焙烧-浸出-磁选回收铜渣中的铁
金属矿物的提取原理
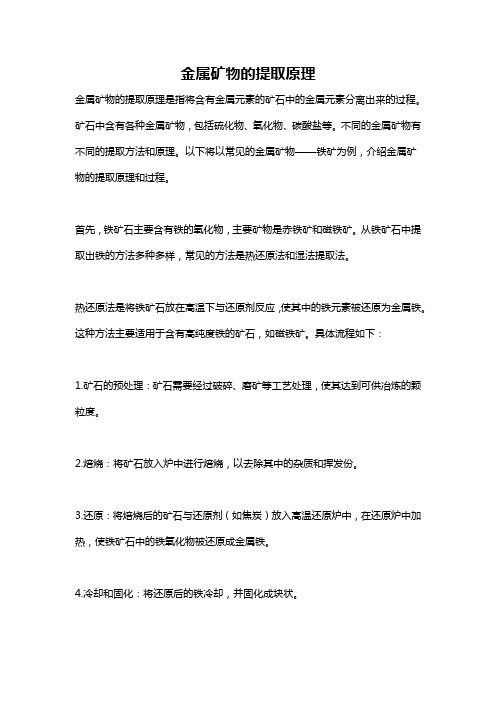
金属矿物的提取原理金属矿物的提取原理是指将含有金属元素的矿石中的金属元素分离出来的过程。
矿石中含有各种金属矿物,包括硫化物、氧化物、碳酸盐等。
不同的金属矿物有不同的提取方法和原理。
以下将以常见的金属矿物——铁矿为例,介绍金属矿物的提取原理和过程。
首先,铁矿石主要含有铁的氧化物,主要矿物是赤铁矿和磁铁矿。
从铁矿石中提取出铁的方法多种多样,常见的方法是热还原法和湿法提取法。
热还原法是将铁矿石放在高温下与还原剂反应,使其中的铁元素被还原为金属铁。
这种方法主要适用于含有高纯度铁的矿石,如磁铁矿。
具体流程如下:1.矿石的预处理:矿石需要经过破碎、磨矿等工艺处理,使其达到可供冶炼的颗粒度。
2.焙烧:将矿石放入炉中进行焙烧,以去除其中的杂质和挥发份。
3.还原:将焙烧后的矿石与还原剂(如焦炭)放入高温还原炉中,在还原炉中加热,使铁矿石中的铁氧化物被还原成金属铁。
4.冷却和固化:将还原后的铁冷却,并固化成块状。
湿法提取法是以化学方法将金属矿物中的金属元素溶解出来,并通过物理或化学方法进行分离纯化。
对于赤铁矿等铁矿石来说,利用湿法提取法进行提取的过程如下:1.浸取:将矿石碎石浸入酸性或碱性溶液中,使金属元素溶解。
2.过滤:将浸取液通过过滤装置过滤,去除其中的固体杂质。
3.沉淀:通过控制溶液的pH值、温度等参数,使金属元素沉淀成金属盐。
4.还原:将金属盐进行还原处理,将金属元素还原为金属。
5.纯化:通过电解、溶剂萃取等方法对金属进行纯化和提纯,得到需要的金属产品。
不同金属矿物的提取过程和原理有所不同,但基本思路都是将金属元素从矿石中分离出来。
金属矿物的提取过程中需要注意保护环境,避免废水、废气、废渣等对环境造成污染。
同时,提取过程中还要考虑能源消耗和成本因素,以实现高效、低能耗、低污染的提取方法。
焙烧-浸出-磁选回收铜渣中的铁
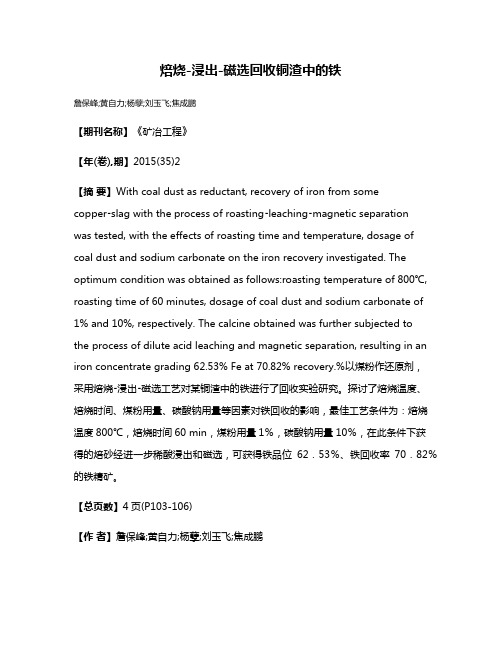
焙烧-浸出-磁选回收铜渣中的铁詹保峰;黄自力;杨孽;刘玉飞;焦成鹏【期刊名称】《矿冶工程》【年(卷),期】2015(35)2【摘要】With coal dust as reductant, recovery of iron from somecopper⁃slag with the process of roasting⁃leaching⁃magnetic separation