数控加工中切削用量的合理选择
铣削加工切削用量的选择
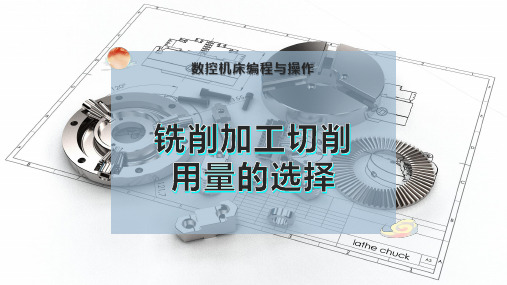
数控机床加工的切削用量
(3)确定进给速度
进给速度是数控机床切削用量中的重要参数。主要根 据零件的加工精度和表面粗糙度要求以及刀具、零件的材 料性质来选取。当加工精度和表面粗糙度要求高时,进给 速度应该选择得小些。一般应该在20mm/min~50mm/min 范围内选取。最大进给速度受机床刚度和进给系统的性能 的影响,并与数控系统中脉冲当量的大小有关。
总之,切削用量的具体数值应根据机床性能、相关的 手册并结合实际经验用类比法来确定,同时使主轴转速、 铣削深度以及进给速度三者能够相互适应,以形成最佳的 切削用量。在选择进给速度时,还应该注意零件加工中的 特殊因素。例如在轮廓加工中,当零件轮廓有拐角时,刀 具容易产生“超程”和“欠程”现象,从而导致加工误差。
数控机床编程与操作
数控机床加工的切削用量
切削用量主要包括:铣削深度、铣削速度、进给速度。 对于不同的加工方法,需要选用不同的切削用量,合理选择 切削用量的原则是:粗加工时,一般以提高生产率为主,但 也应该考虑经济性和加工成本;半精加工和精加工时,一般 应在保证加工质量的前提下,兼顾切削效率、经济性和加工 成本。具体选用数值应该根据机床说明书、切削用量手册, 并结合实际经验而定。 (1)铣削深度
数控机床编程与操作
效措施还是应该尽可能采取大的铣削深度。因为切削速度v 与刀具耐用度的关系成反比,所以切削速度v 的选取主要取
决于刀具耐用度。切削用量的选取可根据实际经验或参阅有 关手册。
主轴转速n(r/min)由切削速度v 来选定:
n= 1000v /(πd)
式中:v ——切削速度mm /min,由刀具耐用度决定;
在机床、工件和刀具刚度允许的情况下,应以最小的进 给次数切除待加工余量,最好一次切除待加工余量,以提高 生产效率。为了保证零件的加工精度和表面粗糙度,可留少 许余量留待最后加工。数控铣床的精加工余量一般可取 (0.2~0.5mm)。
(数控加工)数控加工的切削用量精编
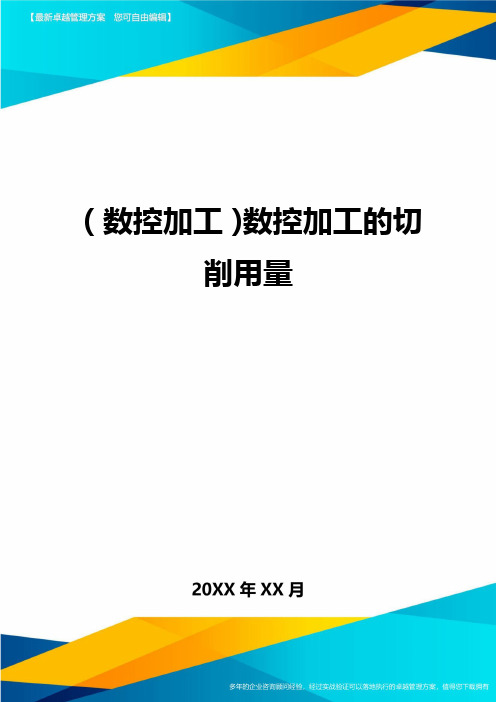
(数控加工)数控加工的切削用量数控加工的切削用量2009-6-119:42:00来源:作者:余英良,于辉阅读:1418次我要收藏1切削用量选择1.1数控加工花键轴的切削用量为了保证零件的加工精度,零件分为粗车加工和精车加工。
在粗、精车零件装夹方式和刀具选择的基础上,选定零件数控加工的切削参数如下:在数控精车车削加工中,零件轮廓轨迹的加工余量为0.8÷2=0.4mm。
主轴转速、背吃刀量等的选择参见表1。
表1数控加工花键轴工序卡及切削用量1.2数控加工轴承座的切削用量为了保证零件的加工精度,零件分为粗车加工和精车加工。
在粗、精车零件装夹方式和刀具选择的基础上,选定零件数控加工的切削参数如下:在数控精车车削加工中,零件轮廓轨迹的加工余量为0.8÷2=0.4mm。
主轴转速、背吃刀量等的选择参见表2。
表2数控加工轴承座工序卡及切削用量2相关内容概述金属切削加工的目的,就是用各种类型的金属切削刀具把J:件毛坯上的多余部分从毛坯上剥离开来,得到图样所要求的零件形状和尺寸。
图1车削加工中切削用量nextpage2.1切削用量切削用量是指机床在切削加工时的状态参数。
切削用量包括切削速度、进给速度和背吃刀量。
参见图1。
2.1.1切削速度切削刃上的切削点相对于工件运动的瞬时速度称为切削速度。
切削速度的单位为m/min。
切削速度和机床主轴转速之问进行转换的关系为:(1)2.1.2进给速度是刀具在单位时间内沿进给方向上相对于工件的位移量,单位为mm/min。
2.1.3背吃刀量己加工表面和待加工表面之问的垂直距离。
背吃刀量的计算公式为:(2)式(1)、式(2)中n为主轴(工件)转速,d为工件直径,dω、dm见图1。
在切削加工中,切削速度、进给速度和背吃刀量3个参数是相互关联的。
