流化床制粒影响因素的探讨
流化床干燥设备中颗粒干燥速率的研究进展

流化床干燥设备中颗粒干燥速率的研究进展流化床干燥设备是一种广泛应用于工业生产中的干燥设备,通过内部气流的流动来实现颗粒物料的干燥。
在流化床干燥设备中,颗粒的干燥速率直接影响着整个干燥过程的效率和成本。
因此,对于流化床干燥设备中颗粒干燥速率的研究具有重要的意义。
近年来,针对流化床干燥设备中颗粒干燥速率的研究取得了一系列的进展。
这些研究主要集中在以下几个方面:颗粒粒径对干燥速率的影响,气流速度对干燥速率的影响,颗粒形状对干燥速率的影响以及流化床结构对干燥速率的影响。
首先,颗粒粒径对干燥速率的影响是研究颗粒干燥速率的重要方面之一。
实验证明,颗粒粒径越小,干燥速率越大。
这是因为颗粒粒径越小,单位质量的颗粒表面积越大,从而与干燥介质接触的面积也增大,进而加快了水分的扩散速度。
研究还表明,颗粒粒径在一定范围内对干燥速率的影响并不明显,而在较大粒径范围内逐渐显现出效应。
其次,气流速度对干燥速率的影响也是研究的重点之一。
实验结果显示,流化床中的气流速度越大,颗粒干燥速率越快。
这是因为较大的气流速度会增加颗粒与气流之间的接触面积,使得水分从颗粒表面更快地蒸发出来。
然而,当气流速度过大时,会导致颗粒的剧烈运动和过度破碎,从而影响干燥效果。
另外,颗粒形状对干燥速率也有一定的影响。
实验研究发现,颗粒越接近于球形,干燥速率就越快。
这是因为球形颗粒的表面积与质量的比值最小,从而水分的扩散路径最短,干燥速率最快。
较大的表面积和边缘效应使得非球形颗粒的干燥速率较慢。
此外,流化床结构对干燥速率也有一定的影响。
研究结果表明,流化床的直径、高度和气流分布等因素都对干燥速率产生一定的影响。
较大的流化床直径和高度可以增加颗粒与气流之间的接触时间,从而提高干燥速率。
而均匀的气流分布可以使得颗粒受到更加充分的干燥,从而提高整个干燥系统的效率。
综上所述,流化床干燥设备中颗粒干燥速率的研究取得了一系列的进展。
这些研究进展为优化流化床干燥设备的设计和改进提供了重要的参考。
流化床干燥设备中颗粒物料的流化性分析
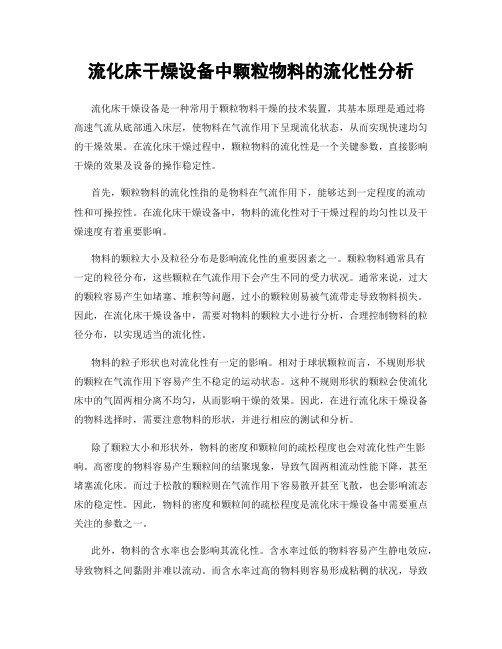
流化床干燥设备中颗粒物料的流化性分析流化床干燥设备是一种常用于颗粒物料干燥的技术装置,其基本原理是通过将高速气流从底部通入床层,使物料在气流作用下呈现流化状态,从而实现快速均匀的干燥效果。
在流化床干燥过程中,颗粒物料的流化性是一个关键参数,直接影响干燥的效果及设备的操作稳定性。
首先,颗粒物料的流化性指的是物料在气流作用下,能够达到一定程度的流动性和可操控性。
在流化床干燥设备中,物料的流化性对于干燥过程的均匀性以及干燥速度有着重要影响。
物料的颗粒大小及粒径分布是影响流化性的重要因素之一。
颗粒物料通常具有一定的粒径分布,这些颗粒在气流作用下会产生不同的受力状况。
通常来说,过大的颗粒容易产生如堵塞、堆积等问题,过小的颗粒则易被气流带走导致物料损失。
因此,在流化床干燥设备中,需要对物料的颗粒大小进行分析,合理控制物料的粒径分布,以实现适当的流化性。
物料的粒子形状也对流化性有一定的影响。
相对于球状颗粒而言,不规则形状的颗粒在气流作用下容易产生不稳定的运动状态。
这种不规则形状的颗粒会使流化床中的气固两相分离不均匀,从而影响干燥的效果。
因此,在进行流化床干燥设备的物料选择时,需要注意物料的形状,并进行相应的测试和分析。
除了颗粒大小和形状外,物料的密度和颗粒间的疏松程度也会对流化性产生影响。
高密度的物料容易产生颗粒间的结聚现象,导致气固两相流动性能下降,甚至堵塞流化床。
而过于松散的颗粒则在气流作用下容易散开甚至飞散,也会影响流态床的稳定性。
