精馏塔机械设计方案
化工原理课程设计任务书-精馏塔

板式精馏塔的设计指导书一、设计内容1.设计方案的确定(设计方案简介:对给定或选定的工艺流程、主要设备的形式进行简要的论述。
)(1)操作压力 (2)进料状态 (3)加热方式 (4)热能利用2.主要设备的工艺设计计算(1)物料衡算; (2)热量衡;(3)回流比的确定;(4)工艺参数的选定;(5)理论塔板数的确定3.塔板及塔的主要尺寸的设计(设备的结构设计和工艺尺寸的设计计算。
)(1)塔板间距的确定(2) 塔径的确定(3) 塔板布置及板上流体流程的确定4. 流体力学的计算及有关水力性质的校核5. 板式精馏塔辅助设备的选型:典型辅助设备主要工艺尺寸的计算,设备的规格、型号的选定。
6.绘制流程图及精馏塔的装配图: 工艺流程图:以单线图的形式绘制,标出主体设备与辅助设备的物料方向,物流量、能流量,主要测量点。
主要设备的工艺条件图:主体设备工艺条件图是将设备的结构设计和工艺尺寸的计算结果用一张总图表示出来。
图面上应包括如下内容:①设备图形:指主要尺寸(外形尺寸、结构尺寸、连接尺寸)、接管、人孔等;②.技术特性:指装置的用途、生产能力、最大允许压强、最高介质温度、介质的毒性和爆炸危险性;③.设备组成一览表:注明组成设备的各部件的名称等。
应予以指出,以上设计全过程统称为设备的工艺设计。
完整的设备设计,应在上述工艺设计基础上再进行机械强度设计,最后提供可供加工制造的施工图7.编写设计说明书:设计说明书的内容:①目录;②设计题目及原始数据(任务书);③简述酒精精馏过程的生产方法及特点(设计方案简介),④论述精馏总体结构(塔型、主要结构)的选择和材料选择;⑤精馏过程有关计算(物料衡算、热量衡算、理论塔板数、回流比、塔高、塔径塔板设计、进出管径等) (工艺计算及主要设备设计);⑥设计结果概要(设计结果汇总):主要设备尺寸、衡算结果等;⑦主体设备设计计算及说明;⑧主要零件的强度计算(选做);⑨附属设备的选择(辅助设备的计算和选型,选做);⑩参考文献;(11)设计评述(后记)及其它.整个设计由论述,计算和图表三个部分组成,论述应该条理清晰,观点明确;计算要求方法正确,误差小于设计要求,计算公式和所有数据必需注明出处;图表应能简要表达计算的结果。
板式精馏塔的设计

密封件的设计需要考虑到密封性能、耐高温和耐腐蚀性等因素。在实际设计 中,一般选用机械密封或填料密封等形式,并需要对密封件的材料和制造工艺进 行严格筛选和考核。 4.3支架设计支架是板式精馏塔的支撑部件,主要作用是固 定板片和密封件等元件。支架的设计需要考虑到设备的强度、稳定性和操作方便 性等因素。
2.3数据采集为了进பைடு நூலகம்板式精馏塔的设计,需要采集物料的物性参数、操作 条件以及类似设备的运行数据等。
2.4设计参数计算根据采集的数据和流程规划,计算板式精馏塔的主要参数, 包括塔高、塔径、板数、间距、流体力学等。
2.5辅助设计进行辅助设计,包括塔内件的材料选择、制造工艺、结构设计 等,确保塔体和内部构件的稳定性和耐用性。
传感器设计需要考虑到测量的准确性、稳定性和可靠性等因素。在实际设计 中,一般选用电感式、电容式、光电式等传感器形式,并需要对传感器的位置和 数量进行合理布置和选择。 5.