粗加工中,为提高效率,壹般采用较大的背吃刀量。
此时切削速度和进给速度相对较小;在半精加工和精加工阶段,壹般采用较大的切削速度、较小的进给量和背吃刀量,以获得较好的加工质量。
刀具及切削用量在数控加工中的合理选用

1 数 控 加 工 常 用 刀 具 的 种 类 及特 点
数控加 工的特点是高速 、 高效 以及 自动化程 度高 . 所 以刀具的选 择要符合其特点 。 包括 通用刀具 、 通用连接刀柄及少量专用刀柄 ( 刀柄 要联结刀具并安装在机床动刀头上) 1 . 1 数控刀具 的分类方法 根据刀具 的结 构、 材料 以及切 削工艺可分为诸 多类别 . 在结构上 分: 整体式 、 镶嵌 式和特殊形式 ; 如果 选择焊接或 机夹式联结 的话 , 机 夹式又分不转位和可转位两种 : 在材料上的分为高速钢、 硬质合金 、 金 刚石和其他材料的刀具。切削工艺上分为车削刀具( 分外 圆、 内孔 、 螺 纹、 切割刀具等 ) 、 钻削刀具( 包括钻头 、 绞刀 、 丝锥等) 、 镗削刀具、 铣削 刀具等。数控机床对刀具有一系列的要求 , 耐用 、 稳定 、 易调 、 可换等 , 为 了符合这些要求 . 最近几年夹式 可转位刀具被广 泛使用 . 占整 个数 控刀具的 3 0 %~ 4 0 %. 金属切 除量 占总数 的 8 0 %~ 9 0 % 1 . 2 数控刀具与普通机床上所用刀具 相比 . 主要有 以下特 点 ( 1 ) 刚性 好 ( 尤其是粗加 工刀具 ) 、 精度 高、 抗振及 热变形 小 ; ( 2 ) 互换性 好 , 便 于快速换 刀 ; ( 3 ) 寿命高 , 切 削性能稳 定 、 可靠 ; ( 4 ) 刀具 的尺 寸便于调 整 , 以减 少换刀调 整时 间 : ( 5 ) 刀 具应能可 靠地断 屑或 卷屑 , 以利于切 屑的排 : ( 6 ) 系列化 、 标 准化 , 以利于编 程和刀具 管
加 工 中刀具的分 类和特 点, 把 刀具在数控 自动编程 中的合理选用做 了详细的分类与说 明。
【 关键词 】 刀具 ; 编程 ; 数控加 工; 合理选用
数控加工中刀具的选择和切削用量的确定
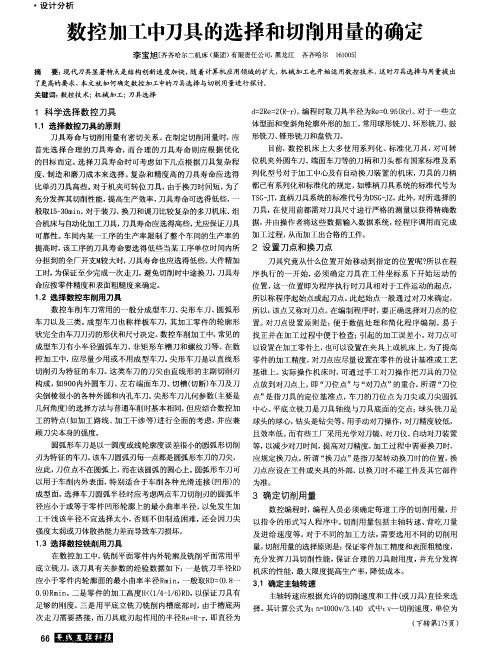
构成 ,  ̄ n g o o 内外 圆车刀、 左 右端面车刀、 切槽 ( 切断) 车刀及刀 点放 到对刀点上, 即“ 刀位 点” 与“ 对刀点” 的重合。 所谓 “ 刀位
尖倒棱很小的各种外圆和 内孔车刀。 尖形车刀几何参数 ( 主要是 点” 是指刀具的定位 基准 点, 车刀 的刀位 点为刀尖或 刀尖 圆弧
圆弧形车刀是以一 圆度或线轮廓度误差很小的圆弧形切削 等, 以减少对刀时间, 提 高对刀精度。 加工过程 中需要换刀时, 刃为特征 的车刀。 该车刀圆弧刃每一点都是圆弧形车刀的刀尖, 应规定换刀点。 所谓 “ 换刀点” 是指刀架转动换 刀时的位置 , 换 应此 , 刀位 点不在圆弧上 , 而在该圆弧的圆心上 。 圆弧形车刀可 刀点应 设在 工件或夹具 的外部 , 以换刀 时不碰工件及其它部件
工时, 为保证至少完成一次走刀, 避免切削时中途换 刀, 刀具寿 序 执行 的一开始 , 必须 确定刀具在 工件坐标 系下开始 运动 的 命应按零件精度和表面粗糙度来确定。
1 . 2选择数控车削用刀具
数控 车削车刀常用 的一 般分成型车刀、 尖 形车刀、 圆弧形 所 以, 该点又称对刀点。 在编制程序 时, 要正确选择对刀点的位 车刀以及 三类 。 成型车刀也称 样板车刀, 其加 工零 件的轮廓形 置。 对刀点设置 原则是: 便于数值 处理和简 化程 序编制 。 易于
