PCB干膜培训教材(完整)
合集下载
PCB干膜培训教材(完整)PPT课件

1.有较高的分辨率,一般线宽可做4mil; 2.干膜应用在图形电镀工艺中,电镀加厚在高而 垂直的夹壁间进行,在镀层厚度小于抗蚀剂厚 度时,可以防止产生镀层突延和防止去膜时抗 蚀剂嵌入镀层下面,保证线条精度;
3.干膜的厚度和组成一致,避免成像时的不连 续性,可靠性高; 4.应用干膜,大大简化了印制板制造工序,有利 于实现机械化、自动化。
干膜工艺流程详细介绍
磨板 贴膜 曝光
显影
蚀刻或电镀
褪膜
干菲林 Cu
基材 底片
一、磨 板
磨板的作用:基板前处理主要是解决表面清洁度和表 面粗糙度的问题。粗化铜面,便于菲林附着在铜面上 。 磨板的种类:化学磨板、机械磨板。 机械磨板工艺:
酸洗 水洗 磨板 水洗 水洗 吸干 热风干
以上关键步骤为酸洗和磨板段。
四、 显 影
显影的作用:
是将未曝光部分的干菲林去掉,留下感光的部分 。
显影的原理:
未曝光部分的感光材料没有发生聚合反应,遇弱 碱Na2CO3(0.8-1.2%)溶解。而聚合的感光材料则留在 板面上,保护下面的铜面不被电镀或蚀刻药水溶解。
• 6.干膜起皱 • 7.干膜与基板铜表面之间出现气泡
干膜的类型
• v 1.溶剂型干膜
使用有机溶剂作显影剂和去膜剂,例如用 1.1.1三氯乙烷显影,二氯甲烷去膜,这两种溶 剂遇
火不燃烧。醋酸丁酯等有机溶剂也可用作显影和去膜, 但易燃烧,很不安全。 溶剂型干膜是美国最早研制并投 入大量生产的一种干膜,我国早期也研制过。它的优点 是 技术成熟,工艺稳定,耐酸耐碱,应用范围广。但是, 使用这种干膜需要消耗大量的有机溶剂,需 要价格昂贵 的显影和去膜设备及辅助装置,生产成本高,溶剂有毒, 污染环境,所以日趋以水溶 性干膜所取代,仅在特殊要 求时才使用。
PCB工艺培训教材

用丝印网将阻焊泥漏印于板面通过预烘去除挥发形成半固化预烘丝印第二面字符对位曝光膜层通过对位曝光被光照的地方阻焊膜交连反应没照的地方在碱液作用下显影掉
工艺技术培训
印制线路板 PCB
PCB, 全称print circuit board, 是在覆铜板上贴上干膜,经曝光 显影、蚀刻形成导电线路图形在 电子产品起到电流导通与信号传 送的作用,是电子原器件的载体.
光致抗蚀层 聚酯保护膜
主要原材料介绍
覆铜板
铜箔 绝缘介质层 铜箔
主要原材料介绍
半固化片
主要作用: 多层板的粘结材料,起到多层板内层层间的粘接作用。 主要特点: 一定温度与压力作用下,树脂流动并发生固化 不同型号,其固化厚度不一致,用来调节板厚度 存放环境: 恒温、恒湿
主要原材料介绍
铜箔
外光成像
外光成像
图形电镀
目的: 使线路、孔内铜厚加厚到客户要求标准 流程: 除油 微蚀 预浸 镀铜 浸酸 镀锡 流程原理: 通过前处理,使板面清洁 ,在镀铜、镀锡缸 阳极溶解 出铜离子、锡离子,在电场作用下 移 动到阴极,其得到电子,形成铜层、锡层。 注意事项 : 镀铜厚度、镀锡厚度、镀铜、锡均匀性 掉锡、手印、撞伤板面
黑化
目的: 使内层铜面形成微观的粗糙,增强层间化片的 粘接力。 流程: 除油 微蚀 预浸 黑化 烘干 流程原理: 通过除油、微蚀,黑氧化在干净的铜面上形成 氧化铜与氧化亚铜的棕红色膜层,增强粘接力 注意事项: 黑化不良、黑化划伤、黑化过厚、过溥 挂栏印、板面手印、板面油污
层压
目的:
使多层板间的各层间粘合在一起,形成一完整多层板。
化学沉铜
目的: 对孔进行孔金属化,使原来绝缘的基材表面 沉积上铜,达到层间电性相通. 流程: 溶胀 凹蚀 中和 除油 除油 微蚀 浸酸 预浸 活化 加速 沉铜 流程原理: 通过前面的除胶渣,将孔内的钻孔钻污去除, 使孔内清洁 ,后通活化在表面与孔内吸附胶体钯, 在沉铜缸内发生氧化还原反应,形成铜层附于板面。 注意事项: 凹蚀过度 孔露基材 板面划伤
工艺技术培训
印制线路板 PCB
PCB, 全称print circuit board, 是在覆铜板上贴上干膜,经曝光 显影、蚀刻形成导电线路图形在 电子产品起到电流导通与信号传 送的作用,是电子原器件的载体.
