PFMEA制作实例
FMEA第五版(实例)2023

PFMEA 过程潜在失效模式及影响分析
过程职责: 保密级别:
PMEA 编
页 码:
编制者/日期: 批准/日 期:
版本 号:
第
页, 共
页
结构分析
功能分析
失效分析
风险分析
优化
工 序 编 号
过程项目系 统、子系统 、组件要素 或过程名称
过程步骤
过程影响 因素
注塑机台
过程项目的功能系 统、子系统、组件
要素或过程功能
PFMEA 措施优
先级 (AP)
特 殊 特 性
预防措施
探测 措施
责任 目标 人姓 完成
名 时间
状态
采取 基于 证据 的措
施
实 际 时 间
严 重 度 S
发 生 度 O
探特 测 殊 PFMEA 备注
度 特 AP
D性
工厂:检验来料是 否符合要求
工厂:生产无法使用
针对已制
客户:马达装配
检验来料是 否符合要求
a.作业人员
作业不规范
b.标签打印 包装作业指导
错误\粘贴
书
错误
2
作业员检查
2
L
70
入库储存
储存过程
仓管员
工厂:成品仓储
客户:马达装配 最终用户:车灯转 动
工厂:重复发货增加
将成品放置 规定库位
产品标识与库 位要求是否一
致
工厂成本 客户:影响客户装配
最终用户:无影响
6
a、发货时
发错
b、无法追 现场标识不
2
IQC检验
4
L
最终用户:车灯转
最终用户:影响产品
产
六步法pfmea案例
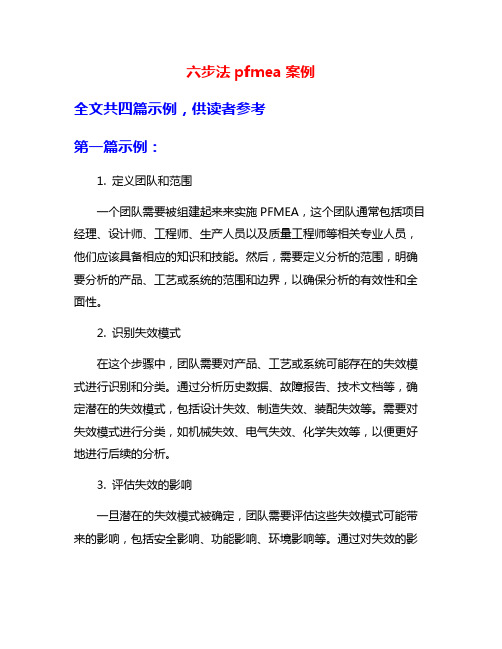
六步法pfmea案例全文共四篇示例,供读者参考第一篇示例:1. 定义团队和范围一个团队需要被组建起来来实施PFMEA,这个团队通常包括项目经理、设计师、工程师、生产人员以及质量工程师等相关专业人员,他们应该具备相应的知识和技能。
然后,需要定义分析的范围,明确要分析的产品、工艺或系统的范围和边界,以确保分析的有效性和全面性。
2. 识别失效模式在这个步骤中,团队需要对产品、工艺或系统可能存在的失效模式进行识别和分类。
通过分析历史数据、故障报告、技术文档等,确定潜在的失效模式,包括设计失效、制造失效、装配失效等。
需要对失效模式进行分类,如机械失效、电气失效、化学失效等,以便更好地进行后续的分析。
3. 评估失效的影响一旦潜在的失效模式被确定,团队需要评估这些失效模式可能带来的影响,包括安全影响、功能影响、环境影响等。
通过对失效的影响进行评估,可以确定关键的失效模式,并优先制定控制措施,以确保产品质量和可靠性。
4. 评估失效的频率和检测能力在这一步骤中,团队需要评估每个失效模式发生的频率和检测能力,即失效的可能性和检测的有效性。
通过对失效频率和检测能力的评估,可以确定高风险的失效模式,并制定相应的控制措施,以减少失效的发生和提高检测的有效性。
5. 制定和实施控制措施基于前面的分析,团队需要制定和实施相应的控制措施,以减少潜在的失效发生和影响。
这些控制措施可以包括设计改进、工艺优化、操作规程更新等,确保产品或系统在生产和使用过程中能够达到预期的性能和可靠性要求。
6. 监控和持续改进团队需要建立一个监控机制来跟踪控制措施的实施效果,并进行持续改进。
通过监控失效模式的发生和影响,可以及时调整和改进控制措施,以确保产品或系统的质量和可靠性得到持续改进。
通过六步法PFMEA的实施,可以帮助团队深入分析潜在失效模式,制定有效的控制措施,从而提高产品质量、减少生产成本和不良问题,提升企业的竞争力。
建议企业在产品设计和生产过程中广泛应用PFMEA方法,并不断优化和完善实施流程,以实现持续的质量改进和效率提升。
完整实用的过程PFMEA实例(注塑企业)
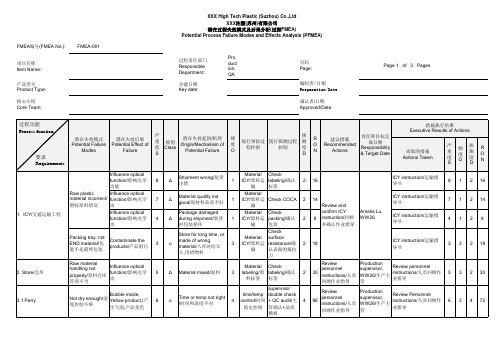
过程责任部门 Responsible Department:
Pro duct ion, QA
关键日期 Key date:
页码 Page:
编制者/日期 Preparation/Date
确认者/日期 Approved/Date
Page 1 of 3 Pages
பைடு நூலகம்
过程功能
Process function 要求
Imaging lens Dia.,
Dim 1: 5.78±0.03 Influence out of spec./镜头 assembly/影响装配
3
直径尺寸超规
Review PM mould
Order start
Production personnel instruction,
o
Wrong insert/嵌入错误
Contaminate the products/产品脏污
3
2. Store/仓库
Raw material handling not properly/原料仓库 管理不当
Influence optical function/影响光学 功
5
3.1 Perry
Not dry enough/湿 度控制不够
1
release
Dim check/尺
plan/订单开 寸确认
2
6
PM mould /点检 磨具
supervisor, incoming inspection WW26/生产主 optical inserts/人员回顾
时包装损坏
输
包装
并确认作业指导
ICY instruction/运输指 导书
ICY instruction/运输指 导书
PFMEA 粗车 范例
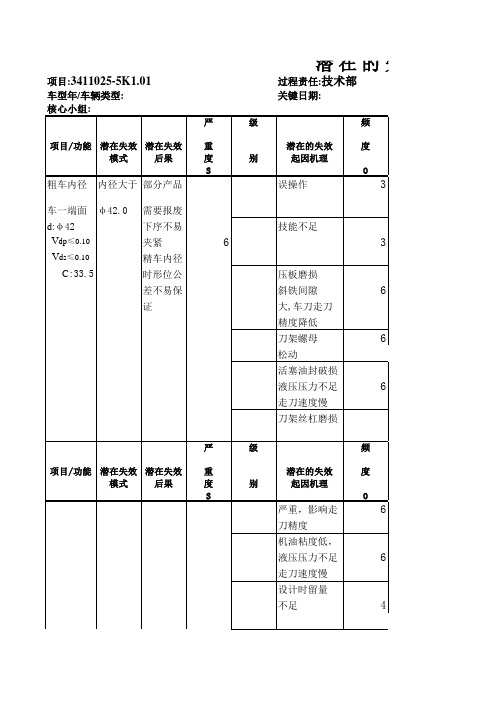
6
108 传送带
设备点检
修磨或更换 维修班
修磨或更换 导轨面
6
90 导轨面
侯国生 3月12日
设备点检
修磨或更换 维修班
修磨或更换 压板
6
90 压板
侯国生 3月12日
措施后果 S O D R P N
3
3
3
27
3
3
3
27
3
3
2
18
措施后果 S O D R P N08 压板
侯国生 3月9日
设备点检 设备点检
5
90 紧固或更换 侯国生
刀架螺母 更换漏油油 维修班
紧固或更换 油封破损漏 油马上更换 修磨或更换
3月15日 刀架螺母 侯国生 3月10日
6
设备点检
现行过程控制 预防 探测 探 测 度 D R N P
108 封
修磨或更换 维修班
责任和 目标 完成 日期
6
6
4
5
百分表示针 转动不灵敏 标准件误差大
5
5
机油杂质多, 堵塞滤油网, 致使液压力
严 重 度 S 级 别 潜在的失效 起因机理 频 度 O
6
项目/功能 潜在失效 潜在失效 模式 后果
不足 d≤φ41.7影响后 工序 精 车内径 产生废 品 刀架螺母 松动 电机传送带张 力过松,主轴转 速达不到额定 转速 导轨面磨损 严重,导轨精度 下降,导致走刀 精度下降, 压板磨损 斜铁间隙 大,车刀走刀 精度降低 技能不足 误操作
换滤油网 3月12日
责任和 目标 完成 日期
现行过程控制 预防 探测
探 测 度 D
六步法pfmea案例

六步法pfmea案例全文共四篇示例,供读者参考第一篇示例:案例背景:某家汽车零部件制造公司在生产过程中发现了一个频繁出现的问题:某零部件的尺寸偏差过大,导致装配时无法完全契合,进而影响产品的性能和质量。
为了解决这一问题,公司决定使用六步法PFMEA 进行分析和改进。
步骤一:确定分析范围团队确定了分析的范围为某零部件的生产工艺。
他们明确了问题的具体表现,以及对产品性能和质量的影响。
团队还确定了分析的目的是为了找出可能引起零部件尺寸偏差的潜在故障模式,并制定相应的控制措施。
步骤二:收集相关信息团队开始收集相关信息,包括零部件的设计图纸、生产工艺流程、设备参数、材料性质等。
他们还对生产现场进行实地考察,观察生产过程中的关键环节,并与相关工程师和操作人员进行沟通交流,了解他们对问题的认识和看法。
