铣床夹具设计
铣床夹具设计说明书【操作指南】
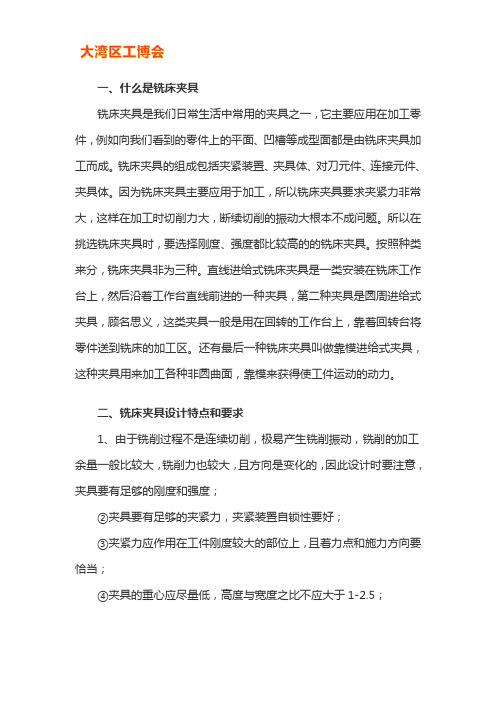
一、什么是铣床夹具铣床夹具是我们日常生活中常用的夹具之一,它主要应用在加工零件,例如向我们看到的零件上的平面、凹槽等成型面都是由铣床夹具加工而成。
铣床夹具的组成包括夹紧装置、夹具体、对刀元件、连接元件、夹具体。
因为铣床夹具主要应用于加工,所以铣床夹具要求夹紧力非常大,这样在加工时切削力大,断续切削的振动大根本不成问题。
所以在挑选铣床夹具时,要选择刚度、强度都比较高的的铣床夹具。
按照种类来分,铣床夹具非为三种。
直线进给式铣床夹具是一类安装在铣床工作台上,然后沿着工作台直线前进的一种夹具,第二种夹具是圆周进给式夹具,顾名思义,这类夹具一般是用在回转的工作台上,靠着回转台将零件送到铣床的加工区。
还有最后一种铣床夹具叫做靠模进给式夹具,这种夹具用来加工各种非圆曲面,靠模来获得使工件运动的动力。
二、铣床夹具设计特点和要求1、由于铣削过程不是连续切削,极易产生铣削振动,铣削的加工余量一般比较大,铣削力也较大,且方向是变化的,因此设计时要注意,夹具要有足够的刚度和强度;②夹具要有足够的夹紧力,夹紧装置自锁性要好;③夹紧力应作用在工件刚度较大的部位上,且着力点和施力方向要恰当;④夹具的重心应尽量低,高度与宽度之比不应大于1-2.5;⑤要有足够的排屑空间。
切屑和冷却液能顺利排出,必要时可设计排屑孔。
2、为了调整和确定夹具相对于机床的位置及工件相对于刀具的位置,铣床夹具应设置定位键和对刀装置。
定位键安装在夹具底面的纵向槽中,一般采用两个,其距离越远,定向精度越好。
定位键不仅可以确定夹具在机床上的位置,还可以承受切削扭矩,减轻螺栓的负荷,增加夹具的稳定怀,因此,铣平面夹具有时也装定位键。
除了铣床夹具使用定位键外,钻床、镗床等专用夹具也常使用。
三、铣床夹具设计的注意事项1.首先要对零件的工艺进行分析,对零件的平面度和表面粗糙度都逐一进行分析和归总。
2.选定毛坯的制造形式。
3.选择铣削方式。
铣削包括端面铣、周边铣、对称铣削、非对称铣,选择一个更加有利的铣削方式。
铣床夹具设计 (2)

铣床夹具设计简介铣床夹具是用于夹固定工件并使之达到精确位置,以便进行铣削加工的工具。
它在机械制造领域起着重要的作用,广泛应用于车间和工厂中。
在本文档中,我们将详细介绍铣床夹具的设计要点,包括夹具的类型、设计原则、选择材料以及制造工艺。
夹具的类型夹具的类型根据其功能和应用可以分为以下几类:1.平口夹具:用于夹持平面工件,通常由两个平面夹具板和夹紧螺钉组成。
2.V口夹具:用于夹持圆柱形工件,具有两个V形夹具板,可提供更好的工件夹持力。
3.U形夹具:适用于夹持较大的工件,采用U形夹具来固定工件并提供充分的夹持力。
4.弹性夹具:使用弹性材料制成,可以根据工件的形状进行夹持,适用于复杂形状的工件。
根据实际需求选择合适的夹具类型非常重要,不同类型的夹具具有不同的特点和适用范围。
设计原则在设计铣床夹具时,需要考虑以下几个原则:1.安全性:夹具在夹持工件时必须能够提供足够的夹持力,并防止工件在铣削过程中产生位移或脱离夹具的情况。
2.刚性:夹具的刚性越高,能有效避免工件的振动和变形,提高铣削加工的精度。
3.精确性:夹具设计应该考虑到工件的精度要求,并通过合适的夹持方式使工件达到所需的精度。
4.可靠性:夹具的设计应该保证长时间使用不发生故障,并且易于调整和维修。
以上原则是夹具设计的基本要素,设计师在设计过程中应该合理应用,并且根据具体情况进行优化。
材料选择夹具的材料选择主要考虑以下几个因素:1.强度:夹具需要具备足够的强度来夹持工件,因此选择具有高强度和刚性的材料是必要的。
