切削用量选择
合理选择切削用量
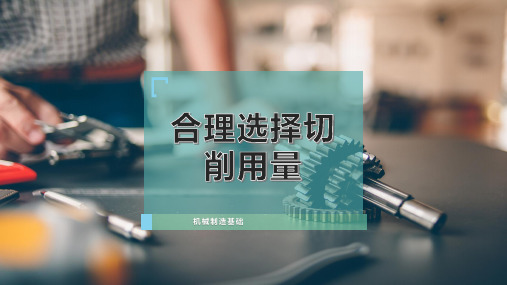
16
课堂实训——选择切削用量
机械制造基础
3)确定切削速度 vc 根据已知条件和已确定的 ap 和 f 值,由P139-140页表得切削速度 vc 130~160 m/min。由于该轴为
细长轴,应选取较小的切削速度,因此切削速度 vc 130 m/min。计算机床转速为
n 1 000vc 1 000 130 1 035 r/min πd 3.14 40
70~80
背吃刀量 ap/(mm)
2~6 进给量 f /(mm/r)
0.3~0.6
切削速度 vc /(m/min)
100~120 90~110 70~90 70~90 50~70 60~80 60~70
6~10
0.6~1
70~90 60~80 50~70 50~70 40~60 50~70 50~60
0.4~0.7 0.6~0.9
0.4~0.6
跳到 P144
5
二、进给量的选择
机械制造基础
续表
铸铁及 铜合金
16×25
20×30 25×25
40
0.4~0.5
60
0.6~0.8
0.5~0.8
0.4~0.6
100
0.8~1.2
0.7~1
0.6~0.8
0.5~0.7
400
1~1.4
1~1.2
0.8~1
0.6~0.8
寸为 46 mm×350 mm,加工尺寸为 39 mm×300 mm。在普通卧式车床CA6140上加工,使用焊接式硬
质合金YT15车刀,刀杆截面尺寸为16 mm×25 mm,刀具几何参数为
o 15,o 8,r 75, s 0,rε 1 mm,br1 0,
切削用量的选择

切削用量的选择切削速度、进给量和切削深度三者称为切削用量。
它们是影响工件加工质量和生产效率的重要因素。
车削时,工件加工表面最大直径处的线速度称为切削速度,以v(m/min)表示。
其计算公式:v=πdn/1000(m/min)式中:d——工件待加工表面的直径(mm)n——车床主轴每分钟的转速(r/min)工件每转一周,车刀所移动的距离,称为进给量,以f(mm/r)表示;车刀每一次切去的金属层的厚度,称为切削深度,以ap(mm)表示。
为了保证加工质量和提高生产率,零件加工应分阶段,中等精度的零件,一般按粗车一精车的方案进行。
粗车的目的是尽快地从毛坯上切去大部分的加工余量,使工件接近要求的形状和尺寸。
粗车以提高生产率为主,在生产中加大切削深度,对提高生产率最有利,其次适当加大进给量,而采用中等或中等偏低的切削速度。
使用高速钢车刀进行粗车的切削用量推荐如下:切削深度ap=0.8~1.5mm,进给量f=0.2~0.3mm/r,切削速度v取30~50m/min(切钢)。
粗车铸、锻件毛坯时,因工件表面有硬皮,为保护刀尖,应先车端面或倒角,第一次切深应大于硬皮厚度。
若工件夹持的长度较短或表面凸不平,切削用量则不宜过大。
粗车应留有0.5~1mm作为精车余量。
粗车后的精度为IT14-IT11,表面粗糙度Ra值一般为12.5~6.3μm。
精车的目的是保证零件尺寸精度和表面粗糙度的要求,生产率应在此前提下尽可能提高。
一般精车的精度为IT8~IT7,表面粗糙度值Ra=3.2~0.8μm,所以精车是以提高工件的加工质量为主。
