影响切削用量的因素
影响切削用量的因素

影响切削用量的因素切削用量是切削加工中一个重要的参数,影响着加工质量、加工效率和切削工具的寿命。
以下将介绍影响切削用量的几个主要因素:1.材料性质:不同材料具有不同的硬度、强度、韧性等性质,这些性质对切削用量有直接影响。
硬度高的材料通常需要较大的切削力才能达到要求的加工精度,因此需要较大的切削用量。
而材料的韧性高则需要较小的切削用量,以避免过度切削导致刀具断裂。
2.切削速度:切削速度是指单位时间内切削刀具通过加工件上相同长度的距离。
切削速度的高低直接影响到切削用量。
一般而言,切削速度越高,切削用量越小;切削速度越低,切削用量越大。
3.切削深度:切削深度是指切削刀具垂直于工件表面进入的深度。
切削深度的大小直接影响到切削用量。
一般而言,切削深度越大,切削用量越大;切削深度越小,切削用量越小。
4.进给量:进给量是指切削刀具在单位时间内对工件进行加工的长度。
进给量的大小直接影响到切削用量。
一般而言,进给量越大,切削用量越大;进给量越小,切削用量越小。
5.切削润滑方式:切削润滑方式主要包括全润滑和干式切削两种。
全润滑方式下,通过使用冷却液进行切削润滑可以降低摩擦和热量的产生,减少切削用量。
而干式切削方式下,由于缺乏润滑,摩擦和热量较大,容易导致切削用量增加。
6.切削刀具材料和几何形状:切削刀具的材料和几何形状直接影响到切削用量。
良好的刀具材料和几何形状能够提高切削效率和降低切削用量。
例如,使用硬质合金刀具和适当的刀具形状可以降低切削力,减小切削用量。
7.切削条件:切削条件包括冷却液的类型和喷射方式、进给方式等。
这些条件的正确选择可以降低切削用量。
合适的冷却液类型和喷射方式能够减少摩擦和热量的产生;合理的进给方式能够降低切削力,减小切削用量。
总之,切削用量受到材料性质、切削速度、切削深度、进给量、切削润滑方式、切削刀具材料和几何形状以及切削条件等多个因素的影响。
在实际生产中,应根据具体情况选择合理的切削用量,以提高加工质量和效率,并延长刀具的使用寿命。
切削用量三要素范文
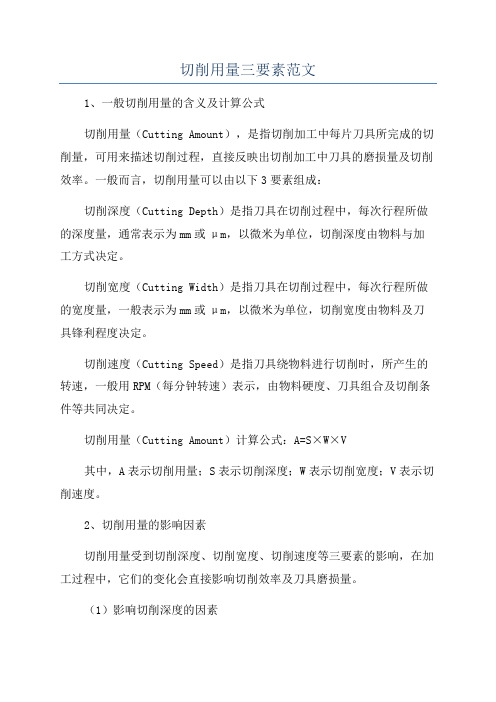
切削用量三要素范文
1、一般切削用量的含义及计算公式
切削用量(Cutting Amount),是指切削加工中每片刀具所完成的切削量,可用来描述切削过程,直接反映出切削加工中刀具的磨损量及切削效率。
一般而言,切削用量可以由以下3要素组成:
切削深度(Cutting Depth)是指刀具在切削过程中,每次行程所做的深度量,通常表示为mm或μm,以微米为单位,切削深度由物料与加工方式决定。
切削宽度(Cutting Width)是指刀具在切削过程中,每次行程所做的宽度量,一般表示为mm或μm,以微米为单位,切削宽度由物料及刀具锋利程度决定。
切削速度(Cutting Speed)是指刀具绕物料进行切削时,所产生的转速,一般用RPM(每分钟转速)表示,由物料硬度、刀具组合及切削条件等共同决定。
切削用量(Cutting Amount)计算公式:A=S×W×V
其中,A表示切削用量;S表示切削深度;W表示切削宽度;V表示切削速度。
2、切削用量的影响因素
切削用量受到切削深度、切削宽度、切削速度等三要素的影响,在加工过程中,它们的变化会直接影响切削效率及刀具磨损量。