步骤三:识别潜在故障模式通过分析收集到的信息,团队识别出了可能导致零部件尺寸偏差的潜在故障模式。
包括:材料供应质量不稳定、设备操作不规范、工艺参数设置不当等。
每个故障模式都被赋予一个风险等级,以确定其重要性和优先级。
步骤四:确定故障影响团队分析每个故障模式的影响范围,包括对产品性能、质量、交付时间等方面的影响。
他们还评估了每个故障模式的可能性和频率,以确定其潜在风险。
步骤五:制定改进控制措施基于对故障模式和影响的分析,团队制定了一系列改进控制措施,以降低潜在风险。
加强材料供应商管理、优化生产工艺流程、规范设备操作规程等。
每个控制措施都被赋予一个责任人和执行时间表,以确保实施和落实。
步骤六:跟踪和持续改进团队制定了一个跟踪和持续改进计划,以监控改进控制措施的执行情况和效果。
他们定期对实施情况进行评估和审查,继续识别和解决可能存在的风险和问题,确保质量和性能的持续提升。
通过六步法PFMEA的分析和改进,该汽车零部件制造公司成功解决了零部件尺寸偏差的问题,提高了产品的质量和性能,降低了生产过程中的风险和损失,进一步提升了企业的竞争力和市场地位。
新版(七步法案例)PFMEA

头下R角偏小 一冲设计不合理 模具制作有偏差 冷墩时光钉直径偏大
5
增加抽风机或空调
2 检查/核对 2
6
要求供应商对模具尺寸进行 中限管理并提供出货检验报
告
3
目视/ 核对/检测
2
6
每隔两个小时对锁紧螺丝紧 固一次
3
检查
2
8
修理模具R角位置
3 检测 2
8
修改一冲相关尺寸
3 检测 2
6
要求供应商对模具尺寸进行 中限管理并提供出货检验报
05 热处理
硬度检测 (维式硬度计)
产品外观及硬度性能符合图纸 目视检测产品外观及仪器检测产品硬度性
要求
能符合图纸要求
电镀后表面发黑
产品从清洗区清除杂质后进入淬火炉进行
渗碳淬火(预热区860℃-60/+20℃,保温
产品表面硬度与芯部硬度需符 区900℃ ±10℃,淬火区 860℃ ±10
合图纸工艺要求:
完成状态
结合经验重新设计一冲模具
2020/3/10 8 2 1 ※ L
完成状态
严格要求模具厂商按我司图纸尺寸制作 2020/3/10 6 2 1
L
我司模具按图纸中限尺寸设计,并要求模具厂 完成状态 商对每批模具进行尺寸检验并提供检验报告到 2020/3/10 7 2 1 ※ L
我司核对
完成状态
要求牙板供应商严格按标准要求设计牙板并提 供检测数据报告
提供检测报告
对
高成
2020/3/10
要求牙板供应商严格按标准要求设计牙板
目视/核 对
董茂文
2020/3/10
将主模模腔尺寸定义在中限并要求供应商 目视/核
PFMEA的例子
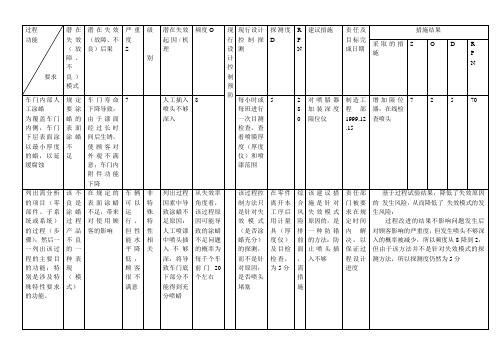
在规定的表面涂蜡不足,带来对使用顾客的影响
车辆可以运行,但性能水平降低,顾客很不满意
非特殊特性相关
列出过程因素中导致涂蜡不足原因:人工喷漆中喷头插入不够深,将导致车门底下部分不能得到充分喷蜡
从失效率角度看,该过程原因可能导致的涂蜡不足问题的概率为每千个车前门20个左右
RPN
建议措施
责任及目标完成日期
措施结果
采取的措施
S
O
D
R
P
N
车门内部人工涂蜡
为覆盖车门内侧,车门下层表面涂以最小厚度的蜡,以延缓腐蚀
规定要涂蜡的表面涂蜡不足
车门寿命下降导致:由于漆面经过长时间后生锈,使顾客对外观不满意;车门内附件功能下降
7
人工插入喷头不够深入
8
每小时或每班进行一次目测检查,查看厚度(厚度仪)和喷漆范围
7
人工插入喷头不够深入
8
每小时或每班进行一次目测检查,查看喷膜厚度(厚度仪)和喷漆范围
5
280
对喷腊器加装深度限位仪
制造工程部1999.12.15
增加限位器,在线检查喷头
7
2
5
70
列出需分析的项目(零部件、子系统或系统)的过程(步骤);然后一一列出该过程的主要目的功能;特别是涉及特殊特性要求的功能。