切削用量应选用较小的切削深度ap=0.1~0.3mm和较小的进给量f=0.05~0.2mm/r,切削速度可取大些磨普通车刀视频。
我用数控车加工锻件,吃刀为4-6毫米,走刀0.3,转速才280.但车刀干不了四五个活就不行了请问下怎么刃磨的好?刀刃、排屑槽多宽?感觉问题应该就是在排屑槽里满意答案网友回答2014-05-03把0.3进给改0.15,不知直径多大70以下转速800,还有就是磨完刀让懂磨刀的人看看锻件毛坯是否可以利用数控车床进行粗加工,主要是轴类锻件,最大进刀量大约多少,材料45#,能用焊接刀吗?当然可以了,但是最好用现在比较先进的扒皮数控,该车床专门针对粗车设计,包括各类锻件;普通经济型数控也可以,但是一定根据产品特点下手,不可盲目进行锻件粗车;而且吃刀量以单边3-5mm为最佳;当然不是绝对,一定结合实际车削情况适当调整吃刀;,不然对机床不利;能用焊接到,但是要选用耐冲击的材料走刀F0.25转速S430用专用的刀杆个刀吧单边2.5mm可根据情况调整数控车钢件和车铸件有什么不一样,2011-05-02 17:40ni576962600|分类:职业教育|浏览477次进给,转速大概在多少知道的举个例子.......我以前是做铸件的,还有钢件精车的的一些技巧??比如粗车第一刀车多少,留多少余量精车等等?分享到:2011-05-08 14:14提问者采纳如果是45钢和50钢的话粗加工F给0.32 D至少2.5,如果不是很细的话转速要根据工件大小而定,余量精车至少要0.5,太少了车不亮精加工F给0.1左右,转速给高点如果是30MM的话我都给2500左右!这要看什么材料普通钢1mm,不锈钢20丝,直径大的转速也底,cnc机床已知车削长度2200mm,车削进给0.4mm/min,主轴转速180转,求2200mm要花多少时间车削完。
切削用量的选用原则有哪些【切削加工必知 】

切削加工中的切削速度、进给量和切削深度的总称被称为切削用量,它是生产加工中主要的工艺参数。
这个参数会严重影响到工件的加工精度和表面粗糙度,同时,对于设备、刀具以及生产效率都有严重的影响。
切削用量的选用原则都有哪些?1、一般原则切削用量要根据工件的材料、精度要求和表面粗糙度要求以及高举的材料和机床的功率与刚度情况进行选择。
同时在选择切削用量的时候,一般还要先选定切削的深度,然后选定进给量,最后确定切削速度。
2、切削深度的选择进行粗加工的时候,在留出精细加工余量之后,在机床—刀具—工件系统的刚度允许的情况下,尽可能用较少的走到次数将粗加工余量切除。
不能一次切除时,应该按照先多后少的不等余量的方法进行加工。
为了避免损坏刀具,在进行有硬皮的铸件或切削不锈钢等切削表层冷硬的材料时,要加深切削深度,最好超过硬皮或冷硬层厚度。
精加工时,为了逐步提高加工精度和表面光洁度,应采取逐步减小切削深度的方法,多次走刀、如果精加工的刀具良好,也能在一次窃取较大余量下得到高精度和较好的表面质量。
3、进给量的选择选择粗加工进给量时一般要考虑一下几个因素:(1)机床—刀具—夹具系统的刚度,如果系统刚度好,进给量可以增加,反之,进给量要小一些。
(2)卷屑还是断屑,进给量可以选择大一些,若为卷屑,则进给量应该选择小一些。
(3)断续切削还是连续切削,断切削因有冲击,考虑刀具的强度,进给量应选小些,连续切削进给量可适当选大些。
选择精加工进给量时,主要应考虑工件表面粗糙度的要求,一般粗糙度数值越小,进给量也要相应减小。