S G  ̄T , 直柄刀具系统 的标准代号为D S G  ̄Z , 此 外, 对所选择的 充分发挥其切削性能, 提高生产效率, 刀具寿命可选得低些, 一 T 刀具 , 在使用前都需对刀具尺寸进行严格 的测量 以获得精确数 般取 1 5 — 3 0 m i n 。 对于装刀、 换刀和调刀 比较 复杂的多刀机床、 组 并 由操 作者将这些 数据输入数 据系统, 经程序调用而完成 合机床与 自动化加工刀具 , 刀具寿命应 选得高些 , 尤应保证刀具 据, 从而加工出合格的工件。 可靠 性。 车 间内某—工序 的生产率 限制 了整个车间的生Fra bibliotek率的 加工过程 ,
数控机床加工的切削用量

单元4数控机床加工的切削用量教学目的1、了解数控机床的运动(主运动、进给运动);2、了解数控机床加工刀具的角度及其作用;3、了解数控机床加工中有关切削层的参数及其作用;4、了解数控机床加工中的切削用量及其选用原则。
5、掌握常用不同材料零件在粗加工、半精加工和精加工时的切削用量选用;教学重点1、数控机床加工刀具的角度及其作用;2、数控加工中粗加工、半精加工和精加工时的切削用量选择;教学难点1、刀具的角度及其作用;2、切削用量选用教学方法讲练结合教学内容一、车削加工与刀具1. 车削加工原理在普通车床和一般数控车床上,可以进行工件的外表面、端面、内表面以及内外螺纹的加工。
对于车削中心,除上述各种加工外,还可进行铳削、钻削等加工。
从上述介绍可以看出:在切削过程中,刀具和工件之间必须具有相对运动,这种相对运动称为切削运动。
根据切削运动在切削过程中的作用不同可以分为主运动、和进给运动。
各种机床的主运动和进给运动参见下表。
主运动是指机床提供的主要运动。
主运动使刀具和工件之间产生相对运动,从而使刀具的前刀面接近工件并对工件进行切削。
在车床上,主运动是机床上主轴的回转运动,即车削加工时工件的旋转运动。
2)进给运动进给运动是指由机床提供的使刀具与工件之间产生的附加相对运动。
进给运动与主运动相配合,可以形成完整的切削加工。
在普通车床上,进给运动是机床刀架(溜板)的直线移动。
它可以是纵向的移动(与机床主轴轴线平行),也可以是横向的移功(与机床主轴轴线垂直),但只能是一亇方向的移动。
在数控车床上,数控车床可以同时实现两亇方向的进给,从而加工出各种具有复杂母线的回转体工件。
在数控车床中,主运动和进给运动是由不同的电机来驱动的,分别称为主轴电机和坐标轴伺服电机。
它们由机床的控制系统进行控制,自动完成切削加工。
2. 切削用量切削用量是指机床在切削加工时的状态参数。
不同类型的机床对切削用量参数的表述也略有不同,但其基本的含义都是一致的,如下图所示。
数控车削用量的选择原则

数控车削用量的选择原则
首先得说说切削速度这玩意儿。
它就好比是车子在马路上跑的速度。
速度太快呢,就像开车超速,容易出问题,比如刀具磨损得快,工件表面质量也可能变得粗糙。
但要是速度太慢,那加工效率就低得可怜,就好比是老年代步车在高速路上慢悠悠地晃悠,这谁等得及啊?所以呢,选择切削速度得综合考虑刀具材料、工件材料这些因素。
比如说,加工硬度高的工件,速度就得适当慢一点,就像爬山遇到陡坡,咱得小心翼翼地走;要是加工比较软的材料,速度就可以适当提一提,就像在平地上骑车,可以撒欢儿跑。
再讲讲进给量。
这进给量啊,就像是吃饭,一口吃多少得有个度。
进给量太大,刀具受力就大,容易崩刀,就好比一个人吃饭太急,容易噎着;进给量太小呢,加工时间就会变长,效率低下,就像吃饭细嚼慢咽到天黑都吃不完一顿饭。
一般来说,粗加工的时候,进给量可以大一点,把多余的材料快速地去掉,就像开荒种地,先把大块的土翻起来;精加工的时候,进给量就得小一点,这样才能保证工件表面的光洁度,就像给脸蛋儿做精细护理,得慢慢来。
还有切削深度,这就像是挖土的深度。
粗加工时,切削深度可以大一些,把大部分余量去掉,就像盖房子打地基,得挖得深一点才稳当;精加工时,切削深度就要小很多啦,只是把最后的一点点余量去掉,让工件达到要求的尺寸和精度,就像给蛋糕最后抹上一层细腻的奶油,得轻轻来。
另外,刀具的耐用度也得考虑进去。
刀具就像是战士的武器,要是武器老是坏,那这仗还怎么打?所以要根据刀具的材料和性能,合理选择车削用量,让刀具能够多干会儿活儿,这样既能保证加工质量,又能节省刀具成本,一举两得啊!。