光致抗蚀层 聚酯保护膜
主要原材料介绍
覆铜板
铜箔 绝缘介质层 铜箔
主要原材料介绍
半固化片
主要作用: 多层板的粘结材料,起到多层板内层层间的粘接作用。 主要特点: 一定温度与压力作用下,树脂流动并发生固化 不同型号,其固化厚度不一致,用来调节板厚度 存放环境: 恒温、恒湿
主要原材料介绍
铜箔
外光成像
外光成像
图形电镀
目的: 使线路、孔内铜厚加厚到客户要求标准 流程: 除油 微蚀 预浸 镀铜 浸酸 镀锡 流程原理: 通过前处理,使板面清洁 ,在镀铜、镀锡缸 阳极溶解 出铜离子、锡离子,在电场作用下 移 动到阴极,其得到电子,形成铜层、锡层。 注意事项 : 镀铜厚度、镀锡厚度、镀铜、锡均匀性 掉锡、手印、撞伤板面
黑化
目的: 使内层铜面形成微观的粗糙,增强层间化片的 粘接力。 流程: 除油 微蚀 预浸 黑化 烘干 流程原理: 通过除油、微蚀,黑氧化在干净的铜面上形成 氧化铜与氧化亚铜的棕红色膜层,增强粘接力 注意事项: 黑化不良、黑化划伤、黑化过厚、过溥 挂栏印、板面手印、板面油污
层压
目的:
使多层板间的各层间粘合在一起,形成一完整多层板。
化学沉铜
目的: 对孔进行孔金属化,使原来绝缘的基材表面 沉积上铜,达到层间电性相通. 流程: 溶胀 凹蚀 中和 除油 除油 微蚀 浸酸 预浸 活化 加速 沉铜 流程原理: 通过前面的除胶渣,将孔内的钻孔钻污去除, 使孔内清洁 ,后通活化在表面与孔内吸附胶体钯, 在沉铜缸内发生氧化还原反应,形成铜层附于板面。 注意事项: 凹蚀过度 孔露基材 板面划伤
外层干膜培训资料

注意事项
1、每班清洗退膜缸过滤器中过滤网及缸中的过滤网,防 止膜渣堵塞过滤网、喷管、喷嘴,并对退膜缸内四周 及缸底清洗干净。 2、每班更换一次水洗缸,清洗过滤网及过滤筒。 3、巡线人员每4个小时巡线检查所有的压力、温度、速 度、液位酸洗是否正常。生产过程中,巡线人员发现 滤渣要满出网外必须及时清理,防止药水溢出缸外。 4、每周对退膜线做一次保养,清洗烘干段及风机过滤筒 5、每班对酸洗药水化验一次,控制在要求范围内,防止 板面氧化影响AOI假点数。
二、工艺流程
前处理 ↓ No No No 清洁 ┌ - - ┌ --┬-─ ┐ ↓ 菲 │ │ ↓ 贴膜 菲 生 贴 林 生 │ 黑 ↓ 林 Yes 产 保 Yes 检 Yes 产 Yes 检 菲 对位 ←─ 的←─ 前←─护←─ 查←─ 前←─ ←─ 林 ↓ 清 检 膜 机 检 查 制 曝光 洁 查 检 查 作 ↓ │ 查 ↑ 显影 └ ─ ─ ─ ─ ─ ─ ─┘ ↓ No 退 回 蚀刻 ↓ 退膜 → 检、修板→出板
Hale Waihona Puke 检板一、目的:检查显影后板面质量,进行修理。 检查蚀刻后在线生产板有无明显蚀刻不净、残铜等。 检查退膜后板有无氧化、退膜不净等。
二、注意事项;
注意戴手套检板、拿板,放板动作双手拿板边、轻拿轻放, 不要大板靠小板擦花干膜、板面