2.耐磨性:夹具在长时间使用过程中,与工件接触会产生摩擦和磨损,选择具有良好耐磨性的材料能够延长夹具的使用寿命。
3.热稳定性:夹具在铣削过程中会受到热力的影响,因此选择具有良好热稳定性的材料可以避免夹具因温度变化而变形或失效。
4.加工性能:夹具的制造过程通常需要进行切削、铣削等加工过程,因此选择加工性能良好的材料对制造夹具也非常重要。
常见的夹具材料有钢材、铝合金等,具体选择应根据实际需求进行综合考虑。
铣床夹具设计实训报告册
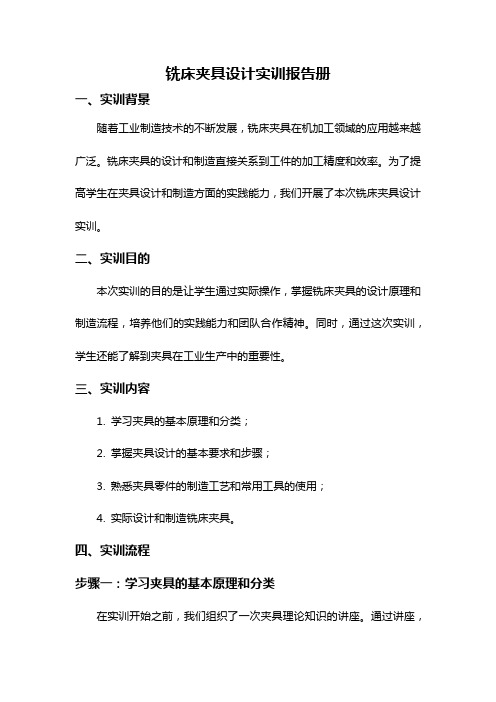
铣床夹具设计实训报告册一、实训背景随着工业制造技术的不断发展,铣床夹具在机加工领域的应用越来越广泛。
铣床夹具的设计和制造直接关系到工件的加工精度和效率。
为了提高学生在夹具设计和制造方面的实践能力,我们开展了本次铣床夹具设计实训。
二、实训目的本次实训的目的是让学生通过实际操作,掌握铣床夹具的设计原理和制造流程,培养他们的实践能力和团队合作精神。
同时,通过这次实训,学生还能了解到夹具在工业生产中的重要性。
三、实训内容1. 学习夹具的基本原理和分类;2. 掌握夹具设计的基本要求和步骤;3. 熟悉夹具零件的制造工艺和常用工具的使用;4. 实际设计和制造铣床夹具。
四、实训流程步骤一:学习夹具的基本原理和分类在实训开始之前,我们组织了一次夹具理论知识的讲座。
通过讲座,学生熟悉了夹具的基本原理,如定位、固定和过程装置,并学习了常见夹具的分类和应用场景。
步骤二:掌握夹具设计的基本要求和步骤为了让学生更好地掌握夹具设计的方法和技巧,我们组织了一次夹具设计的讲解。
学生了解了夹具设计的基本要求,如保证工件的位置和姿态精度,以及提高加工效率等。
并按照设计流程,学习了夹具设计的步骤和注意事项。
步骤三:熟悉夹具零件的制造工艺和常用工具的使用在实际制造夹具零件之前,我们对学生进行了一次夹具零件制造工艺和常用工具的培训。
通过理论课和实际演示,学生了解了夹具零件的加工流程和常用制造工具的使用方法。
步骤四:实际设计和制造铣床夹具在前期的学习和培训之后,学生开始了实际的铣床夹具设计和制造。
我们分成若干小组,每个小组负责设计和制造一种类型的夹具。
通过学生的协作和努力,最终完成了一批高质量的铣床夹具。
五、实训成果通过这次实训,学生不仅掌握了夹具设计和制造的基本技能,还培养了自己的实践能力和团队合作精神。
在制造过程中,学生积极解决问题,不断改进设计方案,并最终成功实现了铣床夹具的设计和制造。
这些成果不仅提高了学生的工程素质,也为他们今后的职业生涯打下了坚实的基础。
机床夹具设计步骤和实例

机床夹具设计步骤和实例机床夹具是用于在机床上夹持工件或刀具的装置,用于保持工件的位置稳定,使其能够被加工。
机床夹具设计的步骤主要包括需求分析、夹具类型选择、夹具基础结构设计、夹具强度计算、夹具定位系统设计、夹具操作系统设计、夹具零件设计和夹具组装等。
以下为机床夹具设计步骤和一个实例:步骤1:需求分析首先,需要了解加工工件的要求和工艺流程。
通过与工艺人员或工程师的交流,了解工件的形状、材料、尺寸等特性,以及工件的精度要求、加工工艺和工时要求等。
根据需求分析,明确夹具的基本功能、定位方式和操作方式。
步骤2:夹具类型选择根据加工工件的特性和加工工艺的要求,通过参考手册或专业书籍选择合适的夹具类型。
常见的夹具类型包括平板夹具、顶升夹具、转角夹具、滑块夹具、气垫夹具等。
根据不同的工件形状和加工要求,选择适合的夹具类型。
步骤3:夹具基础结构设计根据工件的形状和夹持要求,设计夹具的基础结构。
夹具的基础结构通常由夹紧装置、支撑装置和定位装置组成。
夹紧装置主要用于夹持工件,支撑装置用于保持工件的平衡和稳定,定位装置用于确保工件的位置准确。
步骤4:夹具强度计算根据夹具类型和加工工件的特性,计算夹具的强度。