感谢观看
2、基本设计流程板式精馏塔的设计流程包括以下几个方面:
2.1设计目标确定首先需要明确板式精馏塔的设计目标,包括分离的物料种 类、分离的纯度、处理能力、操作压力和温度等。
2.2流程规划根据设计目标,确定板式精馏塔的流程。流程规划包括物料的 预处理、进料方式、操作模式、加热和冷却方式以及塔内件的结构设计等。
板式精馏塔的设计
基本内容
板式精馏塔是一种广泛应用于化工、石油、食品和医药等行业的蒸馏设备。 它通过将液体混合物进行多次汽化和冷凝,从而将不同沸点的组分分离出来。本 次演示将详细介绍板式精馏塔的设计流程、塔体设计、传质元件设计、控制系统 设计以及数据分析与结果呈现。
1、引言板式精馏塔是一种高效的分离设备,通过多次汽化和冷凝将液体混 合物分离成不同沸点的组分。在化工、石油、食品和医药等行业,板式精馏塔被 广泛应用于原料的预处理、产品的提纯和分离以及废液的处理等。因此,板式精 馏塔的设计对于工业生产过程的经济性和效率具有重要意义。
化工原理课程设计(化工机械设计部分)精馏塔

化工机械设计部分设计条件:设计压力0.1Mpa ,工作温度130℃,设计温度150℃,介质名称为苯—氯苯,介质密度为973㎏/3m ,基本风压300N/㎡[1],地震烈度为8,场地类别Ⅱ,塔板数量22,塔高26m ,保温层材料厚度为100mm ,保温层密度为300㎏/3m一 塔体及封头厚度设计1壳体材料选取 该塔工作温度为130℃,设计压力为0.12Mpa ,塔体内径3400mm ,塔高21米。
介质苯-氯苯有轻微的腐蚀性,选用强度较好的16MnR ,16MnR 在设计温度下的许用应力[]t σ=170Mpa ,Rel=345Mpa ,腐蚀裕量2C =2mm ,采用双面对接焊缝,局部无损探伤,焊接系数为Φ=1.02塔体厚度计算计算压力:0.12c p MPa = 2C mm = []170tMPa σ= D=4600mm 1.0φ=圆筒的计算厚度:[]0.1246001.35217010.12c i tcp D mm p δσφ⨯===⨯⨯--设计厚度:2 1.352 3.35d C mm δδ=+=+=考虑到其受到风载荷、地震载荷、偏心载荷和介质压力作用,取名义厚度:8n mm δ= 有效厚度:.8 2.8 5.2e n C mm δδ=-=-=3封头厚度计算 (封头采用标准椭圆形封头,材料与筒体相同)计算压力:0.12c p MPa = 2C mm = []170tMPa σ= 4600i D mm = 1φ=封头厚度:[]0.146001.35217010.50.120.5c itcp D mm p δσφ⨯===⨯⨯-⨯-设计厚度:2 1.352 3.35d C mm δδ=+=+= 取名义厚度:8n mm δ=有效厚度:.8 2.8 5.2e n C mm δδ=-=-=二 塔设备质量载荷计算1 筒体、圆筒、封头、裙座的质量【8】 2附件的质量 3塔内构件的质量筛板塔塔盘单位质量265/N q kg m = 塔内构件的质量:22020.785 4.62265237534i m D Nq kg πN ==⨯⨯⨯=4 保温层的质量 5平台、扶梯的质量查得平台单位质量2150/P q kg m = 笼式扶梯单位质量40/F q kg m = 其中平台数3n =,笼式扶梯高度为26000mm 平台、扶梯的质量㎏()()222204002340210.785 4.6162 4.616150389754f p m q H D D q kg π⎡⎤⎡⎤=⨯++-⨯⨯=⨯+⨯+-⨯⨯=⎣⎦⎣⎦6操作时物料的质量 7水压试验质量 8 操作质量: 9 全塔最大质量m max =m 01+ m 02+ m 03+ m 04+ m a + m w =377326 10 全塔最小质量m min =m 01+0.2 m 02+ m 03+ m 04=43256kg计算前先对塔进行分段,以地面为0-0截面,裙座人孔为1-1截面,塔低封三塔的自振周期四 风载荷与风弯矩的计算【6】① 0-0截面风弯矩0031241213124123()()()2222w l l l lM P P l P l l P l l l -=+++++++++=91.00510(mm)N ⨯ ②1-1截面风弯矩2-2截面风弯矩五地震弯矩的计算第一振型脉动系数: 0.02 衰减指数:0.95 塔总高:26m 自振周期 T1=0.36场地特征周期:0.35g T =(表8-2) 地震影响系数最大值:max 0.24α=(表8-3) 地震影响系数:10.077α= H (0-0)=0mmH (1-1)=1000mm H (2-2)=7000mm底截面处地震弯矩:00810161.259.691035E M m gH N mm α-=⨯=⨯⋅ 1—1截面处地震弯矩:()113.5 2.5 3.58102.581.25101449.1710175E m g M H H h h N mm H α-=-⋅+=⨯⋅2—2截面处地震弯矩:1.1 偏心弯矩的计算不设置再沸器所以不考虑1.2 各种载荷引起的轴向应力1.2.1 计算压力引起的轴向应力 1.2.2 操作质量引起的轴向应力各截面操作质量: 0—0截面1—1截面 2—2截面 8634585437799891.2.3 最大弯矩引起的轴向应力最大弯矩:1.3 塔体和裙座危险截面强度与稳定性校核1.3.1 截面的最大组合轴向拉应力校核截面2-2,塔体的最大组合轴向拉应力发生在正常操作的2-2截面上,其中[]170tMpa σ=,[]t1.0, 1.2=1.21701=204pa K K M σΦ==Φ⨯⨯⎡⎤⎣⎦载荷组合系数,塔体的最大组合轴向啦应力发生在正常时的截面2-2上所以满足要求1.3.2 塔体与裙座稳定性校核塔体截面2-2上的最大组合轴向压应力 所以满足要求 其中0.0940.000212i eA R δ== 查图5-9得(16MnR ,200℃) E=1.86×510 []170tMpa σ=【6】 塔体1-1截面上的最大组合轴向压应力查图5-9得(Q235-B 150℃)E=2×510[]113tMpa σ= 塔体截面0-0上的最大组合轴向压应力1.4 塔体水压试验和吊装时的应力校核1.4.1 水压试验时各种载荷引起的应力液柱静压:1000260.26H g MPa γ=⨯=试验压力:[][]1.250.125T t p p MPa σσ==试验压力和液柱静压力引起的环向应力: 试验压力引起的轴向啦应力: 最大质量引起的轴向压应力 :弯矩引起的轴向应力1.4.2 水压试验时应力校核筒体环向应力校核0.9310.5s K MPa σ= 16MnR (345s MPa σ=)170.48310.5T MPa MPa σ=〈,满足要求 最大组合轴向拉应力校核22max 20.070.9310.5s MPa Mpa σσφ-=-〈=,满足要求最大组合轴向压应力校核1.5 基础环设计1.5.1 基础环尺寸裙座外径:4600164616os D mm =+= 基础环外径:046004005000b D mm =+=基础环内径:46004004200ib D mm =-=基础环伸出宽度:()()115000461619222ob os b D D mm =-=-=基础环面积:()22257776004obos b A D D mm π=-= 基础环截面系数:()448361.61032obos b obD D Z mm D π-==⨯1.5.2 基础环的动力校核所以取以上俩者较大的max 1.56MPa σ=。
新型复合式内部能量集成的精馏塔的机械设计与水力学模拟

新型复合式内部能量集成的精馏塔的机械设计与水力学模拟引言精馏技术广泛应用于化工、医药、精细化工等行业,投资和能耗较高。
内部热集成精馏塔(internally heat integrated distillation column,HIDiC)是一种新型精馏技术,它结合了热泵精馏和透热精馏节能的特点。
这种结构一方面将精馏段塔顶热端蒸气的余热充分利用回收;另一方面塔段间的透热使得各塔板的传质推动力平均化,实现逐板传热,提高了精馏塔的热力学效率。
因此该技术具有极大的节能效率,与常规蒸馏塔相比节省的能耗可达30%~60%,这是理论上最先进的精馏技术,受到了众多学者的关注。
随着CFD 理论的发展,研究人员开始利用CFD模拟的方法研究塔板的水力学特征。
相比实验,CFD 可以更加精确地描述塔板上的流动情况,可以预测塔板的板效率,Wang 等对隔板塔塔盘流场进行了水力学模拟,并与实验结果进行了对比,两者具有极大的相似性。
