卧式数控车床如何合理选择切削用量
合理选择切削用量
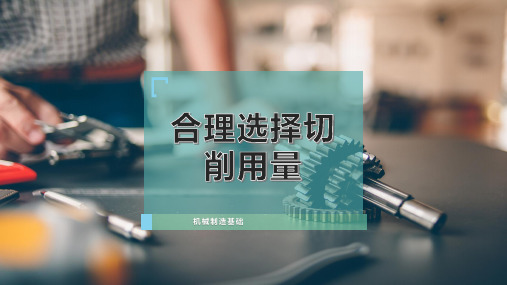
16
课堂实训——选择切削用量
机械制造基础
3)确定切削速度 vc 根据已知条件和已确定的 ap 和 f 值,由P139-140页表得切削速度 vc 130~160 m/min。由于该轴为
细长轴,应选取较小的切削速度,因此切削速度 vc 130 m/min。计算机床转速为
n 1 000vc 1 000 130 1 035 r/min πd 3.14 40
70~80
背吃刀量 ap/(mm)
2~6 进给量 f /(mm/r)
0.3~0.6
切削速度 vc /(m/min)
100~120 90~110 70~90 70~90 50~70 60~80 60~70
6~10
0.6~1
70~90 60~80 50~70 50~70 40~60 50~70 50~60
0.4~0.7 0.6~0.9
0.4~0.6
跳到 P144
5
二、进给量的选择
机械制造基础
续表
铸铁及 铜合金
16×25
20×30 25×25
40
0.4~0.5
60
0.6~0.8
0.5~0.8
0.4~0.6
100
0.8~1.2
0.7~1
0.6~0.8
0.5~0.7
400
1~1.4
1~1.2
0.8~1
0.6~0.8
寸为 46 mm×350 mm,加工尺寸为 39 mm×300 mm。在普通卧式车床CA6140上加工,使用焊接式硬
质合金YT15车刀,刀杆截面尺寸为16 mm×25 mm,刀具几何参数为
o 15,o 8,r 75, s 0,rε 1 mm,br1 0,
数控加工中切削用量的合理选择汇总
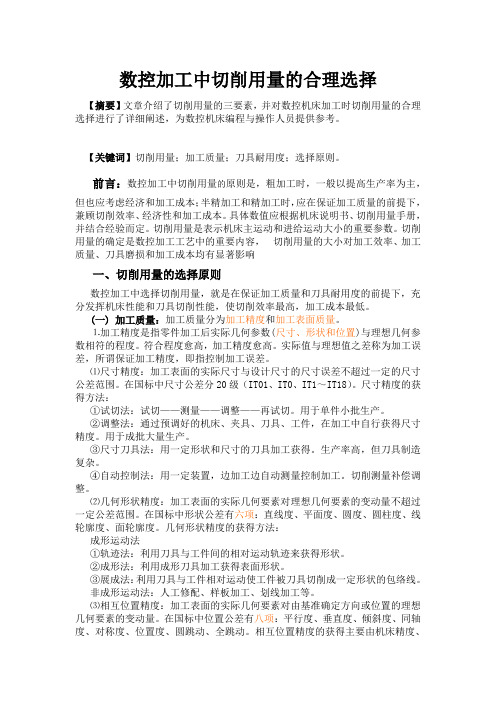
数控加工中切削用量的合理选择【摘要】文章介绍了切削用量的三要素,并对数控机床加工时切削用量的合理选择进行了详细阐述,为数控机床编程与操作人员提供参考。
【关键词】切削用量;加工质量;刀具耐用度;选择原则。
前言:数控加工中切削用量的原则是,粗加工时,一般以提高生产率为主,但也应考虑经济和加工成本;半精加工和精加工时,应在保证加工质量的前提下,兼顾切削效率、经济性和加工成本。
具体数值应根据机床说明书、切削用量手册,并结合经验而定。
切削用量是表示机床主运动和进给运动大小的重要参数。
切削用量的确定是数控加工工艺中的重要内容,切削用量的大小对加工效率、加工质量、刀具磨损和加工成本均有显著影响一、切削用量的选择原则数控加工中选择切削用量,就是在保证加工质量和刀具耐用度的前提下,充分发挥机床性能和刀具切削性能,使切削效率最高,加工成本最低。
(一) 加工质量:加工质量分为加工精度和加工表面质量。
⒈加工精度是指零件加工后实际几何参数(尺寸、形状和位置)与理想几何参数相符的程度。
符合程度愈高,加工精度愈高。
实际值与理想值之差称为加工误差,所谓保证加工精度,即指控制加工误差。
⑴尺寸精度:加工表面的实际尺寸与设计尺寸的尺寸误差不超过一定的尺寸公差范围。