选择数控铣加工中的刀具和切削用量的分析
在 应 用 数 控 铣加 工进 行 工件 加 工 时 , 为 提 高 其 加 工 精度 ,
降低刀具材料损耗 , 提高数控铣加工效率 , 对数控铣加工刀具
提 出 了一 定要 求 。在 选 择 刀 具时 , 应 综合 考 虑 数控 铣 机 床 中刀
在 数控 铣 加 工 中 , 刀 具磨 损 、刀 具 测量 及 更 换均 是 由人 工 进 行 操作 来完 成 , 其辅 助 作 业时 间 花 费较 多 , 为 实现 数 控 铣加 工 的 经济 效 益 , 应 合理 安 排 刀具 次 序 , 并 遵 循 以下 原 则 : 尽量 减 少 刀 具数 量 ; 一 次装 夹完 成其 所 有 加工 部 位 ; 先铣 后钻 ;完 成 曲面 精加工 后进 行二 维 轮廓精 加 工作业 。
槽加 工 尺寸 精 度 ,多采 取两 刃键 槽 铣 刀 。在 选择 孔 加 工 刀具 应 用中 , 因数控机床孔加工多采取的是无钻模形式 , 工件切削条 件较差 , 在进行钻头选择时 , 应 保 证 钻 头 直 径 d满 足 1 / d≤ 5 的条件 ; 在进 行 工件 钻 孔 操 作 时 , 需 要通 过 中心 钻 进 行 定位 , 保 证孔 加 工定 位 精 度 ; 在 处理 工件 精 纹 之 前 , 可 以应 用 浮动 绞 刀 进 行操 作 ; 在 处 理工 件 镗孔 时 多选 择 多 刃镗 刀 头进 行 工 件切 削; 为 降低切 削振 动 , 应选 择较粗 或 较短 刀具 刀杆 。 1 . 4 数 控铣加 工刀 具排 列 顺序原 则
照 数 控铣 刀 具 结 构 , 可 以将 其 划 分为 特殊 型式 、整 体 式 、镶 嵌 式 三种 类 型 ; 按 照 数控 铣 刀 材 质 可 以划分 为 金 刚石 刀 具 、硬质 合 金 刀 具、 高速 钢 刀 具及 其 他 材 料刀 具等 ; 以切 削工 艺 为标 准 则 可 以将 数 控铣 刀分 为 球头 刀 、 平端 立铣 刀 、 圆角 立 铣 刀与 锥 度 铣刀 等 。
数控加工工艺中重要参数的确定
数控加工由于其高精度、高效率的特点,被广泛应用于机械加工领域。
在运用数控设备加工工件的时候,由于加工参数较多且编程步骤较复杂,因此需要操作者具有相关工作经验。
而对于刚接触数控加工的新人来说,学会参数确定及编程十分重要。
本文就来具体介绍一下数控加工工艺中重要参数如何确定。
一、切削用量的确定在进行数控编程的过程中,需要确定每道工序的切削用量,并且使用指令的形式写入到程序中。
在生产中,切削用量包括主轴转速、进给速度以及背吃刀量等等。
而对于切削用量的选择来说,保证零件加工精度和表面粗糙度充分发挥刀具切削性能,保证合理刀具寿命是选择且销量的重要原则。
二、进给速度的确定进给速度是数控机床切削用量中的十分重要的一个参数,主要根据零件的加工精度、表面粗糙度、刀具、工件的材料来确定。
确定进给速度的原则主要有以下几个方面:(1)为了让生产效率提高,当工件的质量可以得到满足时,可选择较高的进给速度。
(2)在切断、加工深孔或用高速钢刀具加工时,可以适当选择较低的进给速度。
(3)当加工精度、表面粗糙度要求比较高的时候,可以适当选择小一些的进给速度。
(4)当刀具空行程,可以设定该机床数控系统最高进给速度。
三、背吃刀量的确定背吃刀量在确定的时候需要根据机床、工件和刀具的刚度作为主要参考因素,在刚度允许的条件下,让背吃刀量尽可能与工件的加工余量相等,这样做的好处是可以减少走刀次数,提高生产效率。
同时,为了保证加工表面质量,可以留少许加工余量。
切削用量的选择是否合理,对于发挥机床潜力与刀具的切削性能,实现优质、高产、低成本和安全操作具有很重要的作用。
在对车削用量进行选择时,要注意粗车时,可以选择一个尽可能大的背吃刀量,其次选择一个较大的进给量,最后确定一个合适的切削速度。
而在精车时,加工精度和表面粗糙度要求较高,加工余量不大且均匀,因此选择较小的背吃刀量和进给量。
