第二章铸造
第二章-铸造工艺方案的确定
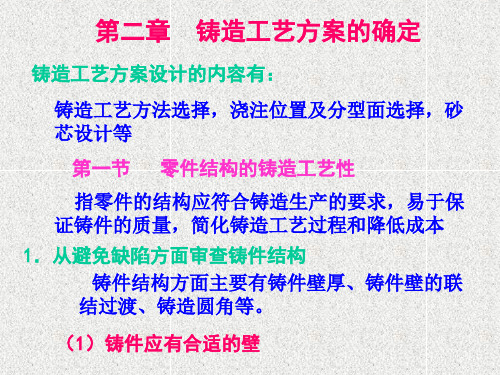
课堂讨论 图3-2-26
1.应使铸件全部或大部分置于同一半型内
图2-15 轮毂分型方案
2.应尽可能减少分型面数目 铸件的分型面少,铸件精度容易保ቤተ መጻሕፍቲ ባይዱ,且砂箱数目 少
图2-16 确定分型面数目的实例
3.平直分型面和曲折分型面的选择 尽可能选择平直分型面以简化工装结构及
其制造、加工工序和造型操作
图2-17 摇臂铸件的分型面
最小壁厚/㎜
高温合金
铝合金
0.6~1.0
1.5~2.0
0.8~1.5
2.0~2.5
1.0~2.0
2.5~3.0
—
3.0~3.5
—
3.5~4.0
铸件尺寸㎜
50×50 100×100 225×225
金属型铸造时铸件的最小壁厚
铝硅合 金
最小壁厚/㎜
铝镁合金、镁合 铜合金 金
灰铸铁
2.2
3
2.5
3
2.5
3
3
(1)改进妨碍起模的凸台、凸缘和肋板结构
改进妨碍起模的铸件结构 a)不合理 b)合理
教材220面,学生看,老师提问
(2)尽量取消铸件外表侧凹
图2-6 外壁内凹的框形件 a)不合理 b)合理
(3)有利于砂芯的固定和排气 (4) 减少或简化分型面(P221)
轴承架铸件
P222
(5)便于铸件的清理 (P222,图3-2-15) (6)简化模具制造 (P222,图3-2-16)
原则:
铸件精度和生产批量 吃砂量要求 吃砂量的确定
吃砂量: 铸件表面所需要的的最小型砂厚度。
根据铸件大小、重量、厚度、种类以 及型砂的特性和砂箱的结构确定。
吃砂量过小 砂型紧实困难,易引起胀砂、包砂、掉砂、
第二章 铸造锻压和焊接工艺基础2总结
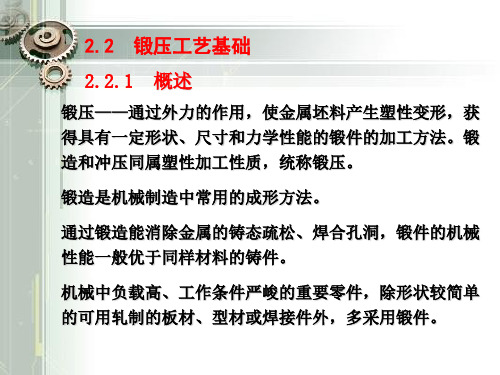
粒粗大的铸态柱状晶组织好;
钢中有网状二次渗碳体时,钢的塑性将大大下降。
(3)变形温度的影响 大多数金属温度升高后塑性增加,变形抗力降低, 可锻性好。 温度升高后原子热能增大,原子结合力减弱,易变 形。可用较小锻打力产生较大的变形而不破裂。 当铁碳合金在723ºC以上时的单相奥氏体状态下具
常用的锻压机械有锻锤、液
压机和机械压力机。
锻锤具有较大的冲击速度, 利于金属塑性流动,但会产 生震动; 液压机用静力锻造,有利于
锻透金属和改善组织,工作 平稳,但生产率低;
机械压力机行程固定,易于 实现机械化和自动化。
机械压力机
锻造按坯料在加工时的温度可分为: 冷锻一般是在室温下加工。 热锻是在高于坯料金属的再结晶温度(800℃)上加工。 温锻是将处于加热状态,但温度不超过再结晶温度 (300~800℃之间)时进行的锻造加工。 钢再结晶温度约为727℃,但普遍采用800℃为划分线。 热锻用于大多数行业的锻件。 温锻和冷锻主要用于汽车、通用机械等零件的锻造。
来越差。
合金元素会形成合金碳化物,使钢的塑性变形抗力增大, 塑性下降,通常合金元素含量越高,钢的塑性成形性能
也越差。
杂质元素磷会使钢出现冷脆性,硫使钢出现热脆性,降 低钢的塑性成形性能。