夹具的强度计算包括静态强度和动态强度两个方面。
静态强度主要考虑夹具在夹持工件时的受力情况,包括切削力、惯性力等;动态强度主要考虑夹具在工件加工过程中的振动和冲击力,保证夹具结构能够承受夹持工件时的各种力。
步骤5:夹具定位系统设计根据工件的定位要求,设计夹具的定位系统。
夹具的定位系统应能够满足工件的精度要求,并确保工件的位置准确。
定位系统常采用定位销、定位块等形式,根据工件的形状和加工特点选择合适的定位方式。
步骤6:夹具操作系统设计根据夹具的使用要求,设计夹具的操作系统。
夹具的操作系统主要包括夹紧装置的控制方式和操作机构的设计。
根据夹紧力的大小和控制精度的要求,选择合适的液压夹紧系统或气动夹紧系统。
步骤7:夹具零件设计根据夹具的基础结构、定位系统和操作系统的设计要求,设计夹具的各个零件。
数控铣床工装夹具设计与改进策略
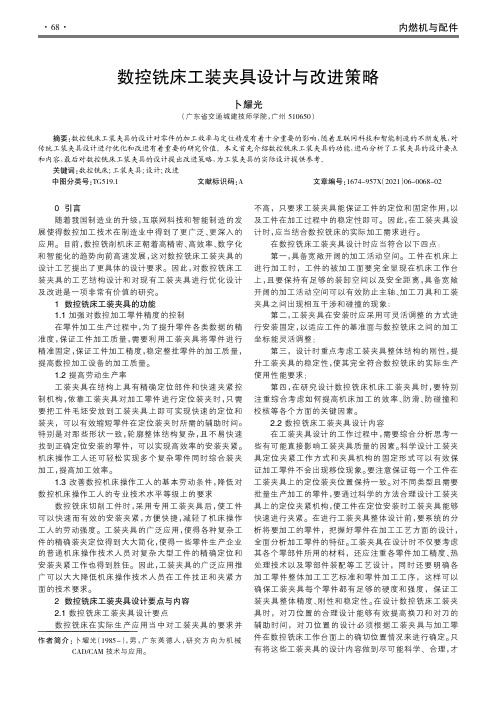
内燃机与配件0引言随着我国制造业的升级,互联网科技和智能制造的发展使得数控加工技术在制造业中得到了更广泛、更深入的应用。
目前,数控铣削机床正朝着高精密、高效率、数字化和智能化的趋势向前高速发展,这对数控铣床工装夹具的设计工艺提出了更具体的设计要求。
因此,对数控铣床工装夹具的工艺结构设计和对现有工装夹具进行优化设计及改进是一项非常有价值的研究。
1数控铣床工装夹具的功能1.1加强对数控加工零件精度的控制在零件加工生产过程中,为了提升零件各类数据的精准度,保证工件加工质量,需要利用工装夹具将零件进行精准固定,保证工件加工精度,稳定整批零件的加工质量,提高数控加工设备的加工质量。
1.2提高劳动生产率工装夹具在结构上具有精确定位部件和快速夹紧控制机构,依靠工装夹具对加工零件进行定位装夹时,只需要把工件毛坯安放到工装夹具上即可实现快速的定位和装夹,可以有效缩短零件在定位装夹时所需的辅助时间。
特别是对那些形状一致,轮廓整体结构复杂,且不易快速找到正确定位安装的零件,可以实现高效率的安装夹紧。
机床操作工人还可轻松实现多个复杂零件同时综合装夹加工,提高加工效率。
1.3改善数控机床操作工人的基本劳动条件,降低对数控机床操作工人的专业技术水平等级上的要求数控铣床切削工件时,采用专用工装夹具后,使工件可以快速而有效的安装夹紧,方便快捷,减轻了机床操作工人的劳动强度。
工装夹具的广泛应用,使得各种复杂工件的精确装夹定位得到大大简化,使得一些零件生产企业的普通机床操作技术人员对复杂大型工件的精确定位和安装夹紧工作也得到胜任。
因此,工装夹具的广泛应用推广可以大大降低机床操作技术人员在工件找正和夹紧方面的技术要求。
2数控铣床工装夹具设计要点与内容2.1数控铣床工装夹具设计要点数控铣床在实际生产应用当中对工装夹具的要求并不高,只要求工装夹具能保证工件的定位和固定作用,以及工件在加工过程中的稳定性即可。
因此,在工装夹具设计时,应当结合数控铣床的实际加工需求进行。
铣床夹具的设计及特点

使用定 向键 、 对刀装置 ; 夹具体要有足够的刚度和稳定性, 结构
要合理 。 4 1 定 向键 : 向键 也 称定 位 键 , . 定 安装 在 夹具 底 面的 纵 向 槽 中 , 般 用 两 个 , 在一 条 直 线 上 , 距离 越 远 , 向 精 度 越 一 安 其 导 高 , 螺钉 紧 固在 夹具 体 上 。 用