was tested, with the effects of roasting time and temperature, dosage of coal dust and sodium carbonate on the iron recovery investigated. The optimum condition was obtained as follows:roasting temperature of 800℃, roasting time of 60 minutes, dosage of coal dust and sodium carbonate of 1% and 10%, respectively. The calcine obtained was further subjected tothe process of dilute acid leaching and magnetic separation, resulting in an iron concentrate grading 62.53% Fe at 70.82% recovery.%以煤粉作还原剂,采用焙烧⁃浸出⁃磁选工艺对某铜渣中的铁进行了回收实验研究。
探讨了焙烧温度、焙烧时间、煤粉用量、碳酸钠用量等因素对铁回收的影响,最佳工艺条件为:焙烧温度800℃,焙烧时间60 min,煤粉用量1%,碳酸钠用量10%,在此条件下获得的焙砂经进一步稀酸浸出和磁选,可获得铁品位62.53%、铁回收率70.82%的铁精矿。
铜渣中铁组分的直接还原与磁选回收
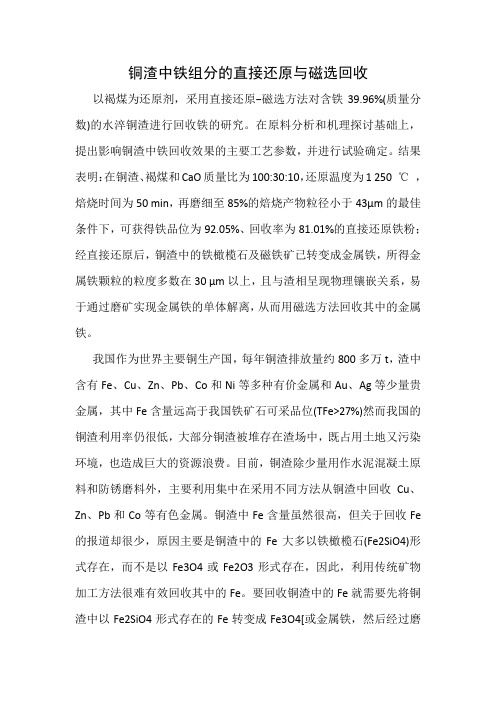
铜渣中铁组分的直接还原与磁选回收以褐煤为还原剂,采用直接还原−磁选方法对含铁39.96%(质量分数)的水淬铜渣进行回收铁的研究。
在原料分析和机理探讨基础上,提出影响铜渣中铁回收效果的主要工艺参数,并进行试验确定。
结果表明:在铜渣、褐煤和CaO质量比为100:30:10,还原温度为1 250 ℃,焙烧时间为50 min,再磨细至85%的焙烧产物粒径小于43µm的最佳条件下,可获得铁品位为92.05%、回收率为81.01%的直接还原铁粉;经直接还原后,铜渣中的铁橄榄石及磁铁矿已转变成金属铁,所得金属铁颗粒的粒度多数在30 µm以上,且与渣相呈现物理镶嵌关系,易于通过磨矿实现金属铁的单体解离,从而用磁选方法回收其中的金属铁。