因此,物料的密度和颗粒间的疏松程度是流化床干燥设备中需要重点关注的参数之一。
此外,物料的含水率也会影响其流化性。
含水率过低的物料容易产生静电效应,导致物料之间黏附并难以流动。
而含水率过高的物料则容易形成粘稠的状况,导致流化床干燥设备的堵塞风险增加。
因此,在进行物料的流化性分析时,需要对物料的含水率进行测试,并根据实际情况进行调整。
综上所述,流化床干燥设备中颗粒物料的流化性分析对于干燥效果的提升及设备的稳定运行具有重要意义。
流化床喷雾造粒颗粒强度的影响因素研究
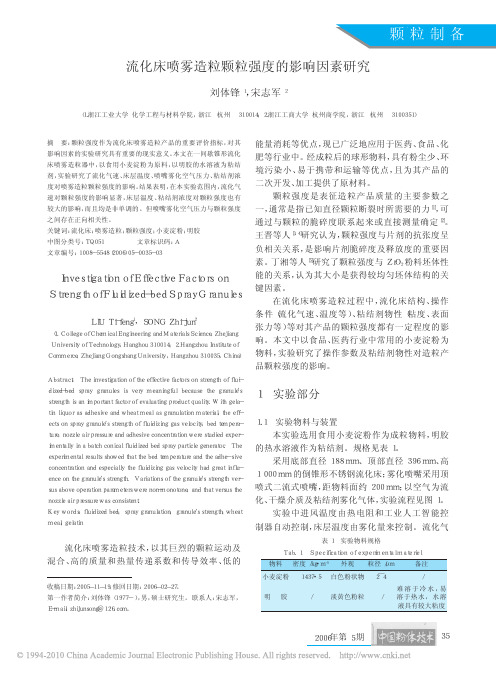
流化床喷雾造粒颗粒强度的影响因素研究
刘体锋 1,宋志军 2
(1.浙江工业大学 化学工程与材料学院,浙江 杭州 310014;2.浙江工商大学 杭州商学院,浙江 杭州 3100351)
摘 要:颗粒强度作为流化床喷雾造粒产品的重要评价指标,对其
影响因素的实验研究具有重要的现实意义。本文在一间歇锥形流化
实验所得样品的球形度较好,肉眼观测其表面 较为光滑,基本无毛刺、凹空。同一实验操作条件 下,不同批次样品的强度值重复性较好,且其颗粒 强度随粒径的增大而增加,实验具有较强的可操作 性及稳定性。 2.1 流化气速对颗粒强度的影响
从图 2 可以看出,造粒产品的颗粒强度随流化 气速的增加,先增加后减小;在流化床操作气速取 值为 2.8 m/s 的实验条件下,颗粒强度取得最大值。 流化气速对颗粒强度的影响主要表现在两个方面:
颗粒强度是表征造粒产品质量的主要参数之 一,通常是指已知直径颗粒断裂时所需要的力[1],可 通过与颗粒的脆碎度联系起来或直接测量确定[2]。 王晋等人[3, 4]研究认为,颗粒强度与片剂的抗张度呈 负相关关系,是影响片剂脆碎度及释放度的重要因 素。丁湘等人[5]研究了颗粒强度与 ZrO2 粉料坯体性 能的关系,认为其大小是获得较均匀坯体结构的关 键因素。
流化床喷雾造粒技术,以其巨烈的颗粒运动及 混合、高的质量和热量传递系数和传导效率、低的
收稿日期:2005- 11- 19,修回日期:2006- 02- 27。 第一作者简介:刘体锋(1977- ),男,硕士研究生。联系人:宋志军, E-mail:zhijunsong@126.com。
能量消耗等优点,现已广泛地应用于医药、食品、化 肥等行业中。经成粒后的球形物料,具有粉尘少、环 境污染小、易于携带和运输等优点,且为其产品的 二次开发、加工提供了原材料。
流化床制粒影响因素的探讨教案资料
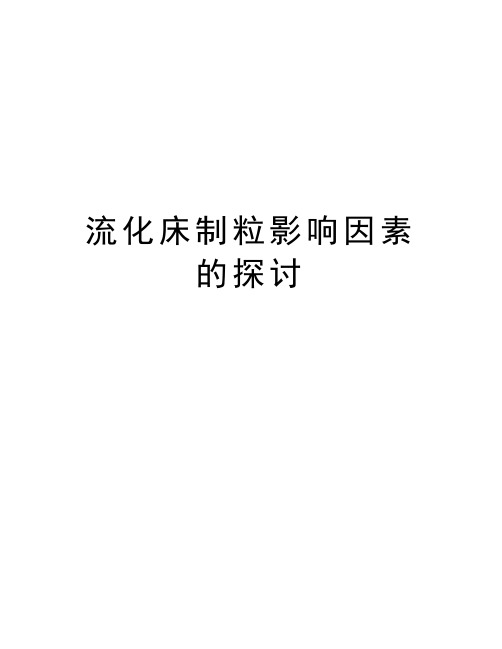
流化床制粒影响因素的探讨流化床制粒影响因素的探讨[关键词]:流化床,制粒,影响因素流化床制粒(fluidized bed granulation)又称沸腾制粒,指利用气流使粉末物料悬浮呈沸腾状,再喷入雾状粘合剂使粉末结合成粒,最后得到干燥的颗粒。
在此过程中,物料的混合、制粒、干燥同时完成,因此又称一步制粒。
1964年Scott等将Wurster方法作了改进并应用于医药工业。
我国于1980年引进沸腾制粒、包衣设备,可取代传统湿法制粒。
1流化床的结构和作用原理流化床制粒机由容器、筛板、喷嘴、捕集袋、空气进出口、物料进出口等部分组成。
经净化的空气加热后通过筛板进入容器,加热物料并使其呈流态化。
此时粘合剂以雾状喷入,使物料粉末聚结成粒子核,进而形成颗粒,同步干燥,得到多孔性、表面积较大的柔软颗粒。
2流化床制粒的优点与挤出制粒相比,流化床制粒有以下优点: (1)混合、制粒、干燥一次完成,生产工艺简单、自动化程度高;(2)所得颗粒圆整、均匀,溶解性能好;(3)颗粒的流动性和可压性好,压片时片重波动幅度小,所得片剂崩解性能好、外观质量佳;(4) 颗粒间较少或几不发生可溶性成分迁移,减小了由此造成片剂含量不均匀的可能性;(5)在密闭容器内操作,无粉尘飞扬,符合GMP要求。
