典型零件的编程.
典型零件的数控编程及加工仿真

• 典型零件的数控编程及加工仿真
班级: 161004 姓名: 王萌 指导教师: 李郁
全文结构
一、数控编程的概述 二、三维建模及工艺规划 三、典型零件仿真加工 四、后处理及代码输出 五、全文总结
一、数控编程的概述 生成数控机床进行零件加工的数控程序 的过程,称为数控编程,有时也称为零 件编程。数控编程可以手工完成,即手 工编程,也可以由计算机辅助完成,即 计算机辅助数控编程。
二、三维建模及工艺规划
该零件毛坯尺寸为130mmX130mmX45mm,主要结 构是由多个不同深度的平面组成的型腔,各平面上分 布有不同尺寸的孔,整体结构并不复杂。
三、典型零件仿真加工
三、典型零件仿真加工
四、后处理及代码输出
五、全文总结
三维建模及工艺规划
Hale Waihona Puke 典型零件仿真加工后处理及代码输出
第三讲典型轴类零件数控车削加工工艺及编程

B
准确定位
B
英制O米制OB:基本功能 0:选购功能 数控车设定—— A功能
2. 进给功能(F功能)
F 功能指令用于在程序中控制切削进给量,有两种指令模式: (1)每转进给模式(G99)
编程格式: G99 F ___; F后面的数字表示主轴每转一转刀具的进给量。 单位:mm/r。
说明:模态指令,一经指定直到被G98取代,一直有效。 系统默认状态,车床上一般常用此种进给量指令方式。
A’ 65,2
B’ 10.01,2
C‘ 18.01,-2
D’ 18.01,-20
E‘ 24,-25
F’ 28,-25 G‘ 48.016,-35 H’ 48.016,-51 I‘ 58.023,-51 J‘ 58.023,-58 K’ 62,-58
符号
含义
编程原点
零件外轮廓走刀路线
工序号 程序段号
工步号 加工内容
粗车左端外轮廓,X轴留0.4、 Z轴留0.1精加工余量
精加工左端面外轮廓,各加工 表面符图示要求
审核
产品名称或代号
零件名称
材料 零件图号
XXX
夹具名称
三爪卡盘
刀具号
刀具规格/ (mm)
主轴转速/ (r/min)
T01
25×25
粗600 精1000
螺纹轴
45钢
XXX
使用设备
车间
CK6132
数控车
进给速度/ 背吃刀量/ 备注 (mm/r) (mm)
恒转速控制 编程格式: S ~
S后面的数字表示主轴转速,单位: r/min。
注意:
在具有恒线速功能的机床上, S 功能指令可限制主轴最高转速
(1)主轴最高转速限制(G50)
《典型零件的数控编程与加工仿真》毕业论文样式

山东职业学院毕业设计(论文)题目:系别:专业:班级:学生姓名:指导教师:完成日期:山东职业学院毕业设计(论文)任务书山东职业学院毕业设计指导书设计题目典型零件的数控编程与加工仿真班级姓名指导教师宋嘎2011年11月一、设计题目:典型零件的数控编程与加工仿真二、背景与目的数控加工的广泛运用给机械制造业的生产方式、产品结构、产业结构都带来了深刻的变化,是制造业实现自动化、柔性化、集成化生产的基础。