我国作为世界主要铜生产国,每年铜渣排放量约800多万t,渣中含有Fe、Cu、Zn、Pb、Co和Ni等多种有价金属和Au、Ag等少量贵金属,其中Fe含量远高于我国铁矿石可采品位(TFe>27%)然而我国的铜渣利用率仍很低,大部分铜渣被堆存在渣场中,既占用土地又污染环境,也造成巨大的资源浪费。
目前,铜渣除少量用作水泥混凝土原料和防锈磨料外,主要利用集中在采用不同方法从铜渣中回收Cu、Zn、Pb和Co等有色金属。
铜渣中Fe含量虽然很高,但关于回收Fe 的报道却很少,原因主要是铜渣中的Fe大多以铁橄榄石(Fe2SiO4)形式存在,而不是以Fe3O4或Fe2O3形式存在,因此,利用传统矿物加工方法很难有效回收其中的Fe。
要回收铜渣中的Fe就需要先将铜渣中以Fe2SiO4形式存在的Fe转变成Fe3O4[或金属铁,然后经过磨矿−磁选工艺加以回收。
高温熔融氧化法[16] 或加入调渣剂方法是两种常见的将铜渣中的Fe2SiO4转化为Fe3O4而磁选回收的有效方法,而关于将铜渣中的Fe2SiO4直接还原成金属铁,再通过磨矿−磁选回收金属铁的方法至今未见报道。
为此,本文作者拟对这种回收Fe的方法进行可行性试验和回收效果研究,以期为回收利用铜渣中的Fe 提供一种新途径。
铜尾渣深度还原回收铁工艺研究
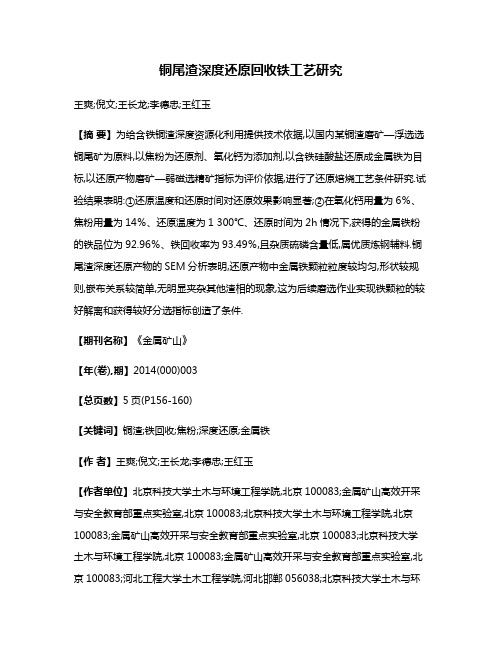
铜尾渣深度还原回收铁工艺研究王爽;倪文;王长龙;李德忠;王红玉【摘要】为给含铁铜渣深度资源化利用提供技术依据,以国内某铜渣磨矿—浮选选铜尾矿为原料,以焦粉为还原剂、氧化钙为添加剂,以含铁硅酸盐还原成金属铁为目标,以还原产物磨矿—弱磁选精矿指标为评价依据,进行了还原焙烧工艺条件研究.试验结果表明:①还原温度和还原时间对还原效果影响显著;②在氧化钙用量为6%、焦粉用量为14%、还原温度为1 300℃、还原时间为2h情况下,获得的金属铁粉的铁品位为92.96%、铁回收率为93.49%,且杂质硫磷含量低,属优质炼钢辅料.铜尾渣深度还原产物的SEM分析表明,还原产物中金属铁颗粒粒度较均匀,形状较规则,嵌布关系较简单,无明显夹杂其他渣相的现象,这为后续磨选作业实现铁颗粒的较好解离和获得较好分选指标创造了条件.【期刊名称】《金属矿山》【年(卷),期】2014(000)003【总页数】5页(P156-160)【关键词】铜渣;铁回收;焦粉;深度还原;金属铁【作者】王爽;倪文;王长龙;李德忠;王红玉【作者单位】北京科技大学土木与环境工程学院,北京100083;金属矿山高效开采与安全教育部重点实验室,北京100083;北京科技大学土木与环境工程学院,北京100083;金属矿山高效