工件 在数 控 铣床 上进 行铣 加工 。 () 2 专用 铣切 夹具 是 特别 为 某一 项 或类 似 的几 项 工件 设 计 制造 的夹 具 , 一般 在批 量 生产 或研 制 时非要 不 可时 采用 。 也便 于一 面 加工 , 面装 卸 工件 , 利 于缩 短 准 备 时 间 , 高 生 一 有 提 产率 , 适宜 于 中批量 生产 。 较 () 4 气动 或液 压夹 具 适 用 于 生产 批 量 较 大 , 用 其 他 夹 具 采 又特 别 费工 、 费力 的工 件 。能减 轻 工劳 动强 度 和提 高生产 率 , 但 此类 夹具 结 构较 复杂 , 造价 往 往较 高 , 而且 制造 周期 较 长 。 () 5 真空 夹具 适 用 于有 较大 定 位平 面或 具 有较 大 可 密封 面
用塞 尺对 刀 , 妨 碍工 件装 卸 。对刀 时 , 刀具 与对 刀块 之 间加 不 在 一塞 尺 , 免 刀具 与对 刀 块直 接 接触 而 损 坏刀 刃 或造 成 对 刀块 避 过早 磨损 。塞 尺 有平 塞尺 和 圆柱 形 塞 尺两 种 , 厚 度和 直 径 为 其 阅相 关手 册 ) 使 用时 , 具 总 图上 应标 明 塞尺 尺 寸及 对 刀 块工 , 夹 作表 面与 定位 元 件之 间 的位置 。对 刀装置 应设 置在便 于对 刀而 且是 工件 切入 的 一端 。 4 3 夹 具 体 设 计 : 提 高铣 床 夹 具 在机 床 上 安 装 的稳 固 . 为 性 , 轻其 断 续切 削 可能 引起 的振 动 , 减 夹具 体不 仅要 有足够 的 刚 度和 强度 , 高度 和宽 度 比也 应 恰 当 , 其 一般 有 H B i 1 2 , / ≤ ~ .5
铣床夹具设计说明书【操作指南】
以下为铣床夹具课程设计说明书,一起来了解一下吧。
目录前言错误!未定义书签。
第1章设计准备工作31.1熟悉加工零件图 31.2加工零件图分析 2第2章结构方案设计 52.1 定位方案设计 52.1.1确定定位方案 52.1.2 选择定位元件,设计定位装置 52.2 夹紧方案设计 62.2.1 确定夹紧方案 62.2.2 夹紧装置设计 62.3 夹具体设计8第3章夹具装配图的绘制 103.1 夹具总装图上应标注的尺寸及公差103.2 夹具总装图应标注的技术条件10第4章误差设计 (12)4.1 误差分析 (12)4.1.1定位误差 (12)4.1.2产生定位误差的原因 (12)4.2定位误差的计算 (12)谢辞16前言由机械加工生产实践可以知道,任何机械加工都不能离开夹具。
不论是使用通用夹具,还是使用专用夹具,总是需要先将工件定位夹紧后,才能进行加工。
所以,夹具是现代机械加工行业中不可缺少的的重要工艺装备之一。
使用夹具可以提高工件的加工精度并保证零件的互换性,提高劳动生产率,同时可以降低劳动强度,改善工人的劳动条件。
使用夹具还可以扩大现有机床的应用范围,充分利用现有的设备资源。
先进的夹具技术,可以获得巨大的经济效果。
夹具的种类很多。
其中,使用范围最广泛的是通用夹具,如车床上用的三爪卡盘和铣床上用的平口虎钳等,这类夹具的规格尺寸已标准化。
由于专用夹具的设计制造在很大程度上影响加工质量、生产效率、劳动条件和生产成本,因此,它是各机械制造厂新产品投资、老产品改进和工艺更新中的一项重要生产技术准备工作,也是每一个从事机械加工工艺的技术人员必须掌握的基础知识。
机床夹具分析夹具的组成夹具的使用对象虽不相同,夹具的结构和功用也不大一样,但是从不同的夹具结构中可以概括出一般夹具所共有的结构组成。
归纳起来,夹具可视为既独立又相互联系的六部分组成。
定位装置是由定位元件组合而成的,其主要作用是确定工件在夹具中的确定位置。
铣床夹具设计[摘要]
前言机械制造工艺学课程设计使我们学完了大学的全部基础课、技术基础课以及大部分专业课之后进行的.这是我们在进行毕业设计之前对所学各课程的一次深入的综合性的总复习,也是一次理论联系实际的训练,因此,它在我们四年的大学生活中占有重要的地位。
在机械制造的机械加工、检验、装配、焊接和热处理等冷热工艺工程中,使用着大量的夹具。