五、常见缺陷及原因
开路缺口
膜上杂物造成开路
常见缺陷及原因
水洗喷淋的压力(Kg/cm2) 酸洗浓度(%) 酸洗喷淋压力(Kg/cm2) 速度(m/min)
1.0-2.5 1-4 1-2 1-6
蚀刻反应原理
蚀刻的原理:在蚀刻过程中,氯化铜中的二价铜 具有氧化性,能将印刷电路板上的铜氧化成一 价铜,所形成的氯化亚铜是不易容于水的,在 有过量的氯离子存在的情况下,能形成可溶性 的络离子。随着铜的蚀刻,溶液中一价铜越来 越多,蚀刻能力很快下降,以至最后失去能力 ,为了保证连续的蚀刻能力,可以通过各种方 式对蚀刻进行再生,使一价铜重新转变成二价 铜,达到正常蚀刻的工艺标准。
PCB工艺流程培训教材(更新)
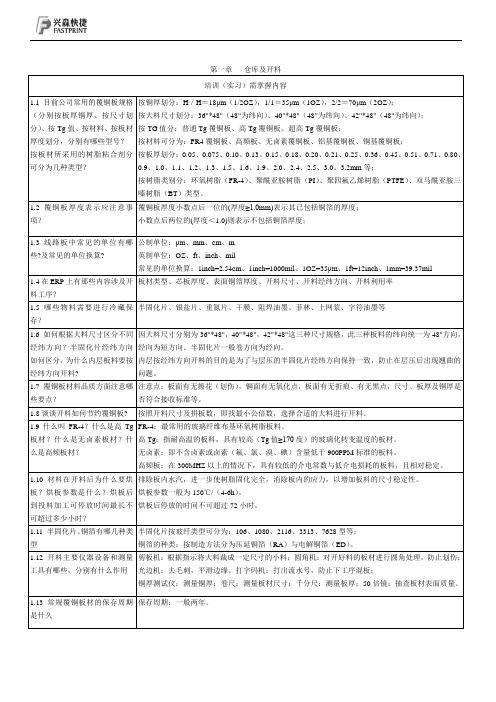
第三章棕化与层压工序
第四章光成像工序
第五章化学沉铜
第六章DES与SES线
第七章热风整平工序
第八章阻焊及字符
第九章实验室
第十章AOI
第十一章电测试
应用范围:孔电阻测试,线圈电阻测试,电感型线路测试,嵌入式电阻测试
第十二章外形
培训(实习)需掌握内容
外形工序一般工艺流程为:前工序→作业准备
板→(金手指倒角)→(成品清洗)→
(1)铣床---铣外形;(
第十三章镀金手指线
第十四章板镀与图镀
第十五章图形电镀镍、金线
第十六章成品检验工序
第十七章综合部分。
PCB知识培训教材.pptx
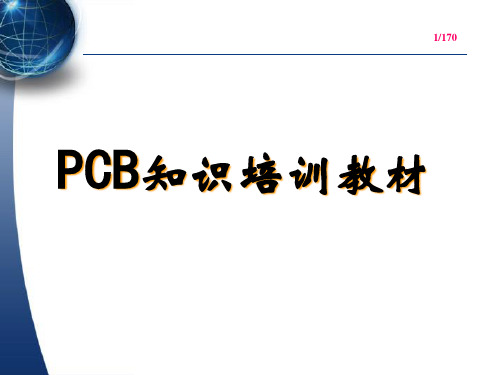
原来的光滑的表面侵蚀后形成有一定粗糙的表面来增加压板后与树脂布的粘合力。
其生产流程如下:
-
4 8 .5 "
typ 0 .1 "
20.1" x 2
4 0 .5 "
-
1 6 .1 " x 3
第 05节:压板
15/170
16/170
注意事项: 1)压板后板厚公差范围计算:
A:HASL板:成品板厚+公差-5mil(上限),成品板厚+公差-3mil(下限) B:沉金、沉银、Entek板:
5/170
相对于过去导线焊接方式,PCB最大的优点可分为三方面: 1)一旦PCB布置完成、就不必检查各零件的连接线路是否正确 这对精密复杂的线路(如电脑),可以省去不少检查功夫。 2)PCB的设计可使所有的信号路径开形成传送的线路,设计者 可以很合理的控制其特有的阻抗。 3)容易测试检修:信号线不会有短路碰线的危险,这对于逻辑电 路而言,只要有系统的布置,要找出其错误的地方就方便多了
1/170
PCB知识培训教材
目录
2/170
第一章 : PCB简介 第二章 : 生产流程简介
第01 节 :开料
第10 节 :线电
第02 节 :内层
第11 节 :蚀板
第03 节 :AOI
第12 节 :S/M &/碳油
第04 节 :棕化
第13 节 :印字
第05 节 :压板
第14 节 :G/F
第06 节 :钻孔
多张P片:A3:777—( )—777, 677—( )—776…...