浅谈数控加工工艺中切削用量的选择
技 术 应 用
浅谈数控 加工工艺中切 削用量的选择
周靖 明 刘 凡( 铁山 中 桥集团 高级技工 学校, 河北 秦皇岛 060 625 )
摘 要 : 削用量是控制 数控机 床 加工质 量好坏 的关键性 因素, 切 而切 削用量 由背吃 刀量、 削速 度 和进 给 量这 三个要 素组 成 , 切 因此 刀具 的
进给量 是切削用量 中的第二要素, 进给量 的大小就决定了 度 的前 提是选择合 理的切削用量 , 理的切 削用量可以将刀具 零件的加工精度和表面粗糙度, 合 而工件材料和刀具 的耐磨度又 切削性能和机床性能发挥到极致 , 如此就降低了加工成 本还提 决定了进给 量的范围。 多齿刀具中, 在 刀具转速 n 、进给 速度 高了切削效率。 不同的加工种类 , 切削用量的选 择也不相 同, 当 v 、 f每齿进给量 f 和刀具齿数 z之 间有这样 一个 关系式:。 z 加工 的工件为粗 加工时, 在保证加 工成 本的前提下尽量提高生 粗加工对工件表面质量 的要求不高, 在切削中刀杆、 床、 机 产 效率。因此在 背吃刀量的选择上要尽可能的加大, 进给量 的 刀片、 工件 等工具的刚度就决 定了走 刀的进 给量 , 因此进 给量
精确度和 自动化程 度都 比较高, 属于机 电一体化 的加工设备 。
在进行粗 加工时, 在保证精加工和半精加工所 需加工余量
数控加工需要把加工零件的图纸作为加工依据来设置相应 的工 的前 提下, 用走 刀一次性将 多余余 量削除, 当余量过 大或者 背 艺, 程序员将工 艺参数编织 为加工程序 输入 程序控 制系统, 控 吃刀量超 出了工艺系统 刚性范围时, 刀切除尽可能的由大 到 走 制 系统会控 制相应 的工件、工具对 零件进行加 工。 但是 , 控 小, 别是第_刀应该让刀 口尽量靠近 里层 , 数 特 这样可以提高工件 机 床加工中的数控编程仍然 是个 急需解决 的问题 , 程序 员根据 表面的平整度 , 同时也可 以减 少接触硬 皮铸 锻件。 若工艺系 统 工艺要求 编写加工程序 时需要处于人机交互 的状态, 这样确定 的刚度较差或者冲 击载荷较大, 作者可降低背吃刀量 从而减 操 的切削用量才 能将误差 降至最低 。 以编程员在数 控编程 中起 小切 削力 。 所 着关键性 的作用, 必须具有一定的实践经验和 切削用量 的确定 当零 件需要进行精加工时, 背吃刀量 选择是根 据粗加工后 原则 , 数控机床 的应 用不仅保证了加工质量 且保证了加工 的效 的加 工余量确定的, 在加工过 程中可逐渐 降低背 吃刀量 , 样 这 率, 是促进数控机床 的产业化实现企业 生产水平和经济效益提 不仅可以提高加工质量还可 以提高加工精度。 在进 行精加工时
切削用量的合理选择
切削用量的合理选择切削用量的合理选择(2021-07-1315:37:22)标签:刀具寿命用量生产率切削性能杂谈分类:数控刀具技术切削用量不仅就是在机床调整前必须确认的关键参数,而且其数值合理是否对加工质量、加工效率、生产成本等有著非常关键的影响。
所谓“合理的”切削用量就是指充分利用刀具切削性能和机床动力性能够(功率、扭矩),在保证质量的前提下,赢得低的生产率和高的加工成本的切削用量。
一制订切削用量时考虑的因素切削加工生产率在焊接加工中,金属切除率与切削用量三要素ap、f、v均维持线性关系,即为其中任一参数减小一倍,都可以并使生产率提升一倍。
然而由于刀具寿命的制约,当任一参数减小时,其它二参数必须增大。
因此,在制定切削用量时,三要素获得最佳女团,此时的高生产率才就是合理的。
刀具寿命切削用量三要素对刀具寿命影响的大小,按顺序为v、f、ap。
因此,从保证合理的刀具寿命出发,在确定切削用量时,首先应采用尽可能大的背吃刀量;然后再选用大的进给量;最后求出切削速度。
加工表面粗糙度精加工时,减小进给量将减小加工表面粗糙度值。