而机床夹具是在机床上用以准确、迅速地安装工件或刀具,从而保证工件与刀具间正确相对位置的一种工艺装备。
一台结构相同、要求相同的机器,或者具有相同要求的机器零件,均可以采用几种不同的工艺过程完成,但其中总有一种工艺过程在某一特定条件下是最合理的。
人们把合理工艺过程的有关内容写成工艺文件的形式,用以知道生产,这些工艺文件即称为工艺规程。
经审定批准的工艺规程是指导生产的重要文件,生产人员必须严格执行。
在机床上加工工件是,为了保证加工精度,必须正确安置工件,使其相对机床切削成形运动和刀具占有正确的位置,这一过程称之为“定位”。
为了不因受切削力、惯性力、重力等外力作用而破坏工件已定的正确位置,还必须对其施加一定的夹紧力,这一过程称之为“夹紧”。
定位和夹紧全过程称为“安装”。
在机床上用来完成工件安装任务的重要工艺装备,就是各类夹具中应用最为广泛的“机床夹具”。
由于能力所限,设计尚有许多不足之处,恳请各位老师给予指导。
目录前言一、零件分析 (3)二、加工工艺设计 (4)1.毛坯的选择2.基准的选择3.工件表面加工方法的选择4.制定工艺路线5.工艺方案的比较和分析6.选择加工设备及工艺装备7.确定切削用量及基本工时8.填写机械加工工艺过程卡和机械加工工序卡三、铣床夹具设计 (12)结束语 (19)参考文献 (20)一、零件分析1、零件的作用题目中的零件为转向拨叉,他是通过扳手扣住左端的方形块,将导向杠杆装入Φ6 mm的孔内,搬动扳手,控制杠杆在机器中的位置,调整好位置后,用M10的螺母将其固定,同而能达到紧固的作用。
数控铣床工装夹具设计与改进建议
数控铣床工装夹具设计与改进建议随着工业智能化的不断推进,数控铣床的应用越来越广泛。
而工装夹具作为数控铣床的重要配套设备,扮演着关键的角色。
本文将围绕数控铣床工装夹具的设计与改进提出相关建议。
对于数控铣床工装夹具的设计,应注重以下几个方面:1. 材料选用:选用高强度、耐磨、耐高温、耐腐蚀的材料,以提高工装夹具的寿命和使用效果。
2. 结构设计:结构应简洁明了,便于安装和拆卸,减少操作的时间和难度。
应考虑夹具的刚性和稳定性,以保证加工精度和稳定性。
3. 夹具定位精度:精确的夹具定位是保证加工精度的关键。
应通过合理设计夹具定位结构,减小夹具的运动误差,提高夹具的定位精度。
4. 夹持力控制:夹具的夹持力也是影响加工质量的关键因素,应通过合理设计夹具夹持结构,保证夹持力的均匀分布和稳定控制。
应根据加工对象的材料特性和加工要求,确定夹持力的大小。
1. 自动化改进:将现有的手动夹具改进为自动夹具,减少人力操作,提高工作效率和质量。
可以借助传感器和控制系统实现夹具自动定位和夹持力的自动调节。
2. 模块化设计:将工装夹具设计为模块化结构,可以根据加工需求将不同功能的模块组合使用,提高工装夹具的灵活性和多功能性。
3. 抗振性改进:在夹具的设计中加入抗振性措施,减小振动对加工精度的影响。
可以采用减震材料、抗振支撑结构等方式来改善夹具的抗振性能。
4. 自适应调节:根据不同的加工对象和加工要求,夹具能够自适应地做出相应的调节,提高加工的适应性和灵活性。
最后需要强调的是,数控铣床工装夹具的设计与改进需要与实际加工需求相结合,充分考虑加工对象的特点和加工要求,合理选择夹具的类型和结构,以提高加工效率和加工质量。
还需不断关注新材料、新技术的发展,时刻保持创新思维,以推动工装夹具的设计与改进。
第八章 铣床夹具
? 5.用圆形转台安装 ? 当铣削一些有弧形表
面的工件,可通过圆 形转台安装
.
(二)铣床夹具的类型
? 夹具安装在工作台上 ? 工件随工作台作进给运动 ? 根据工件的进给方式,夹具分为两种类型: ? 1.直线进给式夹具 ? 2.圆周进给式夹具
.