如何良好地运用数控机床,发挥其高精度、高效率等特点,是制造行业从业人员面临的一个大问题;另一方面,高职院校数控技术专业正是要培养这种掌握数控工艺和加工技术的高端技能型人才。
因此,应该使学生熟练掌握数控加工工艺的制定,数据程序的编制和数控机床的操作等技能,使他们毕业后能够快速上岗,从而提高就业竞争能力。
在三年的学习中,机电一体化技术专业的毕业生系统地学习了本课题所涉及到的《机械设计基础》、《机械制造技术基础》、《机加工设备》、《数控编程与加工》等专业理论知识,为使学生更加全面地掌握所学理论知识,做到融会贯通,在将来的就业竞争、生存竞争中立于不败之地,特设这一课题。
本课题设计目的:1、熟练掌握典型零件的车削加工工艺2、熟练掌握典型零件的铣削加工工艺3、熟练掌握FANUC 0i系统的程序编制4、掌握计算机二维绘图和三维造型的应用5、熟练掌握宇龙数控仿真软件的应用三、设计过程及内容(一)计算机绘图利用Cimatron E软件完成零件的三维造型,并生成二维工程图。
(二)零件的数控加工工艺分析1.零件图样分析2.基准选择3.加工方法与加工方案的确定4.工序和工步的划分5.走刀路线的确定6.工艺装备的选择7.切削用量的确定注:工艺分析务必按以上步骤进行,不可省略。
(三)编制加工工艺文件工件安装和原点设定卡片数控加工走刀路线图数控加工工序卡片数控加工刀具卡片注:此部分应置于毕业论文的附录中(四)编写程序本项目要求采用手工编程(五)程序调试与加工应用宇龙仿真软件进行模拟加工,把仿真结果打印出来,置于毕业论文的附录中。
典型零件的数控编程及加工仿真
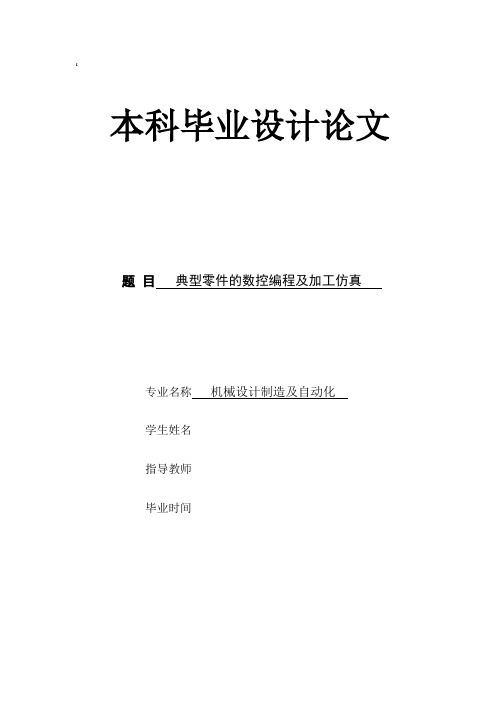
‘本科毕业设计论文题目典型零件的数控编程及加工仿真专业名称机械设计制造及自动化学生姓名指导教师毕业时间毕业设计论文任务书一、题目典型零件的数控编程及加工仿真二、指导思想和目的要求数控加工是一种现代化的加工手段,数控加工技术也成为一个国家制造业发展的标志,利用数控加工技术可以完成很多以前不能完成的曲面零件的加工,而且加工的准确性和精度都可以得到很好的保证。
本次毕业设计题目来源于生产实践,利用UG三维造型软件进行的数控编程与加工仿真。
通过对零件进行三维建模,并模拟数控仿真生成数控程序,加强对UG软件的运用,巩固了机械设计知识。
三、主要技术指标1. 零件图1张;2. 三维建模零件1个;3. 辅助加工程序1份;4. 毕业设计论文1份;四、进度和要求1.搜集相关资料 2周2.加工仿真的中英科技文翻译 2周3.运用UG软件进行三维建模 2周4.运用UG软件进行辅助加工 2周5.运用UG软件数控仿真 2周6.编写说明书(论文) 2周7.准备并完成答辩 2周五、主要参考书及参考资料[1] 刘治映《毕业设计(论文)写作导论》.长沙:中南大学出版社.2006.6[2] 徐伟杨永《计算机辅助与制造》.北京:高等教育出版社.2011.2[3] 于杰《数控加工与编程》. 北京:国防工业出版社.2009.1[4] 赵长明《数控加工工艺及设备》. 北京:高等教育出版社.2003.10.[5] 麓山文化《UG7从入门到精通》.