(2)金属组织的影响 纯金属及单相固溶体的合金具有良好的塑性,其 锻造性能较好; 钢中有碳化物和多相组织时,锻造性能变差; 具有均匀细小等轴晶粒的金属,其锻造性能比晶
(2)金属组织
(3)变形温度 (4)变形速度 (5)应力状态
(1)化学成分的影响
纯金属的可锻性比合金好。
钢含碳量大,强度和硬度高,塑性降低,可锻性变差。 钢的含碳量对钢的可锻性影响很大,对于碳含量分数小 于0.15%的低碳钢,其塑性较好。 随着碳含量的增加,使钢的塑性下降,塑性成形性也越
铸造专题知识讲座

三、铸型充填条件
(1)铸型旳蓄热系数 铸型旳蓄热系数表达铸型从其中旳 金属吸收热量并储存在本身旳能力。
(2)铸型温度 铸型温度越高,液态金属与铸型旳温差 越小,充型能力越强。
(3)铸型中旳气体
四、铸件构造
(1)折算厚度 折算厚度也叫当量厚度或模数,为铸件体积 与表面积之比。
折算厚度大,热量散失慢,充型能力就好。铸件壁厚相同 步,垂直壁比水平壁更轻易充填。 (2)铸件复杂程度 铸件构造复杂,流动阻力大,铸型旳
充型能力不足时,会产生浇不足、冷隔、夹渣、气孔等缺陷。
一、液态合金旳流动性
合金旳流动性是: 液态合金本身旳流动能力。
浇口杯
出气口
0.45%C 铸钢:200 4.3%C 铸铁:1800
浇口杯
出气口
流动性(cm)
温度(℃)
30 0 20 0 10 00
80
60
40
20
0
Pb
20
40
60
80 Sb
合金流动性主要取决于合金化学成份所决定旳结晶特点
第二章 铸造
一、铸造
将液态金属浇注到与零件形状相适应旳铸型型腔中,
待其冷却凝固,以取得毛坯或零件旳生产措施。
二、砂型铸造旳工艺过程
铸件
检验 落砂、清理
合箱
铸造工艺图 零件图
型砂
铸
模型
型
熔化 浇注
芯盒
型
芯砂
芯
冷却 凝固
三、铸造生产旳特点
1.可生产形状任意复杂旳制件,尤其是内腔形状复杂旳 制件。如汽缸体、汽缸盖、蜗轮叶片、床身件等。
孕育铸铁合用于静载荷下,要求较高强度、硬度、耐磨
性或气密性旳铸件,尤其是厚大截面铸件。如重型机床
第2章(1)砂型铸造的造型工艺

零图
铸件
模样
(a)造下型、拔出钉子 (b)取出模样主体 (c) 取出活块
活块造型 1-用钉子连接活块 2-用燕尾连接活块
(4)挖砂造型
当铸件按结构特点需要采用分模造型,但 由于条件限制(如模样太薄,制模困难)仍做成 整模时,为便于起模,下型分型面需挖成曲面 或有高低变化的阶梯形状(称不平分型面),这 种方法叫挖砂造型。
(a)造下砂型 (b)刮平、翻箱 (c)造上型、扎气孔
(d)起箱起模开浇口 (e)合型
(f) 带浇口的铸件
(2)分模造型
分模造型的特点是:模样是分开的,模样 的分开面(称为分型面)必须是模样的最大 截面,以利于起模。分模造型过程与整模造 型基本相似,不同的是造上型时增加放上模 样和取上半模样两个操作。
(4)抛砂造型 是利用高速旋转 的叶片将输送带 输送过来的型砂 高速抛下来紧实 砂型。抛砂造型 适应性强,不需 要专用砂箱和模 板,适用于大型 铸件的单件小批 生产。