专用铣床夹具分析
? 定位元件 ? 夹紧元件
?对刀元件 ?连接元件
.
U型耳座
对刀块
.
4.对刀块及对刀尺寸
对刀块
.
.
.
2.双件铣键槽专用夹具
.
.
小结铣床专用夹具的一般特点
? 连接元件定位键 ? 对刀块和塞尺
.
.
3mm 铣刀 塞尺
工件
? 对刀块
加工尺寸的公差 为0.4mm
50±0.2
若塞尺尺寸为 3mm
则对刀基本尺寸=50-3=37 对刀公差取加工公差的1/4,即为0.1mm 标为对称偏差的形式:37±0.05mm
.
定位面
: 小结
? 定位键与工作台T型槽可用单面贴合,当定位 精度要求高或是重型夹具,可在夹具体的侧面 设置一个找正基面;
.
对刀块使用图例
.
2)塞尺:平塞尺、圆塞尺
? 使用对刀装置对刀时, 在刀具和对刀块之间用 塞尺进行调整,以免损 坏切削刃或造成对刀块 过早磨损。
厚度:1,3,5mm
厚度:Φ3,. Φ5mm
对刀块的位置尺寸
? 总装图上要标注的尺寸 ? 对刀块通常制成单独元件,用螺钉和定位销定
位在夹具体上,其位置应便于使用塞尺对刀和 不妨碍工件的装卸。对刀块工作表面的位置尺 寸(H、L),一般是从定位表面注起 ? 其数值应等于工件相应尺寸的平均值再减去或 加上塞尺的厚度S。其公差常取工件相应尺寸 公差的1/3~1/5。
- 1、下载文档前请自行甄别文档内容的完整性,平台不提供额外的编辑、内容补充、找答案等附加服务。
- 2、"仅部分预览"的文档,不可在线预览部分如存在完整性等问题,可反馈申请退款(可完整预览的文档不适用该条件!)。
- 3、如文档侵犯您的权益,请联系客服反馈,我们会尽快为您处理(人工客服工作时间:9:00-18:30)。
铣床夹具设计地方及周边地区的快速发展需要越来越多的实用型应用型人才。
高等职业教育根据“必须、够用”原则培养出一大批能把科学发现转化应用技术,把产品设计转化为工艺流程,把宏观决策转化为微观管理的技术型和管理型的人才。
正是在这种背景下,我们为全面提升自身的知识结构、能力结构和素质结构进行此次毕业设计。
毕业设计是继专业基础课程如机械制造工艺学、工程力学、机械设计、差与技术测量、夹具设计等之后,并在一定生产实习的基础上进行的一个教学环节,要求我们综合运用所学知识,根据零件的结构特点和产品的加工要求,进行加工工艺规程和夹具的设计。
机床夹具是保证机械产品质量高、数量多、成本的一种极重要的工艺装备。
其主要作用是:可靠地保证工件的加工质量,提高加工效率,减轻劳动强度,充分发挥和扩大机床的工艺性能。
机床夹具设计是工艺装备设计的重要组成部分。
一个好的设计,应能稳定地保证工件的加工质量,生产效率高,成本低,排屑方便,操作安全、省力,制造、维护容易等其衡量指标。
本人设计的课题是气缸体工艺及其液压夹紧铣床夹具设计。
原始数据及设计要求见设计任务书。
通过本次毕业设计,我能够综合的运用机械制造工艺学中的基本知识和理论,结合生产实习中的实践知识,独立地分析和解决工艺问题,已初步具备设计一定复杂程度的零件的工艺规程能力和运用夹具设计的基本原理和方法.拟订夹具设计方案,完成夹具结构设计的能力,并熟悉和运用相关手册、图表等技术资料及编写技术文件等技能的一次综合训练的机会,为今后从事的工作打下良好的基础。
作为一名高职院校的学生,我深知自己知识、能力和经验的不足,正是这种不足让我在今后的工作中更加谦虚谨慎、脚踏实地、不断进步,敬请各位老师多多指教。
第一章零件的工艺分析该气动缸体只有一个加工表面(上表面,以∮80的孔为中心)平面的技术要求只要是对平面度,表面粗糙度的要求0.05。
1.1平面度分析平面度是指平面的平整程度,符号表示本零件的顶面和基准面的平面度误差在整个平面内最大不允许超过0.05mm ,即平面度公差为0.05mm。
1.2 表面粗糙度表面粗糙度是指加工表面上具有较小间距和峰谷所组成的微观几何形状特性该零件粗糙度要求为4。
第二章毛坯的制造形式毛坯的选择对零件工艺过程的经济性有很大影响,工序数量,材料消耗加工工时等都取决于所选择的毛坯,但要提高毛坯的质量往往会使毛坯制造困难,需要复杂的工艺和昂贵的设备,增加了毛坯的成本,这两者是矛盾的。