(1)影响切削深度的因素
切削深度主要受到机床行程、切削精度及切削条件等因素影响,如它们的变化将会使切削深度发生变化,进而会影响切削用量。
数控车床加工工艺编程-切削用量三要素
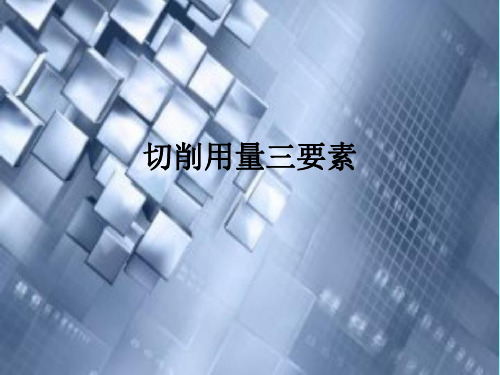
切削用量是表示主运动及进给运动大小的参数。
它包括:切削速度Vc (或主轴转速n)、 切削深度ap、进给量f 三要素。
1)切削深度是指工件上已加工表面和待加工 表面间的垂直距离。
在工艺系统刚性和机床功率允许的条件下, 尽可能选取较大的切削深度,以减少进给次 数。当工件的精度要求较高时,则应考虑留 有精加工余量,一般为0.1~0.5mm。 切削深度ap计算公式:ap= 式中: dw—待加工表面外圆直径,单位 mm dm—已加工表面外圆直径,单位mm.
2)切削速度是切削刃选定点相对于工件的主 运动的瞬时速度。
① 车削光轴切削的速度,由工件材料、直径、刀 具的材料及加工性质等因素所确定。 切削速度Vc计算公式: v = πdn / 1000
式中: d—工件或刀尖的回转直径,单位mm n—工件或刀具的转速,单位r/min
② 车削螺纹主轴转速n 切削螺纹时,车床的主轴转 速受加工工件的螺距(或导程)大小、驱动电动机升 降特性及螺纹插补运算速度等多种因素影响,因此对 于不同的数控系统,选择车削螺纹主轴转速n存在一 定的差异。 数控车床车螺纹时主轴转速计算公式:n≤–k 式中: p—工件螺纹的螺距或导程, 单位mm。 k—保险系数,一般为80。
• 3)进给速度
进给速度是指单位时间内,刀具沿进给方向移动的 距离,单位为mm/min,也可表示为主轴旋转一周时 刀具在进给方向上相对工件的位移量,单位为mm/r。
• 我们怎么来确定进给速度的原则呢?
• ①当工件的加工质量能得到保证时,为提高生产率 可选择较高的进给速度。
• ②切断、车削深孔或精车时,选择较低的进给速度。 • ③刀具空行程尽量选用高的进给速度。 • ④进给速度应与主轴转速和切削深度相适应。
切削用量三要素计算公式

切削用量三要素计算公式切削用量三要素计算公式是指在切削过程中,根据切削速度、进给速度和切削深度来计算切削用量的公式。
切削用量是切削过程中切除材料或切削液的量,是衡量切削过程中切削效果的一个重要指标。
在切削加工过程中,切削用量的合理控制对于提高切削效果、延长刀具寿命和提高加工效率都起到至关重要的作用。
切削用量三要素包括切削速度、进给速度和切削深度。
切削速度是指刀具与工件相对运动的速度,单位通常是m/min。
进给速度是指切削刃每转一周,工件上移动的距离,单位通常是mm/rev。
切削深度是指刀具切削刃在一个工件上的进入深度,单位通常是mm。
切削用量的计算公式为:切削用量=切削速度×进给速度×切削深度切削用量的计算公式可以根据不同的切削形式和加工要求进行调整。
下面将分别介绍一些常用的切削用量计算公式。
1.对于铣削加工:切削用量=切削宽度×进给速度×加工长度其中,切削宽度是指铣刀径向切削刀具之间的距离,通常是成刀具直径的倍数。
2.对于车削加工:切削用量=切削深度×进给速度×加工长度其中,切削深度是指刀具在工件中切削的最大深度。
3.对于钻削加工:切削用量=钻孔直径×进给速度×加工长度其中,钻孔直径是指钻头直径,进给速度是指每转一周,工件上移动的距离。