流化床适于中成药,尤其是浸膏量大、辅料相对较少的中药颗粒的制备,及对湿和热敏感的药物制粒。
3 影响流化床制粒的因素3.1 制粒材料用亲水性材料制粒时,粉末与粘合剂互溶,易凝集成粒,故适宜采用流化床制粒。
而疏水性材料的粉粒需藉粘合剂的架桥作用才能黏结在一起,溶剂蒸发后,形成颗粒。
无论是亲水性还是疏水性材料,粉末粒度必须达到80目以上,否则制得的颗粒有色斑或粒径偏大,分布不均匀,从而影响药物的溶出和吸收。
通过进料前将原辅料在机外预混可改善制粒效果。
吸湿性材料黏性强、流动性差、引湿性强,在贮存过程中易吸潮,若用以制粒则受热时会使其中易溶成分溶解导致物料软化结块,未喷雾即出现粘筛和大面积结块,沸腾几乎停止(又称塌床)。
流化床技术中重要的影响因素有哪些
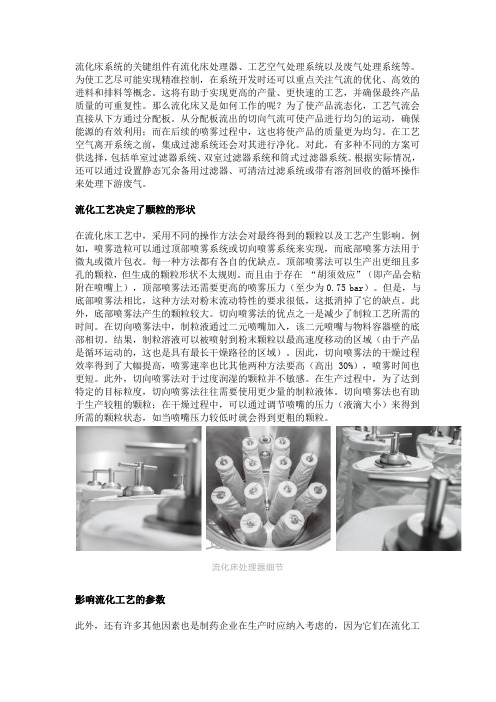
流化床系统的关键组件有流化床处理器、工艺空气处理系统以及废气处理系统等。
为使工艺尽可能实现精准控制,在系统开发时还可以重点关注气流的优化、高效的进料和排料等概念。
这将有助于实现更高的产量、更快速的工艺,并确保最终产品质量的可重复性。
那么流化床又是如何工作的呢?为了使产品流态化,工艺气流会直接从下方通过分配板。
从分配板流出的切向气流可使产品进行均匀的运动,确保能源的有效利用;而在后续的喷雾过程中,这也将使产品的质量更为均匀。
在工艺空气离开系统之前,集成过滤系统还会对其进行净化。
对此,有多种不同的方案可供选择,包括单室过滤器系统、双室过滤器系统和筒式过滤器系统。
根据实际情况,还可以通过设置静态冗余备用过滤器、可清洁过滤系统或带有溶剂回收的循环操作来处理下游废气。
流化工艺决定了颗粒的形状在流化床工艺中,采用不同的操作方法会对最终得到的颗粒以及工艺产生影响。
例如,喷雾造粒可以通过顶部喷雾系统或切向喷雾系统来实现,而底部喷雾方法用于微丸或微片包衣。
每一种方法都有各自的优缺点。
顶部喷雾法可以生产出更细且多孔的颗粒,但生成的颗粒形状不太规则。
而且由于存在“胡须效应”(即产品会粘附在喷嘴上),顶部喷雾法还需要更高的喷雾压力(至少为0.75 bar)。
但是,与底部喷雾法相比,这种方法对粉末流动特性的要求很低,这抵消掉了它的缺点。
此外,底部喷雾法产生的颗粒较大。
切向喷雾法的优点之一是减少了制粒工艺所需的时间。
在切向喷雾法中,制粒液通过二元喷嘴加入,该二元喷嘴与物料容器壁的底部相切。
结果,制粒溶液可以被喷射到粉末颗粒以最高速度移动的区域(由于产品是循环运动的,这也是具有最长干燥路径的区域)。
因此,切向喷雾法的干燥过程效率得到了大幅提高,喷雾速率也比其他两种方法要高(高出 30%),喷雾时间也更短。
此外,切向喷雾法对于过度润湿的颗粒并不敏感。
在生产过程中,为了达到特定的目标粒度,切向喷雾法往往需要使用更少量的制粒液体。
药物制粒技术及流化床制粒影响因素的探讨
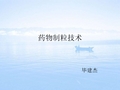
药物制粒技术
毕建杰
制粒的含义
• 在制药工业中,制粒作为粒子的加工过程,要达 到某种工艺或剂型的相应要 求,几乎与所有固体 制剂的制粒制备及质量相关,制成的颗粒可以是 最终成型产 品也可以是中间体。如颗粒剂、微丸、 滴丸等必须通过制粒成型;片剂、胶囊剂 需借助 制粒改善颗粒的流动性与可压性,以便于充填、 分剂量和压片;为了方便 粉末的处理也经常需制 成颗粒;供直接压片用的辅料也常需制成颗粒; 药物经制 粒后可使制剂产生预期的速效或长效作 用等。