过程改进的结果不影响问题发生后对顾客影响的严重度,但发生喷头堵塞的概率被减少,所有频度从5降到1(完全不会发生),但由于该方法并不是针对失效模式的探测方法,所有探测度仍然为5分。
ቤተ መጻሕፍቲ ባይዱ过程
功能
要求
潜在失效(故障、不良)模式
潜在失效(故障、不良)后果
严重度
扬声器PFMEA案例

有警告的危害
当潜在的失效模式在有警告的情况下影响车辆安全运行和/或涉及不符合政府法规的情形时,严重度定级非常高
或可能在有警告的情况下对(机器或总成)操作者造成危害
9
很高
车辆/项目不能工作(丧失基本功能)
或100%的产品可能需要报废,或者车辆/项目需在返修部门返修1个小时以上
8
高
车辆/项目可运行但性能水平下降。
案例:
某音响制造公司为某汽车制造商设计制造一车用扬声器。以下是汽车制造商提出的(部分)要求:
安装尺寸▼:外形图标注,为4’扬声器。
可靠性要求:3年无故障▼。
阻抗:8.0±0.8 OHM at 400Hz
特性灵敏度级:88±2dB
f0:120±15Hz
额定功率:8W
长期最大功率:20W
注:其中带▼为特殊特性。
扬声器主要技术参数:
…………
内部要求:
易于装配,一次装配合格率(直通率)大于99%。
案例:为了保证产品设计意图完整地贯彻到生产过程中,公司组建了PFMEA小组。小组组长由工艺工程师王五担任,小组成员有品质工程师赵六,SQE钱七,以及计划将来进行该产品生产的生产车间主任贾师傅。
PFMEA小组首先利用特性矩阵,将产品关键特性对应到生产过程的中,在此基础上,PFMEA小组开发了PFMEA
2006-10-30:SQE小组,确定批准要求并完成供应商手册。2008-10-01,供应商满足手册要求
尤全
10-30前投入使用
5
2
2
20
过程FMEA的标准表
系统潜在失效模式及后果FMEA编号
子系统(PFMEA)共页,第页
部件设计责任编制人
车型年/车辆类型关键日期FEMA日期(编制)(修订)
- 1、下载文档前请自行甄别文档内容的完整性,平台不提供额外的编辑、内容补充、找答案等附加服务。
- 2、"仅部分预览"的文档,不可在线预览部分如存在完整性等问题,可反馈申请退款(可完整预览的文档不适用该条件!)。
- 3、如文档侵犯您的权益,请联系客服反馈,我们会尽快为您处理(人工客服工作时间:9:00-18:30)。
不可能-肯定不可能检测出 微小-控制方法可能检测不出 很小-控制方法检测出的机率很低
很小-控制方法检测出的机率很低
中等-控制方法可能检测出 中等-控制方法可能检测出
具
4
中上-控制方法检测出的机率较高
防
防错-后续工位不能接受;作业准备、首 件检查时进行量检具检测
多重防错-供应、选择、安装、确认。不能通过 缺陷产品
包装运输的分析
Potential Failure Mode and Effects Analysis
潜在失效模式与后果分析-5
FMEA的升版时机-1
• 工程设变时 –材料变更 –工具或加工手段变更 –LAY-OUT顺序变更 –场地变更 –主要人员变更
Potential Failure Mode and Effects Analysis
Potential Failure Mode and Effects Analysis
潜在失效模式与后果分析-18
•每一失效模式可能有若干个潜在的后果,最后的严重度应 根据最严重的后果而确定。
Potential Failure Mode and Effects Analysis
潜在失效模式与后果分析-19
PFMEA包含哪些
物料来源
材料包装、运输的分析 协力厂生产能力分析 供应商可靠性、稳定性分析
DFMEA问题点的延伸分析
IQC,FQC的分析
生产制程的分析