4.对于镗削加工:切削用量=镗孔直径×进给速度×加工长度其中,镗孔直径是指镗刀直径。
需要注意的是,切削用量的计算公式只是一个理论值,实际加工时往往需要根据具体材料性质、刀具情况、工件形状和加工要求等因素进行适当调整。
切削用量的合理选取对于加工质量的影响非常大。
合理的切削用量可以确保工件表面质量良好,避免切削过程中产生过大的切削力和切削热量,减少工件表面的热影响区,避免刀具磨损过快和强制振动的产生,提高切削效率和工件精度。
因此,在选择切削用量时应充分考虑刀具材料、刀具形状、刀具刃数、切削方式、切削速度和切削深度等因素,并根据实际情况进行调整。
简述切削用量的选用原则。
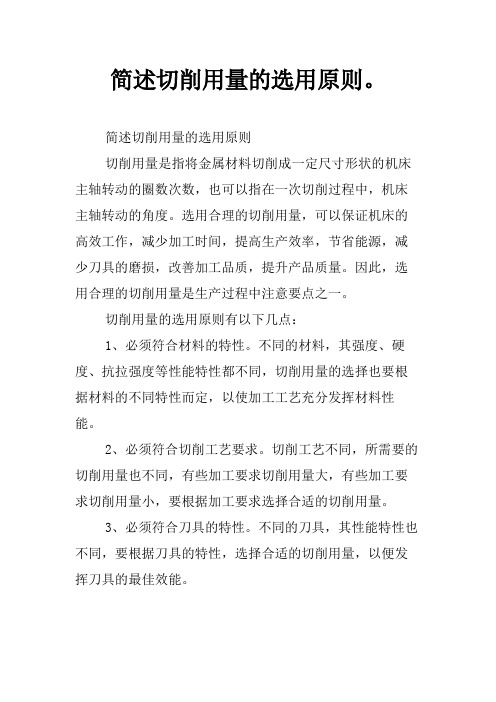
简述切削用量的选用原则。
简述切削用量的选用原则切削用量是指将金属材料切削成一定尺寸形状的机床主轴转动的圈数次数,也可以指在一次切削过程中,机床主轴转动的角度。
选用合理的切削用量,可以保证机床的高效工作,减少加工时间,提高生产效率,节省能源,减少刀具的磨损,改善加工品质,提升产品质量。
因此,选用合理的切削用量是生产过程中注意要点之一。
切削用量的选用原则有以下几点:1、必须符合材料的特性。
不同的材料,其强度、硬度、抗拉强度等性能特性都不同,切削用量的选择也要根据材料的不同特性而定,以使加工工艺充分发挥材料性能。
2、必须符合切削工艺要求。
切削工艺不同,所需要的切削用量也不同,有些加工要求切削用量大,有些加工要求切削用量小,要根据加工要求选择合适的切削用量。
3、必须符合刀具的特性。
不同的刀具,其性能特性也不同,要根据刀具的特性,选择合适的切削用量,以便发挥刀具的最佳效能。
4、必须符合机床的特性。
不同的机床,其转速、功率等性能特性也不同,切削用量的选择也要根据机床的特性来决定,以保证机床的最佳效能。
5、必须符合工件尺寸要求。
切削用量必须根据工件尺寸的大小来选择,如果工件尺寸较大,则切削用量越大,反之,切削用量越小。
6、必须符合加工精度要求。
当加工的精度越高时,切削用量就越少,而加工的精度越低时,切削用量就越大。
7、必须考虑切削方法的特点。
切削方法的特点包括:切削的深度和宽度,刀具的刃口形状,机床的转速,切削液的种类和流量等,这些都会影响切削用量的选择。
8、必须考虑切削液的特点。
不同的切削液具有不同的特性,要根据切削液的性质,选择适当的切削用量,以更好地发挥切削液的效用。
以上就是切削用量的选用原则的简介,要想使机床的加工效率达到最高,切削用量的选用是必不可少的,并且要根据不同材料、不同机床、不同刀具、不同加工工艺等多种因素,来确定适当的切削用量,以保证加工质量和加工效率。
切削用量三要素

根据已选定的背吃刀量ap、进给量f及刀具耐用度T,就可 按公式计算切削速度Vc和机床转速n。
切削用量及选择
① 粗车时,ap 、f均较大,所以Vc较低,精加工时,ap 、f均较小, 所以Vc较高。
② 工件材料强度、硬度较高时,应选较低的Vc;反之,Vc较高。 材料加工性越差,Vc较低。
对于粗加工来说,要尽可能保证较高的金属切除率和必要 的刀具耐用度。
提高切削速度,增大进给量和背吃刀量,都能提高金属切除率。但在
这三个因素中,影响刀具耐用度最大的是切削速度,其次是进给量,影 响最小的是背吃刀量。所以,在选择粗加工切削用量时,应优先考虑采