但是有时进给量过小,表面粗糙度数值反而会增大,这是由于刀具圆弧刃的切削厚度是变化的,靠副切削刃处,切削厚度比刃口圆弧半径小得多,以至于有部分金属未切除,被挤在刀具的副后面磨损成沟槽,切削一段时间后,设置可出几条沟槽,其间的距离等于进给量,所以,使工件的已加表面的粗糙度度值增大。
4、切削速度的选择选择切削速度主要应该根据工件和刀具的材料,使在已选定的切削深度和进给量的基础上达到一定的刀具耐用度。
切削 用量的合理选择
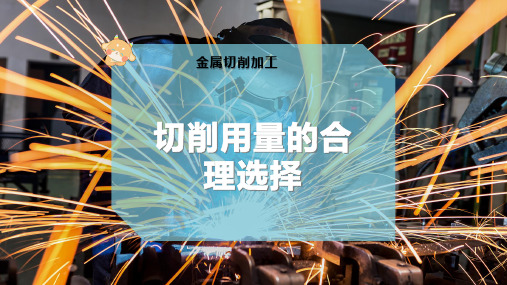
2)根据机床说明书,取机床实际进给量 =0.51mm/r。 3)检验机床进给机构允许的进给量。参考CA6140车床说 明书,查出机床进给机构允许的最大进给抗力为:FMfmax= 3528N。 计算切削时进给力为:
统、工件刚度以及精加工时表面粗糙度要求,确定进给量。
3)根据刀具寿命,确定切削速度。 4)所选定的切削用量应该是机床功率所允许的。
1.2切削用量的合理选择方法
1.背吃刀量的合理选择
背吃刀量一般是根据加工余量来确定。 粗加工(表面粗糙度Ra=50~12.5μm)时,尽可能一 次走刀即切除全部余量,在中等功率的机床上加工,取 ap=8~10mm;加工余量太大或余量不均匀、工艺系统刚性 不足或者断续切削时,可分几次走刀。 半精加工(Ra=6.3~3.2μm)时,取ap=0.5~2mm。 精加工(Ra=1.6~0.8μm)时,取ap=0.1~0.4mm。
1.5切削用量的优化概念
切削用量的优化是指在一定的预定目标及约束条件下, 选择最佳的切削用量。
在实际生产中,由于各种条件(加工零件、机床、刀 具、夹具等)都在变化,很难确定出一组最合理的切削用 量数值。
利用切削用量优化的方法,在确定加工条件下,综合 考虑各个因素,通过计算机辅助设计,能找出满足高效、 低成本、高利润和达到表面质量要求的一组最佳的切削用 量参数。实际切削用量的优化过程就是建立优化目标的数 学模型,用计算机求极值。主要目标函数有三个。
床功率是否允许。 在实际生产中,切削用量的合理选择,既可参照有关 手册的推荐数据,也可凭经验根据选择原则确定。
1.3车削用量的合理选择例题
切削用量的选择和计算公式

切削用量的选择和计算公式切削用量的选择和计算是机械加工中非常重要的一环,它直接影响到加工效率、加工质量和工具的使用寿命。
正确选择和计算切削用量可以使加工过程更加稳定和高效。
本文将介绍切削用量的选择和计算公式,并探讨其在机械加工中的应用。
切削用量的选择。
切削用量是指在切削加工过程中,刀具与工件之间的相对运动距离。
切削用量的选择需要考虑到工件材料、刀具材料、切削速度、进给速度等因素。
一般来说,切削用量越大,切削效率越高,但是过大的切削用量会导致刀具磨损加剧,甚至损坏刀具。
因此,在选择切削用量时需要在保证加工效率的前提下,尽量减小刀具的磨损。
切削用量的计算公式。
切削用量的计算公式通常包括切削速度、进给速度和刀具的切削刃数。
切削速度是指刀具在工件表面的相对运动速度,通常用Vc表示,单位为m/min。
进给速度是指刀具在工件表面的进给速度,通常用f表示,单位为mm/r。
刀具的切削刃数是指刀具上切削刃的数量,通常用z表示。