A4:一般类型八层及以上板(包括阻抗板)
B1:内层铜厚为2 OZ,3 OZ的板
C1:Tg=170℃类型的板
MPCB基础知识通用培训教材
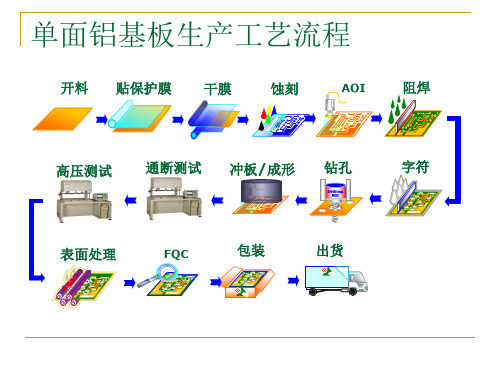
进料 → 备钻咀 → 钻孔 → 检验
铝基板生产工艺流程—钻孔物料
钻咀:采用硬质合金材料制造,它是一种钨钴类合金,以碳化钨
(WC)粉末为基体,以钴(CO)作为粘合剂,经加压烧结而成, 具有高硬度、非常耐热,有较高的强度,适合于高速切削,但韧性
差、非常脆。 直径范围: ¢0.2-¢6.3mm
钻咀结构:
铝基板生产工艺流程—阻焊
阻焊-显影:
目的---将未发生聚合反应的油墨利用溶液去除掉。
显影的主要控制项目:
浓度---1%Na2CO3 ; 速度--- 2 m/min- 4.2 m/min(依油墨而定); 温度--- 30±2℃; 喷淋压力--- 1.5-2.5kg/cm2 ;
铝基板生产工艺流程—字符
沉镍金:先在电路板裸铜表面反应沉积形成一层含磷7-9%的镍镀层, 厚度约3-5um,再于镍表面置换一层厚度约0.05-0.15um的纯金层。
铝基板生产工艺流程—表面处理
各种表面处理的优点:
工艺
沉镍金
( ENIG)
沉锡
沉银
无铅喷锡
(Immersion Tin) (Immersion silver) (Lead free HASL)
Cu Al
退膜
铝基板生产工艺流程—AOI
AOI
目的:利用光学原理比对工程资料进行精确检查,找出缺陷点。 检测的项目:焊盘缺陷,缺口,焊盘直径缩小,针孔,凹陷;线条缺 陷,如短路,开路,线宽/线间距,缺口,凹陷,铜渣,针孔等。 确认人员不光要对测试缺点进行确认,另外就是对一些可以直接修补 的确认缺点进行修补。
垫板:
防止钻孔披锋; 提高孔位精度; 减少钻咀损耗。
沟长 本体长
全长
钻尖角 直径
铝基板生产工艺流程—钻孔物料
钻咀:采用硬质合金材料制造,它是一种钨钴类合金,以碳化钨
(WC)粉末为基体,以钴(CO)作为粘合剂,经加压烧结而成, 具有高硬度、非常耐热,有较高的强度,适合于高速切削,但韧性
差、非常脆。 直径范围: ¢0.2-¢6.3mm
钻咀结构:
铝基板生产工艺流程—阻焊
阻焊-显影:
目的---将未发生聚合反应的油墨利用溶液去除掉。
显影的主要控制项目:
浓度---1%Na2CO3 ; 速度--- 2 m/min- 4.2 m/min(依油墨而定); 温度--- 30±2℃; 喷淋压力--- 1.5-2.5kg/cm2 ;
铝基板生产工艺流程—字符
沉镍金:先在电路板裸铜表面反应沉积形成一层含磷7-9%的镍镀层, 厚度约3-5um,再于镍表面置换一层厚度约0.05-0.15um的纯金层。
铝基板生产工艺流程—表面处理
各种表面处理的优点:
工艺
沉镍金
( ENIG)
沉锡
沉银
无铅喷锡
(Immersion Tin) (Immersion silver) (Lead free HASL)
Cu Al
退膜
铝基板生产工艺流程—AOI
AOI
目的:利用光学原理比对工程资料进行精确检查,找出缺陷点。 检测的项目:焊盘缺陷,缺口,焊盘直径缩小,针孔,凹陷;线条缺 陷,如短路,开路,线宽/线间距,缺口,凹陷,铜渣,针孔等。 确认人员不光要对测试缺点进行确认,另外就是对一些可以直接修补 的确认缺点进行修补。
垫板:
防止钻孔披锋; 提高孔位精度; 减少钻咀损耗。
沟长 本体长
全长