用大的背吃刀量,其次考虑采用大的进给量,最后才能根据刀具耐用度 的要求,选定合理的切削速度。
由此可见,选择切削用量的基本原则是首先选取尽可能大 的背吃刀量;其次要在机床动力和刚度允许的范围内,同时又满 足已加工表面粗糙度的要求的情况下,选取尽可能大的进给量, 最后利用《切削用量手册》选取或用公式计算确定最佳切削速度。
切削用量及选择
3.2 切削用量三要素的确定
(1)背吃刀量的选择
背吃刀量根据加工余量确定。
切削用量及选择
半精加工、精加工时首先要保证加工精度和表面质量, 同时应兼顾必要的刀具耐用度和生产效率,此时的背吃刀量 根据粗加工留下的余量确定。为了减小工艺系统的弹性变形, 减小已加工表面的残留面积,半精加工尤其是精加工,一般 多采用较小的背吃刀量和进给量。为抑制积屑瘤和鳞制的产 生,用硬质合金刀具进行精加工时一般多采用较高的切削速 度;高速钢刀具则一般多采用较低的切削速度。
已加工表面和待加工表面间的垂直距离,单位为mm。
对于外圆车削的深度可用下式计算:
ap=(dw-dm)/ 2 mm
切削用量的合理选择
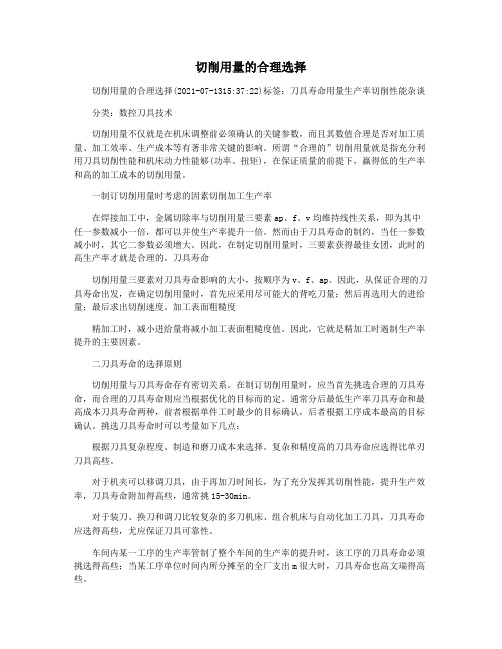
切削用量的合理选择切削用量的合理选择(2021-07-1315:37:22)标签:刀具寿命用量生产率切削性能杂谈分类:数控刀具技术切削用量不仅就是在机床调整前必须确认的关键参数,而且其数值合理是否对加工质量、加工效率、生产成本等有著非常关键的影响。
所谓“合理的”切削用量就是指充分利用刀具切削性能和机床动力性能够(功率、扭矩),在保证质量的前提下,赢得低的生产率和高的加工成本的切削用量。
一制订切削用量时考虑的因素切削加工生产率在焊接加工中,金属切除率与切削用量三要素ap、f、v均维持线性关系,即为其中任一参数减小一倍,都可以并使生产率提升一倍。
然而由于刀具寿命的制约,当任一参数减小时,其它二参数必须增大。
因此,在制定切削用量时,三要素获得最佳女团,此时的高生产率才就是合理的。
刀具寿命切削用量三要素对刀具寿命影响的大小,按顺序为v、f、ap。
因此,从保证合理的刀具寿命出发,在确定切削用量时,首先应采用尽可能大的背吃刀量;然后再选用大的进给量;最后求出切削速度。
加工表面粗糙度精加工时,减小进给量将减小加工表面粗糙度值。
因此,它就是精加工时遏制生产率提升的主要因素。
二刀具寿命的选择原则切削用量与刀具寿命存有密切关系。
在制订切削用量时,应当首先挑选合理的刀具寿命,而合理的刀具寿命则应当根据优化的目标而的定。
通常分后最低生产率刀具寿命和最高成本刀具寿命两种,前者根据单件工时最少的目标确认,后者根据工序成本最高的目标确认。
挑选刀具寿命时可以考量如下几点:根据刀具复杂程度、制造和磨刀成本来选择。
复杂和精度高的刀具寿命应选得比单刃刀具高些。
对于机夹可以移调刀具,由于再加刀时间长,为了充分发挥其切削性能,提升生产效率,刀具寿命附加得高些,通常挑15-30min。
对于装刀、换刀和调刀比较复杂的多刀机床、组合机床与自动化加工刀具,刀具寿命应选得高些,尤应保证刀具可靠性。
车间内某一工序的生产率管制了整个车间的生产率的提升时,该工序的刀具寿命必须挑选得高些;当某工序单位时间内所分摊至的全厂支出m很大时,刀具寿命也高文瑞得高些。
切削用量 切削用量三要素