根据切削速度、进给速度和刀具的切削刃数,切削用量的计算公式可以表示为:切削用量 = 切削速度×进给速度×刀具切削刃数。
在实际应用中,切削用量的计算公式可以根据具体的加工情况进行调整,以满足加工的要求。
切削用量的应用。
切削用量的选择和计算在机械加工中具有重要的应用价值。
正确选择切削用量可以提高加工效率,降低成本,提高产品质量。
同时,合理的切削用量还可以延长刀具的使用寿命,减少刀具的更换次数,降低加工成本。
在实际加工中,切削用量的选择和计算需要结合具体的加工情况进行调整。
例如,在加工硬质材料时,可以适当增大切削用量,以提高加工效率;在加工精密零件时,可以适当减小切削用量,以保证加工精度。
此外,切削用量的选择还需要考虑到刀具的类型、刀具的磨损情况、工件的材料和形状等因素。
总之,切削用量的选择和计算是机械加工中非常重要的一环。
正确选择和计算切削用量可以提高加工效率、降低成本、提高产品质量。
第四节 切削用量选择讲解
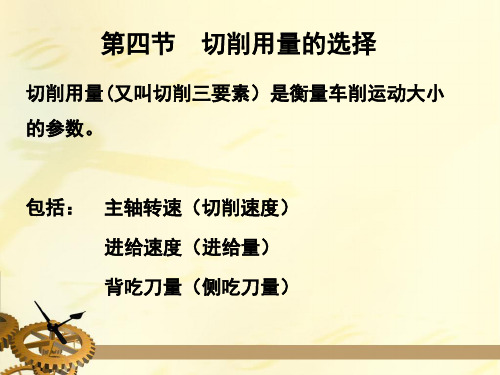
π dn
切削速度示意图
①车削光轴切削速度 Vs=1000Vc/πd Vs—主轴转速,r/min Vc—切削速度,m/min d—工件待加工表面直径,mm
②车削螺纹主轴转速n 在切削螺纹时,车床的主轴转速过高会使螺
纹破牙,因此对于一般数控车床车螺纹时主轴转 速计算公式:
注意:切断、车槽时的切削深度为车刀主切削刃 的宽度
① 背吃刀量aP(mm)的选择
粗加工(Ra10~80μm)时,一次进给应尽可能切除全部
余量。在中等功率机床上,背吃刀量可达8~l0mm。
半精加工(Ra1.25~l0μm)时,背吃刀量取为0.5~2mm。 精加工(Ra0.32~1.25μm)时,背吃刀量取为
第四节 切削用量的选择
切削用量(又叫切削三要素)是衡量车削运动大小 的参数。
包括: 主轴转速(切削速度) 进给速度(进给量) 背吃刀量(侧吃刀量)
(1) 背吃刀量(切削深度)
切削深度为工件上已加工表面和待加工表面间的 垂直距离,单位为mm。即:ap=(dw-dm)/2 其中:
dw—工件待加工表面的直径,(mm) dm—工件已加工表面的直径,(mm)
表面特征
表面粗糙度值 加工方法举例
明显可见刀痕
Ra100、Ra50、 粗车、粗刨、粗
Ra25、
铣、钻孔
微见刀痕
12.5、Ra6.3、 精车、精刨、精
Ra3.2、
铣、粗铰、粗磨
看不见加工痕迹, Ra1.6、Ra0.8、 微辩加工方向 Ra0.4、
精车、精磨、精 铰、研磨
暗光泽面
Ra0.2、Ra0.1、 研磨、珩磨、超
例3:车削直径为300mm的铸铁带轮外圆,若切削速 度为60m/ min,试求车床主轴转速。
切削用量的选择
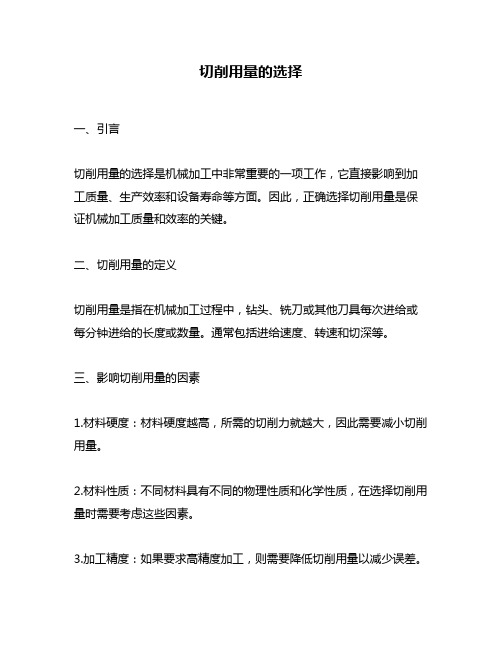
切削用量的选择一、引言切削用量的选择是机械加工中非常重要的一项工作,它直接影响到加工质量、生产效率和设备寿命等方面。
因此,正确选择切削用量是保证机械加工质量和效率的关键。
二、切削用量的定义切削用量是指在机械加工过程中,钻头、铣刀或其他刀具每次进给或每分钟进给的长度或数量。
通常包括进给速度、转速和切深等。
三、影响切削用量的因素1.材料硬度:材料硬度越高,所需的切削力就越大,因此需要减小切削用量。
2.材料性质:不同材料具有不同的物理性质和化学性质,在选择切削用量时需要考虑这些因素。