三、制芯 为获得铸件的内腔或局部外形,用芯砂或 其他材料制成的、安放在型腔内部的铸型组元 称型芯。绝大部分型芯是用芯砂制成的。砂芯 的质量主要依靠配制合格的芯砂及采用正确的 造芯工艺来保证。 浇注时砂芯受高温液体金属的冲击和包围, 因此除要求砂芯具有铸件内腔相应的形状外, 还应具有较好的透气性、耐火性、退让性、强 度等性能,故要选用杂质少的石英砂和用植物 油、水玻璃等粘结剂来配制芯砂,并在砂芯内 放入金属芯骨和扎出通气孔以提高强度和透气 性。
④可塑性 指型砂在外力作用下变形,去除外力
后能完整地保持已有形状的能力。可塑性好,造型操作 方便,制成的砂型形状准确、轮廓清晰。
⑤退让性 指铸件在冷凝时,型砂可被压缩的能
力。退让性不好,铸件易产生内应力或开裂。型砂越紧 实,退让性越差。在型砂中加入木屑等物可以提高退让 性
第二章铸造成形讲解

•薄壁处受压力,厚壁处受拉力
•变形
防止变形的措施
• 设计铸件时尽可能壁厚均匀,形状对称。 • 采取同时凝固。 • 设计“反变形”量。
•时效处理:有内应力的铸件在加工前置于 露天半年以上,或550~650ºC去应力退火。
3、铸件的裂纹与防止
• 热裂 热裂是铸件在高温下产生的裂纹。 其形状特征是:裂纹短,缝隙宽,形状 曲折,缝内呈氧化色。
• 2、铸造合金的收缩 • 3、缩孔与缩松
铸件的凝固方式之一
• 逐层凝固
– 纯金属和共晶 成份的合金, 结晶温度是一 固定值。凝固 过程由表面向 中心逐步进行
温度
固 表层
液 中心
铸件的凝固方式之二
• 糊状凝固
– 结晶温度范围 很宽的合金, 从铸件的表面 至心部都是固 液两相混存。
铸件的凝固方式之三
铸造 碳钢 0.35 1610
白口 铸铁 3.00 1400
灰口 铸铁 3.50 1400
液态 收缩 1.6
2.4
3.5
凝固 固态 总收缩 收缩 收缩 (%)
3
7.8 12.46
12~ 4.2 5.4~6.3
12.9 6.9~ 0.1 3.3~4.2 7.8
铸件中的缩孔与缩松
• 缩孔和缩松的形成 液态合金在冷凝过 程中,若其液态收缩和凝固收缩所缩减 的容积的得不到补足,则在铸件最后凝 固的部位形成一些孔洞
1、合金的流动性 2、浇注条件 3、铸型填充能力
充型能力不强,则易产生浇不足(short run) 、 冷隔(short run)…等。
合金的充型能力之一
合金的流动性
• 合金的流动性是指熔融合金的流动能力。– 流动性好,充型能力强,便于浇出轮廓清 晰、薄而复杂的铸件。
第2章 砂型铸造讲解
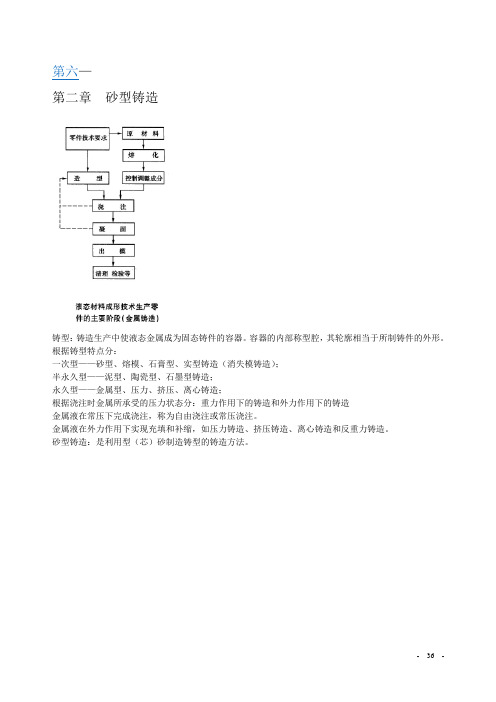
第六—第二章砂型铸造铸型:铸造生产中使液态金属成为固态铸件的容器。
容器的内部称型腔,其轮廓相当于所制铸件的外形。
根据铸型特点分:一次型——砂型、熔模、石膏型、实型铸造(消失模铸造);半永久型——泥型、陶瓷型、石墨型铸造;永久型——金属型、压力、挤压、离心铸造;根据浇注时金属所承受的压力状态分:重力作用下的铸造和外力作用下的铸造金属液在常压下完成浇注,称为自由浇注或常压浇注。
金属液在外力作用下实现充填和补缩,如压力铸造、挤压铸造、离心铸造和反重力铸造。
砂型铸造:是利用型(芯)砂制造铸型的铸造方法。
整模造型分模造型一、概述1 缺点、优点:砂型铸造是铸造生产中最广泛的一种方法,世界各国用砂型铸造生产的铸件占总产量的80-90%。