Rodríguez-Ángeles等通过对隔板塔的机械设计以及CFD 模拟,对隔板中筛板上的水力学参数进行了优化,提高了塔盘的传质效果。
较多的研究者对于HIDiC的研究只是停留在能量优化以及控制策略上,但对于与理想的HIDiC 理论相吻合的模型以及机械结构的设计和水力学模拟较少,本文基于以上问题,在HIDiC理论的基础上构建了新型的HIDiC 塔节,并用CFD 软件进行了水力学分析。
1 机械设计首先建立内部能量集成的精馏塔理论模型,如图1 所示,提馏段塔顶蒸气经压缩机加压升温后进入精馏段塔底部,精馏段塔底回流液经节流阀减压后回到提馏段塔顶部与原料混合。
两塔段间通过塔壁或换热板进行热量交换,精馏段蒸气在上升中冷凝,提馏段回流液在回流中蒸发,这样精馏段冷凝器和提馏段再沸器的热负荷会大幅减小。
图1 内部能量集成的精馏塔示意图Fig.1 Schematic diagram of internal heat integrated distillation columns 以苯和甲苯为分离物系,饱和液体进料,进料压力为常压。
乙苯-苯乙烯精馏塔设计

毕业设计题目年产10万吨苯乙烯工艺设计姓名所在系部化学工程专业班级有机化工指导老师前言本设计的内容为10万吨/年乙苯脱氢制苯乙烯装置,包括工艺设计,设备设计及平面布置图。
本设计的依据是采用低活性、高选择性催化剂,参照鲁姆斯(Lummus)公司生产苯乙烯的技术,以乙苯脱氢法生产苯乙烯。
苯乙烯单体生产工艺技术:深度减压,绝热乙苯脱氢工艺乙苯脱氢反应在绝热式固定床反应器中进行,其特点是:转化率高,可达55%,选择性好,可达90%。
特殊的脱氢反应器系统:在低压(深度真空下)下操作以达到最高的乙苯单程转化率和最高的苯乙烯选择性。
该系统是由蒸汽过热器、过热蒸汽输送管线和反应产物换热器组成,设计为热联合机械联合装置。
整个脱氢系统的压力降小,以维持压缩机入口尽可能高压,同时维持脱氢反应器尽可能低压,从而提高苯乙烯的选择性,同时不损失压缩能和投资费用。
所需要的催化剂用量和反应器体积较小,且催化剂不宜磨损,能在高温高压下操作,内部结构简单,选价便宜。
在苯乙烯蒸馏中采用一种专用的不含硫的苯乙烯阻聚剂。
它经济有效且能使苯乙烯焦油作为燃料清洁地燃烧。
工业设计的优化和设备的良好设计可使操作无故障,从而可减少生产波动.本设计装置主要由脱氢反应和精馏两个工序系统所组成。
原料来自乙苯生产装置或原料采购部门,循环水、冷冻水、电和蒸汽来由公用工程系统提供,生产出的苯乙烯产品到成品库。
此设计过程中,为了计算方便,忽略了一些计算过程,故有一定的误差,另由于计算时间比较仓促,有些问题不能够直接解决。
设计中有不少错误之处,请指导老师予以批评指正,多提出宝贵意见。
苯乙烯设计任务书一、设计题目:年产10万吨苯乙烯的生产工艺设计二、设计原始条件:2、操作条件:年工作日:300天,每天24小时,乙苯总转化率为55%乙苯损失量为纯乙苯投料量为4.66%配料比:原料烃/水蒸汽=1/2.6(质量比)温度T:第一反应器进口温度630℃,出口温度580℃第二反应器进口温度630℃,出口温度600℃压力P:床层平均操作压力1.5 * 105 Pa(绝)3、选择性:C8H10→C8H8+H2 (1)C8H10→C6H6+C2H4 (2)C8H10+H2→C7H8+CH4 (3)1、2、3(1)90%(2)3%(3)7%4、5、6(1)92%(2)3%(3)5%4、催化剂条件:(1)采用11#氧化铁催化剂,d=3mm,h=13mm (2)允许通入乙苯空速为:(0.5~0.9)Nm3乙苯/(m3Cat.h) (3)=1050kg/m3 =1500kg/m35、参考数据:(1)反应器直径D=2 m(2)取热损失为反应热为4%(3)k=exp(11.281-2545/RT)(4)K=exp(15.344-14656.5734/T)(5)Cat的有效系数η1=0.7 η2=0.667(6)填料情况:取瓷环为25×25的拉西环,所填高度为250mm,锥形高度为250mm,锥角取900(7)压力:第一反应器进口压力为1.8 * 105 Pa,出口压力为1.2 * 105 Pa,平均压力为1.5 * 105 Pa,压降ΔP=0.6 * 105 Pa。