钻尖角 直径
PCB 教育训练教材
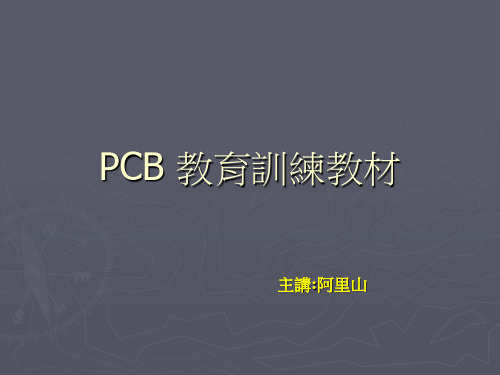
按IPC-CF-150將銅箔分為兩個類型 IPC-CF-150將銅箔分為兩個類型 TYPEE 表電鍍銅箔 TYPEW 表輾軋銅箔 將之分成八個等級 class 1到class 4是電鍍銅箔 1到 4是電鍍銅箔 class 5到class 8是輾軋銅箔 5到 8是輾軋銅箔
輾軋銅箔
是將銅塊經多次輾軋製作而成, 是將銅塊經多次輾軋製作而成,其所輾出之寬度受到技術限制很難達到標 準確尺寸基板是要求(3尺 準確尺寸基板是要求(3尺*4尺),而且很容易在輾制過程中造成報廢,因表面 ),而且很容易在輾制過程中造成報廢, 粗糙不夠,所以與樹脂之結合能力比不好, 粗糙不夠,所以與樹脂之結合能力比不好,而且製造過程中所受應力需要做 熱處理之回火刃化(Heat 熱處理之回火刃化(Heat treatment or Annealing),故其成本較高. Annealing),故其成本較高.
玻織紗在紗束中之左旋(z)與右旋 玻織紗在紗束中之左旋 與右旋(s) 與右旋
絞
玻璃紗
玻璃紗
玻璃布是由經紗(Warp)及緯紗(Fill)所縱橫交織而成的,因經紗的長 整經 Warping 度很長,關係著布料的整體品質,故需就所織出布幅寬度,將所買來的 原紗重新加以密集間隔排列,也就是重新將多卷原紗同時平行排繞在等 待織布的經軸上(Warp beam)經紗對整卷布料的品質影響要較緯紗為 大,故需將買來的經紗重整一次以保證布的品質。緯紗則是直接繞在緯 管上(Qvill or bobbin)去織布即可,無需再做其他整理及處理
早期的織布機都地用梭子牽引緯紗,快速往復穿過一上一下的經紗 織布 Weaving 而織成布匹的,不但吵聲太大,且機械繁親容易損壞。業者現在都
已改良為無梭織布機,即改用速度更快的壓縮空氣或水體來帶動緯 紗。用於基板的玻璃布,自始至終都只用一種平織法(Plain 自始至終都只用一種平織法( 自始至終都只用一種平織法 Weave) Weave),是經緯上下交錯的,因這種織法的尺寸最具安定性也最 不易變形,而且重量及厚度也最均勻。
干膜培训教材(SES)

以电镀供应商工艺要求为准。
3. 基本工艺要求
去膜
去膜液浓度 :2.0~3.0%(NaOH浓度) 去膜液温度 :45~55 ℃ 去膜压力 水洗压力 去膜点 :2.0~3.0kgf/cm2 :1.0~3.0kgf/cm2 :50~60%
3. 基本工艺要求
蚀刻、去锡/ 蚀刻、去锡/锡铅
以蚀刻药水和去锡药水供应商工艺要求为准。
3. 基本工艺要求
前处理
水洗 吸干 烘干 : 多过3个缸(循环水)喷淋压力:1~3Kgf/cm2 循环水 喷淋压力: ~ 个 循环 喷淋压力 : 通常用2支海绵吸水辘 通常用 支海绵吸水辘 吸水 :热风吹风量为 4.0~9.0m3/min 热风吹 热风 ~ 热风的温度为80~ ℃ 热风的温度为 ~90℃ 其它控制项目 水裂点: 其它控制项目 :水裂点:>20s 粗糙度1.5<Rz<3.0 粗糙度
AQ-4088 AQSPGSPG-152 ADVADV-401
40 15 40
2. 线路板图形制作工艺
两种镀通孔线路板制作的比较 两种镀通孔线路板制作的比较 通孔线路板制作的
Tenting制程
研磨 贴膜
SES制程
全板电镀铜 基铜 玻璃纤维底料 曝光原件 干膜
曝光
显影
蚀板