制粒技术的发展趋势
随全球制药技术、制药工业竞争的日益加 剧及我国加入WTO后所面临的 严峻形势, 对提高制剂产品质量的要求进一步加强, 对制粒技术的要求也越来越 高。药物制粒 技术的趋势是向设备大型化、结构紧凑化、 制粒工艺高新技术化、 多功能连续化、高 效快速化方向发展。
• 高速湿法制粒中应用的高速剪切混合制粒机,现以卧式 高速剪切混合制粒机 为主。卧式高速剪切混合制粒机 其制粒原理是将混合及制粒两道工序在同一容器 中完 成,采用下旋式搅拌,搅拌桨安装在锅底,并与锅底形 成间隙。搅拌叶面能 确保物料碰撞分散成半流动的翻 滚状态,并达到充分的混合。随着黏合剂的注 入,使 粉料逐渐润湿,物料形状发生变化。而位于锅壁水平轴 的剪切刀与搅拌桨 的旋转运动产生涡流,使物料被充 分混合、翻动及碰撞,此时处于物料翻动必经 区域的 剪切刀可将团状物料充分打碎成颗粒。同时,物料在三 维运动中颗粒之间 的挤压、碰撞、摩擦、剪切和捏合, 使颗粒摩擦更均匀、细致,最终形成稳定球 状颗粒从 而形成潮湿均匀的软材。其中,制粒颗粒目数大小受物 料的特性、剪切 刀的转速和制粒时间等因素制约。
流化床制粒技术:优势虽多,影响因素也需重视
流化床制粒技术:优势虽多,影响因素也需重视流化床制粒也叫一步制粒,主要是将常规湿法制粒的混合、制粒、干燥3个步骤在密闭容器内一次完成的方法。
流化床制粒可以使药物粉末在自下而上的气流作用下保持悬浮的流化状态,粘合剂液体将由上部或下部向流化室内喷入,粉末再聚结成颗粒。
流化床制粒有很多优点,比如,对物料的干混、湿混、搅拌、颗粒成型、干燥都在同一台流化床设备内完成,这就减少了大量的操作环节,并节约了生产实践。
流化床制粒还可以使生产在密封环境中进行,这样不但可以防止外界对药物的污染,而且能够减少操作人员同具有刺激性或毒性药物和辅料接触的机会。
另外,通过流化床制粒技术制得的颗粒粒度均匀,流动性和圧缩成形性较好。
还能使在组分中含量非常低的药物在制得的颗粒中分布更均匀。
值得一提的是,流化床还能制得多层和多相的功能性粒子。
尽管流化床制粒技术优点很多,但其毕竟是一个较为复杂的过程,也受到很多因素的影响。
比如设备因素,在流化床制粒机中,空气分流板及容器军队粒子的运动产生影响。
其中,容器的材料和形状对粒子运动的影响更大。
如果操作者在使用顶喷流化床时,喷嘴的位置会影响喷雾均匀性和物料的湿润程度,而为了使粒径分布尽可能窄,应尽量调整喷雾面积与湿床表面积一样大。
因为如果位置太高,液滴从喷嘴达到物料的距离较长,增加了液相介质的挥发,造成物料不能湿润完全,呈现喷雾干燥的现象。
而当喷嘴位置太低时,粘合剂雾化后就不能与物料充分接触,所得颗粒粒度不均匀,而且喷嘴前缘也容易出现喷射障碍。
有专家提醒,使用转动切喷流化床制粒时,混合器的构造对制粒也会产生很大的影响。
再比如处方因素,包括物料的性质、粘合剂的选择等。
笔者了解到,在流化床制粒中,粒径和粒径分布是物料较为重要的物理学性质。
物料粉末的粒径越小,物料的表面积就越大,所需粘合剂的量也越大。
用亲水性材料制粒时,粉末与粘合剂互溶,易凝集成粒,故适宜采用流化床制粒。
而用疏水性材料的粉粒,则需要依靠粘合剂的架桥作用才能粘结在一起,溶剂蒸发后,形成颗粒。
流化床制粒技术介绍综述
流化床制粒技术介绍摘要:目的:介绍流化床制粒特点、制粒过程中各因素对制粒的影响及操作中容易出现的问题。
方法:将近十几年来国内外的有关文献近20 篇分类、整理并结合作者实际操作中的体会进行综述。
结果与结论:与其他制粒方式相比,流化床制粒具有制得的颗粒粒度均匀、流动性、压缩成形性好,组分中含量非常低的药物在颗粒中分布更均匀,节约生产时间,更符合GMP 规范的要求等优点。