精馏塔(板式)设计

PA α= ∗ PB
(三)塔板数的确定 1、作出x-y相图 、作出 相图 2、最小回流比及操作回流比 、 3、理论板数及加料位置 、 ①求精馏塔的汽、液相负荷 求精馏塔的汽、
∗
R = 1.5 Rmin
L′ = L + qF = RD + qF
V ′ = V + (q − 1) F = ( R + 1) D + (q − 1) F
化工原理课程设计
(6)冷凝器的选择 ) 塔顶产品(全凝器)和塔釜产品(冷却器) 塔顶产品(全凝器)和塔釜产品(冷却器) (7)加料方式的选择 ) 高位槽或泵 (8)工艺流程 ) 3、正戊烷和正己烷的性质、用途等 、正戊烷和正己烷的性质、
化工原理课程设计
二.工艺计算
主要内容是( 主要内容是(1)物料衡算 (2)确定回流比 (3)确定理论板数和实 际板数 (4)塔的气液负荷计算 (5)热量衡算 塔设备的生产能力一般以千克/小时或吨/年表示, 塔设备的生产能力一般以千克/小时或吨/年表示,但在理论板 计算时均须转换成kmol/h,在塔板设计时 在塔板设计时, 计算时均须转换成kmol/h,在塔板设计时,气液流量又须用体积 流量m /s表示 因此要注意不同的场合应使用不同的流量单位。 表示。 流量 m3/s 表示 。 因此要注意不同的场合应使用不同的流量单位 。 (一)全塔物料衡算 1、原料液及塔顶、塔底产品的摩尔分数 、原料液及塔顶、
化工原理课程设计
②求精馏段、提馏段的操作线方程 求精馏段、
R xD y= x+ R +1 R +1
③作图求出理论板数 ④逐板计算求理论板数
WxW L + qF y′ = x′ − L + qF − W L + qF − W
丙酮水连续精馏塔设计方案

丙酮水连续精馏塔设计方案第一章流程的确定及说明一.加料方式加料方式有两种:高位槽加料和泵直接加料。
采用高位槽加料,通过控制液位高度,可以得到稳定的流量和流速,通过重力加料,可以节省一笔动力费用,但由于多了高位槽,建设费用相应增加;采用泵加料,受泵的影响,流量不太稳定,流速也忽大忽小,从而影响了传质效率,但结构简单,安装方便。
如果采用自动控制泵来控制泵的流量和流速,其控制原理较复杂,且设备操作费用高。
本设计采用高位槽进料。
二.进料状况进料状况一般有冷液进料和泡点进料。
对于冷液进料,当组成一定时,流量一定,对分离有利,省加热费用,但其受环境影响较大;而泡点进料时进料温度受季节、气温变化和前段工序波动的影响,塔的操作比较容易控制。
此外,泡点进料时,基于恒摩尔流假定,精馏段和提镏段的塔径基本相等,无论是设计计算还是实际加工制造这样的精馏塔都比较容易。
综合考虑,设计上采用泡点进料。
三.塔顶冷凝方式塔顶冷凝采用全凝器,塔顶出来的气体温度不高,用水冷凝。
四.回流方式回流方式可分为重力回流和强制回流。
对于小塔型,回流冷凝器一般安装在塔顶,其优点是回流冷凝器无需支撑结构,其缺点是回流冷凝器回流控制较难。
如果需要较高的塔处理量或塔板数较多时,回流冷凝器不适合于塔顶安装,且塔顶冷凝器不易安装、检修和清理。
在此情况下,可采用强制回流,塔顶上升蒸汽量采用冷凝器以冷回流流入塔中。
本次设计为小型塔,故采用重力回流。
五.加热方式加热方式分为直接蒸汽加热和间接蒸汽加热,直接蒸汽加热时蒸汽直接由塔底进入塔内,由于重组分是水,故省略加热装置。
但在一定的回流比条件下塔底蒸汽对回流液有稀释作用,使理论塔板数增加,费用增加。
间接蒸汽加热时通过加热器使釜液部分汽化,维持原来的浓度,以减少理论板数,缺点是增加加热装置。
本次设计采用间接蒸汽加热。
六.加热器采用U型管蒸汽间接加热器,用水蒸气作加热剂。
因为塔较小,可将加热器放在塔内,即再沸器。
这样釜液部分汽化,维持了原有浓度,减少理论塔板数。
过程设备设计精馏塔毕业设计说明书
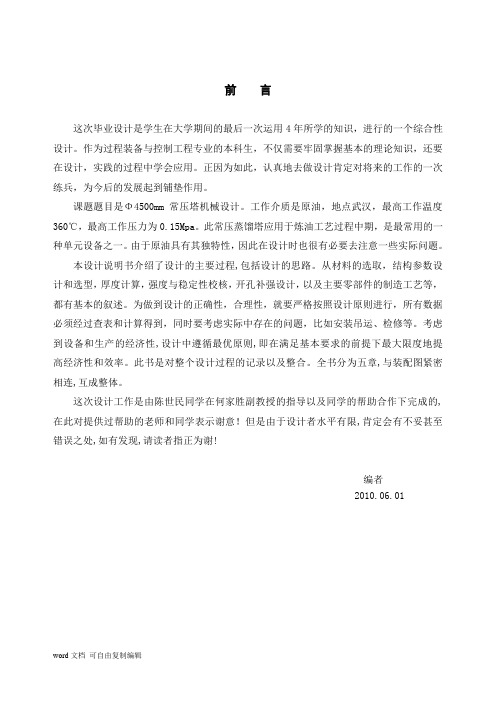
前言这次毕业设计是学生在大学期间的最后一次运用4年所学的知识,进行的一个综合性设计。
作为过程装备与控制工程专业的本科生,不仅需要牢固掌握基本的理论知识,还要在设计,实践的过程中学会应用。
正因为如此,认真地去做设计肯定对将来的工作的一次练兵,为今后的发展起到铺垫作用。