型砂:将原砂或再生砂+粘结剂+其它附加物所混制成的混合物。
砂型(芯):型(芯)砂在外力作用下成形并达到一定的紧实度或密度成为砂型(芯)。
2 砂型的种类湿型:由原砂、粘土、附加物及水按一定比例混碾而成湿型砂;用湿型砂春实,浇注前不烘干的砂型。
干型:经过烘干表面干型:表面仅有一层很薄(15-20mm)的型砂被干燥,其余部分仍然是湿的。
化学自硬砂型:砂型靠型砂自身的化学反应而硬化。
造型:制造砂型的工艺过程。
造芯:制造砂芯的工艺过程。
选择合适的造型(芯)方法和正确的造型(芯)工艺操作,对提高铸件质量、降低成本、提高生产率有极重要的意义。
1 按型(芯)砂粘(固)结机理分类机械粘结造型(芯)、化学粘结造型(芯)、物理固结造型(芯)2 按造型(芯)的机械化程度分类(1)手工造型(芯)手工造型(芯)是最基本的方法,这种方法适应范围广,不需要复杂设备,而且造型质量一般能够满足工艺要求,所以到目前为止,在单件、小批量生产的铸造车间中,手工造型(芯)仍占很大比重,在航空、航天、航海领域应用广泛。
缺点:劳动强度大、生产率低、铸件质量不易稳定。
模样造型、刮板造型、地坑造型,各种造型方法有不同的特点和应用范围。
第二章 合金的铸造性能
第三节 铸件中常见的缺陷及防止
铸件中的缩孔与缩松 铸件应力 铸件的变形 铸件的裂纹 铸造偏析 铸件中的气孔
一、铸件中的缩孔与缩松
缩孔的形成 缩松的形成 影响缩孔、缩松形成的因素 缩孔和缩松的防止方法
缩孔的形成
定义:液态金属在铸型内凝固过程 中,由于液态收缩和凝固收缩,使 体积缩小,若其收缩得不到补充, 就在铸件最后凝固处形成大而集中 的孔洞称为缩孔。
形成的条件:铸件呈逐层凝固方式 凝固。 易形成缩孔的金属:纯金属或共晶 成分的合金。
缩松的形成
定义:液态金属在铸型内凝固过程中, 由于液态收缩和凝固收缩,使体积缩 小,若其收缩得不到补充,就在铸件 最后凝固处形成细小而分散的孔洞称 为缩松。 形成的条件:铸件呈糊状凝固方式凝 固。 易形成缩松的金属:非共晶成分或有 较宽结晶温度范围的合金。
2.浇注条件
浇注温度:浇注温度越高,流动性
越好。
充型压力:充型压力越大,流动性
越好。
3.铸型结构及填充条件
铸型的蓄热能力:铸型的蓄热能力强, 充型能力差。 铸型温度:铸型温度高,有利于液体 金属充型。 铸型中气体:铸型中气体愈多,充型 的阻力阻力愈大。 铸型结构:铸型结构缩
一 铸造合金的凝固
铸造合金的凝固方式 影响凝固方式的因素
影响铸件凝固方式的主要因素 :
(1)合金的结晶温度范围
(2)铸件的温度梯度
二、铸造合金的收缩
收缩阶段 影响收缩的因素
浇注温度 合金的浇注温度越高,也太收缩量 越大,其总收缩量增加。
机械制造基础铸造第二章
机械制造基础
第二章 铸造成型
§2-1.2
金属与合金的铸造性能
液态合金的充型能力
—— 液态 合金充满铸型型 腔,获得形状完 整、轮廓清晰铸 件的能力。 充型能力不足容易出现浇 不足、冷隔缺陷,尤其对 于薄壁铸件
机械制造基础
第二章 铸造成型
影响充型能力的因素:
1. 合金的流动性 ——液态合金本身的流动能力。