因此毛坯的种类和制造方法的选择要根据毛坯的类型和具体的生产条件决定。
同时应该注意到,充分使用新工艺、新技术、新材料的可能性,以便降低零件生产总成本提高质量。
零件材料为HT200,其表面形状比较复杂,内腔也较复杂,因此选择铸造的方法获得毛坯,铸型用的材料来源广泛,价格低廉,铸件可部分用废零件或废金属料熔炼而成。
此外,铸件的形状尺寸与零件很接近,因而节约了大量金属材料和加工工时,同时铸件抗压强度高,抗振性好,易于加工但生产周期长,需要进行时效处理,以消除内应力。
据以上分析,采用铸造的方法获得毛坯是比较合理的。
第三章铣削方式的选择3.1 端面铣端面铣削是指用铣刀端面齿刃进行的铣削,是利用分布在铣刀端面上的刀尖来加工平面的,在铣床上铣削平面,尤其是较宽,较大的平面和大平面,大都采用端面铣削的方法加工,用端面铣削的方法铣出的平面,其平面度主要取决于铣床主轴轴线与进给方向的垂直度,若主轴与进给方向垂直,则刀尖旋转时的轨迹为一个与进给平行我圆环,这个圆环割出一个平面,此时,铣刀刀尖在工件表面铣出网状的刀纹。
若铣床主轴与进给方向不垂直,则相当于一个倾斜的圆环,把工件切出一个凹面,此时,工件表面将形成单向胡形刀纹,在铣削过程中,若进给方向是从刀尖高的一边移向低的一边时,则会产生“拖刀”现象,反之则无“拖刀”现象3.2周边铣削周边铣削是指用铣刀周边齿刃进行的铣削是指利用分布在铣刀圆柱面上的刀刃来铣削并形成平面,所以周边铣削适用于加工不太宽和较窄的平面,也适用于周边铣削加工,对宽度大于120mm的平面,就不太合适,除特殊情况外最好采用端面铣削,用周边铣削的方法铣出的平面,其平面度主要取决于铣刀饿圆柱度,因为用周边铣削方法铣出的平面,相当于工件在圆柱下做直线运动时被辗出一个平面,是用圆柱铣刀铣削平面的情况,精削时要保证铣刀的圆柱度。
3.3 端面铣削和周边铣削的比较端面铣削时,由于端铣刀杆短,刚性好,刀片装夹方便,尤其是可转位铣刀,适用于进行高速铣削移动铣削,能显著提高生产率和减少表面粗糙度值。
端铣刀的直径最大可达1m左右,能一次铣出较宽的表面,同时工作的刀齿比较多,故震动小而平稳,效率也高。
端铣刀的刃磨没有圆柱形铣刀要求严格,在一把端铣刀上,若各个刀齿刃磨的高低不齐,半径方向也出入不等,但对铣出平面的平面度是没有影响的,只对铣削时平稳性和表面粗糙度值有影响。
用端面铣削获得的平面只可能是凹面,从使用情况看大都只允许凹不允许凸;而用周边铣削获得平面,则凸和凹都可能产生,因此用端面铣削平面比较合理。
对于铣削用量相同,并在端铣刀上不采用修光刀刃等措施的情况下,用周边铣削加工出的表面粗糙度值小。
用周边铣削时,能一次切除较大的铣削层深度(吃刀量)据以上分析与比较本工件采用端面铣削的方法。
3.4端面铣削时的顺铣与逆铣端面铣削时,根据铣刀与工件之间的相对位置不同而分为对称对称铣削和非对称铣削。
3.5对称铣削工件处在铣刀中间时的铣削称为对称铣削,铣削时,刀齿在工件的前半部分为逆铣,在进给方向的铣削分力 Ff与进给方向相反。
刀齿在工件的后半部分为顺铣,与进给方向相同。
对称铣时,在铣削层宽度较窄和铣刀齿数少的情况下,由于Ff 在进给方向上的交替变化,使工件和工作台容易产生窜动。
另外,在横向的水平分力Ff 较大,对窄长的工件易造成变形和弯曲,所以只有在工件宽度接近铣刀直径时才采用对称铣削。
3.6非对称铣削工件的铣削层宽度偏向铣刀一边时的铣削称为非对称铣削,即铣刀中心与铣削层宽度的对称线处在偏心状态下的铣削,非对称铣削时有顺铣和逆铣两种。
非对称逆铣铣削时,逆铣部分占的比例大,在各个刀齿上的F 之和与进给方向相反,所以不会拉动工作台。
端面铣削时刀刃切入工件虽由薄到厚,但不等于从零开始,因而没有因而没有像周边铣削时那样的缺点,从薄处切入刀齿的冲击反而较小,故振动较小,另外工件所受的垂直铣削力Ff 又于铣削方式无关,因此在端面铣削时,应采用非对称逆铣。
非对称顺铣,铣削时,顺铣部分占的比例大,为在各个刀齿上的Fv 之和,与进给方向相同,故易拉动工作台。
在铣削塑性和韧性好,加工硬化严重的(如不锈钢和耐热刚等)材料时,采用不对称顺铣,以减少切削粘附和提高刀具寿命,此时必须调整好丝赶副的传动间隙。