课题题目是Φ4500mm常压塔机械设计。
工作介质是原油,地点武汉,最高工作温度360℃,最高工作压力为0.15Mpa。
此常压蒸馏塔应用于炼油工艺过程中期,是最常用的一种单元设备之一。
由于原油具有其独特性,因此在设计时也很有必要去注意一些实际问题。
本设计说明书介绍了设计的主要过程,包括设计的思路。
从材料的选取,结构参数设计和选型,厚度计算,强度与稳定性校核,开孔补强设计,以及主要零部件的制造工艺等,都有基本的叙述。
为做到设计的正确性,合理性,就要严格按照设计原则进行,所有数据必须经过查表和计算得到,同时要考虑实际中存在的问题,比如安装吊运、检修等。
考虑到设备和生产的经济性,设计中遵循最优原则,即在满足基本要求的前提下最大限度地提高经济性和效率。
此书是对整个设计过程的记录以及整合。
全书分为五章,与装配图紧密相连,互成整体。
这次设计工作是由陈世民同学在何家胜副教授的指导以及同学的帮助合作下完成的,在此对提供过帮助的老师和同学表示谢意!但是由于设计者水平有限,肯定会有不妥甚至错误之处,如有发现,请读者指正为谢!编者2010.06.01摘要原油常压蒸馏作为原油加工的一次加工工艺,在原有加工流程中占有举足轻重的作用,其运行的好坏直接影响到整个原有加工的过程。
而在蒸馏加工的过程中最重要的分离设备就是常压塔。
因此,常压塔的设计好坏对能否获得高收益,搞品质的成品油油着直接的影响。
本次设计的常压塔是原油炼制工艺过程的中期塔设备。
设计时要考虑实际要求,遵循塔设备的设计原则,要经历需求分析、目标界定、总体结构设计、零部件结构设计、参数设计和设计实施这几个过程。
- 1、下载文档前请自行甄别文档内容的完整性,平台不提供额外的编辑、内容补充、找答案等附加服务。
- 2、"仅部分预览"的文档,不可在线预览部分如存在完整性等问题,可反馈申请退款(可完整预览的文档不适用该条件!)。
- 3、如文档侵犯您的权益,请联系客服反馈,我们会尽快为您处理(人工客服工作时间:9:00-18:30)。
精馏塔机械设计方案1.1 塔设备概论塔设备是化工、石油化工和炼油、医药、环境保护等工业部门的一种重要的单元操作设备。
它的作用是实现气(汽)——液相或液——液相之间充分的接触,从而达到相际间进行传质及传热的目的。
可在塔设备中完成的常见的单元操作有:精馏、吸收、解吸和萃取等。
此外,工业气体的冷却与回收、气体的湿法净制和干燥,以及兼有气液两相传质和传热的增湿、减湿等。
塔设备应用面广、量大,其设备投资费用占整个工艺设备费用较大的比例。
在化工或炼油厂中,塔设备的性能对整个装置的产品产量、质量、生产能力和消耗定额以及三废处理和环境保护等各个方面都有着重大影响。
因此,塔设备的设计和研究受到化工、炼油行业的极大重视。
为了使塔设备能更有效、更经济地运行,除了要求它满足特定的工艺条件外,还应满足以下要求:(1)气(汽)液两相充分接触,相际间的传热面积大;(2)生产能力大,即气液处理量大;(3)操作稳定,操作弹性大;(4)流体流动的阻力小,即流体通过塔设备的压力降小。
这将大大减少生产中的动力消耗,以降低操作的费用;(5)结构简单,制造、安装、维修方便,并且设备的投资及操作费用低;(6)耐腐蚀,不易堵塞。
方便操作、调节和检修。
塔设备的分类:(1)按操作压力可分有加压塔、常压塔以及减压塔;(2)按单元操作可分有精馏塔、吸收塔、介吸塔、萃取塔、反应塔、干燥塔等;(3)按件结构可分有填料塔、板式塔;(4)按形成相际接触界面的方式可分为具有固定相界面的塔和流动过程中形成相界面的塔。
1.2 常压塔的主要结构在塔设备的类别中,由于目前工业上应用最广泛的是填料塔以及板式塔,所以主要考虑这两种类别。
考虑到设计条件,成分复杂,并且板式塔和填料塔相比效率更高一些,更稳定,液——气比适用围大,持液量较大,安装、检修更容易,造价更低,故选用板式塔更为合理。
板式塔是一种逐级(板)接触的气液传质设备。
塔使用塔板作为基本构件,气体自塔底向上以鼓泡或喷射的形式穿过塔板上的液层,使气——液相密切接触而进行传质与传热,并且两相的组分浓度呈阶梯式变化。
塔盘采用浮阀型式。
因为浮阀塔在石油、化工、等工业部门应用最为广泛,并具备优异的综合性能,在设计和选用时经常作为首选的板式塔型式。