(1). 流动性的测试 螺旋形试样法
机械制造基础
第二章 铸造成型
(2). 影响流动性的因素:
合金的种类:
灰口铸铁、硅黄铜流动性最好, 铸钢的流动性最差。 灰口铸铁:l 1000 mm 硅黄铜: l 1000 mm 铸钢: l 200 mm
机械制造基础
第二章 铸造成型
(2)机器造型
指用机器完成全部或至少完成紧砂 操作的造型工序。 1)特点: ①提高了生产率,铸件尺寸精度较高; ②节约金属,降低成本; ③改善了劳动条件; ④设备投资较大。 2)应用:成批、大量生产各类铸件。
机械制造基础
第二章 铸造成型
3)机器造型方法 ①震压造型: 先震击紧实,再用较低的比压(0.15 -0.4MPa )压实。 紧实效果好,噪音大,生产率不够高。 ②微震压实造型: 对型砂压实的同时进行微震。 紧实度高、均匀,生产率高,噪音仍较大。
要预热后再浇注合金液。
(3). 铸型的排气能力,流动阻力,充型能 力,所以铸型要留出气口。
机械制造基础
第二章 铸造成型
2.1.2.2 铸件的收缩 ① 液态收缩阶段
② 凝固收缩阶段 ③ 固态收缩阶段
T ① ② ③
2铸造
2).铸件的变形和防止 铸件变形的一般规律:厚的部位呈内凹,簿的部 分呈外凸。为防止铸件变形,除合理设计零件结 构外,在工艺上可采用反变形法。
沿高度方向如 何变形
3).铸件的裂纹与防止 当铸件的内部应力超过金属抗拉强度时, 铸件便产生裂纹。
• 热裂纹是在固相线附近形成的裂纹。其 形状特征是,裂纹短、缝隙宽形状曲折, 缝内表面呈氧化颜色, • 防止热裂纹的方法:正确设计零件结构 外应合理地选用型砂和芯砂的粘结剂, 以改善其退让性。严格限制钢和铸铁中 硫的含量。
• 2、侵入气孔 • 是由于铸型表面层聚集的气体侵入液态 合金而形成的气孔。 • 侵入气孔的特征是多位于铸件局部表面 附近,尺寸较大,呈椭圆形或梨形。 • 防止方法:降低型砂、芯砂的发气量和 提高铸型的排气能力。
3、反应气孔 • 液态合金与铸型、冷铁、芯撑或熔渣之 间,因化学反应产生气体而形成的气孔, 称为反应气孔。 • 反应气孔多分布在铸件表层下1-2毫米处, 呈皮下气孔。
§1-2 铸件的凝固 铸型中的合金从液态转变为固态的过程, 称为铸件的凝固,或称一次结晶。 • 铸件的凝固 • 在铸件凝固过程中,一般存在着固相区、 凝固区和液相区三个区域,其中凝固区 是液相与固相共存的区域,凝固区的大 小对铸件质量影响较大,按照凝固区宽 窄,分为逐层凝固、中间凝固和体积凝 固三种凝固方式,如图2-4所示。
• 3.体积凝固 当合金的结晶温度范围很 宽,或因铸件截面温度梯度很小,铸件 凝固时,其液固共存凝固区很宽,甚至 贯穿整个铸件截面,如图2-4(c)所示。 • 影响铸件凝固方式主要因素是合金的 结晶温度范围(取决于合金化学成分) 和铸件的温度梯度。合金的结晶温度范 围越小,凝固区域越窄,越倾向于逐层 凝固。当合金成分一定时,凝固方式取 决于铸件截面上的温度梯度,温度梯度 越大,对应的凝固区域越窄,越趋向于 逐层凝固。
材料成形技术--第2章 铸造成形
2)设备投资大,生产准备周期长,只适于大量生产。