开采与安全教育部重点实验室,北京100083;北京科技大学土木与环境工程学院,北京100083;金属矿山高效开采与安全教育部重点实验室,北京100083;河北工程大学土木工程学院,河北邯郸056038;北京科技大学土木与环境工程学院,北京100083;金属矿山高效开采与安全教育部重点实验室,北京100083;北京科技大学土木与环境工程学院,北京100083;金属矿山高效开采与安全教育部重点实验室,北京100083【正文语种】中文【中图分类】TD925.7;TD926.4铜渣是铜冶炼过程中产生的固体废弃物,我国每年新增铜渣量达1 000万t左右,累计堆积量已达到1.2亿t[1]。
硫酸盐焙烧-浸出法分离高炉粉尘中锌铁的研究

硫酸盐焙烧-浸出法分离高炉粉尘中锌铁的研究硫酸盐焙烧-浸出法分离高炉粉尘中锌铁的研究引言:高炉粉尘是冶炼铁矿石过程中产生的副产品之一,其中含有大量的有价值金属,如铁、锌等。
然而,高炉粉尘中的金属元素之间往往相互混合,使得其分离和回收变得困难。
近年来,研究人员提出了许多不同的分离方法,硫酸盐焙烧-浸出法是其中一种有效的分离方法。
本文将对硫酸盐焙烧-浸出法分离高炉粉尘中锌铁的研究进行探讨。
实验方法:1.样品制备:将高炉粉尘样品收集后进行研磨,得到颗粒大小均匀的样品。
2.硫酸盐焙烧:将样品与硫酸盐在高温下反应,将锌铁矿石转化为硫酸盐或氧化物。
3.浸出:将焙烧后的样品与浸出剂(如硫酸、盐酸等)进行溶解,使得锌和铁能被溶解出来。
4.分离:通过滤纸或其他方法分离出溶液中的沉淀,其中包含了锌和铁等金属元素。
5.分析:对分离出的沉淀进行化学分析,确定其中含有的锌和铁的含量。
实验结果:经过硫酸盐焙烧-浸出法分离,我们得到了高炉粉尘中的锌和铁的含量。
实验结果显示,通过合适的焙烧温度和浸出剂浓度,可以有效地将锌和铁分离开。
分析结果显示,焙烧后的样品中锌的含量明显增加,而铁的含量则大幅度减少。
这说明硫酸盐焙烧-浸出法可以高效地分离高炉粉尘中的锌和铁。
讨论:硫酸盐焙烧-浸出法是一种通过氧化和溶解的方法将锌和铁分离的有效手段。
在焙烧过程中,硫酸盐可以与锌和铁发生反应,将其转化为相应的硫酸盐或氧化物。
而在浸出过程中,选择合适的酸性浸出剂可以有效地将硫酸盐或氧化物溶解出来。
通过这种方法,我们可以快速、高效地将高炉粉尘中的锌和铁分离出来,从而实现其进一步的回收和利用。
结论:本研究通过硫酸盐焙烧-浸出法成功分离了高炉粉尘中的锌和铁。
硫酸盐焙烧-浸出法是一种高效的分离方法,通过合适的焙烧温度和浸出剂浓度可以实现锌和铁的有效分离。