北京:机械工业出版社2012,2[6] 朱焕池《机械制造工艺学》. 北京:机械工业出版社.2003.4[7] 李提仁《数控加工与编程技术》. 北京:北京大学出版社.2012.7[8] 焦小明《机械加工技术》. 北京:机械工业出版社.2005.7[9] 龚桂义《机械设计课程设计图册》(第三版).高等教育出版社.2010.[10] 薛顺源《机床夹具设计》.机械工业出版社,2001.[11] 肖继德陈宁平《机床夹具设计》.机械工业出版社,2002.[12] 张世昌《机械制造技术基础》.天津大学出版社,2002.[13] 刘建亭《机械制造基础》.机械工业出版社,2001.[14] 庄万玉丁杰雄《制造技术》.国防工业出版社,2005.[15] 韩鸿鸾荣维芝《数控机床加工程序的编制》. 北京:机械工业出版社.2002.12[16] 周湛学《机电工人识图及实例详解》.北京:化学工业出版社.2011.12[17] 施平《机械工程专业英语教程》.第二版.电子工业出版社.学生指导教师系主任摘要数控编程是一种可编程的柔性加工方法,它的普及大大提高了加工效率。
数控加工中心典型零件编程实例
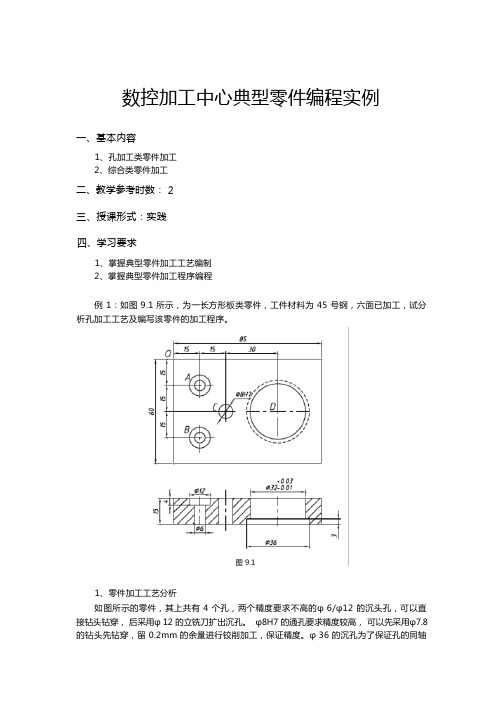
数控加工中心典型零件编程实例一、基本内容1、孔加工类零件加工2、综合类零件加工二、教学参考时数:2三、授课形式:实践四、学习要求1、掌握典型零件加工工艺编制2、掌握典型零件加工程序编程例 1:如图 9.1 所示,为一长方形板类零件,工件材料为 45 号钢,六面已加工,试分析孔加工工艺及编写该零件的加工程序。
图 9.11、零件加工工艺分析如图所示的零件,其上共有 4 个孔,两个精度要求不高的φ 6/φ12 的沉头孔,可以直接钻头钻穿,后采用φ 12 的立铣刀扩出沉孔。
φ8H7 的通孔要求精度较高,可以先采用φ7.8的钻头先钻穿,留 0.2mm 的余量进行铰削加工,保证精度。
φ 36 的沉孔为了保证孔的同轴度和表面的垂直度可以采用背镗工艺,因此该零件安排的加工工艺过程如下:(1)为保证孔间距精度,先采用中心钻点孔。
(2)采用φ 6 的钻头钻削两个φ6 孔。
(3)采用φ7.8 钻头钻削φ8 孔留余量0.2mm 。
(4)采用φ30 钻头钻留余量2mm 。
(5)扩φ 12 沉孔。
(6) 粗镗φ32 孔留余量 0.03mm 。
(7)背镗φ36 孔至尺寸。
(8)铰φ 8H7。
(9) 精镗φ 32 孔。
2、刀具及切削用量的选择加工零件所需的刀具及其切削用量选择见表。
表 加工刀具及切削用量3、确定编程原点位置及相关的数值计算根据工艺分析, 为方便计算与编程, 如图10.1所示, 选左上角的O 点为工件坐标系原点。
4个点位的坐标如下:A (X = 15.00 Y = -15.00)B (X = 15.00 Y = -45.00)C (X = 30.00 Y = -30.00)D (X = 60.00 Y = -30.00) 4、参考程序程序段O100 程序名号G40 G80 G49; 安全设定。
