第二章 铸造成形
材料成形技术基础(问答题答案整理)

材料成形技术基础(问答题答案整理)第二章铸造成形问答题:合金的流动性(充型能力)取决于哪些因素?提高液态金属充型能力一般采用哪些方法?答:因素及提高的方法:(1)金属的流动性:尽量采用共晶成分的合金或结晶温度范围较小的合金,提高金属液的品质;(2)铸型性质:较小铸型与金属液的温差;(3)浇注条件:合理确定浇注温度、浇注速度和充型压头,合理设置浇注系统;(4)铸件结构:改进不合理的浇注结构。
影响合金收缩的因素有哪些?答:金属自身的化学成分,结晶温度,金属相变,外界阻力(铸型表面的摩擦阻力、热阻力、机械阻力)分别说出铸造应力有哪几类?答:(1)热应力(由于壁厚不均、冷却速度不同、收缩量不同)(2)相变应力(固态相变、比容变化)(3)机械阻碍应力铸件成分偏析分为几类?产生的原因是什么?答:铸件成分偏析的分类:(1)微观偏析晶内偏析:产生于具有结晶温度范围能形成固溶体的合金内。
(因为不平衡结晶)晶界偏析:(原因:(两个晶粒相对生长,相互接近、相遇;(晶界位置与晶粒生长方向平行。
)(2)宏观偏析正偏析(因为铸型强烈地定向散热,在进行凝固的合金内形成一个温度梯度)逆偏析产生偏析的原因:结晶速度大于溶质扩散的速度铸件气孔有哪几种?答:侵入气孔、析出气孔、反应气孔如何区分铸件裂纹的性质(热裂纹和冷裂纹)?答:热裂纹:裂缝短,缝隙宽,形状曲折,缝内呈氧化颜色冷裂纹:裂纹细小,呈连续直线状,缝内有金属光泽或轻微氧化色。
七:什么是封闭式浇注系统?什么是开放式浇注系统?他们各组元横截面尺寸的关系如何?答:封闭式浇注系统:从浇口杯底孔到内浇道的截面逐渐减小,阻流截面在直浇道下口的浇注系统。
(ΣF内<ΣF 横<f直下端<f直上端)< bdsfid="120" p=""></f直下端<f直上端)<> 开放式浇注系统:从浇口杯底孔到内浇道的截面逐渐加大,阻流截面在直浇道上口的浇注系统。
kxx第2章铸造成形习题及参考答案

kxx第2章铸造成形习题及参考答案习题第2章铸造成形填空题:1、铸造⽅法从总体上可分为普通铸造和特种铸造两⼤类,普通铸造是指砂型铸造⽅法,不同于砂型铸造的其他铸造⽅法统称为特种铸造,常⽤的特种铸造⽅法有:()、()、()、()、()等。
2、凝固过程中所造成的体积缩减如得不到液态⾦属的补充,将产⽣()或()。
3、对砂型铸件进⾏结构设计时,必须考虑合⾦的()和铸造()对铸件结构提出的要求。
4、()是铸造合⾦本⾝的物理性质,是铸件许多缺陷()产⽣的基本原因。
5、浇注位置是指造型时()在铸型中所处的位置,它影响铸件的质量。
6、铸造应⼒按产⽣的原因不同,主要可分为()和()两种。
7、铸件上各部分壁厚相差较⼤,冷却到室温,厚壁部分的残余应⼒为()应⼒,⽽薄壁部分的残余应⼒为()应⼒。
8、任何⼀种液态⾦属注⼊铸型以后,从浇注温度冷却⾄室温都要经过三个联系的收缩阶段,即()、()和()。
9、在低压铸造、压⼒铸造和离⼼铸造时,因⼈为加⼤了充型压⼒,故()较强。
提⾼浇铸温度是改善合⾦()的重要措施。
10、铸件浇铸位置的选择必须正确,如重要加⼯⾯、⼤平⾯和薄壁部分在浇铸时应尽量(),⽽厚⼤部位应尽量(),以便安放冒⼝进⾏()。
单项选择题:1、下列合⾦流动性最好的是:()①普通灰铸铁;②球墨铸铁;③可锻铸铁;④蠕墨铸铁。
2、摩托车活塞应具有良好的耐热性、热膨胀系数⼩,导热性好、耐磨、耐蚀、重量轻等性能。
在下列材料中,⼀般选⽤:()①铸造黄铜;②合⾦结构钢;③铸造铝硅合⾦;④铸造碳钢。
3、在下列铸造合⾦中,⾃由收缩率最⼩的是:()①铸钢;②灰铸铁;③铸造铝合⾦;④⽩⼝铸铁4、图⽰圆锥齿轮铸件,齿⾯质量要求较⾼。
材料HT350,⼩批⽣产。