3.加工精度:如果要求高精度加工,则需要降低切削用量以减少误差。
4.设备能力:设备本身也有其最大可承受的进给速度、转速等限制,需要根据设备能力进行选择。
5.加工方式:不同的加工方式对于所需的切削用量也有影响,例如铣削和车削的切削用量选择不同。
四、切削用量的选择方法1.根据材料硬度选择切削用量:一般来说,材料硬度越高,所需的切削力就越大,因此需要减小切削用量。
但是也需要注意,如果切削用量过小,则会导致加工时间过长、工具磨损严重等问题。
2.根据加工精度选择切削用量:如果要求高精度加工,则需要降低切削用量以减少误差。
此时可以通过增加进给次数或减小每次进给长度来实现。
3.根据设备能力选择切削用量:设备本身也有其最大可承受的进给速度、转速等限制,需要根据设备能力进行选择。
如果超过了设备能力,则会导致设备故障或者加工效率下降。
4.根据材料性质选择切削用量:不同材料具有不同的物理性质和化学性质,在选择切削用量时需要考虑这些因素。
例如对于易碎材料,应该采取小进给、低转速的方式进行加工。
5.根据加工方式选择切削用量:不同的加工方式对于所需的切削用量也有影响,例如铣削和车削的切削用量选择不同。
一般来说,铣削时需要较大的切削用量,而车削时则需要较小的切削用量。
五、切削用量的优化1.合理选择刀具:不同类型的刀具适用于不同材料和加工方式,在选择刀具时需要考虑这些因素。
切削用量选用原则

切削用量选用原则切削用量是指在加工过程中对工件进行切削时所使用的切削刀具、刀具材料、切削速度、进给量等参数的选择和调整。
合理选用切削用量是提高加工效率、保证加工质量和延长切削工具寿命的重要因素之一。
本文将从切削刃数、切削深度、切削速度、进给量和切削方式等方面介绍切削用量选用的原则。
一、切削刃数的选择原则切削刃数是指刀具上的切削刃数目。
切削刃数的选择应根据工件材料和加工要求进行。
对于硬度较高的材料,应选用切削刃数少、刀具强度大的刀具,以提高刀具的抗断裂能力和刀具寿命;对于材料硬度较低的工件,可以选用切削刃数多的刀具,以提高切削效率。
二、切削深度的选择原则切削深度是指刀具在每次切削中所能切削的最大距离。
切削深度的选择应根据工件材料、刀具强度和加工要求来确定。
一般情况下,切削深度应尽可能大,以提高切削效率。
但是,在选择切削深度时也要考虑刀具的抗断裂能力和加工表面质量,避免过大的切削深度导致刀具断裂或加工表面粗糙。
三、切削速度的选择原则切削速度是指刀具在切削过程中的线速度。
切削速度的选择应根据刀具材料、工件材料和加工要求来确定。
切削速度过高会导致刀具过热,影响切削质量和刀具寿命;切削速度过低则会降低切削效率。
因此,切削速度的选择应综合考虑切削质量、刀具寿命和切削效率的要求。
四、进给量的选择原则进给量是指刀具在单位时间内沿着工件表面移动的距离。
进给量的选择应根据工件材料、切削刃数和加工要求来确定。
进给量过大会导致切削力过大,影响加工表面质量和刀具寿命;进给量过小则会降低切削效率。
因此,进给量的选择应综合考虑切削力、加工表面质量和切削效率的要求。
五、切削方式的选择原则切削方式包括顺向切削、逆向切削和侧向切削等。
切削方式的选择应根据工件形状、切削刃数和加工要求来确定。