G28 G91 Z0; 经当前点,返回换刀点。
G28 X0 Y0;返回机床原点。
G54; 坐标系设定。
N1 M06 T01; 换1号刀 ( φ3mm中心钻), 适用无机械手盘式刀库。
数控车床典型零件编程与仿真加工

实践与探索Exploration数控车床典型零件编程与仿真加工文/张耀明 唐六元定要事先考虑周全,设计好软、硬件交换方案,准确无误后再进行交换检查。
(8)特殊处理法。
当今的数控系统已进入PC基、开放化的发展阶段,其中软件含量越来越丰富,有系统软件、机床制造者软件,甚至还有使用者自己的软件,由于软件逻辑的设计中不可避免的一些问题,会使得有些故障状态无从分析,例如死机现象。
对于这种故障现象则可以采取特殊手段来处理,比如整机断电,稍作停顿后再开机,有时此法可能将故障消除。
维修人员可以在自己的长期实践中摸索其规律或者采取其他有效的方法。
二、电气维修与故障的排除 电气故障的分析过程也就是故障的排除过程。
因此电气故障的一些常用排除方法在上述的分析方法中已综合介绍过了,下面列举几个常见电气故障供维修者参考。
1.电源故障电源是维修系统乃至整个机床正常工作的能量来源,它的失效或者故障,轻者会丢失数据,重者会造成停机重者会毁坏系统局部甚至全部。
发达国家由于电力充足,电网质量高,因此其电气系统的电源设计考虑较少,这对于我国有较大波动和高次谐波的电力供电网来说就略显不足,再加上人为因素,难免出现由电源而引起的故障。
2.数控系统位置环故障 (1)位置环报警。
可能是位置测量回路开路、测量元件损坏、位置控制建立的接口信号不存在等。
(2)坐标轴在没有指令的情况下产生运动。
可能是漂移过大、位置环或速度环接成正反馈、反馈接线开路、测量元件损坏。
3.机床坐标找不到零点可能是零方向在远离零点、编码器损坏或接线开路、光栅零点标记移位、回零减速开关失灵。
4.机床动态特性变差如果机床动态特性变差,工件加工质量下降,甚至在一定速度下机床发生振动。
这其中有很大一种可能是机械传动系统间隙过大甚至磨损严重,或者导轨润滑不充分甚至磨损造成的。
对于电气控制系统来说则可能是速度环、位置环和相关参数已不在最佳匹配状态,应在机械故障基本排除后重新进行最佳化调整。
典型零件数控加工工艺分析及编程
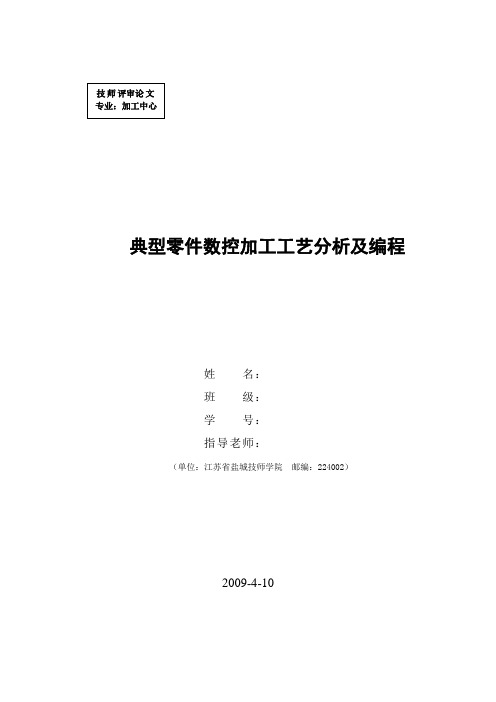
典型零件数控加工工艺分析及编程姓名:班级:学号:指导老师:(单位:江苏省盐城技师学院邮编:224002)2009-4-10典型零件数控加工工艺分析及编程【摘要】针对典型零件选择机床、夹具、刀具及量具,拟定加工工艺路线、切削用量等,编写数控加工的程序。
【关键词】工艺编程一、数控加工工艺路线的设计工艺路线是指零件加工所经过的整个路线,也就是列出工序名称的简略工艺过程。
工艺路线的拟定是制订工艺规程的重要内容,其主要任务是选择各个表面的加工方法,确定各个表面的加工顺序及整个工艺过程的工序数目和工序内容。
数控加工工艺路线的设计与通用机床加工工艺路线的设计的主要区别在于它往往不是只从毛坯到成品的整个过程,而仅是几道数控加工工序工艺过程的具体描述。