经上述端铣时顺铣与逆铣的对比与分析,在端面铣削时采用非对称逆铣。
第四章刀具的选择4.1基本要求铣刀切削部分的常用材料应满足以下基本要求:4.1.1硬度在常温下,刀具切削部分必须具有足够的硬度才能切入工件,由于在切削过程中会会产生大量的热量,因而要求刀具材料在高温下仍能保持其硬度,并继续进行切削。
4.1.2韧性和强度高的强度和好的韧性在切削过程中,刀具要承受很大的冲击力,所以刀具眼材料要具有较高的强度,否则易断裂和损坏。
由于铣刀受到冲击和振动,因此铣刀条件还具备好的韧性,才不易崩刃,碎裂。
4.1.3铣刀切削部分的材料的要求刀具的切削的切削部分不但要承受切削过程中的高温,高压及冲击载荷,而且还要受到切削中工件的强烈摩擦,因此,作为刀具切削部分的材料必须具备较高的硬度,韧性,此外,还需有良好的冷热加工性能。
4.2常用材料具有上述性能的材料很多,常用的铣刀材料有高速工具钢和硬质合金两种。
4.2.1高速工具钢(高速钢和锋钢等)有通用高速钢和特殊用途高速钢两种,通用高速钢是指加工一般金属材料用的高速钢,其牌号有W18Cr4V.W6Mo5Cr4V等。
W18Cr4V是钨高速钢,具有较好的综合性能,常温时该材料硬度为HRC62~65,在600℃高温时,硬度约为HRC51,抗弯强度约为3500MPa,磨削性能好。
所以各种通用铣刀都采用这种牌号的高速钢材料制造。
W6Mo5Cr4V是钨钢系高速钢,它的抗弯强度、冲击韧性和热塑性均比W18Cr4V 好,而磨削性能稍比W18Cr4V差,而其他情况基本相同。
用于其热塑性和韧性较好故常用于制造成形刀具和承受冲击力较大的铣刀。
特殊用途高速钢是通过改革高速钢的化学成分来改变其切削性能而发展起来的。
它的常温硬度和高温硬度比才常用高速钢高,这种材料的刀具主要用于加工耐热钢,不锈钢,高温或超强度材料等难加工材料。
近年来,我们研究成功了许多新型高速钢。
用于制造铣刀的新型高速钢牌号为 W6Mo5Cr4V2Al,C50(钢)和W6Mo5Cr4V5SiN6Al20钢等。
高速钢具有以下特点:1)合金元素如W(钨),Cr(铬),Mo,V等的含量较高,淬火硬度可达62~70,在600℃高温下,仍能保持较高的硬度2)刃口强度和韧性好,抗振性强,能用于制造切削速度较低的刀具,即使刚性较差的机床,采用高速钢铣刀仍能顺利切削。
3)工艺性能好,锻造焊接、切削加工和刃磨都比较容易,还可以制造形状复杂的刀具。
4)与硬质合金材料相比,能有硬度较低,热硬性和耐磨性较差等特点。
4.2.2硬质合金硬质合金是以金属碳化物化WC(碳化钨)、TiC(碳化钛)和以Co(钴)粘接剂粉末冶金工艺制造而成,其主要特点如下:1).耐高温。
在800~1000度左右仍能保持良好的切削性能切削时可选用比高速钢高4~8倍的切削速度。
2).常温硬度高,耐磨性好。
3).抗弯性低,冲击刃度差,切削刃不易刃磨的很锋利。
为了节省高速刚,直径较大而不太薄的铣刀大多作成镶齿刀,为提高生产效率和铣刀寿命;成型铣刀很多采用涂层刀齿。
经上分析,比较后决定采用高速钢镶齿三面刃铣刀。
根据图样给定的平面宽度尺寸现选用外径为200mm,Z=20的镶齿三面刃铣刀。
第五章铣削用量在铣削过程中所选用的铣削用量称为铣削用量,铣削用量包括铣削层宽度,铣削层深度,铣削速度和进给量,铣削用量的选择,对提高生产效率,改善工件表面粗糙度和加工精度都有密切的关系。
选择铣削用量,是在保证铣削加工质量和工艺系统刚性所允许的前提下进行的,首先应选用较大的每齿进给量,最后确定铣削速度。
铣削层深度选择铣削层深度主要根据工件的加工余量和加工表明的精度来确定,当加工余量不大时,应尽量一次进给铣去全部加工余量,只有当工件的加工精度要求较高或加工表面粗糙度小于Ra6.3时,才分粗精铣两次进给。
因本工件为铸铁,所选刀具为高速钢铣刀,现选取粗铣时的铣削层深度为5~7mm,精铣铣削层深度为0.5~1mm。
5.1每齿进给量的选择粗铣时,限制进给量提高的主要因素是切削力,进给量主要根据铣床进给机构的强度,刀轴尺寸,刀齿强度以及机床夹具等工艺系统的刚性来确定,在强度,刚度许可的条件下,进给量应尽量选的大些。