板式初馏塔的总体结构见装配草图。
板式塔除了各种件之外,主要由塔体、支座、人孔或手孔、除沫器、接管、吊柱及扶梯、操作平台组成。
(1) 塔体塔体即塔设备的外壳,常见的塔体由等直径、等厚度的圆筒和上下封头组成。
对于大型塔设备,为了节省材料偶尔采用不等直径、不等厚度的塔体。
塔设备一般情况下安装在室外,因而塔体除了承受一定的操作压力(压或外压)、温度外,还要考虑到风载荷、地震载荷、偏心载荷等。
此外还要满足在试压、运输及吊装时的强度、刚度及稳定性要求。
本设计中精馏塔为常压0.11MPa,采用等直径等厚度型式。
(2) 支座塔体支座是塔体安放到基础上的连接部分。
它必须保证塔体固定在稳定位置上进行正常的操作。
为此,它应当具备足够的强度和刚度,并且能承受各种操作情况下的全塔重量,以及风力、地震等引起的载荷。
最常用的塔体支座是裙式支座(简称为“裙座”)。
(3) 人孔及手孔人孔和手孔一般都是为了安装、检修检查和装填填料的需要而设置的。
在板式塔和填料塔中,各有不同的设置要求。
本精馏塔体设有人孔。
(3)接管塔设备的接管是用来连接工艺管路的,把塔设备与相关设备连成系统。
按接管的用途,分为进液管、出液管、进气管、出气管、回流管、侧线抽出管和仪表接管等。
本初馏塔的主要接管见草图。
(4) 吊柱安装于塔顶,为了在安装和检修时,方便塔件的运送。
2 精馏塔基本结构的设计2.1 设计条件已知给定设计条件如下:工作介质:EVA,塔径:1000mm工作参数:设计压力0.11MPa ,最高工作温度150℃开口及接管根据现场确定。
工作地点:地震基本烈度为7度,基本风压0.30KN/m 2。
2.2 塔高的确定(1) 塔的顶部封头高度顶部空间高度取mm h a 250=(2) 塔的主体高度主体高度:mm H 136501=(3) 椭圆形封头根据JB/T4746-2002 ,选用DN1000×8—Q345R 型号封头。
如图2-1。
EHA 椭圆形封头参数见表2-1。
图2-1 椭圆封头表2-1 EHA椭圆形封头参数公称直径DN /mm 总深度H/mm表面积A/mm2容积V/ mm3直边高度h/mm质量m/kg1000 250 1.16 0.151 40 72.1(4)裙座的高度裙座的高度是指从塔底封头切线到基础环之间的高度。
具体尺寸如下图2-2所示,裙座的全部高度是V和U相加和得到。
其中U是由工艺决定的,在此常压塔设计中可以取裙座总高为mmH50002图 2-2 裙座(5) 塔的总高度mm H H h H a 1890050001365025021=++=++=2.3 塔盘选型与设计2.3.1 塔盘型式及设计选用的是浮阀式塔盘,这类塔盘的塔盘板开有阀孔,安装了能在适当围上下浮动的阀片,其形状有圆形、条形、方形等。
由于浮阀与塔盘板之间的流通面积能随着气体负荷的变动而自动调节,因而在较宽的气体负荷围,均能保持着稳定操作。
气体在塔盘板上以水平方向催促,气液接触时间长,雾沫夹带量少,液面落差也小。
浮阀式具有生产能力大,操作弹性大,效率高,塔板结构及安装较泡罩简单且重量轻,制造费用低的优点。
浮阀塔F-型(国外通称V-型)是用钢板冲压而成的圆形阀片,浮阀塔F-型下面有三条阀腿,将三条阀腿装入塔板的阀孔之后,用工具将腿下的阀脚扭转90度,则浮阀就被限制在浮孔只能进行上下运动而不能脱离塔板。
当气速较大时,浮阀塔F-型浮阀被吹起,此时达到最大开度;当气速较小时,气体的动压头小于浮阀自身重量,于是浮阀塔F-型浮阀下落,浮阀周边上三个朝下倾斜的定距片与塔板接触,此时的开度最小。
定距片的作用是保证最小气速时还有一定的开度,使气体与浮阀塔F-型塔板上液体能均匀地鼓泡,避免浮阀与塔板粘住。
浮阀是浮阀塔的气液传质元件。
目前国应用最为广泛的是F1型浮阀。
F1型浮阀分为轻阀和重阀两种,轻阀采用1.5mm薄板冲压而成,其质量约为25kg;重阀采用2mm薄板冲压,其质量约为33kg。
由于轻阀漏液量较大,除真空操作时选用外,一般情况使用重阀。
浮阀的阀片及阀腿是整体冲压的,阀片的周围还冲有三个下弯的小定距片。
在浮阀关闭阀孔时,它能使浮阀与塔板间保留一个小的间隙,一般约为2.5mm,阀片四周向下倾斜,并有锐边,更利于气体进入液层的湍动作用,有利于气液传质。