因此在工艺路线设计中一定要注意到,由于数控加工工序一般都穿插于零件加工的整个工艺过程中,因而要与其它加工工艺衔接好。
⒈工序的划分根据数控加工的特点,数控加工工序的划分一般可按下列方法进行:⑴以一次安装、加工作为一道工序。
这种方法适合于加工内容较少的零件,加工完后就能达到待检状态。
⑵以同一把刀具加工的内容划分工序。
有些零件虽然能再一次安装加工中加工很多代加工表面,但考虑到程序太长,会受到某些限制(主要是内存容量),机床连续工作时间的限制(如一道工序在一个工作班内不能结束)等,此外,程序太长会增加出错与检索的困难。
因此程序不能太长,一道工序内容不能太多。
⑶以加工部位划分工序。
对于加工内容很多的工件,可按其结构特点将加工部位分成几个部分,如内腔、外形、曲面或平面,并将每一部分的加工作为一道工序。
⑷以粗、精加工划分工序。
对于加工后易发生变形的工件,由于对粗加工后可能发生的变形需要进行校形,故一般来说,凡要进行粗、精加工的过程,都要将工序分开。
⒉顺序的安排顺序的安排应根据零件的结构和毛坯,以及定位、安装与夹紧的需要来考虑。
顺序安排一般应按以下原则进行:⑴上道工序的加工不能影响下道工序的定位与夹紧,中间穿插于通用机床加工工序的也应综合考虑;⑵先进性内腔加工,后进行外形加工;⑶以相同定位、夹紧方式或用同一把刀具加工的工序,最好连续加工,以减少重负定位次数和换刀次数。
典型轴类零件加工工艺与编程

典型轴类零件加工工艺与编程一、引言轴类零件是机械加工中非常常见的零件类型,其具有复杂的外形和高精度的加工要求。
为了满足零件加工的需求,制定适当的加工工艺和编程方案是非常关键的。
本文将介绍典型轴类零件的加工工艺和编程方法,帮助读者更好地理解和应用于实际的加工过程中。
二、典型轴类零件加工工艺2.1 零件材料选择在选择轴类零件的加工工艺之前,首先要考虑的是零件的材料选择。
常见的轴类零件材料包括铝合金、不锈钢和钢等。
根据零件的具体应用和要求,选择适当的材料能够提高加工效率和产品品质。
2.2 加工工艺流程典型轴类零件的加工工艺流程一般包括以下几个步骤:1.零件装夹:根据零件的形状和要求,选择合适的夹具进行装夹,确保零件的稳定和准确性。
2.设计刀具:根据零件的形状和要求,选择适当的刀具进行加工。
常见的刀具有立铣刀、刨刀和车刀等。
3.粗加工:使用合适的刀具进行粗加工,根据零件的形状和要求,进行适当的切削操作,以去除多余的材料。
4.精加工:在粗加工的基础上,使用更小的切削量进行精细加工,以达到所需的精度和表面质量。
5.修整工序:根据零件的要求,使用刮刀或砂纸等工具进行修整操作,以改善零件的表面质量。
6.检测与测量:对加工完成的零件进行检测和测量,确保零件的尺寸和形状符合要求。
7.表面处理:根据需要,对零件进行表面处理,如喷漆、阳极氧化或镀铬等。
2.3 加工工艺参数在进行轴类零件加工时,需要确定适当的加工工艺参数,以保证加工质量和效率。
常见的加工工艺参数包括:•进给速度:切削刀具在加工过程中每单位时间内移动的距离,通常以毫米/分钟(mm/min)表示。