制粒过程中需对设备参数、进口温度、流化风量、粘合剂的性质和物料的性质等综合考虑。
流化床制粒也称一步制粒法,是将常规湿法制粒的混合、制粒、干燥3 个步骤在密闭容器内一次完成的方法。
1959 年,美国威斯康星州的Wurster 博士首先提出流化床制粒技术,随后该技术迅速发展,并广泛用于制药、食品及化工工业。
我国于上世纪80 年代相继从Aeromatec 公司、德国Glaft 公司、日本友谊株式会社引进流化床制粒设备。
近年来,由于医药行业面临的GMP 认证,流化床在我国药厂已得到普遍应用。
我公司将从流化床制粒的原理和优点、流化床类型的选择、流化床制粒过程中设备参数、工艺参数、处方参数对制粒的影响等方面进行综述。
1 流化床制粒原理在流化床制粒机中,压缩空气和粘合剂溶液按一定比例由喷嘴雾化并喷至流化床层上正处于流化状态的物料粉末上。
首先液滴使接触到的粉末润湿并聚结在其周围形成粒子核,同时再由继续喷入的液滴落在粒子核表面上产生粘合架桥作用,使粒子核与粒子核之间、粒子核与粒子之间相互结合,逐渐形成较大的颗粒。
干燥后,粉末间的液体桥变成固体桥,即得外形圆整的多孔颗粒。
因流化床制粒全过程不受外力作用,仅受床内气流影响,故制得的颗粒密度小,粒子强度低,但颗粒的粒度均匀,流动性、压缩成形性好。
2 流化床类型选择流化床制粒设备有空气压缩系统、加热系统、喷雾系统及控制系统等组成。
主要结构由容器、空气分流板、喷嘴、过滤袋、空气进出口、物料排出口等组成。
按其喷液方式的不同分为3 类:顶喷流化床、转动切喷流化床、底喷流化床。
流化床制粒工艺混合均匀度不合格原因
流化床制粒工艺混合均匀度不合格原因流化床制粒是一种常用的制粒工艺,通过将颗粒物料与气体流化剂在流化床中进行充分混合,使颗粒物料形成颗粒状,具有制粒效果好、颗粒尺寸均匀等优点。
然而,在实际生产中,有时会发现流化床制粒工艺的混合均匀度不合格的情况。
本文将分析流化床制粒工艺混合均匀度不合格的原因,并提出相应的解决方案。
混合均匀度不合格是指在流化床制粒过程中,颗粒物料的成分分布不均匀或颗粒尺寸不一致。
这可能导致制粒效果不理想,影响产品质量。
那么,造成混合均匀度不合格的原因有哪些呢?流化床制粒工艺中,颗粒物料的物性差异是影响混合均匀度的一个重要因素。
不同颗粒物料的密度、形状、表面性质等都会对混合均匀度产生影响。
如果颗粒物料之间的物性差异较大,就会导致混合效果不佳。
因此,在流化床制粒工艺中,需要选用物性相近的颗粒物料,以提高混合均匀度。
流化床制粒工艺中,流化剂的选择和气流速度对混合均匀度也有重要影响。
流化剂的选择应考虑其密度和流动性能,以保证颗粒物料在床层中能够充分混合。
此外,气流速度过大或过小都会影响颗粒物料的混合均匀度。
过大的气流速度会造成颗粒物料的剧烈运动,导致颗粒物料之间的分离和堆积现象,从而影响混合效果;而过小的气流速度则会使颗粒物料无法有效地混合在一起。
因此,在实际生产中,需要根据具体情况选择合适的流化剂和气流速度,以提高混合均匀度。
流化床制粒工艺中,颗粒物料的进料方式和流化床结构也会对混合均匀度产生影响。
进料方式不当会造成颗粒物料的聚集或分散,进而影响混合效果。
在实际生产中,可以采用多点进料的方式,将颗粒物料均匀地分散到流化床中,以提高混合均匀度。
针对流化床制粒工艺混合均匀度不合格的原因,可以采取以下解决方案:1. 优化物料选择:在选择颗粒物料时,应尽量选择物性相近的颗粒物料,以提高混合均匀度。
2. 调整流化剂和气流速度:根据具体情况,选择合适的流化剂和气流速度,以保证颗粒物料在床层中充分混合。
流化床干燥设备中颗粒漂移的分析与控制
流化床干燥设备中颗粒漂移的分析与控制随着工业生产的发展和节能减排的广泛推广,流化床干燥设备在许多行业中被广泛应用。