切削用量切削用量三要素切削用量切削用量三要素切削用量切削用量三要素切削用量是指切削速度 v c 、进给量 f 〔或进给速度 v f 〕、背吃刀量 a p 三者的总称,也称为切削用量三要素。
它是调整刀具与工件间相对运动速度和相对位置所需的工艺参数。
它们的定义如下:〔一〕切削速度 v c切削刃上选定点相对于工件的主运动的瞬时速度。
计算公式如下v c=( π d w n )/1000 (1-1)式中 v c ——切削速度 (m/s) ;dw ——工件待加工外表直径〔 mm 〕;n ——工件转速〔 r/s 〕。
在计算时应以最大的切削速度为准,如车削时以待加工外表直径的数值进行计算,因为此处速度最高,刀具磨损最快。
〔二〕进给量 f工件或刀具每转一周时,刀具与工件在进给运动方向上的相对位移量。
进给速度 v f 是指切削刃上选定点相对工件进给运动的瞬时速度。
v f=fn 〔 1-2 〕式中 v f ——进给速度〔 mm/s 〕;n ——主轴转速〔 r/s 〕;f ——进给量〔 mm 〕。
〔三〕背吃刀量 a p通过切削刃基点并垂直于工作平面的方向上测量的吃刀量。
根据此定义,如在纵向车外圆时,其背吃刀量可按下式计算:a p = 〔 d w — d m 〕 /2 〔 1-3 〕式中 d w ——工件待加工外表直径〔 mm 〕;dm ——工件已加工外表直径〔 mm 〕。
涂层刀片为了提高刀具〔刀片〕外表的硬度和改善其耐磨性、润滑性,通过化学气相沉积和真空溅射等方法,在硬质合金刀片外表喷涂一层厚度 5~ 12μ m以下的TiC、 TiN或 Al 2O 3等化合物材料。
TiC 涂层刀片,硬度可达 3200HV,呈银灰色,耐磨性好,容易扩散到基体内与基体粘结牢固,在低速切削温度下有较高的耐磨性。
TiN 涂层刀片 TiN硬度为 2000HV,呈金黄色,色泽美观,润滑性能好,有较高的抗月牙洼型的磨损能力,与基体粘结牢固程度较差。
- 1、下载文档前请自行甄别文档内容的完整性,平台不提供额外的编辑、内容补充、找答案等附加服务。
- 2、"仅部分预览"的文档,不可在线预览部分如存在完整性等问题,可反馈申请退款(可完整预览的文档不适用该条件!)。
- 3、如文档侵犯您的权益,请联系客服反馈,我们会尽快为您处理(人工客服工作时间:9:00-18:30)。
影响切削用量的因素有:
机床切削用量的选择必须在机床主传动功率、进给传动功率以及主轴转速范围、进给速度范围之内。
机床—刀具—工件系统的刚性是限制切削用量的重要因素。
切削用量的选择应使机床—刀具—工件系统不发生较大的“振颤”。
如果机床的热稳定性好,热变形小,可适当加大切削用量。
刀具刀具材料是影响切削用量的重要因素。
表1是常用刀具材料的性能比较。
数控机床所用的刀具多采用可转位刀片(机夹刀片)并具有一定的寿命。
机夹刀片的材料和形状尺寸必须与程序中的切削速度和进给量相适应并存入刀具参数中去。
标准刀片的参数请参阅有关手册及产品样本。
表1 常用刀具材料的性能比较
工件不同的工件材料要采用与之适应的刀具材料、刀片类型,要注意到可切削性。
可切削性良好的标志是,在高速切削下有效地形成切屑,同时具有较小的刀具磨损和较好的表面加工质量。
较高的切削速度、较小的背吃刀量和进给量,可以获得较好的表面粗糙度。
合理的恒切削速度、较小的背吃刀量和进给量可以得到较高的加工精度。