在国标中尺寸公差分20级(IT01、IT0、IT1~IT18)。
尺寸精度的获得方法:①试切法:试切——测量——调整——再试切。
用于单件小批生产。
②调整法:通过预调好的机床、夹具、刀具、工件,在加工中自行获得尺寸精度。
用于成批大量生产。
③尺寸刀具法:用一定形状和尺寸的刀具加工获得。
生产率高,但刀具制造复杂。
④自动控制法:用一定装置,边加工边自动测量控制加工。
切削测量补偿调整。
⑵几何形状精度:加工表面的实际几何要素对理想几何要素的变动量不超过一定公差范围。
在国标中形状公差有六项:直线度、平面度、圆度、圆柱度、线轮廓度、面轮廓度。
几何形状精度的获得方法:成形运动法①轨迹法:利用刀具与工件间的相对运动轨迹来获得形状。
切削用量的确定

总之,切削用量的具体数值应根机床性 能、相关的手册并结合实际经验用类比方 法确定。同时,使主轴转速、切削深度及 进给速度三者能相互适应,以形成最佳切 削用量。
2.进给速度的确定 进给速度是数控机 床切削用量中的重要参数,主要根据零件 的加工精度和表面粗糙度要求以及刀具、 工件的材料性质选取。最大进给速度受机 床刚度和进给系统的性能限制。确定进给 速度的原则:
1)当工件的质量要求能够得到保证时, 为提高生产效率,可选择较高的进给速度。 一般在100200mm/min范围内选取。
1.主轴转速的确定主轴转速应根据允许的 切削速度和工件(或刀具)直径来选择。 其计算公式为: n=1000v/πD 式中 v---切削速度,单位为m/min,由刀具的耐用 度决定;n-- -主轴转速,单位为 r/min; D----工件直径或刀具直径,单位为mm。 计算的主轴转速n最后要根据机床说明书选 取机床有的或较接近的转速。
2)在切断、加工深孔或用高速钢刀具加 工时,宜选择较低的进给速度,一般在 20~50mm/min范围内选取。
高时,进给速度应选小些,一般在20~ 50mm/min范围内选取。
3)刀具空行程时,特别是远距离“回零” 时,可以设定该机床数控系统设定的最高 进给速度。
3.背吃刀量确定 背吃刀量根据机床、 工件和刀具的刚度来决定,在刚度允许的 条件下,应尽可能使背吃刀量等于工件的
切削用量的确定
数控编程时,编程人员必须确定每道 工序的切削用量,并以指令的形式写入程 序中。切削用量包括主轴转速、背吃刀量 及进给速度等。对于不同的加工方法,需 要选用不同的切削用量。切削用量的选择 原则是:保证零件加工精度和表面粗糙度, 充分发挥刀具切削性能,保证合理的刀具 耐用度;并充分发挥机床的性能,最大限 度提高生产率,降低成本。
数控车削中切削用量的选择
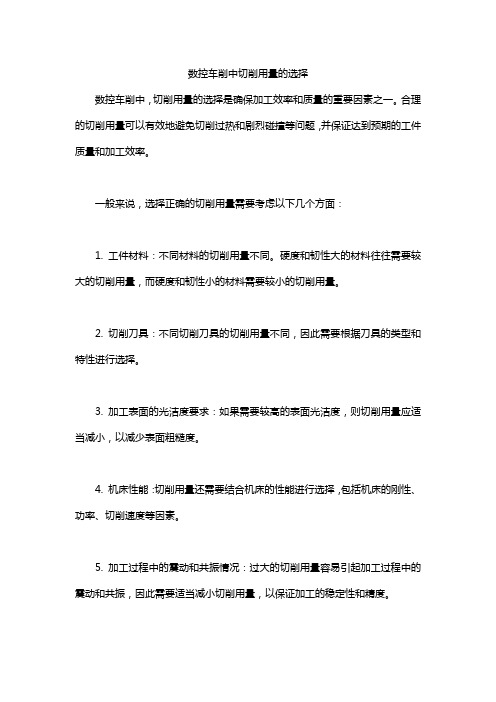
数控车削中切削用量的选择
数控车削中,切削用量的选择是确保加工效率和质量的重要因素之一。
合理的切削用量可以有效地避免切削过热和剧烈碰撞等问题,并保证达到预期的工件质量和加工效率。
一般来说,选择正确的切削用量需要考虑以下几个方面:
1. 工件材料:不同材料的切削用量不同。
硬度和韧性大的材料往往需要较大的切削用量,而硬度和韧性小的材料需要较小的切削用量。