本研究为高炉粉尘中金属元素的回收和利用提供了一种可行的解决方案。
未来,还可以进一步研究优化分离条件,以提高回收率和提纯度,并对分离后的金属元素进行进一步的利用和应用。
钢铁冶炼中采用焙烧法的铁精矿提炼技术

钢铁冶炼中采用焙烧法的铁精矿提炼技术钢铁产业是国家重要的基础产业之一,其发展水平直接关系到国家的经济实力和国家的安全利益。
铁矿石是钢铁冶炼的主要原料之一,其提炼技术影响了钢铁产业的生产效率和生产成本。
在钢铁冶炼中,焙烧法是一种重要的铁精矿提炼技术,其通过矿石中氧化铁的还原获取铁,具有高效、节能、环保等特点。
一、铁精矿焙烧工艺流程铁精矿焙烧工艺流程一般分为三个阶段:加热、焙烧和冷却。
在加热和焙烧过程中,铁精矿中的氧化铁逐渐还原为亚氧化铁和金属铁,同时伴随着氧化反应。
而在冷却阶段,则是将矿石冷却至室温,以保证合格的产品产出。
二、焙烧法的优点1.高效节能焙烧法采用的是高炉前处理技术,可大幅度降低高炉内焦炭的消耗,生产出的铁水可以直接进入高炉冶炼,同时还可以减少高炉内的还原反应次数,提高生产效率,节约能源。
2.提高产品品质采用焙烧法进行铁精矿提炼可以保证产品的品质,避免因矿石品质不佳、矿石成分难以控制等因素影响产品品质的问题。
3.环保焙烧法的炉渣中能够固定其它金属元素,治理危废物质。
三、提高焙烧效率需要注意的问题1.掌握好焙烧温度铁精矿在不同温度下还原状况不同,掌握好焙烧温度可以保证还原反应进行顺利,提高焙烧效率。
2.保证气流充足铁精矿焙烧需要大量的氧气参与,因此保证气流充足是至关重要的。
3.控制炉温炉温是影响焙烧效率的关键因素之一,需要根据矿石的化学成分、含铁量、含硫量等多种因素来控制炉温,以提高焙烧效率。
综上所述,焙烧法是一种高效、节能、环保的铁精矿提炼技术,在钢铁产业中具有广泛的应用前景。
在生产实践中,需要掌握好焙烧温度、保证气流充足、控制炉温等多种技术和操作问题,才能够提高焙烧效率,优化铁精矿提炼工艺,从而更好地发挥焙烧法的优点,推动钢铁产业的高质量发展。
回收铜渣中铜铁的先进基础工艺
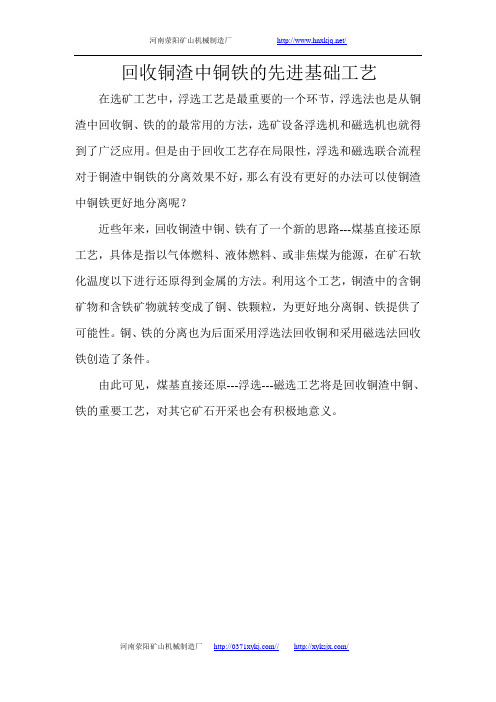
河南荥阳矿山机械制造厂/
回收铜渣中铜铁的先进基础工艺在选矿工艺中,浮选工艺是最重要的一个环节,浮选法也是从铜渣中回收铜、铁的的最常用的方法,选矿设备浮选机和磁选机也就得到了广泛应用。
但是由于回收工艺存在局限性,浮选和磁选联合流程对于铜渣中铜铁的分离效果不好,那么有没有更好的办法可以使铜渣中铜铁更好地分离呢?