作业流程及作业手法的分析 工装治具的合理性、适用性分析 上岗人员技能及惰性分析 使用材料的分析 生产中半成品的转移路线及工具的分析
• 使用标准表单(客户特殊要求依客户的为准 )
• 工程试作时使用1.0版量产时升版更新
• 从1.0版开始建立覆历表,并适时更新
• 所用表单格式不可更改或拉动
• 应将防呆措施一览表相对应以降低频度
Potential Failure Mode and Effects Analysis
潜在失效模式与后果分析-10
Potential Failure Mode and Effects Analysis
潜在失效模式与后果分析-27
以下是以S/O/D/RPN为基础需 进行对策的项目的判定依据
提出建议行动的优先级 Priority to take actions S=9/10(必须有针对根本原因的行动) 高S×O项目 / Higher S×O 高RPN项目 / Higher RPN Practice Exercise:
潜在失效模式与后果分析-13
图例1详解
一处编号 两处蓝字 两处黄字
1-1:1为制造流程图的工程站编号; -1为该工程站的第一张 预防栏中的方式不列入探测度的考量 表示在没有工程设变的情况下只能改变 频度和探测度 三个红色字体分别代表三种需对策的情况
三处红色加大字体
Potential Failure Mode and Effects Analysis
潜在失效模式与后果分析-14
FMEA 表头 •使用了正确的FMEA1.2版的表格 •包含了正确的编制日期(A表日期)和更新日期 •所有核心小组的成员已被识别 •包含了产品品号、车型年份和FMEA编号 •包含了FMEA编制者及责任部门(用于车厂联系)
Potential Failure Mode and Effects Analysis
Potential Failure Mode and Effects Analysis
潜在失效模式与后果分析-21
•若频度数定为1,则这一原因造成失效只存在理论 上的可能性,且小组中的任何成员都不曾遇到因这 一原因造成的失效。
Potential Failure Mode and Effects Analysis
潜在失效模式与后果分析-8
PFMEA的组成顺序
• 料件及进料部份
• 半成品加工部份
• 成品组装部份
• 成品测试部份
• 包装运输部份
• 市场问题部份
Potential Failure Mode and Effects Analysis
潜在失效模式与后果分析-9
制作PFMEA的一般原则
• 依A表时程完成
实
作
生技课FMEA表格的填写规则
Potential Failure Mode and Effects Analysis
潜在失效模式与后果分析-11
图例1:
Potential Failure Mode and Effects Analysis
潜在失效模式与后果分析-12
过程:
失效模式1
失效效应1 失效效应2 。 。 失效原因N
严 重 度-SGM版
等级
10 9 8 7
顾客的后果
在无警告的情况下影响车辆安全运行和/或涉及不符合政府法规 在有警告的情况下影响车辆安全运行和/或涉及不符合政府法规 车辆\项目不能工作(丧失基本功能)
制造/装配后果
或可能在无警告的情况下不对(机器或总成)操作者造成危害 或可能在有警告的情况下不对(机器或总成)操作者造成危害 或100%的产品可能需要报废,或者车辆/项目需在返修部门返修1 小时以上 或产品需进行分拣 /一部分需报废,或车辆\项目在返修部门返修 0.5~1小时以上
潜在失效模式与后果分析-6
FMEA的升版时机-2
• 发现问题时
–市退反馈的问题 –客户抱怨的问题
–生产过程中发现的问题
–QC人员发现的不良缺失
• 效应确认及应用时
–对策完成时或对策效果显现时
Potential Failure Mode and Effects Analysis