冷却液冷却液同时具有冷却和润滑作用。
带走切削过程产生的切削热,降低工件、刀具、夹具和机床的温升,减少刀具与工件的摩擦和磨损,提高刀具寿命和工件表面加工质量。
使用冷却液后,通常可以提高切削用量。
冷却液必须定期更换,以防因其老化而腐蚀机床导轨或其他零件,特别是水溶性冷却液。
以上讲述了机床、刀具、工件、冷却液对切削用量的影响。
切削用量的选择原则,下面主要论述铣削加工的切削用量选择原则。
铣削加工的切削用量包括:切削速度、进给速度、背吃刀量和侧吃刀量。
从刀具耐用度出发,切削用量的选择方法是:先选择背吃刀量或侧吃刀量,其次选择进给速度,最后确定切削速度。
1.背吃刀量a p或侧吃刀量a e
背吃刀量a p为平行于铣刀轴线测量的切削层尺寸,单位为㎜。
端铣时,a p为切削层深度;而圆周铣削时,为被加工表面的宽度。
侧吃刀量a e为垂直于铣刀轴线测量的切削层尺寸,单位为㎜。
端铣时,a e为被加工表面宽度;而圆周铣削时,a e为切削层深度,见下图。
铣削加工的切削用量图
背吃刀量或侧吃刀量的选取主要由加工余量和对表面质量的要求决定:
①当工件表面粗糙度值要求为Ra=12.5~25μm时,如果圆周铣削加工余量小于5㎜,端面铣削加工余量小于6㎜,粗铣一次进给就可以达到要求。
但是在余量较大,工艺系统刚性较差或机床动力不足时,可分为两次进给完成。
②当工件表面粗糙度值要求为R a=3.2~12.5μm时,应分为粗铣和半精铣两步进行。
粗铣时背吃刀量或侧吃刀量选取同前。
粗铣后留0.5~1.0㎜余量,在半精铣时切除。
③当工件表面粗糙度值要求为R a=0.8~3.2μm时,应分为粗铣、半精铣、精铣三步进行。
半精铣时背吃刀量或侧吃刀量取1.5~2㎜;精铣时,圆周铣侧吃刀量取0.3~0.5 ㎜,面铣刀背吃刀量取0.5~1 ㎜。
2.进给量f与进给速度V f的选择
铣削加工的进给量f(㎜/r)是指刀具转一周,工件与刀具沿进给运动方向的相对位移量;进给速度Vf(㎜/min)是单位时间内工件与铣刀沿进给方向的相对位移量。
进给速度与进给量的关系为V f = n f(n为铣刀转速,单位r /min)。
进给量与进给速度是数控铣床加工切削用量中的重要参数,根据零件的表面粗糙度、加工精度要求、刀具及工件材料等因素,参考切削用量手册选取或通过选取每齿进给量fz,再根据公式f =Zf z(Z为铣刀齿数)计算。
每齿进给量f z的选取主要依据工件材料的力学性能、刀具材料、工件表面粗糙度等因素。
工件材料强度和硬度越高,f z越小;反之则越大。
硬质合金铣刀的每齿进给量高于同类高速钢铣刀。
工件表面粗糙度要求越高,fz就越小。
每齿进给量的确定可参考表2选取。
工件刚性差或刀具强度低时,应取较小值。
表2 铣刀每齿进给量参考值
3.切削速度V c
铣削的切削速度V c与刀具的耐用度、每齿进给量、背吃刀量、侧吃刀量以及铣刀齿数成反比,而与铣刀直径成正比。
其原因是当f z、a p、a e和Z增大时,刀刃负荷增加,而且同时工作的齿数也增多,使切削热增加,刀具磨损加快,从而限制了切削速度的提高。
为提高刀具耐用度允许使用较低的切削速度。
但是加大铣刀直径则可改善散热条件,可以提高切削速度。
铣削加工的切削速度V c可参考表3选取,也可参考有关切削用量手册中的经验公式通过计算选取。
表3 铣削加工的切削速度参考值。