电镀铜/锡或锡/铅 碱性蚀板
C O O- C O O H- + N a
+ N a
C O O- + N a COO - + N a
- COO
N a O H /H 2 O
- COO + N a
C OOH
C OOH
COOH
C O O- + N a
C O O- + N a
C O O- + N a
- 1、下载文档前请自行甄别文档内容的完整性,平台不提供额外的编辑、内容补充、找答案等附加服务。
- 2、"仅部分预览"的文档,不可在线预览部分如存在完整性等问题,可反馈申请退款(可完整预览的文档不适用该条件!)。
- 3、如文档侵犯您的权益,请联系客服反馈,我们会尽快为您处理(人工客服工作时间:9:00-18:30)。
机器保养
取出吸水棉泡入清水中; 清洗过滤网 显影缸水洗缸的清洗:排空水洗缸.显影药水,加入 清水至标准液并加入NaOH,浓度为5%,开循环喷洗 2h后排掉,加入清水至标准液喷淋10min排掉。 加入清水至标准液并加入H2SO4,浓度为3开循环喷 洗2h后排掉,再每缸加入清水至标准液位开循环喷 洗10分,排净废水; 把吹风.烘干段的风刀拆下清洗
干膜工艺流程详细介绍
磨板 贴膜 曝光 显影
蚀刻或电镀
Cu 干菲林 基材
底片
褪膜
一、磨
板
磨板的作用:基板前处理主要是解决表面清洁度和表 面粗糙度的问题。粗化铜面,便于菲林附着在铜面上。 磨板的种类:化学磨板、机械磨板。
机械磨板工艺:
酸洗 水洗 磨板 水洗 水洗 吸干 热风干
以上关键步骤为酸洗和磨板段。
生产控制(注意)事项
6.从插板架上收板后只能斜着靠在放板架上,不能平 叠,以免压伤干膜流胶; 7.没用完的干膜用黑色胶纸包扎,并且平着摆放贮存 以防错位; 8.每割膜200PNL需更换刀片一次并检查割膜效果; 9. 压膜后需静放 15 分钟方可曝光 , 压膜 48H 之内必须 曝光完毕,否则返洗处理; 10.保证压膜出板温度超过50℃;
操作规范
1.放板和接板人员都必须带手套操作
2.两手持板边,不要裸手接触到拼板单元内 3. 轻拿轻放,小心擦花板面,取板一块一块
插架 4.放板时,先后板间距不能小于2cm,以免叠 板 5.放板人员检查板面是否有异常情况,如擦 花、压伤等
工艺参数控制
1.H2SO4浓度3-5% 2. 磨痕:10-16MM 3.速度: 2.0-3.0m/min 4.水洗压力:1.0-2.0kg/cm2 5.烘干温度:85-95 ℃
品质要求
板面无保护膜、干膜碎 板面无胶迹、无擦花 无显影过度、显影不净 NPTH孔无破孔
显影点测试
将已贴干膜的未曝光板三至四块(可选用返 洗板),约等于药水缸的长度,按正常条件 调节好参数开启显影机,将板一块接一块放 入显影机,等第一块刚出显影缸,最后一块 完全进入显影缸时,立即关掉显影泵,将板 传出显影机,观察显影干净的长度达到4060%为合格。
二、贴 膜
贴膜时,先从干膜上剥下聚乙烯保护膜,然
后在加热加压的条件下将干膜抗蚀剂粘贴在 铜面上。干膜中的抗蚀剂层受热后变软,流 动性增加,使抗蚀剂流入板面的微观结构内, 借助于热压辊的压力和抗蚀剂中粘结剂的作 用完成贴膜
二、贴 膜
贴膜的作用:是将干膜贴在粗化的铜面上。
保护膜 干菲林
贴膜机将干膜通过压轳与铜面附着,同时 撕掉一面的保护膜。
2——循环水洗3——循环水洗4——清水洗— —吹干——烘干
操作规范
1. 放板时,先后板间距不能小于2cm,以免 叠板 2. 接板人员戴手套接板、插架时一块一块的 插架,确保板面不被刮花 3.检查有无撕膜干净、批量性的显影不净问 题