近些年来,回收铜渣中铜、铁有了一个新的思路---煤基直接还原工艺,具体是指以气体燃料、液体燃料、或非焦煤为能源,在矿石软化温度以下进行还原得到金属的方法。
利用这个工艺,铜渣中的含铜矿物和含铁矿物就转变成了铜、铁颗粒,为更好地分离铜、铁提供了可能性。
铜、铁的分离也为后面采用浮选法回收铜和采用磁选法回收铁创造了条件。
由此可见,煤基直接还原---浮选---磁选工艺将是回收铜渣中铜、铁的重要工艺,对其它矿石开采也会有积极地意义。
河南荥阳矿山机械制造厂///。
铜渣浮选尾料中回收铜铁的研究

从图 4 中可以看出,随着焦炭加入量的增加,熔炼炉渣含铁 逐渐降低,当焦炭加入量达到 9% 以上时,熔炼炉渣中含铁不再 发生大幅降低,说明在焦炭加入量达到 9% 时,铜渣浮选尾料中 的铁基本被还原完全,同时考虑到生产实际中成本,选择焦炭的 加入量为 9% 为宜。 3.2 氧化钙加入量对熔炼炉渣含铁的影响
将铜渣浮选尾料磨碎至粒度为 200 目时,做扫描电镜分析, 结果如图 2 所示。
图 1 金川铜渣浮选尾料的 XRD 分析
收稿日期 :2020-05 作者简介 :刘瑜,女,生于 1976 年,汉族,四川邻水人,本科,副教授,研究方向 : 冶金工程、教育教学管理。
图 2 金川铜渣浮选尾料 SEM 照片
对 a、b、c、d、e 五点进行能谱分析,结果见表 2 所示。
金川铜渣浮选尾料中含铜 0.24%、含铁 42.58%、含二氧化硅 30.89%。 1.2 铜渣浮选尾料的晶相结构
通过 XRD 分析可知金川铜渣浮选尾料主要成分为 Fe2SiO4 和 Fe3O4。 1.2.1 铁橄榄石 Fe2SiO4
铁橄榄石属于斜方晶系,硬度为 6.5,比重为 4.32,熔点为 1205℃,颜色深灰。铁橄榄石是铜渣中的主要脉石矿物,含量较 高,结晶粒度较粗,形状较为规则。 1.2.2 磁铁矿相 Fe3O4
表 2 能谱分析结果
Fe
O
Si
Al Cu Zn Ca Mg
S
a 83.8 13.457 1.092 1.651 — — — — —
- 1、下载文档前请自行甄别文档内容的完整性,平台不提供额外的编辑、内容补充、找答案等附加服务。
- 2、"仅部分预览"的文档,不可在线预览部分如存在完整性等问题,可反馈申请退款(可完整预览的文档不适用该条件!)。
- 3、如文档侵犯您的权益,请联系客服反馈,我们会尽快为您处理(人工客服工作时间:9:00-18:30)。
表 2㊀ 铁物相分析结果
物相 硫酸铁 金属铁 磁铁矿 赤褐铁矿 铁橄榄石 合计 含量 / % 0.19 0.14 7.20 13.51 22.69 43.73
占有率 / % 0.43 0.32 30.89 16.47 100.00 51.89
焙烧时,添加的煤粉的工业分析结果见表 3㊂
表 3㊀ 煤粉工业分析结果( 质量分数) / %
渣进行了焙烧⁃浸出⁃磁选工艺回收其中铁的研究㊂
用率很低,大部分铜渣被堆存在渣场中,既占用土地又 污染环境,也造成巨大的资源浪费
[5] [4]
㊂ 然而我国铜渣利 ㊂ 由于铜渣中的
化学成分及铁物相分析结果分别见表 1 2㊂ 通过偏光 显微镜㊁矿相显微镜对铜渣入选之前的原渣样品进行光 铁矿物,其中铁矿物主要为磁铁矿㊁铁橄榄石;非金属矿 物主要为橄榄石㊁辉石㊁长石㊁石英㊁玻璃质和其他脉石 43.73%,其它可利用元素含量都很低㊂ 铁物相分析结果 表明,尾矿中的铁主要以铁橄榄石和磁性铁形式存在㊂ 矿物㊂ 化学元素分析结果表明, 浮铜尾矿中铁品位为 学分析,结果表明,原渣样品中金属矿物主要为铜矿物㊁
焙烧 温 度 800 ħ , 煤 粉 用 量 1%, 碳 酸 钠 用 量
图 7㊀ 碳酸钠用量实验结果
2.5㊀ 优化条件下的扩大实验
煤粉用量 1%,碳酸钠用量 10%㊂ 在此条件下,按照图 3 62.53%㊁铁回收率 70.82% 的工艺指标㊂ 2.6㊀ 焙烧前后试样的 XRD 分析
确定优化条件:焙烧温度 800 ħ ,焙烧时间 60 min,
第 35 卷第 2 期 2015 年 04 月