2. 切削刀具:不同切削刀具的切削用量不同,因此需要根据刀具的类型和特性进行选择。
3. 加工表面的光洁度要求:如果需要较高的表面光洁度,则切削用量应适当减小,以减少表面粗糙度。
4. 机床性能:切削用量还需要结合机床的性能进行选择,包括机床的刚性、功率、切削速度等因素。
5. 加工过程中的震动和共振情况:过大的切削用量容易引起加工过程中的震动和共振,因此需要适当减小切削用量,以保证加工的稳定性和精度。
选择合适的切削用量可以帮助实现加工效率和质量的平衡,提高数控车削加工的效率和质量。
数控机床加工的切削用量

数控机床加工的切削用量数控机床加工的切削用量包括切削速度V c (或主轴转速n)、切削深度a p 和进给量f ,其选用原则与普通机床基本相似,合理选择切削用量的原则是:粗加工时,以提高劳动生产率为主,选用较大的切削量;半精加工和精加工时,选用较小的切削量,保证工件的加工质量。
1. 数控车床切削用量 1)切削深度a p在工艺系统刚性和机床功率允许的条件下,尽可能选取较大的切削深度,以减少进给次数。
当工件的精度要求较高时,则应考虑留有精加工余量,一般为0.1~0.5mm 。
切削深度ap计算公式:a p =式中: d w —待加工表面外圆直径,单位mm d m —已加工表面外圆直径,单位mm. 2)切削速度Vc① 车削光轴切削速度V c 光车切削速度由工件材料、刀具的材料及加工性质等因素所确定,表1为硬质合金外圆车刀切削速度参考表。
切削速度Vc 计算公式: Vc=式中: d —工件或刀尖的回转直径,单位mm n —工件或刀具的转速,单位r/min表1 硬质合金外圆车刀切削速度参考表2mw d d注:表中刀具材料切削钢及灰铸铁时耐用度约为60min 。
②车削螺纹主轴转速n 切削螺纹时,车床的主轴转速受加工工件的螺距(或导程)大小、驱动电动机升降特性及螺纹插补运算速度等多种因素影响,因此对于不同的数控系统,选择车削螺纹主轴转速n 存在一定的差异。
下列为一般数控车床车螺纹时主轴转速计算公式:n≤–k式中:p—工件螺纹的螺距或导程,单位mm。
k—保险系数,一般为80。
3)进给速度进给速度是指单位时间内,刀具沿进给方向移动的距离,单位为mm/min,也可表示为主轴旋转一周刀具的进给量,单位为mm/r。
⑴确定进给速度的原则①当工件的加工质量能得到保证时,为提高生产率可选择较高的进给速度。
②切断、车削深孔或精车时,选择较低的进给速度。
③刀具空行程尽量选用高的进给速度。
④进给速度应与主轴转速和切削深度相适应。
⑵进给速度V f的计算 V f = n f式中:n—车床主轴的转速,单位r/min。
数控机床加工的切削用量

数控机床加工的切削用量包括切削速度V c (或主轴转速n)、切削深度a p 和进给量f ,其选用原则与普通机床基本相似,合理选择切削用量的原则是:粗加工时,以提高劳动生产率为主,选用较大的切削量;半精加工和精加工时,选用较小的切削量,保证工件的加工质量。
1. 数控车床切削用量 1)切削深度a p在工艺系统刚性和机床功率允许的条件下,尽可能选取较大的切削深度,以减少进给次数。