压力铸造主要用于生产铝、锌、镁等有色合金铸件, 如发动机缸体、缸盖、箱体、支架等。
4. 低压铸造
低压铸造:用较低压力将金属液由铸型底部注入型腔, 并在压力下凝固以获得铸件的方法。 (1).低压铸造的工艺过程 : 低压铸造的工艺过程如图2-26所示,包括如下过程:
续
刮板造型 用刮板代替模样造型。节约木材, 用于等截面或回转体大中 缩短生产周期,生产率低,技术水 型铸件的单件、小批生产 平高,精度较差 两箱造型 最基本的造型方法。各种 铸型由上型和下型构成,各类模样, 铸型,各种批量 操作方便
三箱造型
铸件两端截面尺寸比中间大,必须 主要用于手工造型,具有 有两个分型面 两个分型面的铸件的单件、 小批生产
5. 离心铸造
离心铸造:将金属液浇入高速旋转的铸型中,使其在离心 力作用下成形并凝固的铸造方法。可用金属型也可用砂型
(1).离心铸造的类型 根据铸型旋转轴的空间位置,离心铸造可分为立式 和卧式两大类。 1)立式离心铸造:铸型绕垂直轴旋转,如图2-27a,b所 示。在离心力和重力的共同作用下,内表面为回转抛物 面,因此用于高度小于直径的圆环类或成形铸件。
主要特点如下:
R 1) 铸件 的 精 度 和 表 面质量高 ;尺寸公差 IT11∼IT14, a 12.5∼ Ra 1.6;
2)可制造形状较复杂的铸件; 3)适用于各种合金铸件,尤其是高熔点和难以加工的高 合金钢,如耐热合金、不锈钢、磁钢等。 4)工艺过程较复杂,生产周期长,使加工费和消耗的材 料费较贵,多用于小型零件。 熔模铸造适用于制造形状复杂,难以加工的高熔点合 金及有特殊要求的精密铸件;主要用于汽轮机、燃汽轮机 叶片、切削刀具、仪表元件、汽车、拖拉机及机床等零件 的生产。
- 1、下载文档前请自行甄别文档内容的完整性,平台不提供额外的编辑、内容补充、找答案等附加服务。
- 2、"仅部分预览"的文档,不可在线预览部分如存在完整性等问题,可反馈申请退款(可完整预览的文档不适用该条件!)。
- 3、如文档侵犯您的权益,请联系客服反馈,我们会尽快为您处理(人工客服工作时间:9:00-18:30)。
第二章铸造
【导入新课】
铸造是指通过熔炼金属,制造铸型,并将熔融金属浇注到铸型型腔中,待其凝固后得到一定形状、尺寸和性能的铸件的成形方法。
铸造方法有砂型铸造和特种铸造两大类。
砂型铸造是一种将液体金属浇入到砂质铸型中,待其冷却、凝固后,将砂型破坏取出铸件的铸造方法。
砂型铸造的工艺过程一般由造型(制造砂型)、造芯(制造砂芯)、烘干(用于干砂型铸造)、合型(合箱)、浇注、落砂、清理及铸件检验等组成。
由于砂型铸造简单易行,原材料来源广,铸造成本低,见效快,因而在目前的铸造生产中占主导地位,用砂型铸造生产的铸件约占铸件总产量的90%。
【讲授新课】
2.1 砂型铸造
一、造型材料
1. 造型材料的组成
(1) 原砂
常指硅砂(石英砂),其主要成分为二氧化硅(SiO
2
)。
(2) 黏结剂
主要作用是使型砂、芯砂具有一定的强度和可塑性。
其主要成分是氧化铝(Al
2O
3)。
(3) 附加物
指除黏结剂外,为改善型砂或芯砂性能而加入的物质,使其具有某种特性。
2. 造型材料的性能要求
(1) 可塑性
(2) 强度