MINING AND METALLURGICAL ENGINEERING
矿㊀ 冶㊀ 工㊀ 程
Vol.35 ɴ2 April 2015
焙烧 ⁃浸出 ⁃磁选回收铜渣中的铁
詹保峰, 黄自力, 杨㊀ 孽, 刘玉飞, 焦成鹏
①
( 武汉科技大学 冶金矿产资源高效利用与造块湖北省重点实验室,湖北 武汉 430081)
而 Fe2 O3 在高温条件下通过炭( 煤粉) 可还原成 Fe3 O4 : 3Fe 2 O 3( s) +C( s)������������ 2Fe 3 O 4( s) +CO( g) (3)
θ
匀,在一定温度下进行焙烧,焙砂经稀酸浸出得到浸出 渣, 浸 出 渣 通 过 磁 选 回 收 铁 精 矿㊂ 实 验 流 程 如 图 3 所示㊂
图 6㊀ 煤粉用量实验结果
2.4㊀ 碳酸钠用量的影响
碳酸钠用量的影响如图 7 所示㊂ 由图 7 可知, 随着碳 酸钠用量增加,铁品位呈上升趋势,铁回收率呈下降趋 势,当碳酸钠用量为 10% 时, 铁精矿品位和铁回收率
图 4㊀ 焙烧温度实验结果
焙烧温度 800 ħ ,焙烧时间 60 min,煤粉用量 1%,
实验原料为某铜渣选矿厂浮选铜的尾矿, 其主要
铁大部分以铁橄榄石形式存在, 少部分以磁性氧化铁 形式存在, 且粒径小, 常规磁选时只起到机械分离作 用 物加工方法 ,因此,尽管铜渣中 Fe 含量很高, 但利用传统矿
[6]
的铁就需要先将铜渣中的 Fe 2 SiO 4 转变成 Fe 3 O 4 或金
①
很难有效回收其中的铁; 要回收铜渣中
第 35 卷
43.73 0.24
Fe
表 1㊀ 铜渣浮铜尾矿化学多元素分析结果( 质量分数) / %
Cu 0.31 3.43 Pb Zn 0.23 0.012 0.6 23.19 3.75 Mo Co S SiO 2 Al 2 O 3 CaO 3.32
MgO 1.3
Na2 CO3(s) +SiO2(s)������������ Na2 SiO3(s) +CO2(g) (4) 2FeO( s) +SiO 2( s)������������ 2FeO㊃SiO 2( s) (5)
见图 1,可以看出控制焙烧温度在 1 200 K 以上, 可使 铁橄榄石分解,主要生成 Fe 3 O 4 ㊂
上述反应的吉布斯自由能 Δ r G m 与温度 T 的关系
图 3㊀ 实验流程 图 1㊀ 反应( 1) ( 3) 的吉布斯自由能变化
铁橄榄石 的 分 解㊂ 而 且, 在 高 温 条 件 下 还 发 生 反 应 线见图 2㊂
如图 8 所示㊂ 焙烧前, 试样中主要结晶矿物相为铁橄 榄石,其次为磁铁矿,而焙砂中的主要结晶矿物相为磁 铁矿,其次为赤铁矿, 说明焙烧过程中, 硅酸铁转化成 了铁的氧化物㊂
106
矿㊀ 冶㊀ 工㊀ 程
第 35 卷
㊀ ㊀ 3) 铜 渣 焙 烧 过 程 中, 硅 酸 铁 转 化 成 了 铁 的 氧 化物㊂ 参考文献:
通过高温焙烧的方法使铁橄榄石分解,反应式为: 3(2FeO㊃SiO 2 ) ( s) +O 2( g)������������ ㊀ ㊀ 2Fe 3 O 4( s) + 3SiO 2( s) (1) (2)
水式多用真空抽滤机㊁101 - 3EBS 型电热鼓风干燥箱㊁
与此同时,Fe 3 O 4 被氧化生成 Fe 2 O 3 : 4Fe 3 O 4( s) +O 2( g)������������ 6Fe 2 O 3( s)
关键环节,因此本文重点考察焙烧条件对铜渣中回收 2.1㊀ 焙烧温度的影响 焙烧 时 间 60 min, 煤 粉 用 量 1%, 碳 酸 钠 用 量
由于焙烧使铁橄榄石转化为磁铁矿, 是本工艺的
10%,焙烧温度的影响如图 4 所示㊂ 由图 4 可知, 随着 焙烧温度升高,铁精矿品位升高,而铁回收率降低㊂ 考 虑到高温需要更多的能耗, 认为适宜的焙烧温 度 为 800 ħ ,此温度条件下铁精矿品位和铁回收率分别为 61.99% 和 70.71%㊂
属铁 [7-9] ,再通过磁选方法加以回收㊂ 本文针对某铜