最佳浇5①采⽤在热节处加明、暗冒⼝或冷铁以实现顺序凝固②尽量使铸件壁厚均匀以实现同时凝固③提⾼浇注温度④采⽤颗粒⼤⽽均匀的原砂以改善填充条件多项选择题:1、液态合⾦浇注温度冷却到室温所经历的收缩阶段有:()①⾼温收缩;②液态收缩;③凝固收缩④低温收缩;⑤固态收缩2、挖沙或假箱造型时候,分型⾯:()①⼀定是曲⾯;②⼀定是圆锥⾯;③可以是平;④⼀定是平⾯;⑤可以是曲⾯3、影响液态合⾦充型能⼒的主要因素是:()①合⾦的结晶特性;②浇注温度;③合⾦的收缩率;④铸造⼯艺凝固原则;⑤铸件壁厚和铸型条件4、影响液态合⾦充型能⼒的主要因素是:()①合⾦的结晶特性;②浇注温度;③合⾦的收缩率;④铸造⼯艺凝固原则;⑤铸件壁厚和铸型条件5、产⽣缩孔、缩松的基本原因:()①液态收缩;②固态收缩;③凝固收缩;④线收缩;⑤等温收缩结构改错题:1、如下图所⽰,浇铸位置是否合理?若不合理请改为合理。
第二章 液态成形工艺——铸造
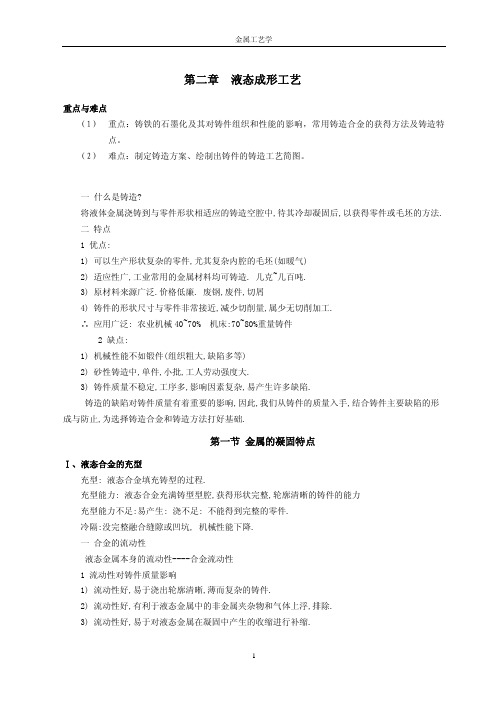
金属工艺学第二章 液态成形工艺重点与难点(1)重点:铸铁的石墨化及其对铸件组织和性能的影响,常用铸造合金的获得方法及铸造特点。
(2)难点:制定铸造方案、绘制出铸件的铸造工艺简图。
一 什么是铸造?将液体金属浇铸到与零件形状相适应的铸造空腔中,待其冷却凝固后,以获得零件或毛坯的方法.二 特点1 优点:1) 可以生产形状复杂的零件,尤其复杂内腔的毛坯(如暖气)2) 适应性广,工业常用的金属材料均可铸造. 几克~几百吨.3) 原材料来源广泛.价格低廉. 废钢,废件,切屑4) 铸件的形状尺寸与零件非常接近,减少切削量,属少无切削加工.∴ 应用广泛: 农业机械40~70% 机床:70~80%重量铸件2 缺点:1) 机械性能不如锻件(组织粗大,缺陷多等)2) 砂性铸造中,单件,小批,工人劳动强度大.3) 铸件质量不稳定,工序多,影响因素复杂,易产生许多缺陷.铸造的缺陷对铸件质量有着重要的影响,因此,我们从铸件的质量入手,结合铸件主要缺陷的形成与防止,为选择铸造合金和铸造方法打好基础.第一节 金属的凝固特点Ⅰ、液态合金的充型充型: 液态合金填充铸型的过程.充型能力: 液态合金充满铸型型腔,获得形状完整,轮廓清晰的铸件的能力充型能力不足:易产生: 浇不足: 不能得到完整的零件.冷隔:没完整融合缝隙或凹坑, 机械性能下降.一 合金的流动性液态金属本身的流动性----合金流动性1 流动性对铸件质量影响1) 流动性好,易于浇出轮廓清晰,薄而复杂的铸件.2) 流动性好,有利于液态金属中的非金属夹杂物和气体上浮,排除.3) 流动性好,易于对液态金属在凝固中产生的收缩进行补缩.12 测定流动性的方法:以螺旋形试件的长度来测定: 如 灰口铁:浇铸温度1300℃ 试件长1800mm.铸钢: 1600℃ 100mm3 影响流动性的因素主要是化学成分:1) 纯金属流动性好:一定温度下结晶,凝固层表面平滑,对液流阻力小2) 共晶成分流动性好:恒温凝固,固体层表面光滑,且熔点低,过热度大.3) 非共晶成分流动性差: 结晶在一定温度范围内进行,初生数枝状晶阻碍液流二 浇注条件1 浇注温度: t↑ 合金粘度下降,过热度高. 合金在铸件中保持流动的时间长,∴ t↑ 提高充型能力. 但过高,易产生缩孔,粘砂,气孔等,故不宜过高2 充型压力: 液态合金在流动方向上所受的压力↑ 充型能力↑如 砂形铸造---直浇道,静压力. 压力铸造,离心铸造等充型压力高.三 铸型条件1 铸型结构: 若不合理,如壁厚小, 直浇口低, 浇口小等 充↓2 铸型导热能力: 导热↑ 金属降温快,充↓ 如金属型3 铸型温度: t↑ 充↑ 如金属型预热4 铸型中气体: 排气能力↑ 充↑ 减少气体来源,提高透气性, 少量气体在铸型与金属液之间形成一层气膜,减少流动阻力,有利于充型.