当工件的精度要求较高时,则应考虑留有精加工余量,一般为0.1~0.5mm 。
切削深度ap计算公式:a p =式中: d w —待加工表面外圆直径,单位mm d m —已加工表面外圆直径,单位mm. 2)切削速度Vc① 车削光轴切削速度V c 光车切削速度由工件材料、刀具的材料及加工性质等因素所确定,表1为硬质合金外圆车刀切削速度参考表。
切削速度Vc 计算公式: Vc=式中: d —工件或刀尖的回转直径,单位mm n —工件或刀具的转速,单位r/min表1 硬质合金外圆车刀切削速度参考表2mw d d注:表中刀具材料切削钢及灰铸铁时耐用度约为60min。
②车削螺纹主轴转速n切削螺纹时,车床的主轴转速受加工工件的螺距(或导程)大小、驱动电动机升降特性及螺纹插补运算速度等多种因素影响,因此对于不同的数控系统,选择车削螺纹主轴转速n存在一定的差异。
下列为一般数控车床车螺纹时主轴转速计算公式:n≤–k式中:p—工件螺纹的螺距或导程,单位mm。
k—保险系数,一般为80。
3)进给速度进给速度是指单位时间内,刀具沿进给方向移动的距离,单位为mm/min,也可表示为主轴旋转一周刀具的进给量,单位为mm/r。
⑴确定进给速度的原则①当工件的加工质量能得到保证时,为提高生产率可选择较高的进给速度。
②切断、车削深孔或精车时,选择较低的进给速度。
③刀具空行程尽量选用高的进给速度。
④进给速度应与主轴转速和切削深度相适应。
⑵进给速度V f的计算 V f = n f式中:n—车床主轴的转速,单位r/min。
如何选择合适的切削用量?
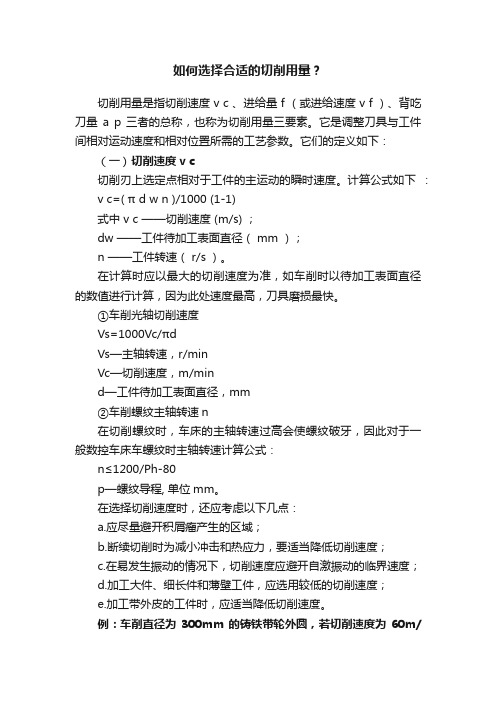
如何选择合适的切削用量?切削用量是指切削速度 v c 、进给量 f (或进给速度 v f )、背吃刀量a p 三者的总称,也称为切削用量三要素。
它是调整刀具与工件间相对运动速度和相对位置所需的工艺参数。
它们的定义如下:(一)切削速度 v c切削刃上选定点相对于工件的主运动的瞬时速度。
计算公式如下:v c=( π d w n )/1000 (1-1)式中 v c ——切削速度 (m/s) ;dw ——工件待加工表面直径( mm );n ——工件转速( r/s )。
在计算时应以最大的切削速度为准,如车削时以待加工表面直径的数值进行计算,因为此处速度最高,刀具磨损最快。
①车削光轴切削速度Vs=1000Vc/πdVs—主轴转速,r/minVc—切削速度,m/mind—工件待加工表面直径,mm②车削螺纹主轴转速n在切削螺纹时,车床的主轴转速过高会使螺纹破牙,因此对于一般数控车床车螺纹时主轴转速计算公式:n≤1200/Ph-80p—螺纹导程, 单位mm。
在选择切削速度时,还应考虑以下几点:a.应尽量避开积屑瘤产生的区域;b.断续切削时为减小冲击和热应力,要适当降低切削速度;c.在易发生振动的情况下,切削速度应避开自激振动的临界速度;d.加工大件、细长件和薄壁工件,应选用较低的切削速度;e.加工带外皮的工件时,应适当降低切削速度。