铜渣数量达 1 500 万吨㊂ 铜渣中含有相当数量的铁㊁ 铜㊁锌㊁ 铅㊁ 钴㊁ 镍等有价金属和少量金㊁ 银等贵金属㊂ 特别是铜渣中的铁, 其品位一般可达 40% 左右, 远高 于我国铁矿石的可采品位 27%
[3]
,
1㊀ 实㊀ ㊀ 验
1.1㊀ 实验原料
流程进行了浮铜尾矿的扩大实验, 可得到铁精矿品位 实验所用浮铜尾矿焙烧前后的 X 射线衍射结果
图 5㊀ 焙烧时间实验结果
2.3㊀ 煤粉用量的影响
10%,煤粉用量的影响如图 6 所示㊂ 由图 6 可知, 当煤 粉用量增加,铁精矿品位升高,但铁回收率降低㊂ 实验
焙烧温度 800 ħ , 焙烧时间 60 min, 碳酸钠用量
固定碳 76.29 灰分 13.59 挥发分 8.81 水分 1.31
图 2㊀ 反应( 4) 和( 5) 的吉布斯自由能变化
2FeO㊃SiO2 更稳定,可防止铁氧化物再生成硅酸铁㊂
由图 2 可见, 反应温度在 800 K 以上,Na 2 SiO 3 比
1.2㊀ 实验原理
1.3㊀ 实验设备及试剂 实验设备:SXZ - 10 型实验室电炉㊁XCSQ - 57 ˑ 70 型湿式强磁选机㊁JJ - 1 型电动搅拌器㊁SHZ - D 型循环 300 mL 石墨坩埚等㊂ 1.4㊀ 实验方法 试剂:硫酸㊁碳酸钠,均为分析纯㊂ 将铜渣浮铜尾矿与碳酸钠㊁ 煤粉等按一定比例混
[2]
ZHAN Bao⁃feng, HUANG Zi⁃li, YANG Nie, LIU Yu⁃fei, JIAO Cheng⁃peng
time of 60 minutes, dosage of coal dust and sodium carbonate of 1% and 10%, respectively. The calcine obtained was
Recovery of Iron from Copper⁃slag with Process of Roasting⁃Leaching⁃Magnetic Separation
( Hubei Key Laboratory for Efficient Utilization and Agglomeration of Metallurgic Resources, Wuhan University of Science and Technology, Hubei 430081, Wuhan, China) Abstract: With coal dust as reductant, recovery of iron from some copper⁃slag with the process of roasting⁃leaching⁃ magnetic separation was tested, with the effects of roasting time and temperature, dosage of coal dust and sodium carbonate on the iron recovery investigated. The optimum condition was obtained as follows: roasting temperature of 800 ħ , roasting 62.53% Fe at 70.82% recovery. further subjected to the process of dilute acid leaching and magnetic separation, resulting in an iron concentrate grading Key words: copper⁃slag; iron; roasting; leaching; magnetic separation ㊀ ㊀ 我国是世界上主要的铜生产国, 近年来冶炼精铜 产量增长迅速,2013 年我国精炼铜 684 万吨 [1] , 按照 目前火法炼铜每生产 1 吨金属铜产渣 2.2 吨计算
由于反应(4) 的发生,加入一定量 Na 2 CO 3 可促进
硫酸浓度 18.7%,液固比 4 ʒ1,浸出时间 60 min㊂