Ⅱ、铸件的凝固和收缩一 铸件的凝固1 凝固方式:铸件凝固过程中,其断面上一般分为三个区: 1—固相区 2—凝固区 3—液相区 对凝固区影响较大的是凝固区的宽窄,依此划分凝固方式.1) 逐层凝固:纯金属,共晶成分合金在凝固过程中没有凝固区,断面液,固两相由一条界限清楚分开,随温度下降,固相层不断增加,液相层不断减少,直达中心.2) 糊状凝固合金结晶温度范围很宽,在凝固某段时间内,铸件表面不存在固体层,凝固区贯穿整个断面,先糊状,后固化.故---3) 中间凝固大多数合金的凝固介于逐层凝固和糊状凝固之间.2 影响铸件凝固方式的因素1) 合金的结晶温度范围范围小: 凝固区窄,愈倾向于逐层凝固如: 砂型铸造, 低碳钢 逐层凝固, 高碳钢 糊状凝固金属工艺学2) 铸件的温度梯度合金结晶温度范围一定时,凝固区宽度取决于铸件内外层的温度梯度.温度梯度愈小,凝固区愈宽.(内外温差大,冷却快,凝固区窄)二 合金的收缩液态合金从浇注温度至凝固冷却到室温的过程中,体积和尺寸减少的现象---.是铸件许多缺陷(缩孔,缩松,裂纹,变形,残余应力)产生的基本原因.1 收缩的几个阶段1) 液态收缩: 从金属液浇入铸型到开始凝固之前. 液态收缩减少的体积与浇注温度质开始凝固的温度的温差成正比.2) 凝固收缩: 从凝固开始到凝固完毕. 同一类合金,凝固温度范围大者,凝固体积收缩率大.如: 35钢,体积收缩率3.0%, 45钢 4.3%3) 固态收缩: 凝固以后到常温. 固态收缩影响铸件尺寸,故用线收缩表示.2 影响收缩的因素1) 化学成分: 铸铁中促进石墨形成的元素增加,收缩减少. 如: 灰口铁 C, Si↑,收↓,S↑ 收↑.因石墨比容大,体积膨胀,抵销部分凝固收缩.2) 浇注温度: 温度↑ 液态收缩↑3) 铸件结构与铸型条件铸件在铸型中收缩会受铸型和型芯的阻碍.实际收缩小于自由收缩.∴ 铸型要有好的退让性.3 缩孔形成在铸件最后凝固的地方出现一些空洞,集中—缩孔. 纯金属,共晶成分易产生缩孔*产生缩孔的基本原因: 铸件在凝固冷却期间,金属的液态及凝固受缩之和远远大于固态收缩.4 影响缩孔容积的因素(补充)1) 液态收缩,凝固收缩 ↑ 缩孔容积↑2) 凝固期间,固态收缩↑,缩孔容积↓3) 浇注速度↓ 缩孔容积↓4) 浇注速度↑ 液态收缩↑ 易产生缩孔5 缩松的形成由于铸件最后凝固区域的收缩未能得到补足,或者,因合金呈糊状凝固,被树枝状晶体分隔开的小液体区难以得到补缩所至.1) 宏观缩松肉眼可见,往往出现在缩孔附近,或铸件截面的中心.非共晶成分,结晶范围愈宽,愈易形成缩松.2) 微观缩松凝固过程中,晶粒之间形成微小孔洞---凝固区,先形成的枝晶把金属液分割成许多微小孤立部分,冷凝时收缩,形成晶间微小孔洞. 凝固区愈宽,愈易形成微观缩松,对铸件危害不大,故不列为缺陷,但对气密性,机械性能等要求较高的铸3件,则必须设法减少.(先凝固的收缩比后凝固的小,因后凝固的有液,凝,固三个收缩,先凝固的有凝,固二个收缩区----这也是形成微观缩松的基本原因.与缩孔形成基本原因类似)6 缩孔,缩松的防止办法基本原则: 制定合理工艺—补缩, 缩松转化成缩孔.顺序凝固: 冒口—补缩同时凝固: 冷铁—厚处. 减小热应力,但心部缩松,故用于收缩小的合金. 安置冒口,实行顺序凝固,可有效的防止缩孔,但冒口浪费金属,浪费工时,是铸件成本增加.而且,铸件内应力加大,易于产生变形和裂纹.∴主要用于凝固收缩大,结晶间隔小的合金. 非共晶成分合金,先结晶树枝晶,阻碍金属流动,冒口作用甚小. 对于结晶温度范围甚宽的合金,由于倾向于糊状凝固,结晶开始之后,发达的树枝状骨状布满整个截面,使冒口补缩道路受阻,因而难避免显微缩松的产生.显然,选用近共晶成分和结晶范围较窄的合金生产铸件是适宜的.铸造内应力,变形和裂纹凝固之后的继续冷却过程中,其固态收缩若受到阻碍,铸件内部就发生内应力,内应力是铸件产生变形和裂纹的基本原因.