例:车削直径为300mm的铸铁带轮外圆,若切削速度为60m/min,试求车床主轴转速。
解:根据公式Vs=1000Vc/πd=1000 ×60/3.14 ×300=63.69r/min注意:在实际生产中,理论上计算出的主轴转数应从车床转速表中最接近的一档选取。
(二)进给量 f工件或刀具每转一周时,刀具与工件在进给运动方向上的相对位移量。
进给速度v f 是指切削刃上选定点相对工件进给运动的瞬时速度。
v f=fn ( 1-2 )式中 v f ——进给速度( mm/s );n ——主轴转速( r/s );f ——进给量( mm )。
数控切削用量的选择方法
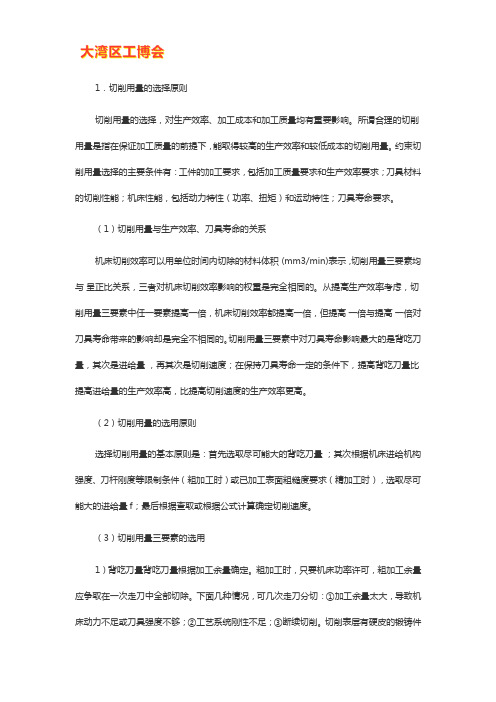
1.切削用量的选择原则切削用量的选择,对生产效率、加工成本和加工质量均有重要影响。
所谓合理的切削用量是指在保证加工质量的前提下,能取得较高的生产效率和较低成本的切削用量。
约束切削用量选择的主要条件有:工件的加工要求,包括加工质量要求和生产效率要求;刀具材料的切削性能;机床性能,包括动力特性(功率、扭矩)和运动特性;刀具寿命要求。
(1)切削用量与生产效率、刀具寿命的关系机床切削效率可以用单位时间内切除的材料体积 (mm3/min)表示,切削用量三要素均与呈正比关系,三者对机床切削效率影响的权重是完全相同的。
从提高生产效率考虑,切削用量三要素中任一要素提高一倍,机床切削效率都提高一倍,但提高一倍与提高一倍对刀具寿命带来的影响却是完全不相同的。
切削用量三要素中对刀具寿命影响最大的是背吃刀量,其次是进给量,再其次是切削速度;在保持刀具寿命一定的条件下,提高背吃刀量比提高进给量的生产效率高,比提高切削速度的生产效率更高。
(2)切削用量的选用原则选择切削用量的基本原则是:首先选取尽可能大的背吃刀量;其次根据机床进给机构强度、刀杆刚度等限制条件(粗加工时)或已加工表面粗糙度要求(精加工时),选取尽可能大的进给量f;最后根据查取或根据公式计算确定切削速度。
(3)切削用量三要素的选用1)背吃刀量背吃刀量根据加工余量确定。
粗加工时,只要机床功率许可,粗加工余量应争取在一次走刀中全部切除。
下面几种情况,可几次走刀分切:①加工余量太大,导致机床动力不足或刀具强度不够;②工艺系统刚性不足;③断续切削。
切削表层有硬皮的锻铸件或切削冷硬倾向较为严重的材料(例如不锈钢)时,应尽量使值超过硬皮或冷硬层深度,以防刀具过快磨损。
半精加工时,可取为0.5~2mm 。
精加工时,可取0.1~0.4 。
2)进给量粗加工时,对表面质量没有太高要求,合理的进给量应是工艺系统所能承受的最大进给量。
限制粗加工进给量的因素是:机床进给机构的强度、刀杆的强度和刚度、硬质合金或陶瓷刀片的强度等。
- 1、下载文档前请自行甄别文档内容的完整性,平台不提供额外的编辑、内容补充、找答案等附加服务。
- 2、"仅部分预览"的文档,不可在线预览部分如存在完整性等问题,可反馈申请退款(可完整预览的文档不适用该条件!)。
- 3、如文档侵犯您的权益,请联系客服反馈,我们会尽快为您处理(人工客服工作时间:9:00-18:30)。