因此,它就是精加工时遏制生产率提升的主要因素。
二刀具寿命的选择原则切削用量与刀具寿命存有密切关系。
在制订切削用量时,应当首先挑选合理的刀具寿命,而合理的刀具寿命则应当根据优化的目标而的定。
通常分后最低生产率刀具寿命和最高成本刀具寿命两种,前者根据单件工时最少的目标确认,后者根据工序成本最高的目标确认。
挑选刀具寿命时可以考量如下几点:根据刀具复杂程度、制造和磨刀成本来选择。
复杂和精度高的刀具寿命应选得比单刃刀具高些。
对于机夹可以移调刀具,由于再加刀时间长,为了充分发挥其切削性能,提升生产效率,刀具寿命附加得高些,通常挑15-30min。
对于装刀、换刀和调刀比较复杂的多刀机床、组合机床与自动化加工刀具,刀具寿命应选得高些,尤应保证刀具可靠性。
车间内某一工序的生产率管制了整个车间的生产率的提升时,该工序的刀具寿命必须挑选得高些;当某工序单位时间内所分摊至的全厂支出m很大时,刀具寿命也高文瑞得高些。
- 1、下载文档前请自行甄别文档内容的完整性,平台不提供额外的编辑、内容补充、找答案等附加服务。
- 2、"仅部分预览"的文档,不可在线预览部分如存在完整性等问题,可反馈申请退款(可完整预览的文档不适用该条件!)。
- 3、如文档侵犯您的权益,请联系客服反馈,我们会尽快为您处理(人工客服工作时间:9:00-18:30)。
数控加工中切削用量的合理选择【摘要】文章介绍了切削用量的三要素,并对数控机床加工时切削用量的合理选择进行了详细阐述,为数控机床编程与操作人员提供参考。
【关键词】切削用量;加工质量;刀具耐用度;选择原则。
前言:数控加工中切削用量的原则是,粗加工时,一般以提高生产率为主,但也应考虑经济和加工成本;半精加工和精加工时,应在保证加工质量的前提下,兼顾切削效率、经济性和加工成本。
具体数值应根据机床说明书、切削用量手册,并结合经验而定。
切削用量是表示机床主运动和进给运动大小的重要参数。
切削用量的确定是数控加工工艺中的重要内容,切削用量的大小对加工效率、加工质量、刀具磨损和加工成本均有显著影响一、切削用量的选择原则数控加工中选择切削用量,就是在保证加工质量和刀具耐用度的前提下,充分发挥机床性能和刀具切削性能,使切削效率最高,加工成本最低。
(一) 加工质量:加工质量分为加工精度和加工表面质量。
⒈加工精度是指零件加工后实际几何参数(尺寸、形状和位置)与理想几何参数相符的程度。
符合程度愈高,加工精度愈高。
实际值与理想值之差称为加工误差,所谓保证加工精度,即指控制加工误差。
⑴尺寸精度:加工表面的实际尺寸与设计尺寸的尺寸误差不超过一定的尺寸公差范围。
在国标中尺寸公差分20级(IT01、IT0、IT1~IT18)。
尺寸精度的获得方法:①试切法:试切——测量——调整——再试切。
用于单件小批生产。
②调整法:通过预调好的机床、夹具、刀具、工件,在加工中自行获得尺寸精度。
用于成批大量生产。
③尺寸刀具法:用一定形状和尺寸的刀具加工获得。
生产率高,但刀具制造复杂。
④自动控制法:用一定装置,边加工边自动测量控制加工。
切削测量补偿调整。
⑵几何形状精度:加工表面的实际几何要素对理想几何要素的变动量不超过一定公差范围。
在国标中形状公差有六项:直线度、平面度、圆度、圆柱度、线轮廓度、面轮廓度。
几何形状精度的获得方法:成形运动法①轨迹法:利用刀具与工件间的相对运动轨迹来获得形状。
②成形法:利用成形刀具加工获得表面形状。
③展成法:利用刀具与工件相对运动使工件被刀具切削成一定形状的包络线。
非成形运动法:人工修配、样板加工、划线加工等。
⑶相互位置精度:加工表面的实际几何要素对由基准确定方向或位置的理想几何要素的变动量。
在国标中位置公差有八项:平行度、垂直度、倾斜度、同轴度、对称度、位置度、圆跳动、全跳动。
相互位置精度的获得主要由机床精度、夹具精度和工件的装夹精度来保证。
⒉加工表面质量是指表面几何形状和表面层的物理力学性能。
表面几何形状包括表面粗糙度,表面波度,宏观几何形状偏差。