(有时相变膨胀受阻,负收缩)一 内应力形成1 热应力: 铸件厚度不均,冷速不同,收缩不一致产生.塑性状态: 金属在高于再结晶温度以上的固态冷却阶段,受力变形,产生加工硬化,同时发生的再结晶降硬化抵消,内应力自行消失.(简单说,处于屈服状态,受力—变形无应力)弹性状态: 低于再结晶温度,外力作用下,金属发生弹性变形,变形后应力继续存在.举例: a) 凝固开始,粗 细处都为塑性状态,无内应力∵两杆冷速不同,细杆快,收缩大,∵受粗杆限制,不能自由收缩,相对被拉长,粗杆相对被压缩,结果两杆等量收缩.b) 细杆冷速大,先进如弹性阶段,而粗杆仍为塑性阶段,随细杆收缩发生塑性收缩,无应力.c) 细杆收缩先停止,粗杆继续收缩,压迫细杆,而细杆又阻止粗杆的收缩,至室温, 粗杆受拉应力(+),(-)由此可见,各部分的温差越大,热应力也越大,冷却较慢的部分形成拉应力,冷却较快的部分形成压应力.预防方法: 1 壁厚均匀 2 同时凝固—薄处设浇口,厚处放冷铁优点: 省冒口,省工,省料缺点: 心部易出现缩孔或缩松,应用于灰铁锡青铜,因灰铁缩孔、缩松倾向小,锡青铜糊状凝固,用顺序凝固也难以有效地消除其显微缩松。
第二章 铸造成型技术

固态收缩→铸造内应力→变形、开裂、体积减小
2、铸件中的缩孔与缩松
缩孔:液态收缩和凝固收缩过程中不能得到金属液补充引起。
特点:产生于铸件厚大部位或上部等最后凝固之处,凝固 温度范围窄的合金(近共晶成分)易发生该缺陷, 可通过特定措施防止。
合金的吸气性
一、 合金的充型能力
液态合金充满铸型型腔,获得尺寸正确、形状完整、 轮廓清晰的铸件的能力。 1、合金的流动性(内 因) 液态合金本身的流动能力,影响充型能力的主要因素之一; (1)概念:液体金属充满铸型的能力,指液体金属在、且 仅在重力作用下 表现出来的流动能力。 (2)对铸件质量的影响: 流动性不好,在铸件上易产生浇不足和冷隔、气孔、 和夹渣、缩孔和热裂等铸造缺陷。 (3)衡量(测定):螺旋形试样的长度
铸造
铸造:是将液态金属浇注到具有与零件形状及尺寸相适应
的铸型空腔中,待冷却凝固后,获得一定形状和性能的零件或 毛坯的方法。
铸造工艺特点及应用
• 可制成形状复杂、特别是具有复杂内腔的毛坯,如箱 体、床身、气缸体等。 • 适应范围广。工业上常用的金属材料都可铸造;铸件 大小几乎不限(铸件外形尺寸可从几毫米到十几米, 壁厚可从1mm到1m ) ;生产的批量不限,既适用于单 件小批生产,又适用于大批量生产。 • 成本低。可直接利用成本低廉的废机件和切屑,设备 费用较低;在金属切削机床中,铸件占机床总重量75% 以上,而生产成本仅占15~30%。
影响收缩的因素
a、化学成分
①常用铸造合金的收缩:灰铸铁<白口铸铁< 铸钢; ②灰铸铁:含C↑,Si ↑,S↓ 铸钢:含C↑ b、浇注温度↑ 收缩↑; 收缩↑; 收缩↓;
第二章铸造成形讲解

•薄壁处受压力,厚壁处受拉力
•变形
防止变形的措施
• 设计铸件时尽可能壁厚均匀,形状对称。 • 采取同时凝固。 • 设计“反变形”量。
•时效处理:有内应力的铸件在加工前置于 露天半年以上,或550~650ºC去应力退火。
3、铸件的裂纹与防止
• 热裂 热裂是铸件在高温下产生的裂纹。 其形状特征是:裂纹短,缝隙宽,形状 曲折,缝内呈氧化色。
• 2、铸造合金的收缩 • 3、缩孔与缩松
铸件的凝固方式之一
• 逐层凝固
– 纯金属和共晶 成份的合金, 结晶温度是一 固定值。凝固 过程由表面向 中心逐步进行
温度
固 表层
液 中心
铸件的凝固方式之二
• 糊状凝固
– 结晶温度范围 很宽的合金, 从铸件的表面 至心部都是固 液两相混存。
铸件的凝固方式之三
铸造 碳钢 0.35 1610
白口 铸铁 3.00 1400
灰口 铸铁 3.50 1400
液态 收缩 1.6
2.4
3.5
