得完全来源于油压。
一般采用低压力、较快速度、较长行程的油缸控制开合模。
合模后,用高压、短行程的油缸使上下模受到合模力。
由于负载和速度变化较大,要求相应的液压系统能提供较大范围变化的压力和流量。
液压系统各缸工作时所需流量计算如下:缸的几何流量Q=式中:Q-几何流量l/minA-有效面积S-缸的行程mt-运行时间s已知各缸行程,运动时间及有效面积,依程序图各缸运动顺序,分别计算各时间段流量如下表。
画出流量时间图(图二)由图二可见系统流量变化较大,在充分考虑了液压系统工作的可靠性、安全性及实用性情况下,采用双联叶片泵作为动力源,能完全满足流量范围变化大的要求,另一方面该泵,具有液压冲击小、压力平稳、噪声小、工作性能较好的优点。
由于采用双联叶片泵,须配有溢流阀-卸荷阀组,以满足不同流量时的要求;同时,在工作过程中,当卸胎装置、装胎装置工作时,所有液压缸均处于不工作状态,如果采取停止泵的运转的方式,会造成泵频繁启动,为避免这一现象,考虑采用电控溢流阀,通过电气控制,使溢流阀平时起安全阀作用,电磁铁带电时处于卸荷状态。
液压源设计成功与否,不仅仅要正确选择液压泵以解决动力源问题,而且需全盘考虑配置,才能达到性能要求。
因此在液压站的设计中,泵与电机的联接采用弹性联轴器,确保同轴度与垂直度的同时具有良好的减振性;在泵和电机的安装上采用立式安装,不仅节省安装空间,且油泵浸于油面以下,油泵自吸良好;主油路中液压油的压力由主溢流阀的工作状态控制,为了保证油液的清洁度,设置精密过滤器(10μm),保证比例系统正常工作。
三、硫化机的保压和泄压硫化机在工作循环中,轮胎硫化需长时间保压(主要是加力缸和中心缸的保压),以确保轮胎质量。
保压性能的好坏,直接影响到轮胎硫化的质量,在设计时,拟定了两种保压方式。
1. 用液控单向阀保压。
如图三所示。
在油缸的进油路上串联一个液控单向阀,利用单向阀锥形阀座的密封性来实现保压。
它在200Mpa压力下,10min内压力降不超过2Mpa。
2. 用蓄能器保压。
如图四所示。
蓄能器与主缸相通,补偿系统漏油,并且在蓄能器出口设单向节流阀,其作用是防止换向阀切换时,蓄能器突然泄压而造成冲击。
采用蓄能器保压24小时内,压力降不超过1~2bar。
两种方式在理论上均有可取之处。
用液控单向阀保压,简单、易于安装。
但随着锥阀磨损或油的污染,液压油的泄漏增加,保压性能将降低,此外,这种方法在保压过程中压力降过大,因此可靠性差。
而采用蓄能器保压,既能节约功率,又能保证1140液压硫化机保压15min 中内压力基本不降。
因而,在1140液压硫化机中采用蓄能器保压。
保压时由于主机的弹性变形、油的压缩和管道的膨胀而贮存了一部分能量,故保压后必须逐渐泄压,泄压过快,将引起液压系统剧烈的冲击、振动和噪声,甚至会使管路和阀门破裂。
因此,设计中采用适当的泄压方式十分重要。
本机中采用延缓换向阀切换时间来达到逐步泄压目的。
即采用带阻尼器中位为Y型的电液换向阀。
当保压完毕反向回程时,由于阻尼器的作用,换向阀延迟换向,使换向阀在中位停留时主缸上腔泄压后再换向回程。
四、比例技术在液压硫化机中的应用硫化机在开合模过程中,油缸行程较大。
合模时,要求油缸首先快速合模,在接近定型时,为防止因速度过大,造成惯性前冲,油缸需要减速,即慢进,然后到位停止,并且二次定型后,完全合模时,合模缸速度也较小。
此外,硫化完毕,上模开启时,为提高效率,应快速开模,在快到达预定位置时,为防止冲击,需要减速到达死点后锁紧。
从以上过程可以看出,开合模油缸在往返行程中,速度和加速度都不同。
根据此工况,利用传统式的液压控制阀拟定控制合模缸的液压原理图如图五。
利用传统式的液压控制阀,由于只能对液流进行定值控制,而换向阀只起开关作用,组成的液压系统较复杂,同时,大量液压阀的应用,也降低了系统的可靠性,且系统的动静态特性都较差。
随着液压技术的发展,60年代末出现了比例技术,由于比例控制具有电液伺服系统优良的动、静态特性的优点,且加工制造简单、价格低廉、工作可靠、维护方便。
因而,在设计中,首次将比例技术这一先进技术应用到液压系统中,提高了产品的技术含量。
利用比例技术实现开合模过程的控制,其液压原理图如图六。
此处仅使用一个比例方向阀便实现了需七个传统液压阀方能实现的功能。
这种控制方式实质就是利用比例方向阀的"连续控制",除了能达到液流换向的作用外,还通过控制换向阀的阀芯位置来调节阀口开度来控制流量。
因此,它兼有流量控制和方向控制的功能,而传统的换向阀仅起开关的作用。
从成本上而言,单个比例阀价格较高,但由于它能取代多个普通液压阀,且动、静态特性良好,而压力损失较普通阀小,有利于降低系统能耗和温度,因此,利用比例阀有较好的性能价格比。
在1140液压式硫化机的设计中,充分考虑了各工况的要求,以最经济、简洁的控制方式来满足机器的各项性能要求,在液压系统的设计中做到了运行平稳、冲击小、可靠性高。
为节省安装时间,在液压阀的安装上没有采用常用的板式联接,而是采用集成式联接,该方法将阀串联叠加,如电气上的集成块,一组即可实现某一功能。
另一方面,对一些溢流阀、单向阀采用插装阀,此种阀直接与阀块中相应的孔配合而与叠加阀构成完整的液压系统,叠加阀与插装阀的使用,使液压站结构布置紧凑,管路简化,安装方便。
五、结束语在实际应用中,液压式硫化机替代机械式硫化机已成为无可置疑的发展趋势。
在这种形势下,作为国内硫化机主要生产厂家,大力开展液压硫化机的开发工作,势在必行。
目前,桂林橡胶机械厂已完成1140液压硫化机的设计工作,并提交用户使用。
1140液压式轮胎定型硫化机由存胎器、装胎装置、机架、中心机构、升降驱动装置、硫化室、调模装置、锁模装置、卸胎装置、后充气、热工管路系统、空气管路系统、液压管路系统、电气仪表控制系统等部分组成。
技术指标如下:1.硫化室数目2个2.硫化室内径1140mm3.加热方式热板式加热4.中心机构形式C型5.最大合模力1360KN6.模具高度范围190~430 mm7.胎圈直径范围12〃~18〃8.最大生胎高度370 mm9.最大生胎外径活络模740mm两半模810 mm10.最大内压2.8Mpa11.最大热板蒸汽压力1.6 Mpa12.最大定型蒸汽压力0.25 Mpa13.控制气源压力0.6 Mpa14.仪表气源净化的0.6 Mpa15.电源三相AC380V±15%50HZ±2%单相AC220V±15%50HZ±2%DC 24V16.负载约16KW17.后充气胎圈直径12〃~18〃胎圈宽度调节范围102~228 mm充气轮胎外径432~863 mm18.重量约14T19.外形极限长X宽X高约4000X3560X4770。