然而,流化床干燥过程中颗粒的漂移现象一直是工程师和研究人员关注的重要问题之一。
本文旨在分析颗粒漂移的原因,并探讨相应的控制方法。
首先,需要了解流化床干燥设备中颗粒漂移的定义和影响。
在流化床干燥过程中,颗粒漂移指的是颗粒物在床层中的不均匀分布现象,即部分颗粒在床层中不断上升,形成集聚,而部分颗粒则下沉到排气口处。
颗粒漂移不仅会导致物料干燥效果的降低,还会增加设备维护和清洗的困难,影响生产效率和产品质量。
颗粒漂移的原因可以归结为:床层流动性差、颗粒尺寸分布不均匀、气体流量分布不均和颗粒间的相互作用力等。
首先,床层流动性差是颗粒漂移的主要原因之一。
床层流动性差指的是床层内部气体流动不均匀,造成颗粒物流团聚和颗粒漂移。
其次,颗粒尺寸分布不均匀也是导致颗粒漂移的重要因素之一。
当床层中存在颗粒尺寸分布不均匀时,较大颗粒会团聚而漂移。
此外,气体流量分布不均也会导致颗粒漂移。
气体流量分布不均指的是气体在床层内的流动不平衡,造成床层内的气团不均匀,从而引起颗粒漂移。
最后,颗粒间的相互作用力也会对颗粒漂移起一定的影响。
颗粒之间的相互作用力包括静电力、颗粒间引力和离心力等。
当相互作用力超过颗粒自身重力时,颗粒就会发生漂移。
为了控制颗粒漂移现象,可以采取以下几种方法。
首先,优化流化床干燥设备的设计和操作参数。
例如,增大床层高度、调整进气速度和控制气体流量等措施可以改善床层流动性,减少颗粒漂移。
其次,对颗粒进行粒径分级,控制颗粒尺寸分布的均匀性。
采用筛分、分级等方法,减少颗粒尺寸的差异,可以降低颗粒漂移的发生。
此外,提高气体流量的均匀性也是减少颗粒漂移的有效措施。
通过合理布置进气口和排气口,确保气体流动均匀,可以减少颗粒漂移的发生。
最后,可以采用适当的颗粒表面处理方法来减少颗粒间的相互作用力。
例如,对颗粒进行静电除尘、表面改性等措施,可以减少颗粒之间的相互作用力,从而减少颗粒漂移。
- 1、下载文档前请自行甄别文档内容的完整性,平台不提供额外的编辑、内容补充、找答案等附加服务。
- 2、"仅部分预览"的文档,不可在线预览部分如存在完整性等问题,可反馈申请退款(可完整预览的文档不适用该条件!)。
- 3、如文档侵犯您的权益,请联系客服反馈,我们会尽快为您处理(人工客服工作时间:9:00-18:30)。
流化床制粒影响因素的探讨
[关键词]:流化床,制粒,影响因素
流化床制粒(fluidized bed granulation)又称沸腾制粒,指利用气流使粉末物料悬浮呈沸腾状,再喷入雾状粘合剂使粉末结合成粒,最后得到干燥的颗粒。
在此过程中,物料的混合、制粒、干燥同时完成,因此又称一步制粒。
1964年Scott等将Wurster方法作了改进并应用于医药工业。
我国于1980年引进沸腾制粒、包衣设备,可取代传统湿法制粒。
1流化床的结构和作用原理
流化床制粒机由容器、筛板、喷嘴、捕集袋、空气进出口、物料进出口等部分组成。
经净化的空气加热后通过筛板进入容器,加热物料并使其呈流态化。
此时粘合剂以雾状喷入,使物料粉末聚结成粒子核,进而形成颗粒,同步干燥,得到多孔性、表面积较大的柔软颗粒。
2流化床制粒的优点
与挤出制粒相比,流化床制粒有以下优点:(1)混合、制粒、干燥一次完成,生产工艺简单、自动化程度高;(2)所得颗粒圆整、均匀,溶解性能好;(3)颗粒的流动性和可压性好,压片时片重波动幅度小,所得片剂崩解性能好、外观质量佳;(4) 颗粒间较少或几不发生可溶性成分迁移,减小了由此造成片剂含量不均匀的可能性;(5)在密闭容器内操作,无粉尘飞扬,符合GMP要求。
流化床适于中成药,尤其是浸膏量大、辅料相对较少的中药颗粒的制备,及对湿和热敏感的药物制粒。