凝固 固态 总收缩 收缩 收缩 (%)
3
7.8 12.46
12~ 4.2 5.4~6.3
12.9 6.9~ 0.1 3.3~4.2 7.8
铸件中的缩孔与缩松
• 缩孔和缩松的形成 液态合金在冷凝过 程中,若其液态收缩和凝固收缩所缩减 的容积的得不到补足,则在铸件最后凝 固的部位形成一些孔洞
1、合金的流动性 2、浇注条件 3、铸型填充能力
充型能力不强,则易产生浇不足(short run) 、 冷隔(short run)…等。
合金的充型能力之一
合金的流动性
• 合金的流动性是指熔融合金的流动能力。– 流动性好,充型能力强,便于浇出轮廓清 晰、薄而复杂的铸件。
机械制造基础铸造第二章

机械制造基础
第二章 铸造成型
§2-1.2
金属与合金的铸造性能
液态合金的充型能力
—— 液态 合金充满铸型型 腔,获得形状完 整、轮廓清晰铸 件的能力。 充型能力不足容易出现浇 不足、冷隔缺陷,尤其对 于薄壁铸件
机械制造基础
第二章 铸造成型
影响充型能力的因素:
1. 合金的流动性 ——液态合金本身的流动能力。
(1). 流动性的测试 螺旋形试样法
机械制造基础
第二章 铸造成型
(2). 影响流动性的因素:
合金的种类:
灰口铸铁、硅黄铜流动性最好, 铸钢的流动性最差。 灰口铸铁:l 1000 mm 硅黄铜: l 1000 mm 铸钢: l 200 mm
机械制造基础
第二章 铸造成型
(2)机器造型
指用机器完成全部或至少完成紧砂 操作的造型工序。 1)特点: ①提高了生产率,铸件尺寸精度较高; ②节约金属,降低成本; ③改善了劳动条件; ④设备投资较大。 2)应用:成批、大量生产各类铸件。
机械制造基础
第二章 铸造成型
3)机器造型方法 ①震压造型: 先震击紧实,再用较低的比压(0.15 -0.4MPa )压实。 紧实效果好,噪音大,生产率不够高。 ②微震压实造型: 对型砂压实的同时进行微震。 紧实度高、均匀,生产率高,噪音仍较大。
要预热后再浇注合金液。
(3). 铸型的排气能力,流动阻力,充型能 力,所以铸型要留出气口。
机械制造基础
第二章 铸造成型
2.1.2.2 铸件的收缩 ① 液态收缩阶段
② 凝固收缩阶段 ③ 固态收缩阶段
T ① ② ③
(最新整理)成形第2章铸造

质量不变过程: 铸造、塑性成形、表面处理等
()
1
物 质
质量减少过程:切削加工、热切割、板料冲裁等
流
质量叠加过程:焊接、胶接和机械连接等
2021/7/26
5
2.能量流 各种能量的消耗和转化过程称为能量流
10~14.5 12~14
5~8
1.3~2.0 1.5~2.0 0.7~1.0
浇注温度:随着浇注温度的提高,金属冷却时的
液态收缩会增大,总体积收缩相应大。
铸型条件:铸件冷却过程中,由于各部分冷却速度
的不同,使收缩相互制约而不能自由收
缩,也可能受到铸型、型芯等的阻碍而
不能自由收缩。
阻碍越大,收缩越小
2021/7/26
借助高倍放大镜才能发现的缩松称为显微缩松。
铸件有缩松缺陷的部位,在气密性试验时易渗漏
特征:多产生在铸件的轴线附近和热节部位 (即厚度较大,冷速较慢的金属积聚处)
凝固温度范围越宽,糊状凝固越明显,铸件 越易产生缩松缺陷
2021/7/26
15
结果:
缩孔:铸件最后凝固上部的集中的体积收缩
缩松:铸件最后凝固区间的分散的体积收缩
3.信息流 形状信息流 性能信息流
产品的加工要求
将生产过程中的物质流、能量流和信息流系统 化,即“机械制造技术系统” ,具有“自动化、 柔 性化、高效化”的综合效果特征
4.材料成形技术的发展趋势
(1) 优化常规工艺
(2) 新型加工方法不断出现
(3) 高新技术与工艺紧密结合
2021/7/26
6
第2章 铸造
材料成形技术--第2章 铸造成形

2)设备投资大,生产准备周期长,只适于大量生产。