顺向切削适合于切削刃数少、工件表面平整度要求高的情况;逆向切削适合于切削刃数多、切削力大的情况;侧向切削适合于切削刃数多、工件形状复杂的情况。
切削方式的选择应综合考虑加工要求、切削质量和切削效率。
- 1、下载文档前请自行甄别文档内容的完整性,平台不提供额外的编辑、内容补充、找答案等附加服务。
- 2、"仅部分预览"的文档,不可在线预览部分如存在完整性等问题,可反馈申请退款(可完整预览的文档不适用该条件!)。
- 3、如文档侵犯您的权益,请联系客服反馈,我们会尽快为您处理(人工客服工作时间:9:00-18:30)。
第一章 机械制造工艺编制基础知识
铣 削 速 度
选择时,按公式计算或查切削用量手册 对大平面铣削也可参照国内外的先进经 验,采用密齿铣刀、选大进给量、高速铣 削,以提高效率和加工质量。
第一章 机械制造工艺编制基础知识
刨削用量的选择 刨削背吃刀量 刨削背吃刀量的确定方法和车削基本相同 刨削进给量 刨削进给量可按有关手册中车削进给量推 荐值选用 粗刨平面根据背吃刀量和刀杆截面尺寸 按粗车外圆选其较大值 精加工时按半精车、精车外圆选取 刨槽和切断按车糟和切断进给量选择 刨削速度 根据实践经验选定切削速度,或按车削速 度公式计算,
第一章 机械制造工艺编制基础知识
计算切削功率PC 校 核 机 床 功 率 查机床说明书车床电动机功率PE 机床传动效率ηM=0.8 PC< PE. ηM OK
第一章 机械制造工艺编制基础知识
校 核 机 床 进 给 机 构 的 强 度 计算主切削力Fc、切深抗力Fp、进给力Ff 摩擦系 数uc=0.1 F进=Ff +us(Fc +Fp) 查机床纵向进给机构允许的最大作用力Fmax
第一章 机械制造工艺编制基础知识
时间定额确定的方法 总结过去的经验并参考有关的技术资料直 接估计确定 以同类产品的工件或工序的时间定额为依 据,进行对比分析推算 通过对实际操作时间的测定和分析 来确定
第一章 机械制造工艺编制基础知识
在选择切削速度时,还应考虑方面: 粗车时,背吃刀量和进给量均较大,故选择较 低的切削速度;精加工时,背吃刀量和进给量均 较小,则选择较高的切削速度 加工材料的强度和硬度较高时,应选较低的切 削速度 刀具材料的切削性能较好时,应选较高的切削 速度 精加工时,应尽量避免积屑瘤和鳞刺的区域 断续切削时,宜适当降低切削速度 易发生振动的情况下,切削速度应避开自激振 动的临界速度 加工大件、细长件和薄壁件时,应选用较低的 切削速度 加工带外皮的工件时,应适当降低切削速度
主运动 主运动是切下金属所必须的最主要的运动。 通常它的速度最高,消耗机床功率最多。 进给运动 将被切削金属层不断投入切削,以全部 切除掉所有切削余量的运动。进给运动 可以是连续运动,也可以是间歇运动。
切削运动中主运动只有1个。进给运动 可以是1个,可以是两个或多个运动
当主运动与进给运动同时进行时,刀具切削刃上 某一点相对工件的运动称为合成切削运动,其大小 与方向用合成速度向量ve表示。合成速度向量等于 主运动速度与进给运动速度的向量和。即 ve=vc+vf
F进<Fmax
举例
OK
第一章 机械制造工艺编制基础知识
车 削 力 实 验 公 式
Fc C Fz a p
F f C Fx a p
Fp C F y a p
x Fz
f
f
f
y Fz
y Fx
K Fz
x Fxx Fy源自K FxK Fyy Fy
查表法确定切削力