潜在失效模式与后果分析-7
Case Case Case Case A B C D 严重度S× 2 10 3 3 频度O× 5 2 3 10 不易探测度D 8 2 5 2 =RPN 80 40 45 60
潜在失效模式与后果分析-22
频 度-SGM版
等级
10 9 8 7 6 5 4 3 2 1
失效可能性
很高 很高 高 高 中等 中等 中等 低
PPM
>50000 50000 20000 10000 5000 2000 1000 500
过程能力PPK
<0.55 >0.55 >0.78 >0.88 >0.84 >1.00 >1.10 >1.20
潜在失效模式与后果分析-1
PFMEA制作实例
作为一个合格的制程工程师,我们应预防问 题,而不仅是发现问题。
——编者语
Potential Failure Mode and Effects Analysis
潜在失效模式与后果分析-2
APQP成员的组成
• 营业部门 • 采购部门
• 工程部门
• 品保部门
完整的FMEA
• 制造部门
TEAM
Potential Failure Mode and Effects Analysis
潜在失效模式与后果分析-3
PFMEA制作时机
• 依A表规定时程
• 新产品雏形完成 • 工程试作前
Potential Failure Mode and Effects Analysis
潜在失效模式与后果分析-4
Potential Failure Mode and Effects Analysis
潜在失效模式与后果分析-17
•潜在失效后果 •在DFMEA中,针对每一失效模式,已列出对零件、部件、高一级的总成、系 统、整车、政府法规和顾客的后果 •在PFMEA中,针对每一失效模式,已列出对下一级使用者、下游的所有使用者、 最终顾客、整车性能、操作者安全、政府法规符合性和设备的后果 •所有的后果都与失效模式相关联 •对每一后果都评定了严重度 •未将失效原因列为失效后果
或对操作/操作者而言有轻微的不方便或无影响
Potential Failure Mode and Effects AnalysisBiblioteka 潜在失效模式与后果分析-20
假定一:认为本工序的原材料是合格的;潜在失效原因可以是 假定二:考虑本工序的原材料的变差;潜在失效原因可以是:
材料过硬、定位孔位臵不对等
•潜在失效起因/机理 •对于严重度为9或10失效后果,其失效原因是根本原因,相应的零件特性已被记录 •若适用,对于同一失效模式列出了多个失效原因 •在确定失效原因时,“两种假设”都被使用了 •未将失效后果误列为失效原因 •在DFMEA中,未将“作业员错误”或“设备故障”列为失效原因 •在PFMEA中,未将“作业员错误”或“设备故障”列为失效原因,尤其是对关键 特性、重要特性和涉及安全的特性
采取对策的时机
• S, S× O, RPN值最高的项目 • RPN值超过定义及格值的项目
(SGM标准为40分,TTE标准为80分2004年11月开始)
• 包含特殊特性的项目
• 单项值超出及格范围的项目
(即严重度S/频度O/探测度D中的一项)
Potential Failure Mode and Effects Analysis
潜在失效模式与后果分析-15
•功能 •识别了所有的功能及目的 •功能表述的形式为动词-名词-可测定的程度 •技术规范、工程要求和工艺要求被明确表述
Potential Failure Mode and Effects Analysis
潜在失效模式与后果分析-16
会怎样出错(失效)?
•潜在失效模式 •所有的失效模式已被识别 •在PFMEA中,应使用“为什么零件会被据收”来表述失效模式 •没有将失效后果或原因列入失效模式
TTE标准
很低
很低
100
<10
>1.30
>1.67