压力铸造主要用于生产铝、锌、镁等有色合金铸件, 如发动机缸体、缸盖、箱体、支架等。
4. 低压铸造
低压铸造:用较低压力将金属液由铸型底部注入型腔, 并在压力下凝固以获得铸件的方法。 (1).低压铸造的工艺过程 : 低压铸造的工艺过程如图2-26所示,包括如下过程:
续
刮板造型 用刮板代替模样造型。节约木材, 用于等截面或回转体大中 缩短生产周期,生产率低,技术水 型铸件的单件、小批生产 平高,精度较差 两箱造型 最基本的造型方法。各种 铸型由上型和下型构成,各类模样, 铸型,各种批量 操作方便
三箱造型
铸件两端截面尺寸比中间大,必须 主要用于手工造型,具有 有两个分型面 两个分型面的铸件的单件、 小批生产
5. 离心铸造
离心铸造:将金属液浇入高速旋转的铸型中,使其在离心 力作用下成形并凝固的铸造方法。可用金属型也可用砂型
(1).离心铸造的类型 根据铸型旋转轴的空间位置,离心铸造可分为立式 和卧式两大类。 1)立式离心铸造:铸型绕垂直轴旋转,如图2-27a,b所 示。在离心力和重力的共同作用下,内表面为回转抛物 面,因此用于高度小于直径的圆环类或成形铸件。
主要特点如下:
R 1) 铸件 的 精 度 和 表 面质量高 ;尺寸公差 IT11∼IT14, a 12.5∼ Ra 1.6;
2)可制造形状较复杂的铸件; 3)适用于各种合金铸件,尤其是高熔点和难以加工的高 合金钢,如耐热合金、不锈钢、磁钢等。 4)工艺过程较复杂,生产周期长,使加工费和消耗的材 料费较贵,多用于小型零件。 熔模铸造适用于制造形状复杂,难以加工的高熔点合 金及有特殊要求的精密铸件;主要用于汽轮机、燃汽轮机 叶片、切削刀具、仪表元件、汽车、拖拉机及机床等零件 的生产。
- 1、下载文档前请自行甄别文档内容的完整性,平台不提供额外的编辑、内容补充、找答案等附加服务。
- 2、"仅部分预览"的文档,不可在线预览部分如存在完整性等问题,可反馈申请退款(可完整预览的文档不适用该条件!)。
- 3、如文档侵犯您的权益,请联系客服反馈,我们会尽快为您处理(人工客服工作时间:9:00-18:30)。
适用于收缩大或壁厚差别大,易产生缩孔的合金铸 件,如铸钢、高强度灰铸铁、可锻铸铁等。动画演示
(2)合理确定内浇道位置及浇注工艺
内浇道的引入位置应按照顺序凝
固原则确定;浇注温度和浇注速度应
图2-12 热应力的形成
2.收缩应力
由机械阻碍产生,一般都是拉应力,在形成应力的 原因消除时,应力也随之消除。但如果临时拉应力和残 留热应力同时作用在某瞬间超过铸件的强度极限时,铸 件将产生裂纹。如图2-13所示。
3.减小和消除铸造应力的措施
1)合理设计铸件结构。尽量避免牵制收缩的结构,如壁厚 均匀,壁之间连接均匀等。
铸造性能是表示合金铸造成形获得优质铸件的能力; 用充型能力、收缩性等来衡量。
2.1.2.1 充型能力
充型能力:熔融金属或合金充满铸型型腔,获得形 状完整、轮廓清晰铸件的能力。主要影响因素有:
1. 金属或合金的流动性
流动性是熔融金属的流动能 力,合金的流动性用浇注流动性 试样的方法来衡量,一般采用如 图 2-3 所 示 的 螺 旋 形 试 样 。 流 动 距离越长,表明流动性越好。
图2-3 螺旋形标准试样
决定合金流动性的主要因素有:
1)合金的种类。
2)合金的成分。同种合金,成 分不同,其结晶特点不同,流 动性也不同。如图2-4所示铅锡 合金的流动性与相图的关系;
纯金属和共晶合金在恒温下结 晶,为逐层凝固方式,如图2-1a 所示,凝固层表面光滑,阻力
小,故流动性好,同时共晶合
和线收缩系数(1 0C )
合金的收缩过程可分为三个阶段:如图2-6所示。
1)液态收缩。指合金从浇注温度冷却到液相线温度过程中 的收缩。
2)凝固收缩。指合金在液相线和固相线之间凝固阶段的收 缩。结晶温度范围越大,收缩率越大。液态和凝固收缩时金 属液体积缩小,是形成缩孔和缩松的基本原因。