第一章 机械制造工艺编制基础知识
铣削用量的选择 铣 削 背 吃 刀 量
如外圆车削时,工件做旋转运动,刀具作纵向直线 运动,形成了工件的外圆表面。在新的表面的形成过 程中,工件上有三个依次变化的表面: 待加工表面: 即将被切去金属层的表面; 加工表面: 切削刃正在切削着的表面; 已加工表面: 已经切去一部分金属 形成的新表面。
动画
金属切削机床的基本运动有直线运动和回转运 动。但是,按切削时工件与刀具相对运动所起的 作用来分,可分为主运动和进给运动。
第一章 机械制造工艺编制基础知识
工时定额的确定
时间定额又称为工时定额,是在生产技术组 织条件下,规定一件产品或完成某一道工序 需消耗的时间;产量定额是在一定的生产组 织条件下,规定单位时间内生产合格产品数 量的标准。 目前,多数企业采用时间定额来反映劳动生 产率。
第一章 机械制造工艺编制基础知识 一、时间定额 时间定额不仅是衡量劳动生产率的指标, 也是安排生产计划,计算生产成本的重要 依据,还是新建或扩建工厂(车间)时计 算设备和工人数量的依据。 制定合理的时间定额是调动工人积极性 的重要手段,在使用中,时间定额还应定 期修订,以使其保持平均先进水平。
第一章 机械制造工艺编制基础知识
钻削用量的选择 钻削用量的选择包括确定钻头直径D、进 给量f和切削速度v(或主轴转速n) 钻头直径 钻头直径D由工艺尺寸要求确定,尽可能一 次钻出所要求的孔。当机床性能不能胜任时, 才采取先钻孔、再扩孔的工艺,这时钻头直 径取加工尺寸的0.5~0.7倍 进给量 标准麻花钻的进给量可查表选取 钻削速度 钻削速度通常根据钻头寿命按经验选取
碳素结构 钢和合金 结构钢
16X25
20 40 60 100 400 20 40 60 100 600
20~30 25X25
注:有冲击时,进给量应减小20%。
第一章 机械制造工艺编制基础知识
在半精加工和精加工时,则按表面粗糙度的要求,根据 工件材料、刀尖圆弧半径、切削速度按表选择进给量
第一章 机械制造工艺编制基础知识
第一章 机械制造工艺编制基础知识 拟订工艺路线是指拟订零件加工所经 过的有关部门和工序的先后顺序。 工艺路线的拟订是制订工艺规程的重 要内容,其主要任务是确定定位基准, 选择各个加工表面的加工方法,确定各 个表面的加工顺序以及整个工艺过程的 工序数目和工序内容。它与零件的加工 要求,生产批量及生产条件等多种因素 有关。
切削速度 VC
Cv v m xv T ap f
yv
kv
或查工艺手册确定
速度
切削速度v确定 机床转速 n=1000v/Πdw(r/min) 查机床说明书,与上式计算最接近 的机床转速,确定实际转速n实 按v= Πdwn实/1000 确定实际切削速度
第一章 机械制造工艺编制基础知识
外圆车削时切削速度公式中的系数和指数
根据加工余量来确定铣削背吃刀量 粗铣时,一般选铣削背吃刀量等于加工余量 半精铣及精铣时,通常分两次铣削,半精铣时背 吃刀量一般为0.5~2mm 精铣时,铣削背吃刀量一般为0.1~1mim或更小
第一章 机械制造工艺编制基础知识
每 齿 进 给 量
可由切削用量手册中查出,其中推荐值均 有一· 个范围。 精铣或铣刀直径较小、铣削背吃刀量较 大时,用其中较小值,大值常用于粗铣。 加工铸铁件时,用其中较大值,加工钢 件时用较小值。