卧式数控车床如何合理选择切削用量本文就卧式数控车床如何合理选择切削用量进行探讨。
一. 原始资料:无论编制加工工序卡-即制定工艺方案还是调装设计都需要掌握以下资 料,做为刀具选择.卡具设计以及选择切削用量的依据。
1 工件图:包括形状.尺寸.公差.形位公差.粗糙度和其他技术要求。
特别强调的是本序 加工的部位必须明确,用于及可能影响装卡部位的形状要表示清楚。
2.毛坯图:毛坯形状.尺寸,加工余量,材料.硬度等。
3.生产纲领:即年产量或单件时间,这对招标项目尤为重要。
4.验收要求:机床验收时对工件考核什麽项目,有无Cp 值和其它要求。
5.用户对工件定位基准.卡紧面.辅助支承 等要求,或指定参考的卡具样式。
6. 对刀具选择要求:用国产刀具或国外指定厂家 的刀具,特殊刀具是否自备等。
7. 用户单位,件名.件号等也应标明,以便管理。
二 选择切削用量的原则:1. 总的要求:保证安全,不致发生人身事故或设备事故;保证加工质量。
在上述 两项要求的前提下充分发挥机床的潜力和刀具的切削性能,选用较大的切削用量以提高生产率;不应超负荷工作,不能产生过大的变形和震动。
2. 一般原则:切削用量选择的原则是提高生产率,即切削时间缩短。
切削时间可按下式计算: . (min)1000pp a f V DL a f n L t ⨯⨯⨯⨯⨯⨯=⨯⨯=πδδ………(1) 式中: L -每次走刀的行程长度 (mm )δ-工件单边总余量 (mm )n -主轴转数 (r/min ) D -工件直径 (mm ) αp -吃刀深 (mm ) f -进给量 (mm/r ) V -切削速度 (m/ min )从(1)式中可知要使切削时间最短,必须使 V ,f, αp 的乘积为最大。
提高 V ,f, αp 都能提高生产率,且影响程度都是一样的。
但是对刀具耐用度的影响三者是不相同的。
切削用量与刀具耐用度的一般关系式为:式中: C R -刀具耐用度系数,与刀具. 工件材料和切削条件有关。
X.Y.Z -指数,分别表示各切削用量对刀具耐用度的影响程度。
用YT5硬质合金车刀切削σb =0.637GP α的低碳钢(f>0.7mm/r )切削用量与刀具耐用度的关 系为:T =75.025.25pRfV C α⨯⨯ (3)从(3)式中可以看出,切削速度V 对刀具耐用度的影响最大,进给量f 次之,吃刀深αp 影响最小。
这与三者对切削温度的影响完全一致。
反映出切削温度 对刀具耐用度有着很重要的影响。
在优选切削用量以提高生产率时,其选择顺序应为:首先尽量选用最大吃刀深αp 然后根据加工条件选用最大的进给量f ,最后才在刀具耐用度或机床功率所允许的情况下选取最大切削速度V 。
三.吃刀深αp:一般情况下,机床工艺系统刚度允许时,粗车吃刀深在保留半精车. 精车余量后,尽量将粗车余量一次切除。
如果总加工余量太大,一次切去所有加工余量会产生明显的振动,甚至刀具强度不允许. 机床功率不够,则可分成两次或几次粗车。
但第一刀吃刀深应尽量大,以消除表面硬皮.切除沙眼气孔等缺陷,从而保护刀尖不与毛坯接触。