3)固态收缩。指合金 从固相线温度冷却到室 温时的收缩。用线收缩 率表示。它对铸件形状 和尺寸精度影响很大, 是铸造应力、变形和裂 纹等缺陷产生的基本原 因。
1.热应力
由热阻碍引起,落砂后热应力仍存在于铸件内,是一 种残留铸造应力,以框架铸件为例,说明残留热应力的形 成过程,如图2-12所示,其热应力形成过程分三阶段。
第一阶段,两者都塑性 变形,无热应力;
第二阶段,一塑性,一 弹性,仍无热应力;
第三阶段,两者均弹性 变形,冷却慢的受拉, 快的受压。残留热应力 和合金的弹性模量、线 收缩系数、铸件各部分 壁厚差别及温度差成正 比。 动画演示
1. 缩孔和缩松的形成 (1)缩孔的形成 形成条件,金属在恒温或很窄的温度 范围内结晶,铸件壁以逐层凝固方式凝固。形成过程如 图2-7所示:动画演示
缩孔产生的基本原因是合金的液态收缩和凝固收缩值 大于固态收缩值,且得不到补偿。缩孔产生的部位在铸件 最后凝固区域,此区域也称热节。
图2-7 缩孔形成过程示意图
2. 缩孔和缩松的防止 一定成分的合金,缩孔、缩松的数量可以相互转化,但
其总容积基本一定,如图2-9所示。
防止缩孔和缩松的 基本原则是:采用 合理的工艺条件, 使缩松转化为缩孔, 并使缩孔移至冒口 中。
图2-9铁碳合金成分与体积收缩率的关系
(1)按照顺序凝固原则进行凝固
是指采用各种工艺措施,使铸件上从远离冒口的部分
2)尽量选用线收缩率小、弹性模量小的合金。
3)采用同时凝固的工艺。如图2-14所示,各部分温差小, 不易产生热应力。主要用于收缩较小的普通灰铸铁、结晶 范围大,不易实现冒口补缩,对气密性要求不高的锡青铜 铸件等。
4)设法改善铸型、型芯的退让性,合理设置浇冒口。
5)对铸件进行时效处理。自然时效、热时效(去应力退 火)和共振时效。
a)
b)
c)
图2-6 铸造合金收缩过程示意图
a) 合金状态图 b) 一定温度范围合金 c) 共晶合金 I—液态收缩 II—凝固收缩 III—固态收缩
2. 影响收缩的因素
1)化学成分; 2)浇注温度越高,过热度越大,收缩越大; 3)铸件结构和铸型条件,铸件结构造成各部分冷却速度 不同,产生内部应力阻碍收缩;铸型和型芯产生机械阻 力。
4. 影响铸件凝固方式的因素
1)合金的结晶温度范围: 结晶温度范围越小,凝固区域 越窄,越倾向于逐层凝固。低碳钢,近共晶成分铸铁倾 向于逐层凝固,高碳钢、远共晶成分铸铁倾向于糊状凝 固。
2)铸件的温度梯度:在合金的结晶温度范围已定时,若铸 件的温度梯度由小变大,则凝固区由宽变窄,倾向于逐层凝 固。如图2-2所示。
4)劳动条件较差,劳动强度较大。
铸造在机械制造业中应用十分广泛,在各种类型的 机器设备中铸件占很大比重。如表2-1所示。
表2-1 各类机械工业中铸件重量比
机械类别
%
机床、内燃机、重型机器 风机、压缩机 拖拉机 农业机械 汽车
70~90 60 ~ 80 50 ~ 70 40 ~ 70 20 ~ 30
1)逐层凝固:纯 金属或共晶成分的 合金的凝固,如图 2-1a;
2)糊状凝固:结 晶温度范围很宽的 合金的凝固,如图 2-1c;
图2-1 铸件的凝固方式
a)逐层凝固 b)中间凝固 c)糊状凝固
3)中间凝固:介于逐层凝固和糊状凝固之间,大多数合 金为此凝固方式,如图2-1b所示。
ቤተ መጻሕፍቲ ባይዱ
铸件质量与凝固方式有关,逐层凝固时,合金充型能 力强(流动性好),便于防止缩孔、缩松。而糊状凝固时, 充型能力差,易产生缩松。
2.1.3.3 铸件的变形与裂纹
1.铸件的变形
残留铸造应力超过铸件材料的屈服极限时产生的翘曲 变形。如图2-15所示的框架铸件,图2-16的T形梁,当刚度 不够时,将产生如图所示的变形。再如图2-17所示的车床 床身的变形。