3 影响流化床制粒的因素
3.1 制粒材料
用亲水性材料制粒时,粉末与粘合剂互溶,易凝集成粒,故适宜采用流化床制粒。
而疏水性材料的粉粒需藉粘合剂的架桥作用才能黏结在一起,溶剂蒸发后,形成颗粒。
无论是亲水性还是疏水性材料,粉末粒度必须达到80目以上,否则制得的颗粒有色斑或粒径偏大,分布不均匀,从而影响药物的溶出和吸收。
通过进料前将原辅料在机外预混可改善制粒效果。
吸湿性材料黏性强、流动性差、引湿性强,在贮存过程中易吸潮,若用以制粒则受热时会使其中易溶成分溶解导致物料软化结块,未喷雾即出现粘筛和大面积结块,沸腾几乎停止(又称塌床)。
因此,在制粒前应先进行干燥。
经喷雾干燥的浸膏粉粒松散均匀、含水量低、流动性好,易于“流化”,是目前最佳沸腾制粒粉料。
对于黏性特别大和引湿性强的浸膏粉,可制成浓缩流浸膏作为粘合剂喷雾,以其它黏性不大的原、辅料做颗粒母核。
吸湿性较差(如淀粉)的材料成粒较困难,如以水为粘合剂,制得的淀粉颗粒细小,且较松散;改用淀粉浆或糊精浆等黏度较大的溶液作粘合剂,可制得较大粒径的颗粒。
若中药浸膏粉与辅料的密度相差较大,则沸腾时从下至上的物料密度逐渐减小,无法混匀,成粒也困难,压得的片剂色斑严重。
对此可采用前述制成浓缩流浸膏作粘合剂喷雾的方法解决。
但也可能会带来两个问题:(1)流浸膏黏度过大,喷枪易堵塞,所得颗粒粒径也偏大;(2)所得颗粒中流浸膏的含量偏低,与处方量不匹配。
此时必须选择适当的辅料或改进前处理。
制粒材料本身的含水量也会影响颗粒质量。
一般情况下,颗粒粒径随含水量的增加而增大。
因此,进料后应先预热物料进行适当干燥,再喷粘合剂。
3.2进风温度
进风温度高,溶剂蒸发快,降低了粘合剂对粉末的润湿和渗透能力,所得颗粒粒径小、脆性大、松密度和流动性小;有些粘合剂雾滴在接触粉料前就己挥干,造成颗粒中细粉较多。
若温度过高,还会使颗粒表面的溶剂蒸发过快,得到大量外干内湿、色深的大颗粒。
此外,有些粉料高温下易软化,且黏性增大、流动性变差,易粘附在容器壁上,逐渐结成大的团块;甚至物料熔融、粘结在筛板上,堵塞网眼造成塌床。
温度过低,则湿颗粒不能及时干燥,相互聚结成大的团块,也会造成塌床。
3.3进风湿度
进风湿度大,则湿颗粒不能及时干燥,易粘结粉料。
当以易吸湿的中药浸膏粉为底料时,若进风湿度大,往往可能在物料预热时就产生大量结块,造成塌床。
因此,应控制环境湿度,降低进风空气的湿度。
3.4粘合剂黏度
粘合剂黏度大,形成的雾滴大,所得颗粒粒径大、脆性小、硬度大。
也易使物料结块,堵塞喷嘴,造成粘合剂实际流速低,颗粒中细粉多;甚至在喷嘴处会有粘合剂的液滴滴入物料中,造成塌床。
若粘合剂黏度低,则形成的雾滴小,物料成粒困难,所得颗粒中细粉偏多,且较松散。
3.5粘合剂流速
粘合剂流速大,形成的雾滴大,则粘合剂的润湿和渗透能力大,所得颗粒粒径大,脆性小。
在雾化压力确定的条件下,粘合剂流速增加,颗粒的堆密度大。
流速过大时,湿颗粒不能及时干燥会聚结成团块,造成塌床;较小时,颗粒粒径小,有时因雾滴较小而易失去溶剂造成颗粒中细粉多。
3.6雾化空气压力
压力增大,易使粘合剂形成细雾,降低对粉末的湿润能力,所得颗粒粒径小、脆性大,而松密度和流动性则不受影响。
压力过高会改变流化状态,使气流紊乱,粉粒在局部结块;压力较小则粘合剂雾滴大,颗粒粒径大。
3.7风量
风量指进入容器的空气量,其大小(可通过调节风门大小控制)直接影响物料的沸腾状态。
风量大,物料保持良好的沸腾状态,有利于制粒,且热交换快,颗粒干燥及时,但细粉也稍偏多。
但若风量过大,物料沸腾高度过于接近喷枪,致使粘合剂雾化后还未分散就与物料接触,所得颗粒粒度不均匀。
且捕集袋上也容易堆积大量粉尘,影响正常操作。