~1.2% 显影液温度:30±2℃ 显影压力:2.0±0.5kg/cm2 水洗压力:1.0-2.0kg/cm2 烘干温度:50~60℃ 显影速度:3.0-4.0m/min
四、 显 影
显影的作用: 是将未曝光部分的干菲林去掉,留下感光的部分。 显影的原理:
未曝光部分的感光材料没有发生聚合反应,遇弱 碱Na2CO3(0.8-1.2%)溶解。而聚合的感光材料则留在 板面上,保护下面的铜面不被电镀或蚀刻药水溶解。
显影流程
入板 —— 显影 —— 循环水洗 1—— 循环水洗
生产控制(注意)事项
4.抽真空时需要加赶气动作,确保曝光良好 5. 对位 10-15pnl 板需用粘尘辘清洁曝光菲林、曝光 台面、对位台一次;每对位 20-30pnl板需送检菲林 一次;每曝光30分钟,需用菲林水清洁曝光机玻璃 与MYLAR一次。 6.曝光完成后的板停放15MIN以上再显影 7.每菲林曝光次数严格按照程序文件规定控制 :500600次报废
品质要求
1.对位时干膜的聚脂薄膜不被撕起 2.对位时没有偏孔、对反等情况
3.曝光图象清晰,无曝光不良情况
曝光操作环境的条件(无尘房控制)
1. 温湿度要求:20±3°C,55±10%。 (干菲林储存的要求,曝光机精度的要求,底片储存 减少变形的要求等等。) 2. 洁净度要求: 达到万级。 (主要是图形转移过程中完全正确的将图形转移到板 面上,而不允许出现偏差。) 3. 抽真空要求:图形转移的要求,使图形转移过程中不 失真。
干膜的类型
使用有机溶剂作显影剂和去膜剂,例如用 1.1.1三氯乙烷显影,二氯甲烷去膜,这两种溶 剂 遇火不燃烧。醋酸丁酯等有机溶剂也可用作显影和去 膜,但易燃烧,很不安全。 溶剂型干膜是美国最早研 制并投入大量生产的一种干膜,我国早期也研制过。 它的优点是 技术成熟,工艺稳定,耐酸耐碱,应用范 围广。但是,使用这种干膜需要消耗大量的有机溶剂, 需 要价格昂贵的显影和去膜设备及辅助装置,生产成 本高,溶剂有毒,污染环境,所以日趋以水溶 性干膜 所取代,仅在特殊要求时才使用。
生产控制(注意)事项
1.检查各喷嘴是否堵塞、破损、缺少;
2.检查各过滤网是否干净、破损; 3每次生产前根据不同板厚做磨痕试验,确认
OK后方可进行生产。 4定时的进行机器保养(保养详见操作指示)
磨痕试验
取一片未作图形的厚度与生产板相同的废板作测试板,打开 输送→放板入上刷(下刷)位置→关闭输送→打开上刷(下 刷)→调整手柄调压到电流设定值磨板8-10秒→关闭磨刷→ 打开输送→取出测试板、测量磨痕宽度在工艺条件内(宽度 均匀一致、磨痕均匀),不合要求,调整磨刷,重新试磨痕; (生产前.每班一次)
生产控制(注意)事项
1.根据不同板的尺寸,装上相适应尺寸干膜; 2.装上干膜,调整上/下干膜对整齐,过热辘后检查是 否OK且干膜两端热辘是否粘有干膜碎: 3.贴膜之前每块板必须经过辘尘,减少尘埃 4. 放板贴膜时 , 板与板之间距必须保持 3-5mm 以上以 免叠板 5.把刚贴膜板趁热割膜,垂直插架冷却,不可热板叠 板;
品质要求
1.贴膜前板面进行辘尘清洁 2.贴膜前板面温度50
±5℃ 3.贴膜无起皱,无气泡 4.板边割膜整齐,无干膜碎
三、对位曝光
曝光即在紫外光照射下,光引发剂吸收了光
能分解成游离基,游离基再引发光聚合单体 进行聚合交联反应,反应后形成不溶于稀碱 溶液的体型大分子结构。