图2-15 框架铸件的变形
图2-16 T形梁的变形
防止铸造应力的方法也是防止变形的根本方法; 同时在工艺上还可以采用反变形法,提早落砂去应力 退火消除机械应力。
三者综合应用是消除缩孔缩松的有 效措施,如图2-11所示。
动画演示
图2-11 冒口冷铁的作用
2.1.3.2 铸造应力
铸造应力:铸件的固态收缩受到阻碍而引起的内应力。可 分为热应力和收缩应力; 热阻碍:铸件各部分由于冷却速度不同,收缩量不同而 引起的阻碍,由其引起的应力称热应力。 机械阻碍:铸型、型芯对铸件收缩的阻碍,由其引起的应 力称机械应力(收缩应力)。
2.1.3 铸造性能对铸件质量的影响
收缩是造成缩孔、缩松、应力、变形和裂纹的基本原 因;充型能力不好,铸件易产生浇不到、冷隔、气孔、夹 杂、缩孔、热裂等缺陷。
2.1.3.1 缩孔和缩松
凝固结束后在铸件某些部位出现的孔洞。大而集中的 孔洞称为缩孔,细小而分散的孔洞称缩松。缩孔缩松可使 铸件力学性能大大降低,以致成为废品。
防止热裂的措施:
➢ 应尽量选用凝固温度范围小、热裂倾向小的合金;
➢ 提高铸型、型芯的退让性,减小机械应力;
➢合理设计浇道、冒口; ➢对于铸钢、铸铁件,严格控制硫含量,防止热脆性。
2)冷裂 是铸件处于弹性状态即在低温时形成的裂纹。 其表面光滑,具有金属光泽或呈微氧化色,裂纹穿过晶 粒而发生,外形规则,常是圆滑曲线或直线。防止方法 是尽量减少铸造应力。
体收缩率 线收缩率
V
V0 V0
V1
100
%
V
t0
t1 100 %
l
l0 l1 l0
100 %
l t0
t1 100 %
式中 V0 、V1 ——合金在 t0 、t1 时的体积(m3); l0 、l1 ——合金在 t0 、t1 时的长度( m ); V 、 l ——合金在 t0 至t1 温度范围内的体收缩系数
2)液态金属的性质:具有粘度和表面张力。
2. 液态金属的凝固 液态金属由液态转变为固态的过程,包括形核和长
大两个过程。得到的凝固组织(铸态晶粒形态、大小、 分布、缺陷等)取决于成分、冷却速度、形核条件等。
3. 铸件的凝固方式
在铸件凝固过程中,铸件断面上存在三个区域,即固相 区、凝固区和液相区。其中凝固区对铸件质量有较大影响。 铸件的凝固方式也可根据凝固区的宽窄来划分,如图2-1。
金熔点最低,故流动性最好。
而亚共晶合金,为中间凝固方 式,复杂枝晶阻碍流动,故流
图2-4铅锡合金的流动性与相图的关系
动性差,如图2-1c所示。
3)杂质和含气量。固态夹杂物使粘度增加,流动性下降; 如灰铁中的MnS;含气量越少,流动性越好。
2. 浇注条件
1)浇注温度越高,保持液态的时间越长,流动性越好; 温度越高,合金粘度越低,阻力越小,充型能力越强。 故提高浇注温度能有效提高充型能力;但过高吸气量和 总收缩大,易产生铸造缺陷。故在保证充型能力的前提 下温度应尽量低。生产中薄壁件常采用较高温度,厚壁 件采用较低浇注温度。
2.铸件的裂纹:
当铸造应力超过金属的强度极限时,铸件便产生裂 纹。可分为热裂和冷裂。
1)热裂 在凝固末期高温下形成的裂纹。裂纹表面被氧 化而呈氧化色,裂纹沿晶粒边界产生和发展,外形曲折而 不规则;裂纹短,缝隙宽。
产生原因:凝固末期,合金绝大部分已成固体,但强度和 塑性很低,当铸件受到机械阻碍产生很小的铸造应力就能 引起热裂。分布在应力集中处或热节处。
第1节 液态成形理论基础
2.1.1 金属的凝固 2.1.2 金属与合金的铸造性能 2.1.3 铸造性能对铸件质量的影响
2.1.1 金属的凝固
1. 液态金属的结构与性质
1)液态金属的结构:固态金属经加热变为熔融状态即得 液态金属,是由呈有序排列的游动原子集团组成,其结 构与原有固体结构相似,但热运动剧烈,温度越高,热 运动越剧烈,原子集团越小,游动越快。