半精车和精车加工,其吃刀深是根据加工精度和表面粗糙度要求,由粗车后留下余量确定的。
最后一刀吃刀深不宜太小,否则会产生刮擦.对粗糙度不利。
四. 进给量f:粗车时的进给量主要考虑进给伺服电机功率.刀杆尺寸.刀片厚度.工件的直径和长度等因素。
在工艺系统刚度和强度允许的情况下,可选用较大进给量.反之适当减少。
如加工小孔.因刀杆直径小,应降低进给量。
孔深.刀杆悬伸长,则需进一步降低进给量。
由于钻头横刃钻孔进给力较大,进给量往往受到Z向伺服电机力矩制约。
半精加工和精加工的进给量受到工件加工精度和粗糙度限制,由于加工精度和粗糙度往往形成对应关系。
半精加工和精加工进给量大小的确定着眼于表面粗糙度。
表1为加工精度和粗糙度对照表,当用户图纸标注不全时可以参考。
表面粗糙度理论值Rm ax计算公式:Rm ax=100082⨯erF(μ) (4)V T m = C o (5)式中:T —刀具耐用度(min)m —指数,表示V 对T的影响程度C o—系数,与刀具.工件材料和切削条件有关上式为重要的刀具耐用度方程式,指数m表示V 对T的影响程度,耐热性愈差的刀具材料其m值愈小.则切削速度V 对刀具耐用度T的影响就愈大。
对高速钢刀具m=0.1~0.125;硬质合金刀具m=0.2~0.4;陶瓷刀具m约为0.4。
在常用的切削速度范围内公式(5)完全可以适用,但在较宽的切削速度范围内实验就不完全适用了。
刀具耐用度优化指标有三种:一是经济耐用度(最低成本耐用度),采用此种耐用度成本低有利于市场竞争,在产品初创阶段.不太畅销阶段最为适宜。
二是最大利润耐用度,宜用于产品销路畅通.供不应求时以获最大利润。
三是最大生产率耐用度,是在产品急需情况下如战时.救灾等不计成本时采用。
常规生产理应采用最大利润耐用度,但在实际应用中生产厂家往往没有明确的刀具耐用度优化指标,按班次.或观察磨损情况换刀。
一般对制造刃磨都比较简单. 成本不高的刀具耐用度可低一些,反之则高一些。
在通用机床上,资料推荐以及从用户使用情况分析,硬质合金车刀耐用度大致为60~90 min,钻头耐用度大致为80~120 min,硬质合金端铣刀耐用度大致为90~180 min。
对于装卡调正比较复杂的刀具其耐用度要高,如组合机床刀具其耐用度常为通用机床的3~9倍。
加工大型工件时,如车削很长的轴.为避免中途换刀,刀具耐用度也要高一些,可相当于中小件加工刀具其耐用度的2~3倍。
知名刀具厂商的样本对每种刀具及加工相应材料都推荐了切削速度,实用中我们根本达不到其推荐值,这是因为其所取刀具耐用度较低。
刀具厂商所取刀具耐用度大体属最大生产率耐用度,而正常生产取耐用度时间要高得多,以SANDVIK硬质合金刀片为例,该公司是以刀具耐用度15 min为准给定的切削速度,(ISCAR,株州刀具公司也是15 min,其它公司未明确)其指数m按样本数据推算该公司取m=0.25,故公式(5)表达为:V ×15 0.25 = C 0 ... ... (6)刀具耐用度在不是15 min情况下使用,切削速度就要乘上修正系数如表4:例如车削45钢:刀片材料GC4025,进给量f=0.4 mm/ r,SANDVIK样本推荐切削速度为290m/ min。