表面层的物理力学性能包括表面层冷作硬化,表面层残余应力,表面层金相组织的变化 。
(二) 刀具耐用度T :所谓刀具耐用度是指刃磨后的刀具从开始切削至达到磨钝标准时,所用的切削时间。
影响刀具耐用度的因素,归纳起来可以分为五个方面:切削用量,刀具的几何参数,工件材料,刀具材料,刀具的刃磨质量和润滑冷却条件。
⒈切削用量:切削用量包括切削速度V( 主轴转速S) 、进给量F 、背吃刀量ap ,通常称为切削用量三要素。
切削用量对刀具耐用度的影响可用如下关系式表达:p p n m Ta f v C T 111= 0111>>>p n m (式中C T 是刀具耐用度系数) 由上式看出,切削速度对刀具耐用度影响最大,进给量次之,背吃刀量影响最小。
例如用YT15硬质合金车刀,以f=0.3~0.75的进给量车削σb=7.5kgf/mm 的碳素钢时,当切削速度v 增大一倍时,刀具耐用度下降97%;进给量f 增大一倍时,刀具耐用度下降70%,而背吃刀量ap 增大一倍时,刀具耐用度下降仅40%左右,因此当确定了刀具耐用度的合理值后,应首先考虑增大背吃刀量ap ,然后根据加工条件和加工要求选择尽可能大的进给量和切削速度。
⒉刀具几何参数:刀具几何参数对刀具耐用度有较显著的影响,是刀具几何参数合理、先进与否的重要标志之一。
⑴前角γo :前刀面与基面间的夹角即为前角。
前对刀具耐用度的影响很明显,如太大,刃口锋利,切屑变小,切削力小,切削轻快,但刀刃的强度降低,散热差,且易破损;如太小又使切削力和切削温度增加过多,在这两种情况下耐用度都会下降,前角γo 对刀具耐用度的影响呈“驼峰形”,它的峰顶前角耐用度最高。
⑵主偏角Kr :主切削刃与进给方向间的夹角即为主偏角。
主偏角减小,刀具强度增加,改善散热条件,耐用度增高。
⑶副偏角Kr ':副切削刃与进给反方向间的夹角即为负偏角。
负偏角主要影响已加工表面的粗糙度和刀尖强度,若减小Kr ',则表面的粗糙度降低,刀具强度增加,但Kr '过小,会使副切削刃与已加工面的摩擦增加,引起震动,降低表面质量。
适当减小负偏角和增大刀尖圆弧半径都能提高刀具强度,改善散热条件,使刀具耐用度提高。
⒊工件材料:工件材料的强度、硬度越高,产生的切削温度越高,故刀具磨损越快,刀具耐用度越低。
切削碳素结构钢时,钢的含碳量对刀具耐用度有较大的影响。
含碳量越高,渗碳体和珠光体的比重就越大,硬度就越高,刀具的磨损也就越快。
因此切削高碳钢时刀具磨损较快,耐用度较低;切削中碳钢时刀具磨损就相对较慢,耐用度也相对较高。
此外加工材料的延伸率越大或导热系数越低,均能使切削温度升高,刀具耐用度降低。
⒋刀具材料:刀具材料的种类很多,常用的有工具钢(碳素工具钢、合金工具钢和高速钢)、硬质合金、陶瓷、金刚石和立方氮化硼等。
碳素工具钢和合金工具钢,因耐热性很差,只宜作手工刀具。
陶瓷、金刚石和立方氮化硼,由于质脆、工艺性差及价格昂贵等原因,仅在较小的范围内使用。
目前最常用的刀具材料是高速钢和硬质合金。
刀具切削部分材料是影响刀具耐用度的主要因素,改善刀具材料的切削性能,使用高,就越耐磨,耐用度也越高。
⒌刀具刃磨质量和冷却润滑条件:⑴刀具的刃磨质量对刀具的耐用度有很大的影响。
如硬质合金刀具用碳化硅(SiC)砂轮刃磨后,若不用细油石研磨,则由于刀刃有锯齿状的微小缺口、前后刀面表面粗糙度较高等原因,刀具的磨损较快,耐用度低,有时还易崩刃。
实践表明,经过仔细研磨的车刀,耐用度可比未研磨的提高50%左右。
⑵切削液分为水基冷却润滑液和油基冷却润滑液,水基冷却润滑液主要起冷却作用,油基冷却润滑液主要起润滑作用。
使用切削液能降低切削区的温度并减少刀具与工件、刀具与切屑间的摩擦,对提高刀具耐用度是有利的。
实验表明,用乳化液(水基冷却润滑液的一种)能降低切削区温度50℃~100℃,用切削油能降低切削区温度40℃~60℃。
所以,高速钢刀具在切削负荷较重的条件下,则多用水基冷却润滑液,切削负荷较轻而精度较高和表面粗糙度要求较低的条件下则多用油基润滑液,使刀具与工件表面间形成润滑膜,减少摩擦。