浮阀的最大开度是由阀腿的高度决定的,一般约为12.5mm。
F1型浮阀的基本参数见表2-2。
表2-2 F1型浮阀的基本参数浮阀的排列:浮阀最好以三角形排列,此时各排浮阀垂直于液流方向,使气液两相均匀接触。
对分块式塔盘,由于塔盘板分块的宽度是统一的,所以采用等腰三角形排列。
在垂直于液流的方向上,浮阀的中心距t固定不变,一般定位75mm。
等腰三角形的高为100mm。
在排列浮阀时,还应注意外围浮阀与塔壁和堰之间保留相当的距离,以利于安装和操作,则我们取80mm。
分块式塔盘外围浮阀的中心与进口堰、溢流堰的距离,一般为100mm。
2.3.2 塔盘的结构设计塔盘按结构可分为整块式和分块式两种类型。
由于本次塔设计的塔径大于800mm,故采用分块式塔盘。
直径较大的板式塔,为便于制造、安装、检修,可将塔盘板分成数块,通过人孔送入塔,装在焊于塔体壁的塔盘支撑件上。
选用自伸梁式。
选择具有可调节堰、可拆降液板、自伸梁式塔盘板的单流塔结构。
2.3.3 塔盘板(1)用自伸梁式(2)塔盘板的分块矩形塔盘板用于塔盘中间部分,端部取3个卡子;弧形塔盘板及切角矩形塔盘板用于塔壁附件。
(3)塔盘板的结构尺寸塔盘板的支撑件,支撑圈、支撑板和降液板连接带焊在塔壁上,用以支持塔盘板和降液板。
塔盘板外沿与塔壁的间隙为15mm;塔盘板与支持圈连接处的紧固件尺寸取120mm;塔盘板之间连接的紧固件间距取180mm;自伸梁高度L=80mm。
支持圈和支持板宽度见表2-3。
表2-3支持圈和支持板宽度(4)支持件结构塔盘上的降液板及受液盘分为可拆结构及焊接的固定结构。
固定结构的降液板和受液盘,与支持圈、支撑板一起,都焊在塔壁上,形成塔盘的固定件。
(5)排液孔板式塔在停止操作时,塔盘、受液盘、封液盘等应均能自行排净存液,否则就需要开设排液孔。
在这些盘中开设一个直径约为10mm的排液孔。
(6)降液管及受液盘降液管应选用弓形降液管。
当降液面积占塔盘总面积的12%以上时,应选用倾斜式降液管。
它的下部截面约为上部截面的56%,这样就可以扩大塔盘的有效面积。
一般取倾斜降液板的倾斜角为10度。
可拆式弓形降液管是由焊在塔壁上的连接带、以及可拆的降液板和紧固件装配而成。
用M10螺栓紧固时,在降液板间的连接处均用直径为12mm的圆孔。
在降液板与连接带的连接处,连接带上要用直径为12mm的圆孔,降液板上用14×40mm的长圆孔,以便于安装、调整。
受液盘选用凹形受液盘。
可拆式结构的每个可拆卸零件均应能通过人孔。
在受液盘的下方设加强筋板,则凹形受液盘的深度约为70mm。
封液盘:在塔或塔段最低一层塔盘的降液管末端,应设置封液盘,以保证降液管出口处的液封。
入口堰:进口堰距传质元件边缘的最小距离约为60mm。
当出口堰顶高度大于降液管底边时,在正对第一排气液接触元件的上游,设置直径为8mm圆钢或小型角钢构成入口堰。
对于分块式塔盘,入口堰分段的焊在分块的塔盘板上,与塔盘板构成一体。
出口堰:与可拆式降液管配用的出口堰,可用角钢或者用钢板弯成角钢形状,用紧固件连接到塔盘支持件或降液板上。
堰板的两侧用紧固件固定在降液板的连接带上。
塔盘零件的最小厚度见表2-4。
表2-4 塔盘零件的最小厚度2.3.4 塔盘主梁和支梁的设计(1)主梁①主梁的安装方向,应垂直平行于液体的流向。
②主梁的结构应采用整体式。
③主梁应安装在与塔壁焊接的支座上,并用螺栓与焊与塔壁或支座上的连接板相接。
④当塔盘必须设置主梁时,应设法尽量减少主梁的高度,以减少它对工艺操作的影响,并要求在安装时,人员能从梁底下通过。
(2)支梁①单独设置的支梁,应采用角钢或槽钢制造,且宽度不宜超过75mm。
②支梁连接与支持圈、支持板或主梁连接时,在表面应覆盖一堵板。
③焊于主梁或支梁的螺栓,其规格应大于或等于M12。
2.3.5 塔盘的紧固件紧固件应优先使用标准件,螺柱的规格应不小于M10。
因为连接处有垫片,所以塔板与支持圈的间距应不大于150mm,即取100mm。
塔盘板之间的连接可使用螺纹连接紧固件,选上可拆连接型式。
塔盘版与支持板或支持圈的连接用于螺纹卡板紧固件。
卡子由卡板、椭圆垫板、圆头螺栓以及螺母组成。
卡板与圆头螺栓焊成一个整体,点焊时应使螺栓尾部沟槽的方向与卡板的长度方向平行,以此来辨别卡板的方位。