风量小,物料沸腾状态差,湿颗粒干燥不及时,易造成塌床。
3.8喷嘴位置
喷嘴位于流化室顶部,其高度影响颗粒的粒径分布。
为使粒径分布尽可能窄,应尽量调整喷雾面积与湿床表面积一样大。
喷嘴位置越接近流化粉体,所得颗粒粒径越大,脆性下降,但流动性变化甚微,松密度变化也不大;但过近时,易产生与风量过大时相同的情况。
若位置过高,则会使粘合剂喷到壁上,使颗粒中细粉增多。
3.9静床深度
静床深度是指物料沸腾前占容器的深度,其大小取决于机械设计的生产量和物料性质。
采用锥形床时,静床深度低,颗粒成长明显。
因在线速度小,近壁处流化性不佳,静床深度愈大这种情况愈明显。
静床深度较浅时流化效果好,粒子均有机会与雾滴相遇,达到传热、传质效果。
若太浅则气流直接穿透物料层,不能形成较好的流化状态,影响颗粒质量。
3.10其它因素
喷枪种类、捕集袋质量及振摇频次对颗粒质量也有一定影响。
影响粘合剂雾化效果的因素有粘合剂黏度、流速、雾化空气压力及喷枪种类(单气流、双气流、高速飞轮和高压无气喷枪等)。
单气流喷枪价廉但雾化效果欠佳;双气流喷枪价格合理、效果较佳。
使用时应选择雾化压力低、雾粒粒径分布窄、雾锥对称的喷枪和光滑、通透性好的捕集袋。
若底料中黏性强的粉料较多,应增加振摇频次。
颗粒成型后,若干燥温度过高、时间过长,颗粒之间磨擦也会产生较多的细粉。
4流化床制粒在实际生产中的问题
一般颗粒粒径偏大时,可采用降低粘合剂流速、在其中加入水或乙醇、加热以降低黏度,以及提高进风温度或加大风门的方法解决;粒径偏小时则反之。
但有时加大粘合剂流速会使大颗粒的粒径进一步增大,同时细粉量反而更多。
其原因是粉粒量过大,或粘合剂总量偏低、流速偏大,使粘合剂不能均匀分布,使一部分粉粒无法接触粘合剂。
此时要降低固体物料投料量,或降低粘合剂流速并增加其总量,以改善其均匀性,提高颗粒质量。
当连续使用流化床制粒机时,筛板的网眼易被细粉堵塞,捕集袋上也会粘附较多的细粉,造成风量降低,颗粒不易干燥而结块;有时干燥时间延长数倍,颗粒均匀性差。
因此,连续使用一段时间后,应清洗容器和筛板,必要时更换捕集袋(可观察“捕集袋负压”这一参数,当捕集袋粘附有较多细粉时,通透性会变差,此参数值会变大)。
静电是引起细粉粘附捕集袋又一主要原因,可在捕集袋支架上连接导线,将静电导走。
此外,流化床制得的颗粒以及后序加工生产的片剂等都有卫生学要求。
因此在生产过程中对所接触的热空气、压缩空气都应保证无菌。
热空气一般来源于洁净区的空气,本身具有一定的洁净级别。
并且在进气管道中都装有初、中效或高效过滤器,以保证空气质量;压缩空气应用无油压缩机及压缩空气吸附式干燥器,所用管道为不锈钢。
采用AO级(5×10-7)空气过滤器,二级过滤器选用ACS级(除臭过滤器)。
定期检查,定期更换过滤介质,并对管路清洗消毒。
生产结束后对设备的清洗也是保证产品质量的重要一环。
随着制剂装备的发展,在位清洗技术(clean-in-place,CIP)被引入医药生产中。
CIP清洗技术符合GMP的要求,是生物制药行业的发展方向。
CIP洗涤过程是物理作用和化学作用两方面共同完成的。
物理作用包括高速湍流、流体喷射和机械搅拌;而化学作用则是通过水、表面活性剂、碱、酸和卫生消毒剂进行的,占有主要地位。
在位清洗流化床内一般装有能360°喷射液体的高压喷头,其通过管道与控制系统及清洗液(洗涤剂、纯水等)相连,清洗过程能按预先设置的清洗程序自动进行(无须拆卸设备),以将设备内部完全洗净并消毒。
5 结语
流化床制粒所得颗粒的粒径是颗粒长大和在外力作用下磨损二者保持平衡的结果。
本法技术要求较高,需综合考虑粘合剂的喷雾效果和物料的流化状态,以制得质量合格的颗粒。
(中国医药工业杂志第35卷第9期)。