为一般用户做工艺方案时,选定刀具耐用度90 min,则V90 = 290 ×0.64 = 185 m/ min对大量生产.用户要求较高生产率的,选定刀具耐用度60 min,则V60 = 290 ×0.71 = 205 m/ min一般情况下先确定切削速度.再根据工件直径计算机床转数。
某些情况下切削速度反过来是根据机床转数确定的。
如受到机床最高转数. 最低转数.分档转数限制;卡具.中心架允许最高转数限制;以及由于工件刚度不足.尺寸过大限制了转数等。
另需强调一点,精加工和半精加工为了抑制积屑瘤的产生.提高表面加工质量,黑色金属应采用较高的切削速度(>80~100 m/ min)。
精车时车刀的磨损往往是影响加工精度的重要因素,因此除选用耐磨性较好的刀片外,还应尽可能使车刀在最佳切削速度范围工作。
六.切削用量推荐值:前述像SANDVIK等著名刀具厂商.对应各种材料,各种加工方式的刀片种类齐全,样本中有条件列出各种情况的切削用量推荐值,可参考选用或按确定的刀具耐用度折算选用。
但有的刀具厂商刀具品种不全,针对性不强,也没有完整的切削用量推荐值。
可参考下列各表选用。
硬质合金涂层刀片车削外圆端面切削用量推荐值表5车刀。
对于孔加工.由于刀杆刚度薄弱,切削用量随刀杆的长径比增加而减少。
长径比L/D>4时,要用硬质合金刀杆代替钢制刀杆。
L/D>6时则应用防振刀杆。
钻孔采用高速钢钻头时,一般用外部冷却。
其切削用量与钻头直径有关.与长径比L/D 有关。
在L/D≤3,外部冷却时,推荐值如表7。
钻孔采用硬质合金钻头时,其切削用量推荐值如表8,9。
硬质合金钻头L/D≤3钻孔(外部冷却)切削用量推荐值表8用内冷却硬质合金钻头时,可提高切削速度其切削用量推荐值如表9。
当采用硬质合金可换刀片钻头其切削速度更高,但进给量有所减小。
见各厂商刀具样本。
经镗孔或扩孔后铰孔,其加工余量不能太大:2αp =0.06~0.30mm切削速度要低,进给量要大。
加工钢件切削速度V=1.5~5 m/ min,进给量f=0.3~2.0mm;加工铸件切削速度V=8~10 m/ min,进给量f=0.5~1.0mm。
三角形刀片车螺纹.切尖槽时切削用量推荐值见表10。
机卡.切槽刀片切宽槽切削用量推荐值见表11。
三角形刀片车螺纹.切尖槽切削用量推荐值表10机卡.切槽刀片切宽槽切削用量推荐值表11深αp 要相应增加,轴向切削力作用使刀片倾斜以造成适于切削的刀具偏角。
车螺纹时螺距和牙型角决定了螺纹深度,螺纹刀尖往往比较薄弱.要求切入次数较多。
表12列出公制螺纹单刀加工外螺纹时的切入次数。
加工内螺纹时. 切入次数要增加2~3次;用陶瓷刀.以及加工不锈钢切入次数也要增加2~3次。
车梯形螺纹切入次数也可参考表12。
车蜗杆较车梯形螺纹要难些,因齿深更深,螺旋角更大还需要自制多把刀具。
有的多头蜗杆导程很大必须使用高速钢刀具在极低转数下切削,每次吃刀深应在0.1~0.2 mm范围内递减,最后一刀避免小于0.08 mm。