(3) 耐火性
(4) 透气性
(5) 退让性
二、砂型
用型砂制作,包括形成铸件形状的空腔、型芯和浇冒口系统的组合整体称为铸型。
三、浇注系统、冒口及溢放口
1. 浇注系统
浇注系统的作用是保证熔融金属平稳、均匀、连续地充满型腔,阻止杂质进入型腔;控制铸件的凝固程序,供给铸件收缩时需要补充的金属熔液。
浇注系统又称浇口,由浇口杯、直浇道、横浇道、内浇道组成。
2. 冒口
冒口作用:补充收缩之外,还有排气、除渣、排泄低温金属、检视浇注情况及观
察是否已铸满等功能。
3. 溢放口
其功能是排泄气体,以免因排气不良而阻碍金属液往前流动,另外也可以排泄劣
质的低温金属液及熔渣。
四、造型
用造型混合料和模样等工艺设备制造砂型的过程称为造型。
造型通常分为手工造型、机器造型两大类。
手工造型的基本程序:
1. 制作下砂型
2. 制作上砂型
3. 起出模样及开设浇注系统
4. 合模与浇铸
【课堂小结】
本次课主要学习了铸造的相关知识,了解了造型材料的组成及对造型材料的性能要求,熟悉了砂型的制作过程,认识砂型铸造系统的组成及作用,以长方形铸件为例,学习了整个造型的过程。
造型材料
砂型铸造砂型
浇注系统、冒口及溢放口
造型过程
【课后作业】
课后演练:1—3
2.2 特种铸造
【导入新课】
砂型铸造是最基本的铸造方法,不论铸件尺寸的大小、形状的繁简以及金属材料的种类,均可适用。
但其最大的缺点是砂型只能用一次,不适合大量生产;且受到砂型本身的限制,铸件精度太差,表面粗糙。
为了弥补砂型铸造的各项缺点,因此,各种特种铸造法也应运而生。
特种铸造是一种全新的铸造方法,它具有一些砂型铸造不可比拟的优点,在有些铸造方面得到越来越广泛的应用。
常见的特种铸造方法有金属型铸造、压力铸造、离心铸造和熔模铸造。
【讲授新课】
2.2 特种铸造
一、金属型铸造
金属型铸造就是在重力作用下将熔融金属浇入金属型腔获得铸件的制造方法。
(1) 金属型铸造生产的铸件的机械性能比砂型铸件高
(2) 铸件的精度和表面光洁度比砂型铸件高,而且质量和尺寸稳定。
(3) 铸件的工艺收得率高,液体金属耗量减少,一般可节约15%~30%。
(4) 不用砂或者少用砂,一般可节约80%~100%的造型材料。
此外,金属型铸造的生产效率高,铸件产生缺陷少,工序简单,易实现机械化和自动化。
但金属型铸造也有一些不足之处,如:
(1) 金属型铸造成本高,不宜小批生产。
(2) 金属型不透气,无退让性,易造成铸件浇铸不足、开裂或形成铸铁件白口等缺陷。
(3) 铸件外型和内腔均不宜太复杂,壁厚不宜太薄。
(4) 金属型铸造时,铸型的工作温度,合金的浇注温度和浇注速度,铸件在铸型中停留的时间,以及所用的涂料等,对铸件质量均有很大的影响,因此需要严格控制。
二、压力铸造
压力铸造(又称压铸)是指在高压作用下使液态或半液态金属以较高的速度充填压铸型型腔,并在压力作用下凝固成形而获得铸件的一种铸造方法。
1. 热室压力铸造
热室压力铸造的金属熔解炉装置在压铸机内,其浇道及柱塞经常浸在高温的金属液中,故称为热室压力铸造。
2. 冷室压铸
冷室压铸的原理与热室法大同小异,但为了便于压铸熔点比较高的金属(如Al、Cu、Mg等),而将熔解炉与压铸机分开,以免压铸机经常处于高温环境而发生故障。