硬质合金刀具耐热性较好,一般可以不用切削液,但在用高温合金加工一般钢料的精加工中,为了提高刀具的耐用度,保证加工精度和表面粗糙度,也可以用乳化液或极压切削油进行冷却润滑。
综上所述,我们在分析清楚影响刀具耐用度的这些因素及它们之间的相互关系后,可先根据工件材料的具体情况,选用适宜的刀具材料和切削用量,选择合适的刀具几何参数,保证刀具的刃磨质量和冷却润滑条件,以保障较高的刀具耐用度。
(三) 粗、精加工时切削用量的选择原则:⒈粗加工时,一般以提高生产效率为主(较高的金属切除率),但也应考虑经济性和加工成本(必要的刀具耐用度)。
切削用量的选择原则首先选取尽可能大的背吃刀量;其次要根据机床动力和刚性的限制条件等,选取尽可能大的进给量;最后根据刀具耐用度确定最佳的切削速度。
增大背吃刀量可使走刀次数减少,增大进给量有利于断屑。
⒉半精加工和精加工时, 应在保证加工质量的前提下,兼顾切削效率、经济性和加工成本。
切削用量的选择原则首先根据粗加工后的余量确定背吃刀量;其次根据已加工表面的粗糙度要求,选取较小的进给量;最后在保证刀具耐用度的前提下,尽可能选取较高的切削速度。
具体数值应根据机床说明书、切削用量手册,并结合实践经验而定。
⑴背吃刀量ap(mm)背吃刀量ap根据加工余量和工艺系统的刚度确定。
在机床、工件和刀具刚度允许的情况下,ap就等于加工余量, 这是提高生产率的一个有效措施。
为了保证零件的加工精度和表面粗糙度,一般应留一定的余量进行精加工。
数控机床的精加工余量可略小于普通机床。
具体选择如下:粗加工时,在留下精加工、半精加工的余量后,尽可能一次走刀将剩下的余量切除;若工艺系统刚性不足或余量过大不能一次切除,也应按先多后少的不等余量法加工。
第一刀的ap应尽可能大些,使刀口在里层切削,避免工件表面不平及有硬皮的铸锻件。
当冲击载荷较大(如断续表面)或工艺系统刚度较差(如细长轴、镗刀杆、机床陈旧)时,可适当降低ap,使切削力减小。
精加工时,ap应根据粗加工留下的余量确定,采用逐渐降低ap的方法,逐步提高加工精度和表面质量。
一般精加工时,取ap=0.05~0.8mm;半精加工时,取ap=1.0~3.0mm。
⑵切削宽度ae(mm)一般ae与刀具直径D成正比,与背吃刀量ap成反比。
在数控加工中,一般ae的取值范围为ae=(0.6~0.9)D。
⑶进给量(进给速度)F(mm/min或mm/r)进给量( 进给速度)是数控机床切削用量中的重要参数,根据零件的表面粗糙度、加工精度要求、刀具及工件材料等因素,参考切削用量手册选取。
对于多齿刀具,其进给量F、刀具转速n、刀具齿数z及每齿进给量fz的关系为F= n×z ×fz。
粗加工时, 由于对工件表面质量没有太高的要求,F主要受刀杆、刀片、机床、工件等的强度和刚度所承受的切削力限制,一般根据刚度来选择。
工艺系统刚度好时,可用大些的F;反之,适当降低F。
半精加工、精加工时,F应根据工件的表面粗糙度Ra要求选择。
Ra要求小的,取较小的F,但又不能过小,因为F过小,切削厚度hD过薄,Ra反而增大,且刀具磨损加剧。
刀具的副偏角愈大,刀尖圆弧半径愈大,则F可选较大值。
还应注意零件加工中的某些特殊因素。
比如在轮廓加工中,选择进给量时,应考虑轮廓拐角处的超程问题。
特别是在拐角较大、进给速度较高时,应在接近拐角处适当降低进给速度,在拐角后逐渐升速,以保证加工精度。
⑷切削速度V(m/min)根据已经选定的背吃刀量、进给量及刀具耐用度选择切削速度。
可用经验公式计算,也可根据生产实践经验在机床说明书允许的切削速度范围内查表选取或者参考有关切削用量手册选用。
在选择切削速度时,还应考虑:应尽量避开积屑瘤产生的区域;断续切削时,为减小冲击和热应力,要适当降低切削速度;在易发生振动的情况下,切削速度应避开自激振动的临界速度;加工大件、细长件和薄壁工件时, 应选用较低的切削速度;加工带外皮的工件时,应适当降低切削速度;工艺系统刚性差的,应减小切削速度。