三、对位曝光
品质要求
6.1板面无氧化、无油污、无水迹、无胶迹 6.2磨痕均匀,无擦花、刮痕 6.3板面清洁,孔内及板面干燥
机器保养
1.取出吸水棉泡入清水中 2.水洗、酸洗缸的清洗:水洗缸、酸缸各加入NaOH,浓
度为5-10%,开循环喷洗2hr,排净废液加入清水于标准液位, 开循环喷洗30分,排除废水加入清水至标准液位,往水洗缸. 酸缸各加入5L H2SO4,开循环喷洗2hr,排净废液; 7.6.加入清水于标准液位,开循环喷洗30分,排除废水; 7.7.加入清水于标准液位,开循环喷洗15分,检查传送.喷嘴. 压力表运行是否正常;排除废水
曝光的作用是曝光机的紫外线通过底片使菲林 上部分图形感光,从而使图形转移到铜板上。
底片 干菲林 Cu 基材
曝光反应过程
在曝光过程中,干膜的光聚合反应是需要经
过一个过程才能完成的。如下:
单 体 消 耗 增 加
诱导 区
单体耗 尽 区
曝光时间增加
单体耗 尽 区
操作规范
1. 对位人员对位前对自己的台面用菲林水进行清洗 确保台面干净 2.对位前检查菲林与工卡要求的版本相一致 3. 对位粘胶纸时保证其在菲林的遮光边上,对位人 员不允许留长指甲及戴戒指类,以免刮花菲林 4.拿板的时候必须轻拿轻放并放置在放板架上 5.曝光人员曝光之前对曝光玻璃和MYLAR进行清洗
PCB干膜培训教材
撰写: 日期:2009年5月4日
培训概要
1.简单叙述干膜的特性、种类及结构 2.详细介绍干膜工艺流程:
A操作规范
B工艺控制参数 C生产控制(注意)事项 D品质要求 E机器保养 3.干膜工序常见问题的讲解
什么是图像转移
制造印制板过程中的一道工序就是将照相底版上的电路 图像转移到覆铜箔层压板上,形成一种抗蚀或抗电镀的 掩膜图像。抗蚀图像用于“印制蚀刻工艺”,即用保护 性的抗蚀材料在覆铜箔层压板上形成正相图像,那些未 被抗蚀剂保护的不需要的铜箔,在随后的化学蚀刻工序 中被去掉,蚀刻后去除抗蚀层,便得到所需的裸铜电路 图像。而抗电镀图像用于“图形电镀工艺”,即用保护 性的抗蚀材料在覆铜层压板上形成负相图像,使所需要 的图像是铜表面,经过清洁、粗化等处理后,在其上电 镀铜或电镀金属保护层(锡铅、锡镍、锡、金等),然后去 掉抗蚀层进行蚀刻,电镀的金属保护层在蚀刻工序中起 抗蚀作用。
干膜的特点
1.有较高的分辨率,一般线宽可做4mil; 2.干膜应用在图形电镀工艺中,电镀加厚在高 而垂直的夹壁间进行,在镀层厚度小于抗蚀剂 厚度时,可以防止产生镀层突延和防止去膜时 抗蚀剂嵌入镀层下面,保证线条精度; 3.干膜的厚度和组成一致,避免成像时的不连 续性,可靠性高; 4.应用干膜,大大简化了印制板制造工序,有 利于实现机械化、自动化。
干膜工序常见的问题
1.显影后铜表面留有残膜
2.掩孔法效果不良 3.导线变细或未曝光区的光致抗蚀层显影时
(显影不净)
不易被冲洗掉 (曝光不良) 4.显影时干膜受损或显影后发现干膜起翘或 边缘不整齐 (显影过度) 5.当导线电镀锡铅时出现光致抗蚀膜层边缘 起翘而造成渗锡现象 (渗镀)
生产控制(注意)事项
1. 生产前检查各工艺参数是否在控制范围之内 2. 生产每2-4小时检查一次喷嘴是否堵塞 3. 接板人员接板的时候检查板面情况,如有显影不 净或过度、掩膜孔是否破裂。及时反馈出来并及时 的作出调整参数 4.定时的进行机器保养(保养详见操作指示) 5.每2小时做1次氯化铜试验,确认是否有显影不净 问题