三、离心铸造法
离心铸造法是将熔融金属浇入水平轴、立轴或倾斜轴旋转的铸型,使金属液在离心力的作用下,充填铸型并结晶的铸造方法。
四、熔模铸造
熔模铸造又称失蜡铸造,就是用易熔材料制成模样,在模样表面多次反复地涂盖耐火涂料,制成型壳,熔掉易熔模样后经高温焙烧,即可浇注熔融金属从而获得铸件的铸造方法。
【课堂小结】
本次课主要学习了特种铸造的相关知识,了解了金属型铸造、压力铸造、离心铸造、熔模铸造的工作过程。
并将四种常见的特种铸造进行了比较,使大家对铸造有一个清晰认识。
金属型铸造
特种铸造压力铸造
离心铸造
熔模铸造
【课后作业】
课后演练:1—3
2.3 铸件的清理与检验
【导入新课】
铸造结束后,所取出的铸件不一定符合产品要求,可能存在一些铸造过程中产生的多余结构,这些结构都必须予以清除。
同样,铸件清理结束后,必须进行检验,检验其是否符合设计和使用要求。
【讲授新课】
2.3 铸件的清理与检验
一、铸件清理
铸件清理是指清除铸件表面粘砂、型砂、多余金属(包括浇口、冒口、飞翅)等操作过程。
1. 浇口、浇道和冒口的清除
2. 清砂
3. 飞翅(又称飞边)
二、铸件常见缺陷
1.气孔
造型材料水分过多或含有大量发气物质,透气性差,浇注速度过快。
2. 缩孔
铸件在凝固过程中收缩得不到足够熔融金属的补充。
3.砂眼
型砂强度低,紧实度不足;合箱前未将型腔中的散落砂除去;合箱时将砂型压崩,浇注速度太快等。
4.粘砂
型砂的耐火性太差或浇注温度过高。
5.裂纹
铸件壁厚相差过大,浇注系统开设不合理,铸件内部铸造应力过大,型砂与砂芯退让性差等。
6.冷隔与浇不到
金属液未能正常地充满型腔所致。
7.夹渣
浇注时未将炉渣挡住,使炉渣进入型腔所致。
三、铸件检验与修补
铸件质量主要包括外观质量、内在质量和使用质量。
外观质量包括铸件表面粗糙度、表面缺陷、尺寸偏差、形状偏差、重量偏差;内在质量主要指铸件的化学成分、物理性能、机械性能、金相组织以及存在于铸件内部的孔洞、裂纹等缺陷;
使用质量指铸件在不同条件下的工作耐久能力,包括耐磨、耐腐蚀、疲劳、吸震等性能,以及被切削性、可焊性等工艺性能。
对铸件的质量进行控制与检验。
首先要制定从原材料、辅助材料到每种具体产品控制和检验的工艺守则与技术条件。
对每道工序都要严格按工艺守则和技术条件进行控制和检验。
最后对成品铸件作质量检验。
铸件缺陷常用的修补设备有氩弧焊机、电阻焊机、冷焊机等。
【课堂小结】
本次课主要学习了铸件的清理与检验,铸件的清理内容有:清除铸件表面粘砂、型砂、多余金属(包括浇口、冒口、飞翅)等。
铸件常见缺陷有:气孔、缩孔、砂眼、粘砂、裂纹、冷隔与浇不到、夹渣,分析了缺陷的特点及产生的原因。
最后学习了铸件的检验与修补方法。
浇口
铸件的清理内容冒口
飞翅
气孔
缩孔
砂眼
铸件常见缺陷粘砂
裂纹
冷隔与浇不到
夹渣
外观检验:表面粗糙度、表面缺陷、尺寸形状偏差、重量偏差铸件的检验
内在检验:音频、超声、涡流、X射线和γ射线
质量与外观要求不高:氩弧焊机
铸件缺陷常用的修补
精密铸件:冷焊机
【课后作业】
课后演练:1—3。