切 削 用 量 同 加 工 生 产 率 的 关 系
p 1 / tm
LW d w LW tm 3 nW ap f 10 vap f
p A0 vfap
A0=1000( dW LW ) 切削用量三要素同生产率均保持线性关 系,即提高切削速度、增大进给量和背 吃刀量,都能“同样地”提高劳动生产 率
进给量f
表:硬质合金车刀及高速钢车刀粗车外圆和端面时的进给量
工件材料
车刀刀杆 工件直径 尺寸 dw BXH (mm) (mmXmm)
背吃刀量ap(mm) ≤3 >3~5 >5~8 >8~12 12以上 走刀量f(mm) 0.3~0.4 0.4~0.5 0.5~0.6 0.6~0.9 0.8~1.2 0.3~0.4 0.4~0.5 0.6~0.7 0.8~1.0 1.2~1.4 ---0.4~0.5 0.5~0.7 0.6~0.9 0.8~1.2 ---0.3~0.4 0.5~0.7 0.7~0.9 1.0~1.2 ------0.3~0.5 0.5~0.6 0.6~0.8 ------0.4~0.6 0.5~0.7 0.8~1.0 ---------0.4~0.5 0.5~0.6 ---------0.4~0.7 0.6~0.9 ---------------------------0.4~0.6
ap
w m
2
mm
当粗车余量△太大或加工的工艺系统刚性较差、 断续切削时,则加工余量△分两次或数次走刀后切 除。通常使: 1 第一次走刀的背吃刀量apl为: a ( 1 ~ ) 3 4 第二次走刀的背吃刀量ap2为: 2 3
p2
a p1 ( ~ ) 3 4
第一章 机械制造工艺编制基础知识
第一章 机械制造工艺编制基础知识
切 削 用 量 与 刀 具 耐 用 度 的 关 系
T
Cv v f a
1 m 1 n 1 p p
切削用量三要素v、f、对刀具耐用 度的影响程度不同,影响最大的是 v,其次是f,影响最小的是。
第一章 机械制造工艺编制基础知识
切 削 用 量 选 择 原 则
首先,选取尽可能大的背吃刀量; 其次,根据机床动力和刚性限制条 件或已加工表面粗糙度的要求,选 取尽可能大的进给量;最后,利用 《切削用量手册》选取或者用公式 计算确定切削速度。
第一章 机械制造工艺编制基础知识
粗 加 工 时 切 削 速 度 的 选 择 硬质合金车刀切削热轧中碳钢的平均切削 速度为1.67m/s 切削灰铸铁的平均切削速度为1.17m/s 切削合金钢比切削中碳钢切削速度要降低 20%~30% 切削调质状态的钢件或切削正火、退火状 态的钢料切削速度要降低20%~30% 切削有色金属比切削中碳钢的切削速度可 提高100%~300%
进给速度vf 单位时间的进给量,单位mm/s(mm/min) 进给量f 工件或刀具每回转一周时两者沿进给运动方向的相对 位移,单位是mm/r(毫米/转)。 它是衡量进给运动 大小的参数 对于铣刀、铰刀、拉刀、齿轮滚刀等多刃切削工具, 在它们进行工作时,还应规定每一个刀齿的进给量fz, 即后一个刀齿相对于前一个刀齿的进给量,单位是 mm/z(毫米/齿)。 显而易见 v f= f · n=fZ· z· n mm/s或mm/min z为齿数
Cv v m xv T ap f
yv
kv
K v 切削速度修正系数
kv kMv ksv ktv kkrv kkr' v krv kBv