•切削速度:切削刀具相对于工件表面移动的速度,通常以米/分钟(m/min)表示。
•切削深度:每次切削过程中刀具与工件之间的距离,通常以毫米(mm)表示。
•刀具压力:刀具与工件之间的压力,通常以牛顿(N)表示。
•加工冷却液:加工中使用的冷却液,可降低加工温度,减少刀具磨损和工件变形。
- 1、下载文档前请自行甄别文档内容的完整性,平台不提供额外的编辑、内容补充、找答案等附加服务。
- 2、"仅部分预览"的文档,不可在线预览部分如存在完整性等问题,可反馈申请退款(可完整预览的文档不适用该条件!)。
- 3、如文档侵犯您的权益,请联系客服反馈,我们会尽快为您处理(人工客服工作时间:9:00-18:30)。
• 通过上述分析,可采取以下几点工艺措施。 • ① 对图样上给定的几个精度要求较高的尺寸, 因其公差数值较小,故编程时不必取平均值,而 全部取其基本尺寸即可。 • ② 在轮廓曲线上,有三处为过象限圆弧,其 中两处为既过象限又改变进给方向的轮廓曲线, 因此在加工时应进行机械间隙补偿,以保证轮廓 曲线的准确性。 • ③ 为便于装夹,坯件左端面应预先车出夹持 部分,右端面也应先粗车并钻好中心孔。毛坯选 φ60mm棒料。
• (4)切削用量选择 • ① 背吃刀量的选择 • 轮廓粗车循环时选ap=3mm,精车时ap=0.25mm; • 螺纹粗车循环时选ap=0.4mm,精车时ap=0.1mm。 • ② 主轴转速的选择 • 车直线和圆弧时,查表2-1选粗车切削速度 vc=90m/min 精车切削速度vc=120m/min。 • 然后计算主轴转速n, 粗车时为500r/min,精车时为 1200r/min。车螺纹时主轴转速 n=320r/min。 •
• (6)数控加工工艺卡片拟订 • 将前面分析的各项内容综合成表2-7所 示的数控加工工艺卡片,此表是编制加工 程序的主要依据和操作人员配合数控程序 进行数控加工的指导性文件,主要内容包 括工步顺序、工步内容、各工步所用的刀 具及切削用量等。
• (3)确定加工顺序及走刀路线 • 加工顺序的确定按由内到外、由粗到精、由 近到远的原则确定,在一次装夹中应尽可能加工 出较多的工件表面。结合本零件的结构特征,可 先加工内孔各表面,然后加工外轮廓表面,由于 该零件为单件、小批量生产,故走刀路线的设计 不必考虑最短进给路线或最短空行程路线。 • 外轮廓表面的车削走刀路线可沿零件轮廓顺 序进行,如图2-2所示。
典型零件的编程
第2章 数控车削加工工艺
2.3 典型零件的加工工艺分析 2.1 轴类零件 以图2-1所示的典型轴类零件为例,所用机床为配备HNC-21T数控系统的CJK 数控车床,表面由圆柱、圆锥、顺圆弧、逆圆 弧、双曲线、螺纹等表面组成,其中多个直径 尺寸有严格的尺寸精度和表面粗糙度等要求; 球面Sφ50mm的尺寸公差还兼有控制该球面形 状(线轮廓)误差的作用;尺寸标注完整,轮 廓描述清楚;零件材料为45钢,无热处理和硬 度要求。
• (2)确定加工顺序及进给路线 • 加工顺序按由粗到精、由近到远(由右到左)的原 则确定,即先从右到左进行粗车(留0.25mm的精车余 量),然后从右到左进行精车,最后车削螺纹。 • HNC-21T数控车床具有粗车循环和车螺纹循环的功 能,只要正确使用编程指令,机床数控系统就会自行确定 其进给路线,因此,该零件的粗车循环和车螺纹循环不需 要人为确定其进给路线(但精车的进给路线需要人为确 定)。该零件从右到左沿零件表面轮廓的精车进给路线如 图2-22所示。
图2-2 轴承套零件
• (1)零件图工艺分析 • 该零件表面由内外圆柱面、内圆锥面、顺圆 弧、逆圆弧及外螺纹等表面组成,其中多个直径 尺寸与轴向尺寸有较高的尺寸精度和表面粗糙度 要求;零件图尺寸标注完整,符合数控加工尺寸 的标注要求;轮廓描述清楚完整;零件材料为45 钢,切削加工性能较好,无热处理和硬度要求。 • 通过上述分析,采取以下几点工艺措施。 • ① 零件图上带公差的尺寸,因公差值较小, 故编程时不必取其平均值,而取基本尺寸即可。 • ② 左右端面均为多个尺寸的设计基准,故在 相应工序加工前,应该先将左右端面车出来。 • ③ 内孔尺寸较小,镗1:20锥孔与镗φ32孔及 15°斜面时需掉头装夹。
• (2)确定装夹方案 • 内孔加工时以外圆定位,用三爪自动定心卡 盘夹紧。加工外轮廓时,为保证一次安装加工出 全部外轮廓,需要设一圆锥心轴装置(如图2-24 所示的双点画线部分),用三爪卡盘夹持心轴的 左端,心轴的右端留有中心孔并用尾座顶尖顶紧 以提高工艺系统的刚性。
图2-24 外轮廓车削装夹方案
图2-2 外轮廓加工走刀路线
• (4)刀具选择 • 将选定的刀具参数填入表2-6所示的轴承套数控加工 刀具卡片中,以便于编程和操作管理。 • (5)切削用量选择 • 根据被加工表面的质量要求、刀具材料和工件材料, 参考切削用量手册或有关资料选取每转进给量,然后计算 主轴转速与进给速度。 • 背吃刀量的选择因粗、精加工而有所不同。粗加工时, 在工艺系统刚性和机床功率允许的情况下,应尽可能取较 大的背吃刀量,以减少进给次数;精加工时,为保证零件 表面粗糙度要求,背吃刀量一般取0.1~0.4mm较为合适。
图2-1 精车轮廓进给路线
• (3)刀具选择 • ① 选用φ5中心钻钻削中心孔。 • ② 粗车及平端面选用90º 硬质合金右偏刀, 为防止副后刀面与工件轮廓干涉(可用作图法检 验),副偏角不宜太小,选35°。 • ③ 为减少刀具数量和换刀次数,精车和车螺 纹选用硬质合金60°外螺纹车刀,刀尖圆弧半径 应小于轮廓最小圆角半径, 取rε=0.15~0.20mm。 将所选定的刀具参数填入数控加工刀具卡片中 (见表2-4),以便于编程和操作管理。
• ③ 进给速度的选择 • 先查表2-3选择粗车、精车时进给量分 别为 0.4 mm/r和0.15mm/r。 • 再计算粗车、精车时的进给速度分别 为 200mm/min和180mm/min。 • 综合前面分析的各项内容,并将其填 入表2-5(数控加工工艺卡片)。
• 2.2 轴套类零件
• 以图2-2所示的轴承套零件为例,分析轴套类零 件的数控车削加工工艺(单件、小批量生产)。